Технология производства пеллет: как делают, оборудование
Пеллеты – это наиболее востребованный вид биотоплива, которое имеет вид небольших гранул. Изготавливаются такие гранулы из отходов сельскохозяйственной и деревообрабатывающей промышленности, благодаря чему их себестоимость достаточно низка. Кроме этого технология производства пеллет крайне проста и не требует особых затрат.
0.1. Пеллеты из лузги риса
В качестве исходного сырья для производства пеллет могут использоваться следующие материалы:
- Щепки;
- Опилки;
- Стружка и другие отходы деревообрабатывающей промышленности;
- Солома;
- Скорлупа орехов;
- Жмых винограда и других культур;
- Лузга подсолнечника и другие отходы сельскохозяйственной промышленности;
- Торф и так далее.
Стоит отметить, что такое сырье имеет низкую стоимость. Кроме этого производство пеллет выполняет роль утилизации отходов, что в свою очередь избавляет предприятия от дополнительных растрат на вывоз мусора.
Благодаря высокой теплотворной способности топливные гранулы пользуются большим спросом среди отопительных предприятий. Кроме этого твердотопливные котлы имеют наиболее высокий уровень КПД, а также низкую стоимость начальной установки оборудования. Это делает такое топливо наиболее выгодным для отопления домов. Поэтому пеллеты нашли применение не только в промышленных отопительных станциях, но и в частных домах для топки каминов и котлов.
1. Технология изготовления пеллет
Топливные гранулы уже достаточно давно имеются на Российском рынке, благодаря чему многие слышали о таком топливе, однако, далеко не все знают, как делают пеллеты. Это достаточно простой процесс, который не требует больших энергетических затрат. Кроме этого, для топки специальной печи используется тоже сырье, к примеру, опилки, из которых и делаются пеллеты.
Итак, линия по производству пеллет состоит из следующих элементов:
- Устройство для крупного дробления сырья;
- Специальная сушилка;
- Аппарат для мелкого дробления сырья;
- Увлажнитель;
- Гранулятор пеллет;
- Устройство для охлаждения и фасовки готовой продукции.
Стоит отметить, что оборудование для изготовления топливных гранул может быть мобильным и промышленным. Мобильные установки для изготовления пеллет, как правило, оснащены дизельным мотором. Они имеют компактные размеры, а также могут быть перевезены в любое удобное место. Конечно, обратная сторона медали заключается в том, что такое оборудование не может «похвастаться» высокой производительностью, и подходит больше не для предприятия, а для частного использования. Отдельного внимания достойны промышленные линии для изготовления топливных гранул.
1.1. Промышленные линии по производству пеллет
Промышленные линии для изготовления пеллет состоят из тех же элементов, что и мобильные, только они имеют гораздо большие размеры. Технология изготовления топливных гранул также одинакова как для мобильных установок, так и для промышленных линий. Более того, независимо от того, какое исходное сырье используется, производственный процесс полностью идентичен. Поэтому в качестве примера будет описана технология производства пеллет из опилок.
1.2. Крупное дробление
Мелкие древесные отходы, к примеру, опилки и стружка, доставляются при помощи специальной техники на специальный механизированный склад (так называемый подвижный пол). Далее подвижные стокеры, которые действуют благодаря гидравлическим приводам, выполняют возвратно-поступательные движения, загребая сырье и доставляя его в устройство для крупного дробления. Здесь сырье измельчается до нужных размеров и перемешивается.
В этот же момент часть опилок подается в бункер. Эти опилки необходимы для топки теплогенератора, который в свою очередь вступает в действие на втором этапе. При помощи шнека опилки подаются в камеру сгорания. Продукты горения из теплогенератора подаются в смеситель, куда под воздействием низкого давления, создаваемого дымососом, подается холодный атмосферный воздух и поставляемое на сушку измельченное сырье.
В первую очередь продукты горения перемешиваются с воздухом. При этом устройство автоматически регулирует пропорции смешивания. Это в свою очередь позволяет поддерживать необходимый уровень температуры теплоносителя. И только после этого теплоноситель перемешивается с только поступившим, еще влажным сырьем. Далее сырье подается в барабанную сушилку.
1.3. Барабанная сушилка
Это установка для производства пеллет, в которой сырье захватывается лопастями. Они поднимают сырье наверх, после чего оно проходит сквозь поток теплоносителя, при этом продвигаясь к выходу. Сразу за выходом располагается специальное устройство под название уловитель. Оно необходимо для улавливания камней, а также для сортировки сырья в случае, если это не было сделано изначально.
Просушенное сырье всасывается в так называемый циклон. Делается это путем разряжения воздуха при помощи дымососа. Сам циклон имеет принцип действия сепаратора – в результате центробежной силы опилки, которые имеют большую плотность и вес, оседают и остаются внизу. В этот момент более легкий отработанный теплоноситель выходит в дымоход.
Специальный шлюзовой затвор перемещает определенные дозы высушенных и нагретых опилок из циклона в распределитель потока, после чего они попадают в устройство мелкого дробления.
1.4. Молотковая дробилка
В момент перемещения сырья из сушилки в молотковую мельницу часть опилок поступает в теплогенератор. Оставшаяся часть поступает в дробилку. Здесь происходит окончательное дробление сырья. После такого измельчения опилки больше похожи на муку, и с этого момента именно так принято называть сырье. Далее мука подается в циклоны, в которых происходит отделение сырья от воздуха.
После этого мука попадает в шнековый транспортер, затем в наклонный шнековый транспортер, далее в бункер гранулятора. Внутри бункера гранулятора имеется аппарат, который препятствует образованию комков и слеживание муки.
Из бункера мука попадает в смеситель, в котором сырье смешивается с паром либо водой. Делается это при помощи процесса кондиционирования.
2. Пеллеты из соломы и лузги риса: Видео
2.1. Пресс для производства пеллет
Внутри пресса мука располагается между вращающейся матрицей и прессующими вальцами. Благодаря этому сырье продавливается в радиальные отверстия, которые имеются на матрице. Таким образом, происходит формирование гранул. Делается это при огромном давлении.
Далее выдавленные из радиальных отверстий гранулы обламываются неподвижным ножом. Готовые пеллеты падают вниз и через рукав выходят из гранулятора.
На выходе из пресс-гранулятора гранулы имеют высокую температуру. Кроме этого они являются весьма хрупкими. Для охлаждения и придания большей прочности пеллеты попадаются в устройство для охлаждения. В колонне для охлаждения вентилятор всасывает воздух через слой пеллет. Таким образом, происходит одновременное охлаждение гранул и отсасывание неспрессованной муки в циклон.
В результате охлаждения уровень влажности пеллет падает, что влечет за собой некоторые физико-химические изменения, обеспечивающие гранулам более высокую прочность, а также требуемую влажность и температуру.
После этого происходит отсеивание пеллет от крошки и фасовка готовой продукции в мешки. Как можно заметить вся технология гранулирования пеллет происходит без дополнительных расходных материалов. Кроме этого низкая стоимость топливных гранул объясняется высокой производительностью подобных установок, при низких энергетических затратах.
Технологический процесс производства пеллет из опилок, стружки, шелухи.
Принцип производства пеллетПроцедура, при которой сырье под действием высокого давления при нагреве прессуется, называется брикетированием топливной стружки, шелухи, опилок и т.д. Суть производства пеллет схож с изготовлением топливных брикетов Нильсен.
Данное твердое древесное топливо имеет отличную теплоотдачу, не имеет химических добавок и положительно влияет на окружающую среду.
Технология гранулирования пеллетОсновой изготовления гранулированных частиц – пеллет — является технологический процесс прессования мелких древесных отходов, шишек, соломы, лузги, семечек и т.д.
Гранулирование пеллет было изобретено ещё в 1947 году, с тех пор процесс постоянно совершенствуется, при этом принцип не меняется. Исходное сырье отправляется в дробилку, затем образовавшаяся мука из опилок добавляется в сушилку, и в гранулятор, где формируются топливные гранулы.
- Измельчение древесины. Дробильное оборудование измельчает сырье до размеров не более 2 мм. Чем мельче исходный результат, тем меньше в дальнейшем идет энергозатрат на сушку.
- Высушивание. Для прессования пригоден материал, влажность которого находится в диапазоне 7-11%. При несоответствии показателей требуется дополнительное увлажнение или сушка. Сушилки бывают барабанные и ленточные. Сушильный агрегат может работать на топочном газе, горячем воздухе и паре из воды.
- Дополнительная обработка сухого сырья. Стабильную работу пресса обеспечивают частицы, не превышающие в размере 5 мм. Большие части пропускают через дезинтегратор, мельницу или стружечный станок.
- Стандарты влажности. Сырье, имеющее влажность менее 8% сложно прессовать. Шнековые смесители, подают пар, увлажняют основу, тем самым увеличивая её прочность и эластичность для дальнейшей обработки.
- Гранулирование. В процессе прессования повышается температура древесной муки.
Из древесины выделяется лигнин, который склеивает элементы в плотные цилиндрические топливные гранулы.
- Фасовка и упаковка. Охлажденные древесные гранулы фасуют в мешки от 5 до 1000 кг.
Рекомендуется прессовать отходы одной древесной породы. Кора, попадающая в стружку, не влияет на процесс и успешно гранулируется. Загрязненность материала песком, землей может привести к быстрому износу оборудования.
Идеальным считается прессование пеллет из зерновой и рапсовой соломы, шелухи семечек, кукурузных початков. Предварительно измельченная солома в своем составе может иметь элементы длиной до 65 мм. Более высокой теплоотдачей обладают пеллеты из опилок и стружки. Древесные гранулы предпочитают использовать в бытовых пеллетных котлах в домах, коттеджах и т.д.
Способ производства пеллет прост, безупречно работает в обычных условиях и гарантирует получение продукции, которая востребована на внешнем и внутреннем потребительском рынке.
Оборудование для производства пеллет из опилок, Как делают пеллеты
Линия гранулирования необходима для создания гранул твердого биотоплива. В такую линию входят прессы, смесители, бункеры, охладительные колонны, активный и пассивный циклоны, пневматическая сортировка, радиальный вентилятор, комплекты пневмотранспортных труб и панель управления.
Функция линии брикетирования состоит в создании брикетов топлива на основе переработанных спрессованных отходов деревообработки, включая солому, камыш, стружку и прочие. Брикеты формируются под воздействием давления брикетирующего пресса и высоких температур.
Рубильные дисковые машины или дробилки предназначены для дробления древесины до образования технологической щепы. Машина работает с отходами деревообрабатывающей промышленности, для их загрузки используется вертикальная воронка. Для мелкого дробления чаще всего характерно использование молотковых мельниц.
