Оборудование для производства фанеры: линия и технология изготовления
Производство фанеры является очень сложным, но прибыльным бизнесом. Для открытия предприятия по производству фанеры необходимо, прежде всего, приобрести оборудование, которое используется для этого процесса. Стоит помнить, что качественное оборудование способно значительно упростить процесс производства фанеры.
Оборудование для изготовления фанеры
Для производства фанеры чаще всего используются лущильный, калибровочный и раскроечный станки. С помощью лущильного станка осуществляется получение тонкой поперечной стружки. На этих станках обрабатываются короткие бревна, которые по-другому называются чураки. На суппорте станка устанавливается нож, который при вращении бревна срезает с него слой древесины. Этот слой древесины имеет слой толстой и беспрерывной ленты, которую называют шпоном.
Для улучшения качества шпона и увеличения его прочности во время лущения шпона производится обжим древесины. Для этого используется прижимная линейка.
Калибровочный станок используется для пропуска бревен с сечениями. Благодаря этому станку обеспечивается удаление участков бревен, которые выступают за просветы в нем. Закомелистая часть наиболее толстых бревен обтачивается благодаря наличию калибрующих ножей. Благодаря возможности регулировать положение ножей на роторе можно обрабатывать на этом станке бревна различного сечения. Раскроечные станки предназначаются для раскройки фанеры. Они характеризуются большими габаритами, что позволяет разрезать фанеру на листы разнообразных разрезов.
Для того, чтобы просканировать недостатки отобранного материала используются специальные станки. Ими являются измерители количества влаги, а также конвейеры.
Иногда на производстве фанеры используются линии, благодаря которым осуществляется сортировка шпона.
Технология производства фанеры
Производство фанеры состоит из нескольких этапов. К основным из них относится:
- Подбор материала;
- Снятие коры;
- Снятие слоя шпона на лущильном станке;
- Просушка шпона.
К подбору материала для фанеры необходимо подходить очень тщательно. Зачастую для производства фанеры используют шпон из березы, ольхи, бука, сосны и т.д. Для создания удобств в работе материал проваривается в специальном бассейне. Этот процесс значительно повышает качество сырья.
На лущильном станке снимаются первый слой шпона, после чего его разделяют на отдельные листы. Качество шпона зависит от вида древесины. При наличии в шпоне большого количества влаги его отправляют на просушку. Далее производится склеивание листов шпона.
Вы можете прямой сейчас узнать какое оборудование для производства сетки рабицы нужно и открыть прибыльный бизнес в этом направлении.
Производство профнастила — замечательный бизнес. Всё об этом Вы можете узнать тут.
Для склеивания шпона используются специальные материалы. Клеящие составы изготавливаются в механизированных смесителях, после чего они подаются желобки нескольких клеевых вальцов. Прокатывается клеящий состав с обеих сторон пиломатериала. Далее промазанные клеем листы шпона склеиваются с помощью пневматических, гидравлических или винтовых прессах.
При склеивании фанеры в комнатной температуре их необходимо продержать в помещении около 6 часов. Наиболее эффективным является прессование фанеры при повышенной температуре. В таких условиях на склеивание шпона уходит всего несколько минут.
В том случае, если производится гнутая фанера
Линия по производству фанеры
Выпуск фанеры требует наличия специальных линий. Это специализированное оборудование, которое значительно упрощает процесс производства. Работа линии заключается в следующем. Древесина в виде бревна или чурака очищается от разнообразных загрязнений, а также с нее снимается кора. Для этого в течение нескольких часов применяется влаготермическая обработка.
После того, как древесина прошла процесс размягчения, ее закрепляют в специальном станке, который вращается вокруг своей оси. К чураку подводится лущильный нож и с его помощью снимается с него тонкий слой древесины. Благодаря этой процедуре вырабатывается стружка. Эта стружка и становится основой будущей фанеры.
Шпон раскраивается на листы. Эти листы проходят процесс сортировки согласно их качеству. При этом учитывается наличие трещин, сучков и разнообразных незначительных дефектов. Далее листы проходят процесс сушки, после чего их собирают в пакеты. Улаживаются листы в пакеты по принципу перпендикулярности.
Базовый лист фанеры должен быть расположен симметрично. После того, как пакет сформирован, его смазывают специальным клеящим составом. Благодаря клею из отдельных листов шпона образуется единый и цельный лист фанеры. После этого фанера проходит процесс высыхания и охлаждения. На этом процесс производства на линии заканчивается.
Во время производства шлифованной фанеры используются специальные шлифовальные станки, на которых она проходит соответствующую обработку.
В случае изготовления ламинированной фанеры используется специальная пленка, которая наклеивается сверху на фанеру.
Благодаря этой пленке фанера имеет отличные технические характеристики, а также повышенный уровень износоустойчивости. Ламинирование фанеры может быть выполнено как с одной, так и с двух сторон. Водостойкую фанеру во время производства обрабатывают специальными смолами.
