Изготовление обуви своими руками — ручное производство
Обувь ручной работы пользуется большим спросом благодаря качеству и долговечности – обычно производство обуви ручной работы основано на натуральных материалах, требует более высокие требования к качеству готовой продукции. Соответственно, цена на обувь, сшитую вручную, будет выше в сравнении с изделиями, сшитыми на автоматизированном производстве.
Фирмы обуви ручного производства
Даже в век максимальной автоматизации обувь, изготовленная вручную, не является чем-то диковинным. Классические английские производства, которые высоко ценятся во всем мире:
- Crockett&Jones;
- Loake;
- Grenson;
Они выпускают обувь из натуральной кожи и замши, сшитую на ручном производстве. Этапов производства при этом значительно больше, чем при массовом автоматизированном изготовлении. Пара может изготавливаться в течение месяца, в зависимости от типа материала и сложности формы.
Что касается форм и конструкций, наиболее популярными ботинками в ручном исполнении являются:
- Оксфорды;
- Дерби.
Они отличаются по типу шнуровки. Оксфорды имеют закрытую шнуровку, скрытую передней частью ботинка. Боковые части пришивают клинообразно, возможна перфорация.
Дерби же, напротив, имеют открытую шнуровку, а боковые части нашивают поверх передней части таким образом, чтобы при развязывании шнуровки ботинок свободно расходился. Дерби также может иметь перфорацию и считается наиболее универсальной обувью для любого случая.
Особенности конструкции
Всю структуру обуви разделяют на верхнюю и нижнюю часть. В составе верхней части состоят такие элементы:
- Носок – закрывает пальцы ног, выдерживает наибольшие механические нагрузки при носке.
- Союзка – закрывает тыльную часть стопы и соединяет носок, язычок и берцы.
- Берцы – закрывают голеностопный сустав, их пришивают к союзке.
- Люверс – верхняя часть обуви, предназначенная для отверстий или крючков шнуровки.
- Задник – защищает пятку и стопу, фиксирует пятку, изготавливается из жесткой кожи.
- Язычок – покрывает верхнюю часть ступни, пришивается к союзке.
- Стелька – соединяет верхнюю и нижнюю части.
В составе нижней части изделия:
- Подошва – сшивается по контуру с верхней частью, делится на подметки, геленок, рант и наполнитель.
- Каблук – приподнимает пятку и крепится к подошве, верхний слой может быть каучуковым.
- Набойка – защищает каблук от протирания.
- Рант – связующий элемент между деталями.
- Защитные вставки – предотвращают истирание нижнего слоя каблука.
- Наполнитель – заполняет пространство под стелькой, повышает комфорт при эксплуатации.
- Супинатор – деревянная или металлическая деталь, закрепляемая между подошвой и стелькой.
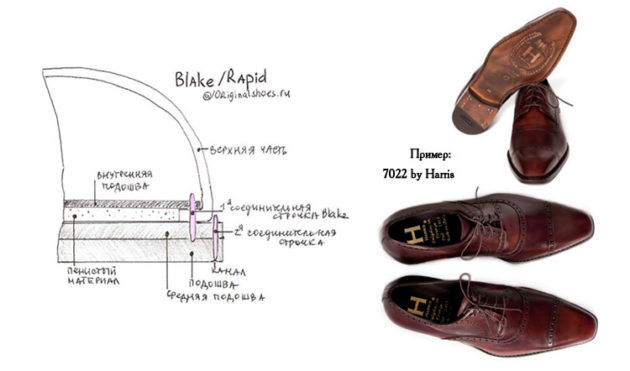
Особенности конструкции
Знание конструкции обуви позволяет изготовить каждую деталь более качественно, в соответствии с ее предназначением.
Этапы изготовления
Для изготовления обуви своими руками понадобится немало времени, но сам процесс несложный и зависит, в основном, от правильности замеров и качества исходных материалов. Весь процесс можно разделить на девять этапов.
Снятие мерок
Без этого этапа не обходится пошив обуви по индивидуальному заказу, то же касается и одежды. Снятие мерок осуществляется, главным образом, для замера параметров будущей колодки.
Создание макета
Подготовив по меркам колодку, шьют предварительный макет. Для его создания шьют по готовой колодке из тонкой натуральной кожи. Здесь же следует определиться, какой вид будет у модели, как располагаются швы, имеется ли рисунок или перфорация.
Подготовка выкройки
Заготовка для будущей пары ботинок вырезается из листа натуральной замши или кожи. Важно оставлять небольшой попуск на сжатие и шов – строго по контуру замеров вырезать нельзя, иначе обувь будет мала как минимум на размер.
Стадия обметки
Сшитые по выкройкам верхние части будущей пары ботинок соединяют вместе. Это трудоемкая часть работы, поскольку при обметке верхней части ботинок может потребоваться обтачивание кожи, подравнивание края, его подкрашивание.
Натягивание заготовки
На этом этапе уже готова колодка для будущей пары ботинок, а также верхняя ее часть. Теперь эту верхнюю часть в прямом смысле натягивают встык на ранее подготовленную колодку. На этом этапе наиболее важным шагом является укладка стельки, так как от правильности ее укладки зависит удобство при эксплуатации обуви.
Нашивка ранта
Рантом называют тонкую кожаную полоску, соединяющую все части ботинка, уже натянутые на колодку. Это изобретение принадлежит Чарльзу Гудиеру – благодаря его технологии, обувь может быть расшита по местам соединения рантом и починена в случае, например, потрескавшейся колодки, подошвы.
Пришивание подошвы
Подошва может быть выполнена из разных материалов – их следует заранее уточнить у заказчика, подсказав ему наиболее подходящий вариант к желаемой паре. Часто делают кожаные или каучуковые подошвы.
Пришитые подошвы укрепляются небольшими гвоздиками – мастера используют их для прямоты и надежности каблука. Последний набирают из толстой кожи в несколько слоев.
Окрашивание подошвы
После пришивания подошвы и набивания каблука необходимо окрасить их необходимым цветом – выбор цвета зависит от тона ботинок. При подсыхании нанесенной краски, подушка полируется для нанесения фирменной маркировки мастера.
Полирование
Ручное изготовление ботинок заканчивается самым важным этапом – полированием и доведением до идеального состояния готовой пары. После полирования получается ровная, упругая, идеально вычищенная пара с прочными соединениями.
Видео по теме: Индивидуальный пошив обуви Головань
promzn.ru
Производство обуви: оборудование, материалы и технология
Обувь всегда является востребованным товаром среди населения, поэтому обувная промышленность является популярной отраслью бизнеса. В современное время на рынке представлено много моделей данной продукции различных производителей и фабрик.
Мировая конкуренция
На сегодняшний день многие покупатели желают иметь не только качественную и практичную обувь, но и соответствующую модным тенденциям. Среди экспертов данной сферы деятельности замечено, что доходы российских фабрик и спрос на продукцию, напрямую зависят от иностранных производителей.
Обувная промышленность хорошо развита в Китае. С одной стороны, продукция из Китая славится невысокой ценой, однако, плохим качеством. С другой стороны, существует немало известных европейских брендов с продукцией высокого качества, и соответственно, завышенной стоимостью.
Из-за быстрого повышения цен на импортную продукцию и некачественного товара и Китая, все больше покупателей начинают отдавать предпочтение отечественному производителю. Поэтому многие предприниматели задумываются об открытии фабрики по производству обуви.
Чтобы потеснить китайских производителей и соперничать с европейскими поставщиками, необходимо выпустить дизайнерский модельный ряд с какой-либо изюминкой.
Технология производства обуви в промышленных масштабах осуществляется в несколько этапов:
- Проектирование и создание моделей обувного ряда с разработкой всей необходимой документации.
- Производство обуви и сбыт партий.
Технология пошива
Предварительно материалы, используемые в производстве, необходимо:
- тщательно проверить на соответствие качественным характеристикам;
- отсортировать в производственные партии;
- направить в раскройный цех.
Первым делом дизайнерами-специалистами разрабатывается дизайн и внешний вид будущей модели, создается эскиз, выполняется заготовка.
Для создания производства по пошиву обуви необходимы соответствующие материалы, одни из них являются основными, другие – вспомогательными.
Основные материалы применяются для изготовления наружных, внутренних и промежуточных элементов верхних и нижних частей изделия:
- разные виды кожи;
- меха;
- текстильные материалы.
К вспомогательным материалам относятся детали, предназначенные для отделки и украшения моделей:
- различная обувная фурнитура;
- текстильно-галантерейные изделия;
- клей.
Таким образом, для изготовления обуви существует достаточно большой выбор материалов. Однако, самый лучший из них – натуральная кожа.
Помимо натурального сырья, в последнее время все чаще применяются синтетические материалы для производства обуви, которые значительно дешевле. Однако, многие из них не только дешевле, но часто и практичнее природных аналогов.
Раскройный цех
Именно в раскройном цеху выполняется создание эскиза обуви, моделирование изделия и раскрой деталей.
Из заранее подготовленного материала изготавливаются составные части обуви, для получения которых предназначены два специальных вырубочных пресса:
- один – для работы с верхними деталями;
- второй – для нижних деталей изделия.
Некоторые части обуви вырезаются вручную при помощи трафарета.
Пошивочный участок
Верх обуви изготавливается отдельно от подошвы и включает в себя следующие детали:
- Переднюю часть изделия – носок;
- Среднюю часть изделия – союзку;
- Часть, фиксирующую верх ноги – язычок;
- Заднюю часть изделия, фиксирующую пятку – задник.
Необходимое оборудование
Перед тем как сшивать детали, необходимо каждую часть истончить, чтобы швы были ровными и аккуратными. В пошивочном цехе выполняется сшивание подготовленных деталей. Необходимо следующее оборудование для производства обуви:
- Швейные машины;
- Пошивочный конвейер;
- Машина для вставки подносков;
- Машина для загибки краев и разглаживания швов;
- Машина для формовки кожаных нашивок на носок обуви.
Технология крепления подошвы
Подошва крепится к верху обуви разными способами:
- Клеевым;
- Прошивным;
- Комбинированным;
- Вулканизацией.
Клеевой способ популярен, поскольку надежен и недорогой в выполнении. При правильном выполнении технологии склейки, вероятность проникновения влаги между верхом и подошвой практически невозможна. Однако, при склеивании некачественным клеем или с нарушением правил крепления, обувь может быстро развалиться.
Прошивной способ крепления подошвы к верху обуви недостаточно практичен к проникновению влаги, также высокая вероятность повреждения прошивной нити.
Комбинированный метод предполагает использование клеевого и прошивного способов.
Вулканизация – части изделия (верх и низ) практически свариваются в одно целое. Используя такой способ, вероятность отсоединения подошвы от верха практически исключается. Недостаток у данного способа один – ограниченность в выборе материалов.
Пошив внутренней части
Внутренняя часть обуви подшивается подкладкой, которая может быть выполнена из следующих материалов:
- кожаная;
- текстильная;
- из искусственных материалов;
- комбинированная из разных материалов;
- шерстяная на тканой основе;
- из натурального меха на кожаной основе.
От качества выполнения соединения деталей зависит качество будущей модели.
Соединение частей изделия
Способ скрепления верхних и нижних частей обуви отвечает за многие эксплуатационные характеристики:
- гибкость;
- легкость;
- износостойкость.

Гибкость обуви
После того как верх изделия будет готов, он натягивается на колодку и с нижней ее стороны закрепляется со стелькой. Этот процесс называется – «затяжка». На этом этапе в носок и задник будущей обуви устанавливаются формовочные элементы:
- в носок – подносок;
- в задник – усилитель жесткости в виде пластиковой пластины или дополнительных слоев кожи.
Колодки могут быть выполнены по-разному, в зависимости от будущей модели. Они могут быть в следующем выполнении:
- цельные;
- раздвижные;
- сочлененные;
- с выпиленным клином.
Фасон колодки зависит от тенденций моды, поскольку это является основной технической характеристикой, от которой зависит вид будущей изготовленной модели.
Производство стелек
Внутрь готового изделия вкладываются стельки. Стельки могут быть выполнены из разного сырья. Материал, из которого изготавливается стельки, должен быть качественным, поскольку именно он будет впоследствии соприкасаться с ногой человека. Стелька может быть выполнена из влагостойкого картона или синтетического нетканого материала.
Для изготовления обувных стелек выбранная ткань прессуется на специальном оборудовании. Затем машиной для шлифовки обрабатываются края и промазываются специальным клеем, после чего проходят еще одну прессовку.
Стельки к модели можно приобретать отдельно, исходя из потребностей, это могут быть:
- утепленные стельки;
- ортопедические;
- другие варианты.
Заключительный этап
Изготовление обуви после крепления подошва завершается окончательной отделкой изделия:
- необходимо отрезать излишки материала;
- вклеить мягкие подпяточники;
- вложить стельки;
- сформировать голенища.
Завершающим этапом является обработка готового изделия при помощи специальных покрытий:
- восков;
- спреев;
- кремов.
При необходимости выполняется вставка шнурков, крючков и других аксессуаров и фурнитуры.
Готовая продукция поступает в отдел проверки качества, где сортируется, маркируется, упаковывается попарно и группируется по партиям для сбыта.
Организация бизнеса
Если хорошо ознакомиться с данной отраслью, обувная промышленность может стать прибыльным доходом. Необходимо ознакомиться со всеми нюансами производства, пошива обуви, выбора материалов и оборудования, а также соблюдать ряд последовательно выполняемых операций и действий.
Для организации бизнеса в сфере производства обуви необходимо выполнение следующих пунктов:
- приобретение производственного помещения с необходимым оборудованием;
- приобретение материалов;
- сертификация и декларация продукции;
- договора по сбыту готовой продукции.
Перед тем как закупать материалы и оборудование, стоит определиться со стилем будущих коллекций. Формат изделий может быть разный – производство классической кожаной обуви, резиновые или спортивные модели. Кроме того, можно выбрать одно направление продукции: либо производство мужской обуви, либо производство женской обуви. Очень прибыльна и востребована среди покупателей детская продукция.
Следует учитывать и сезонные периоды. Как правило, сезон начинается с осени и идет до весны следующего года. В летнее время:
- пересматривается ассортимент;
- разрабатываются новые модели;
- обновляется оборудование.
Следует учитывать также, что одной из больших проблем и трудностей обувного производства, является отсутствие качественного отечественного сырья для производства обуви. Поэтому, изделия, которые производятся в нашей стране, почти наполовину состоит из импортных материалов.
Таким образом, обувная промышленность России не является сильной стороной нашей страны и уступает в объемах производимой продукции многим странам.
В заключение
Если иметь оригинальную идею, которая позволит выделить коллекцию на фоне конкурентов, а также учитывать потребности и пожелания покупателей, обувная промышленность может стать прибыльным производством.
Видео по теме: Производство обуви
promzn.ru
Обувь своими руками, выбор материалов, пошаговый алгоритм создания
Несмотря на огромный ассортимент самой разной обуви на полках магазинов, часто люди заинтересованы в самостоятельном изготовлении тапочек, туфель или ботинок. Объясняется подобное желание многими причинами: возможностью удешевить готовое изделие, получить модель уникального дизайна, идеально соответствующую параметрам стопы, или даже попросту попробовать силы в новой для себя сфере. Как бы там ни было, чтобы сделать обувь своими руками, необходимо детально изучить все этапы производства, подобрать подходящее сырье и инструментарий, грамотно построить выкройку, выполнить множество других действий. Процесс длительный и сложный, требующий недюжинного терпения, концентрации внимания, усидчивости, при этом он вполне посильный, интересный и познавательный.
Особенности конструкции
Современный рынок представляет множество моделей обуви, которые отличаются друг от друга материалом и внешним видом. Перед изучением этапов изготовления изделий из кожи или замши стоит ознакомиться с конструкцией, составными частями, их отличиями.
Элементы, из которых состоит верхняя часть обуви:
- Носок — часть, закрывающая поверхность пальцев стопы, сохраняет ногу от механических повреждений, чаще всего вступает в контакт с внешней средой.
- Союзка — деталь, закрывающая тыльную поверхность стопы. При ходьбе постоянно поддается изгибам, поэтому деформируется первой.
- Берцы — охватывают нижние части голени и голеностопного сустава. При эксплуатации эта часть практически не поддается негативному воздействию извне.
- Люверс — место, предназначенное для проведения шнурков, веревок.
- Задник — деталь, которая закрывает пяточную часть стопы.
- Язычок — часть, прикрепленная к основанию ботинка, фиксирует ногу, предотвращает попадание внутрь пыли, грязи, мелких деталей.
- Стелька — слой мягкой и приятной кожи (или другого материала), который контактирует непосредственно со стопой, смягчает ходьбу, убирает дискомфортные ощущения даже при беге.
Нижняя часть обуви представлена следующими элементами:
- Подошва — самая значимая деталь низа, которая определяет не только удобство при хождении, но еще долговечность изделия. Она защищает ногу от неприятного контакта с грунтом, смягчает механическое воздействие при прыжке, беге, ходьбе.
- Каблук — деталь, которая предназначена для подъема пяточной части стопы. Может быть разных формы и размера, все зависит от модели, сезонной конструкции.
- Набойка — прикрепляется к поверхности каблука, защищает его от истирания.
- Рант — деталь, отвечающая за крепление низа обуви.
- Защитные вставки — элементы, сделанные из хлопковой ткани и полиуретана, предотвращающие натирание пятки, появление мозолей.
- Наполнитель — материал, который обеспечивает воздухопроницаемость, тепло, вентиляцию, защиту от сезонных погодных условий.
- Супинатор — деталь, которая размещается между подошвой и основой стельки, создает нужные жесткость и упругость.
На подошву приходятся огромные нагрузки, она подвергается постоянному износу при контакте с землей, поэтому материал для ее производства должен быть качественным и прочным.