Сушильные аэродинамические комплексы необходимы для уменьшения влажности опилок, такие комплексы являются частью линий гранулирования. Грануляторы существуют для переработки производственных отходов путем создания из них гранулированного биотоплива.
Для координации роботы тех или иных линий производства пеллет необходимо щитовое оборудование, оно представляет собой шкафы управления, обеспечивающий автоматический процесс производства.
Контроль качества продукции — важнейшая составляющая производства, для этого предприятие должно быть оснащено локальными лабораториями на всех участках производства. Данные лаборатории позволяют осуществлять контроль прочности, зольности, теплоты сгорания и влажности производимой продукции. Очень важно отбирать некондиционную продукцию для дальнейшей переработки.
Дополнительное оборудование также играет немаловажную роль, поскольку производство пеллет — высокотехнологичный и многоуровневый процесс, в котором задействовано множество механизмов. Производство необходимо оснастить весовыми дозаторами для сыпучей и мелкокусковой продукции, для подготовки древесины часто используют колуны, раскалывающие колоды, и станки для окорки бревен. Если какое-то оборудование необходимо постоянно обеспечивать энергией, в работе может применяться маслостанция. Также важно использование высококачественных промышленных ножей (рубильных, стружечных и т.д.).
Полезно: оборудование для производства топливных брикетов.
Как делают пеллеты
Процесс производства пеллет условно можно разделить на шесть этапов.
- На начальном этапе происходить крупное дробление подготовленного сырья, такое измельчение необходимо, чтобы дальше сырье можно было просушивать.
- Второй этап представляет собой просушку крупно раздробленного сырья в барабанных или ленточных сушильных комплексах, в зависимости от конкретного сырья и требований производства.
- На третьем этапе высушенные компоненты еще раз измельчаются, на выходе при этом должно получиться сырье по размерам не больше 4 мм.
- Чтобы избежать пересушенного сырья и таким образом обеспечить лучшее спрессовывание, сырье отправляется на водоподготовку в смесительные емкости, где смешивается с дозированной водой либо обрабатывается паром.
- Пятый этап представляет собой самую важную часть производства — прессование сырья. Это непосредственное формирование пеллет под давление матричного пресса. После прессования пеллеты охлаждаются.
- Заключительный шестой этап производства — это окончательный контроль качества, просеивание и расфасовка.
Частный инвестор с 2006 года (акции, недвижимость). Владелец бизнеса, специалист по интернет маркетингу.
Оборудование для производства пеллет
Европа повсеместно переводит угольные электростанции на сжигание пеллет, активно субсидирует частный сектор для установки пеллетных котлов. Спрос на топливо постоянно растет, и производство пеллет является очень выгодным и перспективным бизнесом.
Наша компания готова поделиться опытом в области производства гранулированного топлива, и мы можем с уверенностью заявить:
- оборудование
для производства пеллет — это ключ для бизнес-отношений с Европой.
Для получения ценового предложения сообщите нам адрес вашей электронной почты внизу этой страницы
Видео производства топливных пеллет
Преимущества производства топливных пеллет
- это новый сегмент рынка, где еще не сложились жесткие конкурентные условия;
- спрос на брикеты и пеллеты постоянно повышается;
- технология производства этого вида продукции проста и экономична;
- оборудование для производства пеллет реализуется по высоким ценам, но быстро окупается.
Зарубежное оборудование для производства пеллет — основа бизнеса, который всегда будет прибыльным и успешным, а также увеличиваться в стоимости!
Компания Pellet & Briquette machine предлагает:
- производство и поставка видов оборудования, необходимых для производства топливных пеллет;
- установление обоюдовыгодных партнерских отношений;
- уникальное предложение по закупке всего объема гранулированного топлива;
- проработанные варианты по
организации деятельности, связанной с производством пеллет.
Ответы на любой из ваших вопросов предоставят квалифицированные менеджеры P&B MACHINE. Специалисты компании подберут и предложат вам оборудование, равно соответствующее как производственным потребностям вашего предприятия, так и вашим финансовым возможностям.
Получить коммерческое предложение *
*оборудование производства пеллет ЕС
Склад опилок Живое дно
Одной из проблем, с которой приходится сталкиваться владельцам производств с использованием сыпучего сырья естественной влажности (щепа, опилки, измельченный торф и т.п.), является организация подачи материала от места складирования в производственную зону.
В силу характерных особенностей, под такую сырьевую массу недостаточно просто подвести транспортер: слежавшаяся масса опилок или щепы имеет обыкновение «зависать», образовывать своды, и обычный способ транспортировки позволяет изъять из бункера лишь близлежащую часть сырья.
Описание склада «Живое дно»
Отличным
решением для подобных ситуаций служит склад «Живое дно», реализуемый компанией
«P&B MACHINE»: это бункер особого типа, пол которого состоит из движущихся
стокеров-скребков. Свое название такие склады получили из-за особого типа
механизации, используемой в придонном пространстве накопительной емкости.
Склады, организованные по принципу «живого дна», применяются для подачи топлива в котельных, работающих на измельченных древесных и отходах. В последние все шире практикуется еще одно перспективное применение таких бункеров – в составе технологических линий для производства топливных пеллет и брикет на основе древесно-растительного сырья, совместно с рубительными машинами.
Как это работает:
- В районе дна накопителя смонтированы движущиеся скребки, которые имеют в сечении клиновидную форму.
- На холостом ходу (движение от устья накопителя) скребки взрезают засыпанное в бункер сырье острым краем.
- На рабочем ходу (движение к устью транспортера) стокеры захватывают щепу, опил или торф тупым краем, и подтаскивают его к началу транспортера.
- Таким образом, сырье
перемещается на транспортер со всей площади склада, обеспечивая
оптимальную загрузку и не допуская «холостой» работы оборудования.
Компания «Pellet & Briquette machine» принимает заказы на поставки складов «Живое дно» объемом 100м3 и производительностью 2000кг/час заинтересованным покупателям. Наши специалисты подробно разъяснят Вам принцип работы бункера, уточнят стоимость, дадут необходимые консультации и рекомендации, помогут в формировании и оформлении заявки на приобретение продукции.
Получить коммерческое предложение
Технологии производства пеллет
Твердое топливо (биотопливо, пеллеты) представляет собой гранулы, цилиндрической формы, полученные путем прессования из высушенных, предварительно измельченных отходов растительного происхождения (сырья). Гранулы предназначены для получения тепла методом сжигания. Гранула — имеет от 10 до 30 миллиметров в длину и от 6 до 10 миллиметров в диаметре. Одному кубическому метру нефтепродуктов (10 000 квт/час) соответствует около двух тонн или трех кубических метров гранул.В условиях истощения природных запасов и постоянно возрастающих цен на энергоносители актуальным является поиск альтернативных источников энергии. Одним из путей решения указанной проблемы является использование в качестве топлива отходов перерабатывающей промышленности из растительного сырья (отходы древесины, лузги подсолнечника, соломы, костры льна, и т.д.).
По теплотворной способности твердое топливо приближается к бурому углю, а по экологическим параметрам имеет преимущество не только перед ним, но и перед другими видами топлива (каменным углем, мазутом и т.д.).
В настоящее время биотопливо представляет собой полезную форму обогрева для домов для одной семьи, составляя конкуренцию системам обогрева с использованием нефти и электричества, также является эффективной альтернативой на местных станциях обогрева и даже на тепловых станциях.
Пеллеты (топливные гранулы) — это глубоко переработанный и экологически чистый вид топлива. Преимуществом использования прессованного биотоплива является, во-первых, бoльшая теплотворная способность по сравнению с кусковыми отходами, пылью и т.д. Во-вторых, меньшая стоимость оборудования для котельных установок мощностью до 2МВт, по сравнению с установками по сжиганию древесных отходов. Объем склада для хранения пеллет может быть уменьшен как минимум до 50%, по сравнению со кладом для древесной щепы. Гранулы могут храниться в непосредственной близости от жилых помещений (подвальные или подсобные помещения), так как этот материал биологически неактивный, поскольку прошел термическую обработку. Он менее подвержен самовоспламенению, а так как не содержит пыли и спор, которые также могут вызывать аллергическую реакцию у людей. Гранулы можно грузить погрузчиками или пневмотранспортом. Пневмотранспортом их можно поднимать на высоту до 20 метров.
Производить гранулы из сухого размолотого сырья научились давно и данная технология применяется в зерновой и сахарной промышленности.
Мы предлагаем высокотехнологичное комплексное оборудование. Особое внимание следует уделить именно на промышленное назначение гранул. Невозможно производить качественную продукцию кустарным способом.
Если вы намереваетесь производить гранулы высокого качества из сырого материала, имеющего непостоянную влажность и различные размеры, содержащего примеси, например, песок, тогда нужен завод, состоящий из следующих участков и оборудования:
- Склада сырья
- Рубительной машины, горохота и молоткового измельчителя
- Сушильной камеры
- Гранулятора
- Системы для охлаждения гранул
- Склада для хранения готовой продукции
- Оборудования для удаления пылеобразного вещества с гранул
- Участка упаковки продукции
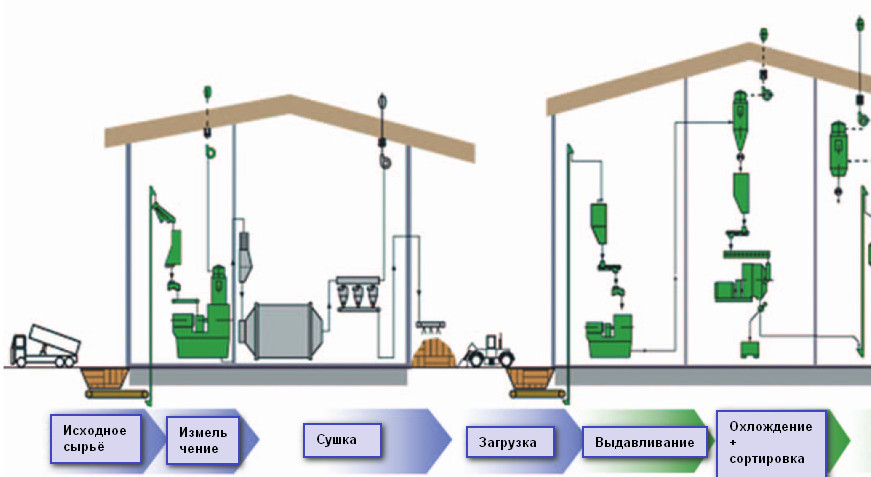
Наибольший размер частиц дробленого высушенного сырья не должен превышать половины диаметра готовой гранулы.