Популярные модели оборудования
Лущильный станок СЛ-720
На производствах фанеры используются разнообразные станки. От качества оборудования зависит скорость процесса изготовления фанеры, а также его качество. Именно поэтому к подбору оборудования необходимо подходить очень ответственно. Существует множество фирм, которые занимаются производством оборудования для изготовления фанеры. Наиболее популярными среди станков для производства фанеры считаются:
- Лущильный станок для производства шпона СЛ-720 (1600). С помощью этого станка древесина обрабатывается без дополнительных усилий. Определение оптимального положения оси обеспечивается благодаря наличию специального приспособления. Наличие дебаркера обеспечивает высокое качество начальной обработки чурака. С помощью хорошей фрезы заготовке придается правильная форма. Наличие гибкого гофрированного шланга позволяет беззаботно удалять отходы во время работы.
Хотите открыть свое дело по производству плитки, но не знаете с чего начать? Сперва узнайте, как осуществляется изготовление керамической плитки.
Всё об изготовлении бетона здесь.
Как наладить производство брусчатки? Информация на странице http://buisiness-oborudovanie.com/dlya-dorozhnyx-pokrytij-kamnya/oborudovanie-dlya-proizvodstva-bruschatki/.
- Станок для производства лущенного шпона CЛ-800 (1600) характеризуется наличием специального устройства, с помощью которого устанавливается бревно для его обработки. С помощью этого станка можно обрабатывать заготовки, диаметр которых составляет от 110 до 740 миллиметров. Этот станок способен производить четыре метра шпона в час.
Делительный станок СД-800
Станок делительный для рубки шпона СД-800 (1600). С помощью этого агрегата осуществляется деление ленты шпона на отдельные дощечки или листы необходимой ширины. Задается ширина листа с помощью специального электронного устройства. Использовать этот агрегат необходимо на одной линии со станком по производству шпона. Ширина обрабатываемого шпона может составлять до 1600 миллиметров.
- Калибровочный станок по дереву производится на основе станков эстакадного типа. Наличие высокооборотного привода позволяет управлять скоростью работы станка. Удобства при работе на станке придаются благодаря возможности автоматического управления столом. Благодаря этому агрегату осуществляется калибровка поверхности плиты.
Раскроечный станок по дереву FDB Maschinen FR 6020 предназначается для обработки фанеры. Это изделие характеризуется компактностью, высоким уровнем сборки и наличием специальных устройств, благодаря которым значительно упрощается процесс обработки дерева.
Все станки производятся из материалов высокого качества, что обеспечивает им прочность, надежность и длительный срок эксплуатации. После производства все станки проходят ряд испытаний, что обеспечивает им высокий уровень износоустойчивости, а также значительно упрощает процесс производства фанеры.
Видео про изготовление фанеры
buisiness-oborudovanie.com
Китай Линия по Производству Фанеры, Китай Линия по Производству Фанеры список товаров на ru.Made-in-China.com
MOQ: 1Комплект
- Тип: Горизонтальный Токарный Станок
- Автоматическая ранг: Автоматический
- Точность: Высокоточный
- Настройка режима: Наполный Тип
- Управление Режим: ЧПУ
- Источник питания: Электрический
-
Поставщики с проверенными бизнес-лицензиями
Поставщики, проверенные инспекционными службами
Linyi Qunshan Machinery Co., Ltd. - провинция: Shandong, China
ru.made-in-china.com
Не нашли нужного оборудования? Напишите нам через форму обратной связи или напрямую обратитесь к менеджеру по адресу [email protected]!
____________________________ * Информацию о процедуре приобретения оборудования Вы найдёте, перейдя сюда — Порядок работы * Ознакомиться с образцами документов для приобретения и прочей полезной информацией вы можете здесь — Информация для клиента * Просмотреть отзывы наших партнёров и оставить свой, Вы можете, перейдя в раздел — Отзывы * Наши дилерские сертификаты, а также фотоотчёт нашей деятельности, представлены здесь — Фотогалерея |
Новости 13.12.2018 06.12.2018 27.11.2018 06.04.2015 13.11.2014 Подписка на рассылку |
xn--80aaxagcbv8akg.xn--p1ai
Производство фанеры как частный бизнес
Довольно прибыльной отраслью некрупного бизнеса является производство фанеры из шпона. Но чтоб хорошо заработать в этой сфере, нужно правильным образом выбирать стратегию с тактикой для ведения дел. В этом помогут знания тематики и четкий, выверенный бизнес-план. Следует реально оценивать ожидаемые доходы, а также затратную часть и закупку необходимых станков, оптимальные проценты для получения кредитов, если таковые понадобятся.
Производство стройматериалов из древесины во все времена приносит стабильный доход. Сегодня без использования фанерных листов не обходится строительство частных домиков, дач, коттеджей и внутренняя отделка интерьеров, изготовление различной мебели, и поэтому производство фанеры – по-прежнему перспективный бизнес.
