Этапы производства керамзита | ООО «АКЗ» (Алексинский керамзитовый завод)
Для того чтобы материал получился высокого качества, важно грамотно подобрать сырье и подходящую технологию производства. ООО «АКЗ» раскрывает секреты всех этапов и технологию производства керамзита.
Для того чтобы материал получился высокого качества, важно грамотно подобрать сырье и подходящую технологию производства. Технология производства керамзита включает следующие основные этапы:
- добыча сырья (глины) в карьере и его транспортирование в глинозапасник;
- лабораторные испытания;
- дробление глины. На выходе получаются сырцовые гранулы установленного размера;
- термическая обработка сырцовых гранул, включающая сушку, обжиг и последующее охлаждение продукта;
- при необходимости дробление готового продукта;
- контроль качества производимого товара;
- сортировка керамзита по фракциям;
- складирование товара;
- фасовка товара;
- отгрузка заказчику.
Разработку месторождений глинистых пород производят открытым способом. Для добычи глинистого сырья используют одноковшовые и многоковшовые экскаваторы, ведущие разработку в карьере по всей высоте уступа, при необходимости с выделением отдельных пластов материала.
Мягкие глинистые породы добывают в карьерах, работающих сезонно, камнеподобные — в течение всего года. Для обеспечения непрерывной работы заводов устраивают глинохранилища вместимостью до полугодового запаса сырья с предохранением его от промерзания. Запасы глины также хранят в промежуточных конусах, где она вылеживается в течение нескольких месяцев на открытом воздухе.
В результате температурных воздействий, особенно мороза, переменного увлажнения и высушивания происходит предварительное разрушение естественной структуры сырья, значительно облегчающее его последующую переработку в однородную формовочную массу.
Технологические особенности производства керамзита
В качестве сырья для изготовления данной категории нерудных материалов используются преимущественно осадочные глинистые породы.
Результатом обработки исходного сырья являются сырцовые гранулы нужного состава и размеров. Они подвергаются термической обработке — просушиванию, обжигу и охлаждению. На следующем этапе полученный материал сортируется и при необходимости дробится на мелкие фракции.
Оборудование для производства керамзита
Изготовление материала осуществляется с применением широкого спектра дорогостоящего оборудования — смесителей, специальных станков для разрыхления глины, камневыделительных и дырчатых вальцов, сушильных барабанов, печей для обжига, бункеров, пневматических транспортеров и аппаратов для сортировки гравия. Также для производства керамзита используются лотки, конвейеры, силосные банки и другие приспособления, объединенные в технологические линии.
Более подробную информацию читайте в нашей статье «производство керамзита».
Добыча сырья (глины)
1 этап производства керамзита.
Добыча сырья (глины)
2 этап производства керамзита.
Добыча сырья (глины) однокошковым экскаватором. 3 этап производства керамзита.
Добыча сырья (глины) однокошковым экскаватором. 4 этап производства.
Транспортироване глины в глинозапасник
5 этап производства керамзита
Транспортироване глины в глинозапасник
6 этап производства керамзита
Дробление глины
Дробление глины
8 этап производства керамзита
Транспортирование глины в сушильный барабан 9 этап производства керамзита
Термическая обработка сырцовых гранул
10 этап производства керамзита
Термическая обработка сырцовых гранул
11 этап производства керамзита
Термическая обработка сырцовых гранул
12 этап производства керамзита
Термическая обработка сырцовых гранул
13 этап производства керамзита
Транспортирование готового продукта в силоса 14 этап производства керамзита
Готовый продукт
15 этап производства керамзита
Отгрузка готового продукта заказчику
16 этап производства керамзита
Отгрузка готового продукта заказчику
17 этап производства керамзита
Отгрузка готового продукта заказчику
18 этап производства керамзита
Обслуживание оборудования
19 этап производства керамзита
Контроль качества
20 этап производства керамзита
Обслуживание техники
21 этап производства керамзита
Лабороторные испытания
22 этап производства керамзита
Взаимодействие с партнерами
23 этап производства керамзита
Ведение складской логистики.
24 этап производства керамзита.
Созерцание на природу.
25 этап производства керамзита.
Технология производства керамзита
Как известно, слово “керамзит” имеет греческое происхождение и означает “обожженная глина”. Технология производства материала заключается в подготовке глины и последующем тепловом ударе, в результате которого она приобретает вид вспученных гранул, ее внешняя оболочка оплавляется и таким образом герметизируется. Так можно описать процесс вкратце, но давайте рассмотрим его поподробнее.
Керамзит изготавливают из осадочных глинистых и метаморфических камнеподобных пород (глинистые сланцы, аргиллит и т.п.). Они неоднородны, в их составе есть включения кварца, полевого шпата, гидрослюды, железистых и органических примесей. Из всего многообразия сырья лучше всего использовать глины, содержание кварца в которых не превышает 30%.
Для того, чтобы узнать, насколько определенный материал подходит для изготовления качественного керамзита, проводят специализированные исследования — проверяют легкоплавкость, возможность и уровень вспучивания во время обжига, а также его интервал.
Для увеличения коэффициента вспучивания в состав добавляют разнообразные натуральные и искусственные компоненты — мазут, соляровое масло, алунит, перлит и др.
В процессе переработки материалов из сырца получают гранулы. Их сушат, обжигают в печи и охлаждают. Гранулы имеют различный размер и состав, поэтому их сортируют, а при необходимости дробят для получения более мелких фракций. После этапа сортировки керамзит можно складировать, фасовать и отправлять на место использования.
Керамзитовые гранулы получают четырьмя способами: сухим, мокрым, пластическим и порошково-пластическим. Выбор напрямую зависит от качества исходного сырья.
Сухой способ применяют для камнеподобных составов, однородных пород, в которых нет вредных компонентов. Сырье подвергают дроблению и помещают в печь с вращающимся барабаном.
Мокрый способ (иначе — шликерный) заключается в том, что глину укладывают в специальные емкости и разводят водой. Полученную массу называют шликером. Его подают сначала в шламбассейн и далее в печь. В барабане печи материал дробится на гранулы, сушка происходит посредством выделяемого газа. Данный способ более затратный, поэтому его применяют в том случае, когда исходное сырье чрезмерно влажное.
Наиболее распространен пластический способ. Рыхлое сырье увлажняют и перерабатывают в вальцах. Далее из полученной массы изготавливают гранулы и запекают их в печи. Пластика позволяет создавать материал с самыми лучшими эксплуатационными свойствами, его структура гомогенизируется и имеет довольно высокий коэффициент вспучивания.
В случае использования порошково-пластического способа сухое сырье в виде порошка разводят водой. Из полученного состава формируют гранулы, запекают и сушат.
Финальным этапом производства керамзита является охлаждение гранул. Оно начинается еще в печах, т.к. в барабан поступает воздух извне, а далее материал перемещают в аэрожелоба, барабанные холодильники и другие установки.
Прочность керамзита также во многом зависит от скорости охлаждения. Необходимо строго придерживаться технологии, ведь если процесс будет слишком быстрым, гранулы потрескаются, а если наоборот, медленным — керамзит размягчится.
В идеале охлаждение должно происходить по следующей схеме: непосредственно после вспучивания гранул их нужно охладить до 800-900 градусов Цельсия, а далее в течение 20 минут постепенно понижать температуру до 600-700. После этого охлаждать материал можно в любом темпе. В таком случае нет высокого термического напряжения. Это приводит к тому, что в керамзите формируются кристаллические минералы, увеличивающие его прочность.
Керамзитовый завод: технология производства керамзита
3. Сушка сырьевых гранул
Технология производства керамзита
1. Добыча и хранение сырья
Разработка месторождений глинистых пород обычно выполняется открытым способом. Выделяют месторождения мягких и камнеподобных глинистых пород.
Для переработки мягкого глинистого сырья обычно используют различного рода ковшовую технику (экскаваторы, фронтальные погрузчики), которые, как правило, ведут разработку по всей высоте уступа, без разделения на отдельные пласты.
В случае разработки камнеподобных глинистых пород (аргеллиты, сланцы) первоначально производятся буровзрывные работы.
Разработка и добыча мягких глинистых пород производится сезонно (в период промерзания не производится), разработка камнеподобного сырья ведется круглогодично.
Вылеживание глиняного сырья в течение нескольких месяцев происходит в промежуточных конусах на открытом воздухе, благодаря чему в результате температурных воздействий (переменного увлажнения, высушивания, мороза) и выветривания происходит разрушение естественной структуры глиняного сырья, что в дальнейшем существенно облегчает его обработку.
Для обеспечения непрерывности производственного процесса, а также для производства керамзита в зимний период (предотвращение промерзания), хранение запасов сырья осуществляется в глинохранилищах.
2. Переработка исходного сырья
Способ переработки исходного сырья зависит от его характеристик. Существует четыре технологические схемы переработки исходного сырья (производства керамзитового гравия):
сухой способ — самый простой способ производства керамзита, который заключается в дроблении исходного материала с последующим обжигов во вращающихся печах. Как правило, данный способ применим только к камнеподобному глинистому сырью, которое должно иметь однородный состав (исключать вредные включения), достаточно высокий коэффициент вспучивания и влажность не более 9%.
мокрый (шликерный) способ — данный способ заключается в разведении глины в воде в специальных емкостях (глиноболтушках), в результате чего получают глиняную жижу — шликер (влажностью не менее 50%), который в последствии подается в шликербассейны, а затем во вращающиеся печи.
Во вращающихся печах устанавливаются «бьющие» цепи, за счет нагрева которых происходит высушивание шликерной массы и дальнейшее ее размельчение на керамзитовый гранулы.
пластический способ — способ, получивший наибольшее распространение. Данный способ напоминает производство керамического кирпича. Первоначально разрыхленное исходное сырье в увлажненном состоянии перерабатывают в вальцах (или глиномешалках), затем из полученной пластичной массы на ленточных шнековых прессах, либо дырчатых вальцах, формуются гранулы (похожие на цилиндр), которые при дальнейшей обработке окатываются и округляются.
порошково-пластичный способ — способ, который отличается от пластичного лишь структурой исходного сырья. В данном случае исходное сырье не рыхлится, а производится его помол. Затем глиняный порошок увлажняется и формуется в гранулы.
Сушка и обжиг сырьевых керамзитовых гранул производится во вращающихся пачах керамзитового завода. С целью исключения слипания сырьевых гранул в печи может производится дополнительная сушка гранул в сушильных барабанах, где сырьевые гранулы окатываются и становятся прочнее. Также возможно применение слоевых подготовителей, которые также выполняют первоначальную подсушку сырья до нулевой влажности и предварительный нагрев перед обжигом.