Изготовление своими руками обуви требует соблюдения многих правил. Для каждой из описанных деталей существуют свои нюансы производства.
Материалы и инструменты
Перед тем как сделать обувь своими руками, важно подобрать правильный материал и собрать нужные инструменты. Взрослую или детскую продукцию чаще всего изготавливают из кожи, замши, текстиля. Популярностью пользуется именно натуральная кожаная обувь, потому что она долговечная, практичная, износостойкая, шансов натереть ноги гораздо меньше. Из этого сырья делают: кроссовки, ботинки, сапоги, туфли, кеды, шлепки.
Замша — приятный, мягкий, эластичный материал, используемый как для взрослой, так и для детской обуви. В ней нет лицевого слоя, она трудоемкая в изготовлении, поэтому достаточно дорогая. Текстиль — применяется для пошива летней обуви, пинеток для детей, кед, а также домашних тапочек. Материал очень нежный, мягкий, приятный на ощупь. В такой обуви нога всегда дышит, получает нужную вентиляцию, комфорт, тепло.
Текстиль экологически чистый, поэтому чаще всего его используют для изготовления детской обуви.

Кожа
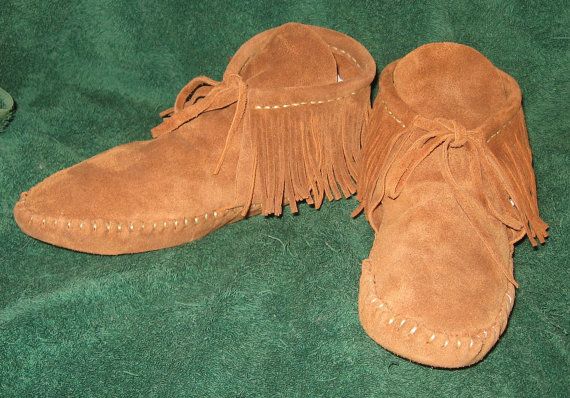
Замша
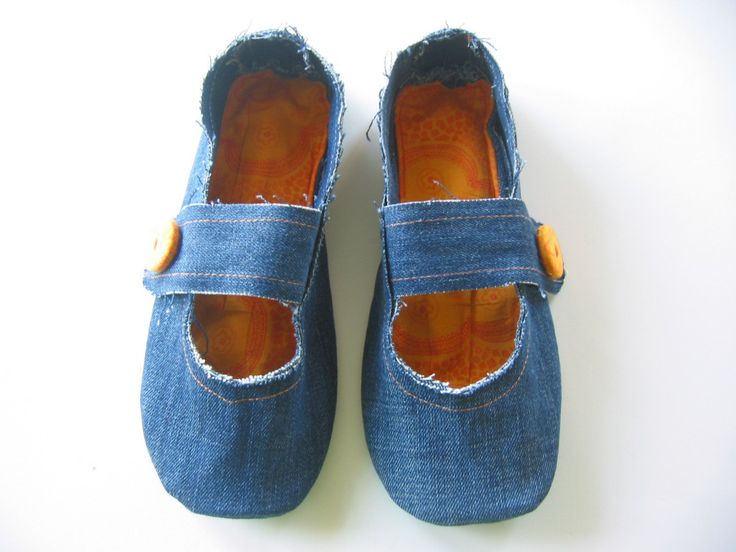
Текстиль
При изготовлении подошвы своими руками применяют:
- Кожу — обладает повышенной стойкостью, прочностью, защищает ногу от внешних повреждений, позволяет ей дышать. Кожаную подошву сделать своими руками не сложнее, чем из любого другого материала.
- Резину — износостойкий материал, устойчивый к морозам, перепадам температуры, обладающий термопластичностью. Характеризуется прочностью, практичностью, долговечностью. Единственным минусом является повышенная маркость такой подошвы.
- ПВХ — дешевый материал, который обладает хорошей износостойкостью, его можно красить. Используется для изготовления зимней обуви. Недостаток — слишком тяжелый.
- ТЭП — изготавливается из термопластичной резины, характеризуется хорошей износостойкостью, не скользит на мокрой дороге. Недостаток — невозможно придать четкие и ровные очертания.
- Полиуретан — имеет низкую теплопроводность, мягкий, легкий, из него изготавливаются любые сезонные модели. Легко поддается ремонту. Обувная индустрия часто использует этот материал. Недостаток — непрочный, быстро истирается.
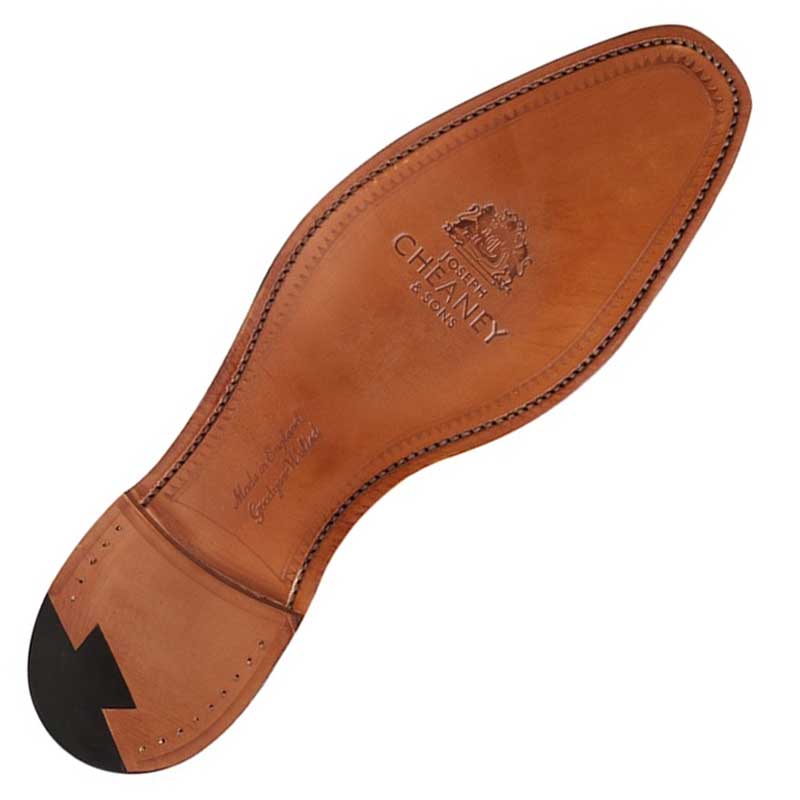
Кожа
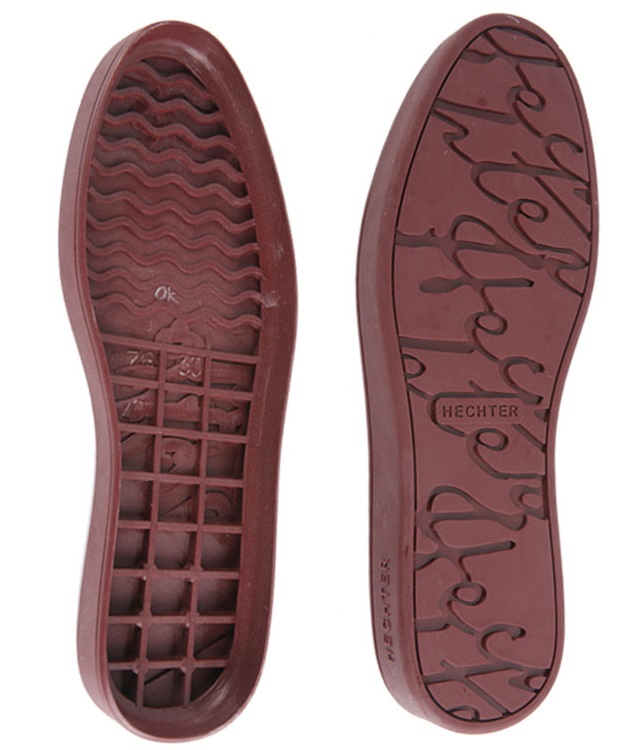
Резина
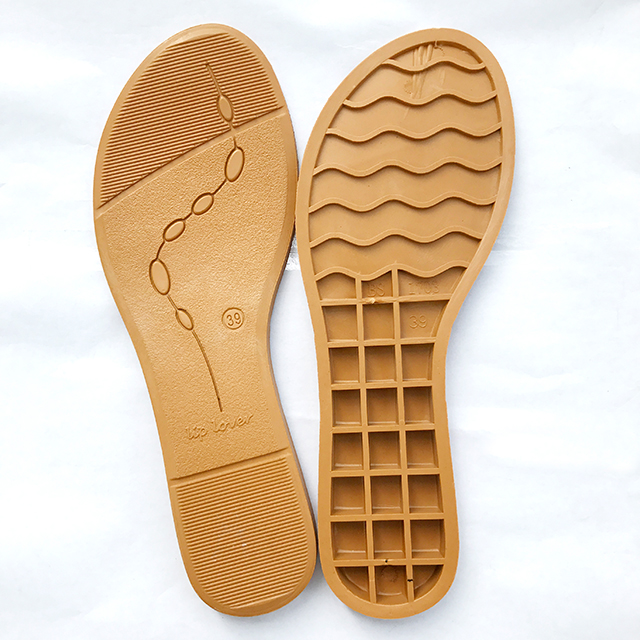
ПВХ
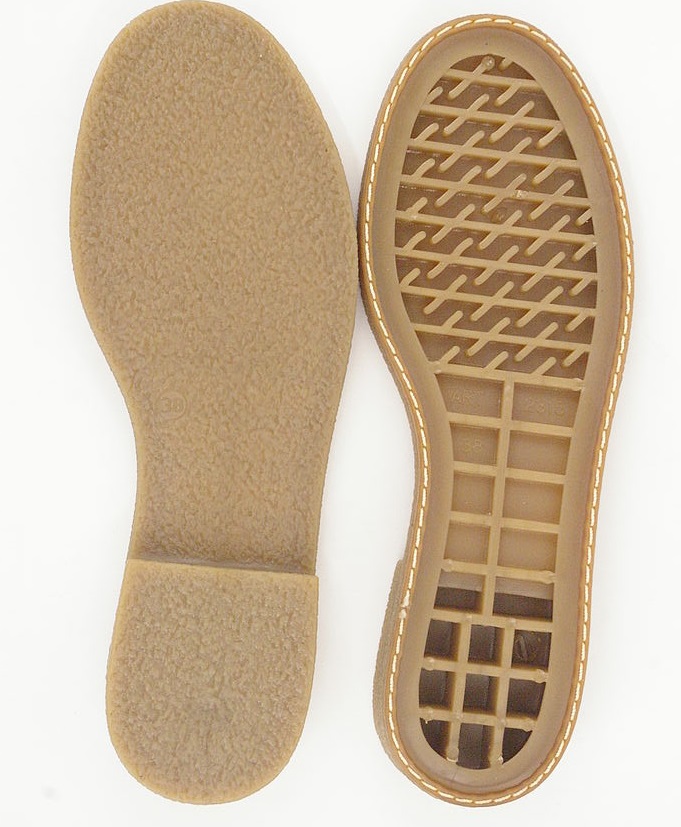
ТЭП
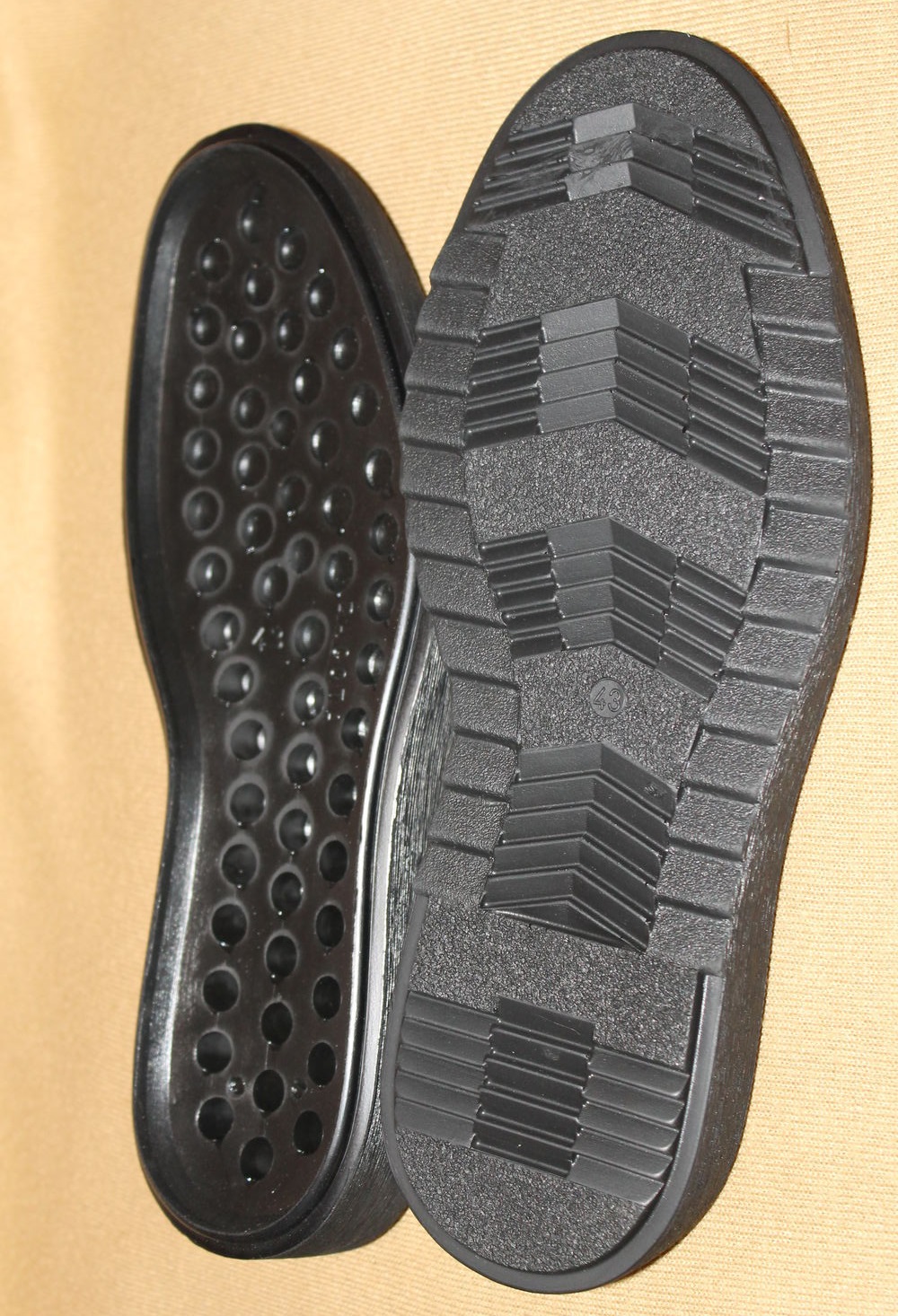
Полиуретан
Пошив обуви будет невозможен без следующих инструментов и расходного сырья:
- напильник;
- токмач;
- пчелиный воск;
- шило;
- затяжные клещи;
- молоток;
- сапожный нож;
- полиуретановый клей «Десмокол»;
- гвозди;
- изолента.
Позаботиться о наличии всех необходимых материалов и инструментов стоит заранее, только потом можно переходить к процессу изготовления.
Этапы изготовления
Создание туфель или сапог состоит из последовательных этапов, которые важно соблюдать.
Снятие мерок
Снятие мерок для пошива обуви — первый значимый этап, он помогает определить нужный размер выбранной модели. Пошагово процесс выглядит так:
- нога ставится на белый лист бумаги, стопа обводится по контуру;
- ее длина определяется как расстояние между выступающим пальцем и пяткой, ширина — как расстояние между точками в самой широкой ее части;
- измеряется обхват подъема и лодыжки с помощью мерной ленты;
- определяются обхваты: икроножной мышцы (для высоких сапог), косой через пятку, стопы в самой узкой и самой широкой частях.
Карандаш при обведении стопы надо держать перпендикулярно плоскости бумаги.
Каждая снятая мерка записывается на лист, затем эти параметры используются при изготовлении макета и выкройки.
Создание макета
Следующим этапом создается колодка. В качестве материала используют дерево, которое характеризуется повышенной твердостью, устойчивостью ко влаге. Например, бук, березу, клен. Для работы понадобятся два куска дерева, предпочтительно квадратного сечения.
При выборе брусков надо понимать, какого типа колодка должна получиться: у сапожной горловина должна быть повыше, примерно на 3 см по сравнению с туфельной. Если для первой берется брусок сечением 15 × 15 см, то для второй будет достаточно 12 × 12 см.
Из инструментов нужны:
- топор;
- киянка;
- ножовка по дереву;
- рашпиль;
- набор стамесок и круглых резцов.
Кроме того, пригодится старая обувь, хорошо облегающая ногу. Пошаговый алгоритм:
- На одной стороне бруса рисуется по меркам подошва, а сбоку лекалом вырисовывается профиль будущей желаемой модели.
- Между верхней и нижней частями нужно сделать центральные линии, просверлив два сквозных отверстия.
- Ножовкой или топориком удаляются все ненужные сучки и осколки. После этого заготовке придается форма, схожая с формой ноги.
- Более грубая обработка делается с помощью киянки и стамесок. Потом в ход идут круглые резцы, так как в некоторых местах колодка бывает не только выпуклой, но и вогнутой внутрь.
- В конце проводится шлифовка с использованием наждачной бумаги или рашпилей. Если в обуви планируется каблук, для него нужно создавать специальное углубление.