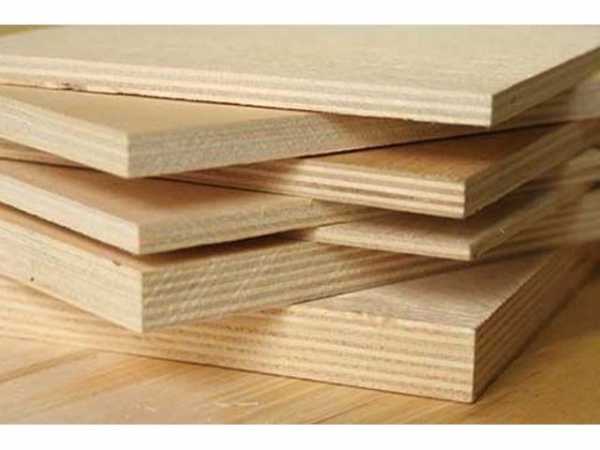
Фанера из шпона
Немного о сортаменте и разновидностях материала
Касаемо обработки, фанерный лист разделяют на:
- нешлифованный (или НШ),
- шлифованный с одной из сторон (или Ш1),
- двухсторонний (Ш2).
А согласно количеству брака поверхности материала, выделяют несколько сортов: начиная с элиты (сорт Е), где отсутствуют видимые дефекты древесины, заканчивая 4-м, который допускает практически любые «недостатки внешности». Сортамент изделия определяется условиями ГОСТа за №3916.1-96 для древесины.
Сортамент фанер
По виду используемого клея определяется марка:
- ФСФ – изготовленная с применением смоляного клея (фенолформальдегид). Она обладает водостойкостью, используется для внутренних работ, и в местах повышенной влажности;
- ФК – используется карбамидный клей. Такая фанера из шпона с низкими показателями водостойкости, быстро набухает, может потерять свою форму;
- ФБ – пропитывается бакелитовым лаком (перед сборкой и склеиванием). Такие листы из древесины используют для работ в неблагоприятных условиях, фанера выдерживает воздействия щелока, микроорганизмов, морской воды.
Ламинированная фанера. При ее изготовлении используют спецсоставы для покрытий. Такая фанера оптимально противостоит воздействиям жидкостей, отличается мощным запасом износостойкости. Её применяют для прицепов, контейнеров, вагонов, яхт; в изготовлении мебели с оборудованием, при отделке строений.
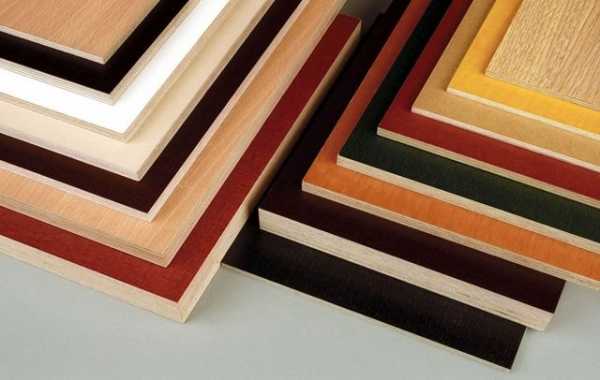
Фанера ламинат
А еще: по своему назначению материал подразделяется на строительный, авиационный, автомобильный, корабельный, тому подобный. Для чистовой отделки в помещениях нынче в фаворе декоративная фанера, сделанная из древесины ценных пород.
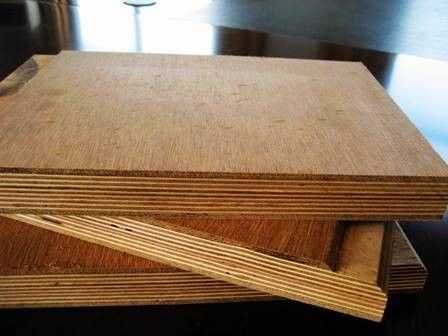
Многослойный и многофункциональный стройматериал
Чтоб заняться производством фанеры конкурентоспособно, вам понадобится высокотехнологичное современное оборудование и подбор квалифицированного персонала.
Техника и перспективы изготовления фанеры
Березовые, хвойные породы – то из чего производится данный материал. Бревна привозят на завод и укрывают от непогоды и солнца — чтоб лучи ультрафиолета не высушили торцы. Возьмем, к примеру, березу — из нее выходит самая прочная фанера.
На производство эта порода дерева привозится в виде сырья: распилованных бревен. Из них формируется подобие вязанки, «перехваченной» массивной цепью из металла.
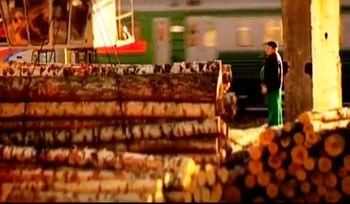
Березовые бревна – сырье для производства фанеры
Эти «вязанки» аккуратным образом перемещаются в бассейн с горячей водой. Тут древесина пропаривается некоторое время.
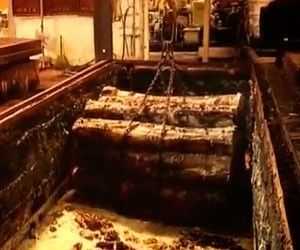
Пропарка сырья
А на поверхность выходит бурая пенка. Это природное вещество — деготь, что выделяется березой.