Обжиг сырьевых гранул на заводе керамзитового гравия является основным технологическим звеном производства керамзита.
Очень важное значение имеет момент совпадения активного газовыделения с переходом гранул в пиропластическое состояние глины (заьвердевание). Как правило, данный момент происходит при температуре свыше 1100° С.
При обжиге сырьевых гранул необходим быстрый подъем температуры, чтобы влага, находящаяся в сырье, не успела выпариться. В противном случае, гранулы получатся более мелкими и тяжелыми (не вспученными).
Самыми распространенными на керамзитовых заводах считаются однобарабанные вращающиеся печи диаметром 2,0-2,5 метра, длиной 35-40 метров, имеющие уклон 3-5%.
Благодаря чему гранулы постоянно перемешиваются, окатываются и обжигаются, передвигаясь вниз по барабану печи на встречу потоку горячего воздуха.
4. Сортировка керамзита по фракциям
Сортировка полученной продукции по фракциям осуществляется в установках типа «грохот». Обычно применяют барабанно-циллиндрические грохоты, реже — многогранные (бураты).
После сортировки керамзит направляют к месту хранения (складирования) используя конвейерные (ленточные) транспортеры, либо пневматические. Последние не получили особого распространения в силу того, что при данном виде транспортирования возможно повреждение гранул и даже их дробление.
Из чего делают керамзит и технология изготовления своими руками
Это легкий материал с гранулированной пористой структурой, представляющий собой продукт ускоренно обожженной глины и глинистых сланцев под высоким температурным режимом. Керамзитовые шарики отличаются плотно спекшейся оболочкой темновато-бурого оттенка, на изломе практически черного. Сегодня постараемся разобраться детально, из чего делают керамзит, рассмотрим его технические показатели.
Состав и характеристики
В составе керамзита содержатся глина и ее сланцы, процесс изготовления проходит методом обжига исходной сырьевой массы в специальных печах
При температуре в 1 000 – 1 300 градусов глина вспучивается и переходит в пиропластическое состояние. С учетом качества исходного материала, создаваемого температурного режима, длительности процесса обжига и иных технологических особенностей изготовления получаются разные технические показатели материала, самыми значимыми из которых считаются размеры зерен, плотность и объемный вес.
Параметры керамзита определены ГОСТом, регламентирующим качественные показатели строительных материалов с пористой структурой. Часть показателей не регулируется, но они все же остаются важными характеристиками. Основные свойства рассмотрим более подробно:
- фракции керамзита. Их всего три, и размеры варьируются в диапазонах 5 – 10, 10 – 20, 20 – 40 мм.
В отдельную категорию вынесены фракции, используемые в строительстве. Это гранулы и щебенка, размеры которых составляют от 2.5 до 10 мм, и широкие смесевые фракции от 5 до 20 мм;
- марки по насыпной плотности. Всего их семь. Этот параметр определяет плотность материала без учета промежуточных участков, образуемых гранулами или осколками;
- показатель прочности. Гравийный материал насчитывает тринадцать марок, для щебня их несколько меньше – всего одиннадцать. Показатель прочности щебня и гравия одной марки отличается. Между керамзитовыми марками по значениям плотности и прочности прослеживается взаимосвязь – рост плотности влечет за собой увеличение прочности;
- коэффициент уплотнения. Данная величина согласовывается с потребителем и не превышает показатель 1.15. Ее применяют для учета уплотнения керамзита в процессе транспортировки и хранения. Пользуются таким показателем часто при погрузке материала и его реализации;
- тепловая проводимость. Один из важных показателей, определяющий теплоизоляционные возможности керамзита.
Диапазон узкий, что подтверждает высокие теплоизоляционные показатели керамзита, и от роста плотности этот коэффициент увеличивается;
- влагопоглощение. Этот важный параметр показывает изменения качеств керамзита под воздействием воды. Керамзит считается относительно устойчивым материалом, значение влагопоглощения составляет 8 – 20 процентов;
- шумоизоляция. Лучших показателей с помощью керамзита можно достичь, засыпав керамзит под деревянный пол;
- устойчивость к морозам. Из-за низкого влагопоглощения и особенностей основного сырья (глины) керамзит обладает высокими морозоустойчивыми свойствами.
Особенности технологии изготовления
С помощью специальных исследований исходного сырья определяют его пригодность к производству керамзита. Основными требованиями к начальному материалу считаются:
- возможность вспучивания от обжига;
- легкая плавкость;
- определенное время для вспучивания.
В сырье иногда добавляют специальные компоненты, улучшающие вспучивание. Это могут быть мазут или соляровое масло, перлит, анулит и т. п.
Результатом переработки сырья становятся сырцовые гранулы с определенными размерами и составом. Их сначала высушивают, потом обжигают и охлаждают. На очередном этапе производства материал рассортировывается по показателю плотности, при необходимости – дробится, чтобы получились более мелкие фракции. В завершении всего керамзит сортируется, складируется либо отгружается для отправки.
Весь процесс по своей сущности выглядит следующим образом: после подготовки глина подвергается тепловому удару, придающему ей пористость и способствующему процессу вспучивания. Из-за оплавлений оболочки керамзит получает герметизацию и становится прочным.
Добыча исходного сырья
Производственный процесс начинается с добычи исходного материала карьерным способом и его перевозки в глинозапасники. Разработки ведутся открытым способом, для этого используются одно- и многоковшовые экскаваторы. Отдельные пласты не выделяются, добыча идет по всей высоте.
При добыче камнеподобных пород в виде аргиллита и глинистых сланцев, используют буровзрывные работы. Такие породы могут разрабатываться в любое время года, а мягкие – только в подходящий для этого период.
Чтобы производственный процесс шел непрерывно, возводятся специальные морозостойкие хранилища для складирования глины, вмещающие полугодовой запас сырья. Можно под хранение использовать промежуточные конусы, в которых глина под открытым воздухом находится несколько месяцев.
Производство керамзитаПод воздействием температуры, периодических увлажнений и высыханий, структурное строение сырья частично нарушается, что существенно облегчает процесс его последующей переработки в однородную массу.
Способы получения керамзитовых гранул
Для изготовления керамзита применяют один из четырех способов
Сухой способ
Применяется, если керамзит получают из плотных каменистых глинистых пород и сланцев, используется иная технология изготовления. Исходный материал размельчается на дробильном оборудовании до получения зерен размером 1 – 20 мм. Керамзитовое сырье обжигается в барабанной печи, охлаждается, распределяется по фракциям. В таком варианте производства не предусмотрен этап формовки зерен, и конечный продукт отличается кубическими угловатыми очертаниями.
Мокрый способ
Глина помещается в большие емкости, называющиеся глиноболтушками. После этого заливается вода, чтобы получился шликер с уровнем влажности до пятидесяти процентов. Насосными установками его перекачивают в шламбассейны, откуда он попадает во вращающиеся печи. В печных барабанах происходит разбивка на отдельные гранулы, которые просушиваются газами, выделяемыми печью.
Способ подразумевает большой расход топлива, так как уровень влажности шликера достаточно высок. Но с его помощью сырье очищается от каменистых вкраплений, в него вводятся добавки, чтобы получилась однородная масса. Применяется такой вариант для сырья, отличающегося большим показателем влажности.
Пластический способ
Подготовленную природную глину, влажность которой не превышает тридцати процентов, подвергают двум этапам помола на специальных зубчатых вальцах – грубом и тонком. От такого процесса образуются гранулы, диаметр которых составляет 5 – 10 мм, поступающие в сушильные барабаны. В них полуфабрикат просушивается, подвергается окончательной обкатке, пока не приобретет овальные формы. После этого начинается обжиг, для которого в печах создается температурный режим от 800 до 1 350 градусов. Процесс проходит под постоянным вращением печных барабанов. Спекшиеся керамические гранулы, которые увеличили свой диаметр из-за вспучивания, попадают во вращающиеся холодильные установки. После остывания наступает последний этап – керамзит рассеивается по фракциям.
Порошково-пластический способ
Как производится керамзит таким способом? Исходный материал в сухом состоянии доводится до порошкообразной массы, потом в него добавляется вода. В итоге образуется пластичная масса, пригодная для формирования гранул. Способ считается довольно дорогостоящим, потому что приходится дополнительно измельчать сырье. Второй недостаток – гранулы подвергаются дополнительной сушке.
Так как качество керамзита зависит от качественного состояния сырца, глину следует хорошо переработать и сформировать из нее гранулы одинаковых размеров, параметры которых увеличатся при вспучивании.
Оборудование для производства керамзита
Из чего делают керамзит, мы выяснили. Остается разобраться, как устроена производственная линия по изготовлению этого строительного материала. В нее входят следующие агрегаты и приспособления:
- устройства для рыхления;
- дырчатые вальцы;
- глиносмесители;
- барабаны для сушки;
- печи, в которых выполняется обжиг;
- бункеры;
- пневматические транспортеры, ленточные и другие конвейеры;
- лотки;
- сортировщики для гравия.
На первичной обработке исходного материала применяется специальная дробильная установка. Состоит она из узла измельчения, в который входят:
- валы лопастного типа, способные совершать вращательные движения по направлению друг к другу;
- жесткая рама;
- зубчатый привод;
- приемочный бункер.
Как только валы начинают свое вращение, сырье измельчается до необходимых размеров. Специальные добавки вводятся через смесительную установку.
Сырье обжигается в печных устройствах с вращающимися барабанами, имеющими цилиндрические корпуса из стального материала. Конструктивно печь состоит из следующих элементов:
- головки для загрузки сырья и выгрузки материала;
- опорной станции;
- приводов;
- уплотнения концов;
- кожуха венцовой пары и т. д.
Печь устанавливается на фундаментной площадке. Опорой служит сварная рама и ролики, регулирующие ее положение.
Изготовление керамзита в домашних условиях
Возможно ли изготовление керамзита своими руками? Для этого потребуется качественное оснащение, с помощью которого можно готовить до 250 тысяч кубометров керамзита за один год. Для приготовления керамзита своими руками пользуются мини-заводами, топливом для которых служат мазут, уголь, газ природный.
При помощи таких заводиков получают керамзитовый песок, размеры гранул которого варьируются от 0. 16 до 5 мм. Для этого гранулированное либо подвергнутое измельчению сырье обжигается в печи.
Зачастую для домашнего пользования покупают специальные дробильные установки, существенно упрощающие весь производственный процесс. Отметим, что с помощью чертежей, необходимых материалов и наличия желания, можно изготовить дробилку своими руками.
