Технология изготовление топливных брикетов из опилок + Видео.
В данном материале описана технология производства топливных брикетов из опилок и другого растительного сырья.
Сырье может представлять собой любые растительные отходы:
- отходы деревообработки;
- отходы сельскохозяйственного растениеводства;
- листва;
- брикет может включать в свой состав вторичное сырье: дрова, старую древесину, макулатуру.
Для переработки опилок понадобится следующее оборудование:
- измельчитель сырья;
- сушилка;
- пресс для брикетов;
- упаковочное оборудование;
- для больших производств понадобится транспортные коммуникации: конвейерные ленты, пневмотранспорт, погрузчики;
- инвентарь: инструменты, емкости.
В видео кратко можно посмотреть процесс, а ниже идет подробное описание как делают брикеты.
Технология производства топливных брикетов
В зависимости от сырья (опилки, листья, лузга)и вида брикета технологическая цепочка может отличаться, но большинство предприятий имеют полный набор указанных ниже технологических операций.
Измельчение и сушка
Эти операции могут меняться местами, либо отсутствовать при мелком производстве (домашняя установка, небольшой цех с небольшим количеством отходов).
Рекомендуем данные операции не исключать даже при небольших объемах, так как они повышают конечное качество брикетов:
- Сушка — обеспечивает лучшее прессование сырья. Как правило проводится в печах туннельного типа со шнековой подачей сырья.
- Измельчение — облегчает прохождение сырья на всех стадиях обработки. Проходит на дробилках различного типа (молотковые дробилки, щепорезы, промышленные шредеры).
Прессование
как работает пресс для брикетов RUF
Подготовленное сырье поступает в установку, где под действием давление нагревается и спекается за счет выделения естественного связующего – лигнина.
При использовании вторичного сырья могут применяться дополнительные связующие, которые вводятся в сырье перед прессом.
В таком случае понадобится бак-смеситель, где сырье и добавки будут смешиваться до равномерного распределения по объему.
При прессовании сырье под давлением нагревается до 240…320 °С, за счет чего происходит спекание брикета. В отдельных моделях прессов сырье может предварительно нагреваться с помощью ТЭНов при поступлении на шнек (брикеты pini-kay).
При прессовании важно не перегружать пресс (работать с соблюдением норм расхода), следить за однородностью сырья.
Смотрите подборку видео как делают топливные брикеты (евродрова) в домашних условиях.
Охлаждение и резка на поленья, упаковка.
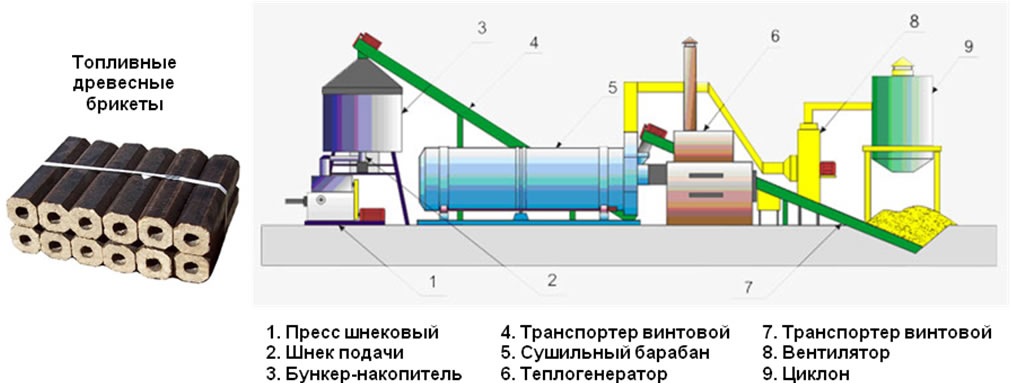
При выходе с пресса готовый брикет обрезается (обламывается) и поступает на паллеты, где охлаждается короткое время. После чего продукцию необходимо упаковать, для того чтобы она не напитывала влагу.
Готовая продукция
брикеты из опилок RUF
В результате прохождения через пресс, получают топливные брикеты трех основных видов:
- RUF (Руф). Получают в гидравлических прессе, готовый продукт выходит в виде кирпича (150×90×60 мм). Требует обязательной упаковки в водонепроницаемую пленку.
- Pini Kay (Пини Кей). Выглядят как брусок заданной длины (25…40 см), производят с помощью шнекового пресса. При производстве брикет выходит с готовой спекшейся пленкой, которая частично препятствует впитыванию влаги. Продукцию можно паковать в полиэтиленовые мешки (биг-беги).
- Nestro (Нестро). Цилиндрические бруски (Æ50…90 мм, длина – 50…100 мм), производятся на гидравлических прессах.
Примеры видео смотрите по ссылке: Какие бывают виды топливных брикетов.
Важные характеристики техпроцесса
Влажность сырья
топливные брикеты pini-kay
Технология производства для любых брикетов требует сушки и измельчения сырья. Если данным фактом пренебречь, то в результате реакция спекания и склеивания при воздействии температуры будет неэффективной: на выходе из перса брикет может развалиться.
Операцией можно пренебречь, если у вас штучное производство (для собственных нужд в очень малых объемах). При условии, что есть помещение, площадка, где сушить сырье и хранить его в сухом состоянии до процесса запуска пресса.
Помните о погоде: от сырья, хранящегося в сырых сараях, толку не будет. Перед тем как сушить щепки или опилки естественным путем, убедитесь, что на отведенной для этого площади, помещения, нет доступа влажного воздуха с улицы.
Альтернативный способ изготовления брикетов — как делают в Африке.
Фотоподборка.
Производительность
Объем производимых брикетов напрямую зависит от доступа к сырью, объемов сбыта и собственного потребления.
Чтобы определиться с объемом, вы должны хотя бы примерно понимать какая часть продукции будет идти на собственные нужды, а какая – на реализацию.
- На обогрев ваших помещений количество брикетов можно примерно рассчитать как ½ от объема ранее затрачиваемых дров. Читайте также чем выгоднее отапливать дровами или брикетами.
- Часть продукции может тратиться на сам производственный процесс – для подогрева воздуха на сушке (примерно 1…3%).
Рассчитывая производительность, учитывайте, что большинство небольших компаний производство ведут до отопительного сезона, после идет активный всплеск продаж, а далее на рынке наступает застой: оборудование останавливается, идет накопление сырье. Работа возобновляется только весной.
Рассчитывая объемы производства, учитывайте фактор сезонности.
Большие компании работают более ритмично: при постоянном доступе к сырью они производят брикеты круглый год. Но торгуют как все – месяц-два перед отопительным сезоном. После чего весь произведенный брикет идет на склад, если нет другого рынка сбыта (или на экспорт в Европу, но европейцы покупают – крупным оптом).
Объем вложений
Также можете ознакомиться с обзором производителей оборудования для изготовления топливных брикетов.
Сделать топливные брикеты своими руками по технологии «руф» или «пини-кей» — достаточно накладно на первом этапе:
- для микробизнеса вложения составляют порядка для 2…4 тыс. долларов для кустарного производства;
- для малого и среднего бизнеса минимум придется стартовать от 10 тыс. долларов на небольшую лесопильню;
- профессиональные линии для постоянной работы в данном направлении стоят от 100…130 тыс. долларов и выше.
Технология производства топливных брикетов из влажного измельченного сырья — — из влажного мелкого сырья
Технология производства топливных брикетов из влажного измельченного сырья
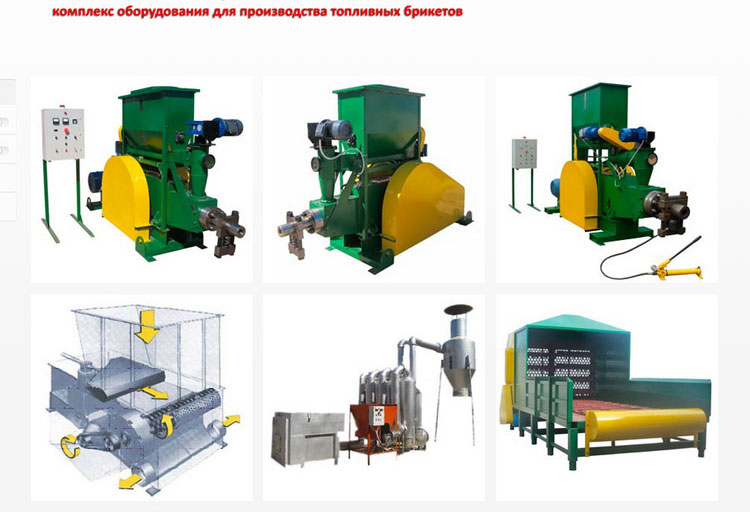
Характеристики сырья: влажность – до 65%, размер частиц – до 50х25х10 мм.
Сырьё подвозится автотранспортом (либо погрузчиком) и ссыпается на механизированный склад “подвижный пол” (1). Стокеры подвижного пола имеют гидравлический привод и под его действием совершают возвратно-поступательные движения. Лопатки (“крылья”) стокеров имеют клиновидную форму, поэтому при движении стокеров сырье с регулируемой скоростью подачи направляется к цепному (скребковому) транспортеру (2), далее сырье подается на дисковый сепаратор (3). На нем от сырья отделяется камни, коренья и т.п. примеси, которые попадают в переносной контейнер (на схеме не показан), а сырьё через самотёк попадает в загрузочную секцию Агрегата Сушки-измельчения (4). Сюда же подаются продукты горения из теплогенератора (5) (подробнее – в статье «Технология сжигания биомассы») и засасывается холодный атмосферный воздух через аварийно-растопочную трубу (6). Первоначально смешиваются продукты горения и холодный воздух, пропорция смешивания регулируется автоматически, что обеспечивает поддержание заданной температуры теплоносителя.
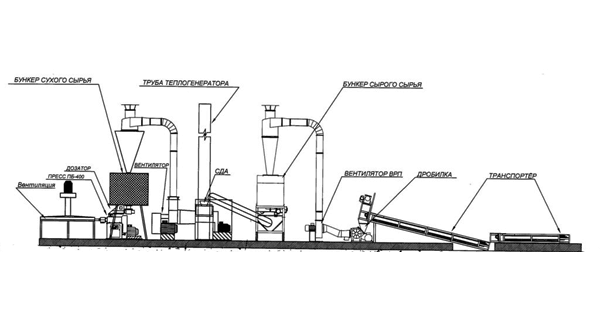

Теплогенератор в данной схеме может загружаться топливом как в ручном (через дверцу), так и в автоматическом режиме — из бункера топлива (7). Пополнение бункера топлива происходит автоматически за счет возврата части муки от осадочного циклона (8) системой пневмотранспорта (17). Опционально бункер топлива может пополняться дополнительным транспортером с отдельного склада топлива (не показан).
Технологии производства топливных шайб и четвертаков имеют незначительные отличия от технологии производства брикетов. Перейти к описанию технологии производства топливных шайб и четвертаков.
Технология производства топливных брикетов в форме параллелепипедов (кирпичиков) имеет незначительные отличия. Перейти к описанию технологии производства топливных брикетов в гидравлических прессах.
Брикеты
Брикеты — спрессованные частицы растительного происхождения, имеющие форму цилиндров диаметром более 25 мм. (либо имеющие в сечении многоугольник, иногда — с отверстием в центре). Брикеты могут быть изготовлены из древесины, тростника, торфа, куриного помета, лузги, соломы, угольной пыли и многих других видов растительного сырья, а также твёрдых бытовых отходов, макулатуры, использованных автопокрышек. Чтобы получить качественные брикеты, необходимо выполнить 3 основных условия: использовать качественное оборудование, строго соблюдать технологию производства, и использовать качественное сырье. …
Экономика производства топливных брикетов
Статья «Экономика производства топливных гранул» дает представление об основных экономических показателях процесса производства топливных пеллет. Аналогично обстоят дела с древесными брикетами, их, наконец-то, распробовали и в России. «Евродрова» охотно покупают и для отопления загородных домов, и для бань, и для каминов. Последнее время спрос на брикеты значительно превышает предложение, из-за чего цена на них иногда доходит до 12 000 руб/т. Такой спрос обеспечивается несколькими серьезными преимуществами брикетов: высокой калорийностью (почти в два раза больше дров) и, самое главное, — длительностью горения — до 12 часов. Экономика производства топливных брикетов по состоянию на апрель 2013 года — в полном тексте статьи.
Топливные брикеты своими руками, домашнее изготовление топлива
В последнее время стало модным использовать для растопки печей не только традиционное топливо в виде дров, ну и другие, альтернативные варианты. Например, все большей популярностью пользуются топливные брикеты, спрессованные под высокой температурой натуральные материалы: опилки, лузга подсолнечника, торф, солома и т.д. Созданные из биологических отходов, 100% натуральные и экологичные, брикеты топлива позволяют эффективно и недорого отпивать дом, баню.
В этой статье мы поговорим о том, как сделать топливные брикеты своими руками из подручных материалов. Для этого вам потребуется купить или сделать подходящее оборудование для переработки отходов жизнедеятельности и изучить, как правильно изготавливать евродрова. Изготовление топливных брикетов своими руками позволит вам решить сразу несколько проблем:
- избавится от отходов;
- получить эффективное и технологичное топливо для отопления жилища;
- сэкономить средства на дровах.
Самодельные брикеты топлива могут быть любой формы
Основные преимущества
Топливные брикеты являются современным видом альтернативного топлива. Их можно использовать в любых печах, каминах, котлах, мангалах, барбекю. Представляют собой евробрикеты цилиндрические заготовки, напоминающие дрова, либо прямоугольные кирпичики. Небольшие габариты позволяют размещать их в топках любого размера.
Из чего делают брикеты? Чаще всего используют древесину (опилки, стружку, пыль), но используют и солому, бумагу, торф, уголь, шелуху семян или орехов и даже навоз. Состав евробрикета может значительно отличаться, в зависимости от того, какая технология используется при производстве.
В то же время все виды сырья, из которого можно произвести еродрова являются природными, абсолютно натуральными.
Изготовление топливных брикетов в домашних условиях позволит создать экологичный продукт, который практически полностью будет сгорать в топке печи и при этом выделять минимум дыма.
Сделанный в домашних условиях евробрикет можно использовать для растопки банной печи или отопления дома. Поскольку сырье спрессовано достаточно сильно и количество влаги минимальное, топливный брикет долго горит, постоянно выделяя большое количество тепла. Интересный момент подметили люди, уже активно использующие подобное топливо: если растапливать экодровами свой мангал и жарить на нем еду, при попадании на брикеты жира он не воспламеняется.
Склад готовых екробрикетов кустарного производства
Для печей, котлов и каминов, работающих на твердом топливе, отличным вариантом станут брикеты из опилок. Они неспешно разгораются, но после горят длительное время и выделяют большое количество тепла. Объясняется это высокой плотностью изделия из прессованной древесины. Теплоотдача от брикетов значительно превышает уровень тепла, получаемый при сгорании даже самых сухими дров, хранение и сушка которых заняли минимум год.
Влажность топливных брикетов составляет 8-9%, сухие дрова в свою очередь имеют показатель в 20%. Получается, что изготавливаемый из той же древесины брикет, горит лучше самой древесины. Такой эффект образуется вследствие того, что при горении топливным брикетам не нужно испарять большое количество влаги.
Брикет горит стабильным огнем, без всплесков, искр, треска, а количество дыма, выделяемого при горении, можно охарактеризовать как малое. Закладывать подобное топливо в печь крайне удобно, поскольку все изделия имеют одинаковую правильную форму.
Небольшая хитрость: если требуется создать интенсивный огонь с большой теплоотдачей, следует закладывать топливные брикеты в топку на некотором расстоянии друг от друга и, наоборот, для поддержания тления, необходимо плотно соединить в топке все экодрова.
Размещение в топке экологических самодельных брикетов топлива
Как и любой товар, топливные брикеты не лишены минусов:
- Прежде всего стоит отметить, что они очень уязвимы к влаге, поэтому продаются в целлофановой упаковке.