Образование дегтя
А еще через некоторое время потемневшие бревна выгрузят из бассейна и оставят на открытом воздухе, чтоб уравнять внутреннюю температуру — тепло должно дойти до самой сердцевины древесины. Если ее распарить хорошенько, она становится пластичной.
После заготовки отправляются на лущение. Бревна на станке оборачиваются вокруг оси, специальный нож убирает кору, снимая широкую стружку. Движение происходит по так называемой спирали Архимеда.

Снятие стружки
Для справки: в третьем столетии до новой эры Архимед изобрел формулу для идеальной спирали — та должна равномерно вертеться вокруг точки, приближаясь с каждым витком к ней на равное расстояние.
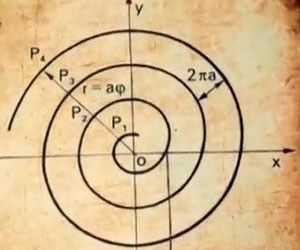
Та самая спираль
Такая спираль позволяет резать с заготовок идеально ровные слои. Эта самая стружка, что снята с бревен, именуется листами шпона.
Длина листов шпона, с одного чурака (так называют бревна-заготовки), порой достигает пятнадцати метров. Лист шпона остается теплым, пропитанным влагой (в течение некоторого времени). Ведь, если бревна предварительно не парить, шпон в процессе лущения станет ломаться, будет рваной. Самый тонкий лист из березы – милиметр в толщину.
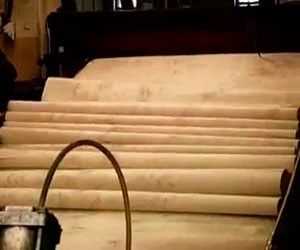
Срезание листа шпона
Кстати, в Штатах, где берез практически нет, фанерный лист режут из хвойных пород. А в Поднебесной – используют тополь.
Стружку затем кроят на специальной гильотине, отправляя в сушилку. Поток горячего воздуха быстро убирает из листов излишнюю влагу, чтоб будущий материал не расслаивался и не шел пузырями.
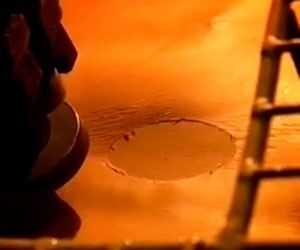
Починочный станок режет дефекты и одновременно ставит заплатки на эти места
Теперь наступает черед сборки. Для листа в один сантиметр толщиной склеивается несколько слоев шпона. Раньше для процедуры использовали казеин — молочный белок. Казеиновый фанерный лист был прочен, однако был не влагостоек и быстро промокал.
Сейчас шпон, в основном, склеивается при помощи смолы формальдегидной — конечный результат получается влагостойким. У фанерного листа нечетное количество слоев (к примеру, пятислойная). Клеем пропитывают только четные листы, что в процессе сборке должны чередоваться с нечетными – сухими. Основное: слои располагаются перпендикулярным образом. Это придает фанере прочность. Так, у первого листа волокна будут располагаться вдоль, а у второго — поперек. Увеличивается, таким образом, противоударная вязкость, то есть способность к поглощению механической энергии.
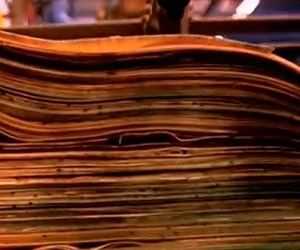
Слои шпона
Пакетированные слои на пару минут отправляются в пресс, сначала холодный. Там сухие, проклеенные «запчасти» схватываются. Это — первый этап, затем следует горячее прессование. Листы будущей фанеры грузятся в подъемником уже в горячий пресс. Под давлением шпон здесь крепко склеивается. Затем в течение суток листы будут остывать, и завершатся процессы полимеризации клеевой основы.
Теперь обрезаются неровные края у шпона, а изделию придается привычный вид.
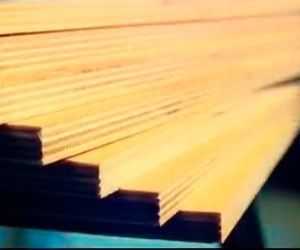
Финальный вариант
Оборудование для бизнеса
Количество и качество станков может варьироваться, зависимо от количества предполагаемого продукта. Но будут необходимыми, по минимуму, следующие станки:
- калибровочный, снимает верхние слои дерева;
- лущильный, снимает основную часть шпона;
- раскроечный, разрезает полотно на необходимого размера листы.
Во сколько может обойтись закупка такого оборудования? К примеру, по оценкам экспертов, сегодня полуавтоматическая линия в цеху может «вылиться в копеечку»: придется выложить от 50 до 65 тыс. долларов. Ну, или прокредитоваться, тогда организация бизнеса на производстве фанерных листов обойдется еще дороже.
Кстати, кроме изготовления обычной, можно производить, к примеру, ламинированную. Изготовление и применение подобного продукта очень востребовано. И заключается в добавочном этапе – покрытии полученного материала пленкой.
Есть ли у вас план?