Для изготовления керамзита в домашних условиях часто пользуются дробильными установкамиНа домашнем мини-заводе производится керамзитовый песок из гравийного некондиционного материала. Для получения глинозольного керамзита используют в виде сырья плавкие породы и золу, полученную при сжигании торфа либо каменного и бурого угля. В результате образуется заполнитель, своими свойствами схожий с простым керамзитом. Зольный керамзитовый материал получается с помощью обжига или безобжиговым методом.
Изготовление керамзита – процесс достаточно энергоемкий. Но высокий уровень производительности и постоянный спрос на этот строительный материал помогают быстро окупить все предварительные затраты.
Технология производства керамзита
Популярность керамзита объясняется его малой стоимостью, большой доступностью и уникальными характеристиками. Для производства керамзита используют специальные глинистые легкоплавкие породы, которые обладают способностью вспучиваться при обжиге. В России залежи таких пород имеются практически в любом регионе, поэтому сырьевая база для изготовления керамзита является легкодоступной.
При помощи несложных исследований можно быстро определить пригодность определенного сорта глины для изготовления керамзита. Сначала определяется химический состав сырья, в нем должно содержаться около 70% окислов кварца и 30% окислов железа. Такое соотношение обеспечивает сырью способность к вспучиванию, от которой и зависит вся схема производства керамзита. Затем производятся опытные образцы, которые исследуются на предмет физических свойств – прежде всего, на прочность и гигроскопичность.
Технология производства керамзита очень несложна и заключается в процессе быстрого (30-40 минут) обжига в печи определенной конструкции сырья (глины), при t от 1050 до 1300 град. по Цельсию. Устанавливаться печное оборудование может на любых площадках, для него не требуется специальных помещений. При производстве керамзита не используется полимерных или химических добавок, применяется только природное сырье. Иногда для того, чтобы вспучивание происходило лучше и быстрее, в первоначальное сырье добавляют недорогие легкогорючие вещества, такие как опилки, мазут, отходы семечек и др., которые полностью сгорят в процессе обжига. Это позволяет уверенно утверждать, что керамзит, по своей сути, совершенно чистый экологический материал. После выхода из печи и остывания, керамзит совершенно готов к использованию. Малая себестоимость производства дает возможность керамзиту успешно конкурировать по цене с строительными материалами самых разных предназначений. Окатыши керамзита имеют мелкопористую структуру, заполненную воздухом и, благодаря своим округлым очертаниям, достаточно прочны при сопротивлении на сжатие. Ориентируясь по размерам зерен, керамзит разделен на несколько фракций: крупная фракция керамзита 10-20 — зерна размером от 10 до 20 мм, средняя фракция керамзита 5-10 — размер зерна до 5 мм и мелкая фракция керамзита 0-5, которая называется керамзитовым песком, зерна которого имеют диаметр менее 5 мм.
Чтобы купить керамзит, звоните: +7 (499) 638-45-78
Технология производства керамзита | Новости в строительстве
Технология производства керамзита основана на способе термоудара с обжигом гранул в монослое, при этом для его получения используется кольцевая (карусельная) печь с вращающимся подом. Такая печь применяется в металлургической промышленности с некоторыми конструктивными изменениями, для закладки стального литья.
Керамзит является основным видом искусственных пористых заполнителей используемых в строительстве, на долю которого приходится свыше 68% объема производства. Получают керамзит из слабовспучивающихся глин, но с повышенным содержанием карбонатных примесей. Технология производства легкого керамзитового гравия, предложенная ЦНИИЭПсельстроем исходит из следующих предпосылок:
1. Скорость нагрева должна быть максимальной, так как это способствует сохранению большей части паров и газов, обусловливающих поризацию.
2. Оптимальная температура обжига гранул ограничивается верхним пределом интервала вспучивания и температурой размягчения глин.
Технология производства керамзита основана на способе термоудара с обжигом гранул в монослое, при этом для его получения используется кольцевая (карусельная) печь с вращающимся подом. Такая печь применяется в металлургической промышленности с некоторыми конструктивными изменениями, для закладки стального литья.
Читать далее на http://stroivagon.ru азерит
Такая печь считается более удачной в технологическом плане. так как она лишена тех недостатков, которые возникают во вращающихся печах, в пересыпающемся слое во время обжига. При этом удается избегать перетирании гранул керамзита и значительные теплопотери в процессе производства. Технология производства керамзита способом термоудара состоит из следующих основных операций:
Читать далее на http://stroivagon.ru -гравий керамзитовый
1. Изготовление сырцовых гранул, сушку сырцовых гранул и предварительную термоподготовку гранул на оборудовании существующих керамзитовых заводах.
2. Обжиг керамзитовых гранул в кольцевой печи и охлаждение керамзита.
Керамзит имеющий наименьшую среднюю плотность образуется в условиях термоподготовки гранул при температуре 200…250°С в течении 25…35 минут.Термоподготовка гранул керамзита в течении 25 минут и более при температуре 300 °С и выше увеличивает плотность гранул на 60…70 %. Установлены следующие оптимальные режимы предварительной термоподготовки гранул керамзита:
1. Сушка в сушильном барабане при температуре 100…120°С в течении 30 минут до остаточной влажности в пределах 12…17 %.
2. Термообработка в течении 25 минут при температуре 200…250°С до остаточной влажности 0…3 %.
Определение оптимальных параметров вспучивания гранул производилось для способа термического удара. При этом замечено что обжиг гранул керамзита из курского суглинка способом термического удара в температурном интервале вспучивания позволяет получить легкий керамзитовые гранулы со средней плотностью 400 кг/м³. То есть на 32 % ниже средней плотности керамзитовых гранул полученных во вращающихся печах (570…600 кг/м³).
Для наглядности основные физико-механические свойства керамзита, полученного способом термоудара в кольцевой печи, приведены в таблицу № 1.
Таблица № 1. Основные физико-механические свойства керамзита, полученного способом термоудара в кольцевой печи
При обжиге гранул керамзита из глины способом термоудара получен керамзит со средней плотностью 280…425 кг/м³. Такие гранулы имеют величину средней плотности значительно ниже, чем керамзитовые гранулы полученные во вращающихся печах. при этом поверхность гранул керамзита получается частично оплавленной но шероховатой и структура равномерно пористая.
Легкий керамзит полученный из слабовспучивающихся глин способом термоудара в кольцевой печи (смотри рисунок-1) выдерживает более 400 циклов замораживания-оттаивания без признаков разрушения (ГОСТ 9753-81*). При этом керамзит имеет сравнительно низкое водопоглощение которое можно объяснить частичным оплавлением его поверхности в процессе производства.
При этом кислотостойкость керамзитовых гранул составляет примерно 90…98 %, а щелочестойкость в пределах 50…60 %. Керамзитовые гранулы показали высокую водостойкость, а коэффициент размягчения составляет всего 0,95…0,96. С использованием в строительстве этого керамзита был получен конструктивный теплоизоляционный керамзитобетон со средней плотностью 850…950 кг/м³, имеющий прочность при сжатии в пределах 3,5…6 МПа.
Предварительный технико-экономический анализ эффективности производства керамзитового гравия способом термоудара показал что снижение средней плотности керамзита в два раза позволит снизить его заводскую себестоимость примерно на 50 %. Разработан проект технологической линии производства керамзитовых гранул способом термоудара в кольцевой (карусельной) печи производительностью 100 тысяч м³ в год.
Производство керамзита
Предложенный способ производства включает сушку и трехстадийную скоростную термообработку гранул керамзита:
1. Предварительная термоподготовка в течении 20…40 минут до 200…400°С.
2. Скоростной подъем температуры до 800…1100°С и изотермическая выдержка при конечной температуре до 10 минут.
3. Вспучивание-скоростной подъем температуры до 1150…1250 °С и изотермическая выдержка при конечной температуре до 5 минут.
Дополнительная термоподготовка при температуре 800…1100°С обеспечивает образование в гранулах окисленной оболочки различной толщины. Характерной особенностью обжига в неподвижном монослое является то, что окисленная оболочка не подвергается абразивному истиранию как при обжиге в пересыпающемся слое и сохраняется до стадии вспучивания.
Это обеспечивает вспучивание гранул при оптимальной температуре без межзернового агрегирования.
Рисунок-1. Технологическая схема обжигового агрегата. Кольцевая печь для получения керамзита способом термоудара.
1- кладка печи, 2-газовоздухопроводы, 3-выгружатель слоев, 4-вентиляционная система, 5- дутьевые вентиляторы , 6-аэрожелоб, 7 вращающийся под печи, 8-привод пода.
Кольцевая печь с внешним диаметром 15 м состоит из стационарных стен и свода, вращающегося футерованного пода , опорно-упорной системы и ванн гидрозатвора. Толщина стационарных ограждений печи 0,8 м, футеровка пода -0,5 м. Диаметр средней окружности пода и ее длина соответственно- 11,2 и 35,5 м( в том числе 30 метров -зона обжига ), ширина канала печи -2,4 м, высота от поверхности пода до замка свода -0,75 м.
Кольцевой канал заканчивается дымоотборной шахтой, из которой дымовые газы подаются в слоевой подготовитель и далее выбрасываются в атмосферу с помощью концевого дымососа. В обжиговом агрегате технологический процесс осуществляется следующим образом:
Термоподготовительные сырцовые гранулы подаются монослоем барабанным разгружателем на вращающийся под печи и перемещаются в зону горения топлива где происходит их вспучивание. Керамзит с поверхности пода удаляется выгружателем и охлаждается в холодильнике. Полученные в период эксплуатации технологические и теплотехнические показатели опытно-промышленного агрегата приведены в таблицу№ 2, в сравнении с аналогичными характеристиками однобарабанной печи 2,5 х 40 м Кольчугинского ССК.
Таблица №2. Физико-механические показатели печных агрегатов
Эти данные а также результаты испытаний привозных глин свидетельствуют о снижении насыпной плотности керамзита на 25…40 % и удельного расхода топлива на 35…45 % по сравнению с производством в однобарабанных печах. Более высокие показатели обжигового агрегата с кольцевой печью обусловлены его следующими тепло-технологическими особенностями.
Обжиг монослоя гранул в стационарных условиях осуществляется при оптимальных температурах вспучивания с перепадом по ширине канала печи ± 5°С без опасности интенсивной агломерации материала. Небольшие конгломераты, образованные точечными сварами гранул, легко разрушаются при падении в приемную течку.
Стабильность температурного режима в печи позволяет использовать для производства керамзита глины с короткими ( менее 50°С) температурными интервалами вспучивания. Следствием интенсификации процесса теплообмена является повышение скорости нагрева материала до 300…350°С/мин, чем обеспечивается скоростной режим обжига-термический удар.