Сделав колодку по меркам, переходят к созданию предварительного макета. Для этого готовое изделие обшивают тонкой, натуральной кожей. В этот момент уже нужно понять, какой будет модель, предусматриваются ли дополнительные внешние дизайнерские швы, рисунки. Они отмечаются на макете предварительно, затем, ориентируясь на готовый внешний вид модели, переходят к более сложным стадиям изготовления.
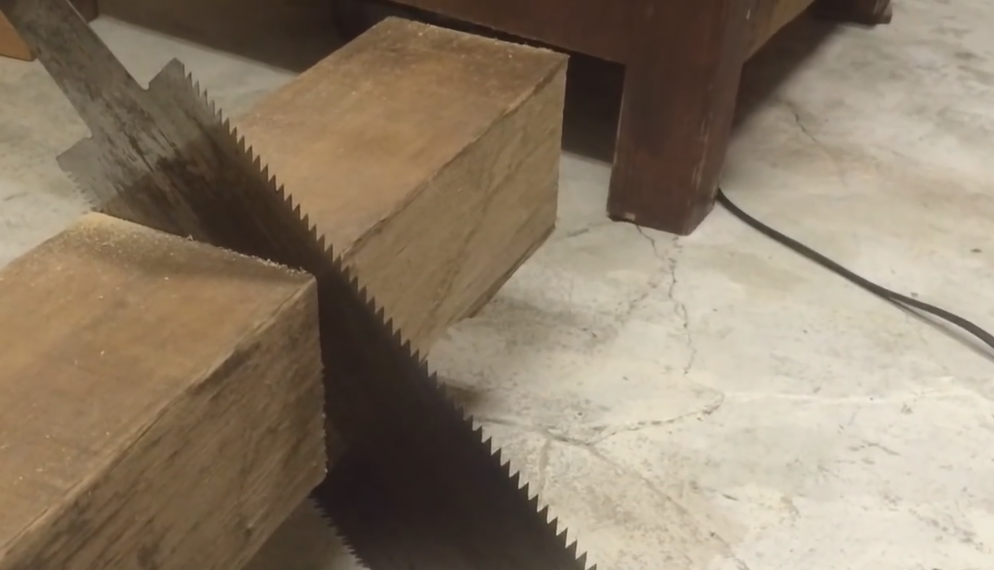
Взять два куска дерева
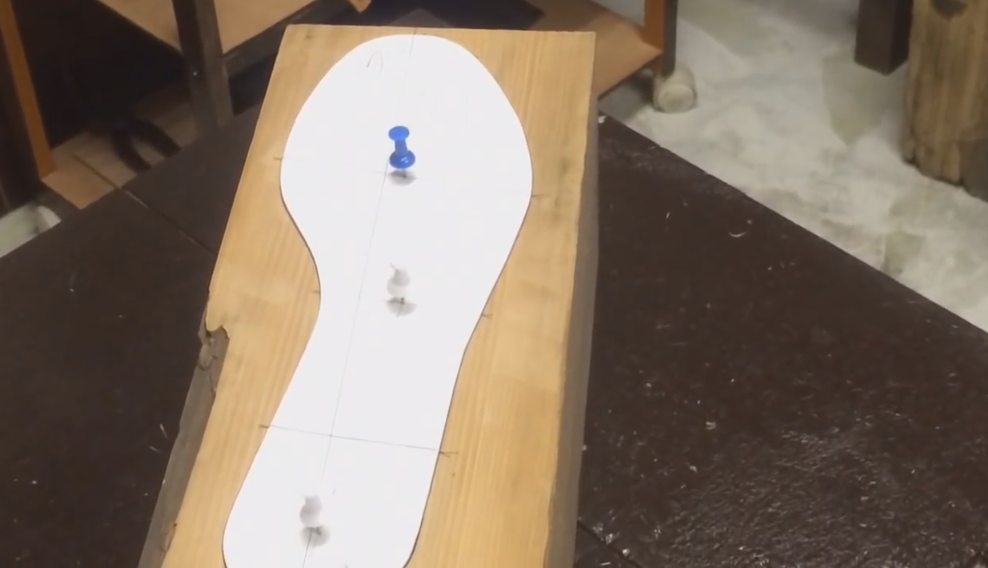
На одной стороне бруса нарисовать по меркам подошву
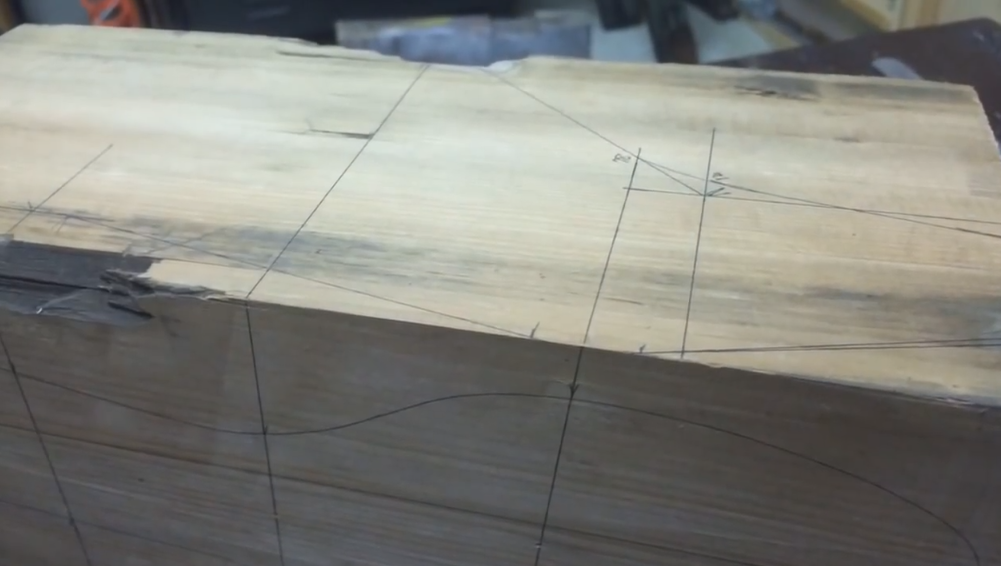
Сбоку лекалом вырисовать профиль будущей желаемой модели
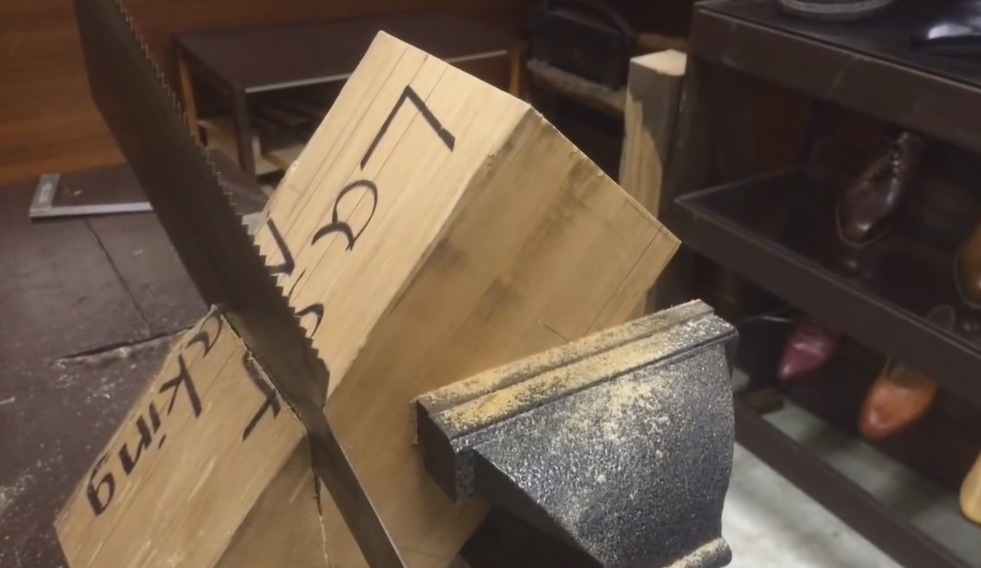
Просверлить два сквозных отверстия между верхней и нижней частями
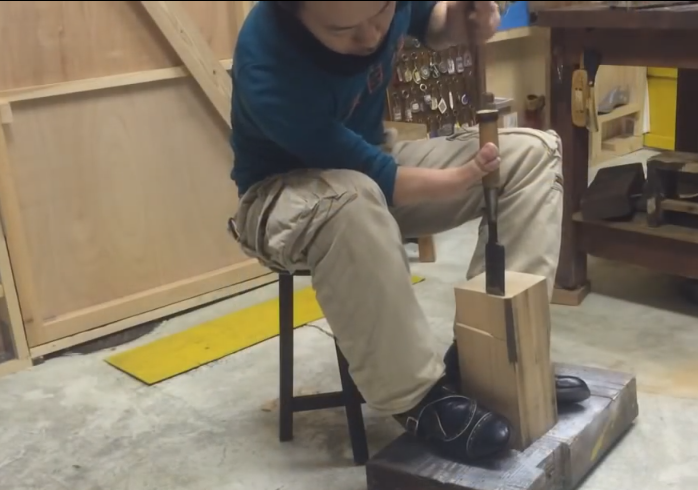
Удалить ненужные сучки и осколки

Более грубую обработку делать с помощью киянки и стамесок
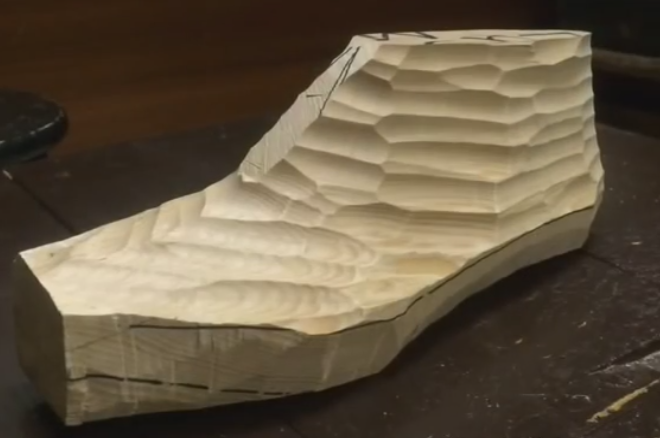
Для выпуклостей и вогнутостей использовать круглые резцы
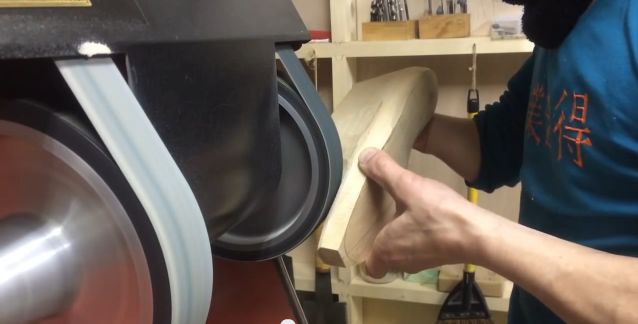
Отшлифовать изделие
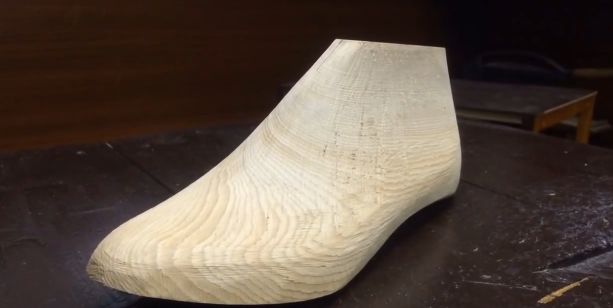
Готовая колодка
Подготовка выкройки и обметка
Выкройка стельки делается на основе обведенной стопы. При этом она должна быть немного длиннее, форму носка выбирают в зависимости от модели.
Верх строится следующим образом:
- По результатам измерений создается форма, показанная на рисунке. Внешняя и внутренняя длины верха должны точно совпадать с длинами внешнего и внутреннего контура стельки.
- Вырез строится приблизительно, учитывая желаемую глубину от носка в направлении подъема. В процессе работы стоит примерять лекало на ногу — для понимания правильности действий.
- По выкройке обуви, ее верхней части, вырезается заготовка из натуральной замши или кожи.
Вырезать заготовку нужно на 2–3 мм больше, нежели сама выкройка. В таком случае при изготовлении обуви она не будет маломерить.
Подкладку кроят по той же выкройке обуви. Верхняя и подкладочная части сшиваются или склеиваются друг с другом. Края нужно максимально подровнять, обточить кожу при необходимости, подкрасить изделие, чтобы оно имело вид, максимально приближенный к желаемой модели обуви.
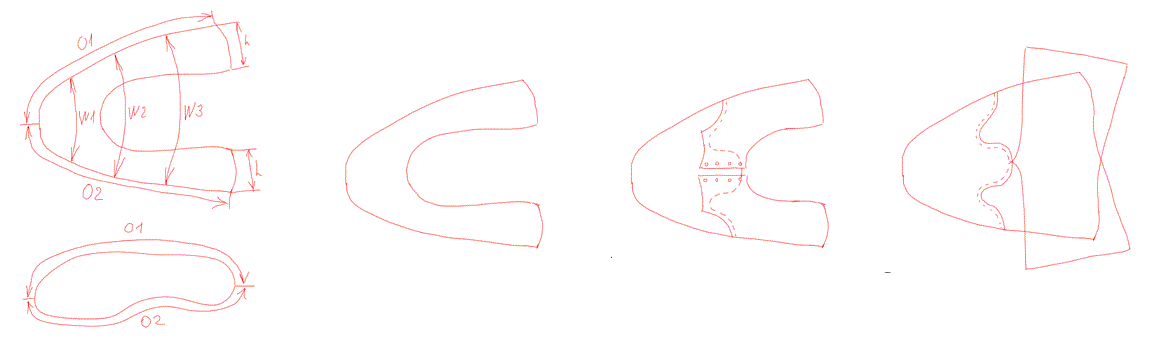
По результатам измерений создать форму
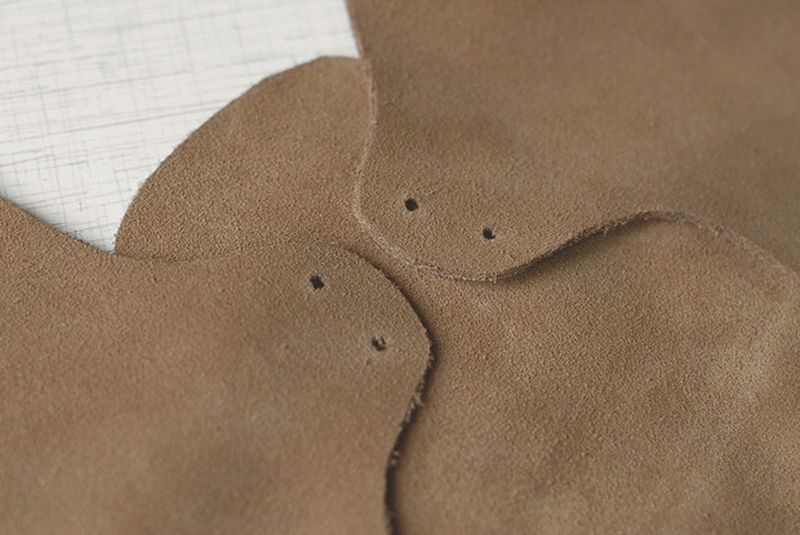
По выкройке вырезать заготовку
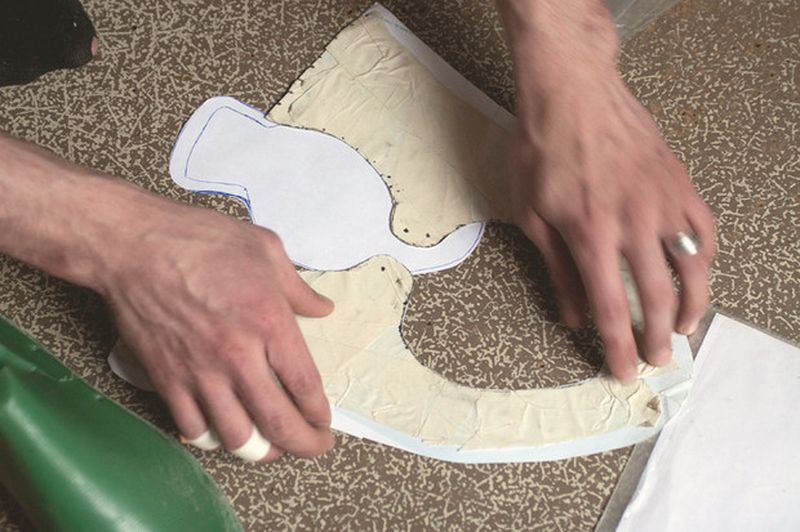
Вырезать подкладку, сшить или склеить с верхней частью
Натягивание заготовки и нашивка ранта
Изготовление продолжается: на подготовленную колодку нужно натянуть верх обуви, важно научиться это делать очень плотно. После чего надо уложить стельку. Этот этап производства особенно важен, от него будут зависеть удобство и комфорт при хождении.
Рант — это тонкая кожаная полоска, которая соединяет все части будущей модели, натянутые на колодку. Наличие этой детали позволяет ремонтировать любую модель в случае повреждения подошвы или колодки.