Приведем наглядный пример. Бизнес-план по открытию цеха производства ФК, нешлифованной фанеры ФК (минимум первоначальных вложений). Для произведения кубометра данного материала требуется примерно 1,5 — 1,8 кубометров бревна березы. Допустим, средняя стоимость его — 2000 р. Допустим, цех обладает мощностью производства 50 кубометров готового листа в месяц. Считаем затраты на цех, они составят:
Таблица калькуляции расходов
Каких результатов ждать?
При загрузке в 50 кубов в месяц, при рыночной цене ФК около 17 тыс. р. За куб, валовый доход будет составлять около 850 тыс. р., при рентабельности около 30%, а чистая среднемесячная прибыль — около 220 тыс. Следовательно, окупаемость денежных вложений в дело – около года.
Но все это при налаженном производстве и рынках сбыта – а везде имеются свои подводные камни.
Подводим итоги
Производство фанерного листа различного сортамента – довольно серьезное и увлекательное дело. Однако, следует помнить, что выстроить с нуля, добиться устойчивой прибыли для крупного производства не каждому будет по силам. Потому и начинать рекомендуют с организации мини цеха, а по времени уже, наработав опыт и навык в технологическом процессе и в управлении персоналом, наладив сбыт продукции, наращивать объем производства фанеры.
Смотрите видео по теме:
viascio.ru
Линия производства фанеры (5000-50000 м³ в год)
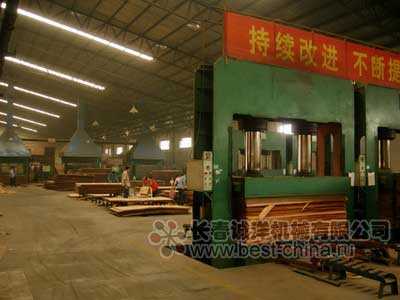
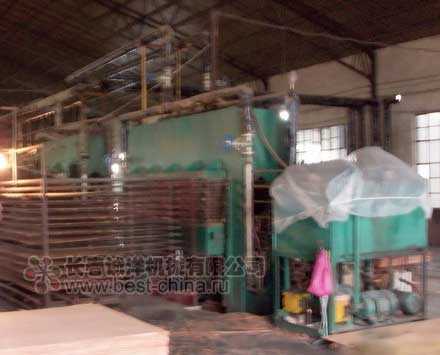
Схема производственного процесса изготовления фанеры
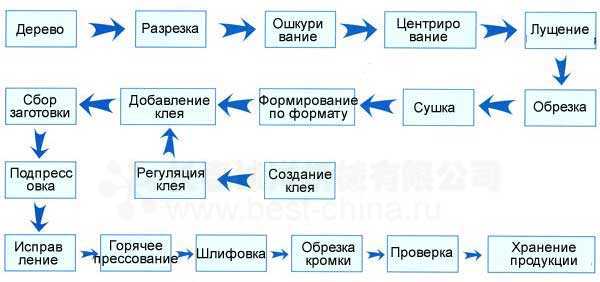
Технические параметры линии
№ | Параметр | Ед. | Производительность | |||
5 000 м³/год | 10 000 м³/год | 15 000 м³/год | 20 000 м³/год | |||
1 | Потребность в дереве | м³ | 6 000 | 12 000 | 18 000 | 24 000 |
2 | Формат фанеры | мм. | 1220×2440 | |||
3 | UF клей 100% | т/год | 250 | 500 | 750 | 1000 |
4 | Давление газа | МПа | 0.8 | 0.8 | 0.8 | 0.8 |
5 | Общая мощность | кВт | 154 | 163 | 262 | 315 |
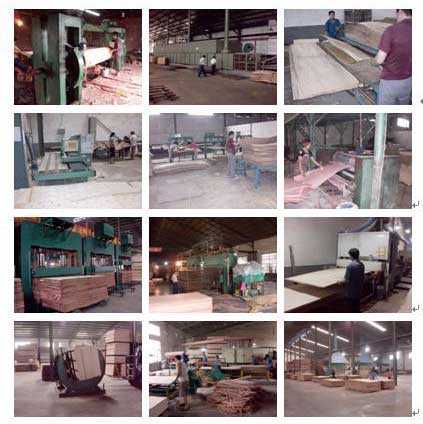
Комплектация линии (4 производительности)
№ | Оборудование | Производительность | |||
5 000 м³/год | 10 000 м³/год | 15 000 м³/год | 20 000 м³/год | ||
1 | 8′ лущильный станок со шпинделем | 1 | 1 | 2 | 2 |
2 | 4′ лущильный станок со шпинделем | 1 | 1 | 2 | 2 |
3 | 8′ лущильный станок без шпинделя | 1 | 2 | 2 | 4 |
4 | 4′ лущильный станок без шпинделя | 1 | 2 | 2 | 4 |
5 | 8′ шлифовальный станок | 1 | 1 | 1 | 1 |
6 | 4′ заточный станок | 1 | 1 | 1 | 1 |
7 | Сеточная сушилка | 1 | 1 | 2 | 2 |
8 | 8′ электрический обрезатель | 1 | 1 | 2 | 2 |
8 | 4′ электрический обрезатель | 1 | 1 | 2 | 2 |
10 | 8′ клееподготовитеьная машина | 1 | 1 | 2 | 2 |
11 | Подпрессовщик | 1 | 1 | 2 | 2 |
12 | Горячий пресс | 8/1 | 15/1 | 12/2 | 15/2 |
13 | 8′ листозагибочный станок | 1 | 2 | 2 | 4 |
14 | 4′ листозагибочный станок | 1 | 2 | 2 | 4 |
15 | Подъёмный стол (гидравлика) | 0 | 2 | 4 | 4 |
16 | Шлифовальный станок | 1 | 1 | 2 | 2 |
17 | Вырезатель дырок | 1 | 1 | 1 | 1 |
18 | Обрезчик кромок | 1 | 1 | 1 | 1 |
Видео производства
лущение, сушка
обдирание, нарезка, починка
соединение, нанесение клея
предпрессование, прессование
шлифование
обрезка кромок, готовая продукция
best-china.ru
Производство фанеры: виды и технология изготовления
Технологический процесс, применяемый на современных фабриках, позволяет создать максимально эффективное производство фанеры высокого качества. В результате получают строительный материал, который используется в изготовлении мебели, разнообразных конструкций и для иных целей.