- Брикеты не способны противостоять механическим воздействиям, особенно изделия, сделанные по технологии РУФ, не обожженные снаружи.
- Если вы захотите наладить изготовление подобных вещей дома, это влетит вам в копеечку, хотя на длинной дистанции выгода непременно будет. Дело в том, что вам придется приобрести установку для измельчения, сушилку и пресс-машину, чтобы проводить весь цикл работ с сырьем. С подходящим оборудованием наладить кустарное производство топливных брикетов можно будет даже в собственном гараже.
Оборудование и сырье
Создавать топливные брикеты своими руками можно из различных видов отходов жизнедеятельности человека. В принципе можно использовать любые вещества, которые смогут нормально гореть. Какие бытовые отходы могут стать полноценным сырьем:
- Прежде всего древесина, опилки и стружка, древесная пыль, листья и ветки деревьев. Порода дерева не играет первостепенную роль, но лучше, чтобы опилки были березовые, дубовые, из ольхи или осины.
- Солома, оставшаяся после сбора урожая пшеницы или кукурузы.
- Картон и бумага. Топливные брикеты из бумаги своими руками сделать куда проще, чем из древесины, вот только бумажный вариант прогорать будет быстрее.
- Хорошим, но редким сырьем могут стать остатки и шелуха семечек, скорлупа орехов.
Состав брикетов может быть разный, а отсюда различные клеевые возможности смеси. В зависимости от применяемого сырья в некоторые брикеты добавляется глина, способствующая связыванию элементов, обычно в пропорции 10 к 1.
Древесные опилки могут стать лучшим сырьем
Чтобы создавать самодельные топливные брикеты понадобиться специальное оборудование. Можно заказать сразу целую линию для домашнего производства, обратившись в конкретную фирму, а можно собрать оборудование по частям, ведь технология изготовления топливных брикетов в сущности проста.
Вся технология основана на трех этапах производства:
- Первый этап предполагает начальную подготовку сырья.
Имеющиеся отходы следует раздробить, размельчить до необходимой консистенции, чтобы состав смеси был однородным.
- Второй этап предусматривает доведение смеси до готового состояния методом сушки. На сушильном станке сырье избавляется от влаги.
- Третий этап предполагает изготовление продукции, здесь происходит прессование топливных брикетов на специальном станке под высоким давлением и температурой.
Шнековый пресс для работы с сырьем
Соответственно для каждого этапа вам потребуется подобрать станок, подходящий под ваше сырье: дробилку, сушилку и пресс.
По большому счету производство топливных брикетов своими руками мало чем отличается от промышленного, разве что здесь не применяют завышенных критериев к качеству продукции и не упаковывают готовые изделия в герметичную оболочку.
Еще одно отличие домашнего производства заключается в том, что в принципе можно исключить сушилку из линии. Сушить сырье и брикеты можно естественным путем под солнцем. Кстати, если сырьем выступают готовые древесные опилки или шелуха семечек, то и дробилка может вам не понадобиться.
Особо умелые мастера сами изготавливают пресс, исходя из своих потребностей и возможностей. В наше время доступ к информации не ограничен, поэтому чертежи устройства любого типа можно найти в свободном доступе в сети. Собрав по чертежам свой пресс, вы сможете сделать уникальный брикетированный товар, который отлично будет гореть в топках печей.
Как изготовить пресс-машину могут подсказать знакомые, уже имеющие дело с подобной техникой кустарного или заводского производства. Можно выбрать шнековый, гидравлический или ударно-механический вариант.
Станок для производства брикетов топлива
Для установки оборудования вам потребуется приличное помещение. В нем придется разместить все станки, сырье и получившиеся изделия. Желательно обеспечить комфортные условия для сушки, чтобы влажность брикетов была минимальной, поэтому позаботьтесь о вентиляции. Для подключения станков потребуется электричество, ну а так как мы изготавливаем топливо, не стоит забывать и о мерах пожарной безопасности.
Производство
Процесс производства, как мы уже говорили, достаточно простой, даже несмотря на то, что проходит он в домашних условиях.
Чтобы сделать брикеты для топки печей своими руками необходимо:
- Подготовить качественное сырье, измельчить его до нужной консистенции, просушить. Для того чтобы улучшить качество горения, в любое сырье можно добавить бумагу.
- При необходимости добавить связующий элемент (глину, лигнин), долить воды, загрузить в пресс-машину.
- Провести прессование изделия в подходящей форме при высоком давлении и желательно высокой температуре.
- Высушить готовое изделие, по возможности упаковать для защиты от внешних факторов. При сушке можно использовать ветошь и бумагу, способные вытянуть из брикета остатки влаги.
Проведя все эти работы вы получите отличное топливо, которым можно легко и быстро истопить баню, обогреть дом. При этом на длительном временном отрезке вы ощутите выгоду и экономию средств от применения подобных экодров.
Отметим, что во время работы следует постараться добиться влажности брикетов не более 10-12%, чтобы они отлично горели. Промышленно изготовленные брикеты имеют влажность менее 10%.
Чтобы убедиться в отменных характеристиках подобного вида топлива, можно купить себе немного евробрикетов на пробу в любом магазине. В то же время для создания подходящей атмосферы можно иногда растапливать камин или печь обычными дровами, ведь применение разных видов топлива не несет взаимоисключающий характер.
Как изготовить топливные брикеты своими руками
Вопрос дачного отопления с каждым годом становится все более острым: все дорожает, как дрова, уголь или торф, так и их доставка. Между тем, потенциальное топливо буквально «валяется» у нас под ногами. В качестве него нам могут послужить стружки и опилки, сухая листва и солома, шелуха всех зерновых культур, щепа и срезанные при обхаживании сада ветки, негодные доски – все это вполне годится, чтобы изготовить топливные брикеты своими руками. А если договориться с управляющим близлежащего лесхоза, парка или свести дружбу с хозяином лесопилки, материала под брикеты для личного пользования у вас будет вполне предостаточно.
Самодельные брикеты из опилок – прекрасное топливо
Для справки
Древесные отходы в их естественном виде отправлять в печь или котел нецелесообразно и даже бессмысленно. Их рыхлость приводит к тому, что прогорание происходит в кратчайшие сроки и сопровождается слабой теплоотдачей. Кроме того, значительная часть опилок просыпается с колосников в зольный поддон, что уменьшает КПД и повышает расход. Всех этих недостатков лишены топливные брикеты из опилок. С экономической точки зрения неразумно не использовать в собственных целях отходы, имеющиеся на даче в изобилии.
В качестве сырья можно использовать и стружку, и солому, и сено, и сухую листву
Плюсы топливных брикетов своими руками
Самодельное горючее имеет массу преимуществ.
- Для топливных брикетов в качестве сырья подходят практически любые отходы, кроме пищевых и искусственных.
В них можно вводить угольную пыль, которая считается неизбежными потерями.
- У топливных брикетов впечатляющая продолжительность горения – до 4 часов. И на протяжении всего этого промежутка будет выделяться тепло.
- Вполне доступно самостоятельное изготовление топливных брикетов. Причем для подобного производства не потребуется серьезных первоначальных вложений.
- При сжигании топливных брикетов дым практически не выделяется.
- Брикеты из опилок и прочих древесных отходов предельно экологичны, ведь для изготовления топливных брикетов применяются только природные компоненты.
- Такое топливо практично и экономично: его себестоимость при самостоятельном производстве в несколько раз ниже такого же количества угля либо дров, а энергоотдача такая же, а то и более высокая. Кроме того, пепел от брикетов из опилок и других отходов из древесины – прекрасное удобрение для культурных растений.
Правда, производство топливных брикетов из опилок требует некоторых временных затрат и физических усилий. С другой стороны, в загородном доме всегда найдется свободное время. А труд, как известно, облагораживает.
Топливные брикеты многофункциональны
Сфера применения
Брикеты из опилок обладают довольно широкой функциональностью. Это топливо может применяться:
- для отопления жилого дома. Брикеты из древесного сырья из-за своей компактности годятся и для каминов, и для печей, и для твердотопливных котлов;
- при протапливании бань и саун, если основной дом у вас обогревается каким-либо другим образом. Брикеты идеально соответствуют всем экологическим условиям;
- на выездах на пикники. Они являются прекрасной альтернативой углю и дровам. Причем могут похвастаться замечательным свойством: при попадании на раскаленный брикет жира, последний не воспламеняется и не чадит.
Кстати, брикеты из опилок, пожалуй, следует рекомендовать и для приготовления пищи в условиях закрытых помещений: запах гари отсутствует, а блюдо обжаривается предельно равномерно.
Немного теории
Перед тем, как заняться изготовлением самодельных брикетов, следует ознакомиться с этапами их промышленного производства. Это поможет не наделать ошибок при создании топлива своими руками. Алгоритм действий на производстве следующий.
- Сырье измельчается до примерно одинакового размера частиц исходного материала.
- Опилки сушатся; уровень влажности должен снизиться процентов до 10.
- Далее идет в ход либо гидравлический пресс, либо экструдер, в зависимости от способа формовки топлива, которому на производстве отдано предпочтение.
- На конечном этапе готовый продукт упаковывается во избежание абсорбции им влаги из атмосферы.
На производстве при изготовлении брикетов из опилок никакого склеивающего материала не используется. Под давлением пресса при самопроизвольном разогреве сырья из древесины выделяется лигнин, который и препятствует распадению готового продукта, сохраняя его заданную форму.
Особенности производства брикетов своими руками
Оборудование, доступное для изготовления топлива в домашних условиях, не позволяет прессу давить на сырье с силой, достаточной для того, чтобы начал выделяться лигнин. Поэтому изготовить брикет без связующих веществ в кустарном производстве не получится.
Кроме того, затраты на сушильное оборудование сделают готовую продукцию нерентабельной – дешевле будет купить традиционные уголь с дровами. С другой стороны, это неудобство несколько упрощает изготовление брикетов своими руками: можно пропустить этап сушки с соблюдением ряда технологических требований. Зато появляется новая трудность: после того, как вы прогнали сырье через пресс для топливных брикетов своими руками, нужно поместить готовую продукцию на просушку. То есть обеспечить пространство под навесом в летнее время или помещение с низкой влажностью и достаточной температурой в другие сезоны.
Впрочем, производством топливных брикетов настоящие мастера топливного дела занимаются исключительно в дачный сезон – а зимой их активно расходуют.
Необходимое оборудование
Несмотря на относительную несложность получения топлива, кое-каким оборудованием обзавестись все же придется. Или приспособить имеющееся под новые нужды. Что потребуется:
- Измельчитель. Без него не обойтись, поскольку, чем мельче сырье, тем плотнее готовый брикет. А при изготовлении его своими руками в ход идет материал самых разных фракций. Тратиться на закупку не придется, если в вашем хозяйстве имеется устройство, рубящее растительность для ее отправки в компост. Изобретатели с умелыми руками приспосабливают под измельчитель старую стиралку активаторного типа – меняют собственно активатор ножами;
- Какая-либо емкость, где сырье будет замешиваться перед помещением в матрицу. Неплохо было бы дополнить «корыто» миниатюрной бетономешалкой или строительным миксером. В отсутствие того и другого готовьтесь к тяжелой физической работе по вымешиванию сырья;
Пресс для брикетирования можно сделать самостоятельно
- Пресс для производства топливных брикетов. Может быть ручным или гидравлическим, иметь вид настенной или напольной установки. В общих чертах пресс для производства брикетов из опилок и других растительных отходов состоит из основательной рамы, выполненной из стали, и того, что можно назвать рабочей частью;
- Матрицы, с помощью которых будут формироваться брикеты.
Могут быть в виде стандартных кирпичиков, но удобнее использовать цилиндрические формы – меньше возни. Хотя складировать и хранить будет несколько сложнее. Матрица обязательно должна иметь перфорированные стенки: через отверстия будет отводиться выдавливаемая прессом из заготовки влага.
Особое внимание стоит уделить моменту прессования. Мускульные воздействия – это траты времени и сил при низкой эффективности. Опытные мастера рекомендуют оснащать пресс для производства топливных брикетов гидравлическим домкратом от автомобиля. Его следует фиксировать на верхней раме пресса вверх ногами.
Алгоритм изготовления топливных брикетов
Своими руками брикетирование проводится не так, как на производстве. Начальный этап схож: ведется измельчение отходов древесного производства. Но затем идет не сушка, а, напротив, замачивание в воде. Или, по крайней мере, хорошее увлажнение, чтобы не пришлось потом сцеживать избыточную влагу.
Далее вводится связующее вещество. Здесь есть три варианта:
- Глина.
Самый дешевый и общедоступный наполнитель. Пропорции с основным материалом 1:10. Прекрасно связывает исходные древесное сырье, однако после использования готовых брикетов получается значительное количество зольных отходов: глина практически не горит.
- Обойный клей. Лишен недостатков предыдущей добавки, вводится в меньшем количестве, но делает производство заметно более дорогим.
- Любая макулатура, включая картон, предварительно измельченная и размоченная. Никаких отходов, практически никаких затрат, пропорции – как в случае с глиной. Недостатка два. Чем мельче фракция опилок, тем больше требуется бумажного наполнителя – это раз. Второе: сушить готовые брикеты придется значительно дольше.
Следующим шагом будет перемешивание – ручное или механизированное. Чтобы изготовить по-настоящему качественный брикет, требуется довести массу до максимально доступной однородности.
Пресс может быть и настенный
Далее сырье закладывается в форму для брикетирования, и в ход идет пресс. На выходе получаются брикеты заданной формы, которые отправляются на сушку. Раскладывать их следует достаточно свободно, чтобы было пространство для вентиляции. Для ускорения процесса высыхания рекомендуется периодически топливо переворачивать. А еще – перекладывать элементы бумагой либо сухой ветошью – эти материалы быстро вытягивают из брикетов избыточную влагу.
Сушить топливные брикеты следует до тех пор, пока их влажность не достигнет хотя бы показателей сырых дров, то есть – 25 %. На деле желательно добиться еще меньшей влажности – теплоотдача затем будет выше. Вы же не торопитесь, так что в жаркую погоду вполне можете позволить себе подержать топливные брикеты на солнышке на неделю дольше. Тем теплее будет в жилище зимой. Учтите, что торопиться вредно: котлы на твердом топливе, так же, как гидролизные, работают только на горючем, чья влажность не выше 30 %. Поторопитесь – будете оплачивать дорогостоящий ремонт или вовсе придется покупать новое отопительное оборудование.
Хорошо просушенное топливо убирается на хранение. Держать брикеты можно в не отапливаемом и достаточно сыром месте, если расфасовать их по полиэтиленовым мешкам, плотно затянуть горловину и герметизировать ее несколькими слоями скотча, проложенными внахлест.
Есть и поводы для сомнений
Пора подумать
Прежде, чем с энтузиазмом заняться брикетированием опилок, решите для себя, насколько вы в этом заинтересованы. При всей внешней простоте процесса, он имеет и существенные недостатки.
- Подготовка сырья и прессование его по формам отнимает достаточно много времени и требует серьезного физического напряжения.
- Если вы хотите, чтобы на просушивание готовых брикетов не влияла погода, придется выделить под них просторное, проветриваемое, сухое помещение, которому явно можно найти другое применение.
- Модернизация с внедрением электрооборудования сказывается на стоимости продукции. В результате изготовление брикетов своими руками становится не способом сэкономить, а хобби, причем недешевым.
- А главное: самодельный брикет из опилок по качеству все же проигрывает фабричному евротопливу.
Если же вы всерьез намерены рационально использовать имеющиеся в вашем распоряжении отходы, подумайте о том, чтобы на них еще и заработать. То есть – о производстве топливных брикетов из опилок в более массовом количестве. Неплохой может получиться бизнес!