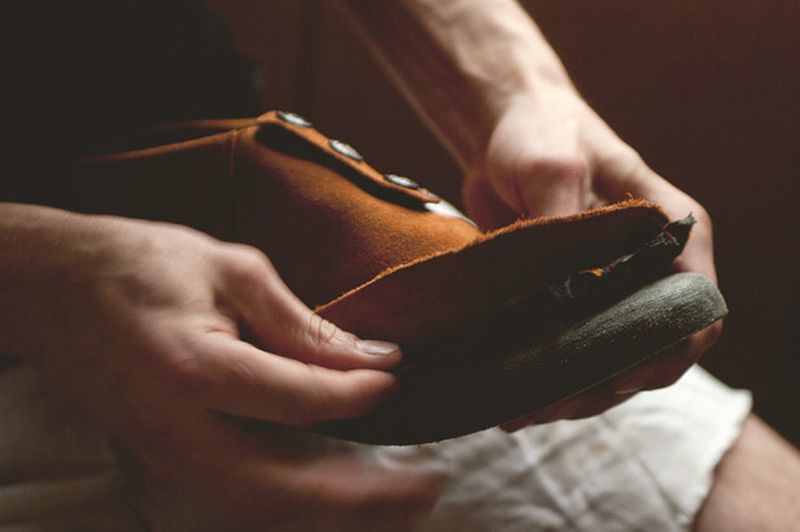
Натянуть верхнюю часть на колодку
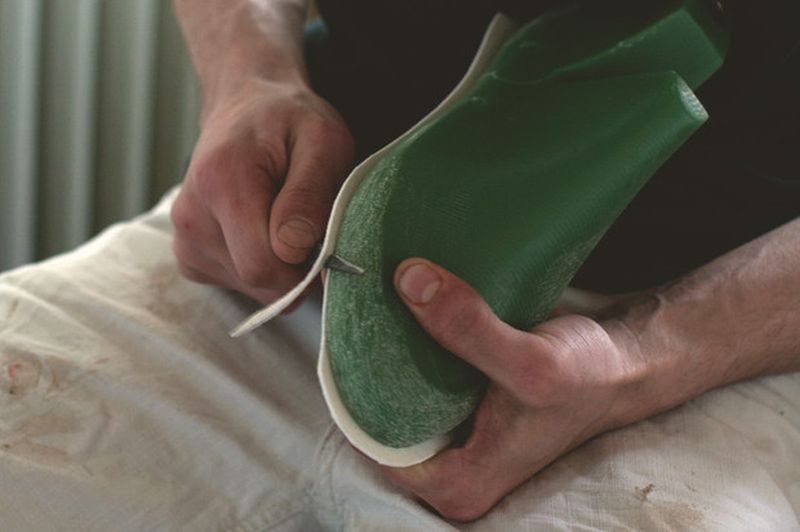
Заготовку для стельки подровнять сапожным ножом
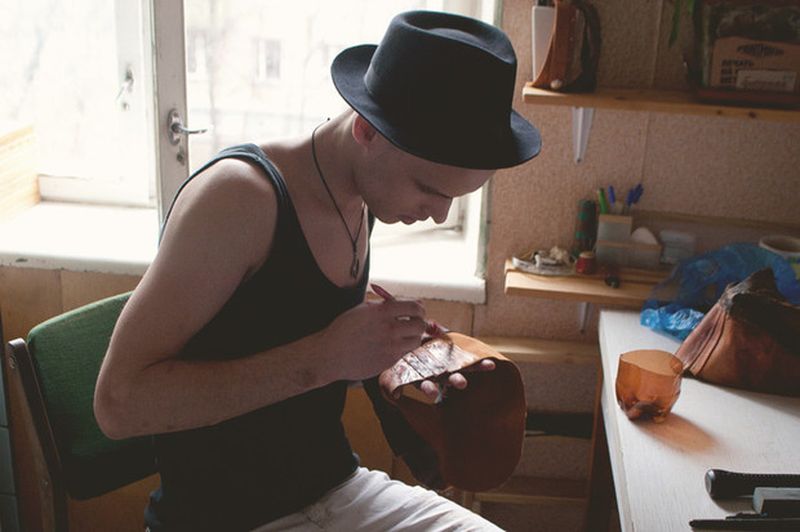
Место крепления стельки промазать десмоколом
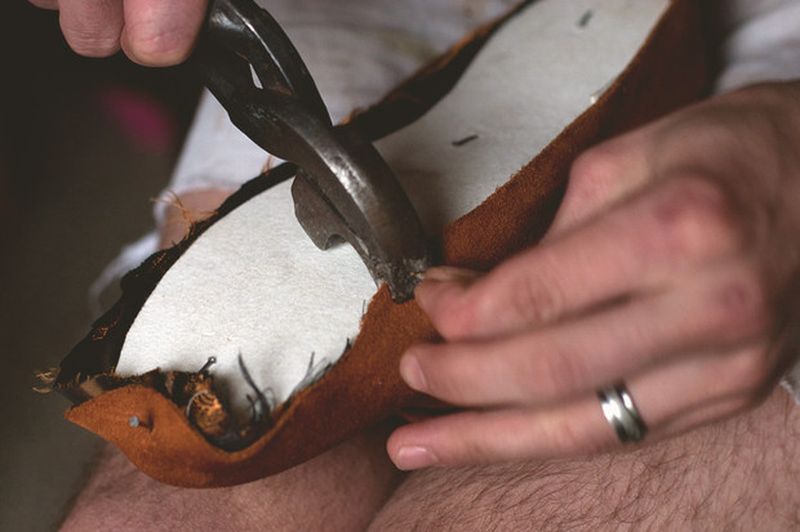
Прикрепить стельку
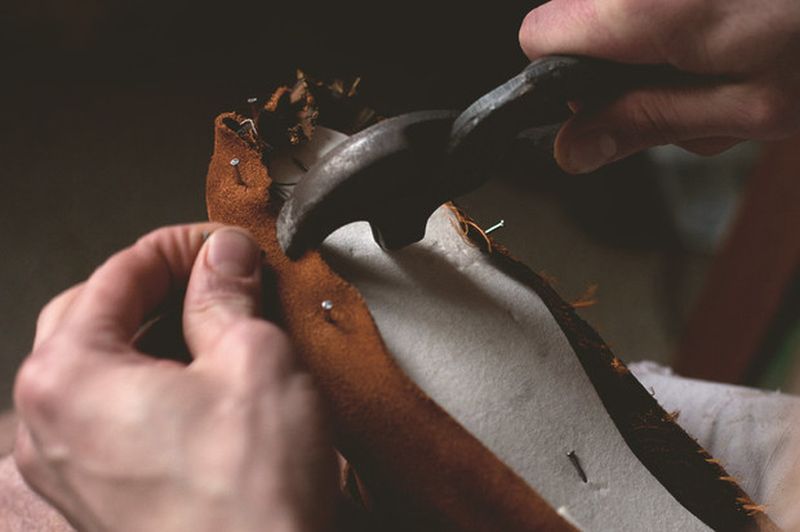
Зафиксировать заготовку обувными гвоздями
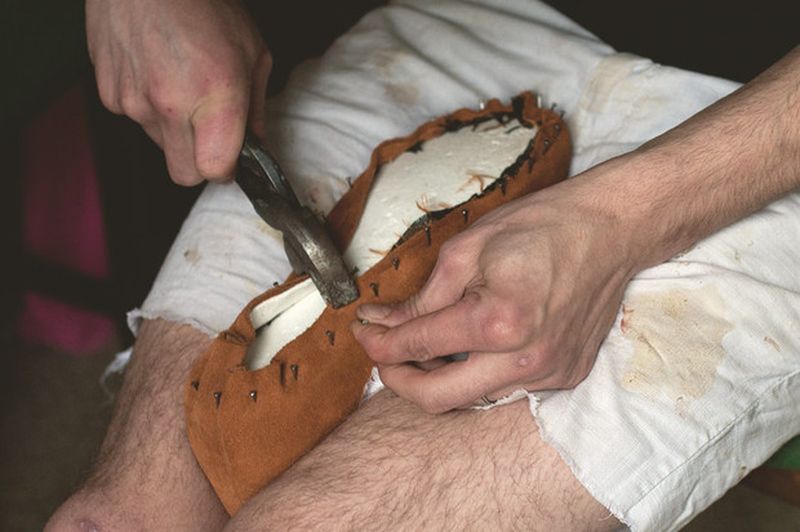
Продолжить работу затяжными клещами
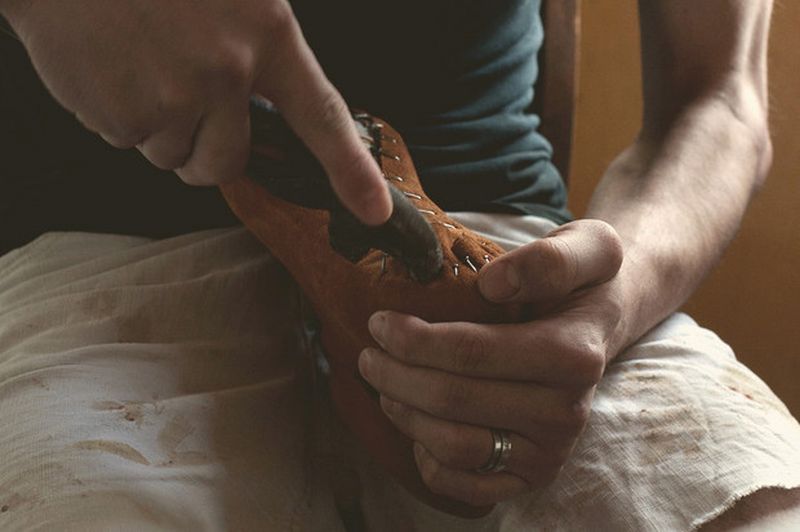
Подтянуть края заготовки как можно плотнее друг к другу
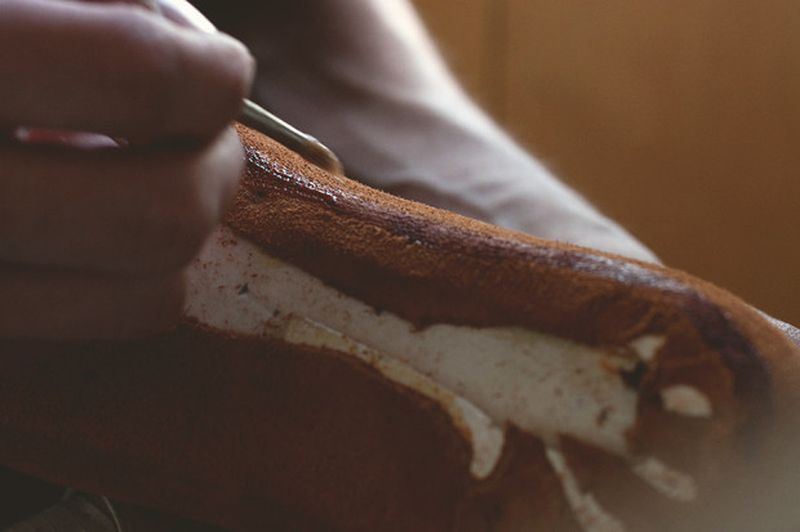
Вытащить гвозди, обрезать излишки замши
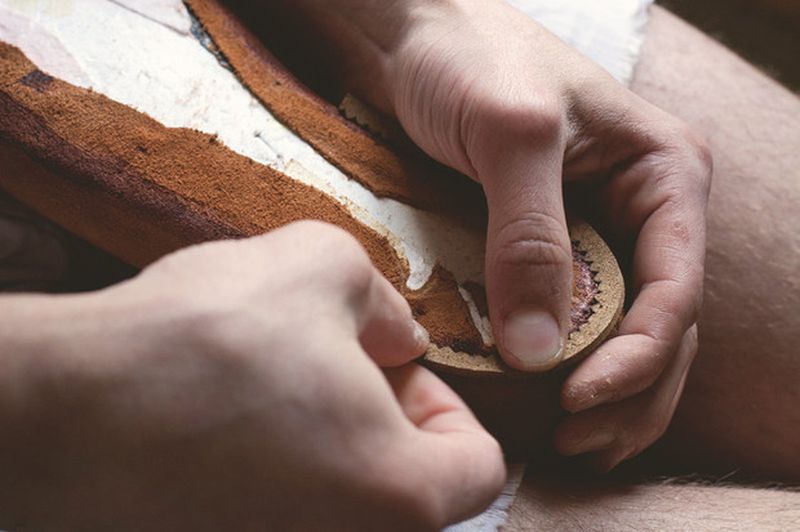
Приклеить декоративный рант из кожкартона
Пришивание, окрашивание и полирование подошвы
Подошва бывает разной, чаще каучуковой или кожаной. Укреплять ее нужно специальными маленькими гвоздиками, которые обеспечивают надежность и долговечность. Если нужно пришить каблук, используют несколько слоев кожи.
Недостаточно просто изготовить модель самому и сшить правильный макет, необходимо еще уметь профессионально окрасить подошву и отполировать ее. Цвет зависит от тона обуви. После нанесения краски нужно подождать, пока она полностью высохнет. Самостоятельное производство обуви заканчивается этапом полировки.