Все сырье должно быть одинаковой влажности по всему объему. Чем более равномерна влажность и однородней масса- тем плотнее будет гранула. Сушка сырья происходит в сушильных камерах барабанного типа, специально разработанных для биомасс. Для такого оборудования особенно высоки требования по пожаробезопасности. Если же Вы будете производить твердое биотопливо из сырья влажностью до 12%, то отпадает необходимость в сушильной камере.
Пресс для гранулирования — это основной механизм всего производства топливных гранул. От его работы зависит качество продукции. В грануляторе осуществляется процесс формирования гранул. В смесителе гранулятора сырье увлажняется и в необходимом количестве подается в гранулятор.Удельная плотность пеллет может достичь 1450кг/м3, а насыпной вес доходит до 750 кг/м3. Необходимая электрическая мощность оборудования производительностью до 2т/ч из сухого сырья составляет 250кВт. Основной персонал 5-8 человек.
Срок окупаемости оборудования составляет 2-2,5 года. Хочется отметить, чем больше производительность оборудования тем меньше срок окупаемости.
Рост потребителей альтернативного топлива из различных стран ежегодно увеличивается. Производство пеллет в ближайшее время будет вносить значительный вклад в мировую стратегию возобновляемых источников энергии.
Публикация материалов Pelleta.Com.Ua разрешается только при условии ссылки на Pelleta.Com.Ua. Для новостных и интернет-изданий обязательной является прямая, открытая для поисковых систем, гиперссылка в первом абзаце на цитируемую статью или новость.
Ссылка на новость: Технологии производства пеллет
Скопируйте и разместите этот код на Вашем сайте:
Технологии производства пеллет
Просмотров: 5770 Добавлена: 06. 09.2008
Технологии производства пеллет
0 5 Среднее: 3.20 Всего: 5 голосов (из 5)Производство пеллет — прибыльное направление бизнеса
Производство топливных пеллет является очень перспективной отраслью по переработке вторичного сырья. Этот процесс позволяет получать топливные гранулы из отходов деревоперерабатывающей промышленности. Часто в их состав добавляют и сельскохозяйственные отходы, например, солому или шелуху подсолнечника. Тепловой энергии, выделяемой при сгорании пеллет недостаточно, чтобы удовлетворять промышленные нужды металлургических заводов. Но они успешно применяются на тепловых электростанциях и в котельных.
Владельцы частных домов также нередко переходят с дров на данный вид топлива. Они обладают целым рядом неоспоримых преимуществ. Во-первых, больше нет необходимости собирать, сушить, распиливать древесину и колоть ее на поленья для топки. Во-вторых, гранулы занимают гораздо меньше места, чем связка дров. В-третьих, пеллеты имеют регламентированное время горения, что позволяет с высокой точностью рассчитать необходимое для камина количество гранул. Пеллеты идеально подходят для туристических походов. В лесу не всегда удается отыскать сухие, пригодные для костра ветки, а, имея с собой несколько упаковок с гранулами, путешественники никогда не останутся прохладной ночью без огня.
Этапы производства топливных пеллет
Технология производства пеллет включает в себя несколько этапов. На первом этапе производится тщательное дробление и измельчение подготовленного сырья, пока не будет получена однородная масса. Затем материал отправляется в сушильные печи, где проходит сушку до тех пор, пока его относительная влажность не достигнет отметки 8%. После сырье проходит еще один этап дробления на более мелкие частицы. На следующей стадии измельченные заготовки обдаются паром, чтобы они лучше склеивались друг с другом. Далее сырье поступает в барабанную установку, где под давлением 300 атмосфер происходит прессовка «древесной муки» и формирование гранул.
На последнем этапе производится просеивание и упаковка готовой продукции. Стоит отметить, что производство осуществляется на безотходной основе. Все отбракованные пеллеты отправляются на вторичную переработку. Из одной тонны отходов в зависимости от их влажности получается 150-250 килограмм топливных гранул. Средняя производительность станка для производства пеллет составляет 2 тонны в час. На обогрев одного подъезда девятиэтажного дома в отопительный сезон уходит примерно 900 килограмм пеллет в неделю.
Заводы по производству пеллет зачастую располагают вблизи сырьевых баз. Это позволяет значительно снизить транспортные затраты на доставку. Хорошее предприятие обычно окупает все расходы через несколько лет работы на полной мощности. Переработка вторичного сырья дает немало преимуществ. Первое: больше нет необходимости заниматься утилизацией отходов, так как они выступают в качестве материалов для новой продукции. Второе: открытие новых предприятий означает появление большого количества рабочих мест, что очень важно в условиях мирового финансового кризиса и высокого уровня безработицы. Третье: производство позволяет получить экологически чистый вид топлива, продукты сгорания которого не наносят ущерб окружающей среде. В развитых странах использование вторсырья и безотходное производство являются одними из приоритетных задач промышленной отрасли. И появление подобных заводов в Российской Федерации является очень важным шагом в деле заботы об охране природы.
Принцип работы линнии по производству пеллет
Линия по производству пеллет состоит из нескольких установок, которые необходимо рассмотреть подробнее. Начинается все с транспортного средства, которое доставляет отходы от производства до места переработки. Привезенное сырье высыпают на склад со специально оборудованным «движущимся» полом. Подвижная поверхность полов позволяет с регулируемой скоростью подавать опилки на дробильный аппарат. Время подачи рассчитывается с учетом циклов работы дробилки, чтобы устройство не переполнялось, но и не простаивало без работы. После дробилки сырье отправляется в сушильную камеру. После доведения относительной влажности до необходимого уровня, сырье отправляется на окончательное измельчение.
Здесь опилки и прочие отходы измельчаются до размера песчинки. После этого «древесная мука» начинает движение к прессовальной камере. По пути она проходит через фильтры, которые блокируют доступ не измельченным частицам. Перед прессовкой сырье попадает в смеситель, в котором проходит обработку паром. Полностью подготовленный материал поступает в гранулятор, в котором происходит его прессовка и формирование гранул. Спрессованные гранулы падают на конвейер, который доставляет их в камеру для охлаждения. Охлажденные пеллеты приобретают твердость, а технологический процесс на этом заканчивается. Далее следует только расфасовка и упаковка готовой продукции в различную тару.
Установка для производства пеллет включает в себя несколько приборов. Первое устройство — это так называемые «подвижные полы», которые работают от гидравлического привода. Они выполняют лишь транспортную функцию, поэтому не содержат ни каких особо интересных приспособлений. Далее следует молотковая дробилка. Как не трудно догадаться из названия, измельчение происходит при помощи молота, которые хорошо справляется с крупными опилками и стружками, но пропускает множество мелких элементов. Предварительно измельченное сырье поступает в сушку, которая благодаря поддержанию высокой температуры забирает у древесины лишнюю влагу.
Далее следует второй измельчитель уже мельничного типа, который позволяет довести материал до размеров муки. Он действует по принципу мельничных жерновов, так что все отходы просто перетираются в однородную массу. В смесителе сырье подвергается обработки паром, который подается из специальных котлов с водой, предварительно нагретой до температуры кипения. Грануляторы для производства пеллет работают по принципу центрифуги. Они затягивают внутрь «древесную муку», затем спрессовывают ее под высоким давлением и выдавливают через специальный трафарет, который придает готовой продукции форму гранул. На выходе расположен специальный нож, который обрезает гранулы до установленной длины. Ну а в камеру для охлаждения подается холодный воздух, который придают пеллетам необходимую твердость.
Производство пеллет как бизнес
Производство топливных гранул пеллет — это четко ориентированный на сырье процесс. И очень важной его частью является бесперебойная доставка материалов для переработки. Пеллеты могут изготавливаться из нескольких материалов. Производство пеллетов из опилок позволяет получить гранулы самого высшего качество. Они имеют максимальную теплоотдачу при сгорании и наибольший срок горения. Высокое качество и характеристики делают их самыми дорогими среди всех видов топливных гранул. Производство пеллет из соломы дает самый дешевый вид биологического топлива. Такие гранулы имеют невысокую теплоотдачу и очень быстро перегорают. На практике очень часто производятся смешанные пелеты, которые состоят из нескольких видов отходов.
Производство биологического топлива является очень перспективным направлением ведения бизнеса. В Европе уже многие предприятия и коммунальные хозяйства выразили желание перейти на топливные гранулы. Поэтому спрос на пеллеты будет ежегодно возрастать, что позволит стабильно получать высокую прибыль. Чтобы открыть свое дело по производству топливных гранул, необходимо в первую очередь изучить спрос. Если потенциальные клиенты найдутся, необходимо заняться поисками поставщиков сырья. Далее в дело вступает логистика, которая поможет выбрать место для завода с удобной транспортной развязкой, чтобы затраты на дорогу были минимальны.
Не обязательно строить технологические сооружения с нуля. Можно арендовать подходящее помещение и оборудовать его под производство. Это позволит сэкономить много времени и сил. Мини производство пеллет можно наладить прямо на лесопилке. Нужно просто договориться с ее руководством и оснастить рабочее место. Такое соседство позволит вообще избежать транспортных издержек на доставку сырья. Также не возникнет проблем с перебоями поставок из-за погодных условий, например сильных снегопадов или оледенения дороги, которые могут мешать дальним переездам. Ну а когда все вопросы по поставщикам и клиентам будут улажены, нужно раздобыть стартовый капитал, получить необходимые лицензии и можно смело начинать свое собственное дело.
Процесс гранулирования биомассы | BioEnergy Consult
Гранулы биомассы — это популярный вид топлива из биомассы, обычно производимый из древесных отходов, сельскохозяйственной биомассы, технических трав и лесных остатков. Помимо экономии на транспортировке и хранении, гранулирование биомассы упрощает и рентабельность обращения. Плотные гранулы кубиков имеют характеристики сыпучести, аналогичные характеристикам зерна злаков. Правильная геометрия и небольшой размер гранул биомассы позволяют производить автоматическую подачу с очень точной калибровкой.Высокая плотность гранул также обеспечивает компактное хранение и рациональную транспортировку на большие расстояния. Пеллеты очень плотные и могут изготавливаться с низким содержанием влаги, что позволяет их сжигать с очень высокой эффективностью сгорания.
