Топливо из масла и опилок
: 29 Сен 2010 , Чарлз Дарвин — великий популяризатор эволюционной идеи , том 34, №4Мировую экономику уже не первый год лихорадит от панических прогнозов насчет истощения запасов нефти и скачков цен на «черное золото». Недаром проблемы в области производства биотоплива, обсуждавшиеся вчера узким кругом специалистов, сегодня выплеснулись на страницы массовых изданий. Наряду с серьезными разработками публике представляют и откровенно спекулятивные проекты, так что разобраться в реальных перспективах «зеленых» технологий порой бывает непросто.
Россия — крупнейший экспортер «черного золота» — сегодня не числится среди лидеров рынка биотоплива, однако работы в этом направлении ведутся и в нашей стране. Специалисты новосибирского Института катализа СО РАН уже создали серию эффективных катализаторов для производства топлива из доступного растительного сырья, включая отходы деревообрабатывающей промышленности
Идея биотоплива не нова – растительное сырье в том или ином виде веками обеспечивало энергетические потребности человечества. Всего 70—80 лет назад даже автомобили ездили на дровах! Машины оснащали газогенераторами, принцип действия которых был основан на газификации древесного топлива.
Такой транспорт появился в Европе уже в начале ХХ в. В нашей стране работы над автомобильными и тракторными газогенераторами начались в 1920-е гг. В основном ими оснащались грузовики, ведь подобный автомобиль должен был везти достаточно тяжелую и объемную газогенераторную установку и целую поленницу дров.
Однако на Западе существовали «дровяные» варианты легковых фиатов и ситроенов, а советские инженеры сумели установить небольшие газогенераторы на легковые ГАЗ-А и «эмку». Последнюю подобную модель «Урал-352» выпускали в Миассе вплоть до 1956 г.
После Второй мировой войны эра биотоплива практически закончилась: резкое увеличение добычи нефти вело к неуклонному снижению стоимости бензина и дизельного топлива. Однако нельзя сказать, что переход к ископаемым углеводородам был окончательным и бесповоротным. То здесь, то там разработчики предлагали альтернативу «черному золоту», в качестве которой чаще всего выступал этиловый спирт, получаемый, как известно, из растительного сырья. Даже первая советская баллистическая ракета Р-1 работала на 75 %-м водном растворе этилового спирта, который сгорал в жидком кислороде. Правда, топливо оказалось низкокалорийным, а сама система – неэффективной.
При таком раскладе к этанолу вернулись бы, скорее всего, не раньше, чем после истощения основных нефтяных месторождений. Однако в дело вмешалась политическая конъюнктура.
Не пить, а ездить
В США работы по биотопливу начались сразу же после введения эмбарго на арабскую нефть в 1973 г. Одним росчерком пера президент Джимми Картер перепрофилировал новый завод по производству спиртных напитков на производство топливного этанола. С тех пор на протяжении последних 30 лет колебания цен на нефть неизменно подогревали интерес ведущих стран к альтернативному горючему.
Настоящим пионером биотоплива стала Бразилия, где заправлять автомобили спиртом начали с 1970-х гг. Основная причина – отсутствие собственных нефтяных месторождений и наличие огромных плантаций сахарного тростника. Сегодня биоэтанол обеспечивает до 40 % потребностей страны в горючем. В Бразилии уже давно покупают в основном так называемые flexible fuel vehicles
К бразильскому результату стремятся все развитые страны мира. США уже сейчас производит почти столько же топлива на основе биоэтанола, сколько и Бразилия, однако его доля на огромном американском топливном рынке пока не превышает 3 %. В ближайшее время здесь планируется построить дополнительно 132 завода по производству топливного этанола из кукурузы, благодаря чему его производство удвоится. Евросоюз планирует к 2015 г. довести потребление биотоплив до уровня около 6 % от общего объема.
Нужно заметить, что сегодня топливный биоэтанол намного более распространен в мире, чем принято думать. Около 80 % всего этилового спирта производится для использования именно в качестве горючего, 12 % – для технических целей, и лишь 8 % имеет пищевое предназначение.
«Зеленый» дизель
Если этанол – частичный заменитель бензина, то для дизельного топлива также имеется возобновляемый заменитель – биодизель. Его получают из метанола и растительных масел, в первую очередь рапсового, пальмового и соевого, методом переэтерефикации.
Безусловным лидером по производству биодизеля являются страны ЕС. В 2009 г. здесь было произведено более 6 млн т биодизельного топлива, и объемы его производства устойчиво растут. Более того, в 2008 г. успешно совершил экспериментальный перелет из Лондона в Амстердам Боинг-747, баки которого были заправлены смесью из кокосового и пальмового масел и авиационного керосина.
Насколько полноценной заменой станут биоэтанол и биодизель традиционному топливу? У этанола есть несомненные преимущества – высокое октановое число (108 против 92—98 у бензина), что позволяет двигателям развивать гораздо более высокую мощность. Процесс сгорания этанола – кислородсодержащего соединения – гораздо эффективнее по сравнению с бензином, что среди прочего уменьшает токсичность выхлопных газов. Однако теплотворная способность этанола почти на 40 % ниже, чем у бензина, что приводит к более высокому расходу топливной смеси. Другим недостатком этанола является его способность поглощать большие количества воды, что приводит к расслоению топлива и ухудшению его качества.
Кроме этого, иногда в качестве катализаторов переэтерификации триглицеридов используют более сложные основания, такие как производное угольной кислоты гуанидин HNC(NH
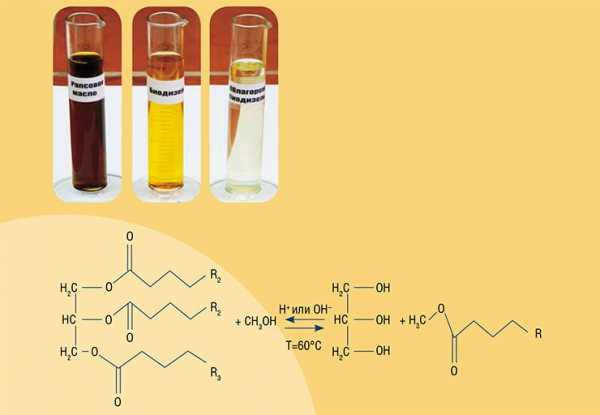
Такая гомогенная технология получения биодизеля, несмотря на простоту, имеет ряд недостатков: полученную смесь продуктов необходимо разделять, нейтрализовать и тщательно промывать. В результате образуются большие количества солей, мыла и сточных вод, которые необходимо утилизировать. Сам же катализатор при этом безвозвратно теряется. Получаемый при этом полезный побочный продукт – глицерин – загрязнен раствором солей и требует дополнительной очистки. Все это повышает себестоимость биодизеля и уменьшает конкурентоспособность этой технологии.
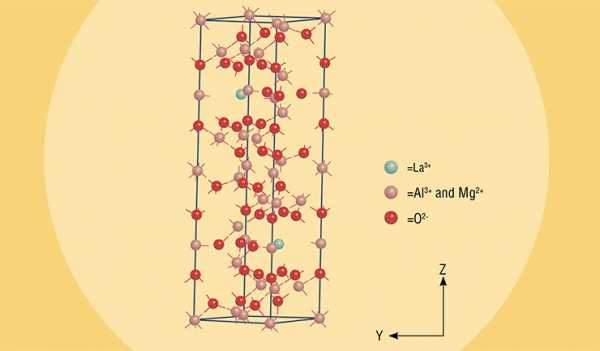
Однако к гетерогенным катализаторам переэтерификации предъявляются особые требования. В частности, они должны быть устойчивы к воде, содержащейся в исходных продуктах.
Все эти требования были учтены в Институте катализа СО РАН при разработке гетерогенных катализаторов переэтерификации. Понимание целевых реакций на молекулярном уровне позволило подойти к процессу разработки осознано и целенаправленно.
Акцент делался не столько на каталитическую активность веществ, сколько на стабильность их работы в реальных условиях. В результате было установлено, что одними из наиболее перспективных катализаторов для получения биодизеля являются гексаалюминаты бария, кальция и лантана.
Биодизель, как и биоэтанол, обладает как недостатками, так и достоинствами. В отличие от обычного дизельного топлива он почти не содержит серы. При попадании в почву или воду полностью разлагается уже через три недели. Кроме того, он обладает хорошими смазывающими характеристиками и более высоким цетановым числом – не менее 51. Однако более высокая вязкость не позволяет использовать его в холодное время года.
Поэтому в США и Европе сегодня проводится политика «мягкой» интеграции биотоплив: в основном, используется топливная смесь, содержащая 10 % этанола и 90 % бензина (стандарт Е10). Значительно реже встречается горючее с более высоким содержанием этанола – Е85.