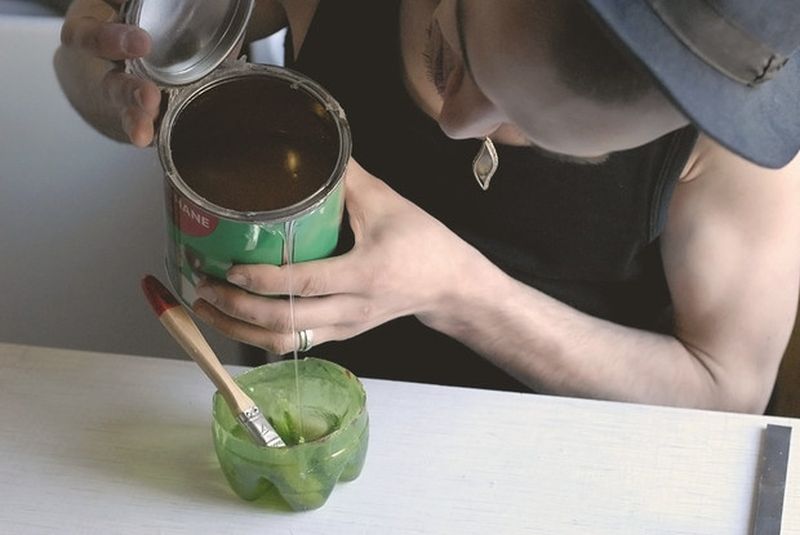
Отлить в небольшую удобную емкость клей
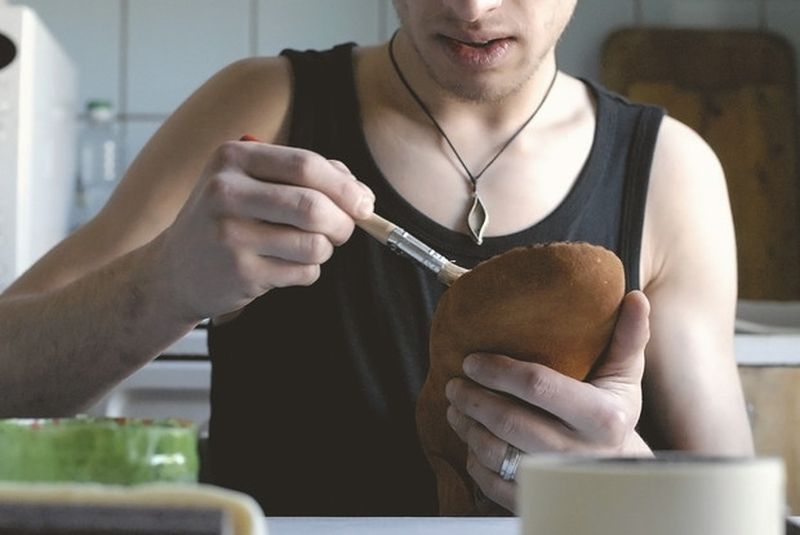
Промазать кисточкой нижнюю часть заготовки обуви
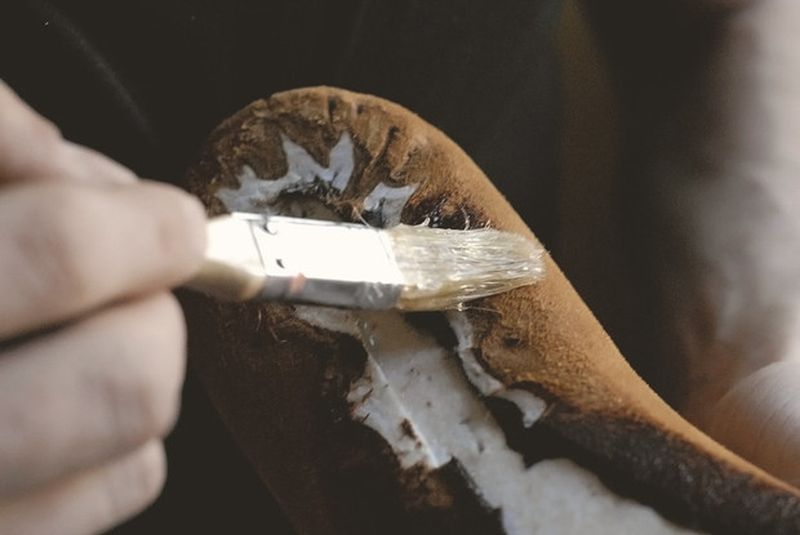
Уделить особое внимание складкам из замши
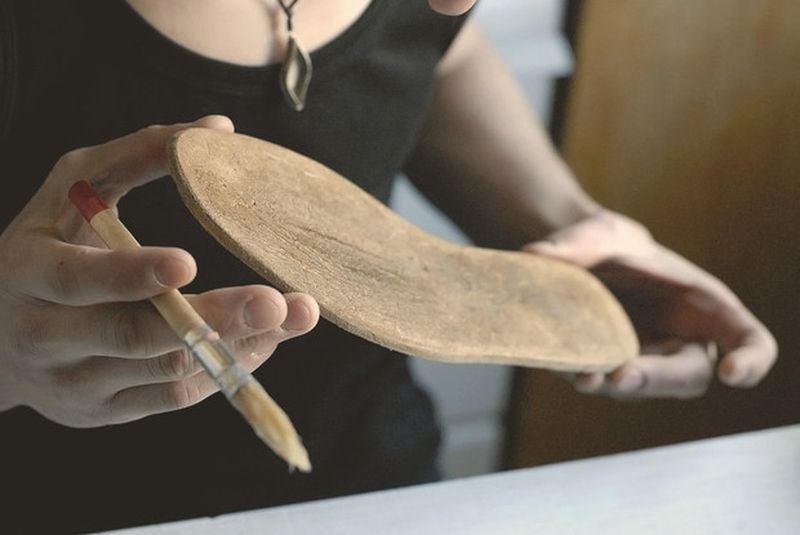
Подошву тоже обработать клеем
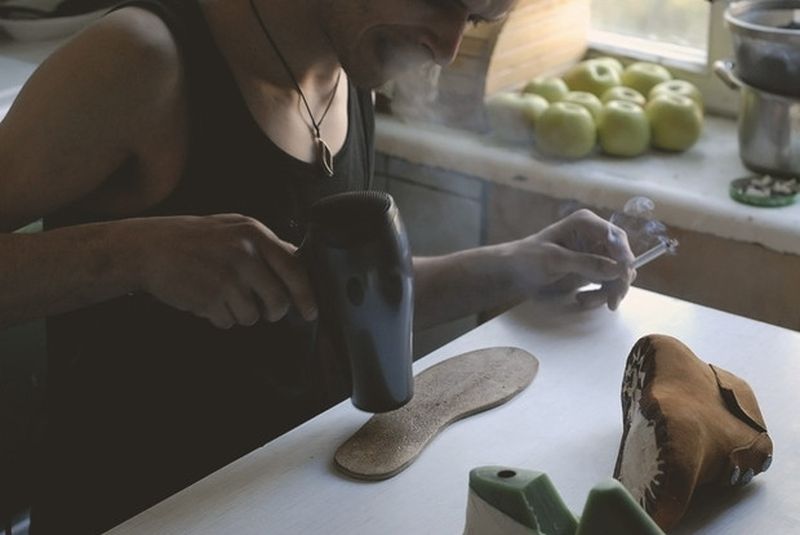
Прогреть феном для активации свойств клея
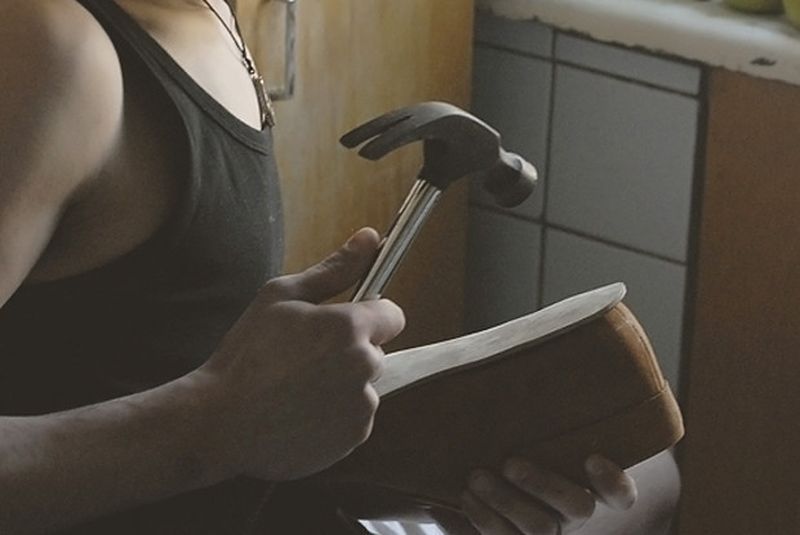
Подошву и заготовку плотно прижать друг к другу, отбить молотком для крепости сцепления
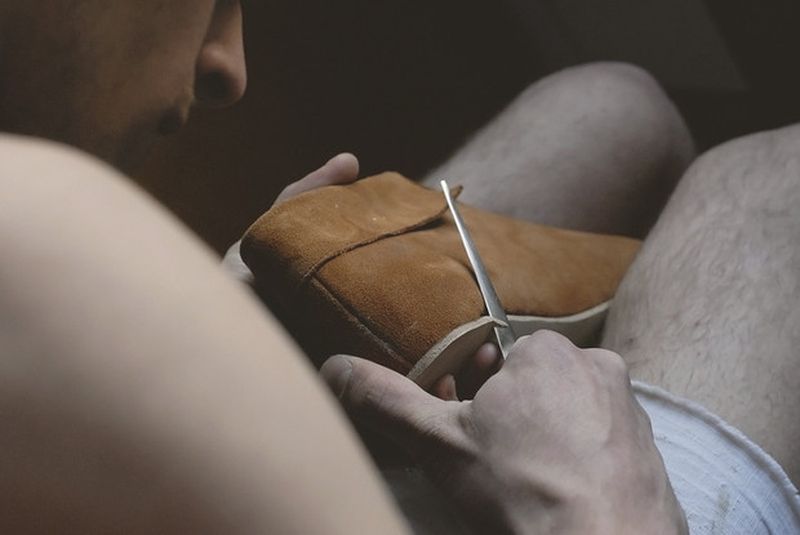
Сапожным ножом обрезать выступающие края
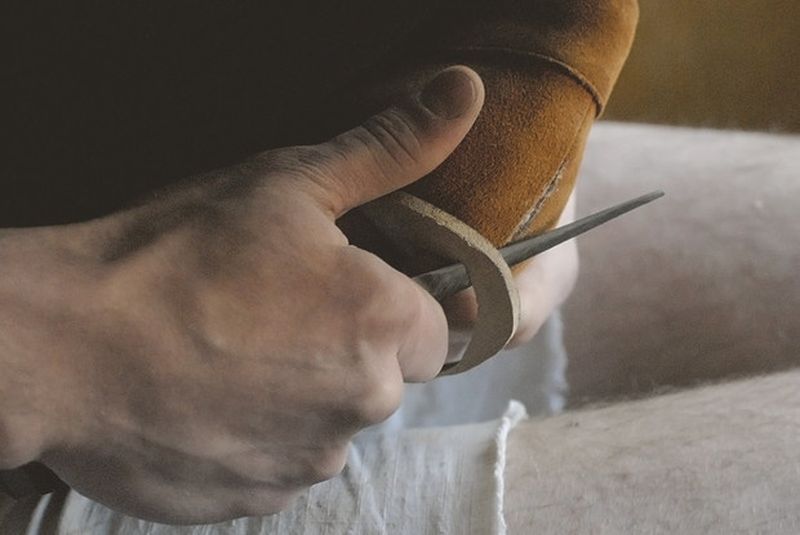
Действовать неспешно и аккуратно
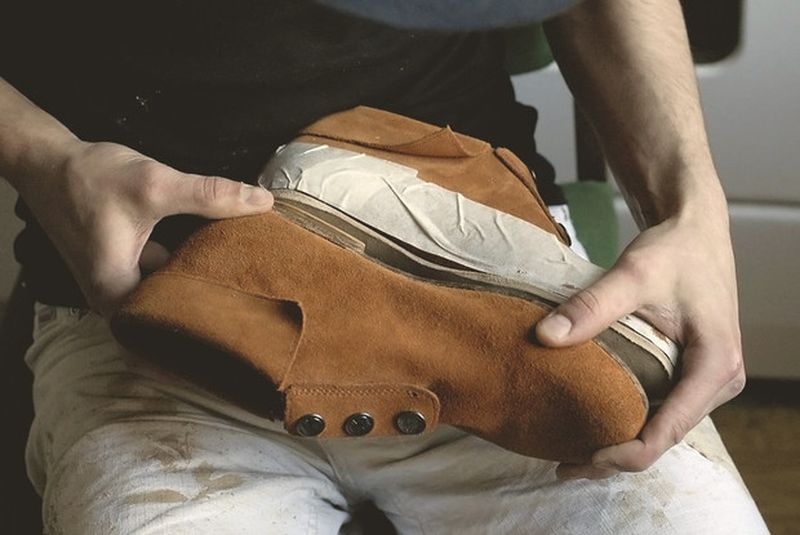
Следующий этап — изготовление каблука и набойки
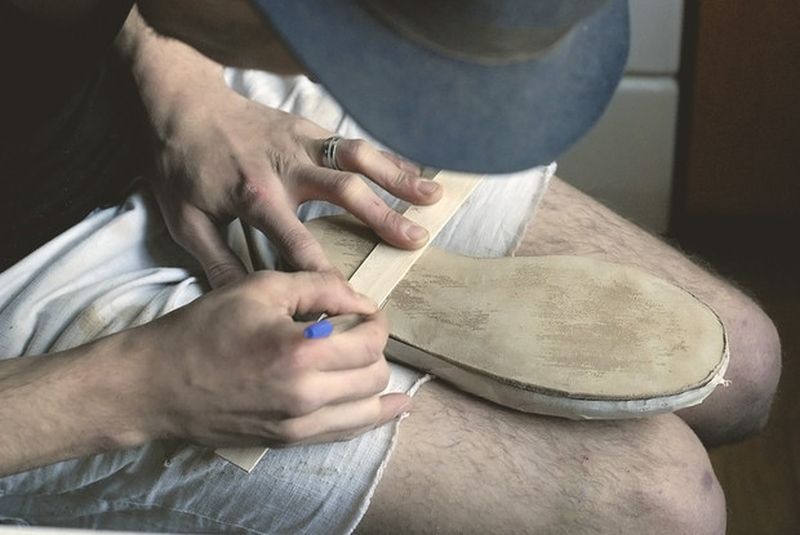
Сделать необходимые замеры
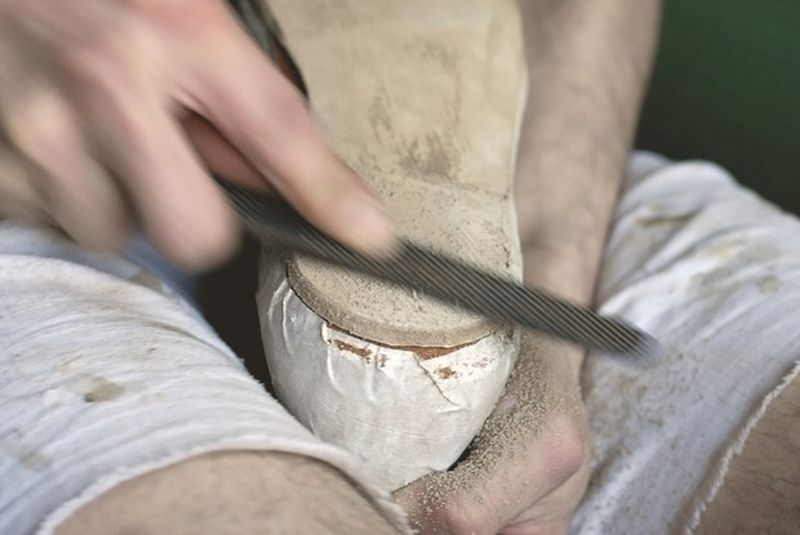
Отшлифовать область крепления каблука напильником
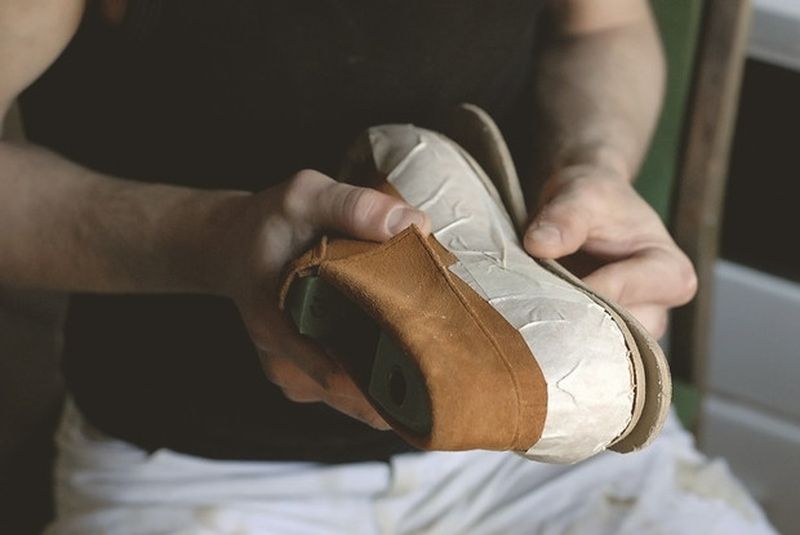
Выполнить примерку
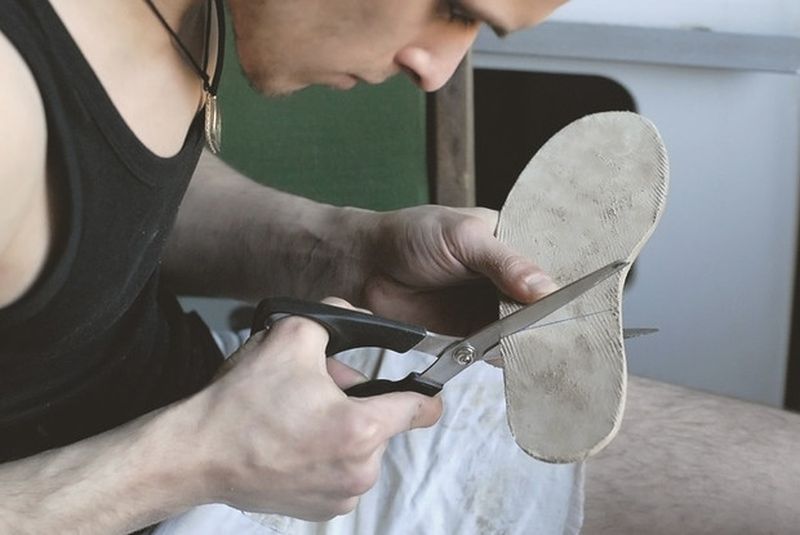
Вырезать каблук из той же кожи, что была использована для подошвы
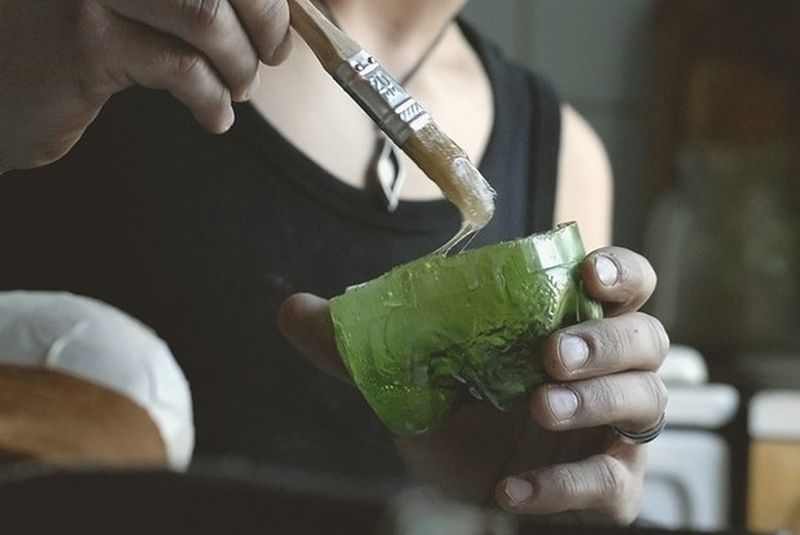
Макнуть кисточку в десмокол
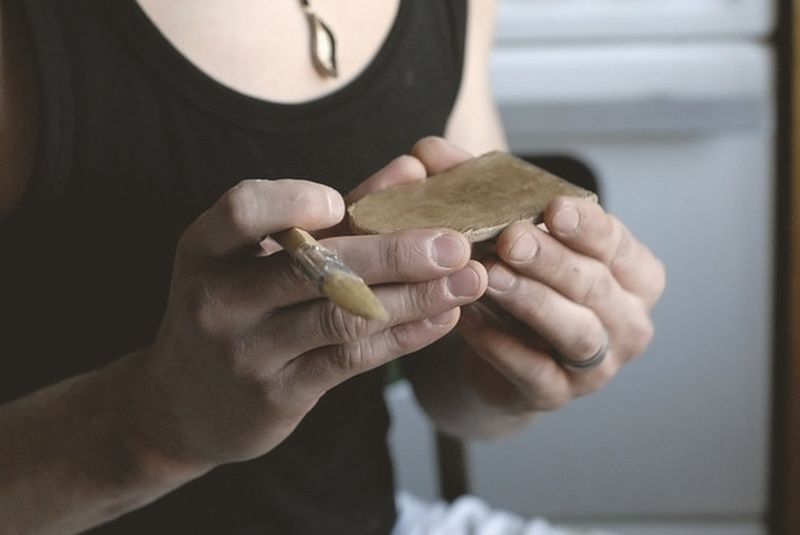
Щедро промазать каблук
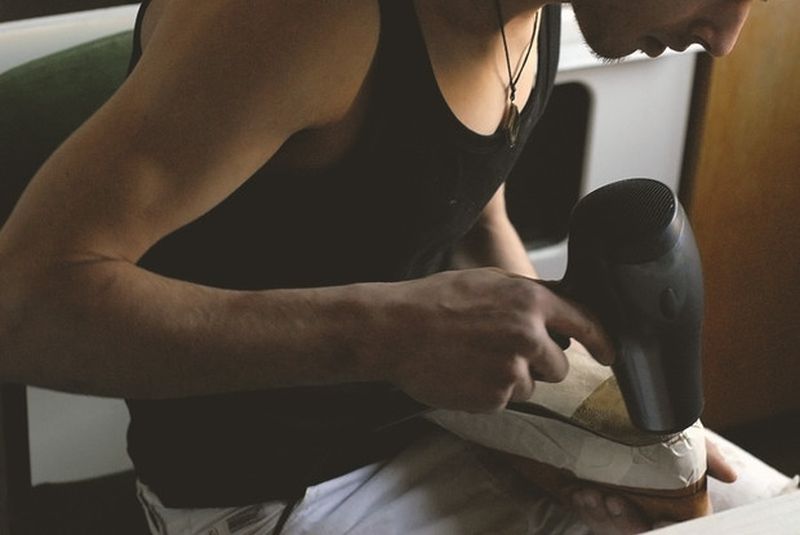
Приклеить и прогреть феном для активации клеящей пленки
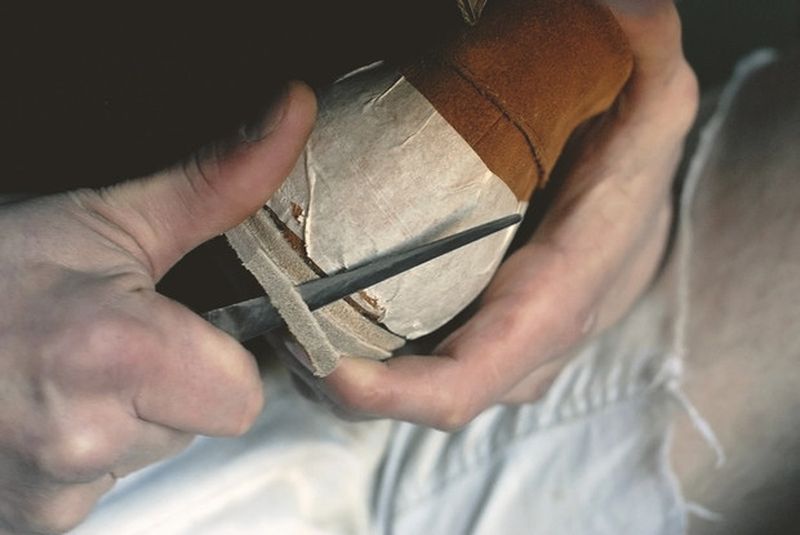
Обрезать края по форме подошвы
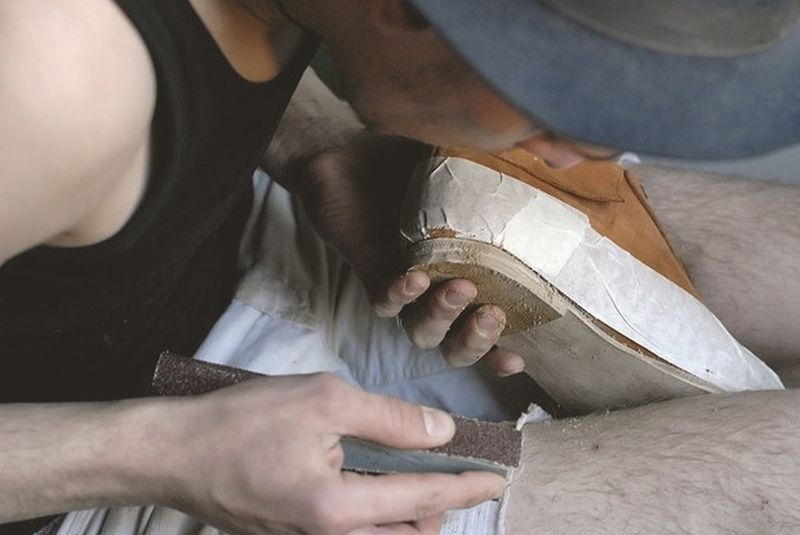
Отшлифовать
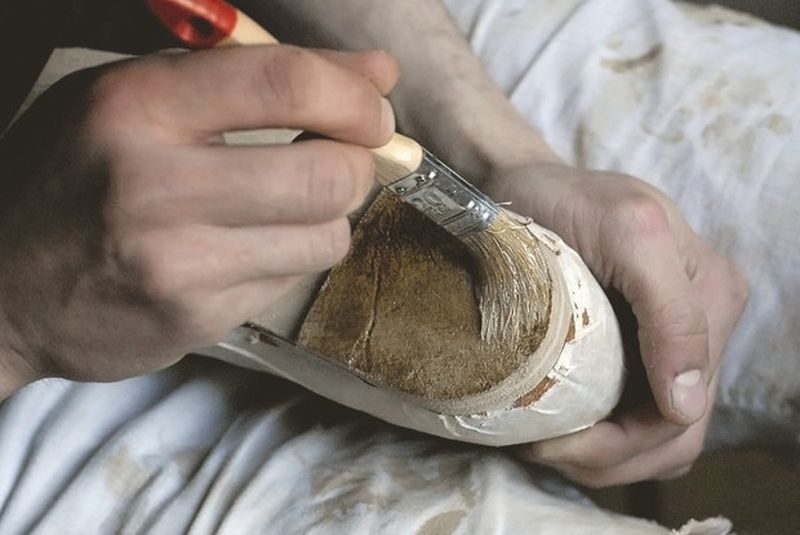
Нанести клей
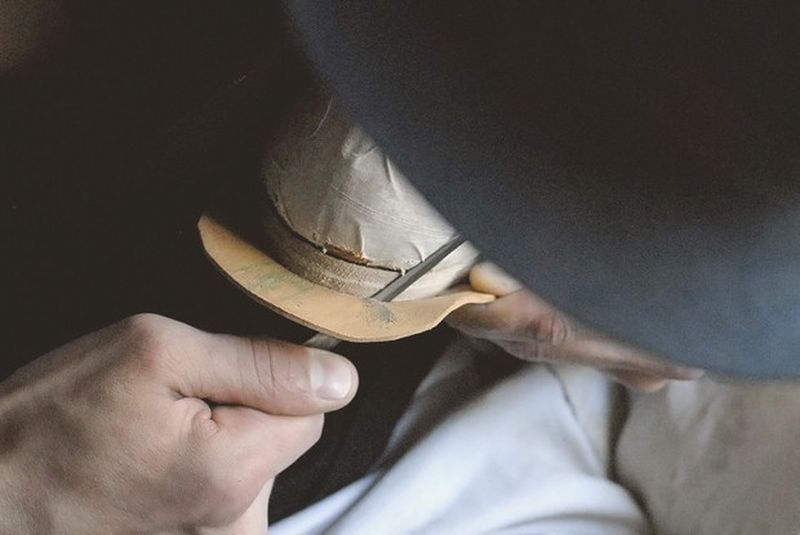
Приклеить набойку
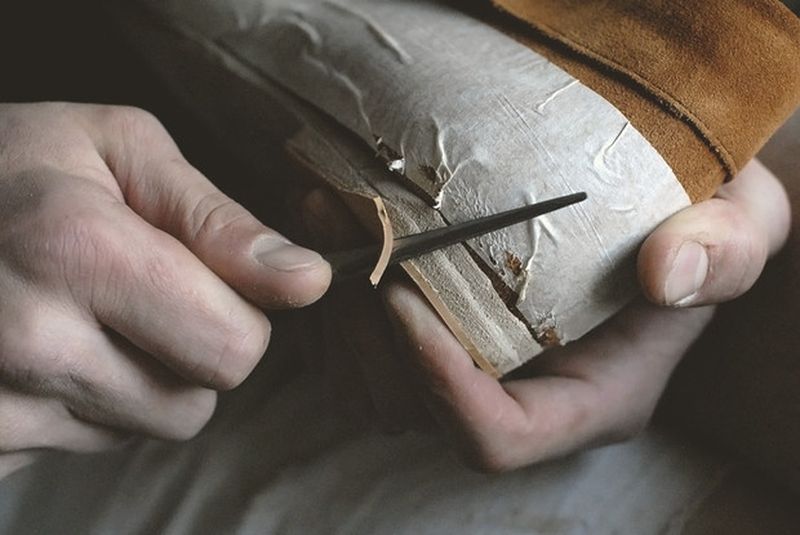
Придать ей нужную форму
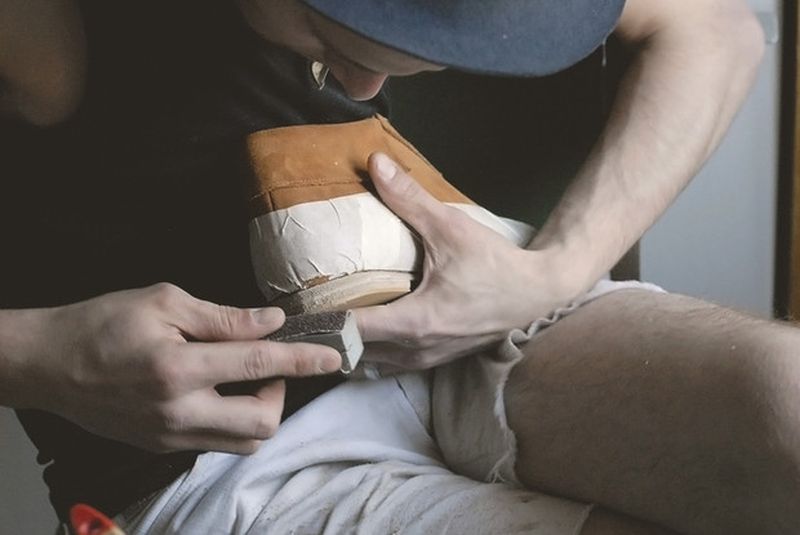
Отшлифовать края каблука
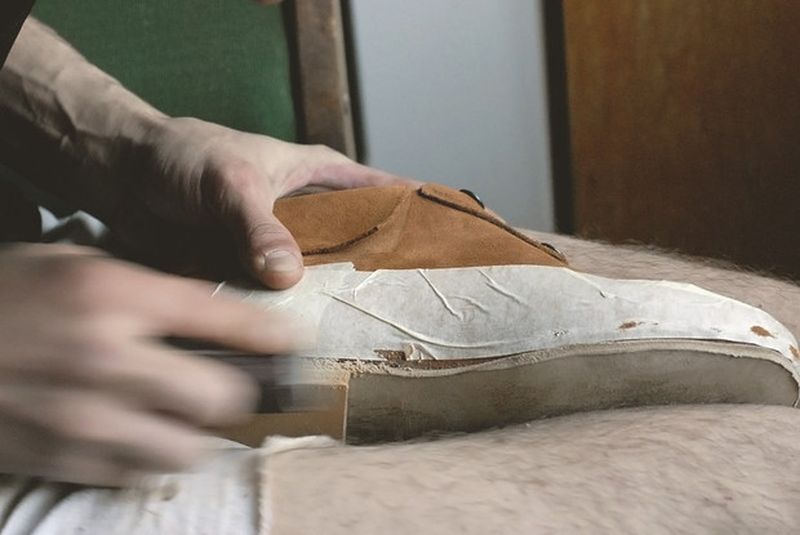
И рант подошвы
Декор
Самодельная обувь ручной работы может украшаться по фантазии мастера, используя различные стразы, банты, заклепки, кнопки и другие аксессуары. Для создания декора используют специальные инструменты. Чаще всего банты или стразы сажаются на клей, реже производители используют миниатюрные гвозди. Для домашнего украшения туфель оптимальным вариантом будет как раз сильнодействующее клеящее вещество, предназначенное специально для декорирования.
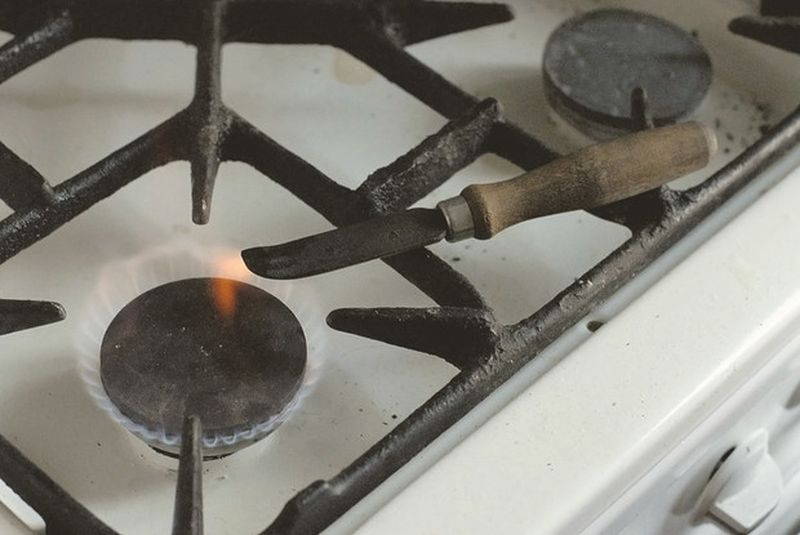
Накалить токмач
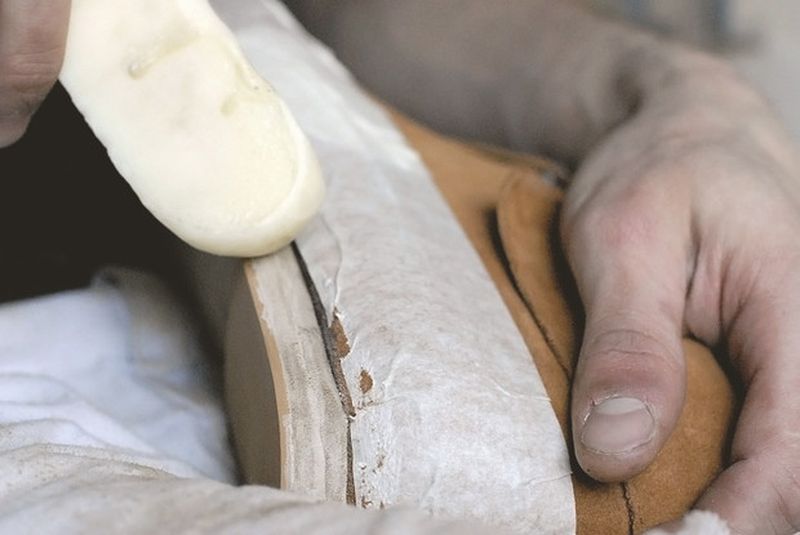
На рант подошвы нанести пчелиный воск
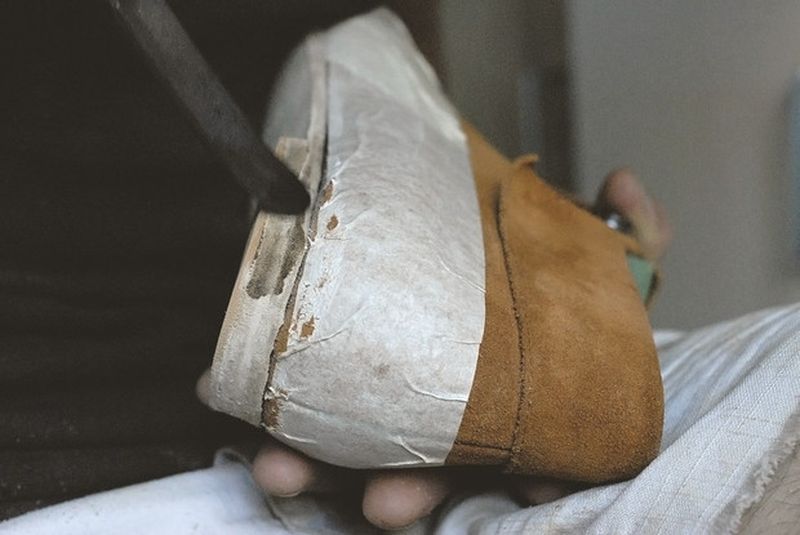
Вжарить воск горячим токмачом
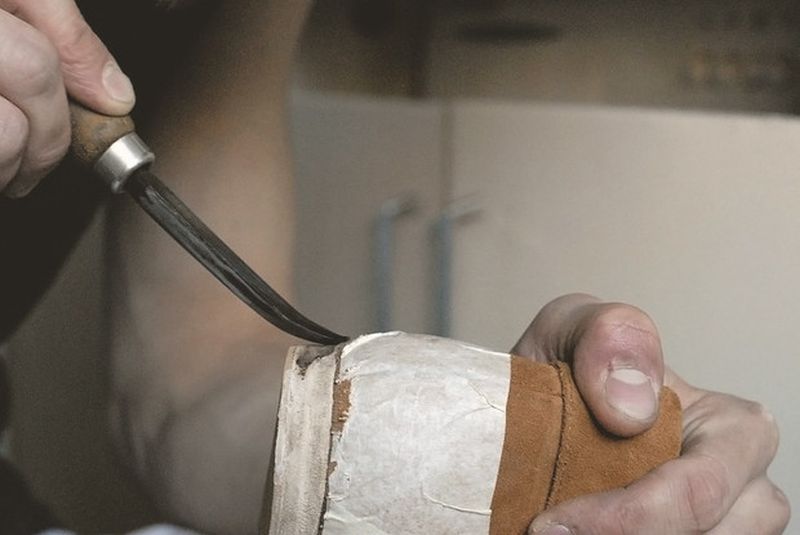
Двигаться по кругу
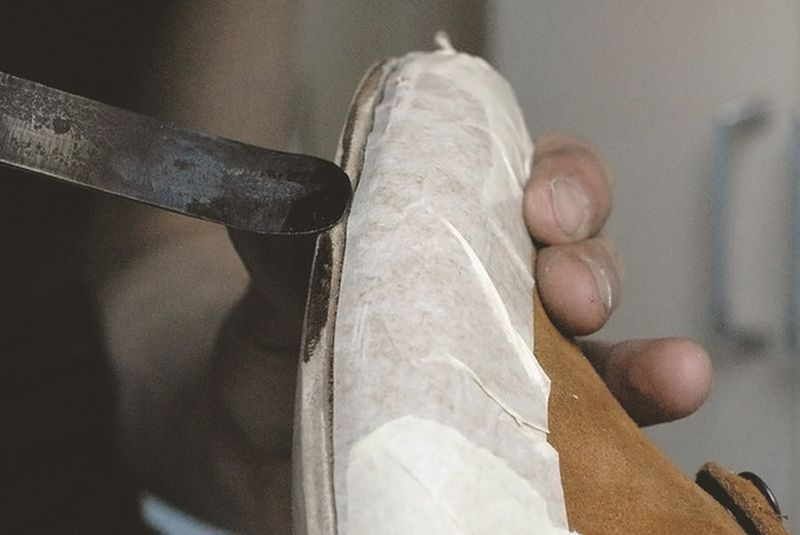
Не пропускать ни одного участка ранта
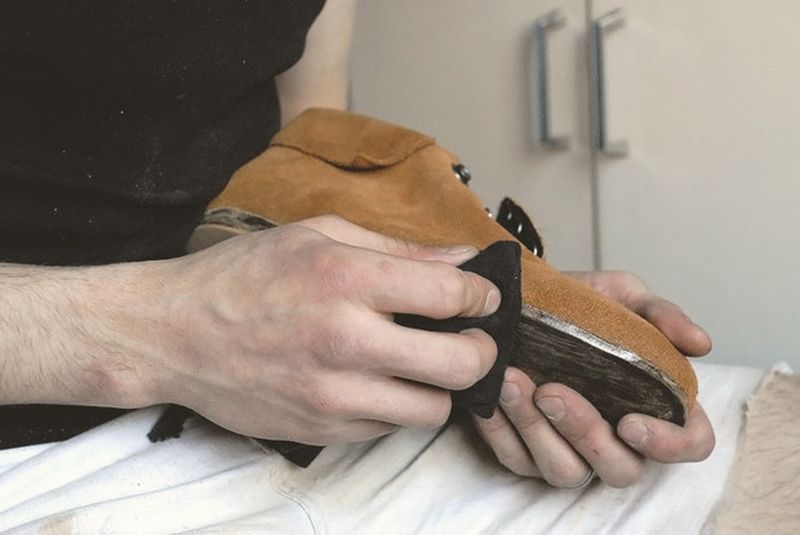
Взять кусок мягкой ткани
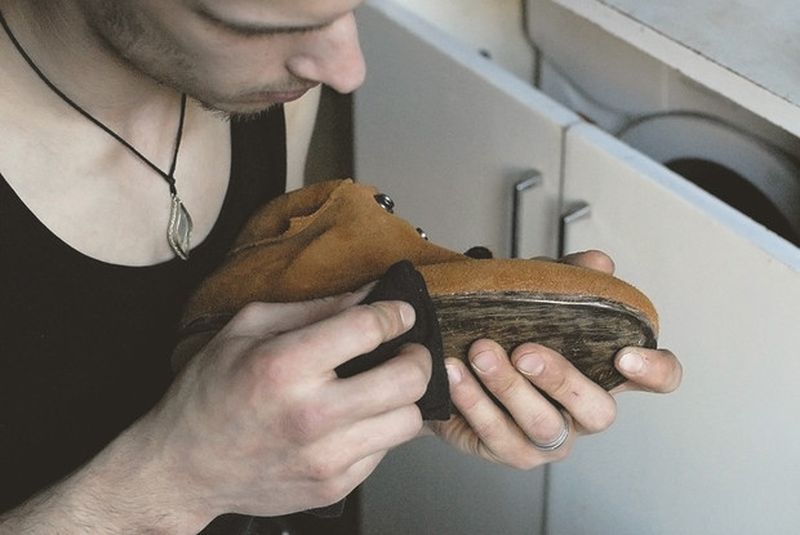
Отполировать боковую часть подошвы
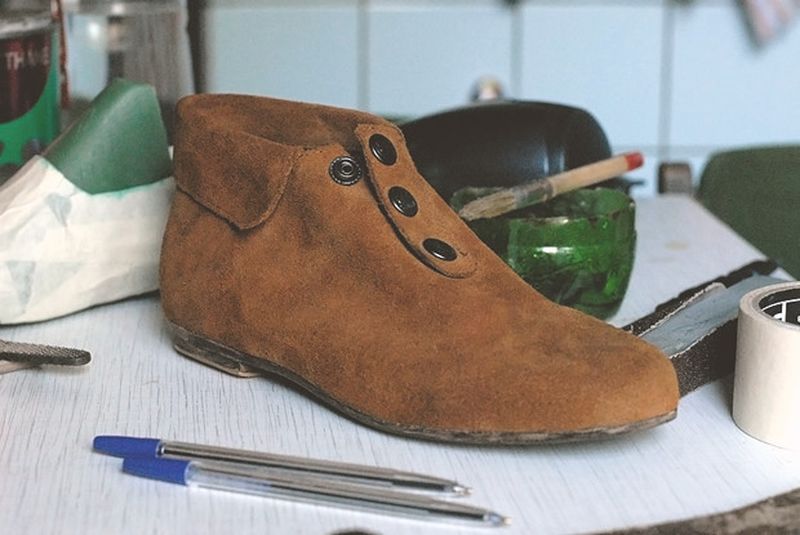
Готовый ботинок
Видео
obuv.expert
Обувь ручной работы: этапы производства