Данные факторы обеспечивают снижение насыпной плотности керамзита на 25…40 % по сравнению с производством во вращающихся печах. Более совершенная тепловая схема кольцевой печи по сравнению с барабанными обеспечивает снижение расхода топливана обжиг в результате снижения теплопотерь с отходящими печными газами при сжигании топлива при относительно небольших коэффициентах избытка воздуха (а=1,3…1,35).
Это объясняется наличием многочисленных горелочных устройств и хорошей герметизацией печного пространства. А также увеличением толщины теплоизоляции, рекуперацией тепла отходящих печных газов путем подогрева первичного воздуха до 300…350°С.
Эти факторы, а также применение эффективного запечного теплообменника-слоевого подготовителя -обеспечивают снижение удельного расхода топлива на 52…60 кг/м³условного топлива. Конструктивные особенности кольцевой печи обеспечивают более высокие эксплуатационно -технические показатели по сравнению с барабанными печами.
При этом существенным преимуществом является сокращение эксплуатационных расходов на ремонт футеровки печи, что обусловлено долговечностью стационарной кладки печи и футеровка пода.
***** РЕКОМЕНДУЕМ выполнить перепост статьи в соцсетях! *****
Производство керамзита
Керамзит — популярный и доступный материал с уникальным сочетанием свойств. Его внедрение в строительство изменило многие технологии и, к тому же, он нашел применение в других областях производства и быта. Это легкий, пористой структуры материал, получаемой по специальной технологии обжига глины.
Глины-сланцы имеют в своем составе до 30% кварца и легко плавятся, причем при обжиге гранул глины, при осуществлении такого процесса, как производство керамзита, они вспучиваются, увеличиваются в объеме, становится прекрасным строительным материалом, по форме напоминающим щебень.
Основные качества керамзита, делающие его незаменимым материалом для строительных работ:
• Он обладает низкой влагопоглощающей способностью, так как при обжиге, на элементах продукта создается защитная пленка. Это очень ценное качество для строительных материалов-наполнителей, применяемых для изоляции.
• Пористая структура снижает коэффициент деформации, поэтому керамзит почти не дает усадки, что ускоряет строительные циклы.
• Имеет отличные теплоизоляционные свойства, которые могут умеренно колебаться в зависимости от технологии производства.
• К другим характеристикам относятся: звуко- и теплоизоляция, огнеупорность, морозоустойчивость, химическая инертность, долговечность, экологическая чистота, доступная цена.
Оборудование для производства керамзита
Производство керамзита отработано достаточно и успешно используются во всем мире. Для создания собственного производства, прежде всего, необходимо специальное оборудование, которое обеспечит все стадии такого процесса как производство керамзита: подсушку сырья, обработку с гранулированием, обжиг, охлаждение керамзита.
Оборудование монтируется на специальной площадке. Производство керамзита начинается с доставки сырья, затем поступающего на приспособления для сушки глины, (глинорыхлитель, камневыделительные вальцы и сушильный барабан). После этого глина подается на линию переработки. Она перемещается на вальцы грубого помола, лопастный смеситель, вальцы тонкого помола и попадает в питатель.
Уже подготовленная смесь, поступает в формовочный агрегат, представляющий собой шнековый пресс, имеющий приставку для грануляции. Порции керамзита уже сформированные, затем доставляются в печь для обжига. Следующий этап – охлаждение в слоевом холодильнике и дальше поступление для транспортировки на ленточный конвейер.
Производительность таких линий от 100000 до 200000 куб. метров в год керамзита. Размер площадки под такой производственный цикл должен быть 7200 – 14000 кв. метров. Собственно производственный цех займет 860 кв. метров, на остальной площади будет расположено вспомогательное оборудование, склады, бытовые строения.
Технология производства керамзита
При выборе оборудования нужно определиться со способом производства керамзита: сухой, пластический, порошково-пластинчатый или мокрый. Сухой возможен тогда, когда есть возможность получать однородную камнебитную глину. Эта глина измельчается и сразу идет на обжиг. Пластический способ требует предварительного увлажнения и перемешивания глины в смесителях.
Затем идет формирование гранул в дырчатых вальцах или шнековых прессах. После чего происходит основной процесс — обжигание в печах. Порошково-пластинчатый вариант предполагает предварительное перемалывание сырья в порошок, увлажнение, гранулирование в дырчатых вальцах, затем обжиг. При мокром методе производства керамзита глина в смесителях превращается в однородную массу, которая поступает в шламбассейн, а оттуда в печь. Чаще всего выбирается пластический способ, как экономически более выгодный.
Вращающиеся печи для производства керамзитового агрегата
Керамзитовый наполнитель, также называемый экслай, или легкий керамзитовый наполнитель (LECA), является полезным материалом во все большем числе отраслей промышленности, в первую очередь в строительстве и садоводстве. Следующими на очереди, вероятно, будут приложения для очистки воды и фильтрации.
Уникальная структура и физические свойства керамзита, которые можно использовать в различных областях, производятся в результате тщательно контролируемой термической обработки (обычно называемой прокаливанием или спеканием), проводимой во вращающейся печи.
Термическая обработка керамзитового заполнителя (прокаливание или спекание)
Свойства керамзита, которые делают его идеальным для использования в определенных областях применения, достигаются благодаря высокотехнологичному производственному процессу.
Глины обычно измельчают, агломерируют и / или сушат в качестве средства подготовки сырья, хотя этот процесс может варьироваться. Экструзия кажется предпочтительным методом агломерации в этих условиях, но можно также изучить другие методы.
В то время как подготовка сырья имеет важное значение при производстве заполнителей керамзита, ключевым процессом, лежащим в основе заполнителей керамзита, является термическая обработка.От этой термической обработки произошло название керамзитового заполнителя, поскольку он используется для физического расширения частиц глины.
Для описания таких методов термической обработки используются различные термины. В этом случае обработка обычно называется прокаливанием или спеканием. Хотя эти два термина часто используются как синонимы, важно отметить, что технически они относятся к разным методам. Поскольку спекание технически происходит при гораздо более высоких температурах, для целей этой статьи мы будем называть его прокаливанием, хотя в некоторых случаях расширенные агрегаты могут быть действительно спеченными.
В случае керамзита прокаливание играет важную роль в создании продукта, который может служить заполнителем керамзита. Температура, обычно от 1050 ° C до 1250 ° C, вызывает выделение газов в результате различных изменений в материале, включая разложение и восстановление оксидов трехвалентного железа, горение органических веществ, продувку захваченной воды и разложение карбонаты .³
Это выделение газов вызывает физическое расширение или вздутие глины, в результате чего она имеет более низкую плотность, более высокую пористость и гораздо большую площадь поверхности внутри материала, а также более твердую поверхность — все характеристики, которые делают ее идеальной для использования. как легкий заполнитель.
Факторы, влияющие на расширение глины при прокаливании
Как и в случае с большинством материалов, для достижения наилучших результатов в производственном процессе необходимо оптимизировать различные факторы. Обширное исследование, проведенное на трех различных источниках глины, показало, что, хотя ряд факторов важен, параметры процесса расширения, которые, возможно, являются наиболее важными, включают: 4
Температура обработки
Температура обработки является наиболее важным фактором в процессе расширения.Было обнаружено, что расширение увеличивается вместе с температурой, чуть ниже температуры плавления конкретной глины (температура плавления варьируется в зависимости от типа глины).
Размер зерна глины
Исследование показало, что размер зерна глины также является определяющим фактором, причем расширение увеличивается по мере уменьшения размера зерна.
Размер пеллет
Размер гранул или агломератов также оказывает влияние на расширение, причем расширение увеличивается вместе с размером гранул. Следовательно, уменьшение размера гранул коррелирует с меньшим расширением.
Время удерживания
Было установлено, что оптимальное время удерживания зависит от типа обрабатываемой глины. Оптимальное время удерживания было важным, поскольку наблюдались последствия как несоответствующего, так и чрезмерного времени.
Вращающаяся печь
Предпочтительным оборудованием для проведения процесса расширения глины является вращающаяся печь.
Вращающиеся печи доступны в конфигурации с прямым или косвенным обогревом, и их часто называют декарбонизатором.Производство заполнителей керамзита обычно осуществляется в печи с прямым нагревом, в которой глина и продукты сгорания находятся в прямом контакте друг с другом.
Обжиговые печис прямым нагревом можно настроить для прямоточного или противоточного воздушного потока, но противоток, как правило, является более эффективной настройкой процесса при этой настройке.
3D Модель вращающейся печи с прямым обогревом
Почему глина как легкий заполнитель
Как и многие легкие заполнители (LWA), использование вспученных глин может обеспечить широкий спектр как экономических, так и экологических преимуществ:
Экономическая выгода
Использование легких заполнителей предлагает множество экономических стимулов, в том числе:
- Снижение затрат на конструкции в строительстве
- Снижение транспортных расходов
- Снижение затрат и уменьшение зависимости от импорта, где это применимо
Экологические преимущества
По данным Европейской ассоциации по производству керамзита (EXCA), керамзит является экологически чистым материалом с рядом экологических преимуществ:
- Снижение выбросов CO 2 при использовании в качестве замены ископаемого топлива
- Снижение выбросов CO 2 в строительстве и на транспорте
- Повышение энергоэффективности зданий
- Возможность 100% вторичной переработки
- Химически инертен (без вредных компонентов и, как следствие, без возможности выделения ЛОС или вымывания загрязняющих веществ
- Преимущества фильтрации воды и воздуха
- Высокое соотношение продукта к сырью (из одного кубометра глины можно получить пять кубометров керамзита)
Кроме того, возможность заключается в использовании восстановленных или переработанных глиняных материалов, что еще больше повышает экологичность этого материала.
Использование LECA
В то время как области применения легкого керамзитового заполнителя (LECA) продолжают расти, в настоящее время существует два основных направления для продуктов LECA:
Строительство
Строительство — наиболее распространенное приложение для LECA. Керамзит можно найти во всех видах бетона, наполнителя и конструкционных компонентов в строительстве и промышленности строительных материалов. Преимущества, которые он может предложить в этой настройке, включают: ²
- Высокая износостойкость при низких эксплуатационных расходах и долгий срок службы
- Прочность и устойчивость
- Полностью негорючие (огнестойкие)
- Возможность 100% вторичной переработки снижает проблемы утилизации
- Легкий вес без ущерба для прочности
- Служит теплоизолятором
- Обеспечивает снижение шума
- Способствует отводу воды
- Нетоксичный
Садоводство
Использование LECA в садоводстве — сравнительно новое применение, но все еще развивающаяся область. Керамзитовые наполнители могут принести множество преимуществ при различных условиях выращивания. Сюда входят:
- Улучшенная аэрация (особенно при использовании в качестве субстрата при выращивании в коммерческих контейнерах) и пониженное уплотнение
- Способность к увеличению содержания воды и питательных веществ
- Повышенная катионообменная емкость
- Устойчивость к разрушению со временем
- Возможно использование в качестве барьера от сорняков
Помимо строительства и садоводства, LECA также исследуется на предмет использования в системах очистки и фильтрации воды.