А о том, как изготовить пресс, смотрите видео:
Как делать брикеты из опилок
На фоне других видов твердого топлива брикеты из отходов деревообработки выглядят не слишком популярными. Это можно объяснить наличием более доступных в плане стоимости дров, притом, что способ сжигания тех и других одинаков. Однако, списывать со счетов данное топливо не стоит, так как оно имеет массу достоинств. Некоторые домовладельцы, оценившие эти преимущества в полной мере, даже начали изготавливать топливные брикеты своими руками. Мы же рассмотрим, как это делается и стоит ли игра свеч.
Общая информация о брикетах
Сырьем для данного вида биотоплива являются мелкие древесные отходы, в основном опилки. Конечно, их можно жечь и так, но это не очень удобно, топлива уходит много и оно быстро прогорает. А все потому что плотность древесной массы невелика, куда больше тепла получится, если сырье предварительно спрессовать. В этом и заключается технология производства брикет.
Помимо древесины в брикетах используются и другие виды сырья, например, солома или каменный уголь. Но поскольку технология изготовления несколько отличается, то ее рассмотрение – вопрос отдельной темы.
Вначале происходит переработка опилок и других отходов, их измельчение и просушивание. Влажность сырья перед прессованием должна находиться в пределах 6—16%, что и обеспечивает сушильное оборудование. Затем идет собственно изготовление топлива, что производится двумя способами:
- с помощью гидравлического пресса сырье формуется в брикеты прямоугольной или цилиндрической формы.
Процесс проходит при давлении от 30 до 60 МПа и высокой температуре;
- методом экструзии на шнековом прессе из готовой смеси выдавливается брикет 4-х или 6-гранной формы под давлением около 100 МПа. Изделие проходит термическую обработку.
Следует отметить, что производство топливных брикетов из опилок не предусматривает добавления в состав смеси связующих компонентов. Под воздействием высокого давления и температуры частицы склеиваются лигнином, он содержится в любой древесине. В результате получаются «кирпичики» или «колбаски», чья теплотворная способность составляет до 5 кВт/кг. Производственный процесс показан на видео:
Примечание. Такую же теплоту сгорания имеют пеллеты, да еще некоторые марки углей. Ниже представлена сравнительная диаграмма, где показан расход разных энергоносителей для выделения одного количества теплоты:
Оборудование для производства брикетов
Прессовое и сушильное оборудование, представляющее собой технологическую линию по производству брикет, в домашних условиях недоступно из-за своей высокой стоимости и габаритов. Домашние мастера используют самодельные станки, позволяющие отформовать смесь для топливных брикетов в кирпичики или «шайбы». Главные элементы подобной установки – это механизм, создающий давление, и сама форма. Как их объединить в одно целое – решать вам, вариантов существует множество.
На данный момент самодельный пресс для брикетов изготавливается домашними умельцами в 3 исполнениях:
- с ручным приводом;
- с применением домкратов;
- с гидравлическим приводом.
Первый вариант самый простой. Из металлической профильной трубы на сварке выполняется рама, которая для удобства может прикрепляться к стене дома или сарая. В нижней части рамы неподвижно устанавливается форма круглой или прямоугольной конфигурации, а сверху на шарнире крепится длинный рычаг. К нему присоединяется нажимной элемент, входящий внутрь формы с небольшим зазором.
Второй и третий варианты отличаются тем, что пресс для опилок механизирован домкратом либо гидроприводом, устанавливаемым вместо рычага. Для того чтобы во время прессования из формы могла вытекать вода, в ее донной части делается несколько небольших отверстий. Конструкция такого станка показана на видео:
Как делать брикеты?
Технологический процесс, применяемый на производстве, в домашних условиях осуществить невозможно. Причина – отсутствие прессового или экструзионного оборудования, способного создать давление хотя бы 30 МПа. Без этого нельзя выделить из древесины лигнин и самодельные брикеты не спрессуются. Выход простой: надо добавить связующее вещество, в качестве которого выступает обычная глина. Ее смешивают с опилками в пропорции 1:10 по массе (1 кг глины на 10 кг отходов), разбавляют водой и тщательно перемешивают.
Получившимся составом наполняют форму и приводят в действие механизм. Если изготовление топливных брикетов производится ручным способом, то необходимо приложить максимальное усилие и держать рычаг до тех пор, пока не сбежит вода. Затем изделие аккуратно извлекается и размещается на площадке под открытым солнцем для просушки. Можно снова приступать к заполнению формы и выдавливанию следующего «кирпича».
Стоит ли делать брикеты в домашних условиях?
В реальной жизни топливные брикеты из опилок, сделанные своими руками, получаются не совсем такими, как это преподносится некоторыми интернет-ресурсами. Это заставляет сомневаться в целесообразности всего предприятия, и вот почему:
- на красочных видеороликах из интернета процесс выглядит просто и легко. В действительности это тяжкий труд, чтобы заготовить нужное количество топлива на сезон, надо затратить немало времени и физических усилий;
- теплота, выделяемая самодельными брикетами при сжигании, гораздо ниже, чем у заводских изделий. Все дело в недостаточной плотности «кирпичей», так как домашние приспособления не могут обеспечить требуемое давление прессования;
- просушивание на солнце не может сравниться с промышленными сушилками, поэтому в топливе содержится влага, влияющая на теплотворную способность;
- самодельное топливо из опилок содержит глину, что не сжигается в топке котла.
Значит, золы будет оставаться больше.
Заключение
Самодельные брикеты позволят достичь двух вещей: исключить мусор и пыль в доме от опилок и избавиться от частых загрузок топки традиционного котла или печи. Когда есть достаточное количество отходов деревообработки и вы желаете использовать их в качестве топлива, необязательно затевать столь трудоемкий процесс. Понятно, что интервал между засыпками топлива в теплогенератор хочется увеличить. Но есть и другой выход, например, котел на опилках продолжительного горения, который при желании можно изготовить самостоятельно. Решение принимать вам.
Топливные гранулы производятся методом прессования древесных отходов очень мелкой фракции. Для получения отходов такой лес
Сухая стружка – это идеальное сырье для производства гранул, она как правило остается от мебельного производства, для такого сырья нужно минимум оборудования. Аналогично хорошим сырьем так же является сухие опилки (до 12% влажности). Из данного вида сырья получаются очень хорошие по качеству топливные гранулы, которые пользуются спросом на любом европейском рынке. А если для производства гранул используется более влажное сырье (13-55%) опилки, стружка, щепа, то для их переработки необходимо первоначальное подсушивание до нормальных 12%.
В таком случае процесс удорожается и усложняется за счет покупки специализированной сушильной установки, а по стоимости она может доходить до 50% стоимости всего оборудования в производственной линии. В связи со специфичностью исходного материала, многие предприятия сталкиваются с проблемой нехватки сырья, встает вопрос собственном «производстве» сырья. Щепу, подходящую для производства гранул, как правило получают из отходов деревообработки и лесопиления (обрезки доски, горбыль) при помощи щепорубительной машины. Экономически доказано что собственное производство сырья оправдывает себя, с его помощью можно постоянно поддерживать высокую производительность предприятия и извлекать прибыль.
Менее развитой, на сегодняшний день, является процесс производства топливных брикетов, но в тоже время этот процесс более прост. В Европе насчитывается несколько некрупных предприятий производителей оборудования. В принципе технология производства брикетов ничем не отличается от технологии производства гранул, но обычно не превышают 500-800 кг/час. При производстве топливных брикетов используют сухое размельченное сырье. Выгоднее всего применять такие линии на мебельных производствах. Топливные гранулы первого класса преимущественно являются экспортным продуктом, а брикетированное топливо возможно в скором времени станет довольно популярным на российском рынке.
Варианты станков для изготовления топливных брикетов
Современные технологии проявляют себя там, где, казалось бы, ничего нового не придумаешь. Примером тому являются топливные брикеты или, как их еще называют, евродрова. Это та же древесина, но за счет спецобработки получившая новые свойства, позволяющие ей сгорать с большей эффективностью.
Для их создания не требуются космические технологии – простейший станок для изготовления топливных брикетов представляет собой пресс. Поэтому наладить получение современного топлива с некоторыми свойствами, улучшенными по сравнению с обычными дровами, можно и своими руками.
Не забудь поделиться с друзьями!Содержание статьи
Чем хороши брикеты
Топливный брикет – измельченная древесина и древесные отходы, спрессованные в форму, удобную для транспортировки и хранения.
В результате обработки на станках прессованием под высоким давлением готовые брикеты приобретают новые качества. Их применение вместо обычных дров в печах, каминах и дровяных котлах дает следующие преимущества:
- повышенная температура горения и, соответственно, лучшая теплоотдача;
- большая плотность брикетов приводит к более длительному горению одинакового объема;
- уменьшенное образование сажи и зольных остатков;
- брикеты выпускаются различной формы – короткие цилиндры, прямоугольные кирпичи.
Но в любом случае они удобны для хранения и переноски.
Если сравнивать с обычными дровами, то ни по одному параметру евродрова не будут хуже. К недостаткам можно отнести то, что по внешнему виду брикета не всегда можно определить конкретную древесину, из которой он изготовлен. И если, например, требуется именно березовый брикет, то приходится положиться на добросовестность производителя.
Изготовление промышленным способом
Первым этапом при получении топливных брикетов в промышленных условиях является измельчение материала на специальных станках. Зачастую сырьем для изготовления брикетов служат отходы деревообработки – стружки, опилки, щепки. Крупные куски дерева измельчаются до состояния опилок размером не более 4 мм.
Затем происходит тщательная сушка древесины. Удельная влажность материала доводится до 10% и даже меньше. Чем суше древесина для последующего брикетирования, тем лучше качество готового топлива.
Завершающий этап – получение самих топливных брикетов. Для этого подготовленное сырье подвергают мощному давлению. Происходит повышение температуры, а из древесной массы выделяется клейкий компонент – лигнин. При большом давлении и в присутствии связующего лигнина древесная масса формируется в единый твердый брикет.
Плотность такого продукта превышает плотность природной древесины в 1,5-2 раза, что обеспечивает брикетному топливу повышенную теплоотдачу и увеличивает длительность горения. При промышленном производстве евродров различают два способа сдавливания.
Метод прессования
В случае прессования исходное сырье подвергается давлению в подготовленных формах с помощью гидравлического пресса. Типовая величина давления в станке для прессовочного производства топливных брикетов составляет 300-600 атмосфер. На выходе получаются брикеты в виде прямоугольных кирпичей или коротких цилиндров, в зависимости от формы, в которой они прессуются.
Метод экструзии
При этом методе происходит постоянное выдавливание древесной массы из выходного отверстия рабочего канала. Сырье загружается в бункер, оттуда подается в рабочий канал, где дополнительно разогревается. Канал выполнен в виде конуса, сужающегося к выходу. Подача сырья из бункера и его сдавливание в рабочем канале производится на станке шнековым винтом. Подобный пресс на основе шнека обеспечивает давление на сырьевую массу до 1000 атмосфер. Выходящая из экструзионной установки спрессованная «колбаска» охлаждается и нарезается на стержни нужного размера.
Брикетирование своими руками – за и против
Самостоятельно сделать пресс и наладить производство топливных брикетов возможно. Но это требует материальных затрат, физических усилий и времени. Надо учитывать и то, что достичь качества евродров, выпускаемых в заводских условиях, вряд ли получится. Конечно, можно приобрести станок, мало уступающий производственному, но затраты на приобретение будут колоссальными.
Необходимо хорошо представлять, для чего требуется собственное производство, какие есть для этого условия и какие предстоят затраты. Может быть, и не стоит отказываться от обычных дров или лучше закупать для отопления уже готовые брикеты.
Плюсы
Положительные стороны домашнего изготовления состоят в следующем. Собственные топливные брикеты не дадут качества горения, как у покупных, но будут эффективнее дров.
Если есть возможность получения большого количества древесных отходов – опилок, мелких обрезков, стружки, коры, – то из них выгоднее сделать спрессованные дрова. Опилки и стружка в чистом виде малопригодны для горения, а после обработки на станке для прессовки опилок из них выходит хорошее топливо.
Можно пустить в дело не только дровяные, но и любые другие горючие отходы – солому, сухие листья, бумагу, картон. По отдельности из них горючий материал – никакой, а в брикетах будет толк. Брикетированное топливо удобно для складирования и для загрузки в топку.
Минусы
Но есть и недостатки, о которых следует помнить. Попытки улучшить качество самодельных евродров могут привести к тому, что будет покупаться дорогостоящее оборудование или постоянно дополняться существующее. В итоге окажется, что выпуск собственных брикетов не оправдает затраты.
Самодельным топливным брикетам требуется место для качественной сушки. Просушивание на солнце не всегда оправданно. Требуется просторное сухое помещение. Хранить самодельные брикеты тоже надо так, чтобы они не впитывали влагу.
Домашние связующие материалы
На самодельных станках добиться давления, при котором из древесной массы выделяется лигнин, практически невозможно. Поэтому в сырье для самостоятельного брикетирования обязательно надо добавлять материалы, которые помогут связать, склеить сырье в монолитный брикет. Чаще всего для этих целей используют:
- глину. Объемная пропорция 1 к 10 древесного сырья;
- клей. Годится любой, но, естественно, лучше брать самый дешевый;
- измельченную бумагу или картон. Помимо того что это тоже горючий материал, в бумаге содержится лигнин. А бумажный лигнин свои клейкие свойства проявляет при замачивании. Правда, потом понадобится дополнительное время на просушку брикетов, содержащих бумагу.
Чтобы связующие добавки в полной мере проявили свои свойства, их надо тщательно перемешивать с горючим сырьем, а потом эту смесь замачивать в воде.
Обратите внимание! При промышленном производстве сырье перед прессовкой тщательно высушивают, а при самодельном – тщательно замачивают.
В этом основное отличие домашнего изготовления. Сушат топливные брикеты уже после прессовки, чтобы они затвердели, держали форму и хорошо горели.
Самодельный станок
Встречаются сведения об изготовлении в домашних условиях самодельных шнековых экструзионных установок. Но даже создатели таких эффективных станков для производства топливных брикетов отмечают, что устройства требуют качественных материалов и использования электродвигателя. Гораздо легче сделать вместо сложного станка обычный пресс.
Ручной пресс
Прессы, использующие только ручные усилия, бывают двух видов – винтовые и рычажные. В винтовых вариантах шток, сдавливающий сырьевую массу, перемещается накручиванием винта. В рычажных прессах давление создается собственными мускульными усилиями, используя длину рычага. На винтовой установке достигается большее давление и качество топливных брикетов становится лучше. Но закручивание и откручивание винта требует времени, поэтому производительность невелика. Рычажные прессы работают быстрее. Нужно только продумать способ или механизм выталкивания готового брикета из прессовочной формы. В этой же форме должны быть отверстия для выхода воды при сдавливании, поскольку при ручном производстве сырье замачивается.
Измельчители
Важным этапом в производстве брикетов является измельчение древесного сырья. Конечно, можно делать это вручную, с применением простейших резаков. Но эффективнее будет механизировать этот процесс. Подойдет роторный станок, применяемый для измельчения растительной массы при производстве удобрений в домашних условиях. Умельцы применяют для этих целей и старые стиральные машины активаторного типа. На активаторе крепятся ножи, измельчающие загруженное сырье.
Станок с использованием готовых механизмов
Усовершенствовать ручной станок можно, снабдив его готовым гидравлическим домкратом или покупным гидравлическим прессом. Потребуются также материалы для крепления механизма и изготовления других элементов конструкции. Форма матрицы, в которой будет прессоваться сырье, может быть круглой или прямоугольной. Для круглых форм можно использовать стальные трубы нужного диаметра.
Основание станка для изготовления топливных брикетов сваривается из швеллеров. Для стоек подходят уголки размером 100 х 100.
Для формовочной матрицы берется толстостенная труба. Диаметр подбирается исходя из желаемых размеров готовых изделий. В трубе равномерно высверливаются несколько отверстий диаметром 4-5 мм для выхода воды при сжатии.