Гранулирование биомассы — это стандартный метод производства твердых энергоносителей высокой плотности из биомассы. Пеллеты производятся нескольких типов и марок в качестве топлива для электростанций, домов и других применений.Оборудование для производства пеллет доступно в различных размерах и масштабах, что позволяет производить как в домашних, так и в промышленных масштабах. Пеллеты имеют цилиндрическую форму, диаметр 6-25 мм и длину 3-50 мм. В настоящее время разрабатываются европейские стандарты для гранул биомассы и классификации сырья (EN 14961-1, EN 14961-2 и EN 14961-6), а также международные стандарты ISO (ISO / DIS 17225-1, ISO / DIS 17225-2 и ISO / ДИС 17225-6).
Описание процесса
Процесс гранулирования биомассы состоит из нескольких этапов, включая предварительную обработку сырья, гранулирование и последующую обработку.Первым шагом в процессе гранулирования является подготовка сырья, которое включает выбор сырья, подходящего для этого процесса, его фильтрацию, хранение и защиту. Используемое сырье — опилки, стружка, древесные отходы, сельскохозяйственные отходы, такие как солома, просо и т. Д. Фильтрация проводится для удаления нежелательных материалов, таких как камень, металл и т. Д. Сырье следует хранить таким образом, чтобы в нем не было примесей и влага. В случаях, когда используются разные типы сырья, для достижения консистенции используется процесс смешивания.
Содержание влаги в биомассе может быть значительно высоким и обычно составляет до 50–60%, которое следует снизить до 10–15%. Вращающаяся барабанная сушилка — наиболее распространенное оборудование, используемое для этой цели. Также можно использовать сушилки с перегретым паром, мгновенные сушилки, сушилки с носовым слоем и ленточные сушилки. Сушка увеличивает эффективность биомассы, и при сгорании почти не образуется дыма. Следует отметить, что сырье не должно быть пересушено, так как небольшое количество влаги помогает связывать частицы биомассы.Процесс сушки является наиболее энергоемким процессом и составляет около 70% от общей энергии, используемой в процессе гранулирования.
Схема гранулирования древесной биомассы
Перед подачей биомассы в грануляторы биомасса должна быть измельчена до мелких частиц размером не более 3 мм. Если размер гранул слишком большой или слишком маленький, это влияет на качество гранул и, в свою очередь, увеличивает потребление энергии. Следовательно, частицы должны иметь правильный размер и быть однородными.Уменьшение размера производится путем измельчения с помощью молотковой мельницы, оснащенной ситом размером от 3,2 до 6,4 мм. Если сырье достаточно большое, перед измельчением оно проходит через измельчитель.
Следующим и наиболее важным этапом является гранулирование, при котором биомасса прижимается к нагретой металлической пластине (известной как матрица) с помощью ролика. Головка состоит из отверстий фиксированного диаметра, через которые биомасса проходит под высоким давлением. Из-за высокого давления увеличиваются силы трения, что приводит к значительному повышению температуры.Высокая температура вызывает размягчение лигнина и смол, присутствующих в биомассе, которые действуют как связующий агент между волокнами биомассы. Таким образом частицы биомассы сливаются с образованием гранул.
Скорость производства и электрическая энергия, используемая при гранулировании биомассы, сильно коррелируют с типом сырья и условиями обработки, такими как содержание влаги и размер корма. Средняя энергия, необходимая для гранулирования биомассы, составляет примерно от 16 кВтч / т до 49 кВтч / т. Во время гранулирования большая часть энергии процесса используется для обеспечения потока биомассы во входные отверстия каналов пресса.
Связующие или смазочные вещества могут быть добавлены в некоторых случаях для получения гранул более высокого качества. Связующие увеличивают плотность и долговечность гранул. Древесина содержит натуральные смолы, которые действуют как связующее. Точно так же опилки содержат лигнин, который скрепляет гранулы. Однако сельскохозяйственные остатки не содержат много смол или лигнина, поэтому в этом случае необходимо добавить стабилизирующий агент. Дистилляторы сушат зерна или картофельный крахмал — некоторые из часто используемых связующих. Использование натуральных добавок зависит от состава биомассы и массового соотношения между целлюлозой, гемицеллюлозами, лигнином и неорганическими веществами.
Из-за трения в матрице выделяется избыточное тепло. Таким образом, гранулы получаются очень мягкими и горячими (примерно от 70 до 90 o C). Перед хранением или упаковкой его нужно охладить и просушить. Затем гранулы можно пропускать через вибрирующее сито для удаления мелких частиц. Это гарантирует, что источник топлива будет чистым и свободным от пыли.
Гранулы упаковываются в мешки с помощью подвесного бункера и конвейерной ленты. Пеллеты хранятся в приподнятых бункерах или силосах на уровне земли. Упаковка должна быть такой, чтобы гранулы были защищены от влаги и загрязняющих веществ. Коммерческие грануляторы и другое оборудование для гранулирования широко доступны по всему миру.
Нравится:
Нравится Загрузка …
СвязанныеИнформация о Салмане Зафаре
Салман Зафар — генеральный директор BioEnergy Consult, а также международный консультант, советник и инструктор, обладающий опытом в области управления отходами, энергии биомассы, преобразования отходов в энергию, защиты окружающей среды и сохранения ресурсов.Его географические области деятельности включают Азию, Африку и Ближний Восток. Салман успешно выполнил широкий спектр проектов в области биогазовой технологии, энергии биомассы, преобразования отходов в энергию, рециркуляции и управления отходами. Салман принимал участие в многочисленных национальных и международных конференциях по всему миру. Он — плодовитый экологический журналист, автор более 300 статей в известных журналах, журналах и на веб-сайтах.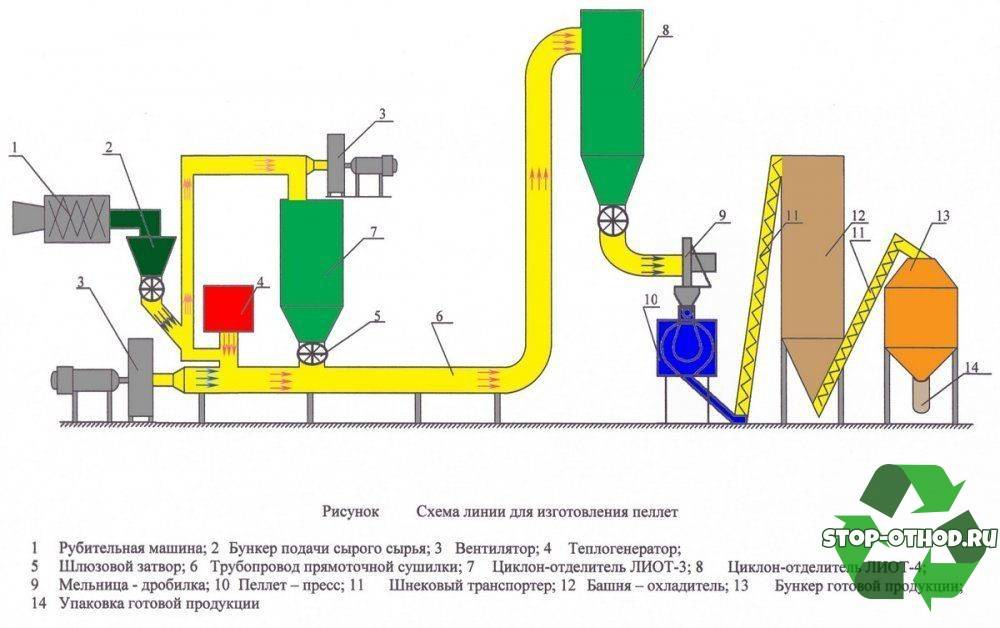
Исследование и исследование технологии производства топливных гранул из биомассы
PDFИсследование технологии производства гранул биомассы
I. Введение в топливные гранулы из биомассы
Энергия — это основа нашего существования и развития. Непрерывное потребление невозобновляемой энергии заставляет людей обращаться к использованию возобновляемых, экологически чистых источников энергии биомассы, в качестве представителя которой используется топливо из биомассы.Энергия биомассы стала стратегическим выбором для устойчивого развития гражданского общества и направления развития. Это может не только восполнить нехватку традиционных источников энергии, но также имеет большие экологические преимущества. По сравнению с другими методами получения энергии из биомассы, гранулированное топливо из биомассы легко добиться массового производства и использования. По удобству он может соперничать с газом и мазутом.
II. Необходимость разработки топлива из биомассы
С ростом потребления традиционной энергии необходимо использовать новую энергию из-за серьезной нехватки ресурсов.В Китае мы владеем богатыми топливными ресурсами в виде гранул. В настоящее время основные ресурсы, которые могут быть использованы, включают: солому сельскохозяйственных культур, топливную древесину, отходы, древесные отходы в твердых бытовых отходах и многое другое. Согласно теоретическим расчетам, наши топливные ресурсы на древесных гранулах могут достигать 5 миллиардов тонн. Топливные гранулы из биомассы обычно относятся к твердому топливу цилиндрической формы диаметром менее 25 мм. Плотность гранул перед прессованием увеличивается до 1,2-1,4 кг / м³. Уменьшение объема от 75% до 90%, что упрощает хранение и транспортировку. Размер однородный с хорошей текучестью, что облегчает автоматическую передачу и сгорание. Топливные пеллеты — это вид природного топлива из биомассы, в процессе производства нет необходимости добавлять клей. Благодаря низкому содержанию влаги легко регулировать воздух для горения, а эффективность горения высокая. Средний выброс газа при сгорании составляет 1,2 г / ч, что намного ниже 7,5 г / ч, предусмотренных USEPA. Гранулированное топливо из биомассы в гранулированной или блочной форме может значительно повысить эффективность сгорания материалов.Тепловой КПД может увеличиться более чем на 80%. Согласно расчетам, количество тепла, вырабатываемого 1,2 т древесных пеллет и 1 т угля, эквивалентно. Топливные гранулы биомассы получают из биологических отходов без химических веществ, таких как делящиеся и взрывоопасные химические вещества. При сгорании не произойдет отравления, взрыва, утечки.
III. Разработка топливных пеллет из биомассы в стране и за рубежом.
3.1 Развитие технологий использования и производства топливных гранул из биомассы в стране и за рубежом.
3.1.1 История развития
Использование топливных горелок на гранулах биомассы началось в 1970-х, но до конца 1980-х многие европейские страны (например, Швеция, Финляндия, Бельгия, Франция, Германия, Италия) начали придавать значение исследованиям и эксплуатации топливных технологий из биомассы в результате мирового энергетического кризиса и роста цен на нефть. В настоящее время он сформировал промышленное производство с замечательными достижениями. Франция начинает использовать гранулы из соломы в качестве корма для дойных коров. В последние годы они также исследуют и производят топливо в форме блоков.Переработка лесных отходов в брикеты определенной формы путем механического прессования достигла практической стадии.