Туфли и ботинки, сделанные полностью вручную, встречаются сегодня очень редко и стоят дорого — примерно от 400 евро, если мы говорим о Венгрии, и примерно от 600 евро, если речь идёт о Западной Европе и более или менее известных мануфактурах. На производство такой обуви затрачивается много времени, но оно того стоит: у туфель полностью ручной работы, например, можно большее число раз заменять подошву; они немного по-другому выглядят, а зачастую ещё и более комфортны. В этой статье мы опишем ключевые этапы создания туфель ручной работы на ранту.
Оглавление:
Раскрой кожи
Естественно, кожа для обуви ручной работы кроится только вручную. Если речь идёт о пошиве обуви на заказ, то используются индивидуальные, специально созданные лекала для вырезания кусков кожи. Для готовой обуви используются стандартные лекала, обычно изготовленные из плексиглаза или другого современного материала.
Для раскраивания шкур обувщики используют нож-кликер, а сама эта процедура называется кликингом (clicking).
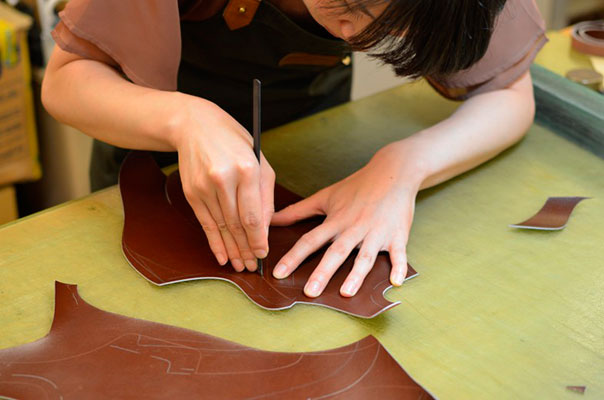
Перед выполняющим её работником стоит непростая задача: нужно использовать шкуру максимально рационально, отбраковав при этом все участки с дефектами. В случае с очень дорогой обувью, сшитой на заказ, используются лишь самые лучшие участки шкуры, причём многие шкуры отбраковываются ещё на этапе закупки.
Сшивание частей верха
На следующем этапе, который называется клоузингом (closing), вырезанные части кожи сшиваются друг с другом — и получается верх обуви.
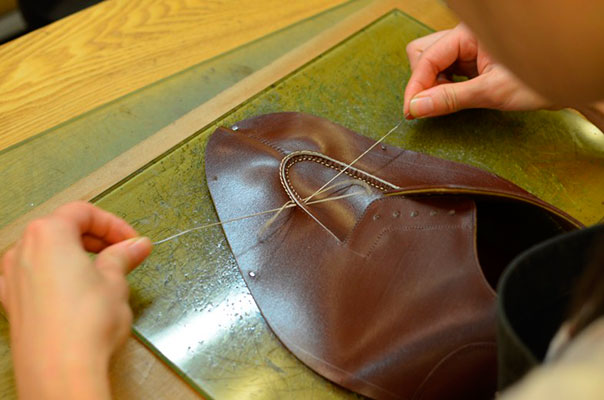
Помимо этого, верх сшивается с подкладкой, а также осуществляется декорирование отдельных частей верха — например, брогирование. На обуви полностью ручной работы брогирование делается вручную, без использования машин — и это занимает довольно много времени по сравнению с брогированием на фабричной обуви, где одна машина может делать дырочки одновременно на десяти кусках кожи.
Натягивание верха на колодку
Готовый верх обуви нужно натянуть на колодку, и эту операцию — ластинг (lasting) — делает ластер (laster). В случае с фабричной обувью ластинг обычно осуществляется полностью или частично с помощью специальных машин, что заметно сокращает издержки.
Как пишет немецкий эксперт по мужскому стилю Бернхард Ретцель, «ластер — это ремесленник, натягивающий кожу на деревянную колодку и временно прибивающий её гвоздиками. Позже, когда верх накрепко пришивается к ранту, гвозди снова вынимаются. Молоток часто намагничивается для облегчения манипуляций с множеством мелких гвоздей».

Стоит добавить, что раньше колодки изготавливались исключительно из дерева, но сегодня в ряде случаев даже для обуви на заказ (bespoke) используются колодки из пластика. У производителей готовой обуви имеются готовые колодки, а мастера, которые шьют заказную обувь, либо вытачивают колодки под клиента, либо используют готовые колодки разных размеров и форм, к которым по мере надобности прикрепляют в необходимые места куски кожи, чтобы добиться соответствия формы колодки форме стопы клиента.