Топливо, содержащее десятую часть этанола, не требует переделки двигателя машины и сегодня разрешено к применению всеми автопроизводителями. Поскольку в Америке в большинстве мегаполисов федеральный закон обязывает продавцов топлива применять кислородсодержащие добавки (норма – 2,7 % кислорода в бензине), то этанол сегодня практически заменил использовавшийся ранее метил-трет-бутиловый эфир. Для автомобилей, работающих на дизельном топливе, применяется смесь, состоящая на 20 % из биодизеля и на 80 % из солярки (марка В20).
Поэтому можно уверенно говорить, что топливные смеси – это уже стандарт сегодняшнего дня.
Такой компромиссный вариант одновременного использования традиционного моторного топлива и биотоплива позволяет использовать все достоинства первого и нивелировать недостатки последнего. Однако имеется другой подход интеграции биотоплив в существующую инфраструктуру потребления – налаживание производства более качественного биотоплива второго поколения.
ОКТАНОВОЕ ЧИСЛО топлива для двигателей внутреннего сгорания – условная величина, характеризующая меру его детонационной стойкости. Детонационная стойкость н-гептана принимается равной 0, а изооктана – 100. Октановое число топлива равно процентному содержанию изооктана в эталонной смеси с н-гептаном, которая ведет себя так же, как и исследуемое топливо.ЦЕТАНОВОЕ ЧИСЛО – характеристика воспламеняемости дизельных топлив, определяющая промежуток времени от впрыска топлива в цилиндр до начала горения. Воспламеняемость α-метилнафталина принимается за 0, гексадекана (цетана) – за 100. Цетановое число дизельного топлива равно объемной доле цетана в модельной смеси. Чем оно выше, тем более спокойно и плавно горит топливная смесь. Оптимальную работу обеспечивают топлива с цетановым числом равным 40—55
Альтернативным процессу переэтерификации триглицеридов жирных кислот и их производных для получения биодизеля может быть каталитический крекинг (разложение углеводородов сырья под действием высокой температуры в присутствии катализаторов), а также гидрокрекинг (крекинг в присутствии водорода).
В результате каталитического крекинга эфиров и триглицеридов жирных кислот образуются углеводороды дизельной, бензиновой и керосиновой фракций. Основным недостатком этого процесса является быстрая коксуемость катализатора – образование на его поверхности углеродных отложений.
В процессе гидрокрекинга используются катализаторы на основе переходных металлов, в присутствии которых происходит целый ряд разнообразных реакций. Основными продуктами гидрокрекинга триглицеридов являются легкие н-алканы С15—С17, которые получили название грин-дизель (Green diesel) или «суперцетан» (Supercetane).
Грин-дизель имеет более высокое цетановое число, чем биодизель и дизельное топливо, а также более высокую стабильность благодаря отсутствию кислородсодержащих функциональных групп. Поэтому сегодня данный процесс привлекает внимание исследователей в большей степени, чем получение биодизеля.
Горючее «из табуретки»
Чем активнее биотопливо входит в нашу жизнь, тем громче голоса скептиков. Так ли экологически безупречно «зеленое горючее»? Не загрязняет ли его производство планету сильнее, чем все автомобильные выхлопы, вместе взятые? И главное – не поставит ли увлечение экотопливом человечество на грань голодной смерти?
Известно, что с одного гектара можно получить не более 0,3 т соевого масла, 1 т – рапсового и 5 т – пальмового. С пальмой – «топливным рекордсменом» среди наземных растений – связывают свои планы на будущее многие азиатские государства. Так, власти Малайзии намерены в ближайшее время полностью перейти на биодизель из пальмового масла. А японская фирма «Toyo» собирается построить на Филиппинах завод по производству биосолярки из кокосовых орехов. Россия же и Европа, по понятным причинам, в первую очередь ориентируются на выращивание рапса.
Одно из преимуществ технологии гидрокрекинга перед переэтерификацией в производстве биотоплив – возможность реализации этого процесса на существующем стандартном нефтеперерабатывающем оборудовании. Кроме того, продукты гидрокрекинга по своему составу и свойствам подобны углеводородам, входящим в состав дизельной и бензиновой нефтяных фракций, поэтому могут быть использованы совместно с ними в двигателях внутреннего сгорания.Для гидрокрекинга растительных масел и жирных кислот, в основном, используются промышленные сульфидированные катализаторы нефтепереработки (NiMo/Al2O3 и CoMo/Al2O3 при температурах 310—360 °С и давлениях водорода 7—15 МПа). Получающиеся продукты – н-алканы – имеют такую же длину углеводородной цепи, что и исходные жирные кислоты; кислород при этом удаляется в виде воды, а глицериновая группа превращается в пропан.
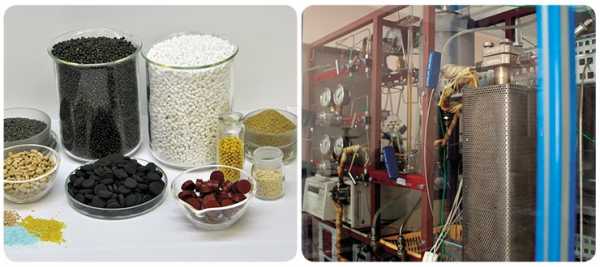
Однако что хорошо для нефти, не очень подходит для растительных масел: из-за низкого содержания серы в исходном сырье катализаторы быстро десульфидируются и дезактивируются. Добавление соединений серы спасает положение, но целевой продукт в результате загрязняется. Поэтому более перспективными являются катализаторы несульфидной природы.
В Институте катализа СО РАН была разработана серия катализаторов на основе никеля и меди, позволяющих эффективно превращать растительные масла и их производные в углеводороды топливного назначения при тех же температурах и давлении водорода, что и промышленные катализаторы.
Следует отметить, что сама по себе медь не обладает каталитической активностью в реакции гидрокрекинга, но она через дополнительную активацию водорода способствует восстановлению оксида никеля при более низкой температуре, а также препятствует побочной реакции метанизации продуктов гидрокрекинга
Вследствие биотопливного бума во всем мире действительно выросли цены на кукурузу и все виды масляничных культур, в том числе даже на те, которые не используются при производстве биодизеля. И если в России по состоянию на 2005 г. пустовало более 15 млн га пашни, потенциально пригодной для выращивания рапса топливного назначения, то большинство других стран не может себе позволить такое «расточительство».
В поисках альтернативного источника биотоплива исследователи все чаще отказываются от использования сельскохозяйственных культур. Например, обращаются к идее переработки органических отходов. Пока акции по использованию отходов носят скорее рекламный характер, однако среди них есть удачные проекты. Например, на аризонском курорте Фаирмонд в биотопливо превращают… отработанный кулинарный жир.
Один из наиболее перспективных источников биодизельного топлива – микроскопические водоросли, такие как известная хлорелла. Микроводоросли обладают рядом преимуществ по сравнению с традиционно используемыми масленичными культурами: они способны накапливать большие (до 75 % сухого остатка) количества жиров; растут быстрее любых других растений; могут жить как в морской, так и в пресной воде. Но главное – они не конкурируют с сельскохозяйственными культурами за посевные площади. Более того, микроводоросли можно выращивать даже в загрязненных нитратами и фосфатами сточных водах, попутно их очищая. А отходы от производства биотоплива из микроводорослей также могут быть переработаны в ценные продукты (биополимеры, пигменты, удобрения).
Впрочем, можно и вовсе не заниматься разведением чего бы то ни было, ведь ценное сырье в буквальном смысле валяется под ногами. Речь идет о переработке отходов деревообрабатывающей промышленности, которая уже сегодня может быть достаточно эффективна не только в экологическом, но и в экономическом плане.
Традиционный продукт переработки древесных отходов – гидролизный спирт (вспомним знаменитую «табуретовку» Остапа Бендара). Однако отходы деревообрабатывающей промышленности можно использовать в качестве сырья для получения топлива более эффективно, если отойти от традиционного выбора между этанолом и бензином. В самом деле, если каждое из этих топлив имеет свои недостатки, нельзя ли создать из опилок новое горючее?
Такие работы уже ведутся во всем мире. С помощью быстрого пиролиза из древесины можно получить продукт, условно названный «бионефтью», – жидкость, похожую на разбавленный деготь. Из-за высокого (до 45 %) содержания кислорода бионефть не пригодна для использования напрямую в качестве моторного топлива. Из нее нужно удалить кислород и насытить водородом, т. е. провести реакцию гидродеоксигенации. И сегодня одна из важнейших задач в этой области – разработка соответствующих катализаторов.