Испытания: залог успеха с керамзитом
Как и во многих случаях термической обработки, испытания являются критическим элементом успешной операции расширения глины. Исследования показали, что идеальные параметры процесса зависят от типа обрабатываемой глины.
Тестирование образцов глины в серийном масштабе для сбора исходных данных процесса — первый шаг в успешной программе тестирования. Данные, собранные во время пакетного тестирования, затем можно использовать для масштабирования тестирования до непрерывных пилотных запусков.Испытания также можно использовать для поиска баланса между идеальными параметрами процесса и тем, что является экономически целесообразным.
Инновационный центр FEECO предлагает различные испытательные печи для проведения как периодических, так и пилотных испытаний. Печи могут быть оснащены различным вспомогательным оборудованием для моделирования различных условий коммерческой эксплуатации.
Испытания различных методов агломерации также могут быть объединены для получения идеальных характеристик гранул для рассматриваемого уникального источника глины.
Печь периодического действия, используемая для испытаний в инновационном центре FEECO
Система автоматизации инновационного центра собирает широкий спектр данных, которые можно отслеживать и анализировать в режиме реального времени для обеспечения непревзойденной прозрачности процесса. Сюда входят точки данных, такие как скорость подачи и продукта, соответствующие показания температуры, давления в системе, отбор проб и анализ газа и многое другое.
Заключение
Керамзитовый керамзит — полезный материал в строительной индустрии, находит применение в садоводстве и водоочистке.Вращающиеся печи — это предпочтительное устройство для переработки глиняных агломератов в керамзит.
Способность оптимизировать параметры процесса для производства керамзита высшего качества имеет решающее значение для успеха операции. FEECO предлагает обширные возможности тестирования для тех, кто находится на этапах процесса и разработки продукта. Затем мы используем данные, собранные в ходе испытаний, для проектирования и производства на заказ коммерческих вращающихся печей высочайшего качества. Для получения дополнительной информации о наших возможностях в отношении керамзитовых заполнителей свяжитесь с нами сегодня!
Линия по производству легкого вспененного глиняного агрегата (LECA)
Что такое легкий керамзитовый заполнитель (LECA)?
Определение : свет
заполнитель керамзита или заполнитель керамзита (LECA или ECA), также называемый керамическим
окатыши — один из самых популярных легких заполнителей, получаемых путем спекания глины. во вращающейся печи примерно до 1200 ° C.
Вращающаяся печь для спекания глины
Сырье и применение : существуют различные типы легкого керамзитового заполнителя, а основные материалы — глина, сланец, сланец, угольный порошок, хвосты и т. д.
LECA в основном применяется в строительстве, внутренняя отделка, сельское хозяйство, садоводство, садоводство, детская площадка, гидропоника, и Т. Д.
Оценка (мм) | Плотность (кг / м 3 ) | Приложения |
0-4 | ≤710 | Легкий бетон, легкий кирпич, сборная плита, легкая плитка, система очистки воды, сельское хозяйство |
4-10 | ≤480 | Легкий бетон, легкая плитка, сборные конструкции плита, аквакультура, шумоизоляция |
10-20 | ≤380 | Легкий бетон, канализация, садоводство, дренажная система |
0-25 | ≤430 | Отделка пола, светлая набивка, дорога строительство, аквакультура |
Перспектива разработки керамзита легкого керамзита
Современный легкий керамзитовый заполнитель
рыночные данные показывают, что рынок LECA изменил свое направление с
традиционная строительная техника для изготовления изделий и садоводства
поддержание.
Перспектива развития LECA
Материалы для производства из традиционных материалов такие как глина и сланец были заменены остатками промышленных отходов и илом и тенденция развития машин превратилась в крупномасштабные и автоматизация.
В связи с тенденцией глобализации защиты окружающей среды, ресурсосберегающая экономика и устойчивая промышленность будут активно продвигаются в разных странах и регионах.
В будущем, сосредоточив внимание на экономического развития, поставщики LECA должны обратить внимание на сокращение загрязнения и растраты ресурсов для обеспечения быстрого и стабильного развития производственные линии.
Технологии производства LECA
Обычно существует два типа LECA. Технология изготовления: спекание и спекание-вспучивание. Разница между ними находится в процессе спекания-расширяется, агрегат расширяется на больший объем.
Производительность LECA при спекании
Агломерационная машина для процесса спекания LECA
- Прочность на сжатие : на сжатие
прочность агломерата относительно высокая, достигая 3,0-7,0 МПа,
а прочность на сжатие высокоспеченных агрегатов может достигать 25-40 МПа.
- Density : плотность спеченного заполнитель крупнее, обычно больше 600 кг / м3, даже некоторые из которых более 900 кг / м3.
- Водопоглощение : водопоглощение обычного спеченного заполнителя немного выше, чем у спеченного вспененного материала. продукт, а высокопрочные изделия аналогичны спеченному вспененному продукту.
- Устойчивость к карбонизации : спеченный заполнитель обладает высокой устойчивостью к карбонизации, поэтому его прочность на сжатие не уменьшится даже под действием углекислого газа.
Характеристики LECA при спекании-расширении
Вращающаяся печь для агломерационного процесса LECA
- Прочность на сжатие : на сжатие прочность агломерированного заполнителя обычно ниже 2,0 МПа, поэтому он в основном используется для внутренней отделки, такой как шумоизоляция и садоводство.
- Теплоизоляционные характеристики : спеченный-вспененный
продукт имеет закрытую микропористую структуру с очень высокой пористостью, что обычно
составляет 48% -70% от общего объема агрегата, что дает только 0.
08-0,15 Вт /(m.k) теплопроводности.
- Низкая плотность : в слое много пор спеченно-вспененный материал, поэтому плотность преимущественно 300-500 кг / м 3 , что составляет лишь половину от спеченного заполнителя. Однако у него есть значительное преимущество в легкости, поэтому его также можно использовать для различных декоративная промышленность и строительство с более низкими требованиями к плотности в строительстве материалы.
- Отличное звукопоглощение и изоляция : среди всех видов агрегатов звукопоглощающие и изоляционные характеристики агломерированного вспененного заполнителя является наиболее выдающимся.
Когда звук проходит через материал, большое количество звуковых волн поглощается его порами, что уменьшает распространение звука.
Для разных процессов требуется разное оборудование.
Агломерационная машина обычно используется в процессе спекания, в то время как роторная
Печь используется в процессе спекания с расширением.
По сравнению с агломашиной роторный печь более эффективна и экологична, поэтому предпочтительное оборудование для поставщиков LECA.
Производственная линия LECA и основные машины
Производство LECA в целом требует семи шагов: дробление, смешивание, измельчение, гранулирование, спекание, охлаждение и просеивание.
Производственная линия LECA
Основное оборудование на производстве LECA Линия включает в себя щековую дробильную машину, смесительную машину, шаровую мельницу, гранулятор, роторная сушилка, грохот, вращающаяся печь, охлаждающая машина.
Щековая дробилка — первичное дробление
Щековая дробилка — это основная машина, которая применяется для крупного, среднего и тонкого измельчения различных руд и горных пород с комплексная прочность от 147 до 245 МПа и превращает их в небольшие куски 10-350 мм.
Зубодробилка, мордоворот
Преимущества : В последние годы FTM
специально разработанная мощная щековая дробилка для нужд дробления
высокопрочный и высокотвердый микроуглеродистый феррохром в металлургии,
горнодобывающая, строительная и другие отрасли промышленности.
Шаровая мельница — дальнейшее измельчение
Шаровая мельница — ключевое оборудование для измельчения материал после измельчения. Шаровая мельница широко используется в производстве цемента, силикатные изделия, новые строительные материалы, огнеупорные материалы, удобрения, шлифовка черных и цветных металлов и стеклокерамики, сухое или мокрое шлифование различных руд и других измельчаемых материалов.
Шаровая мельница
Преимущества : Энергосбережение, гибкий дизайн разгрузочной части, большой порт подачи, высокая эффективность измельчения, хорошая качество футеровки и закрытая система для уменьшения запыленности.
Дисковая грануляционная машина — контроль размера частиц
Диск — это ключевая машина, определяющая частицы керамзитового заполнителя.
Диск гранулирования имеет общую круглую форму.
структура дуги, а степень грануляции может достигать 93% и более. Гранулирование
лоток имеет три выпускных отверстия, которые облегчают прерывистое производство
операций, значительно снижая трудоемкость и повышая эффективность труда.
Дисковая грануляционная машина
Преимущества : Высокая скорость образования шариков, большие округлая прочность частиц, интуитивное управление и простота обслуживания.
Сушилка — удаление воды из LECA
Сушилка в основном используется для сушки определенных влажность или крупность материалов переработки минерального сырья, строительных материалов, металлургия и химическая промышленность, а работа оборудования проста и надежный.
Сушилка
Adv anta ges : длительный срок службы деталей, износостойкость, высокая прочность на сушку, высокая эффективность, простота в эксплуатации, экологичность защита и энергосбережение, усовершенствованная структура и сильная сушильная способность.
Барабанный грохот — отделяющий неквалифицированный LECA
Барабанный сетчатый фильтр часто используется для измельчения
порошкообразных материалов, который имеет хороший просеивающий эффект и стабильную работу
и он производит низкий уровень шума во время рабочего процесса.
Барабанный экран
Преимущества : Оборудование имеет диапазон применения, а также его можно настроить. Имеет низкий уровень шума, высокий эффективность и защита окружающей среды, усовершенствованная система смазки, долгая срок службы, малый угол наклона установки и хороший экранирующий эффект.
Вращающаяся печь — спекание LECA
Вращающаяся печь — самая необходимая машина и играет важную роль в процессе спекания, что определяет производительность LECA.
Вращающаяся печь
Преимущества : Осевое перемещение Цилиндр управляемый, скорость гибкая, установка и обслуживание удобное, а герметичность хорошая.