Сфера применения
Фанера – это строительный материал в форме многослойной плиты, созданный через склеивание слоями лущеного шпона с использованием дополнительных фиксирующих компонентов. Для производства конструкций применяют плиту с разным количеством слоев, склеенных по определенному принципу.
Фанера применяется:
Предел прочности фанеры на изгиб
- Для конструирования больших и маленьких летательных аппаратов.
- Для строительства конструкций разных размеров.
- Во всех направлениях производства мебели.
- В производстве облицовочных материалов.
- В производстве строительных материалов.
- В создании музыкальных инструментов.
- Как основу рекламных щитов.
- Для установки опалубки.
- В производстве тары.
- И в других сферах.
Разновидности фанеры
Сегодня на фабриках производят продукцию, отличающуюся по технологическим и конструктивным признакам в зависимости от сферы применения. Она имеет разную внутреннюю структуру, которая определяет ее эксплуатационные качества.
Виды фанеры:
Характеристика фанеры
- Шлифованная и не шлифованная.
- Профилированная фанера.
- Общего назначения.
- Бакелизированная.
- Ламинированная.
- Армированная.
- Облицовочная.
- Строительная.
- Авиационная.
- Водостойкая.
В зависимости от качества шпона наружного слоя, фанера делиться на 5 сортов: А/АВ, АВ/В, В/ВВ, ВВ/С, С/С.
Стадии производства фанеры
Фабричное производство фанеры разных видов, на некоторых этапах немного отличается, но основной технологический процесс ее изготовления остаётся все тем же.
Существуют следующие этапы производства:
- Подготовка древесины.
- Заготовка шпона.
- Склеивание шпона в листы.
- Нанесение защитного и облицовочного покрытия.
Заготовка древесины для получения фанеры
Для производства фанеры используется шпон из лиственных пород и хвойной древесины. Для наружных слоев предпочитают березу, реже граб, тополь, бук и ольху. Цена березового шпона в закупке материала, является самой дешевой, потому она и обрела такую популярность среди производителей. Граб, тополь, бук и ольху считают дорогостоящими материалами, потому их используют для производства шпона по индивидуальным заказам. С хвойных пород деревьев, часто изготавливают внутренний слой, из-за хорошей прочности и небольшой стоимости этой древесины в закупке.
Привезенный материал в первую очередь проходит калибровку на специальном станке. Снимаются все излишки, сучки и кора в результате достигается ровный круг на срезе в соотношении с центром древесины. Длинные бревна разрезаются на одинаковые чурки и направляются на этап варки.
Древесина должна иметь одинаковую влажность. Это необходимо для сохранения целостности структуры будущей плиты и избегания проблем на этапе производства. Перед лущением, все заготовки на продолжительное время замачивают в теплой воде, тем самым выравнивают их общую влажность.
Размягчённое в воде бревно легче поддается лезвиям станков, это в несколько раз ускоряет процесс нарезания и сохраняет длительное время податливость материала.
В воду могут добавлять вещества, придающие будущим изделиям дополнительные свойства. Как только древесина равномерно пропитываться влагой, ее отправляют на этап изготовления шпона.
Процедура изготовления и отделки шпона

Шпон для производства фанеры
Подготовленные бревна загружают в специальные установки, фиксируя их между тремя валиками и, с помощью лезвий срезают листы или ленту шпона. Валики одновременно фиксируют и вращают бревна с заданной скоростью. Размеры определяют в зависимости от технических характеристик лущильного станка и размеров готовой продукции. Листы складывают в стопки, а ленту сматывают в рулон.
Далее, шпон загружают в форматно-раскроечный станок, с которого выпускают ленту и ножами нарезают ее на листы требуемых размеров. Весь процесс автоматический и настраивается оператором станка.