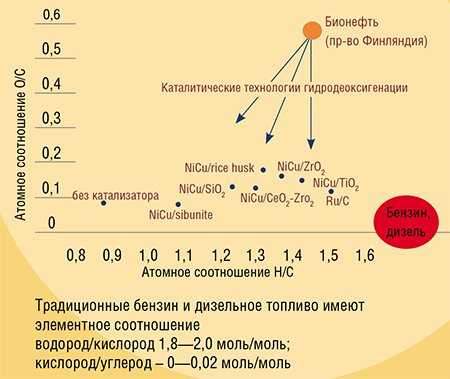
Следующая стадия – гидродеоксигенация полученной таким образом бионефти. В рамках международного проекта BIOCOUP специалисты ИК СО РАН разрабатывают катализаторы нового типа, которые могли бы эффективно справиться с такой задачей.
Здесь были предложены несульфидированные никельсодержащие катализаторы гидродеоксигенации. Серия никелевых и биметаллических медь-никелевых катализаторов, где в качестве носителей использовался ряд оксидов (Al2O3, SiO2 и др.) была протестирована на модельном соединении бионефти – анизоле (метильном эфире обыкновенного фенола) при температуре 300 °С и давлении водорода 0,5 МПа.
Оказалось, что предложенные катализаторы по основным показателям превосходят коммерческие аналоги. Тестирование лучших образцов катализаторов гидродеоксигенации на реальной бионефти в университете Гронингена (Нидерланды) подтвердило их перспективность
Продукты деоксигенации бионефти могут использоваться для дальнейшей переработки на стандартном нефтеперерабатывающем оборудовании совместно с нефтяными фракциями.
Вне зависимости от того, удастся ли разработать эффективные технологии производства биотоплива или нет, остается открытым вопрос: в состоянии ли биоресурсы в принципе обеспечить энергетические потребности человечества?
Любой используемый на Земле вид энергии (кроме атомной) имеет в своей первооснове энергию Солнца. Ежегодно на Землю обрушивается 1012 Вт солнечной энергии, и хотя все наземные растения с помощью фотосинтеза способны аккумулировать менее 1 %, речь идет об огромной величине!
С учетом современных возможностей переработки доступного растительного сырья эксперты прогнозируют, что в ближайшие десятилетия биоэнергетика обеспечит не более одной пятой от общего объема энергопотребления. Это немало, особенно если учесть, что в первую очередь речь идет о замене автомобильного горючего. Что касается содержимого бензобаков, то современные технологии позволят к 2020 г. заменить каждый десятый литр горючего традиционного на горючее, полученное напрямую из растительного сырья. Более того, новые научные разработки, вероятно, скорректируют этот прогноз в сторону увеличения доли биодизеля и биоэтанола.
Что касается России, то хотелось бы, чтобы наша страна стала не столько потребителем смесевых топлив, сколько крупнейшим экспортером биотоплива. При этом предпочтительно, чтобы биотопливо производилось в непосредственной близости от сырьевой базы и с использованием современных отечественных технологий. Безусловно, также необходима корректировка ряда нормативных актов, например, по поводу акцизов на топливный биоэтанол.
Первые шаги уже делаются в обоих направлениях. Так, введен в действие ГОСТ Р 52368—2005 «Топливо дизельное евро», который предусматривает применение биодизеля. Растут посевные площади для выращивания рапса; начато или планируется строительство около двадцати заводов по производству топливного биоэтанола из злаковых культур и т. д. Интенсивность усилий, направленных на создание производств биотоплива из возобновляемого сырья, дает основание надеяться, что наша страна в обозримом будущем будет занимать заметное место в мировом топливном балансе не только благодаря своим запасам ископаемого топлива.
Резюмируя, скажем, что если сравнивать прогресс в биоэнергетике и производстве биотоплив с полетом самолета, то можно считать, что человечество уже прошло точку невозврата и должно двигаться только вперед. И дело теперь лишь за учеными и технологами, которые должны сделать все, чтобы биотоплива стали конкурентными на топливном рынке. В свое время великий Менделеев заметил, что «сжигать нефть все равно, что топить печку ассигнациями». Так не пора ли вернуться к дровам?
Литература
Дундич В. О., Яковлев В. А. Гидродеоксигенация биодизеля в присутствии катализаторов на основе благородных металлов // Химия в интересах устойчивого развития. 2009. Т. 17. С. 527—532.
Яковлев В. А., Хромова С. А., Ермаков Д. Ю. и др. Катализатор, способ его приготовления (варианты) и процесс гидродеоксигенации кислородорганических продуктов быстрого пиролиза биомассы, Патент РФ, 2 335 340, от 10.10.2008, пр. 22.08.2007.
Дундич В. О., Хромова С. А., Ермаков Д. Ю. и др. Исследование никелевых катализаторов реакции гидродеоксигенации биодизеля // Кинетика и катализ. 2010. Т. 51, № 5. С. 728—734.
Yakovlev V. A., Khromova S. A., Sherstyuk O. V. et al. Development of new catalytic systems for upgraded bio-fuels production from bio-crude-oil and biodiesel // Catalysis Today. 2009. V. 144 P. 362—366.
В публикации использованы фото М. Кошелевой
: 29 Сен 2010 , Чарлз Дарвин — великий популяризатор эволюционной идеи , том 34, №4scfh.ru
Брикеты из опилок своими руками: цена оборудования, технология
Для топки печей многие привыкли использовать дрова. На их заготовку уходит много времени и труда, да и стоят они недешево.
Альтернативным и недорогим вариантом для отопления различных помещений являются топливные брикеты из опилок, которые можно не только купить, но и изготовить самостоятельно. Отходы деревообработки прессуются в специальные формы.
Топливные брикеты заменят дрова и уголь, а для их производства применяются опилки, оставшиеся после обработки деревьев.
Преимущества топливных брикетов
- Основным преимуществом брикет для топлива является их более высокая температура горения. За счет низкой влажности и более высокой плотности у них намного выше теплоотдача, чем у дров.
- Они удобны во время перевозки и складирования. Благодаря правильной форме и большой плотности, брикеты обладают большей массой, чем дрова с таким же объемом.
- Изготавливаются из отходов деревообработки. За счет этого их цена намного ниже, чем на уголь или дрова.
- Несложное изготовление. Зная метод технологии, легко можно изготовить брикеты из опилок своими руками.
- Обладая низкой влажностью, они выделяют меньше дыма и сажи, и практически не загрязняют дымоход.
- Имеют ровное горение. Во время топки они не растрескиваются и не разбрасывают угли.
Чтобы знать, как сделать из опилок брикеты для топки, необходимо изучить метод их изготовления, иметь специальное оборудование и подобрать правильное сырье.
Сырье и технология изготовления брикетов самостоятельно
Для изготовления спрессованного продукта, в первую очередь необходимы опилки.
Приобрести их можно на пилорамах. Для самостоятельной переработки можно найти остатки древесины и в других местах. Например, много мелких остатков образуется во время лесозаготовок. Найти обрезки можно в мастерских, где изготавливают изделия из дерева, а также на заводских предприятиях, которые изготавливают мебель.
Для приготовления брикетов подходят деревья любого сорта. Опилкам необходимо иметь:
- размеры до 6-ти мм;
- влажность должна составлять не более 12%;
- подгнивших щепок не должно быть больше 5% от всей массы отходов.
Для приготовления брикетного топлива потребуется обычная глина, которая является связующим элементом. При заводском производстве на смесь из опилок воздействует высокое давление и на выходе получается плотное, спрессованное топливо. При домашних условиях пресс не может создавать такие усилия, поэтому и используются связующие элементы.
Производство топливных брикетов из опилок основано на трех основных этапах:
- Подготовка сырья. Приготовленные отходы дробятся и размельчаются так, чтобы получилась однородная консистенция.
- Изготовление спрессованных форм. С помощью специального станка сырье прессуется под давлением.
- Доведение массы до готового состояния с помощью сушки. Делается это на сушильном станке или естественным путем под солнцем.
Для обустройства брикетной фабрики в домашних условиях, нет особой необходимости в приобретении некоторых дорогостоящих станков.
Сырье можно сушить под солнцем — это исключает покупку сушилки, а если приобрести готовые опилки, то не понадобится и дробилка. Из оборудования для производства брикетов из опилок понадобится только пресс-машина, которую можно сделать самостоятельно, приложив немного усилий и потратив небольшую сумму денег.
Также ее можно приобрести в готовом виде. Есть возможность выбрать станок из нескольких вариантов:
- Гидравлический. Опилки прессуются путем гидравлического сжатия.
- Шнековый. Выдавливаются шнеком через фильеру.
- Ударно-механический. Опилки поршнем пробиваются через фильеру.