Матрица оборудуется съемным дном, необходимым для извлечения готовых брикетов. Но есть более перспективный вариант: дно приваривается к матрице намертво, а с внутренней стороны крепится пружина с диском чуть меньшего диаметра. При прессовке пружина сжимается, а после отведения штока – разжимается, выталкивая диском спрессованный продукт.
Для штока подойдет труба миллиметров 30 в диаметре. К ней приваривается пуансон, свободно входящий в матрицу. Другой конец штока крепится к гидравлическому механизму.
Перед загрузкой в матрицу древесную массу желательно хорошо перемешать. Барабан для перемешивания можно сделать из листовой стали или взять готовый от стиральной машины. Закрепляется барабан на стойках.
Подающий лоток, по которому сырье из барабана загружается в матрицу, тоже делается из стального листа.
На такой установке вряд ли удастся получить сверхплотные евродрова. Но с задачей сделать из рассыпающегося сырья твердый брикет она вполне справится. В итоге из отходов получится продукт, по плотности равный древесине, но спрессованный в удобную форму.
Процесс брикетирования — обзор
7.4 Брикетирование
Сельскохозяйственные отходы горят так быстро, что трудно поддерживать устойчивый огонь из-за сложности управления процессом горения. Кроме того, отходы не подходят по форме и структуре для традиционных угольных котлов и печей. В то время как переработанные древесные отходы нашли некоторое применение в качестве топлива, сжигая их непосредственно в модернизированных промышленных котлах, прямое сжигание сыпучих крупногабаритных сельскохозяйственных отходов неэффективно. Они имеют низкую энергетическую ценность на единицу объема и, следовательно, неэкономичны; они также вызывают проблемы при сборе, транспортировке, хранении и обращении.
Один из подходов, применяемых в некоторых частях мира для улучшенного и эффективного использования сельскохозяйственных остатков, — это их уплотнение в гранулы или брикеты твердого топлива. Это включает уменьшение размера за счет сжатия громоздкой массы. Простота хранения и транспортировки таких улучшенных брикетов твердого топлива (обычно в виде бревен) с высоким удельным весом делает их привлекательными для использования в домашних условиях и в промышленности. В отличие от сыпучей и объемной формы сгорание брикетов может быть более равномерным.Это могло бы сделать возможным сжигание брикетированных материалов непосредственно в качестве топлива в некоторой степени аналогично топливной древесине и углю в бытовых (возможно, модернизированных) печах и печах. Некоторые развивающиеся страны, например Индия, Таиланд и несколько мест в Африке имели опыт замены топливных брикетов на дрова и уголь, чтобы уменьшить проблемы нехватки дров и удаления сельскохозяйственных отходов (Bhattacharya et al., 1989).
Брикетирование улучшает рабочие характеристики горючего материала, увеличивает объемное значение и делает его доступным для множества применений — бытовых и промышленных.Материалы, которые можно брикетировать и использовать в качестве топлива в промышленности, не ограничиваются только сельскохозяйственными отходами. Существует комбинация различных форм материала, включая древесные отходы, опилки, отходы агропромышленного производства, пластик, резину и различные другие формы горючих материалов, которые можно прессовать с помощью мощных промышленных прессов.
Процесс брикетирования — это переработка сельскохозяйственных отходов в брикеты однородной формы, которые легко использовать, транспортировать и хранить. Идея брикетирования заключается в использовании материалов, которые непригодны для использования из-за недостаточной плотности, и их прессовании в твердое топливо удобной формы, которое можно сжигать, как дерево или древесный уголь.Брикеты обладают лучшими физическими характеристиками и характеристиками горения, чем исходные отходы. Брикеты улучшат эффективность сгорания при использовании существующих традиционных печей, в дополнение к уничтожению всех насекомых и болезней, а также уменьшению опасности разрушительного пожара в сельской местности. Таким образом, основные преимущества брикетирования заключаются в том, что они:
- •
Избавляются от насекомых
- •
Уменьшают объем отходов
- •
Производят эффективное твердое топливо с высокой теплотворной способностью
- •
Низкое потребление энергии для производства
- •
Защита окружающей среды
- •
Обеспечение рабочих мест
- •
Менее опасны.
Сырьем, подходящим для брикетирования, является рисовая солома, пшеничная солома, стебли хлопка, стебли кукурузы, отходы сахарного тростника (жмых), фруктовые ветви и т. Д. Однако в предлагаемом комплексе, который будет описан далее в этой главе, стебли хлопка и фрукты ветви лучше всего утилизировать путем брикетирования. Процесс брикетирования начинается со сбора отходов с последующим измельчением, сушкой и уплотнением с помощью экструдера или пресса.
Параметры качества брикетирования
Различные сельскохозяйственные отходы имеют разные структурные и химические свойства.Брикетирование сельскохозяйственных отходов в топливо предназначено для улучшения остаточной ценности, а также экологических критериев; сжигать их в поле не рекомендуется. Свойства остатка и процесса брикетирования определяют качества брикета — горючесть, долговечность, стабильность и т. Д. Среди параметров, с помощью которых измеряется качество брикета, входят прочность сцепления или сжатие, пористость, плотность, теплотворная способность и зольность.
Среди переменных параметров, исследованных разными авторами (El-Haggar et al., 2005) на различных остатках, которые растут в разных местах, при брикетировании используются приложенное давление, влажность материала, размер частиц и температура.
Приложенное давление влияет на плотность брикета; чем выше плотность, тем выше теплотворная способность в кДж / кг. Предполагается, что высокое давление сопровождается некоторым внутренним повышением температуры. Ndiema et al. (2002) заявил, что когда температура брикетируемого материала повышается (предварительный нагрев) выше естественного состояния, для уплотнения потребуется низкое давление.
Однако увеличение плотности снижает легкость воспламенения (т. Е. Предварительного сгорания) твердого топлива; увеличение плотности снижает пористость. Размер частиц материала может влиять на полученную плотность брикета и прочность на сжатие. По природе растительные остатки, подходящие для брикетов, подразделяются на мелкие, грубые и стеблевые (Tripathi et al., 1998).
Уровень влажности материала при сжатии является важным параметром обработки.О значении влажности для уплотнения биомассы сообщали многочисленные исследователи (Faborode and O’Callahan, 1987; Hill and Pulkinen, 1988). Избыточная влажность или недостаточная сушка остатков снижает энергоемкость брикета. Исследования показали, что брикетирование сельскохозяйственных остатков с определенным содержанием влаги может улучшить стабильность, долговечность и прочность брикета. С другой стороны, избыток влаги может затруднить переработку брикетов, привести к получению брикетов плохого качества и увеличить потребность в энергии для измельчения или сушки материала.
Еще одним важным фактором, определяющим качество, является наличие или отсутствие связующего материала. Брикетирование осуществляется либо на связующем, либо без связующего. Связующий агент необходим для предотвращения «отскока» сжатого материала и, в конечном итоге, его возвращения к своей первоначальной форме. При брикетировании без связующего давление и температура вытесняют природный деревянистый материал (связующее), присутствующий в материале, который способствует склеиванию.
Когда в остатке не хватает природного лигнина, который способствует склеиванию (или процент лигнина низкий), необходимо введение связующего для улучшения качества брикета.Однако необходимо сделать соответствующий выбор и количество связующего, чтобы предотвратить дым или выброс летучих веществ, которые отрицательно влияют на людей и окружающую среду. Также материал, в котором отсутствует естественное связующее, можно смешивать с имеющимся. Материалы с натуральным связующим включают, среди прочего, стебли хлопка, опилки, стебли кукурузы. Некоторые искусственные связующие включают деготь, крахмал, патоку или дешевые органические материалы.
В заключение, качество брикета можно определить по следующим параметрам:
- •
Устойчивость и долговечность при обращении, транспортировке и хранении; их можно измерить по изменению веса, размеров и, в конечном итоге, плотности и прочности брикетов в расслабленном состоянии.
- •
Горение (энергетическая ценность) или легкость горения и зольность.
- •
Забота об окружающей среде, т. Е. Токсичные выбросы при горении.
Параметры, определяющие качество брикета:
- •
Давление и / или температура, применяемые во время уплотнения.
- •
Тип материала:
- —
Структура (т.е.грамм. размер, волокнистый, неволокнистый и т. д.)
- —
Химический (например, содержание лигнина-целлюлозы)
- —
Физический (например, размер частиц материала, плотность и содержание влаги)
- —
Чистота (например, следы элемента (сера) и т. Д.).
Параметры, определяющие стабильность и долговечность:
- •
Прочность на сжатие, ударная вязкость.
- •
Время сжатия.
- •
Релаксация: влажность, длина, плотность (параметр после брикетирования). Процесс брикетирования
Помимо свойств, присущих сырью (сельскохозяйственные отходы), процесс брикетирования также может влиять на качество брикетов (Ndiema et al. , 2002). Брикеты из разных материалов или процессов различаются по способам обращения и горению; брикеты из одного и того же материала в разных условиях могут иметь разные качества или характеристики.Кроме того, исходный материал, условия хранения, геометрия брикета, его масса и режим сжатия — все это влияет на стабильность и долговечность брикетов (Ndiema et al., 2002).
Брикеты с низкой прочностью на сжатие могут не выдерживать нагрузки при обращении, например погрузка и разгрузка при пересылке или транспортировке. Стабильность и долговечность брикетов также зависят от условий хранения. Хранение брикетов в условиях высокой влажности может привести к тому, что брикеты будут впитывать влагу, распадаться и впоследствии рассыпаться.Этот распад иногда называют характеристикой релаксации. Процесс брикетирования может быть причиной релаксации брикета. Высыхание может сопровождаться усадкой; также возможно расширение (увеличение длины или ширины брикета).
Процесс брикетирования в первую очередь включает сушку, измельчение, просеивание, прессование и охлаждение. Компоненты типовой установки для брикетирования: (1) оборудование для предварительной обработки; (2) погрузочно-разгрузочное оборудование; и (3) брикетировочный пресс.Оборудование предварительной обработки включает резак / клипсатор и сушильное оборудование (сушилка, генератор горячего воздуха, вентиляторы, циклонный сепаратор и сушильный агрегат). Среди погрузочно-разгрузочного оборудования винтовые конвейеры, пневматические конвейеры и приемные бункеры.
При брикетировании сельскохозяйственных остатков (или смеси остатков) для топливных целей необходимо стремиться к оптимальному сочетанию параметров, которое соответствует желаемому качеству брикета для конкретного применения (бытовое или промышленное топливо). Необходимо приложить усилия для определения набора или диапазона параметров (влажность, размер частиц и приложенное давление или / и температура), которые могут обеспечить оптимальное или желаемое качество брикета (сгорание, долговечность и стабильность, уровень дыма / выбросов). .
Технология брикетирования
Исследования по производству брикетов охватывают наличие сельскохозяйственных отходов (лузга, стебли, трава, стручки, волокна и т. Д.) И агропромышленных отходов, а также осуществимость технологии и процессов их переработки в брикеты в коммерческих целях. количество. Для сжатия биомассы или сельскохозяйственных отходов используются поршневые, шнековые экструдеры, грануляторы и гидравлические прессы.
В ходе многочисленных исследований изучались оптимальные свойства и условия обработки при переработке сельскохозяйственных остатков (по отдельности или в сочетании с другими материалами), со связующими веществами или без них, в качественные топливные брикеты.Желаемые качества брикетов в качестве топлива включают хорошее сгорание, стабильность и долговечность при хранении и обращении (включая транспортировку), а также безопасность для окружающей среды при сгорании. Меры этих свойств включают энергетическую ценность, влажность, зольность, плотность или ослабленную плотность, прочность, легкость воспламенения, дымность и выбросы.
В поршневых прессах давление создается за счет воздействия поршня на материал, упакованный в цилиндр, напротив матрицы. Они могут иметь механическую муфту и маховик или использовать гидравлическое воздействие на поршень.Гидравлический пресс обычно сжимается до более низкого давления.
В шнековом экструдере давление прикладывают непрерывно, пропуская материал через цилиндрический шнек с внешним нагревом фильеры и конических шнеков или без него. Тепло помогает уменьшить трение, а внешняя поверхность брикета каким-то образом карбонизируется с отверстием в центре. Как в поршневой, так и в винтовой технологии приложение высокого давления увеличивает температуру биомассы, а лигнин, присутствующий в биомассе, псевдоожижается и действует как связующее (Tripathi et al., 1998).
В прессах для гранул ролики движутся по перфорированной поверхности, и материал проталкивается в отверстие каждый раз, когда ролик проходит. Плашки изготавливаются либо из колец, либо из дисков. Возможны и другие конфигурации. Обычно прессы подразделяются на прессы низкого давления (до 5 МПа), промежуточного давления (5–100 МПа) и высокого давления (более 100 МПа).
Al Widyan et al. (2002) исследовал параметры преобразования оливкового жмыха (влажность 12%) в стабильные и прочные брикеты; Оливковый пирог является обильным побочным продуктом экстракции оливкового масла в Иордании.Считалось, что на долговечность и стабильность влияют давление брикетирования и содержание влаги в материале.
Кек различной влажности уплотняли в цилиндрическую форму диаметром 25 мм с помощью гидравлического пресса при различных давлениях (15–45 МПа) и времени выдержки (5–20 секунд). Посредством плана эксперимента (DOE) и дисперсионного анализа (ANOVA) были проверены значимость приложенного давления, содержания влаги и времени выдержки. Стабильность брикета выражали в показателях ослабленной плотности (отношение массы к объему) брикета после того, как прошло достаточно времени (около 5 недель) для стабилизации их размеров (диаметра и длины).Для испытания на относительную долговечность каждый брикет падал четыре раза с высоты 1,85 метра на стальную пластину. Прочность принималась как отношение конечной массы, оставшейся после последовательного помета. Метод отмечен как нетрадиционный; расслабленная плотность была принята как лучший количественный показатель стабильности.
Ndiema et al. (2002) провел экспериментальное исследование давления брикетирования на релаксационные характеристики рисовой соломы с использованием уплотняющего плунжера при различных давлениях от 20 до 120 МПа.Характеристики релаксации были взяты как процентное удлинение и доля пустотного объема образца в момент времени t после выброса брикета из фильеры. В лабораторных условиях относительная влажность составляла от 50 до 60%. Время t было зафиксировано на 10 секундах и 24 часах после выброса из штампа. Было отмечено, что как расширение, так и объем пустот уменьшаются с увеличением давления в фильере до тех пор, пока не будет достигнуто давление примерно 80 МПа. При сжатии свыше 80 МПа значительного изменения релаксации брикета не наблюдалось.Исследование пришло к выводу, что для данного размера фильеры и условий хранения часто существует максимальное давление в фильере, при превышении которого не может быть достигнуто никакого существенного увеличения когезии брикета.
(PDF) Анализ технологии производства древесных брикетов, включая затраты и распределение
Филип Ясичек, Дариуш Квасьневски
также имеют свои недостатки, такие как большой разброс в диапазоне влажности (30-60% влажность —
биомассы до переработки в брикеты) и физических свойств, а также ограниченный доступ
к сырью, сезонность и многое другое (Frączek et al., 2011, Niedziółka et
al., 2014). Развитие использования биомассы влечет за собой необходимость увеличения ее ресурсов. Несмотря на
постоянное перепроизводство углекислого газа, а также выбросы пыли в атмосферу и ненадлежащее хранение отходов на полигонах, Vaverkowa et al. (Vaverkowa et al., 2018)
видят потенциал в восстановлении закрытых свалок. Это может компенсировать сбои в системе eco-
, минимизировать негативное воздействие на окружающую среду и обеспечить безопасность при дальнейшем использовании.Affor-
Пустоши могут стать источником энергии биомассы в будущем.
растений, которые могут использоваться для производства твердого биотоплива, включают энергетическую иву, мискантус, мальву Пенсильвании и т. Д.