Кулер — быстрое охлаждение LECA
Одноцилиндровый охладитель является одним из
важное оборудование в системе вращающейся печи. Клинкер из вращающейся печи
(1000-1200 ° C) полностью обменивается с воздухом через вращающийся цилиндр.
лента для охлаждения материала до температуры ниже 200 ° C, в то же время улучшения клинкера
качество и шлифуемость.
Кулер
Преимущества : Высокая термическая эффективность, высокая качество клинкера, быстрое охлаждение и повышенная производительность.
Спецификация производственной линии LECA (для только для справки)
- 01 тип : 0,45-0,9 мм (20-40 меш) Высокая прочность при средней плотности
- 02 тип : 0,9-1,25 мм (16-20 меш) Высокая прочность при средней плотности
- 03 тип : 1.0-1,70 мм (12-18 меш) Высокая прочность при средней плотности
- 04 тип : 0,224-0,65 мм (40-60 меш) Высокая прочность при средней плотности
Производитель оборудования LECA рекомендовано — FTM
Fote Mining Machinery (FTM), расположенная в
Хэнань — один из самых известных поставщиков горнодобывающего оборудования, который стремится
для производства горнодобывающих машин из экологически чистых строительных материалов и обеспечивает
интеллектуальные продукты для горнодобывающей промышленности и передовые решения.
Обладая более чем 30-летним опытом, FTM добился замечательных результатов в производственной линии LECA за счет непрерывного разведка и исследования.
FTM — профессиональный поставщик машины и оборудование для легкого керамзита, а также все оборудование имеет высокое качество и весомые преимущества, а также очень разумные цены.
Одним словом, Fote Mining Machinery — хороший выбор поставщиков LECA при выборе легкого керамзитового заполнителя производители оборудования.Приглашаем проконсультироваться с нами, если у вас есть какие-либо требования о производственной линии LECA.
(PDF) Производство керамзитобетона для легкого бетона из несамовсплывающихся глин
… Спектр источников чрезвычайно разнообразен: многие исследования касались летучей золы угля, остатков сточных вод и отложений, извлеченных из гаваней и воды резервуаров, но в качестве сырья было предложено много различных отходов. Таблица 1 Отходы, предлагаемые в литературе для производства LWA. Твердые бытовые отходы (n = 47) Осадок сточных вод 21 Зола уноса мусоросжигательных заводов 11 [28] [29] [30] [31] [32] [33] [34] [35] [36] [37] [38] Зола сточных вод » 7 [10,24,39,40, [41] [42] [43] Обработка воды 7 [44] [45] [46] [47] [48] [49] [50] Остатки горных работ и карьеров (n = 47) Декоративные камни 8 [47,48, [51] [52] [53] [54] [55] [56] Камни, богатые цеолитами 13 [52,53, [57] [58] [59] [60]] [61] [62] [63] [64] [65] [66] [67] Природные агрегаты 10 [16,20,21, [68] [69] [70] [71] [72] [73] [ 74] [75] Отходы глинистых материалов 9 [16,20,21,67, [76] [77] [78] [79] [80] Обогащение руды 8 [23,31, [81] [82] [ 83] [84] [85] [86] Прочие породы 6 [64,65, [87] [88] [89] [90] Остатки угольных электростанций (n = 35) Летучая зола 26 [15,23, [70] ] [71] [72] [73] [91] [92] [93] [94] [95] [96] [97] [98] [99] [100] [101] [102] [103] [ 104] [105] [106] [107] [108] [109] [110] Зола, шлак 13 [97,98,101,102,108, [111] [112] [113] [114] [115] [116] [117] ] [118] Производство минерального сырья (n = 20) Натриево-известковое стекло 13 [18,23,25,36,55,103,105,115, [119] [120] [121] [122] [123] Полировка керамической плитки 5 [23, 52,53,105,124] Прочие c керамика и стекло 4 [23,121,125,126] Прочие шламы 4 [54,55,105,127] Дноуглубительные работы (n = 24) Водохранилища 16 [18,26,32,34,36,118, [128] [129] [130] [131] [132] ] [133] [134] [135] [136] [137] Порты 9 [123, [138] [139] [140] [141] [142] [143] [144] [145] Металлургическая промышленность »(n = 12) Стальная пыль и шлак 4 [88,96,141,145] Алюминиевый лом 4 [102,122,146,147] Очистка сточных вод 4 [31,81,140,148] Другие источники Загрязнение воздуха 4 [32,143,149,150] Сельское и лесное хозяйство 4 [129, [151] [152] [153] Отработанные катализаторы 3 [56,114,154] Строительство и демонтаж 2 [61,154] для LWA (Таблица 1).
Кроме того, остатки использовались отдельно или в смесях из различных источников отходов. …
Превращение глины в строительный материал — это тяжелая работа.
Каждый день конвейерная лента перемещает около 1000 тонн необработанной глины из глиняного карьера Leca в Дании на завод компании в Хинге. Здесь влажное сырье подвергается жесткой обработке, которая в конечном итоге превратит глину в широко известные коричневые шары Leca ® и другие продукты Leca ® .
«Конвейерная лента транспортирует сырую глину в большие вращающиеся печи.Попутно глина проходит несколько процедур формования, так что в итоге комки оказываются размером с ладонь и размером с большой валун. Это чрезвычайно тяжелая отрасль, в которой, помимо прочего, используются электродвигатели, зубчатые передачи и муфты », — объясняет менеджер по техническому обслуживанию Тонни Хедеванг.
Обжиговые печи выключают только два раза в год
Температура во вращающихся печах составляет около 1200 градусов Цельсия. Тепло высвобождает тысячи маленьких пузырьков газа, которые задерживаются в глине и придают материалу характерную легкость, когда глина превращается в шарики за счет кругового движения печи.Остановка и запуск печей — чрезвычайно дорогостоящая операция, поэтому Leca Denmark уделяет особое внимание предотвращению сбоев в производственном процессе.
«Мы закрываем печи только на Рождество и на летние каникулы, чтобы провести регулярное техническое обслуживание. В остальное время года их нужно постоянно кормить. Механизмы и двигатели очень тяжело работают, поэтому нам нужно иметь надежное оборудование. Продукты и оборудование низкого качества и с коротким сроком службы просто не подходят », — объясняет Тонни.
Тесный контакт с Хойером
Из-за того, что компания уделяет особое внимание эксплуатационной надежности и быстрому обслуживанию, Leca Дания поддерживает тесные контакты со своими поставщиками, включая Hoyer, которые поставляют электродвигатели, шестерни и другие детали трансмиссии.
«Мы не можем быть экспертами во всем, поэтому приятно знать, что Хойер знает фабрику и наше оборудование и может быстро отреагировать в случае возникновения проблем. Например, несколько месяцев назад у нас возникли проблемы с некоторыми муфтами.Что ж, вышло наше постоянное контактное лицо из Хойера, которое осмотрело детали и быстро нашло решение », — вспоминает Тонни.
Факты о Leca Дания
Leca Дания является частью международного концерна Saint-Gobain
Завод в городе Хинге отвечает за производство всей продукции Leca ® в Дании.
Первые продукты Leca ® были разработаны в Дании в 1939 году.
Leca ® используется в качестве изоляционного строительного материала и легкого строительного наполнителя, используемого в зданиях, на дорогах, мостовых пандусах, велосипедных дорожках и портовых сооружениях.
% PDF-1.5
%
1 0 obj>
endobj
2 0 obj>
endobj
3 0 obj> / Метаданные 741 0 R / Pages 6 0 R / StructTreeRoot 361 0 R >>
endobj
4 0 obj>
endobj
5 0 obj>
endobj
6 0 obj>
endobj
7 0 obj>
endobj
8 0 obj>
endobj
9 0 obj> / MediaBox [0 0 595. 276 841.89] / Parent 6 0 R / Resources> / ExtGState> / Font> / ProcSet [/ PDF / Text / ImageB / ImageC / ImageI] >> / StructParents 0 / Tabs / S> >
endobj
10 0 obj>
endobj
11 0 obj>
endobj
12 0 obj>
endobj
13 0 obj>
endobj
14 0 obj>
endobj
15 0 obj>
endobj
16 0 obj>
endobj
17 0 obj>
endobj
18 0 obj>
endobj
19 0 obj>
endobj
20 0 obj>
endobj
21 0 объект>
endobj
22 0 obj>
endobj
23 0 obj>
endobj
24 0 obj>
endobj
25 0 obj>
endobj
26 0 obj>
endobj
27 0 obj>
endobj
28 0 obj>
endobj
29 0 obj>
endobj
30 0 obj>
endobj
31 0 объект>
endobj
32 0 obj>
endobj
33 0 obj>
endobj
34 0 объект> / MediaBox [0 0 595.276 841.89] / Parent 6 0 R / Resources> / Font> / ProcSet [/ PDF / Text / ImageB / ImageC / ImageI] >> / StructParents 1 / Tabs / S >>
endobj
35 0 obj>
endobj
36 0 obj>
endobj
37 0 obj>
endobj
38 0 obj>
endobj
39 0 obj>
endobj
40 0 obj>
endobj
41 0 объект>
endobj
42 0 obj [45 0 R]
endobj
43 0 obj>
endobj
44 0 obj>
endobj
45 0 obj>
endobj
46 0 obj>
endobj
47 0 obj>
endobj
48 0 obj>
endobj
49 0 obj>
endobj
50 0 obj>
endobj
51 0 объект>
endobj
52 0 obj>
endobj
53 0 obj>
endobj
54 0 объект> / MediaBox [0 0 595.