Видео:
Цена станка для изготовления брикетов из опилок зависит от марки и производительности оборудования. Посмотрите стоимость ударно-механических прессов в таблице ниже:
При покупке пресса необходимо учитывать все их плюсы и минусы.
Сделать пресс своими руками
При изготовлении самодельного пресса необходимо определиться, будет это механическая или электрическая конструкция. Механический пресс дает небольшой объем, но при этом у него нет зависимости от электричества.
Самодельный пресс условно делится на три группы:
- С ручным приводом. Из стальной трубы изготавливается рама, которая для удобства во время применения может крепиться к стене. В ее нижней части неподвижно устанавливается форма, а сверху крепится рычаг. Для удобства, форму можно сделать со съемным дном. К рычагу добавляется нажимной элемент, который входит внутрь формы, оставляя небольшой зазор.
- С применением домкратов. Пресс для опилок в качестве рычага механизирован домкратом.
- С гидравлическим приводом. Устанавливается на опорной раме, опорная точка направлена вниз.
Видео:
Приготовление сырья
Этот процесс занимает немного времени, но при этом желательно сохранять правильные пропорции всех ингредиентов:
- Слишком крупные опилки дополнительно дробятся и измельчаются на более мелкие фракции.
- Добавляется немного воды и глина, которая способствует связыванию всех элементов.
- Для улучшения горючих свойств можно добавить немного бумаги.
- Все ингредиенты смешиваются в однородную массу (ручным или механическим способом).
Глину необходимо равномерно распределить по всему объему опилок, она является основным связующим элементом.
Видео:
Процесс создания брикетов
Полученный состав помещается в специальную форму и приводится в работу механизм пресс-устройства. Когда изготовление происходит ручным способом, рычаг следует держать до тех пор, пока полностью не сбежит вода.
С помощью станка процесс происходит значительно быстрее и проще, увеличивается производительность работ, и нет необходимости прилагать физические усилия.
Во время брикетирования смесь под давлением начинает нагреваться и за счет этого происходит спекание. В некоторых станках смесь предварительно нагревается при помощи тэнов во время поступления на шнек. Во время брикетирования главное не перегружать механизм и следить за равномерностью смеси.
Для получения более прочных и не рассыпаемых брикетов, необходимо стенки и дно формы обложить ветошью или бумагой и только потом засыпать смесь и прессовать.
Видео:
Просушка дешевого топлива
Если нет специальной сушилки, то необходимо подготовить место для просушки брикетов. После пресса они будут липкими и влажными, поэтому не рекомендуется складывать их друг на дружку, могут слипнуться.
Вынутые из формы изделия раскладываются для просушки на солнце или в хорошо отапливаемом помещении. Во время сушки можно использовать бумагу или ветошь, которые способны вытянуть из брикетов остаток влаги.
После окончания сушки их желательно упаковать, это необходимо для защиты от внешних факторов. По сравнению с заводскими изделиями, брикеты, изготовленные в домашних условиях значительно легче, сказывается недостаток давления.
Стоит помнить! Чем топливо суше, тем больше его теплоотдача.
Применение топлива из отходов
Продукт можно применять для различных целей:
- топливо вполне можно применить во время приготовления еды в помещениях. При его использовании нет дыма и запаха сажи, а еда готовится равномерно;
- отопление жилых зданий. Плотная и небольшая форма изготовленных брикетов безупречно подходит для печей, каминов и котлов;
- применяется для протапливания бань, саун и теплиц. Подходит ко всем нормам экологии;
- эти изделия хорошо брать с собой во время отдыха на природе. При горении в мангалах, брикет не дымится, а жар сохраняется достаточно долго. При попадании жира на топливо не происходит возгорания.
Процесс изготовления брикетов своими руками достаточно простой, а при их использовании сразу отпадают две проблемы:
- исключается мусор и пыль в доме, которые обычно присутствуют после применения дров или угля;
- избавляют от частых загрузок топлива, самодельные изделия разжигаются легче, горят дольше и дают больше тепла, чем обычные дрова.
К тому же, это достаточно эффективное, дешевое топливо и можно сэкономить, пользуясь брикетами изготовленными самостоятельно.
dachadoma.ru
Переработка древесных отходов в щепу
Процесс лесозаготовки, деревообработки и вторичного производства связан с образованием отходов древесины. Объемы вторсырья древесного производства соизмеримы с объемами готовой продукции. Дополнительным источником древесных отходов являются лесопарки и зеленые насаждения городов, которые периодически подвергаются санитарной вырубке и чистке. Однако, находит полезное применение не более половины остатков древесины. Ценный природный материал просто сгнивает без попыток утилизации. Поэтому переработка древесных отходов и вторичное использование сырья остаются актуальными.
На заготовительных полигонах остаются без переработки следующие виды сырья:
- корни и пни;
- ветви и сучья;
- мелкая древесная зелень;
- опилки и стружки;
- кора и верхушки.
В лесопильном производстве пятая часть от завезенного материала классифицируется как неделовая древесина или дрова, а часть уходит в опилки. На комбинатах по выпуску мебели, фанеры, шпона доля отходов составляет 35–60% от объема пиломатериала.
Стоит отметить, что древесные остатки являются ценным источником сырья для повторной переработки с целью получения изделий и материалов различного назначения. Их переработка послужит экономии природных ресурсов и решению экологических проблем.
Классификация древесного сырья
Отходы древесины классифицируются по плотности:
- кора и луб;
- мягкие – стружки и опилки, пыль, древесная зелень: хвоя и листья;
- твердые или кусковые – сюда относятся пни, горбыли, корни, ветви деревьев, обрезки.
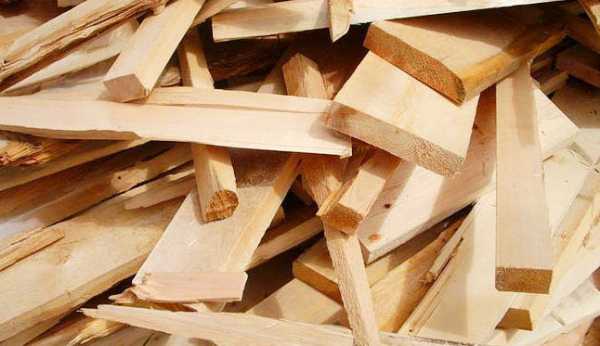
Обрезки древесины
По способу получения:
- при рубке леса: пни, вершины, ветки, кора, обрезки, дрова;
- при обработке кругляка или первичном лесопилении;
- остатки от производства шпона и фанеры: стружки и опилки, обрезки некондиция, рейки, горбыли, кора;
- вторичные отходы мебельных фабрик: обрезки доски, стружка и опилки.
Способы использования
Отходы деревообработки имеют самое широкое применение, они востребованы во многих отраслях хозяйства:
- строительство;
- древесно-стружечные плиты;
- цементно-стружечные плиты;
- арболит;
- кирпич;
- гипсовые листы;
- мебельные щиты;
- бумажное производство
- бумага и картон;
- источник тепловой энергии;
- топливные брикеты и пеллеты;
- дрова;
- сельское хозяйство;
- компост для повышения уровня плодородия суглинистых почв;
- добавка из опилок в почву парников и теплиц;
- подстилка для животных;
- переработка твердых отходов после вываривания экстракта в кормовую муку, обладающую антибактериальным свойством.
Опилки всех видов востребованы в гидролизном и кирпичном производстве, для обогрева и изготовления листов на гипсовой основе, для получения опилкобетона и органического топлива.
В частных хозяйствах деревянными опилками утепляют чердаки и подвалы. В условиях промышленных предприятий опилки необходимы для фильтрации стоков. Смесь опилок с торфом служит отличным наполнителем биотуалета.
На бумажных комбинатах и в сельском хозяйстве используют древесные отходы. Мелкие и крупные щепки, особенно хвойных пород деревьев, нужны для получения особого строительного материала арболита. Переработанные стружки после специальной обработки закладывают в древесно-стружечные и цементно-стружечные плиты, необходимые в жилищном строительстве.
Техника для измельчения древесины в щепу
Способы переработки
Переработка отходов древесины осуществляется по двум основным технологиям:
- химический метод гидролиза – получается в результате скипидар, уксусная кислота, уголь;
- механической – после перемалывания древесины выходит щепа для изготовления строительных плит, гранул и брикетов для отопления.
Перерабатывать древесину начинают с разделения по сортам и породам дерева. Затем сырье разделывают, очищают от участков гнили, обрабатывают паром.
Для очистки от вредных примесей, проникших из почвы либо сточных вод, обрабатывают солевыми растворами.
На следующем этапе материал проходит дробление на машинах с зубчатыми дисками. С целью облегчения процесса и снижения нагрузки на привод, дробилку подвергают парообработке.