(Dubas et al., 2004, Wróbel and Mudryk, 2010).
Наиболее распространенной формой биомассы, перерабатываемой в Польше, является компактное биотопливо, т. Е. Бри-
кетты и гранулы. Это топливо, созданное из сухого измельченного растительного материала под высоким давлением,
, чаще всего без добавления искусственных связующих (Kowalik, 2002, Gostomczyk, 2012).Производство брикетов
включает подвергание материала трем последовательным процессам: сушке, измельчению и прессованию (Kuś and Matyka, 2008). Сырье для их производства:
, полученное в деревообрабатывающей промышленности (все виды опилок, щепа, щепа, кора),
из сельскохозяйственного производства (отходы и производственные остатки, например, солома зерновых) и с
плантаций быстрорастущие растения. В Польше на энергетических плантациях выращиваются энергетическая ива, тополь, черная акация, ванианская мальва Pennsyl-
и мискантус (Frączek et al.2010b).
Эти установки перерабатываются в гранулы или брикеты, и основное различие между ними
заключается в форме и размере, выбранных для целей производства биотоплива. Брикеты могут иметь цилиндрическую форму
или кубовидную, с четырьмя, шестью или восемью блоками, иногда с отверстием в центре.
Их размеры зависят от типа брикетирующего устройства; длина брикета
получаетсяпутем регулировки размеров камеры прессования. Твердое цилиндрическое биотопливо обычно имеет диаметр 60-
80 мм и длину 40-200 мм.Чаще всего используется в каминах индивидуальных потребителей
. Прямоугольные брикеты с квадратным поперечным сечением обычно имеют длину 200-320 мм
и высоту борта 70-100 мм. Их разновидность — брикеты с отверстиями в середине
dle, произведенные на шнековых брикетировочных машинах типа Pini-Kay, характеризующиеся высокой степенью сжатия
. Влажность такого топлива составляет ок. 4% и процесс их сгорания
происходит медленнее, чем у других видов твердого биотоплива (Frączek, 2010a).
Теплотворная способность брикетов зависит от используемого сырья и колеблется от 16 до
18,5 МДж · кг-1 (Kachel-Jakubowska et al., 2014, Niedziółka et al., 2007).
Подробные стандарты оценки качества твердого биотоплива (с низкой и высокой степенью переработки)
можно найти в PN-EN 14961-1: 2010 (Твердое биотопливо — Характеристики топлива и классов — Часть
1: Общие требования) заменены согласно ISO 17225 и PN-EN 14961-22,3,4,5: 2011. Эти документы
включают подробные описания параметров качества отдельных форм биотоплива (брикеты, пеллеты, древесная щепа, древесные отходы, дрова, небольшие тюки соломы, твердая древесина
, семена, косточки, скорлупа и волокнистые материалы) осадок).Описания, входящие в стандарты
, разделены на информационную и нормативную группы. В Польше самый распространенный брикет
— куб 25/30/15 мм.
В других регионах мира брикеты также производятся из рисовой шелухи и кукурузного крахмала
(Муазу и Стегеманн, 2015). Другим примером может быть производство брикетов из
листьев Cerbera Manghas (морского манго) (Sutrisno et al., 2017, Dinesha et al., 2018).
Разработка, свойства и потенциальные области применения высокоэнергетических топливных брикетов, включающих угольную пыль, биологические отходы и пластмассовые изделия после потребления
Разработка и производство брикетов
Разработка топливных брикетов из нетрадиционных исходных материалов может быть обременительной и трудоемкой из-за на необходимость разработки и оценки большого количества образцов брикетов с различным соотношением отходов в смеси (т.е., всего в данном случае 81). Чтобы преодолеть этот недостаток, был разработан последовательный протокол для быстрого определения соответствующих соотношений угольной пыли, биоотходов и пластиковых отходов в смеси отходов, что дает брикеты с высокими энергетическими ценностями и адекватными характеристиками обращения. В этом протоколе брикеты, не удовлетворяющие заданному критерию на каждом этапе, не учитывались на последующих этапах. Этот общий протокол считался идеальным для развивающихся регионов, таких как SSA, поскольку он позволяет быстро создавать прототипы и экономит ресурсы, время и усилия.
Использование имеющихся в свободном доступе отходов и ручного пресса местного производства было мотивировано необходимостью продемонстрировать возможность разработки высокоэнергетических топливных брикетов с использованием местных ресурсов. Ручной пресс, используемый в данном исследовании, может быть изготовлен из металлолома, а его ориентировочная стоимость составляет около 50 долларов США. Ручные ручные прессы, подобные тому, который использовался в этом исследовании, достигают давления сжатия приблизительно 0,05–4 Н / мм 2 [1, 34] по сравнению с 15 Н / мм 2 для автоматизированных систем прессования [8].Использование ручного пресса было мотивировано тем фактом, что некоторые из целевых конечных пользователей технологии в SSA (например, домашние хозяйства, кооперативы, малые предприятия) часто не имеют доступа к электричеству, которое часто является дорогостоящим и ненадежным. В этом отличие от автоматизированных систем прессования, которые относительно дороже, требуют электричества и более сложны в проектировании и изготовлении; таким образом, они недоступны в SSA.
Прочностные характеристики брикетов
Индекс разрушения показывает процент топлива, оставшегося на сите с заданным отверстием (т.е.е., 2,36 мм в данном случае) после испытания брикетов на падение. Показатели разрушения всех брикетов были высокими и превышали рекомендуемые 90% (рис. 3), что свидетельствует о том, что брикеты сохранили свою форму [9, 10]. Значения индекса разрушения, наблюдаемые в настоящем исследовании, аналогичны значениям, указанным для брикетов, изготовленных из биомассы [4, 30] и угольной мелочи [33]. Значения индекса раздробленности соответствовали высокой плотности, наблюдаемой для брикетов (рис. 4). Наблюдаемые высокие значения плотности (1.1–1,3 г / см 3 ) были более чем в три раза выше, чем те, о которых сообщали Любвама и Йига [30] для брикетов биомассы, изготовленных из скорлупы арахиса (0,259 г / м 3 ) и жмыха (0,183 г / м ). 3 ). Высокие значения плотности показывают, что смеси отходов, связующее мелассы и условия прессования, применявшиеся в текущем исследовании, эффективно уплотняли смеси отходов. Высокие значения плотности указывают на то, что брикеты обладают высокой устойчивостью к механическим повреждениям [4].
Несмотря на высокую плотность, значения прочности на сжатие брикетов были умеренными и ниже 1.0 МПа часто рекомендуется для качественных топливных брикетов (рис. 5). Прочность на сжатие указывает на устойчивость брикетов к разрушению при воздействии сжимающих усилий. Прочность на сжатие ниже стандартных значений для высококачественных брикетов, но достаточна для того, чтобы брикеты оставались неповрежденными даже при воздействии умеренных сжимающих усилий во время транспортировки и хранения. Причина относительно низкой прочности на сжатие неясна. Можно было бы ожидать, что включение пластмасс может снизить прочность на сжатие, учитывая пластичность таких материалов и предполагаемый плохой контакт частиц с частицами, вызванный пластиковыми хлопьями.Однако сравнение прочности на сжатие брикета без пластика (т.е. 0,34 МПа для C80 – P0 – S20) с прочностью на сжатие брикета с 20–40% пластика (например, 0,71 МПа для C50 – P40 – S10) не подтверждает это мнение. (Рис. 5). Следовательно, прочность на сжатие может отражать сложные взаимодействия между свойствами и пропорциями исходных материалов, взаимодействия частицы-частицы, механизмы связывания и процесс сжатия. Механизмы, объясняющие развитие прочности во время брикетирования, очень сложны и включают (1) усиление взаимодействий между частицами, таких как блокирование частиц, и (2) образование мостиковых связей между твердыми частицами и патокой [4, 30, 48 ].В целом результаты показывают, что брикеты обладают достаточной прочностью, чтобы их можно было обрабатывать, упаковывать, хранить и транспортировать без значительных повреждений.
Водопоглощение
Три брикета (C50 – P40 – S10, C70 – P20 – S10 и C80 – P20 – S0) из пяти имели приемлемые значения водопоглощения (рис. 6а). Водопоглощение указывает на способность брикетов противостоять воде или высокой влажности, включая набухание во время транспортировки и хранения [4]. Два брикета (C80 – P0 – S20 и C60 – P30 – S10) имели водопоглощение более 30%; таким образом, они могут испортиться, включая разбухание и деформацию, под воздействием воды или высокой влажности во время транспортировки и хранения.Однако в некоторых исследованиях приемлемыми считаются брикеты со значениями водопоглощения менее 50% в минуту [16]. Значительная обратная линейная зависимость наблюдалась между водопоглощением и прочностью на сжатие (рис. 6b). Это соотношение предполагает, что водопоглощающая способность брикетов может быть уменьшена за счет увеличения прочности на сжатие за счет увеличения силы сжатия или времени прессования.
При брикетировании высокое водопоглощение часто связано с присущими им связующими, такими как лигнин, в лигноцеллюлозных биомассах и применяемыми снаружи водорастворимыми органическими связующими, такими как меласса [4].Поэтому два брикета (например, C80 – P0 – S20 и C60 – P30 – S10) с высокой водопоглощающей способностью следует хранить в сухих условиях под навесом или навесом, чтобы избежать порчи. Помимо ухудшения качества во время хранения, высокое водопоглощение влияет на характеристики горения и теплотворную способность брикетов, особенно во время газификации. Например, водяной пар в процессах газификации создает условия насыщения при высоких температурах, что может вызвать быстрое разрушение брикетов [4].В свою очередь, это может снизить общую эффективность системы за счет двух механизмов: (1) потерянные материалы могут выходить из реактора или котла в несгоревшем виде, и (2) материалы могут блокировать поток воздуха в реактор и мешать газификации. процесс.
Энергетическая ценность брикетов
Энергетическая ценность всех трех брикетов была значительно выше, чем у обычных твердых видов топлива, таких как дрова, древесный уголь и уголь, или схожа с ними (рис. 7; таблица 3). Значения энергии также были выше, чем те, которые описаны в литературе для биохаров [47].Биохар образуются в результате пиролиза биомассы, процесса, почти аналогичного тому, который используется для производства древесного угля. В таблице 3 представлено сравнение значений энергии брикетов, разработанных в текущем исследовании, с обычным твердым топливом и другими брикетами, о которых сообщается в литературе. Таким образом, показатели энергии нынешних брикетов были выше, чем у брикетов, о которых сообщалось в литературе. Древесина, включая опилки, имеет относительно низкую энергетическую ценность (16,8–19 МДж / кг) по сравнению с угольной пылью и отходами пластмасс [42].Таким образом, высокая энергетическая ценность нынешних брикетов может быть связана с высокой энергетической ценностью угля и пластиковых отходов. Угольная пыль, используемая в настоящем исследовании, была получена из высококачественного угля в Зимбабве с энергетической ценностью от 25 до 35 МДж / кг [31, 33]. Кроме того, сообщалось, что пластмассы обладают высокими значениями энергии примерно 43,3–46,5 МДж / кг, хотя фактические значения могут варьироваться в зависимости от типа пластика [49]. Высокие энергетические показатели делают брикеты идеальными для различных применений.В целом полученные данные подтверждают исходную гипотезу о том, что высокоэнергетические топливные брикеты с приемлемой прочностью, водопоглощением и энергетическими свойствами могут быть разработаны с использованием соответствующих смесей трех энергоемких исходных отходов.
Таблица 3 Сводка энергетических значений брикетов, разработанных в текущем исследовании, по сравнению с литературнымиОриентировочный анализ энергетического баланса
Чистая энергия, полученная при брикетировании смесей отходов, на порядок превышала энергию, используемую в производственном процессе, что привело к положительному общему энергетическому балансу (Таблица 2).Отношения использованной энергии к полученной энергии в текущем исследовании (7,0–9,0%) были в два раза ниже, чем значения, указанные для брикетов из биомассы (12,13–17,64%) [42]. Положительный энергетический баланс был связан с высокими значениями энергии брикетов, разработанных в текущем исследовании (Таблица 3), которые были примерно в два раза выше, чем у брикетов из биомассы [37, 42]. Обратите внимание, что предполагаемая энергия, необходимая для сушки угольной золы и опилок (2,25 МДж / кг), была основана на данных для влажной биомассы с целевым снижением содержания влаги примерно от 60 до 15% [19, 42].Следовательно, фактические значения энергии для сушки как угольной пыли, так и опилок, как ожидается, будут ниже, чем для влажной биомассы. Поэтому в действительности вполне вероятно, что энергия, необходимая для сушки, и, следовательно, общая энергия для производства брикетов, может быть ниже, чем значения, указанные здесь. Кроме того, одно исследование даже показывает, что энергия, необходимая для сжатия и экструзии брикетов с использованием гидравлической системы, может составлять всего 12–30 МДж / т, что эквивалентно 0,12–0.30 МДж / кг [32]. Таким образом, при использовании таких гидравлических систем существует возможность уменьшить общую используемую энергию и, следовательно, увеличить отношение полученной энергии к используемой энергии. Таким образом, с точки зрения энергетики эти показательные положительные энергетические балансы указывают на возможность брикетирования угольной пыли, пластмасс и биоотходов в высокоэнергетическое твердое топливо для потенциальных применений в системах преобразования отходов в энергию.
Возможное применение брикетов в странах Африки к югу от Сахары
Таким образом, преимущества нынешних брикетов включают (1) высокую энергетическую ценность, сравнимую или даже превышающую обычные невозобновляемые твердые виды топлива, такие как уголь, древесный уголь и дрова (Таблица 3) и (2) предполагаемые лучшие эксплуатационные свойства, чем у исходных гранулированных материалов (т.е.е., опилки, угольная пыль, постпотребительские пластмассы). Кроме того, брикетирование твердых отходов является потенциальным твердым топливом, одновременно снижая риски для здоровья, связанные с нынешней практикой удаления таких твердых отходов.
В странах Африки к югу от Сахары (АЮС) большая часть населения не имеет доступа к электросетевой системе; таким образом, они полагаются на топливо из биомассы, что способствует обезлесению [37]. В этом отношении высокая энергетическая ценность брикетов в сочетании с адекватными эксплуатационными характеристиками делает их идеальной альтернативой традиционным видам топлива из биомассы, таким как дрова и древесный уголь.Эти высокоэнергетические брикеты могут использоваться для отопления и приготовления пищи в домашних условиях либо сами по себе, либо как неотъемлемая часть энергетического баланса, включая обычное топливо из биомассы. На бытовом уровне брикеты можно было бы использовать в традиционных «трехкаменных» кухонных плитах, обычно используемых в SSA, и даже в плитах с пиролитической или биочаровой [22, 25]. Кухонные плиты с пиролитическим / биочарным покрытием более энергоэффективны и выделяют меньше токсичных выбросов, чем традиционные трехкаменные кухонные плиты [22, 25]. Брикеты также могут использоваться для обеспечения энергией для отопления и приготовления пищи в сельских школах и клиниках, которые часто зависят от топлива из биомассы для отопления и приготовления пищи.
Энергетические брикеты также могут использоваться в промышленных системах отопления. В СЮА высокий спрос на топливо для сушки и обработки сельскохозяйственных культур, таких как чай, кофе и табак, был связан с безудержной вырубкой лесов в таких странах, как Зимбабве. Кроме того, промышленное производство обожженных земляных кирпичей и цемента, а также металлургические процессы, такие как плавка, являются энергоемкими процессами, требующими большого количества дров, угля или электроэнергии. Таким образом, брикеты также могут использоваться для зажигания промышленных котлов, обжиговых печей, печей, плавильных печей и помещений для сушки табака, где уголь и дрова в настоящее время являются преобладающими источниками энергии.Примеры таких промышленных применений включают производство стали, гончарные / керамические печи и заводы по производству цемента [50]. На электростанциях, работающих на отходах, брикеты также могут использоваться в качестве альтернативы углю и биомассе для сжигания или совместного сжигания на тепловых электростанциях. Водно-энергетические системы, использующие брикеты в качестве источника энергии, вероятно, будут иметь меньшее воздействие на окружающую среду, чем тепловые электростанции, использующие традиционные виды топлива, такие как уголь и биомасса. Это связано с тем, что в брикетах в качестве исходных материалов используются промышленные отходы, а не чистое сырье, такое как уголь и биомасса.