276 841.89] / Parent 6 0 R / Resources> / Font> / ProcSet [/ PDF / Text / ImageB / ImageC / ImageI] >> / StructParents 2 / Tabs / S >>
endobj
55 0 obj>
endobj
56 0 obj>
endobj
57 0 obj>
endobj
58 0 obj>
endobj
59 0 obj>
endobj
60 0 obj>
endobj
61 0 obj>
endobj
62 0 obj>
endobj
63 0 obj>
endobj
64 0 obj>
endobj
65 0 obj>
endobj
66 0 obj>
endobj
67 0 obj>
endobj
68 0 obj> / MediaBox [0 0 595.276 841.89] / Parent 6 0 R / Resources> / Font> / ProcSet [/ PDF / Text / ImageB / ImageC / ImageI] >> / StructParents 3 / Tabs / S >>
endobj
69 0 obj>
endobj
70 0 obj>
endobj
71 0 объект>
endobj
72 0 obj>
endobj
73 0 объект> / MediaBox [0 0 595.276 841.89] / Parent 6 0 R / Resources> / Font> / ProcSet [/ PDF / Text / ImageB / ImageC / ImageI] / XObject >>> / StructParents 4 / Tabs / S >>
endobj
74 0 объект>
endobj
75 0 obj>
endobj
76 0 obj>
endobj
77 0 obj>
endobj
78 0 obj>
endobj
79 0 obj>
endobj
80 0 obj>
endobj
81 0 объект>
endobj
82 0 объект>
транслировать
xSWsNUSuN ծ / B $ H «& ƘHVUĄEEAQ
I8 «(rs0̅
Керамзит — о сырье и процессе производства
Керамзит из-за своей традиции более распространен и широко распространен, чем можно предположить в современных строительных технологиях. С геологической точки зрения, сырьевая глина — это сначала просто определение размера минеральных частиц. Эти крошечные частицы образовались и возникают, с одной стороны, в результате выветривания и эрозии различных горных пород, а с другой — в результате минерализации и осаждения органических материалов. Высокое давление и температура могут вызвать превращение этих отложений в различные, так называемые метаморфические породы. Таким образом, например, долгое воздействие давления и тепла превращает известняк в мрамор, а глину в сланец.Таким образом, глина является сырьем, которое возникло и до сих пор происходит геологически в результате непрерывных процессов. Это неисчерпаемое сырье было известно с древних времен как исключительно подходящий материал для строительства и других целей. Дохристианские постройки или знаменитые армии в натуральную величину, воспроизведенные из глины, свидетельствуют о прочности этого материала.
От побочного эффекта к 100-летней истории систематического производства керамзита
Систематическое и контролируемое производство керамзита — до тех пор нежелательного побочного продукта производства глиняного кирпича — возникло только ближе к концу 19 века. Первый патент на производство экономичного и структурного керамзита был получен в США в 1918 году. Колыбелью европейского производства керамзита является Дания, где с середины прошлого века керамзит почковидной формы производился в больших масштабах. век. Преимущества этого легкого и, тем не менее, прочного и долговечного строительного материала неуклонно возрастали в ходе его разработки. Помимо изначально преследуемой главной цели снижения веса, сегодня решающими причинами использования керамзита являются превосходная теплоизоляция, сбалансированный микроклимат в помещении и постоянно растущее внимание к строительной биологии.На нашем веб-сайте представлен соответственно широкий спектр продуктов, а также многочисленные преимущества и различные потенциальные области применения.
Принцип производства нашего керамзита
Неочищенная глина, добытая открытым способом, состоящая из натуральной отборной эоценовой глины, содержащей более 60% монтмориллонитовой глины, предварительно смешивается, очищается при подготовке, гомогенизируется и затем подается в одну ряда различных вращающихся печей в зависимости от индивидуального производственного процесса по принципу Лека. После того, как глина сушится при температуре от 300 до 800 ° C и одновременно измельчается и гранулируется оборудованием внутри печи, фактический процесс расширения происходит при температуре прибл. 1200 ° С. Оболочка глиняных гранул достигает точки плавления и спекается, а это означает, что они сплавляются и тем самым становятся более компактными. Одновременно органические компоненты (соединения углерода) внутри газифицируются или сгорают, повышая температуру и превышая точку плавления глины. Дополнительный эффект расширения создается за счет высвобождения кислорода из оксидов, содержащихся в глине, которое начинается при этих высоких температурах.Это происходит в течение относительно короткого времени, поэтому газы не могут достаточно быстро диффундировать и образовывать газовые поры, которые расширяют глину. В результате получается частица в форме почки со стабильной оболочкой и мелкопористой аэрированной сердцевиной для различных потенциальных применений.
керамзитовых шариков в цементе
керамзитовые шары в цементе — les6quarts.

ГЛИНОВЫЕ БЛОКИ — ЦЕМЕНТНЫЕ ДЫМОХОДЫ ТИП А — ТИП
Керамзитовые блоки LGEA — тип Fibrotubi Leca — это блочные элементы, которые позволяют создавать вентиляционные каналы, такие как полости, в которые вставляются дымоходы и дымоходы.Блоки имеют кубическую форму высотой 25 см в облегченном глиняном бетоне, вибропрессованном с прямоугольным / квадратным отверстием.Легкий заполнитель из вспененной глины Hydroponics Aeroponics
Легкий заполнитель из вспененной глины от Techniclay состоит из пористых керамических гранул, образованных путем вспенивания специальной глины при высокой температуре.
Индия линия по производству небольшого легкого керамзита.
Indian Concrete Journals — Индийский бетон. Легкий заполнитель Легкий керамзитовый заполнитель LECA или керамзит эксклай представляет собой легкий заполнитель, полученный путем нагревания глины до температуры около 1200 C 2190 F во вращающейся печи. Выходящие газы расширяют глину за счет тысяч маленьких пузырьков, образующихся во время нагрева, образуя сотыКупить керамзит Керамзитовые шарики — 1 кг онлайн в
Керамзитовые заполнители формируются путем нагревания натуральной глины до температуры 1200 градусов Цельсия.В результате образуется сотовая структура, связанная с глиняным шаром. Глиняные шары обычно имеют округлую форму. Они очень легкие и прочные. Глиняные шарики не изменяют pH почвы.Форум кактусов и суккулентов: Мнения о шариках из гидротонной глины
Hi Lindsey leca — легкий керамзитовый заполнитель или эти глиняные шарики обладают схожими характеристиками с пемзой./5b51ca19e4f31f3.s.siteapi.org/img/2cc1cdf692c6d7098d07f67e2ff26920d0b6d1c0.jpg)
глиняных камешков — Growing Media GroWell Hydroponics
Clay Pebbles — Clean pH Neutral Clay Pebbles. Можно смешивать с растительной средой Coco Soil или Cellmax. Немецкие источники. Быстрая доставка Купить сейчасСреда для выращивания гидропонной расширенной глины на продажу eBay
Высококачественные шарики из гидропонной расширенной глины высшего качества 5 л Гранулы из гальки в мешках. 12,54 фунтов стерлингов. Почти исчез. Высококачественные гидропонные шарики из керамзитовой глины, 10 л, 3 кг, галька, мешокРасширенное использование наполнителя из керамзитовой глины будет иметь вид