Сушка проводится в специальных закрытых помещениях, с автоматическим контролем температуры. Горячий воздух стараются распределять неравномерно, чтобы разделить сушку на несколько последовательных этапов. Рулоны или листы в подвешенном состоянии перемещают по многоэтажной роликовой системе. Это позволяет провести процесс сушки максимально эффективно с соблюдением всех временных ограничений. Влажность шпона должна быть – от 4 до 6%.
После сушки, шпон проходит ОТК. Контролеры и рабочие удаляют все дефектные участки, листы сортируют согласно требуемым размерам и влажности. Готовый элемент отправляют в цех производства фанеры.
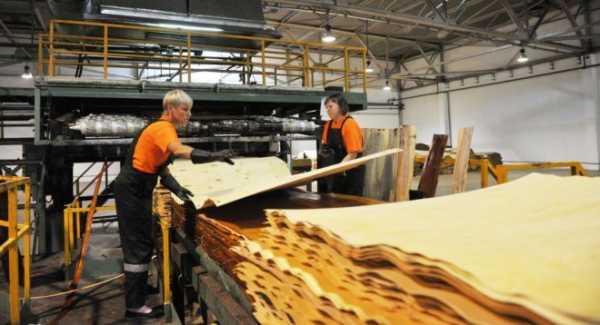
Цех по производству фанеры
Технологический процесс производства
Технологический процесс изготовления фанеры происходит в несколько этапов.
Склеивание
На специально оборудованных столах располагают листы шпона одинакового размера. Их поверхность очищают от древесной пыли и мелкого мусора, чтобы при склеивании не создавалось лишних бугорков. Далее, собирают и группируют по размерам в стопки для будущей склейки каждой плиты.
Вначале изготавливается хвойная фанера, как внутренний слой и будущий каркас. На первый лист наноситься влагостойкий клей, бакелитовая пленка или смола. Сверху его прижимают следующим листом шпона в результате получается своеобразный бутерброд. Процесс могут повторять до получения 3 и более слоев. Вся работа проводиться в хорошо проветриваемых помещениях из-за повышенной токсичности некоторых веществ в составе клея.
Часто, количество слоев увеличивают для повышения прочности. Например, такой способ применяют во время производства строительной фанеры.
Процесс склеивания фанеры
При склеивании волокна древесины каждого нового слоя стараются располагать перпендикулярно предыдущему, что в несколько раз увеличивает прочность будущей конструкции. Если слоев в плите четное количество, это значит, что направление внутренних волокон древесины расположено параллельно друг к другу. Для получения широких полноформатных листов используют способ ребросклеивания по продольным кромкам.
В случае обнаружения поврежденных участков на листах, их вырезают и заменяют специальными заранее подготовленными заплатками. Поврежденный шпон, стараются использовать для создания внутренних слоев фанеры.
Иногда на спиле листа можно увидеть резкие изменения цвета волокон с черными включениями. Это говорит о том, что производитель экономил на закупке качественной древесины, использовал подгнившее второсортное сырье или нарушил технологический процесс изготовления продукции. Такая плита редко когда выдерживает требуемые нагрузки и через непродолжительное время может разрушиться.
Холодное склеивание или термическая обработка под давлением
Первый способ – при холодном склеивании лист фанеры помещают в пресс и оставляют его там при комнатной температуре на 6 часов. После застывания, его отправляют на этап просушки.
Второй способ – готовые тщательно склеенные листы направляют под термопресс, где с давлением и высокой температурой соединения набирают окончательную прочность.
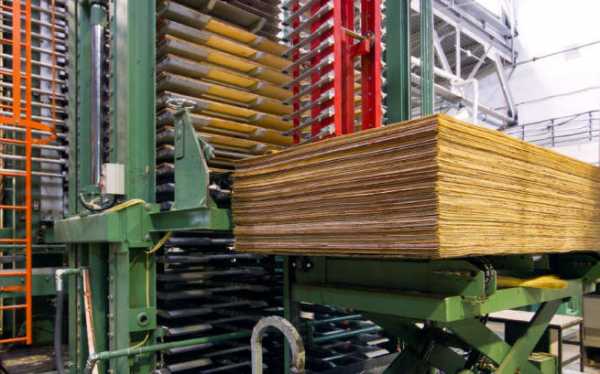
Процесс прессования фанеры
Нанесение покрытия
В отдельном цеху поверхность шлифуют и наносят разнообразные покрытия. Для этого используют всевозможные лаки, краски или готовые наклейки с изображениями.
В зависимости от покрытия фанеру разделяют:
- На облицовочную – состоит из нескольких слоев лущеного шпона. Имеет облицовочное покрытие с одной или с двух сторон.
- Ламинированную фанеру – покрытие чаще всего имитирует древесную структуру.
- Шлифованную и не шлифованную – на поверхности создаётся специфическая текстура.