Преобразование энергоемких промышленных отходов в топливные брикеты для бытового, институционального и промышленного применения потенциально привлекательно в SSA по разным причинам. Эти причины могут также определять первоначальное внедрение и последующее внедрение и даже устойчивость технологии брикетирования. Итак, причины следующие:
- 1.
Помимо высокой энергии, брикеты обладают рядом других потенциальных преимуществ, включая простоту производственного процесса с использованием недорогого ручного пресса, что делает их идеальной технологией преобразования отходов в энергию для таких развивающихся регионов, как SSA.
- 2.
Острая нехватка энергии, сокращающиеся источники дров и отсутствие доступа к высокоцентрализованным электросетям создают идеальные условия для альтернативных источников топлива, таких как брикеты. Это особенно верно в отношении неформальных поселений в трущобах, городских и пригородных районах АЮС.
- 3.
Отходы сырья для брикетирования легко и свободно доступны в SSA. Например, в нескольких странах АЮС (например, в Зимбабве, Южной Африке, Мозамбике и др.) Имеются большие запасы угля и операции по добыче угля, которые производят огромное количество угольной пыли, которая в настоящее время простаивает на складах. Как отмечают Gwenzi et al., [23] и Duku et al. [18] в случае Зимбабве и Ганы, соответственно, указано, что ежегодно образуются большие количества твердых бытовых отходов, в том числе бытовых пластмасс.Более того, большинство стран АЮС имеют экономику, основанную на сельском хозяйстве, при которой в результате переработки сельскохозяйственной продукции образуются большие количества биоотходов. Эти отходы в настоящее время вывозятся на свалки или сжигаются, что создает риски для здоровья человека и окружающей среды. Таким образом, технология брикетирования представляет собой потенциально беспроигрышное решение для решения проблем, связанных с отходами и энергией в SSA.
- 4.
Потенциал для создания малых предприятий и рабочих мест на основе производственно-сбытовых цепочек брикетов, особенно среди молодежи в городских и пригородных районах, по данным Кении [37].Это особенно важно в странах АЮС, учитывая высокий уровень безработицы, обусловленный быстрым ростом населения, низким уровнем индустриализации и экономического развития.
Дальнейшие исследования
Текущее исследование ограничивалось разработкой и производством брикетов и последующей оценкой на основе одномерной статистики. Понятно, что прежде чем полностью реализовать потенциал технологии брикетирования, необходимо восполнить ряд пробелов в знаниях.Эти пробелы в знаниях включают:
- 1.
Необходимость детального физико-химического анализа, включая химический состав и свойства золы,
- 2.
Текущее исследование опиралось на одномерную статистику (например, односторонний дисперсионный анализ) для определения соотношений отходов в смеси, которые дают брикеты с наилучшим сочетанием энергетических свойств и характеристик обработки.Следовательно, требуется систематическая оптимизация производственного процесса с использованием известных инструментов оптимизации при разработке продукта, таких как методология поверхности отклика [27]. Такие будущие исследования должны изучить влияние различных производственных условий, включая соотношение отходов в смеси, время прессования и давление, соотношение твердого вещества и адгезива и их комбинацию.
- 3.
Исследование использования нагретого пластика в качестве связующего, процесса, который потребует строгого автоматического контроля температуры, чтобы пластик мог образовывать жидкую фазу без образования летучих веществ.Такая технология горячего брикетирования может позволить разработать непрерывный процесс производства брикетов в промышленных масштабах.
- 4.
Требуются сравнительные исследования для оценки рабочих характеристик, включая характеристики горения и энергоэффективность высокоэнергетических брикетов по сравнению с обычным твердым топливом в различных потенциальных областях применения, указанных в текущем исследовании.
- 5.
Разработка бизнес-модели, включая анализ рынка и подробный анализ рентабельности брикетов по сравнению с существующими конкурирующими твердыми видами топлива, такими как уголь, древесный уголь и дрова.
- 6.
Подробная оценка жизненного цикла брикетов на окружающую среду, включая парниковые газы и токсичные выбросы, по сравнению с обычным твердым топливом.
- 7.
Комплексная оценка технической, финансовой и социально-экономической осуществимости для определения устойчивости технологии при различных сценариях.
Технология совместного брикетирования угольных отходов и опилок
Буравчук Н.И. и Гурьянова О.В., Композиты из мелкозернистого углеродсодержащего сырья . Ростов-на-Дону: ЮФУ, 2017.
. Google Scholar
Буравчук Н.И. и Гурьянова О.В., Solid Fuel Chem. , 2016, т. 50, нет. 6, стр. 355.
Статья CAS Google Scholar
Елишевич А.Т., Брикетирование угля со связующими , М .: Недра, 1972.
Google Scholar
Тайц Е.М., Андреева И.А., Методы анализа и испытания углей, , М .: Недра, 1983.
Google Scholar
Елишевич А.Т., Рыбаченко В.И., Перекрестов Б.И. и др., Хим. Тверь. Топл. (Москва) , 1974, вып. 4, стр. 94.
Google Scholar
Елишевич А.Т., Хим. Тверь. Топл. (Москва) , 1978, вып. 6, стр. 60.
Google Scholar
Колбановская, А.С., Докл. Акад. АН СССР, , 1962, т. 143, нет. 5, стр. 1159.
CAS Google Scholar
Суринова С.И., Полушкин А.Н., Хим. Тверь. Топл. (Москва) , 1987, вып. 4, стр. 123.
Google Scholar
Воробьев В.Н., Лещенко П.С., Климов Л.К. и др., Хим. Тверь. Топл. (Москва) , 1997, вып. 2, стр. 81.
Google Scholar
Петрова Г.И., Москаленко Т.В., Леонов А.М. и др., Горн. Информ.-Анал. Бюлл., 2010, № 7, стр. 366.
Google Scholar
Макаров А.С., Янко С.В., Дегтяренко Т.Д. и др., Хим. Тверь. Топл. (Москва) , 1993, вып. 3, стр. 41.
Google Scholar
Парфит Г. и Рочестер К., Адсорбция из раствора на границе раздела твердое / жидкое вещество , Лондон: Academic Press, 1983.
Google Scholar
Изучение возможностей и будущего технологии производства брикетов из биомассы для устойчивой энергетики
* Автор для переписки: Айшвария С., Отдел текстиля и одежды, Авинашилингамский институт домашнего образования и высшего образования для женщин, Тамилнад, Индия, тел .: +91 87549, электронная почта: [электронная почта защищена]Дата поступления: 27.11.2018 г. / Дата принятия: 11 декабря 2018 г. / Дата публикации: 17 декабря 2018 г.
Ключевые слова: Биомасса; Брикет; Органические отходы; Управление отходами; Переработка; Брикетирование
Введение
Увеличение количества твердых отходов является серьезной угрозой в современном мире.Это вызывает большую озабоченность в наименее развивающихся странах (НРС) из-за проблем со здоровьем и окружающей средой, связанных с удалением отходов. Наблюдая за 52% органических отходов и 26% вторсырья, которые могут быть переработаны, это игнорирование рециркуляции отходов и неэффективность существующей системы управления отходами является центральной темой данной статьи [1]. В текущем сценарии постоянно растущих цен на топливо мы видим, что дрова и сжиженный нефтяной газ становятся слишком дорогими, а в случае бывшего материала они являются загрязняющими веществами.Мы не можем позволить себе принимать больше рисков из-за уже вызывающих тревогу изменений парниковых газов и озона [2]. Чрезмерная эксплуатация природных ресурсов является результатом увеличения численности населения, что подразумевает рост спроса на новые источники энергии. Многократный рост цен на топливо — еще одна важная движущая сила, которая вызывает потребность в изучении инновационных источников энергии.
Биомасса
Биомасса — это природный материал, который может использоваться в качестве источника топлива. Такие органические отходы могут быть разложены микроорганизмами (биохимическими) или термически уплотненными (термохимическими) для преобразования в форму энергии.Последний выбирают при брикетировании биомассы. Преимущества использования биомассы включают использование рыхлой биомассы и тем самым предотвращение загрязнения воздуха. Такая биомасса будет содержать больше кислорода и меньше углерода, что является хорошим свойством для брикетов [3]. Этот процесс помогает увеличить плотность и долговечность брикета, так как давление составляет 1000 кг / м3. Кроме того, важным фактором является то, что различные отрасли промышленности по всему миру используют уголь для тепловой энергии / отопления, что выделяет парниковые газы, которые будут причиной климатических изменений.Такое брикетирование биомассы будет хорошим источником дохода для сельского населения в дополнение к обеспечению экологически чистой энергии и устойчивости.
Природа биомассы
Отходы природы, такие как листья, древесина, древесные отходы, отходы сельскохозяйственных культур, отходы животноводства и водные отходы, могут быть использованы в качестве брикетов из биомассы ( Рисунок 1 ). Обычно они доступны бесплатно или по низкой цене. В такой стране, как Индия, с широким разнообразием флоры и фауны, неограниченный источник природных ресурсов открывает возможности для переработки органических отходов в источник энергии.Обычно природные материалы состоят из целлюлозы, гемицеллюлозы, лигнина и золы [4].
Как правило, биомассу нельзя использовать напрямую, так как она пушистая, неровная по форме и имеет низкую плотность. После уборки урожая фермеры считают их огромными проблемами, учитывая время, необходимое для разложения, сжигания или захоронения на свалке, и пространство, которое требуется при хранении отходов [5]. Выбор сырья огромен и разнообразен. Он включает опилки, шлифовальную пыль, второстепенные куски дерева, кору и ветки деревьев, сосновые иглы, дикую траву, кофейную шелуху, отходы подсолнечника, рисовую шелуху, скорлупу арахиса, скорлупу миндаля, стебли хлопка, жом сахарного тростника, листья, мусор и т. бесконечные возможности от природы.Прочая бамбуковая пыль, горчичная шелуха / стебли, сосновые иглы, отходы сахарных заводов, отходы джута, кокосовая сердцевина и другие отходы и остатки, такие как клещевина, стебли красного грамма, табачный стебель, отходы чая, пыль шлифовальной машины, кора деревьев, дикие травы и кустарники .
Брикетирование
Брикет из биомассы используется в бедных развивающихся странах в качестве альтернативы топливу для приготовления пищи. Из-за технических ограничений и отсутствия знаний технология брикетирования не пользуется большой популярностью в различных частях мира. Проблемы с производством и различное качество сырья являются важными факторами, снижающими популярность технологии брикетирования.Это метод, который включает в себя прессование мелких частиц органических отходов связующим в течение определенного периода времени, в результате чего получают гранулы или брикетный блок (, рис. 2, ).
Преимущества брикетирования
Брикеты имеют более высокую тепловую ценность, низкую зольность и равномерную скорость сгорания, а также дешевле угля. Низкая влажность и высокая плотность брикетов обеспечивают лучшую эффективность котла. Некогда использованные нефть, уголь, бурый уголь невозможно заменить, но брикеты из биомассы можно переработать в компост.Отсутствие в брикетах серы, золы-уноса делает их экологически чистыми [6]. Дополнительным достоинством является конструкция идеального размера для полного сгорания. Брикеты обладают слабым дымом, без запаха и устойчивым пламенем. Есть добрая воля носить экологическую этикетку, потому что сокращение количества загрязняющих до сих пор отходов является важным фактором для маркетинга и его популярности.
С другой стороны, брикеты могут быть альтернативой дизельному топливу, керосину, мазуту, бурому углю, углю и дровам [7]. Во всех отраслях промышленности и в быту, использующих топливо и энергию, средства использования альтернативного топлива, такого как брикет из биомассы, могут быть очень обнадеживающими для мирового сектора возобновляемой энергетики.Готовый рынок, высокая прибыль, хороший потенциал роста, широкий выбор сырья, легкодоступность сырья делают брикетирование легким выбором. Простота хранения и транспортировки, заменитель угля — основная причина рассматривать брикеты из биомассы в качестве альтернативы энергии.
Процесс брикетирования
Ожидается, что влажность сырья будет менее 12%. Чтобы снизить значение в случае высокой влажности, его можно сушить на солнце или использовать роторную / турбо сушилку для биомассы [8].Собранные агроотходы обычно собираются и подвергаются дроблению, затем сушке и дальнейшему брикетированию. Путешествие проходит от винтового конвейера до бункера, а затем до купы через двигатель. По мере увеличения сжатия, повышения давления и температуры лигнин действует как естественное связующее и способствует уплотнению. Продукт будет вытеснен, а затем охлаждается, чтобы получить готовый продукт ( Рисунок 3 ).
Способы брикетирования
Существует три метода брикетирования, а именно гидравлический, штамповочный и винтовой пресс для брикетирования ( Рисунок 4 ).Каждый из них имеет сырье разного размера и влажности, плотности, емкости, энергии, срока службы пресс-формы, ПЛК, шума, рабочей среды и пользователей, которые перечислены в Таблица 1 ниже.
Гидравлический брикетировочный пресс | Брикетировочная машина штамповочного типа | Шнековый пресс для брикетирования | |
---|---|---|---|
Размер сырья / мм | 3-20 мм | 3-20 мм | 3-5 мм |
Требуемая влажность сырья | 6% -18% | 10% -20% | 8% -12% |
Профиль продукта | Φ = 70 мм | Φ = 70 мм Гранулы: 8 мм, 10 мм, 22 мм, 30 мм | Φ = 40 мм, 50 мм, 60 мм, 70 мм |
Плотность продукта / г / см 3 | 0.8-1,2 | 0,9–1,3 | 1–1,3 |
Производительность / кг / ч | 125 | 800-1200 | 180-1000 |
Энергопотребление / кВт / т | 40-60 | 40-50 | 70-80 |
Срок службы формы | 1000 ч-1500 ч, охлаждение не требуется для формования | 1000 ч-1500 ч, требуется охлаждение формы | 1500-2000 |
ПЛК | да | Да и виброустойчивость | НЕТ |
Шум | Менее 70 дБ | Более 85 дБ | Около 80 дБ |
Рабочая среда | Без пыли | Без пыли | Дым и пепел |
Пользователи | Высокие требования с автоматическим контролем и рабочей средой, сложным сырьевым компонентом. | Высокие требования с производительностью (1-5 т / ч) | Обычно брикеты далее перерабатываются в брикеты из древесного угля |
Таблица 1: Различные типы брикетировочных машин и характеристики, особенности каждого.
Тестирование брикетирования биомассы
Содержание влаги в сырье является наиболее важным параметром при выборе источника брикетов из биомассы. Приблизительный анализ и содержание влаги при 100 градусах Цельсия.Теплотворная способность представляет собой теплотворную способность брикета из биомассы. Его можно найти с помощью калориметра бомбы. Другие тесты включают температуру пламени, термогравиметрический анализ, время воспламенения, время горения, отсутствие токсичных газов в сгоревшем брикете биомассы, связанный углерод, плотность брикета, зольность, летучие соединения в газе [4,9].
Применение брикетов из биомассы
Брикеты из биомассы могут использоваться в красильной промышленности, полиграфии, молочной промышленности, в установках для керамической, химической экстракции и экстракции растворителями, кожевенной промышленности, производстве кирпича и в тепловых установках.Lehra Fuel Tech Pvt. Ltd, Пенджаб (одобрено IREDA) — одно из крупнейших производителей брикетирования в Индии [10].