Технология переработки и необходимое оборудование выбираются исходя из типа древесных отходов.
Специализированное оборудование для переработки древесных отходов подбирается в зависимости от выбранного способа переработки.
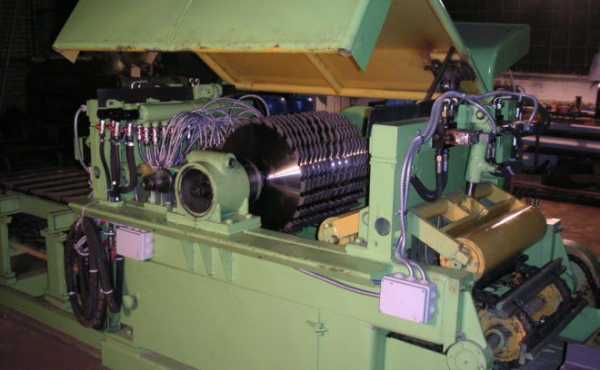
Оборудование для переработки древесины
В любом случае понадобятся:
- пресс-формы;
- шнековый транспортер;
- камера для сушки;
- ручные трамбовки;
- щепорубильный агрегат;
- смесительная станция;
- дровоколы;
- измельчители-шредеры;
- сепараторы;
- брикетировщики;
- газогенератор;
- бункер-накопитель;
- печь для выжигания углей;
- станция управления;
- транспортировщики.
Получение древесного угля
Эффективно утилизировать древесные отходы следует с помощью изготовления древесного угля. Древесный уголь используется в качестве второстепенного компонента в металлургическом и химическом производстве.
В строительных технологиях его используют для теплоизоляции. Как продукт перепроизводства служит добавкой в кормовую смесь для скота и птицы.
Характеризуется древесный уголь высокой теплотворностью и отсутствием токсичности, он полностью состоит из углерода. В процессе горения не выделяет ядовитых веществ, а также он пригоден для приготовления пищи.
Переработка на органическое топливо
В европейских странах обеспокоены вопросами экологии и стараются максимально снизить нагрузку на окружающую среду. Одним из способов служит развитие зеленых технологий и применение экологичного топлива на органической основе. Отработка лесопильной и деревообрабатывающей промышленности успешно используется после переработки как топливо.
Дешевые виды органического топлива, полученные из перемолотых древесных отходов:
Брикеты
Изготавливаются из остатков деревообработки. Могут поддерживать горение в течение 8 часов благодаря высокой плотности. При минимальном выделении угарного газа обеспечивают стойкое тепло.
Пеллеты
Топливный материал в форме гранул с высокой теплотворностью.
Производство дешевых энергоносителей – это решение вопроса утилизации отходов лесопиления, защита природной среды и получение альтернативного вида энергии.
Изготовление топливных брикетов
Одним из перспективных направлений по переработке отходов деревообработки является изготовление топливных брикетов. Популярность твердотопливных котлов растет, потому что они экономичны и эффективны. А теплотворная способность брикетов сравнима с каменным углем.
Количество выделенного тепла при сгорании угля составляет 22 МДж на килограмм, а древесных брикетов – 19. К примеру, теплотворная способность дров 10 МДж/кг. Экологический материал для отопления отличается низкой зольностью, а исходным сырьем служит щепа.
По причине постоянного роста цен на природный газ, потребность в альтернативных источниках тепла будет увеличиваться.
Для оснащения перерабатывающего производства потребуется:
- складское и транспортное оборудование;
- установка для измельчения вторсырья;
- пресс для формовки;
- упаковочная установка;
- сушильный агрегат.
Производство пеллет
Спрос на пеллеты, используемые в быту и на производстве, удерживается на высоком уровне. Продолжительность горения и теплотворная способность зависят от исходного сырья. В большинстве случаев применяются опилки.
Производственная линия включает:
- дробилки;
- сушильное оборудование;
- охладители;
- грануляторы;
- упаковочные машины.
Производство щепы
Прогрессивная технология переработки твердых отходов – это получение щепы. Щепа необходима как технологическое сырье для других производств и топлива. В соответствии с назначением ее разделяют на технологическую щепу и топливную.
Из практических наблюдений стало понятно, что активное горение в топке наблюдается после закладки дробленого материала размером 25–100 мм. Использование крупных древесных остатков не дает эффективного сжигания, потому что не формируется плотный слой.
Измельчение вторсырья происходит на рубительных машинах.
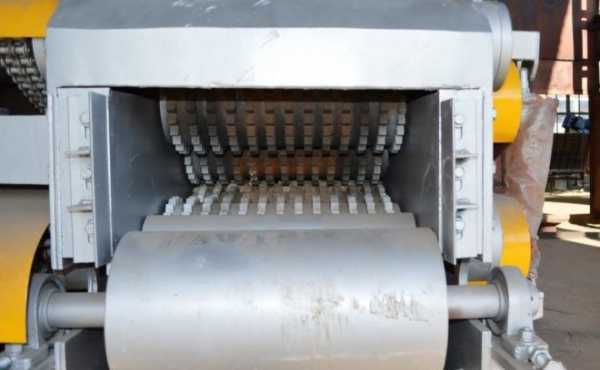
Барабанно-рубительная машина
Их конструкция отличается для различных видов и размеров перерабатываемых остатков и требований по качеству готовой щепы.
Машины встраиваются в технологическую линию. С учетом индивидуальных особенностей производства они выпускаются с горизонтальным и наклонным расположением загрузочного патрона, верхним, нижним и боковым отводом щепы, левого и правого исполнения. Это позволяет создать наилучшие условия работы и повысить производительность.
Размеры древесных отходов влияют на расположение патрона и величину его проходного сечения. План переработки и применяемая технология определяют выбор машины по производительности.
Вторым не менее важным механизмом при переработке в щепу является сортировка гирационного типа. Особенность ее конструкции в том, что короб с несколькими ситами совершает круговое движение в горизонтальной плоскости.
Во время переработки отходов лесопиления на современных установках, основное производство получает огромное количество дополнительного сырья. Благодаря своевременной утилизации отходов древесины, улучшается экологическая ситуация региона, где расположено производство. Поэтому вопрос утилизации древесных отходов поставлен на административном уровне любого края.
Видео: Производство переработка древесины
promzn.ru
Биотопливо из леса — Аналитика Лесной промышленности
Растёт спрос на биотоплива – горючие жидкости, изготовленные из возобновляемых биологических ресурсов. Один из них – древесина. Можно ли из древесины получать топливо, не уступающее нефтяному?
Первое, что нужно уяснить – это то, что именно бензина или керосина из дерева сделать нельзя. Оно не поддаётся разложению на углеводороды с прямой цепью, из которых главным образом состоят нефтепродукты. Однако это не означает, что из него нельзя получать вещества, способные заменить нефтепродукты.
Некоторые любят табуретовку
Первый в списке, конечно же, спирт. Из древесины можно получать два различных вида спирта. Первый, который так и называется древесным – по-научному метиловый спирт. Это вещество очень похоже на привычный этиловый спирт, как по горючести, так и по запаху и вкусу. Однако метиловый спирт отличается тем, что весьма ядовит, и приём его внутрь может привести к смертельному отравлению. Вместе с тем он является высококачественным моторным топливом, его октановое число даже выше, чем у этилового спирта, и намного выше, чем у обыкновенного бензина.
Технология получения метилового спирта из древесины очень проста. Он получается путём сухой перегонки, или пиролиза. Точнее, он является одной из составных частей жижки – смеси кислородсодержащих органических веществ, отделяющихся от свежевыгнанной древесной смолы. Однако выход полученного таким образом спирта слишком мал, чтобы он мог использоваться в качестве топлива. Это делает подобную технологию получения топлива бесперспективной.
Однако из древесины можно получить и этиловый спирт, в намного больших количествах. Этот спирт – так называемый гидролизный – получается при разложении целлюлозы, основного компонента древесины, с помощью серной кислоты. Вернее, при разложении целлюлозы получаются сахара, которые в свою очередь могут быть переработаны в спирт обычным путём. Этот способ получения этилового спирта весьма распространён в промышленности, именно гидролизным способом получают практически весь технический спирт, применяемый в непищевых целях.
Этиловый спирт может быть использован как непосредственно вместо бензина, так и в качестве присадки к бензину. Путём таких присадок получаются различные сорта биотоплива, популярные, в частности, в таких странах, как Бразилия.
Получение этилового спирта путём гидролиза древесины экономически несколько менее выгодно, чем получение его из различных сельскохозяйственных культур. Однако выгодной стороной такого способа получения биотоплива является то, что он не требует отведения сельскохозяйственных площадей под «топливные» культуры, не дающие пищевых продуктов, а позволяет использовать для его производства территории, задействованные в лесном хозяйстве. Это делает получение биотопливного этанола из древесины достаточно практичной технологией.