3.1.2 Технология гранулирования
Сушка: из-за высокого содержания влаги в опилках (обычно 50%) их следует сушить до содержания влаги в сырье 9-12%, чтобы удовлетворить потребность в формовании. Сушилка оборудована вращающимся барабаном прямого нагрева (вращающаяся барабанная сушилка ).
Присыпка: После высыхания сырье необходимо измельчить в порошковой машине.Общий размер 1 мм.
Закалка и отпуск: это относится к размягчению древесного волокна в сырье, пополнению и увеличению количества высокотемпературного пара в сырье. Более чем на половине заводов по производству пеллетного топлива эта технология была применена в процессе производства.
Формование гранул: Большинство заводов по производству гранул из биомассы используют принцип экструзионного формования с роликовыми роликами, что означает вертикально-кольцевую формовочную машину и производительность 2-4 т / ч. Основные компоненты имеют длительный срок службы. Кольцевая матрица составляет 2000-3000 ч, а обжимной валок — 1000-1500 ч.
Охлаждение: Температура гранул, выгружаемых из гранулятора, составляет около 100 ℃, гранулы в таком состоянии легко ломаются и не должны храниться и транспортироваться. Следовательно, пеллеты необходимо охлаждать с помощью холодильника с принципом противоточного охлаждения.
Сборка и упаковка : После охлаждения гранулы собираются и упаковываются в соответствии с различными потребностями потребителей. Спецификации упаковки могут быть разделены на маленькие мешки (16 кг) и большие мешки (900 кг) в зависимости от потребностей. Для крупного потребителя тепловая электростанция может перевозиться на грузовом транспорте или на лодке.
3.1.3 Анализ условий использования
Взяв, к примеру, Америку, Швецию и Австрию, масштабы применения энергии биомассы соответственно составляют 4%, 16% и 10% от их потребления первичной энергии. В Америке общая установленная мощность производства энергии из биомассы составляет более 1 МВт, а единичная мощность составляет 10-25 МВт. Оборудование для сжигания гранулированного топлива из биомассы в Японии, Америке и некоторых европейских странах было промышленно использовано в областях отопления, сушки и генерации.Топливные гранулы из биомассы и соответствующие эффективные отопительные печи с чистым сжиганием были очень популярны, запрет на эффективность нагрева достигает 80-95%.
3.2 Использование условий и производственных технологий Разработка отечественного топливного гранулированного биомассы
3.2.1 История разработки
Условно говоря, мы поздно начали исследования и производство в этой области, но мы уделяем этому много внимания. С 1980 года наше правительство сделало исследования и применение технологий применения топлива из биомассы в качестве ключевого национального вопроса.Технология энергии биомассы перешла на более высокую ступень. Машина для формования соломинок спирально-выталкивающего типа, представленная в 80-х годах, имела определенный масштаб. Но наши исследования в основном сосредоточены на технологиях производства биогаза для крупного и среднего скота и птицы, газификации соломы, централизованной подачи газа и электростанций на полигонах. Для производства топливных гранул из биомассы и исследований в области прямого сжигания нам предстоит пройти долгий путь. В некоторых университетах и научно-исследовательских учреждениях в последние годы были достигнуты определенные достижения и масштабы производства.
3.2.2 Анализ условий использования
Машина для формования соломы спирально-выталкивающего типа, представленная в 80-х годах, сформировала определенный масштаб. Но наши исследования в основном сосредоточены на технологиях производства биогаза для крупного и среднего скота и птицы, газификации соломы, централизованной подачи газа и электростанций на полигонах. Для производства топливных гранул из биомассы и исследований в области прямого сжигания нам предстоит пройти долгий путь. В некоторых университетах и научно-исследовательских учреждениях в последние годы были достигнуты определенные достижения и масштабы производства.Например, разработанная нами грануляторная мельница включает в себя гранулятор с кольцевой матрицей и гранулятор с плоской матрицей , кроме того, они начали исследования по топливной машине для гранулирования биомассы из соломы. С 2002 года первоначальный центрально-южный лесохозяйственный колледж разработал машину для формования топливных гранул из биомассы и подходящую печь для защиты окружающей среды и отопительную печь на основе передовых технологий, импортированных из-за границы (Швеция). Машина для формования гранулированного топлива из биомассы была разработана на основе технологии отечественного гранулятора для производства гранул в сочетании с технологией шведской машины для производства гранулированного топлива из биомассы.Новая экономичная печь, которая может использоваться для приготовления пищи и обогрева, была разработана на основе технологии абсорбирующих горелок, разработанных зарубежными странами, и, в соответствии с конкретной ситуацией в Китае, ее камера сгорания использует метод подачи вторичного воздуха, обеспечивающий достаточное сгорание и высокую теплоотдачу. эффективность. Защита окружающей среды и энергосбережение для обогревателя была разработана на основе импорта передовых зарубежных каминов и совмещена с нашей реальной ситуацией. За счет изменения размера машины, улучшения системы подачи пеллет и увеличения площади теплообменной трубы этот тип нагревателя подходит для домашнего использования.
3.3 Тенденции развития и советы
3. 3.1 Правительство постоянно совершенствует соответствующую политику производства и использования топливных гранул из биомассы и устанавливает систему стандартов топлива.
В настоящее время в нашей стране приняты соответствующие законы и программы по энергии биомассы, также был принят ряд систем топливной промышленности на пеллетах, и мы создали стандартную систему топливных гранул биомассы. Однако наша промышленность по производству топливных пеллет находилась на ранней стадии развития и не была полностью принята рынком.Нам необходимо разработать конкретную политику и меры для содействия использованию и использованию пеллетного топлива и гарантировать, что существующие законы и политика могут работать эффективно. Нам необходимо оказать большую поддержку, особенно в производстве оборудования и использовании исследования рынка пеллетного топлива: сделать совершенное техническое состояние и стандарт по аспектам печей, котлов и камер сгорания, работающих на биомассе.
3. 3.2 Улучшение системы обеспечения качества и создание национального центра сертификации топлива из биомассы и оборудования для сжигания.
EU имеет зрелую и безупречную систему гарантии качества, прежде чем пеллетное топливо и оборудование для сжигания появятся на рынке, они должны быть протестированы в отделе инспекции. Поскольку пеллетное топливо в Китае только началось, система гарантии несовершенная, пеллетное топливо и пеллетное топливо оборудование для сжигания выходит на рынок без тестирования и сертификации, что приводит к значительному различию качества топливных гранул и оборудования для сжигания, это влияет на прогресс в отрасли производства твердого гранулированного топлива из биомассы, поэтому на основе существующего научно-исследовательского учреждения нам необходимо создать комплексные исследовательские институты в совокупность исследований, обнаружения и триединства изучения рынка для содействия изучению рынка, усвоения последней информации о рынке, ускорения трансформации научных исследований в рынок и обеспечения того, чтобы научные исследования отражали его огромную социальную и экономическую ценность : в то же время мы должны учиться из ЕС в опыте тестирования топливных гранул, создали национальную биомассу, чтобы крышка пеллетного топлива и испытательного центра горючего оборудования.
3.3.3 Увеличить зону типичной демонстрационной рекламы, реализовать крупномасштабное производство и регулярно комбинировать с источником сырья
Пеллетное топливо в нашем округе основано на соломе сельскохозяйственных культур, учитывая проблемы радиуса транспортировки, стоимости и хранения в соломе , наши предприятия по производству пеллетного топлива должны ориентироваться на средние предприятия, которые производят 10000 ~ 20000 тонн в год, чтобы мы могли реализовать крупномасштабное производство, в том числе с учетом огромной территории, большой тепловой разницы и различных характеристик соломинок, демонстрационные проекты должны быть созданы в различных областях, чтобы продвинуть развитие нашей топливной промышленности из гранул из биомассы и сделать ее полностью коммерциализированной и маркетинговой.
3.3.4 Дальнейшее изучение механизма формования в биомассе, Улучшение конструкции оборудования и минимизация количества повреждаемых частей и снижение энергопотребления оборудования для гранул имеет проблему высокого энергопотребления, а детали формования (экстрактор шнека, формование, кольцевая матрица, пресс-валок и т. д.} легко изнашиваются. Мы должны провести исследования механизма формования материала биомассы, изменить способ формования и, по возможности, уменьшить трение между материалом и формованием, чтобы продлить срок службы штампа и снизить стоимость.Древесные пеллеты в мелкой упаковке на рынке США — 170 долларов за тонну, в крупной упаковке — около 135 долларов за тонну; Стоимость доставки по Швеции 150 $ / т. Цена FOB на древесные гранулы навалом в Амстердаме составляет 80 долларов за тонну. Если мы импортируем технологию ETS для производства древесных пеллет, себестоимость производства намного ниже, чем за рубежом. По расчетам, себестоимость массового производства составляет около 240 юаней / тонну, розничная цена — 329 юаней / тонну (39 долларов за тонну), несомненно, что эта цена не только на международном рынке, но и в Китае может побороться с ценой на уголь. Таким образом, улучшенная технология также является одним из эффективных методов повышения коэффициента использования.
IV. Исследования в области технологии гранулирования с кольцевой матрицей
4.1 Структура и принцип работы гранулятора с кольцевой матрицей
Гранулятор с кольцевой матрицей состоит из двигателя, редуктора скорости, главной оси, приводного вала, кольцевой матрицы, прижимного ролика, машины принудительной подачи, ножевого компонента, Корпус и шибер. Двигатель приводит в движение кольцевую матрицу и заставляет ее вращаться «входящий материал в кольцевую матрицу приводит во вращение валок, когда материал доставляется в рабочую зону через машину принудительной подачи» с вращением кольцевой матрицы и прижимного валка » материал до того, как прижимной валок был раздавлен в зону сжатия, материал был раздавлен в этой области «промежуток в материале быстро сузился,« напряжение и плотность внутри материалов увеличились », упругая деформация материала превратилась в пластическую деформацию», когда материал достигнув своей плотности, он будет вытеснен через отверстие матрицы, и после определенного временного давления «материал с определенной плотностью выдавил отверстие матрицы» и превратился в гранулы биомассы топливо.