Компании, занимающиеся брикетированием
Биомассу можно производить в гранулы или брикеты. Есть много успешных компаний, которые работают с этим, а именно German Pellets, Enviva, Pinnacle Renewable Energy Group, Pacific BioEnergy Corporation, Выборгская целлюлоза, Rentech, Graanul Invest Group, RWE Innogy, Lignetics, E-pellets, Drax Biomass, General Biofuels, BlueFire. Возобновляемые источники энергии, Pfeifer Group, Biomass Secure Power, Viridis Energy, Westervelt, Energex, Fram Renewable Fuels, Protocol Energy, Premium Pellet Ltd., Гранулы LG, Enova Energy Group, Corinith Wood Pellets, Maine Woods Pellet, Аппалачские древесные гранулы, Bear Mountain Forest Prod, Agropellets, West Oregon Wood Prod, Bayou Wood Pellets, Neova Vaggeryd, Aoke Ruifeng, DEVOTION, Sinopeak-bioenergy, Senon Renewable Energy, Equstock, Weige Bio-tech Energy, New Biomass Holding LLC, Verdo Renewables и Binderholz [10,11].
Разведочные исследования энергии посредством брикетирования
Многие исследования проводятся по использованию органических отходов для брикетирования.Водяной гиацинт, самое быстрорастущее растение, может быть экономичным, экологически чистым, считаться эффективным материалом для брикетирования. Материал может быть использован в качестве сопутствующего горючего на электростанциях, производящих энергию. Остатки биомассы в виде брикетов имеют прогрессивное будущее, поскольку золу после сжигания можно использовать в качестве компоста для улучшения почвы растений с лучшими химическими и гидрофизическими свойствами [12]. Освоение технологии брикетирования позволяет найти экономически выгодное и экологически безопасное решение.Исследование было проведено с использованием отходов хлопкоочистки для брикетирования и показало, что 52% тепловой потребности компании можно было удовлетворить за счет этого нового источника, альтернативного мазуту [6,13].
Также можно сравнить размер частиц, давление прессования и качество брикета. Уменьшение размера частиц и повышенное давление снизили скорость горения. Вместо использования потенциального источника энергии путем сжигания и выделения парниковых газов, можно проводить исследования для повышения эффективности и качества производимых брикетов из биомассы.Поскольку биомасса производится из материалов, которые помогают снизить содержание CO 2 в воздухе, они считаются нейтральными по отношению к CO 2 . Обращение с отходами в этой технике также является гигиеническим [5,12].
Исследование соломы, рисовой шелухи и опилок также может быть объединено в брикет с использованием технологии сложного рычажного (деревянного) пресса, который уплотняется без использования тепловой энергии. Комбинация связующего и биомассы варьировалась и тестировалась. Уменьшается соотношение вяжущего и биомассы, уменьшается теплотворная способность, снижается летучесть, уменьшается влажность, увеличивается зольность (древесина имеет минимум золы), увеличивается количество связанного углерода [11].Исследователи сосредоточили внимание не только на соломе и шелухе, но и на ветках, падающих с деревьев. Другое исследование использования веточек Pterocarpus indicus для брикетирования объясняет, что веточки были смешаны с крахмалом тапиоки в различных пропорциях, из которых 90:10 имеет самую высокую теплотворную способность. Было доказано, что чем меньше размер частиц, тем лучше качество брикета. Эксперименты также подтвердили, что более высокое давление улучшает качество брикета. Частицы размером 60 меш прессовали под давлением 2 МПа.Температура пламени составляла 515 ° C, время воспламенения 251 секунда, время горения 6590 секунд и скорость горения 0,00303 грамм / секунду [5].
Из риса и кофейной шелухи маниока и глины в качестве связующих были изготовлены брикеты. Физические свойства, прочность при падении и теплотворная способность зависят от типа используемого связующего. Механическая целостность и целостность брикета при хранении может быть определена путем испытания брикета на падение. HHV маниоки с кофейной шелухой и рисовой шелухой составляли 22-23 МДж / кг и 16-17 МДж / кг. Значение для глины с кофейной шелухой и рисовой шелухой составляло 13-20 МДж / кг и 10-14 МДж / кг.По сравнению с глиной и маниокой, последний показал себя как отличное связующее с сопротивлением падению до 94%.
Скорлупа арахиса и отходы сахарного тростника (жмых) смешивали с мукой из маниоки (тапиоки) и пшеничной мукой в качестве связующих веществ. Были взяты два типа, а именно карбонизированные и негарбонизированные, и сравнены при двух различных уровнях давления. Выбранные источники (агроотходы) были карбонизированы, и 1000 граммов полученного материала (биоуголь из скорлупы арахиса и жома) были смешаны с 30, 50, 70, 90 г связующих и брикетированы при низком давлении.Другой комплект брикетов высокого давления был разработан со связующим и без него. Образец 1 содержал 1000 граммов скорлупы арахиса без связующего, образец 2 — 250 граммов связующего вещества из муки маниоки, образец 3 — 250 граммов связующего вещества из пшеничной муки, брикетированных при высоком давлении 230 МПа. Теплофизические свойства оценивали с помощью термогравиметрического анализа. Калориметр бомба для определения теплотворной способности. Температура пламени также была проверена. Испытание на падение было проведено для проверки уплотнения частицы в брикете.Теплотворная способность и сопротивление падению оказались хорошими для негарбонизированных брикетов со значениями 16 МДж / кг и 99%. Карбонизированные брикеты из отходов скорлупы и жома арахиса имеют теплотворную способность 21-23 МДж / кг [9].
Рисовые отруби, шелуха и пальма брикетировали на многопоршневом прессе местного производства. Шелуха-отруби и все три отруби-шелуха-пальма имели хорошие топливные свойства ( Рисунок 5 ). Результаты показали, что теплотворная способность меньше, чем у древесного угля, и также низкое время запуска [9].
Заключение
Брикетирование или гранулирование — это процесс улучшения характеристик биомассы как возобновляемого источника энергии путем уплотнения. Плотность означает меньший объем, необходимый для того же количества выходной энергии. Брикетируемое сырье должно иметь цель повысить ценность существующего продукта. Это может быть снижение транспортных расходов или использование материала в качестве топлива, цель должна быть ясной. Крошечный размер частиц (уменьшен с 60 до 1200 кг / м3), эффективность горения на 40%, отсутствие дыма и золы, а также простота транспортировки являются ключевыми факторами для продвижения брикетов с целью сбережения энергии.
Ссылки
- Bundhoo ZMA (2018) Управление твердыми отходами в наименее развитых странах: текущее состояние и существующие проблемы. J Mater Cycles Waste Manag 20: 1867-1877.
- Мухаммад С.Н., Мухаммад А.А., Абдул Н., Анджум М. (2016) Разработка и изготовление экструдера для биомассы с размером брикета диаметром 50 мм. Innov Ener Res 5: 128.
- Акхирадж Б., Анирбан С., Димбендра К. (2018). Экспериментальные исследования по улучшению свойств биомассы топлива методом брикетирования.Int J Innov Res Sci Eng Technol 7: 9431-9438.
- Джадхав П.В., Шашикант Д., Кедарнатх С. (2016). Система брикетов из биомассы: экологически чистые источники тепловой энергии. Int J Innov Res Sci Eng Technol 5: 1165-1171.
- Anggono W, Sutrisno, Suprianto FD, Evander J, Gotama GJ (2018) Исследование брикетов биомассы из отходов веток pterocarpus indicus в качестве альтернативной возобновляемой энергии. Int J Renew Energy Res 8: 1393-1400.
- Хуан Б., Чжао Дж., Гэн И, Тиан И, Цзян П. (2017) Выбросы парниковых газов в текстильной промышленности Китая, связанные с энергетикой.Ресурс Консерв Ресайкл 119, 69-77
- Резания С., Понрадж М., Дин М.Ф., Сонгип А.Р., Сайран Ф.М. и др. (2015) Разнообразные применения водяного гиацинта с упором на устойчивую энергетику и производство для новой эры: обзор. Обновите Sust Energ Rev 41: 943-954.
- Lubwama M, Yiga VA (2018) Характеристики брикетов, полученных из рисовой и кофейной шелухи, для домашнего приготовления в Уганде. Обновите энергию 118: 43-55.
- Ndindenga SA, Mbassib JEG, Mbachamc WF, Manfula J, Graham-Acquaaha S, et al.(2015) Оптимизация качества брикетов из побочных продуктов помола риса. Энергетическая поддержка развития 29: 24-31.
- Lubwama M, Yiga VA (2017) Разработка скорлупы арахиса и брикетов из жома в качестве экологически безопасных источников топлива для приготовления пищи в домашних условиях в Уганде. Renew Energ 111: 532-542.
- https://medium.com/@ReportsonIndia/india-biomass-briquette-market-efad1a33cd36
- https://www.jaykhodiyar.com/how-to-briquette-the-biomass/
- https: // energypedia.info / wiki / Биомасса_Брикеты_% E2% 80% 93_Production_and_Marketing
Почему брикеты? | Магазин ЧП «Брикетировочная техника»
.- Дом
- Информация
- Статьи
- Почему брикеты?
Столетие назад самым дешевым, практичным, эффективным и удобным сырьем для отопления были древесина и уголь, позже их заменили нефть и газ — очень эффективный, но, к сожалению, ограниченный и незаменимый в запасах топлива.По самым оптимистичным прогнозам, нефть и газ закончатся в течение трех-пяти десятилетий, поэтому сейчас во всем мире для производства тепла и электроэнергии используются альтернативные возобновляемые источники энергии.
Само производство брикетов из древесных отходов, сельскохозяйственных и других отходов и является такой альтернативой.
Цены на традиционные энергоносители постоянно растут. К тому же в ЕС повышены требования к чистоте промышленных отходов. Европа очень чувствительна к проблемам окружающей среды и решению проблем окружающей среды.Поэтому производство брикетов из биомассы — чистого топлива — очень важный аспект Киотского протокола.
Основные преимущества топливных брикетов из отходов перед обычным топливом — это их экологичность и возобновляемость, а также высокие показатели теплоотдачи и эффективности. Это позволяет широко использовать древесные гранулы на электростанциях, котлах для отопления частных домов и других объектов.
В основе современных технологий производства брикетов лежат три основных этапа подготовки биомассы: измельчение сырья до однородной массы, его сушка, а затем — в ударном механическом прессе для брикетирования под высоким давлением.Сырьем для изготовления брикетов служат биологические отходы — от шелухи подсолнечника, отделочной бумаги, картона и просто опавших листьев — это все, что просто валяется у нас под ногами!
Производство отходов удобно как с точки зрения логистики, так и с точки зрения энергоэффективности. По сравнению с сырьем, топливные брикеты горят с теплопередачей, в десять раз больше на единицу объема. Два килограмма брикетов выделяют столько же энергии, сколько литр, и в несколько раз дороже масла.Благодаря высокой плотности и низкому содержанию влаги брикеты также очень удобны в хранении и обслуживании, особенно по сравнению с исходным сырьем.
Что выгоднее: производство брикетов или пеллет?
С точки зрения экономической выгоды производство топливных брикетов методом механического брикетирования более привлекательно, поскольку инвестиции в линию брикетирования и стоимость намного ниже по сравнению с линией гранулирования с аналогичной производительностью. На линии брикетирования на базе ударно-механического пресса к качеству сырья предъявляются минимальные требования, поэтому возможно производство брикетов из гораздо большего количества отходов.Однако то и другое технологическое оборудование для производства брикетов позволяет избавиться от дорогостоящего импортного газа до неисчерпаемого и расточительного топлива.
В целом производство брикетов, оборудования для производства топливных брикетов из древесины, соломы, камыша, продажа топливных брикетов в Европе и использование внутреннего рынка — очень прибыльный и перспективный бизнес, потому что наш агропромышленный потенциал позволяет Украине стать ведущим экспортером топливных брикетов в страны Европы
Технико-экономический анализ биобрикета из отходов скорлупы кешью
3.1. Результаты экспресс-анализа и теплотворная способность
Продуктом пиролиза является биоуголь 41,0%, жидкий дым 39,3%, остальное — газ. Biochar проводится на основе предварительного анализа для определения его влажности, золы, летучих веществ, связанного углерода и теплотворной способности. Результаты анализа представлены в.
Таблица 1
Ориентировочный анализ и теплотворная способность биобрикетов из различных материалов.
Материал | Влажность (мас.%) | Зола (мас.%) | Летучие вещества (мас.%) | Неподвижный углерод (мас.%) | Теплотворная способность (МДж / кг) | Каталожный номер | ||||||
---|---|---|---|---|---|---|---|---|---|---|---|---|
Отходы орехов кешью | 5.30 | 4,96 | 17,16 | 72,62 | 29,49 | (Ifa et al., 2019) | ||||||
Смесь шелухи ореха ареки, скорлупы семян Simarouba | 73,821 5,7518,81 | (Ujjinappa and Sreepathi, 2018) | ||||||||||
Скорлупа кешью | — | 5,80 | 29,65 | 64,55 | Хлопок 27,73 | 9057 9021 stalk (Sawadogo et al. .50 | 7,30 | 60,30 | 39,70 | 27,90 | (Wu et al., 2018) | |
Оболочка ядра пальмы | 1,75 | 4,83 | 55.95 | 3970 al., 2017) | ||||||||
кожура банана, кукурузные початки и угольная смесь | 5,14 | 6,06 | 26,18 | 62,62 | 26,36 | (Faizal, 2017) | 1 5.0–1025–30 | 60–68 | 26,50 | (Borowski et al., 2017) | ||
Твердые отходы текстильной промышленности | — | 12,76 | 77,99 | 9,24 | (Авелар и др., 2016) | |||||||
Жмых и отходы кукурузного крахмала | 6,86 | 8,59 | 48,50 | 42,92 | 10,30 | (Занелла и др., 2016) | 5.30 | 5,08 | 18,40 | 71,27 | 29,51 | (Akowuah et al., 2012) |
Биомасса сельскохозяйственного и лесного происхождения | 12,04 | 5,57 9021 | 748,21 Столярски и др., 2013) | |||||||||
Банановые листья | 7,17 | 10,70 | 75,3 | 14,00 | 17,70 | (Майя и др., 2014) | ||||||
821 пыль | 637,35 | 70,37 | 16,65 | 14,94 | (Suvunnapob et al., 2015) | |||||||
Макулатура, 2013 г., | 6,23 | 12,38 ) | ||||||||||
Сушеные листья и макулатура | 6,52 | 12,48 | 75,78 | 5,02 | 17,30 | |||||||
Маис и макулатура | 8,67 14578 | .72 | 78,93 | 20,46 | 18,75 | |||||||
Кокосовая шелуха и макулатура | 7,19 | 15,62 | 65,44 | 19,08 | 18,83 | 9057aste9,63 | 19,01 | |||||
Багасса, опилки и макулатура | 5,96 | 13,58 | 63,65 | 22,16 | 20.42 | |||||||
Смесь жома и кофейной шелухи | 4,40 | 12,00 | 24,00 | 64,00 | 11,13 | (Pallavi et al., 2013) | ||||||
218 218 27.20 | 36.40 | 18.38 | (Onchieku et al., 2012) | |||||||||
Скорлупа лесного ореха | — | 7.00 | 72.00 | 21.00 | 18.89 |
Качество биобрикетов определяется содержанием влаги в биомассе, используемой в качестве исходного материала.При более высоком содержании влаги в биомассе для испарения воды во время сгорания потребуются большие потери энергии за счет теплотворной способности биобрикетов (Aina et al., 2009). По содержанию влаги отходы биобрикетов из орехов кешью имеют более низкое содержание влаги, чем другое сырье. показал влажность материалов. Содержание влаги соответствует стандартам биобрикетов SNI 016235-2000 (<8%) и ISO 17225 (2,2% –15,9%).