Подготовка внутренней подмётки и пришивание ранта
Обувь полностью ручной работы часто шьётся с использованием ранта, причём этот рант пришивается вручную. Во внутренней подмётке (insole) вручную вырезается гребень, и после этого к нему и к верху вручную пришивается рант; сама подмётка тоже вырезается вручную. Это довольно трудоёмкая операция, и в случае с фабричной обувью сам процесс упрощают: гребень не вырезают в самой подмётке, а приклеивают к ней, используя заметно более тонкие подмётки (а сам гребень при этом сделан из текстиля). Рант к подмётке и верху на фабричной обуви пристрачивает машина, и делает это очень быстро.

Вырезание гребня на внутренней подметке

Сшивание ранта, гребня и верха обуви
В чем же заключается преимущество ручной работы на данном этапе? Знатоки говорят, что ручное крепление ранта (hand-welting) позволяет большее число раз заменять подошву; кроме того, hand-welted обувь при прочих равных оказывается более комфортной.
Пришивание подошвы и крепление каблука
После того, как рант соединен с внутренней подмёткой и верхом, на подмётку помещают пробковый наполнитель (cork filling) — это могут быть пробковые брикеты или же вязкая смесь на основе пробковой крошки.
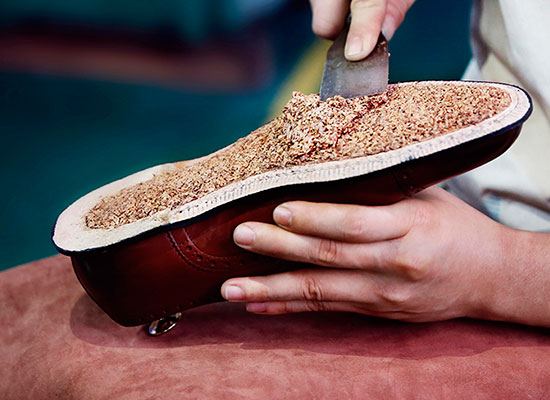
На следующем этапе — soling — рант сшивается с внешней подошвой (outsole).
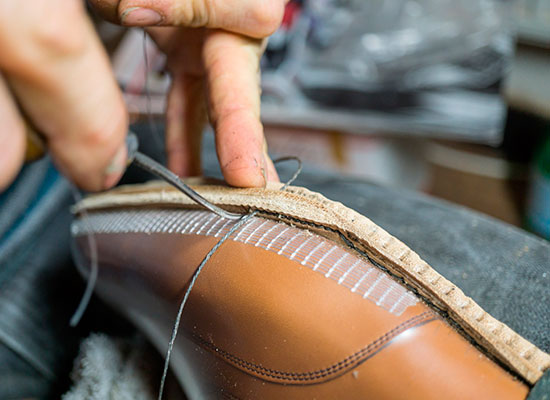
На обуви полностью ручной работы это делается вручную, иглой и нитью — такая операция трудоёмкая и длительная, и поэтому даже на hand-lasted и hand-welted обуви шов, соединяющий рант и внешнюю подошву, довольно часто выполняется с помощью машины. После крепления к верху «талия» (средняя часть) подошвы на туфлях ручной работы обычно изящно закругляется.
Далее осуществляется сборка каблука. На классических туфлях каблуки наборные — они сделаны из нескольких слоев кожи и резины, которые крепятся друг к другу и к подошве при помощи клея и маленьких гвоздиков. На сравнительно недорогих фабричных туфлях часто используются слои не из кожи, а из кожкартона — это обходится дешевле.
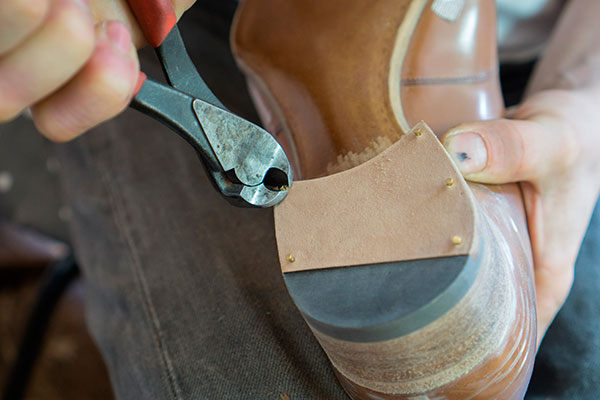
Финишинговые процедуры
После крепления подошвы и каблука туфли проходят ещё несколько процедур. В частности, ребро подошвы и каблука, и сами каблук и подошва шлифуются, вручную окрашиваются и полируются. Верх туфель вручную полируется, на него может наноситься уникальная патина с помощью красок и кремов.

Окрашивание каблука

Окрашивание верха обуви
Внешняя сторона подошвы и её верхний край иногда обрабатываются вручную зубчатыми колесиками. Затем в туфли вставляются стельки, обувь проверяют на отсутствие дефектов, после чего зашнуровывают и упаковывают.