4.2 Состояние исследований технологии гранулирования с кольцевой матрицей
Принцип работы всего процесса разработки гранулятора с кольцевой матрицей остался прежним, но уровень производства и технические характеристики значительно улучшились. В настоящее время широко используемый типовой гранулятор с кольцевой матрицей включает в себя: гранулятор с кольцевой матрицей компании CPM имеет конструкцию привода редуктора с угловым редуктором, он может осуществлять двухскоростной обмен в ручном режиме. Это называется гранулятором с подвижной моделью, в котором неподвижная кольцевая матрица вращается на полом валу большой зубчатой передачи, прижимной валок закреплен на твердом валу с помощью фиксированного устройства.В кольцевой матрице используются трехкомпонентные кольцевые зажимы для фиксации, простота установки и оснащение автоматической системой циркуляционной смазки, безопасность в использовании. Гранулятор с кольцевой матрицей использует двухвалковый пресс, кольцевую матрицу, конструкцию устройства с клиноременной передачей с одним двигателем. Он имеет высокую эффективность производства, низкие эксплуатационные расходы, простую конструкцию и удобное управление. Система может работать с автоматической смазкой и контролем. В нем используется однодвигательный привод, полый вал, кольцевая матрица, шпиндель, ролик, большой ременной привод в сборе и т. Д., Натяжение ременного привода поддерживается хвостовой консолью шпинделя, который является подшипником высокой нагрузки и в состоянии частичной нагрузки.К проектированию, расчету и согласованию предъявляются высокие требования. Гранулятор с кольцевой матрицей компании Munch состоит из двух мельниц: кольцевой матрицы и конической роликовой плашки. Конструктивная форма гранулятора с кольцевой матрицей такая же, как и одноступенчатый синхронный зубчатый ремень компании UMT. В грануляторе с кольцевой матрицей применен клиноременной привод от Munch, большой шкив широкий, основание двигателя выполнено из чугуна, машина довольно тяжелая, но гладкая, низкий уровень шума, пример большого шкива энергоэффективный.
В фиксированной конструкции кольцевой матрицы необходимо использовать трехкомпонентный кольцевой зажим CPM, если использовать болт, на это потребуется много времени. Система может работать с автоматической смазкой и контролем. Трехвалковый гранулятор с кольцевой матрицей — подарок компании UK UMT. типичный гранулятор с кольцевой матрицей. Многие компании производят аналогичные продукты в стране и за рубежом, способ привода включает тип зубчатого и ременного типа. Все грануляторы с трехвалковой кольцевой матрицей Crown используют синхронную зубчатую ременную передачу, среди них тип 350B — двухмоторная синхронная зубчатая ременная передача, другие — все используют двухмоторные клиновые ремни и вторичную синхронную зубчатую ременную передачу.
V. Заключение
У завода по производству пеллет из биомассы будет светлое будущее, однако из-за различных типов ресурсов опыт разработки в зарубежных странах не подходит для нашей страны. Мы должны разработать соответствующую политику для поощрения и эффективного контроля в отношении топливных гранул из биомассы и стандарт разработки
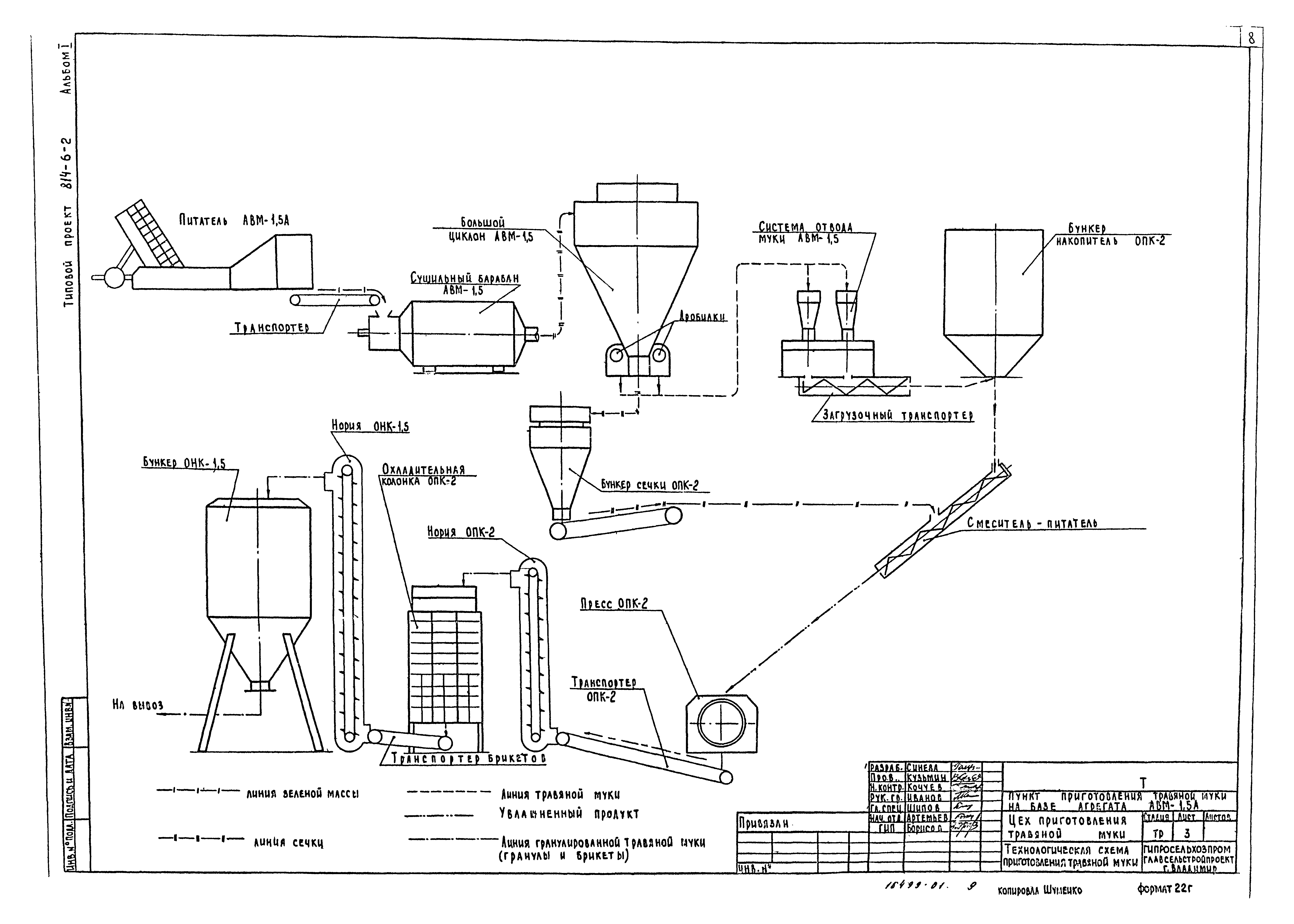
% PDF-1.7 % 1 0 объект >>>] / OFF [] / Order [] / RBGroups [] >> / OCGs [6 0 R 7 0 R] >> / Pages 3 0 R / StructTreeRoot 8 0 R / Тип / Каталог >> эндобдж 5 0 obj > / Шрифт >>> / Поля [] >> эндобдж 2 0 obj > поток 2020-01-23T14: 36: 09 + 01: 002020-01-23T14: 36: 09 + 01: 002020-01-23T14: 36: 09 + 01: 00Приложение Microsoft® Word для Office 365 / pdf
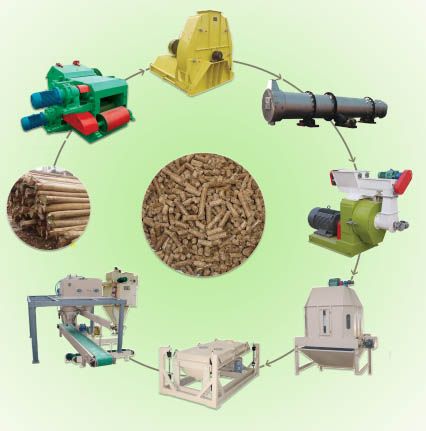
Как производятся торрефицированные древесные гранулы? Посмотреть процесс изготовления пеллет
Прежде чем мы посмотрим, как производятся торрефицированные древесные гранулы, нам нужно обсудить, что они из себя представляют. Лучше всего думать о торрефицированных древесных гранулах как о следующей эволюции топливных гранул. В качестве сырья в основном используется древесина. Однако можно использовать практически любую биомассу, включая коноплю. Торрефицированные гранулы во всех отношениях превосходят стандартные гранулы и решают некоторые из текущих проблем с топливными гранулами.Например, они имеют более высокую плотность энергии и не впитывают влагу. В случае торрефицированных древесных гранул применяется тот же общий процесс, что и для производства древесных гранул. Однако есть некоторые важные отличия, о которых я расскажу ниже.
Первое, что вы заметите, это то, что торрефицированные древесные гранулы имеют черный цвет. Заявление об отказе от ответственности: Привет! Кстати . .. любые ссылки на этой странице, ведущие к продуктам на Amazon или других сайтах, являются партнерскими ссылками, и я получаю комиссию, если вы совершаете покупку.
Торрефицированная биомасса известна под несколькими другими названиями, такими как «искусственный уголь» и «биоуголь». Это потому, что в основном это торрефицированные древесные гранулы, искусственный уголь. Разница между биоуглем и углем на основе ископаемого топлива заключается в возрасте углерода.
Когда мы сжигаем уголь на основе ископаемого топлива, мы выделяем углерод, который не участвовал в углеродном цикле в течение миллионов лет. Следовательно, увеличивается процентное содержание углекислого газа в нашей атмосфере. Однако торрефицированная древесина является частью текущего углеродного цикла.Следовательно, сжигание этого материала возвращает только тот же углерод в существующий цикл. Новая биомасса, выращенная вместо нее, поглотит эти выбросы углерода при сжигании гранул, и цикл начнется снова. Вот почему процесс называют углеродно-нейтральным.
Если вы сравните эти стандартные древесные гранулы с торрефицированными древесными гранулами на изображении выше, вы можете четко увидеть разницу: Изображение — Amazon
Как производятся торрефицированные древесные гранулы
Видео ниже от Blackwood Technology дает хороший обзор их процесса торрефицированных древесных гранул.Процесс изготовления древесных гранул начинается очень похоже на стандартный процесс изготовления гранул. Первоначальная древесина сначала измельчается, а затем обрабатывается на молотковой мельнице. Затем древесина сушится с 50% влажности до 15% с помощью стандартной сушилки для биомассы. Для нормального производства древесных гранул, если влажность ниже 15%, материал готов для гранулирования. Однако именно здесь процесс отличается от обычного завода по производству древесных гранул.
youtube.com/embed/LMlrisB4lxc?feature=oembed» frameborder=»0″ allow=»accelerometer; autoplay; encrypted-media; gyroscope; picture-in-picture» allowfullscreen=»»/> Blackwood Technology описывает процесс торрефицированных древесных гранул.Для производства торрефицированных древесных гранул биомасса затем нагревается примерно до 300 градусов Цельсия в среде с нулевым содержанием кислорода, чтобы не происходило горения. Примерно через 30 минут получается гораздо более чистая форма углеродного топлива с очень низким содержанием влаги. Затем материал обрабатывается с помощью серии грануляторов с кольцевой матрицей для производства торрефицированных древесных гранул.