И терпентин на что-нибудь полезен
Недостатком этанола как топлива является его низкая теплота сгорания. При использовании в двигателях в чистом виде он даёт или меньшую мощность, или больший расход, чем бензин. Решить эту проблему помогает смешивание спирта с веществами с высокой теплотой сгорания. И не обязательно это продукты из нефти: в качестве такой присадки вполне годится скипидар, или терпентин.
Скипидар – тоже продукт переработки древесины, а если конкретно — хвойной: сосен, елей, лиственниц и других. Он достаточно широко применяется как растворитель, а наиболее очищенные его сорта находят применение в медицине. Однако лесоперерабатывающая промышленность в качестве побочного продукта производит большое количество так называемого сульфатного скипидара – низшего сорта, содержащего ядовитые примеси, не только неприменимого в медицине, но и находит весьма ограниченное применение в химической и лакокрасочной промышленности.
Вместе с тем скипидар из всех продуктов переработки древесины более всего похож на нефтепродукт, точнее – на керосин. Он отличается весьма высокой теплотой сгорания, может использоваться как горючее в керосиновых примусах, лампах, керогазах. Пригоден он и в качестве моторного топлива, правда, непродолжительное время: если его заливать в баки в чистом виде, двигатели вскоре выходят из строя из-за засмоления.
Однако скипидар можно использовать в качестве топлива не в чистом виде, а в качестве присадки к этанолу. Такая присадка не сильно снижает октановое число этилового спирта, но повышает теплоту его сгорания. Ещё одна положительная сторона такой технологии изготовления биотоплива в том, что скипидар денатурирует спирт, делает его непригодным для употребления внутрь в качестве алкоголя. А социальные последствия широкого внедрения неденатурированного спирта в качестве топлива могут стать весьма тяжелыми.
Лигниновые отходы – в доходы!
Такой компонент древесины, как лигнин, считается малополезным. Его применение в промышленности значительно менее широкое, нежели у целлюлозы. Несмотря на то, что он находит применение в производстве строительных материалов и в химической промышленности, чаще его просто сжигают прямо на лесохимпроизводстве. Однако, как выясняется, при пиролизе лигнина можно получить более разнообразные продукты, чем при пиролизе целлюлозы.
Лигнин состоит главным образом из ароматических циклов и коротких прямых углеводородных цепей. Соответственно, при его пиролизе получаются преимущественно углеводороды. Однако, в зависимости от технологии пиролиза, можно получать как продукт с высоким содержанием фенола и родственных ему веществ, так и жидкость, напоминающую нефтепродукты. Эта жидкость также пригодна в качестве присадки к этиловому спирту для получения биотоплива.
Разработаны технологии и установки для пиролиза, которые могут потреблять как лигнин из отвалов, так и неразделённые на лигнин и целлюлозу отходы древесины. Более высокие результаты получаются при смешивании лигнина или древесных отходов с мусором, состоящим из выброшенного пластика или резины: пиролизная жидкость получается более нефтеподобной.
Мирный атом и опилки
Ещё одна технология получения биотоплива из древесины разработана совсем недавно российскими учёными. Она относится к области радиохимии, то есть химических процессов, протекающих под воздействием радиоактивного излучения. В опытах учёных из ИФХЭ им. Фрумкина опилки и другие отходы древесины подвергались одновременному воздействию сильного бета-излучения и сухой перегонки, причём нагревание древесины проводилось именно с помощью сверхсильной радиации. Удивительно, но под воздействием радиации состав продуктов, получаемых при пиролизе, изменился.
В пиролизной жидкости, полученной «радиоактивным» способом, было обнаружено высокое содержание алканов и циклоалканов, то есть углеводородов, содержащихся главным образом в нефти. Эта жидкость получилась значительно легче нефти, сравнимой, скорее, с газоконденсатом. Причём экспертиза подтвердила пригодность этой жидкости для использования в качестве моторного топлива или переработки в высококачественные топлива, такие, как автомобильный бензин. Думаем, что это не заслуживает особого упоминания, но проясним ради успокоения страхов радиофобов: бета-излучение не способно вызывать наведённую радиоактивность, поэтому топливо, получаемое этим способом, безопасно и не проявляет радиоактивных свойств само.
Что пускать в переработку
Понятно, что предпочтительнее использовать для производства биотоплива не цельные стволы деревьев, а отходы переработки древесины, такие, как опилки, щепу, веточки, кору, да и тот же лигнин, который идёт в отвалы и печи. Выход этих отходов с гектара поваленного леса, конечно же, ниже, чем древесины в целом, но не следует забывать, что они получаются в качестве побочного продукта в производственных процессах, которые уже идут на многих предприятиях страны, соответственно, отходы производства дешевы и для их получения не нужно вырубать или засаживать под вырубку дополнительные площади леса.
В любом случае, древесина является ресурсом возобновляемым. Способы восстановления лесных площадей давно известны, а во многих регионах страны наблюдается даже и неконтролируемое зарастание лесом заброшенных сельскохозяйственных земель. Так или иначе, Российская Федерация не относится к странам, где к сбережению леса следует относиться со всем тщанием; площадей нашего леса и его потенциала к самовосстановлению вполне достаточно, чтобы загрузить полностью и лесоперерабатывающую промышленность, и производство биотоплив, и многие другие производства.
wood-prom.ru
переработка древесных опилок в топливные брикеты
Переработкой древесины занимаются государственные и частные предприятия. Древесные отходы, как правило, утилизируются, платя экологическим службам районов штрафы, не видя выхода из этого положения.
Простое сжигание опилок с повышенной влажностью встречает понятное сопротивление экологов, так как при этом возникают проблемы неполного сгорания и выделения окиси углерода (угарного газа).
Понятно, что введение в процесс сжигания древесных отходов, даёт вклад в уменьшение потребления экспортного энергоносителя. Заметное количество древесных отходов есть во многих районах.
Существуют различные технологии изготовления топливных древесных брикетов. Применение их в качестве топлива существенно улучшает процесс сгорания. Калорийность древесных брикетов близка к калорийности сухой древесины. Спрос на такое топливо в Западной Европе постоянно высокий. Европейские посредники готовы закупать практически неограниченное количество древесных брикетов.
В Европе выпускаются установки, которые производят древесные брикеты из сырых опилок и где сушка до необходимых для производства топливных брикетов 12% влажности производится с применением газа и дизтоплива.
На техническое основе данного бизнес-плана была выполнена разработка проекта и организовано производство узлов линии шнекового прессования на предприятиях Белоруссии. Принцип работы основного узла – шнекового пресса, аналогичен тому, который фирма «Pini+Key» (Австрия) использует уже десятки лет.
Цена данной установки существенно дешевле западных аналогов при сравнимых эксплуатационных характеристиках.
Стоимость базового комплекта оборудования для производства топливных брикетов, включая шефмонтажные работы, составляет €110 000, общая стоимость проекта, включая пуско-наладочные работы, организационные и начальные эксплуатационные затраты до выпуска продукции, составляет €. Суммы даны без учета НДС.
Вариант 2 предполагает переработку только опилок влажностью не выше 55%. |
||||||
2 | Пресс шнековый | 1 шт. | 113 | 400-600 | 250 | 111 000 |
Шнек подачи | 1 шт. | |||||
Бункер накопитель | 1 шт. | |||||
Барабан сушильный СК-1М | 1 шт. | |||||
Вентилятор | 2 шт. | |||||
Теплоагрегат | 1 шт. | |||||
Циклон | 1 шт. | |||||
Транспортер винтовой | 2 шт. | |||||
Пульт управления | 2 шт. | |||||
НУР 250В (измельчитель) | 1 шт. |
Экономические расчёты даны по состоянию на 01.03.2008 года.
По желанию заказчиков линия может дополнительно комплектоваться: оборудованием переработки отходов древесины в стружку (варианты комплектации 3 и 4).
1. Основная идея проекта
1.1. Цели проекта
Цель проекта заключается в том, чтобы из практически бесплатного сырья, произвести экспортную продукцию. При этом появляется возможность с одной стороны ввести в энергетический баланс отходы, а с другой – улучшить экологическую обстановку.
1.2. Существующие приоритеты и их влияние на проект
Переработка отходов древесины, так или иначе, решается практически во всех странах мира. Восточная Европа, в том числе Российская федерация в целом, в настоящее время существенно отстает по наращиванию объёмов переработки древесины.