string(0) «»
fineshoes.ru
Строительный фен для прогрева поверхностей смазанных клеями — десмаколом и найритом. | Бумажный скотч. Применяется для обклейки колодки при изготовлении лекал модели. | Клеевая тесьма. Применяется при подгибке кожи в швах вокруг горловины туфля для предотвращения их растяжения при носке и при отстрачивании на швейной машинке. |
Нитки №20 и №40. №20 — ставится на верхний шов (при сборке верха обуви), а №40 ставится снизу в челнок машинки. | Клей SAR-306 (полиуретановый) (Старое название — «Десмакол»). Применяется для приклеивания подошвы. При правильном склеивании достигается высочайшая сила склеивания. Оторвать кожу можно только после сильного прогрева (около 80 град.), когда клей плавится и теряет свою прочность. | Найритовый клей — найрит — это хлорпреновый клей. Желательно работать с вытяжкой, т.к. клей довольно резок по запаху, а также вреден для глаз (по-видимому немного разъедает слизистую оболочку глаза.) Желательно искать импортный заменитель найрита. Используется при сборке верха и деталей, не испытывающих больших нагрузок на разрыв. |
Этилацетат — универсальный растворитель для найритовых клеев и десмакола. Иногда он отсутствует в магазине (для обувных комплектующих), тогда можно приобрести отдельный растворитель для найрита и отдельно для десмакола. | Сатреат — протрава. Ею предварительно промазывается полиуретановая подошва, после чего подтравливается ее верхний слой, что позволяет десмаколу глубже внедриться в подошву. Значительно усиливает силу приклеивания подошвы | Кисточки для клеев и протравы желательно использовать качественные — итальянские, т.к. не вовремя выпадающие ворсинки раздражают и замедляют работу. Для хранения кисточек используется отдельная банка, на дне которой всегда налит этилацетат. |
Сапожный молоток — используется исключительно при затяжке обуви, т.к. полукруглая поверхность ударной части позволяет обстукивать сверху кожу, которую только что приклеили к подкладке, тем самым выравнивая под кожей неравномерный слой клея, и «измельчая» случайные пузырьки воздуха, оказавшиеся в клею. Ни в коем случае нельзя этим молотком забивать гвозди и повреждать гладкую поверхность молотка. | Шила. С деревянной ручной для кожи, а без ручки для бумаги при рисовании лекал и переносе линий с одного лекала на другое. Можно пользоваться одним шилом, т.к. в нем заменяются «биты». Обычно «битов» покупается с десяток — разные по толщине и назначению. | Самый главный инструмент — сапожные клещи. Используются в основном при затяжке, но, благодаря своим малым габаритам, зачастую применяется в качестве обычного молотка. |
Щипцы — в основном применяются для выдергивания гвоздей из колодки, но частенько нужны и для других работ — очень необходимая вещь | Плоскогубцы с узкими и длинными губами — применяются при затяжке, чтобы добраться до самых узких складок между гвоздями, куда обычные клещи залезть уже не могут. | Ножницы для кожи и тканей. Не режьте ими бумагу, т.к. быстро от бумаги тупятся. Бумага это почти дерево, только тоненькое 🙂 |
А вот этими ножницами можно резать бумагу, но и кожу тоже ими удобно подрезать, особенно во время затяжки образуются иногода лишнии шмотки кожи, которые удобно подрезать маленькими ножницами. | Фигурные ножницы для кожи. Иногда на туфлях используется рифленый открытый срез кожи. Для этой цели и применяются эти ножницы. | Канцелярка — все что нужно для изготовления лекал. На розовой линейке лежат 2 стержня специально предназначенных для кожи (продаются исключительно в магазине обувных принадлежностей). Они оставляют серебристый цвет, который затем стирается салфеткой, слегка смоченной каким нибудь маслом, либо специальным затирающим маркером, который этот карандаш удаляет. |
Штангенциркуль — необходим при точении колодок и при подгонке левой колодки под правую. | Отвертка — применяется для завинчивания и вывинчивания шурупов из колодки при ее сборке и разборке. | Электродрель — применяется для сверления отверстий в колодках, для дальнейшего завинчивания в них шурупов. |
Электролобзик — применяется при выпиливании овальных слоев будущей колодки из строганной доски. Также удобен при изготовлении всевозможных стеллажей, ящичков и т.д. | Заточные бруски — один грубый для подводки вогнутых щечек ножа — для этого именно применяется брусок с овальными боками. Второй — самый тонкий брусок — для окончательной тонкой заточки режущей кромки. Бруски при работе должны быть мокрыми, поэтому хранятся вместе со своей пластиковой банкой. | Набор ножей для работы с кожей. Самый верхний — для картона и толстой стелечной кожи. Средний — чисто брусовочный нож (Применяется только для утоньшения торцов кожи. Он натачивается перед каждой парой обуви до остроты бритвы, и во время работы подводится на ремне 2-3 раза). Внизу нож для резки и подрезки обычной кожи. Ему не обязательно быть острым как брусовочному ножу, поэтому режущая кромка у него поуже. |
Обычный кухонный нож из нержавейки. Применяется для грубого обстругивания колодок. Несмотря на свою дешевизну, обладает невероятно прочной сталью. Одной хорошей заточки хватает для обработки 2-х пар сосновых колодок. | Вот такой значок на этом ноже. Очень достойная марка — купите — не пожалеете. | Сапожные гвозди. Длина 2,5 см. При покупке возьмите щепотку в руки и убедитесь что не встречается «росщип» — это когда на кончике гвоздя остаются кусочки металла. Такие бракованные гвозди быстро выведут колодку из строя. |
Рашпиль — применяется для шлифовки кожи после затяжки, когда необходимио подровнять затянутую снизу колодки кожу от остатков срезанных складок. | Зажигалки — применяются для отжига разлахмоченного края кожи после отрезки ножницами, а также для отжига узелков толстой нити, когда вручную шьются мокасины или прошивается подошва. | Два типа наждачной шкурки для обработки краев и складок гранитоля (который применяется для укрепления задника и носка туфля). |
Одежная щетка — поможет быстро смести мусор с поверхности стола, что часто бывает нужно при переходе от одной операции к другой. | Кусок мраморной пластины толщиной от 2 до 3 см. (Можно приобрести в мастерской по изготовлению памятников) Применяется при брусовке кожи, когда утончается край кожи. Для этой операции нужна идеально горизонтальная поверхность, по которой легко скользит нож. Также применяется при отбивке стыковых швов (когда 2 куска кожи сшиваются встык, а не внахлест). | Катушка для толстой нитки. Обычно толстая нитка продается в больших катушках, которую невозможно приспособить к бытовой машинке, поэтому приходится вытачивать более компактную высотой 7-8 см. Можно и меньше — на любителя. (Именно эта сделана из черенка от лопаты) |
Струбцины. Маленькие применяются при склеивании колодки, а большая при приклеивании подошвы, чтобы подошва не съехала с нужного положения и не оказалась перекошеной. Т.к. при приклейке подошвы невозможно будет исправить ошибку, т.к. десмакол хватает мертво, поэтому подошву нужно заранее, до разогрева клея тщательно выставлять и прижимать за каблук струбциной, после чего прогревать носок и клеить сначала носок, потом пятку. | Штырь. Для тех, кто не захочет точить колодки самостоятельно, а будет пользоваться покупными понадобится при вытаскивании колодки из готового туфля. Т.к. пока ее не сложишь книжкой колодка фабричная из туфля не выйдет. Самодельная колодка разбирается с помощью шурупов и легко без проблем выходит. | Штырь вставляется в специальное технологическое отверстие наверху колодки и за длинный рычаг давится в сторону носка и колодка складывается и выходит из ботинка или туфля. |
obuv-svoimi-rukami.ru
Этапы изготовления (производства) обуви | ПромЭлектроАвтомат
Рубрика: СтатьиНа сайте ПромЭлектроавтомат собраны описания множества машин для изготовления обуви. Однако, для тех, кто в этой области работает или учится недавно, трудно составить сразу единую картину.
Поэтому в данной обзорной статье “пошагово” рассмотрим, как производится обувь, с научно-популярной точки зрения. Можно сказать, что мы “прогуляемся” по цехам обувного предприятия, и посмотрим, что там происходит.
Неотъемлемой частью гардероба любого человека является обувь. Она необходима нам и жарким летом, и холодной зимой, в уютной домашней обстановке и за пределами дома. Прежде чем оказаться на прилавке обувного магазина, каждая пара должна пройти непростой путь от первоначальных идей модельера до готового изделия.
Идея – проект – лекала
При создании удобной стильной обуви немаловажным является концептуальная идея будущей пары. Модельер, вооружившись новейшими тенденциями в области обувной моды, создает эскиз-проект будущей пары обуви.
На данном этапе помощь модельеру оказывает специалист–технолог, который на основе знаний о строении и усредненных мерках стопы изготавливает колодку для новой модели.
Готовый дизайн-проект помимо изображения, колодки и рекомендаций относительно материалов, из которых будет изготовлена обувь, содержит всю необходимую информацию для цеха раскройки и цеха пошива, а именно лекала-трафареты новой модели и описание технологического процесса пошива.
Прежде чем модель будет запущена в производство, изготавливается первый опытный экземпляр новой обуви.
Раскрой новой модели – дело тонкое
Изготовление, а именно пошив новой модели начинается с цеха раскроя, или раскройного (вырубного) цеха .
Здесь из кожи, прошедшей специальную обработку, с помощью трафаретов и вырубочных прессов вырезаются все требуемые заготовки для данной модели. Помимо деталей верха модели вырезаются и части внутренней отделки. Здесь же выкраивается стелька для будущей пары.
Помимо выше описанных операций на данном этапе проводиться разметка, суть которой заключается в отображении линии предполагаемых швов на деталях будущей пары обуви. Завершает этот этап технологического процесса специальная обработка краёв деталей, благодаря которой они немного истончаются и приобретают нужную толщину, что позволяет легко работать с заготовками в дальнейшем.
Качественный пошив – залог успеха
Прежде чем попасть в затяжной цех, заготовки обуви поступают к специалистам, подготавливающим детали для сборки. Это происходит в швейном цеху, где с помощью специальных швейных машин скрепляются подготовленные в цеху раскроя детали обуви.
В состав швейного цеха также обычно входит оборудование, где заготовки выравниваются, дублируются прокладочными материалами и последовательно склеиваются в соответствии с технологической картой.
Затяжка верха обуви
После окончательного соединения всех деталей кожаного верха и подкладки заготовка фиксируется на стельке при помощи обувной колодки. Это происходит в затяжном цеху. На специальных затяжных машинах мягкий верх обуви соединяется со стелькой. Также проводятся дополнительные операции, позволяющие на заключительном этапе качественно закрепить подошву.
Крепление подошвы
Обычно, для крепления верха обуви к подошве используется клеевой, ниточный или гвоздевой метод крепления. Эти операции проводятся в сборочном цеху. При этом используется подошва, которая может быть получена с другого предприятия.
Литьевой цех
Более современным способом изготовления и крепления подошвы является литьевой способ. В литьевом цеху на верхе обуви со стелькой фиксируется подошва путем прямого прилива резины либо полиуретана.
Упаковка
Перед упаковкой готовой пары с нее срезаются излишки материала (облой), а поверхность обрабатывается специальными восковыми составами и полируется. Обувь сделана – остается только запаковать и отправить коробки с обувью на склад.
Дополнительно
Процесс пошива обуви подробно показан на видео, которое предоставил Иван Яковлев:
Более подробно про технологию производства обуви стоит почитать в разделе Технология обуви, или Статьи.
Литературу по обувному оборудованию и обувной технологии можно скачать здесь.
Интересное по теме:
Пожалуйста, оцените статью!
www.promelectroavtomat.ru
Пошив обуви вручную: vizioner25 — LiveJournal
В этом посте я расскажу как начиналось и выложу фотоисторию последнего проекта.Когда 2 года назад я решил развивать новое хобби, то столкнулся с несколькими проблемами:
1) на русском языке информации об этом ремесле нет вообще, а если есть то в основном описываются устаревшие методы работы;
2) найти русскоязычных специалистов через интернет практически невозможно, потому что основной массив людей, которые умеют это делать уже приклонного возраста и им не до интернета;
3) купить инструмент вообще проблема, так же как и материал.
Долгие поиски привели меня к нескольким мастерам, с которыми я общаюсь до сих пор. Эти люди активно помогают, да и вообще классные ребята. Средни них — Олег Заремба из Киева, мастер очень высокой категории, его работы просто фантастика!
Здесь можно посмотреть небольшую презентацию работ (фото с fb) http://www.youtube.com/watch?v=YpvZ9kS5Mx4
А в России я общаюсь с Андереем Кавешниковым. Он так же как и я давно загорелся этим делом и весьма преуспевает в нем, правда периодически просит за советы закинуть «пятихатку на мобилку», ну или «соточку» :)) Ну, это юмор конечно у нас такой (Андрюха, не обжиайся). Андрей живет в Москве и часто помогает с покупкой материалов или инструмента. Вот его страничка в вк http://vk.com/id957804
Сейчас круг знакомств расширяется и в принципе становится проще.
В фейсбуке есть хорошее сообщество, где общаются наверно почти все европейские и американские ремесленники.
Во Владивсотоке я нашел хорошего человека и мастера из области ремонта. Вместе с Виктором Ивановичем мы учимся и пробуем новые технологии, спорим и обсуждаем о разных процессах. Вообще повезло, что здесь есть человек, которому тоже интересно. В свое время я зашел почти в каждую мастерскую по ремонту обуви с просьбой помочь — везде приклеили бороду, кроме отелье «Петелька» в центре. Поэтому если вам нужен качественный ремонт обуви — идите туда. Там спец с тридцатилетним опытом работы:)
Вот такая фабула. Далее я покажу фотки с процессами последнего пошива. Я пока учусь и мне далеко до совершенства. Каждая пара — это опыт, ошибки, позитив и работа. Пока не было проектов, которыми я 100% был бы доволен. В процессе описания каких-то процессов у меня могут быть ошибки (это для снобов «мастеров). Просто у меня есть цель в этом направлении и пока не добьюсь ее — не отступлю. Надеюсь, что эти картинки будут интересны новичкам и вообще всем, ведь это ремесло только начинает возрождаться в нашей стране.
Цель была такая — попробовать новый метод сборки, да и фасон «дерби» еще раз попрактиковать, так как Кавешников А. меня постоянно троллит оксвордами 🙂
Метод сборки называет Strom welt, картинка ниже:
В общем, обычно я пользовался верхним способом — когда рант (welt) уходил под затяжную кромку. Сейчас же я хочу оставить его снаружи, пришив де просто строчкой, а декоративной строчкой, так называемой «косичкой» (goiser stich).
Фото косички (не мое, для примера, мое будет ниже):
Итак, процесс пошел:
Делаю лекала
Перфорирую вручну
Исрпользую специальную серебрянную ручку, легко стирается и хорошо видна. Вырезаю ножом
Для зигзага использую ножницы, сейчас ищу меньший размер
Тоже самое делаю с деталями подклада, а справа лежит материал на межподклад, так как кода верха мягковата, нужно уплотнить
Помечаю линии для строчки
Под перфорацию подкладываю кожу, чтобы сохранить цвет
Приклеиваю межподклад и прошиваю детали верха
Клею тесьму, чтобы кант ботинка не растягивался
Далее приклеиваю бизик (точное название не помню 🙂 ), придает хороший вид
Сшиваю детали подклада
Тесьма ставится для того, чтобы клей при затяжке не просачивался сквозь строчку
Прошил берцы к задней части подклада
Примеряю 🙂
Сшиваю оставшиеся части
Нужно сказать, что эта машинка сделана не для машина, а для ремонта обуви — она очень грубая и большая. Поэтому я купил новую супер-секси машинку, которая предназначена для пошива 🙂 ее фото будет ниж.
Вот что получилось
Делаю предварительную затяжку, чтобы наметить место под рисунок на носу
Тем временем пробую плести косичку. Нужно сказать, что на всем видео и фото с косичками используется нить почти в 2 раза толще, чем есть у меня. Так как моя нить тоньше, то пришлось и длину стежка делать меньше, всего 5 мм. И на прошивании ранта время таким образом увеличивается в 2 раза.
Пробую деформировать так, как будет при сборке. Появились морщинки в связи с тем, что рант толстый. Поэтому я его благополучно сузил.
Был 2,5, стал вот такой
Пришло время работать со стелькой
Тем временем заготовка сформовалась и пора делать рисунок на нос, заготовка у меня уже была
Наметил и вручную выбиваю
Получилось вот так
Обязательно подкладку, иначе под перфорацией будет белая подкладка. Некоторые просто подклад красят, но на мой взглдя это не очень.
Продолжаю возиться со стелькой
Вырезал «губу» — это та часть, за готорую будет «цепляться» рант с помощью ниток.
Эластичный бинт помогает сформовать стельку, чтобы она идеально приняла форму следа колодки.
Пока стелька формуется делаею жесткие задники. Вставляются между верхом и подкладом для придания жесткоски и формоустойчивости. Потрогайте свою пару — у вас тоже есть, но скорее всего не из кожи :). В этой паре есть небольшой косяк с высотой задника, обусловлено это сборкой верха. В след раз учту
Проверяю толщину.
Вот все детали для придания формоустойчивости. Белый материал — это термопласт. При нагревании становится мягким, принимая заданную форму (ставится на носок). Так же его называю «пинг-понг», потому что он возвращается назад при нажатии. Очень удобно. Обычно я ставлю кожу на подносок, но пока не определился, что нравистя больше.
Вот так выглядит стелька после бинта — идеально прилегает к колодке
Пришло время готовить рант
Намечаю канавку под стежок с помощью специального грувера
Потом делаю разметку под стежок с помощью этого колесика (расстояние 5 мм)
Это я сравниваю разные варианты, как сделать рант еще и красивым, интересным.
В итоге вот такая штука, но в дальнейшем я использовал зиг-заг (будет видно). Вообще в процесс пошива пары проводишь много экспериментов, это увлекает 🙂
Пришло время затягивать пару и я вставляю жетский задник на свое место — между верхом и подкладом
Тоже самое с остальными деталями
Подтягиваем материал
Фиксируем гвоздями. Может показаться, что это простая операция, но на самом деле одна из самых сложных и долгих.
Получилось вот так
Между делом мне приехала профессиональная швейная машинка для пошива верха обуви Garudan, это было торжество! 🙂ё
Вот такую строчку дает 🙂
Просто шик! Жду следующую пару с нетерпением
А вот как раз установка термопласта на подносок
Вот такой цвет и фасон ранта я решил сделать
Готовлю рант — пробиваю отверстия для стежков
И вырезаю зиг-заг
Начал прошивать
Именно здесь я понял, что рант у меня толстый (2,5) — получаются морщинки на сгибе
Поэтому я сделал новый рант, а старый отпорол. Вот здесь видно, как он крепиться к стельке
Обувь изнутри
Супинатор для поддержания свода стопы + устойчивать (дада, у вас тоже такой есть в ботинке) 🙂
Пробка придает комфорт и эастичность.
А потом клеиться подошва
Подошва вид сверху
Далее делается специальный надрез с торца уреза, кожа отгинается и с помощью этого уникального инструмента делается канавка под строчку, которая сшивает подошву и рант.
Вот так и сшивается
После прошивки кожа заклеивается, таким образом строчка прячется и ей не грозит порыв из-за соприкосновения с землей (асфаль и тд).
Между делом сделал приятно Жене 🙂
После набирается каблук. К сожалению, у меня нет фото процесоов набора фликов, потому что эту черновую работу (со станком) дома я делать не могу, а в мастерской у Виктора как-то не фотографируется (забываешь).
Срезаются лишние участки и боковой урез красится
Обработка уреза для меня самая великая проблема, так как нужна специальная химия и двигатель с возможностью регулирования оборотов. Пока этот процесс у меня приметивен — натираю воском и полирую сукном + катушкой с конским волосом. Вообще у меня есть все необходимые катушки, нет химии (спиртовые грунты и тд) и 800 оборотов в минуту. Но это всего лишь дело времени, как-то так.
Пока не вощеный урез
Решил сделать такую стельку :))))) внутри полустелька из паралончика
Цвет подкала не самый лучший, но Андрей предложил хорошую идею — в следующий раз покрашу кожу
Урез после обработки
Конечный результат
И крупнее
В целом, я доволен результатом. Потратил на это дело около 1,5 месяцев. Буду продолжать выкладывать посты, потому что это позволяет структурировать работу. Помимо этого всем рекомендую вести дневник, где можно записывать всякие спорные моменты, чтобы потом проверить на паре и либо продолжать делать так же, либо не делать никогда :))
Есди вам было интересно — подпсиывайтесь
http://instagram.com/itskov
https://www.facebook.com/sergey.itskov
vizioner25.livejournal.com