Каковы преимущества термообработанных древесных гранул?
Стандартные древесные гранулы очень легко впитывают влагу.Вот почему они являются таким хорошим продуктом для подстилки для лошадей. Поджаренные древесные гранулы отталкивают влагу. Поэтому они решают одну из ключевых проблем, связанных с нынешним топливом на древесных гранулах. Они также не производят запаха, но видны дыма и содержат гораздо более высокое содержание энергии, чем современные топливные гранулы. 1 кг торрефицированных древесных гранул содержит такое же количество энергии, как 2 кг стандартных гранул премиум-класса.
При гораздо более высокой плотности энергии это означает, что потребителям пеллетного топлива потребуется меньше поставок пеллетного топлива. Это также означает, что вам понадобится только склад для пеллет, размер которого будет вдвое меньше, чем для стандартных древесных пеллет. Еще одним преимуществом является меньшая транспортировка торрефицированных древесных гранул. Поскольку клиентам требуется меньше топлива для удовлетворения своих потребностей в отоплении, одна и та же цистерна для пеллет может обслужить вдвое больше клиентов.
Только ли дерево можно обжигать?
Нет, вы можете производить торрефицированные гранулы из любой биомассы, включая просо, мискантус, солому и коноплю.Поэтому технологии торрефицированного топлива могут сыграть большую роль в том, чтобы сделать пеллетное топливо более жизнеспособным вариантом для потребителей.
Если вы хотите узнать больше о процессе производства гранул, я бы очень рекомендовал The Pellet Handbook: eBook and Hardcover — Amazon
фактов о производстве древесных пеллет и процессе гранулирования, которые вы должны знать
Пеллеты представляют собой сжатое органическое вещество несферической формы. Что касается древесных пеллет, они производятся из промышленных отходов, получаемых в результате измельчения, и отходов производства изделий из древесины в мебельной и строительной промышленности.Для производства гранул такого типа вам потребуется машина для производства древесных гранул.
Запуск завода по производству малых древесных пеллет
Обладая многолетним практическим опытом в области производства древесных гранул, мы накопили достаточные знания в производстве премиальной машины для производства древесных гранул и комплектного оборудования. В нашей компании есть собственная техническая команда и высокоэффективная административная система. На данный момент мы уже экспортировали комплектную установку по производству древесных гранул и различное оборудование для обработки гранул (как с кольцевой фильерой, так и с плоской матрицей) в более чем 50 стран и регионов по всему миру. Мы навсегда ваш поставщик оборудования для гранулирования.
Машины в установке малого гранулирования
Ниже приводится небольшой блок гранулирования HOT Sell, который соединяет дробильную машину, сушильную машину, пресс для гранул, охладитель древесных гранул и конвейеры.
Машины для производства малых древесных гранул
Производственный процесс этого небольшого завода по производству древесных гранул состоит из пяти этапов. Это разбито ниже:
- Измельчение : Первый этап процесса и сырье, в нашем случае древесина, разбивается на соответствующие части.Дробилку еще называют молотковой мельницей. Размер гранул определяется пользователем, но стандартные размеры варьируются от 2 до 5 мм.
- Сушка : Это второй этап процесса, целью которого является снижение содержания влаги в древесине до менее 10%. Для этого используется осушитель с воздушным потоком.
- Гранулирование / изготовление пеллет ; Это третья и самая важная часть всего этого процесса.Пресс для гранул с плоской матрицей является составной частью используемой системы или установки для производства гранул. Этот пресс может приводиться в действие различными типами двигателей — дизельным, электрическим, бензиновым и т. Д. На гранулах слой — это то место, где форма и форма древесного биотоплива форматируются.
- Охлаждение : Это последний шаг.
Можно выбрать охлаждение гранул естественным путем или включить охладитель в установку для гранулирования. Само собой разумеется, что последний вариант увеличивает стоимость процесса.Первый вариант предполагает, что гранулы просто лягут на землю и остынут. Эти гранулы могут быть горячими до 90 градусов Цельсия, когда они выходят из машины для гранулирования древесины, поэтому важно обращаться с ними осторожно.
Свяжитесь с нами сейчас, чтобы получить более подробную информацию о нашей линии по производству малых древесных гранул и стоимости этой небольшой единицы. Искренне к вашим услугам!
Часто задаваемые вопросы о машине для производства древесных гранул
Машина для производства пеллет с плоской матрицей для переработки древесных отходов и опилок
Древесные пеллеты из нашей пеллетной машины
Краткий и длинный ответ на этот вопрос заключается в том, что они используются в качестве биотоплива.Помимо топлива, их можно использовать как абсорбент или как подстилку для лошадей.
После выхода древесных гранул из машины для производства древесных гранул их можно хранить на складе, в бункере или даже в мешке. Какой бы вариант хранения вы ни выбрали, помните, что крайне важно не допускать попадания влаги на гранулы.
Ответ на этот вопрос предельный. Выбросы опасных органических соединений при сжигании древесных гранул являются относительно низкими по сравнению с другими формами сжигания, в то время как какие-либо неблагоприятные последствия изменения климата в результате сжигания гранул еще не отмечены ни в одном крупном исследовании.
Если вы обдумываете идею использования древесных гранул в качестве горючего источника энергии, вам нужно взглянуть на перечисленные выше преимущества и сделать первый шаг, приобретя машину для производства древесных гранул . ABC Machinery владеет двумя брендами — GEMCO и KMEC. Мы являемся одним из ведущих производителей оборудования для гранулирования и брикетирования биомассы. У нас также есть опыт в разработке линий по производству древесных гранул в промышленных масштабах. Ваши инвестиции не должны быть огромными, поскольку мы предлагаем создать и ввести в эксплуатацию для вас небольшой завод по производству древесных гранул, который может легко разместиться на вашем заднем дворе и доставлен в гараж.Свяжитесь с нами сегодня.
Wood Pellet — обзор
13.4.3 Пеллеты и брикеты
Пеллеты из прессованных опилок или древесных стружек доступны во многих частях мира уже более нескольких десятилетий. Поскольку гранулы спрессованы, они представляют собой более концентрированную форму топлива, чем древесная щепа. Следовательно, им требуется меньше места для хранения, и с ними легче обращаться. Производство древесных гранул требует больше энергии, чем древесная щепа, а капитальные затраты на производство завода высоки; пеллеты, следовательно, дороже щепы.
Древесные гранулы обычно изготавливаются из прессованных опилок, которые являются отходами других отраслей промышленности (например, лесопильных заводов). Гранулы скрепляются естественным лигнином в древесине — обычно связующий клей не требуется. Лигнин составляет примерно от четверти до трети сухой древесины. Он укрепляет древесину, а также обладает водонепроницаемыми свойствами.
Древесные гранулы имеют очень низкое содержание влаги, обычно 6-10%, что означает, что древесные гранулы являются очень хорошим источником энергии, поскольку очень мало энергии в гранулах используется для испарения влаги.Общие свойства древесных гранул:
Влажность: 3,5% –5,5%
Зола: 0,2% –0,5%
Теплотворная способность: 8800 БТЕ / фунт
Насыпная плотность: 600–750 кг / м
Гранулы очень плотные, а низкая влажность (ниже 10%) позволяет их сжигать с очень высокой эффективностью сгорания. Правильная геометрия гранул и небольшой размер позволяют производить автоматическую подачу с очень точной калибровкой.Их высокая плотность также обеспечивает компактное хранение и рациональную транспортировку на большие расстояния.
Древесная щепа — это твердое топливо, получаемое из древесины, которое часто используется в качестве сырья для технической обработки древесины. В промышленности обработка стружки коры часто отделяется после лущения бревен из-за различных химических свойств. Древесная щепа также может использоваться в качестве древесного топлива.
Пеллеты можно использовать в качестве топлива для различных бытовых приборов и систем отопления. Самыми маленькими из них являются пеллетные печи мощностью до 9 кВт, которые подходят для отопления отдельных помещений.Эти печи имеют электронное управление, могут выдавать регулируемую тепловую мощность и требуют дозаправки только один раз в несколько дней. Пеллетные котлы доступны в широком диапазоне мощности от небольших домашних до крупных промышленных масштабов для обогрева школ и больниц. Для бытового потребителя пеллеты представляют собой наиболее удобный вид дровяного отопления. В Скандинавии древесные гранулы доставляются цистернами и перекачиваются в силосы для хранения, откуда они автоматически поступают в котел.
Древесные гранулы используются в печах специальной конструкции.Пеллеты обычно производятся из древесных отходов лесопильных заводов. Древесина проходит довольно длительный процесс трансформации, прежде чем окончательно экструдируется в твердые гранулы. Несмотря на переработку, топливо остается углеродно-нейтральным и поэтому менее вредно для окружающей среды, чем другие ископаемые виды топлива. Для коммерческих предприятий, как и в случае с любым древесным топливом, древесные гранулы не облагаются налогом на изменение климата. В настоящее время в Соединенном Королевстве имеется ограниченное количество заводов по производству окатышей, хотя есть некоторые стимулы производить их из местных источников.Тем временем некоторые пеллеты импортируются. Гранулы для бытовых обогревателей и бойлеров поставляются в предварительно упакованных мешках, обычно весом 22 фунта (10 кг), что делает их удобными по размеру для хранения и загрузки в бункер. Для более крупных моделей котлов пеллеты могут поставляться оптом, но при этом должен быть доступен соответствующий бункер, подключенный к котлу. В настоящее время большая часть пеллет будет поставляться печным цехом, который продает котлы, но для других поставщиков см.
Нашу страницу с ссылками ниже.
Топливные брикеты (иногда называемые топливными брикетами) — особенно брикеты, изготовленные из угля (Speight, 2013), стали важным бизнесом в 20 веке. В 1950-х годах было разработано несколько экономических методов изготовления брикетов без связующего. Множество заводов по всему миру производили буквально десятки миллионов тонн годного к употреблению и экономичного материала, который удовлетворял бытовые и промышленные потребности в энергии. Во время двух мировых войн домашние хозяйства во многих европейских странах изготавливали собственные брикеты из пропитанной макулатуры и других горючих бытовых отходов с помощью простых рычажных прессов (Lardinois and Klundert, 1993).Современные промышленные брикетировочные машины, хотя и намного более крупные и сложные, работают по тому же принципу, хотя продаваемые брикеты сейчас продаются по более высокой цене для периодических барбекю на заднем дворе, а не для повседневного использования.