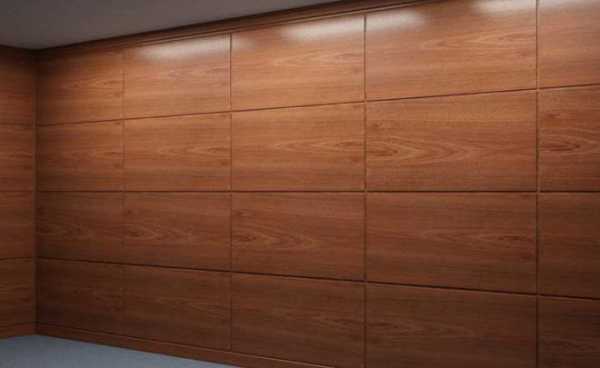
Облицовка фанерой
Особенности производства разных видов фанеры
Бакелизированная фанера – имеет увеличенную прочность структуры. Эффект достигается пропитыванием листов шпона бакелитовой смолой с дальнейшим спрессовыванием, под высоким давлением с температурой 270 °C.
Водостойкая – для производства используется водостойкий фенолоформальдегидный или карбамидоформальдегидный клей.
Профилированная – имеет сложную волнообразную структуру волокон для увеличения продольной прочности.
Армированная – внутри размещают слой, который придает дополнительную прочность будущей плиты, вставка может быть металлопластиковой, стекловолоконной или в форме металлической сетки.
Авиационная фанера – производиться из березового шпона (один из самых легких материалов). Ее могут применять в авиастроении и создании легких конструкций.
Упаковка
Готовая продукция в зависимости от размера и пожеланий заказчика, упаковывается в различные влагозащитные материалы и коробки.
Производство фанеры не требует больших денежных вложений на закупку оборудования и запуск процесса производства. Принцип технологического процесса простой и малозатратный, потому начать свой бизнес по силе каждому предпринимателю.
Видео: Производство фанеры
promzn.ru
Какое необходимо оборудование для производства фанеры? :: BusinessMan.ru
На сегодняшний день одной из самых прибыльных отраслей по производству строительных материалов является изготовление фанеры.
Начинающие предприниматели думают, что нет ничего проще, чем купить станок для производства фанеры и необходимый материал. Но все совсем не так. Для того чтобы получить достаточно большую прибыль, нужно выбрать правильный план развития.
Какую стратегию выбрать
Прежде всего необходимо разработать такую стратегию, которая была бы тщательно выверенной и максимально продуманной. А для этого нужно составить бизнес-план. С его помощью вы сможете оценить тот доход, который будете получить в будущем, продумать, сколько денег вы должны потратить, чтобы получить именно такую прибыль, а также решить, какое оборудование лучше всего подобрать.
Какое оборудование вам придется закупить
Если с затратами на производство и материалами все понятно, то оборудование для производства фанеры нуждается в тщательном выборе. Прежде всего, вы должны понимать, что количество закупаемых аппаратов зависит от того, сколько готовой продукции вы готовы продавать. Но при этом нужно знать, что обязательно нужно купить станки следующих типов:
- лущильный;
- калибровочный;
- раскроечный.
Калибровочный станок помогает снять верхний слой с дерева. Лущильный снимает ту часть шпона, которая находится на верхнем слое древесины. Раскроечный помогает максимально точно разрезать полотно на такие листы, которые вам необходимы для продажи. Как правило, для закупки всего необходимого оборудования начинающему предпринимателю придется потратить около 65 тысяч долларов.
По какой технологии создавать фанеру
Перед тем как сырье попадает в агрегаты, его тщательно отбирают. После этого материал нужно проварить в специальном бассейне для того, чтобы он стал более удобным в работе. Также это позволяет сделать сырье качественнее. После окончания процесса обработки нужно снять кору с древесины, просмотреть, нет ли на ней металлических предметов. Только тогда ее можно подавать в оборудование для производства фанеры.
Сняв на лущильном станке первый слой шпона, его разделяют на отдельные листы. Их нужно отослать в сушилку, где они сортируются. Стоит понимать, что из разных видов деревьев получается разный шпон.
Если в шпоне есть слишком много влаги, то его дополнительно просушивают. После всех необходимых проверок листы склеивают таким образом, чтобы волокна разного шпона соединялись перпендикулярно друг другу. Это делает будущую фанеру более прочной. После этого шпон идет под холодный пресс, а потом на обрезку до нужного размера.
Какие станки позволяют просканировать недостатки древесины
Характеристика оборудования для производства фанеры позволяет уже на первом этапе производства узнать, какие недостатки существуют в материале, и исправить их. Для этого нужно приобрести специальные измерители количества влаги и конвейеры. Также нужно подумать о покупке линии, которая позволяет сушить и сортировать шпон.
Другие агрегаты
Если вы собираетесь производить фанеру, то в ваших цехах обязательно должно присутствовать автоматическое оборудование для прессования горячего типа с выгрузкой и загрузкой, а также для преждевременного прессования. Благодаря тому что древесина там поддается обработке под высоким давлением, она становится более прочной.
С помощью станка для обрезки панелей ваша фанера получит необходимую форму и размер. Также вам понадобятся ленты для транспортировки отходов шпона и готовой продукции. Такие линии являются автоматическими.
businessman.ru