Использование керамзитовых шариков стало популярным во всем мире.Как уже отмечалось, использование керамзитовых шаров для нижеперечисленных проектов оказалось рентабельным, чем использование других заполнителей: Звукоизоляция стен; Усиление плит; Садоводство; Напольные и кровельные панели; Противопожарная защита; Создание освещенных насыпей и т.
Пеностекло Пузырьки Изоляция полости Легкое стекло
Несвязанная неплотная теплоизоляция. Пузырьки из пеностекла GEOCELL обладают отличной текучестью благодаря своей сферической форме.В результате маленькие стеклянные шарики легко заполняют пустоты в перекрытиях потолочных балок и полых стенах, улучшая теплоизоляцию.Гидропоника с шариками из расширенной глины Hydroton — YouTube
Как эти маленькие коричневые шарики могут заменить почву или почвенную смесь на основе торфа? Какие стратегии орошения работают и почему? Мы объясняем, как получить максимальную отдачу oГидропонная среда для выращивания расширенной глины на продажу eBay
Купите среду для выращивания гидропонной расширенной глины и получите лучшие предложения по самым низким ценам на eBay. Большая экономия и бесплатная доставка / сбор многих товаров.Раунды заполнителя из расширенной глины. И легкий измельченный заполнитель из вспененной глины
, известный как легкий заполнитель из вспененной глины или LECA или ECA, — это хорошо зарекомендовавший себя высококачественный, эффективный и прочный легкий заполнитель, подходящий для широкого спектра применений, включая готовый бетон.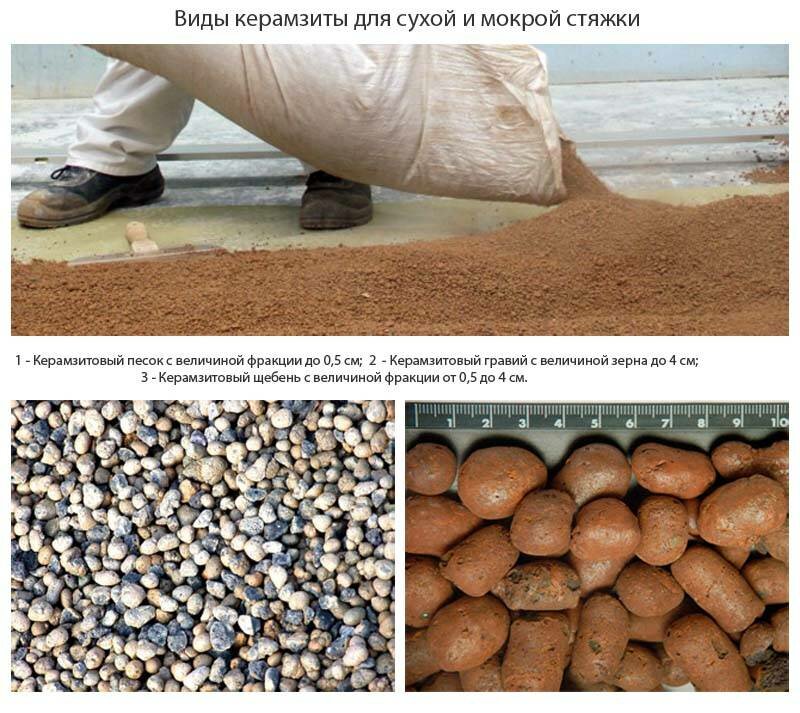
Leca Clay Balls — Specialist Aggregates Ltd
Coloured Lightweight Expanded Clay Aggregate.Особенно подходит для посадки покрытий и ситуаций, например, в вестибюлях торговых центров, гостиниц и общественных зданий, где полные камни могут быть неуместными, но где важна эстетика. Известняк — карбонат кальцияИспользование керамзитовой глины Laterlite
Цементный раствор, состоящий из смеси цемента и воды, должен быть распределен по поверхности рыхлой керамзитовой глины Laterlite после ее выравнивания. Изменяя пропорции воды и цемента с жидкостью, суспензию можно сделать больше при меньшем количестве жидкости, и она будет проникать на большую или меньшую глубину в расширенный слой.глина. Предлагаемая модельШаровая мельница для легкого вспененного глиняного агрегата ZK Вращающаяся цементная мельница
Потерянные инвестиции: Основываясь на характеристиках легкого вспененного глиняного агрегата, вращающаяся печь LECA с двухцилиндровым вкладышем управляет процессом предварительного нагрева и прокаливания.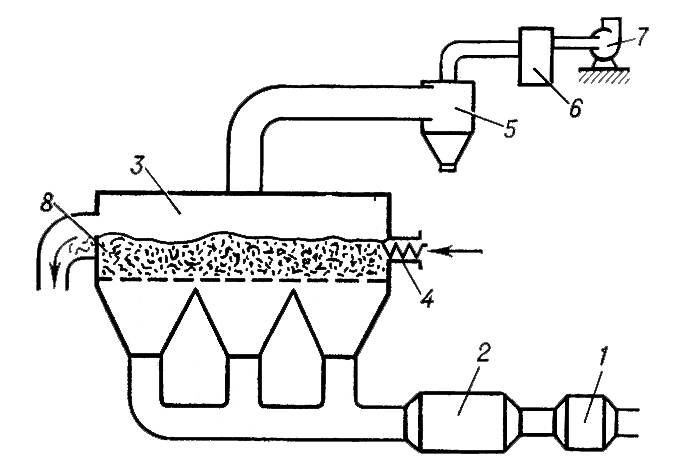
Керамзитовый заполнитель — Википедия
Легкий керамзит или керамзит — это легкий заполнитель, полученный путем нагревания глины до температуры около 1200 ° C во вращающейся печи.Образовавшиеся газы расширяют глину тысячами маленьких пузырьков, образующихся при нагревании, образуя сотовую структуру. LECA имеет приблизительно круглую форму или форму картофеля из-за кругового движения в печи и доступен в различных размерах и плотности. LECA используется для изготовления изделий из легкого бетона и для других целей. Керамзит с добавкой латеритаLaterlite
Универсальность: керамзит с добавлением латерита широко используется в строительстве как сам по себе, так и в смеси со связующими, цементно-известковыми смолами и т.д.. Широко используется в составе бетонов п.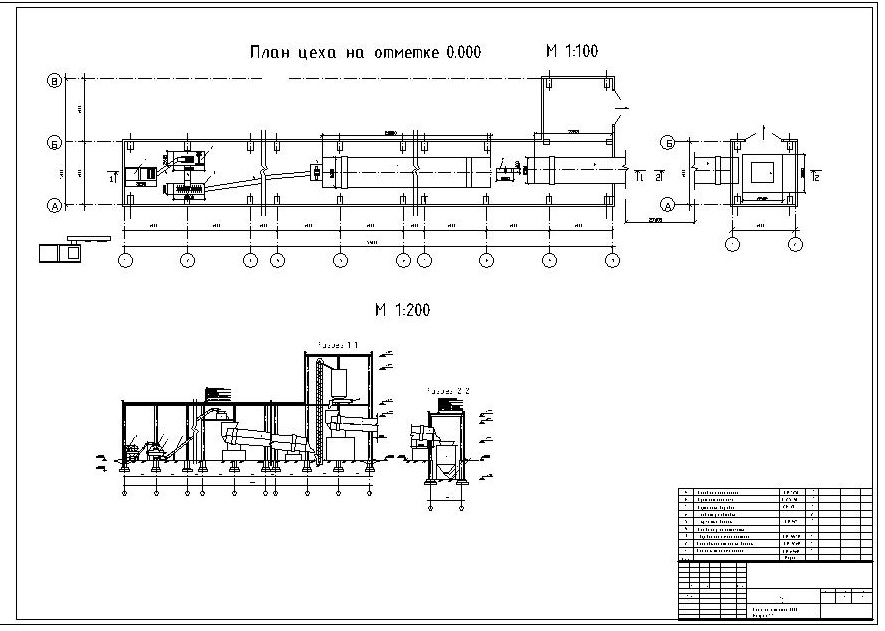
LECA: ГИДРОПОНИКА ДЛЯ ВЫРАЩИВАНИЯ — Гидропоника Садоводство
L.E.C.A. Легкий наполнитель из вспененной глины получают путем нагревания глины на очень сильном огне до тех пор, пока она не вздувается, как попкорн. В результате получается очень грубая среда; Шарики имеют диаметр около 1/4 дюйма. Они обладают превосходным дренажем, и иногда их добавляют в более плотную среду, чтобы способствовать дренажу в сеялке.Легкий заполнитель из вспененной глиныШарики из вспененной глины Тип упаковки: Pp Размер мешка: 0-30 мм Агрегаты из вспененной глины
, известные как легкие заполнители из вспененной глины или LECA или ECA, представляют собой хорошо зарекомендовавшие себя высококачественные, эффективные и долговечные легкие заполнители, подходящие для широкого диапазона соискателей в секторе «Благоустройство, сельское хозяйство и строительство».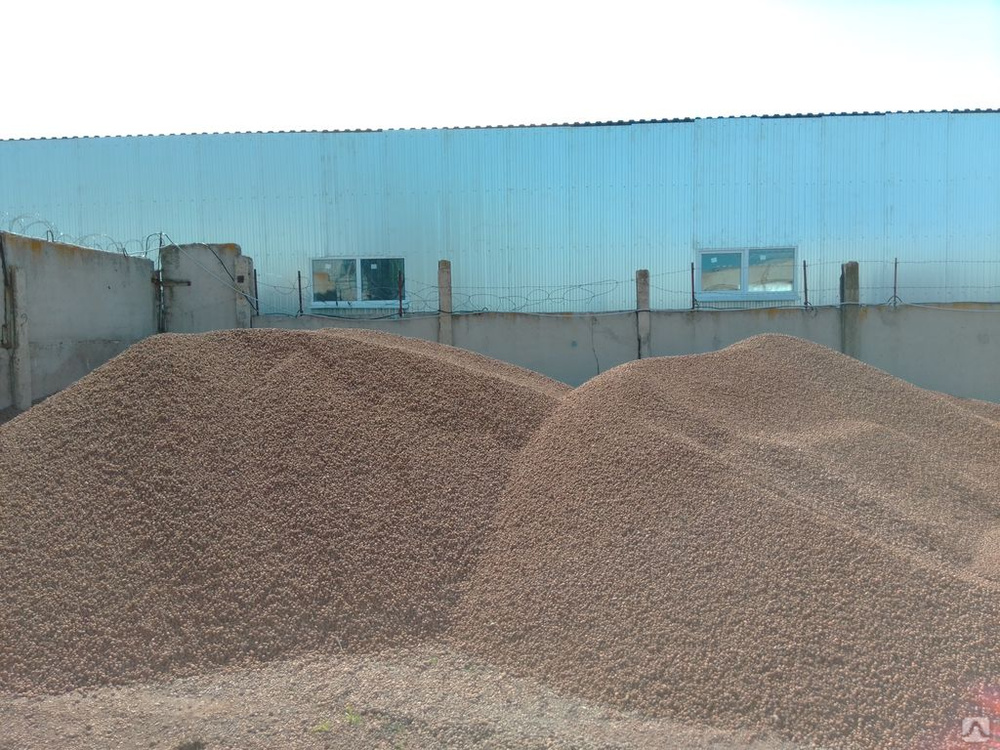
Leca — Легкий керамзитовый заполнитель
Легкий керамзитовый заполнитель Leca выдержал испытание временем в производстве стен Acotec.Leca заменила древесную стружку бетонным материалом в начале 80-х годов прошлого века Acotec. С тех пор эта экономичная технология перегородок успешно проникла на азиатские строительные рынки.Как сделать гальку из глины для гидропоники в домашних условиях LECA Hydroton
Легкий заполнитель из вспененной глины — часто называемый гидротоном или глиняной галькой — состоит из шариков глины, которые были перегреты во вращающейся печи от 1100 до более 2000 F. процесс вызывает лопание, которое создает характерные поры гальки.Эти поры в дополнение к промежуткам между галькой делают Hydroton легкой и воздушной средой для выращивания.What are Expanded Clay Balls? — Аква садоводство
Глиняная галька — это название, данное компании LECA Light Expanded Clay Gite или глиняным шарикам.
Гидротонная галька из керамзитовой гальки. Руководство по выращиванию. Эпическое садоводство.
. При поиске информации по этой теме вы найдете несколько названий: керамзитовая галька, глина и глиняные шарики — все это примеры. Он изготавливается путем нагревания глины до температуры более 2000 градусов по Фаренгейту с помощью вращающейся печи, которая придает ему характерную форму гальки. Этот процесс наполняет глину маленькими пузырьками воздуха, что делает ее идеальной для удержания кислорода, а также гранулы керамзитовой гальки50 л 8-12 мм: Amazon.co.uk
Керамзит — коричневый легкий заполнитель с номинальным размером частиц от 8 мм до 12 мм.
керамзитовых шариков в цементе — les6quarts.be
керамзитовых шариков в цементе; Внутреннее отверждение бетона с применением легкозернистой глины.Внутреннее отверждение для цемента — это практичный способ подачи дополнительной воды во всю бетонную смесь. Другими словами, достижение лучшей гидратации и меньшего количества w.Пеллеты из вспененной глины. Оптовая торговля — Specialist Aggregates Ltd.
Противоскользящий и тормозной песок. Фильтр для гравия и песка и средства для коррекции pH Сушеный в печи Природный гравий Сушеный в печи природный песок Легкие заполнители Тяжелые заполнители Металлы и огнеупоры Галька и кровля Отдых Спорт и досуг Стекло для терраццо и открытого бетона Защита от ультрафиолетовых лучей Glo в темноте и днем GloHow to Используйте гранулы из вспененной глины Hydroton в саду
Что такое гранулы из гидротонной / вспененной глины? Гранулы из керамзита Hydroton изготавливаются путем нагревания глины до температуры более 2000 градусов по Фаренгейту.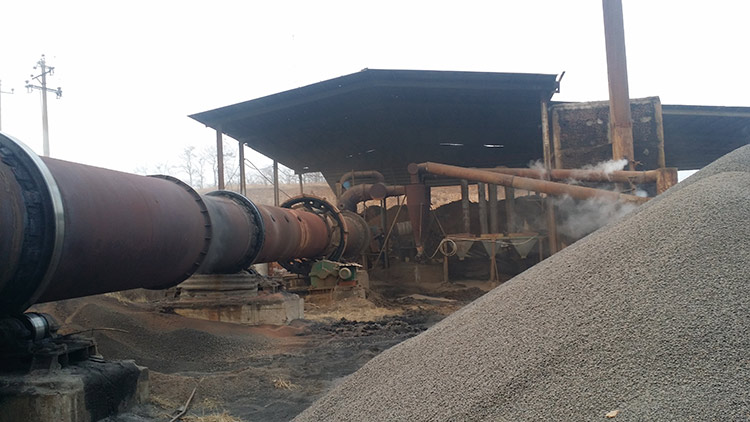