На протяжении более 100 лет неформальные сборщики отходов в Каире отделяют и сушат органические отходы для продажи в качестве твердого топлива для бытового использования. Этот процесс несколько затих, когда стали доступны источники ископаемого топлива. Переход на традиционные виды топлива может оказаться выгодным для тех, кто может себе это позволить, но с учетом экономических и энергетических условий во многих городах городские и сельскохозяйственные отходы остаются жизнеспособным альтернативным топливом.
Брикетирование переживает возрождение, в основном из-за слияния трех критических факторов. Во-первых, последние разработки в области обработки и связывания брикетов резко изменили экономику использования топливных брикетов в качестве энергетического ресурса. Во-вторых, нехватка топливной древесины становится все более острой в большинстве развивающихся стран. Наконец, неуклонно растет озабоченность по поводу окружающей среды, направленная на решение проблемы удаления бытовых и городских отходов, и эту дилемму можно решить с помощью брикетирования.
13.4.3.1 Производство брикетов
Как правило, производство брикетов (брикетирование) включает сбор горючих материалов, которые нельзя использовать как таковые из-за их низкой плотности, и их прессование в твердый топливный продукт любой удобной формы, который можно сжигать. как дерево или уголь. Таким образом, материал сжимается, чтобы сформировать продукт с более высокой объемной плотностью, более низким содержанием влаги и однородным размером, формой и свойствами материала. Брикеты легче упаковывать и хранить, дешевле транспортировать, удобнее использовать, а их характеристики горения лучше, чем у исходных органических отходов.
Сырье брикета должно связываться при сжатии; в противном случае, когда брикет вынут из формы, он рассыпется. Улучшенная когезия может быть получена с помощью связующего, но также и без него, поскольку при высокой температуре и давлении некоторые материалы, такие как древесина, связываются естественным образом. Связующее не должно вызывать образование дыма или липких отложений, а также следует избегать образования избыточной пыли. Могут использоваться два разных типа связующих. Горючие связующие получают из природных или синтетических смол, навоза животных или обработанных обезвоженных осадков сточных вод.К негорючим вяжущим относятся глина, цемент и другие адгезивные минералы. Хотя горючие связующие являются предпочтительными, негорючие связующие могут быть подходящими, если используются в достаточно низких концентрациях. Например, если органические отходы смешаны со слишком большим количеством глины, брикеты не будут легко воспламеняться или гореть равномерно. Подходящие связующие включают крахмал (5–10% мас.) Или мелассу (15–25% мас.), Хотя их использование может оказаться дорогостоящим. Важно определить дополнительные недорогие материалы для использования в качестве связующих для брикетов в Кении и их оптимальные концентрации.Точный метод подготовки зависит от брикетируемого материала, как показано в следующих трех случаях прессования сахарного жома, опилок и городских отходов в брикеты для приготовления пищи.
13.4.3.2 Брикеты из жмыха
Излишки жмыха представляют собой проблему утилизации для многих сахарных заводов. Технология брикетирования остается простой и включает следующие этапы: (1) измельчение, при котором жом измельчается, раскатывается или забивается молотком, (2) сушка, при которой влага удаляется сушкой на открытом воздухе или с использованием принудительного нагретого воздуха в большом вращающемся помещении. барабан, (3) карбонизация, при которой жмых сжигается при ограниченном количестве кислорода в подземной яме или траншеи до тех пор, пока он не карбонизируется до древесного угля, (4) подготовка исходного сырья, при которой карбонизированный жмых смешивается со связующим, таким как глина или патока , (5) прессование и экструзия, при которых материал пропускается через экструдер с механическим или ручным управлением для формирования рулонов древесного угля, (6) сушка, при которой рулоны сушатся на воздухе в течение 1-3 дней, что приводит к их разрушению. на куски и (7) упаковка, в которой брикеты подготавливаются к продаже.
13.4.3.3 Брикеты из древесных опилок
Опилки являются отходами всех видов первичной и вторичной обработки древесины. От 10% до 13% бревна превращается в опилки при фрезеровании. Опилки громоздкие, поэтому их дорого хранить и перевозить. Кроме того, теплотворная способность опилок довольно низкая, поэтому брикетирование является идеальным способом уменьшить объем, увеличить плотность и, таким образом, повысить теплотворную способность. Оборудование, необходимое для производства брикетов из опилок, состоит из сушилки, пресса и экструдера с коническим шнеком и большим вращающимся диском.
Брикеты из опилок формируются под достаточно высоким давлением, чтобы обеспечить сцепление между частицами древесины. При этом лигнин размягчается и связывает брикет, поэтому дополнительное связующее не требуется. Использование брикетов из опилок имеет несколько преимуществ, в том числе (1) цена, которая обычно примерно такая же, как и у топливной древесины, но гораздо удобнее использовать, поскольку они не требуют дальнейшей резки и измельчения, (2) хорошие характеристики горения в любом виде твердых топливная печь и бойлер, (3) быстрое зажигание с последующим чистым сжиганием с оставлением только 1-6% минеральной золы, (4) без серы и горение без запаха, и (5) теплосодержание, которое почти эквивалентен по теплосодержанию угля среднего качества.
13.4.3.4 Брикеты для городских отходов
Удаление твердых отходов (мусора) — одна из наиболее серьезных проблем городской окружающей среды в развивающихся странах. Многие муниципальные власти собирают и надлежащим образом удаляют (в местах, отличных от свалок) менее половины этих отходов. Этот сбой объясняется (1) недостаточным количеством свалок, (2) разнообразием экологических норм, (3) отсутствием достаточных мощностей для обработки и переработки отходов и, наконец, что не менее важно, (4) запланированным устаревание упаковки и многих предметов, составляющих основу отходов.
Открытый сброс или сброс сырой нефти — наиболее распространенный метод, используемый муниципальными властями. Отходы представляют опасность для здоровья, когда они разбросаны по улицам и на свалках. В настоящее время общепринятой экологической философией является то, что отходы имеют ценность и должны использоваться на основе принципов сокращения, повторного использования, восстановления и переработки. Благодаря вторичной переработке городские отходы можно превратить в полезные продукты. В частности, макулатура и листья являются потенциально важным альтернативным источником топлива для приготовления пищи.
Переработка органических горючих материалов в топливные брикеты способствует решению городских проблем, таких как получение доходов, недостаток земли для удаления отходов и поддержание качества окружающей среды. Поскольку ресурсы Земли ограничены, для достижения приемлемого уровня обращения с органическими отходами необходимо более эффективное извлечение и использование ресурсов. Улучшение утилизации органических отходов может восстановить различные естественные циклы, тем самым предотвращая потерю сырья, энергии и питательных веществ.
С другой стороны, ожидается, что спрос на энергию во многих странах приведет к увеличению выбросов парниковых газов в результате сжигания ископаемого топлива. Существует острая необходимость в продвижении экологически безопасных технологий, и брикетирование топлива, по-видимому, является одной из таких технологий, которая удовлетворяет многочисленные потребности общества и окружающей среды.
Текущие потребности сосредоточены на поиске лучших связующих для брикетов из жома, улучшенной теплотворной способности и горения за счет производства брикетов более высокой плотности, внедрения более эффективных методов экструзии и снижения производственных затрат.
Как производятся пеллеты?
Процесс гранулирования
Грузовики с сырьем доставляются на грануляторы каждый день и могут поступать в самых разных формах. Некоторым сырьем могут быть опилки, щепа, обрезки лесопилок и даже целые деревья, непригодные для производства пиломатериалов. Сырье может быть зеленым или свежесушенным, частично высушенным или даже высушенным в печи. При одинаковой обработке этого сырья конечный продукт имеет постоянное содержание влаги, теплотворную способность, зольность и характеристики горения.Очень важно, чтобы все производители пеллет производили пеллеты в соответствии с одним и тем же стандартом, чтобы пеллетные устройства горели и нагревались постоянно. Вот некоторые из процессов:
Дробилки и молотковые дробилки
Некоторые заводы по производству пеллет начинают свой процесс с того, что большие куски древесины пропускаются через дробильную машину для обработки. Они необходимы только для заводов, которые принимают это неоднородное сырье. Есть много различных конфигураций заводов по производству пеллет в зависимости от их источника сырья.Хотя все они не имеют измельчителей, почти все они имеют молотковую мельницу в начале процесса измельчения. Эти машины собирают опилки и древесную стружку и измельчают их до однородного меньшего размера, что обеспечивает быструю и стабильную сушку и продавливание через матрицу для гранул.
Сушилки
Если в грануляторе используется свежее нарезанное сырье, материал, подверженный воздействию погодных условий или высокой влажности, или смесь сырьевых материалов, которые могут содержать влагу, они должны высушить опилки до постоянного уровня влажности.В больших барабанах сушилки можно использовать природный газ, пропан, горелки для опилок или другое топливо для нагрева барабана, отводя лишнюю влагу.
Гранулятор
После высыхания опилки под высоким давлением продавливаются через матрицы. В результате этого процесса опилки нагреваются и выделяют в древесине натуральный лигнин, который связывает опилки. Мельница также определяет плотность гранул, диаметр, долговечность и длину. Все эти характеристики очень важны для стабильной работы пеллетного оборудования.
Охлаждение и хранение
Гранулы выходят из мельницы при температуре от 200 до 250 градусов и становятся мягкими. Градирня используется для снижения температуры и упрочнения гранул. После охлаждения они обычно хранятся в большом бункере до упаковки в мешки или распределения навалом.
Упаковка в мешки или навалом
Самый распространенный метод распространения в США — это укладывать гранулы в 40-фунтовые пластиковые мешки и складывать их на поддоны или салазки.Эти салазки могут содержать от одной до полутора тонн топлива, в зависимости от канала распределения. Упаковка гранул в полиэтиленовые пакеты, поддоны, пакеты с внешним покрытием, термоусадочную пленку, а также рабочую силу и оборудование для их штабелирования и упаковки добавляет от 25 до 30 долларов за тонну. Затем эти салазки отправляются и доставляются по всей стране для получения потребителем в точках розничной торговли или доставки на дом.
Гранулы насыпью загружаются из бункера гранулятора прямо в грузовики для доставки в контейнеры для насыпного хранения.Грузовики для массовых грузов дороже обычных бортовых грузовиков, но имеют гораздо более эффективную систему обработки, перевалки и доставки. В США в настоящее время используется очень мало бытовых систем обработки сыпучих материалов. Перейдите на нашу страницу массовой доставки для получения дополнительной информации.
.