Фирмами «TOS Svitavy», «Briklis» (Чехия) созданы установки для переработки влажных опилок в древесные брикеты производительностью по выходу до 600 кг/час. Однако, европейские цены выше в несколько раз выше, чем на оборудование со схожими возможностями производства Беларуси. Так, например, дилер фирмы «Briklis» может предложить оборудование в комплектации с сушильной установкой комплектации от 290 тысяч USD. Пресс в аналогичной предлагаемой по данному варианту комплектации производства австрийской фирмы Pini+Kay стоит 78000 € .
2. Анализ рынка и стратегия маркетинга
Для иллюстрации свойств древесных брикетов приводится теплотворная способность распространённых видов топлива (МДж/кг).
- Дрова …………………..10;
- Дизельное топливо…….42.7;
- Уголь каменный …….…22;
- Торф………………… …10;
- Брикеты древесные ….19.
При этом древесные брикеты при сжигании выделяют значительно меньше золы и СО2 в связи с чем пользуются стабильным спросом на Европейском рынке.Технологически режим работы установки непрерывен. Отправка по мере накопления объёма на фуру грузоподъёмностью ~ 20 тонн.
3. Особенности производства
3.1. Технологическая схема производства
3.3. Организационно-технический план производства
- Работа по созданию линии содержит следующие, обычные в таких случаях, этапы:
- организационная работа по размещению;
- изготовление нестандартного оборудования;
- закупка комплектующих;
- согласование размещения с контролирующими организациями;
- поставка вспомогательного оборудования;
- общестроительные работы;
- монтаж технологического оборудования, разработка эксплуатационной документации;
- запуск линии.
3.4. Сырьё и материалы
Сырьём для изготовления топливных брикетов являются отходы деревообработки, солома, льнокостра, шелуха подсолнечника и др. отходы.
3.5. Отработка технологических операций
- В линии следующие основные технологические операции:
- оптимизация потока стружки в шнек подачи;
- шнековое прессование.
При пуско-наладочных работах каждый агрегат проходит автономную наладку.
4. Финансовая оценка проекта
4.1. Затраты по основным статьям на создание производства (без учета НДС).
4.1.1. Изготовление основных блоков линии:
Пресс шнековый | 1 шт. |
Шнек подачи | 1 шт. |
Бункер накопитель | 1 шт. |
Барабан сушильный СК-1М | 1 шт. |
Вентилятор | 3 шт. |
Теплоагрегат | 1 шт. |
Циклон | 1 шт. |
Транспортер винтовой | 2 шт. |
Пульт управления | 1 шт. |
НУР 250В (измельчитель) | 1 шт. |
Стоимость оборудования для производства топливных брикетов по п. 4.1.1.1 € 110 000
4.1.2. Изготовление нестандартного оборудования, включая проектирование.
(не входит в поставку базового комплекта линии).
- системы технологических воздуховодов ………………………€4500;
- системы упаковки и оперативного складирования……………€1600;
- системы пожарной сигнализации ………………………………. €2200.
Затраты по п. 4.1.2. € 8300.
4.1.3. Закупка вспомогательного оборудования:
- оборудование системы общей вентиляции…………………..….€ 700;
- оборудование системы освещения и охраны…………….………€ 500;
- оборудование внешнего силового электропитания и кабели ….€ 1900.
Затраты по п. 4.1.3. € 3100
4.1.4. Общестроительные работы на сумму €3800, куда входят:
- ремонт и отделка основного помещения……………………….….€ 1800;
- создание бытовых условий для персонала…………………….….€ 500;
- разводка электропитания……………………………………………€ 400;
- монтаж пожарной и охранной сигнализаций……………………….€ 500;
- монтаж системы вентиляции…………………………………………€ 600.
4.1.5. Дополнительно
- транспортировка оборудования из Беларуси к месту монтажа ………………… € 2400;
- пуско-наладочные работы ……………………………………………………………………………..€ 11100;
- станок для стяжки брикетов пластиковой лентой по 12 штук ……………………….. € 1000.
Затраты по п. 4.1.2 — 4.1.4 зависят от конкретных условий размещения и взяты максимальными, используя метод экспертных оценок.
Затраты по пунктам 4.1.1 — 4.1.5 составят € 163 754.
4.2 Ежемесячные затраты для оценки себестоимости продукции.
4.2.1. Заработная плата:
Для организации полного цикла выпуска древесных брикетов необходима работа бригады из 4-х человек.Таким образом при условии непрерывной работы оборудования для производства топливных брикетов в течение 20 часов в сутки необходима организация работы 3-х бригад. При условии выплаты зарплаты в 250 евро и оценивая в среднем обобщённую налоговую нагрузку в 50 %, получим затрат на сумму €4500 в месяц.
4.2.2. Плата за электроэнергию
при рабочей мощности 80 кВт, при работе 600 часов в месяц и при стоимости за один кВт/час €0.098 составит за месяц ~ € 4704.
4.2.3. Дополнительные затраты.
Затраты на тару и упаковочные материалы:
- при условии непрерывной работы линии 20 часов в сутки, исходя из производительности 400 кг/час готовых брикетов будет произведено 240 тонн готовой продукции, для упаковки которой потребуется, соответственно, 240 европаллет приблизительно на сумму €2000.
- необходимым расходным материалом в прессе является насадка шнека, которая изнашивается при производстве 80-90 тонн продукции и нуждается в замене. В базовую комплектацию входит 4 таких насадки.
Стоимость дополнительной новой насадки составляет €300 . Однако отработанную насадку можно отреставрировать с методом наплавления неограниченное число раз после производства 80-90 тонн древесных брикетов, что стоит ориентировочно €100. Таким образом добавляются ежемесячные затраты €200.
Здесь хотим отметить, что собственно шнек является слабым местом в шнековых прессах и, в частности, в установках брикетирования российского и украинского производства, износ шнека происходит при выработке 20 тонн продукции и даже у австрийского производителя шнек меняется через 40 тонн.
Также из расходных материалов понадобится пластиковая лента для стяжки брикетов по 12 штук перед укладкой на паллеты и стрейч-пленка для обмотки паллет.Таким образом расходы по пп. 4.2.1 – 4.2.3 составят €8956.
4.3. Суммарные расходы
4.3.1. Суммарные расходы на сооружение линии составят € 163 754.
4.3.2. Расходы за месяц её эксплуатации составят €8956.
4.3.3. Сумма расходов для оценки срока окупаемости составит €174 652.
4.4 План финансирования.
Оборудование для производства топливных брикетов поставляется на следующих условиях:
- предоплата 70% стоимости оборудования … €110000*70% = €77000
- срок изготовления – 2 месяца с даты поступления предоплаты. Далее оплачивается 30% стоимости оборудования и стоимость пусконаладочных работ перед отгрузкой и сборкой …………………………………………………………………… €33 000
- оставшиеся 10% стоимости оборудования после подписания акта ввода в эксплуатаци ………………………………………………………….. €13 400;
- к этому моменту должны быть закуплены материалы и выполнены работы по п.п. 4.1.2 – 4.1.5. на общую сумму …………………… €32 000*;
* последняя цифра взята по максимуму и уточняется в конкретном случае.
4.5. План возврата средств
4.5.1. Эксплуатационные затраты в месяц.
Эксплуатационные затраты в месяц оценены в пункте 4.2 и составят €10 907
4.5.2. Планируемая выручка в месяц.
- производительность в час — 0.5 тонны;
- часов непрерывной работы в сутки — 20;
- цена реализации за тонну брикетов — € 100;
Итого планируемая выручка в месяц около €30 000.
4.5.3. Планируемая прибыль в месяц.
€30 000 — €10907 = €19 093
4.5.4. Срок полного возврата
Срок полного возврата средств на создание производства топливных брикетов по проекту составит €174 652 / €19093 = прибл. 9 месяцев.
Гарантия 3 года !!!
Беларусь, г. Минск, ул.Ф.Скорины 54А, к.204 | |
Тел./Факс: 8-10 (375-17) 260-94-13 | |
Коммерческий отдел: 8-10 (375-29) 153-39-35, 379-25-58 | |
E-mail: [email protected] | |
www.biostar.by |
Фотография с сайта 66.ru
СЗАО «БиоСтарИнжиниринг»
www.equipnet.ru
Исследователи нашли способ превратить опилки в бензин
Исследователи объявили об успешном тестировании нового химического процесса преобразования целлюлозы из древесных опилок в углеводородные цепи
Исследователи из Центра химии поверхностей и катализа от Католического университета Лёвена, Бельгия, недавно объявили об успешном тестировании нового химического процесса преобразования целлюлозы из древесных опилок в углеводородные цепи. Эти углеводороды, как утверждают ученые, можно использовать в качестве добавки в бензин или компонента в пластмассах.
Целлюлоза является основным веществом в растительной материи и присутствует во всех несъедобных частях древесины, включая солому, траву, хлопок, и изделий из древесины. На молекулярном уровне целлюлоза содержит длинные углеродные цепи. Однако, сохранить длину этих цепей до сих пор не представлялось возможным, из-за уменьшения кислорода в процессе переработки целлюлозы (атомы кислорода являются связующими между молекулами углеводорода). Ученые смогли разработать новый метод био-переработки целлюлозы для получения углеводородных цепей.
В настоящее время исследователи подали заявку на патент на разработанный ими метод. В лаборатории они построили химический реактор, в который загружают опилки и добавляют катализатор. При нужных показателях температуры и давления процесс получения насыщенных углеводородов (алканов) занимает примерно полдня. По сути, метод позволяет производить нефтехимический продукт из биомассы.
Конечно, полученный продукт является «промежуточным», другими словами, для его преобразования в чистый бензин, необходимы дополнительные этапы обработки. Но даже такой «зеленый» углеводород может иметь и другие области применения, например, в производстве этилена, пропилена и бензола, которые входят в состав пластмасс, резины, изоляционной пены, нейлоновых покрытий и т.д.
Как считают исследователи, с экономической точки зрения целлюлоза имеет большой потенциал. Этот материал доступен везде. Кроме того, производимые из целлюлозы углеродные цепи состоят из 5 – 6-ти атомов углерода – это так называемая «легкая нафта», обладающая свойствами растворителя и по химическим характеристикам очень близкая к бензину.
Как полагают ученые, новый метод окажется особенно полезным для использования в Европе, где мало запасов сырой нефти, а из-за высокой заселенности отсутствует возможность легкой добычи сланцевого газа.
econet.ru
Утилизация отходов древесины, оборудование для переработки древесных отходов, опилок, стружки
Утилизировать древесные отходы путём сжигания и захоронения — распространённая, но, далеко не самая эффективная практика. Да, древесина разлагается быстрее, например, чем пластик, хорошо горит, однако, у этого мусора есть большой потенциал для последующего использования.
Переработанная древесина имеет различное применение. В зависимости от видов ее переработки, из древесины получается:
- скипидар, уголь и уксусная кислота, если она была переработана химическим способом – путем гидролиза;
- при механической обработке дерева, образуется щепа, из которой получается строительный материал – ДСП. Древесные гранулы и брикеты для отопления, тоже являются результатом такой переработки.
Механический процесс более простой и требует меньших затрат.
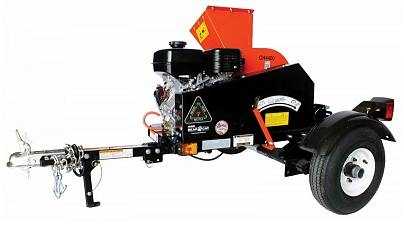
Измельчитель-шредер с погр. BEAR CAT SC5720B +ПСМ. Мобилен, высокая производительность.
К основному оборудованию по переработке древесных отходов, относятся разного вида измельчители:
- Шредеры способны измельчать отходы в независимости от их исходных размеров. Горизонтальные, предназначены для переработки мелких отходов, а вертикальные — для более крупных. Острота режущих ножей шредера, значительно влияет на качество и скорость процесса измельчения.
- Тихоходные измельчители являются менее скоростным, но не менее надежными при этом, и часто употребляемыми на производстве.
- Брикетировочный пресс, производит брикеты для топлива. В дальнейшем, продукт их сгорания, является отличным элементом для удобрения. Отличительной характеристикой такого пресса, является возможность работы с разного вида сырьем, будь то древесина или бумага.
- Силосы, необходимы в больших цехах, так как обеспечивают хранение и транспортировку материала.
Полезно: способы утилизации мусора.
К дополнительному оборудованию относятся деревообрабатывающие станки:
- Строгальный станок, который снимает с обеих сторон древесины поверхность, таким образом, подготавливая ее к следующему процессу обработки.
- Фрезерные станки, используются для дополнительной работы по дереву. После обработки дерева на таком станке, образуется стружка, которая является еще одним материалом для обработки.
- Лущильные станки не производят стружки в процессе своей работы, но благодаря им, производится шпон.
- Окорочные станки применяются для снятия коры с древесины, в два этапа: легкий и более глубокий процесс очистки дерева.
На заводах, которые занимаются переработкой дерева, производится: древесный уголь, брикеты, а так же производится переработка древесных отходов в газ.
Утилизация и переработка опилок, щепы
Многие предприятия просто сжигают опилки, хотя есть другой более рациональный способ. Из опилок и щепы можно изготавливать топливные брикеты. По энерговыделению они сопоставимы с дровами.
Есть несколько способов переработки опилок.
Для переработки опила в топливные брикеты применяются линии шнекового прессования. Они работают на природном газе и дизельном топливе и электричестве.
Популярностью пользуется метод при использовании пресса. Этот метод обладает хорошей производительностью и малыми габаритными размерами оборудования.
Прессование проходит без добавления клея. Преимущество этого в том, что последующее сжигание брикета проходит без выброса в атмосферу ядовитых химических веществ.
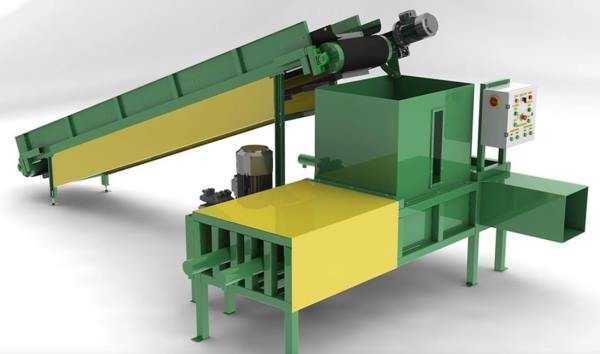
Автоматический пресс для опилок и стружек. Стационарный, высокопроизводительный и автоматизированный. Намного эффективнее и производительнее кустарных ручных прессов.
В частных и коммунальных хозяйствах используют специальное оборудование для дробления веток деревьев, которое прицепляется к трактору или машине через специальный вал. Производительность такого устройства достигает примерно 6 куб метров в час. Прямо на месте осуществляется и прессование опилок. Таким способом получается экологически чистый и готовый к последующему применению продукт.
Есть еще способ использования опила в качестве удобрения для почвы. Так же опил и стружку используют и в качестве сырья для изготовления строительных материалов, и в химическом производстве для изготовления технических жидкостей, спиртов, растворителей и других материалов.
Зачастую в опилки и щепу перерабатываются прочие древесных отходы (например, мебель) для последующей переработки.
Весьма популярным способом переработки древесины является производство угля в специальных углевыжегательных печах.
Линия переработки древесины
Экологичный подход к потребляемым природным ресурсам предусматривает возможность их повторной переработки. Немалую часть в сегменте рециклинга занимает переработка древесины. Этот процесс может осуществляться несколькими способами: химическим, механическим, механико-химическим. Выбор технологического метода будет зависеть от планируемого конечного продукта такой переработки.
- Механическое изменение первоначального вида древесины происходит способом ее измельчения, распиливания, фрезерования, точения, раскалывания, лущения, сверления или строгания. Результатом переработки являются пиломатериалы или волокнистые полуфабрикаты. Если древесные волокна прессовать под большим давлением, то результатом станет производство пеллет -топливных гранул, обладающих предельной энергоконцентрацией.
- Сочетание механического изменения с химическим дает однородный продукт из древесины – стружку, дробленку и шпон, из которых впоследствии изготавливается модифицированная древесина. Промежуточный древесный продукт (полученный механическим путем) посредством синтетического связующего ингредиента под действие давления и определенной температуры подвергается полимеризации. Таким образом производится фанера, ДСП, ДВП, OSB.
- Сугубо химический способ переработки щелочью или кислотой применяется для получения из древесины камеди, растворителей, дубителей, канифоли, составляющих наполнителей для лаков, битумов а также в качестве сырья в производстве бумаги.
Выбор специализированного оборудования, задействованного в многовариантных линиях переработки древесины, огромен. Поэтому комплектацию мощностей следует осуществлять в соответствии с планируемым конечным результатом.
Особо хочется привлечь внимание к производству древесной щепы, или «строительного камня» будущего (как ее иначе называют). Являясь основой комплексного безотходного использования лесных ресурсов, она открывает новые возможности в повторной переработке и утилизации любого вида древесины.
Линия переработки древесины в щепу – наиболее востребованна в этом сегменте производства.
Ввиду своей мобильности и компактности такая установка может использоваться на всех стадиях заготовки и обработки древесины (начиная с измельчения непосредственно на лесных вырубках и заканчивая переработкой отходов больших деревообрабатывающих комплексов).
Переработка тонкомера, брёвен, горбыля.
kudavlozitdengi.adne.info