Имеется недостаток в составе высоколетучих веществ с низким содержанием углерода.В России содержание летучих в биобрикетах из отходов кешью составляло 17,16%. Уровни высоколетучих веществ по результатам этого исследования ниже, чем сообщается в литературе (Akowuah et al., 2012; Onchieku et al., 2012; Stolarski et al., 2013; Tamilvanan, 2013; Maia et al., 2014; Suvunnapob et al., 2015; Zanella et al., 2016; Avelar et al., 2016; Moreira et al., 2016; Abdillahi et al., 2017; Faizal, 2017; Borowski et al., 2017; Sawadogo et al. , 2018; Ujjinappa, Sreepathi, 2018; Wu et al., 2018).Он поддерживает Suvunnapob et al. (2015) пришли к выводу, что древесина с высокой плотностью позволяет производить биобрикеты с более летучими веществами. При низком содержании летучих веществ дым от сгорания биобрикетов будет ниже. Он превращает биобрикеты из отходов орехов кешью в экологически чистые биобрикеты, поскольку они могут уменьшить эффект глобального потепления и служить потенциальным источником твердого возобновляемого топлива. Содержание летучих веществ соответствует японскому стандарту биобрикетов (15–30%) по зольности продуктов, представленных в.Большой объем золы является недостатком, так как это может привести к образованию токсичного порошка из пыли и атмосферы. В сумме это оказывает сильное влияние на сгорание топлива (Sawadogo et al., 2018). Содержание золы в этом исследовании составило 4,96 мас.%, Что ниже заявленного (Tamilvanan, 2013; Abdillahi et al., 2017; Ujjinappa and Sreepathi, 2018). Лучше, если уголь будет иметь более низкий процент зольности, так как это экономит затраты на транспортировку и утилизацию после использования древесного угля (Onchieku et al., 2012). Зольность соответствует стандартам SNI 016235-2000 (<8%), японскому (3–6%) и ISO 17225 (3.3–11,7%) эталоны биобрикетов. Критерии Стандартов качества Тайского сообщества (657/2547) предусматривают, что остаточное содержание золы после сжигания должно быть менее 10% по весу (Suvunnapob et al., 2015).
Содержание фиксированного углерода в древесном угле колеблется от 50% до 95%, но древесный уголь в основном состоит из биомассы. Содержание углерода обычно измеряется как «разница», то есть все остальные составляющие исключаются в процентах от 100, а оставшаяся часть считается количеством «исходного» или «установленного» углерода (ФАО, 1985).Определение общего содержания углерода () было совместимо с другой литературой (Mardoyan and Braun, 2015) и что объем углерода имеет тесную связь с тепловыми величинами в биотопливе (Mardoyan and Braun, 2015). Чем выше содержание углерода, тем лучше производится углерод, поскольку соответствующая теплотворная способность обычно высока (FAO, 1985). Содержание связанного углерода соответствует японским (60–80%) и британским (75,0%) стандартам биобрикетов.
Теплотворная способность — важное свойство биобрикетов, поскольку она отражает энергетическое содержание топлива (Aina et al., 2009). Теплотворная способность биомассы зависит от ее химического состава и содержания влаги (Akowuah et al., 2012). Теплотворные свойства биобрикетов, полученных в этом исследовании, позволяют предположить, что отходы орехов кешью очень подходят для производства биобрикетов, как показано на рис. Теплотворная способность биобрикетов, полученных из отходов орехов кешью (29,49 МДж / кг), в этой работе выше, чем у брикетов, полученных Akowuah et al. (2012) при 20,18 МДж / кг; Тамилванан (2013 г.) при 20,42 МДж / кг; Moreira et al. (2016) при 28 МДж / кг; Абдиллахи и др.(2017) при 29,6 МДж / кг; Файзал (2017) при 26,36 МДж / кг; Боровски и др. (2017) 26,50 МДж / кг; Sawadogo et al. (2018) при 27,73 МДж / кг; Wu et al. (2018) при 27,90 МДж / кг и Удджинаппа и Шрипати (2018) при 18,81 МДж / кг. Производимые биобрикеты обладают свойствами, подходящими для использования в качестве источника энергии. Теплотворная способность соответствует (SNI 016235-2000) (> 20,93) и японским (25,12 МДж – 29,31 МДж). Результаты, полученные в настоящем исследовании, показывают, что биобрикеты из отходов орехов кешью могут успешно конкурировать с углем, являющимся источником возобновляемой энергии.
Биобрикеты, произведенные из отходов скорлупы орехов кешью, имеют рекомендуемые характеристики биобрикетов и имеют рыночный потенциал в Индонезии. Приблизительные характеристики и анализ теплотворной способности биобрикетов, оцененных в этом исследовании, показали, что биобрикеты, изготовленные из отходов скорлупы орехов кешью, имели низкое содержание влаги (5,30%), низкое содержание золы (4,96%) и высокую теплотворную способность (29,49 МДж). / кг) (Ifa et al., 2019).
3.2. Экономический анализ
Согласно Bhujel (2014), биобрикеты использовались в качестве возобновляемых ресурсов биомассы в течение десятилетия.Есть шансы производить и заменять ископаемое топливо, используя отходы растительности и экономические возможности местных жителей. Условия спроса и предложения в настоящее время являются растущими тенденциями, которые доступны в супермаркетах, магазинах шаговой доступности и других торговых точках. Он используется в основном для приготовления пищи, отопления для детей / пожилых людей, дома и в офисных целях. Производство возобновляемой энергии биомассы за счет создания устойчивых рынков — это большие возможности. Biochar снижает уровень красного нитрата; biochar увеличивает обменный потенциал почвенных катионов (Maroušek et al., 2018).
Основной бизнес-целью при проектировании и развитии химического завода является получение экономической выгоды от использования сырья. Повышение экономической стоимости достигается за счет превращения сырья в товар с более высокой рыночной стоимостью для получения некоторой прибыли. Следующие переменные были определены как наиболее важные статьи: прибыль или убыток и добавленная стоимость (Machová and Vrbka, 2018). Ожидается, что после прекращения деятельности доход от продажи недвижимости превысит заявленную величину (Vochozka et al., 2019).
Согласно Ариесу и Ньютону (1955), экономический анализ проводится для определения целесообразности развития химической промышленности. Превосходная химическая промышленность относится к химической промышленности, которая будет приносить финансовую выгоду в том виде, в каком она существует. Сумма налога должна быть уплачена путем расчета суммы основного и оборотного капитала, стоимости производства, дохода от продажи продукта и суммы бесконечных инвестиций.
3.2.1. Предполагаемые инвестиции в основной капитал (FCI)
Капитальные вложения — это сумма денег, потраченная на создание и эксплуатацию фабрики по производству товаров из сырья.Есть два типа капитала: основной и оборотный. Инвестиции в основной капитал (FCI) необходимы для создания заводов и объектов. Он также определяется как общая стоимость установки технологического оборудования, зданий, вспомогательных устройств и инженерных работ, задействованных при создании нового завода (Aries and Newton, 1955). Стоимость приобретенного оборудования сначала рассчитывается, как показано на сайте www.matche.com, и представлена в.
Таблица 2
№ | Оборудование | Итого | Цена за единицу (долл. США) | |
---|---|---|---|---|
1 | Ленточный конвейер (бункер) | 1Склад кокосовой скорлупы | 1 | 180 |
3 | Ленточный конвейер (перед бункером) | 1 | 3,440 | |
4 | 1 | 9057 9057 9057 контейнер для муки|||
5 | Реактор пиролиза | 1 | 7,800 | |
6 | Осушитель | 1 | 4,920 | |
7 | Бункер с низким содержанием материала 1,48 Накопительный бак | 1 | 1,440 | |
9 | Смеситель | 1 | 3,336 905 78 | |
10 | Ленточный конвейер (над накопительным баком) | 1 | 3,680 | |
11 | Ленточный конвейер (над накопительным резервуаром) | 2 | 7,360 | |
1 | 9,520 | |||
13 | Ленточный конвейер (перед резервуаром для хранения) | 1 | 3,680 | |
14 | Пресс для биобрикетов | |||
15 | Транспортер для транспортировки отходов | 1 | 3,680 | |
16 | Поворотный стол | 1 | 8,720 | |
17 | 9057 9057 9057 9057 9057 calorimeter Bomb Bomb | Резервуар для жидкого дыма | 1 | 2,480 |
Итого Стоимость оборудования | 114,440 |
Общая стоимость технологического оборудования составляет 114 440 долларов США.Общая стоимость оборудования составляет 10% от общей стоимости технологического оборудования в размере 125 884 долларов США. Эта цена на оборудование рассчитывается с использованием FCI следующим образом: все компоненты прямых затрат (D) оцениваются путем тестирования цены закупленного поставленного оборудования, которое состоит из закупленного поставленного оборудования, установки, контрольно-измерительных приборов и управления, трубопроводов, электрических систем, благоустройства двора. , здания и хозяйственные помещения. Косвенные затраты (i), такие как проектирование и строительство, проверяются на поставленном приобретенном оборудовании.Кроме того, гонорар подрядчика и непредвиденные расходы определяются на основе общего (D + I) процента, как показано в уравнении. (6) и.
FCI = D + I + Гонорар подрядчика + непредвиденные расходы
(6)
Таблица 3
Компоненты | Стоимость (долл. США) | ||
---|---|---|---|
Цена прибывшего оборудования (E) 125,8578 | |||
Монтаж инструментов, установка 39% E | 49,095 | ||
КИПиА, 28% E | 16,365 | ||
Трубопровод (установка), 31% E | 39,024 | 905 установка), 10% E | 12,588 |
Строительство и обслуживание, 22% E | 36,506 | ||
Ремонт двора, 10% E | 12,588 | ||
Улучшение оборудования, 55% E 90,2578 | 21|||
Земля, 6% E | 7,553 | ||
Итого прямые затраты, D | 368,840 | ||
Инжиниринг и надзор, 32% E | 40, 283 | ||
Затраты на строительство, 34% E | 42,801 | ||
Итого прямые + косвенные затраты, (D + I) | 451924 | ||
Гонорары подрядчиков, 5% (D + I) | 22,596 9057 | ||
Непредвиденные расходы, 10% (D + I) | 45,192 | ||
Общая сумма инвестиций в фиксированные затраты | 519,712 |
Общая сумма инвестиций в основной капитал для установки технологического оборудования, зданий, вспомогательных устройств и инженерные услуги — 519 712 долларов США.
3.2.2. Инвестиции в оборотный капитал (WCI)
Инвестиции в оборотный капитал определяются как затраты, необходимые для ведения бизнеса. Он включает в себя запасы сырья, незавершенные запасы, запасы продукции, расширенный кредит и наличные деньги. Согласно Ариесу и Ньютону (1955), оборотный капитал составляет 10–15% от общих инвестиций или 25% от годовой стоимости продаж продукции. Для этого процесса 15% TCI рассчитывается по формуле. (7).
Общая сумма денег, потраченных на создание и эксплуатацию завода (TCI), составляет 611 426 долларов США.
3.2.3. Себестоимость продукции
Себестоимость продукции прямо или косвенно связана с другими компонентами, такими как администрирование, маркетинг, разработка и т. Д. В общем, он делится на две части: производственные затраты и общие расходы. Затраты на техническое обслуживание относятся к техническому обслуживанию технологического оборудования. Это сумма всех прямых, косвенных и постоянных затрат, полученных при производстве продукта.
и.
Прямые производственные затраты включают сырье, рабочую силу (OL), затраты на надзор, коммунальные услуги, техническое обслуживание и ремонт, эксплуатационные материалы, лаборатории, патенты и лицензионные платежи.
ii.
Косвенные производственные затраты — это расходы, понесенные в результате косвенных производственных операций, а именно амортизация, местные налоги и страхование.
iii.
Фиксированные производственные затраты (FMC). Это расходы, связанные с первоначальными вложениями в основной капитал и ценой, независимо от времени или уровня производства, включая амортизацию, налоги, страхование и арендную плату. Результаты расчета прямых, косвенных и постоянных производственных затрат представлены в.
Таблица 4
Нет Компоненты Стоимость (долл. США) 1 Сырье 132,679 2 9057Надзор 6,626 4 Техническое обслуживание 10,394 5 Поставки завода 1,559 6 9057 9057 9057 9057 9057 9057
105,288 Прямые производственные затраты (DMC) 487,949 8 Накладные расходы на заработную плату 41,577 9 Лаборатория 5,1978 11 Packagin г 42,115 Косвенные производственные затраты (IMC) 175,086 12 Амортизация 41,577 13 9057 9057 9057 9057 9057 9057 9057 9057 9057 9057 9057 9057 % FCI) 5,197 15 Банковские проценты (5.5% ссудный капитал банка) 13,451 Фиксированные производственные затраты (FMC) 65,423 Производственные затраты (MC) 728,457
95 (12)
3.2.4. Общие расходы (GE)
GE — производственные расходы, состоящие из административных расходов, продаж продукции, исследований и расходов. Кроме того, он состоит из 3% административных расходов, 5% затрат на распространение и маркетинг 3.5% затрат на исследования и разработки и 5% затрат на TCI.
GE = административные расходы (3% MC) + расходы на распространение и маркетинг (5% MC) + затраты на исследования и разработки (3,5% MC) + расходы (5% TCI)
(13)
GE = (3% 728 457) + ( 5% 728 457 фунтов стерлингов) + (3,5% 728 457 фунтов стерлингов) + (5% 611 426 фунтов стерлингов)
(14)
Общие производственные расходы без учета производства составляют 114 293 долларов США.
TPC (USD) = MC + GE = 728 457 + 114 293
(15)
Общая стоимость производства (TPC) составляет 842 304 доллара США.
3.2.5. Продажи, прибыль и технико-экономический анализ рентабельности
Продажи — это заводские продукты, проданные клиентам на основе рыночных или минимальных заводских цен.Предполагая, что у фабричного продукта уже есть конкурент, отпускная цена устанавливается на уровне продажной цены конкурентов или ниже. Расчетная валовая и чистая прибыль показана в.
Таблица 5
Объем продаж, долл. США | 1,052,878 | |||
---|---|---|---|---|
Стоимость производства, долл. США | 728,457 | |||
9057 9057 долл. США Общие расходы8 Стоимость, долл. США | 842,304 | |||
Прибыль до налогообложения, долл. США | 210,574 | |||
Налог на прибыль (30%), долл. США | 63,172 | 905 905 Прибыль | 147,402 |
Выручка получается за счет вычитания чистой выручки из себестоимости продукции.С этим показателем связаны два вида доходов: валовой и чистый доход, которые не включают заработную плату до и после налогообложения. Чистая прибыль в размере 147 402 долларов США в год больше, чем у Stolarski et al. (2013) на сумму 37 627,4 евро или 43 000,59 долларов США в год.
Помимо ориентации на прибыль, бизнес должен вернуть деньги, полученные от ссуды, задуманной как мера дохода с использованием основного капитала или выплаченного времени (POT). Уровень возврата инвестиций и периода выплаты варьируется в зависимости от риска, связанного с производством на предприятии (Peters and Timmerhaus, 2003).
Проверка экономической осуществимости также представляет собой форму графика зависимости производственных мощностей от затрат. Он образует точку останова и точку безубыточности. Заводы, как правило, несут убытки, если они работают на мощности ниже точки безубыточности. Хорошее значение точки безубыточности для химических заводов обычно находится в диапазоне от 40% до 60% (Aries and Newton, 1955).
3.2.6. Чистая приведенная стоимость (NPV)
NPV — это сумма всех текущих значений чистого дохода, прогнозируемого каждый год (Smith, 2005).Каждый денежный поток уменьшается и делится на число, которое отражает альтернативные издержки владения капиталом, до тех пор, пока он не будет заработан или израсходован. NPV является одним из критериев, используемых для одновременной оценки расходов (отток денежных средств) и доходов (приток денежных средств) (Dhaundiyal and Tewari, 2015).
Это подход, используемый для измерения чистой приведенной стоимости. Текущие допущения определяют первоначальное время оценки, совпадающее с оценкой нулевого (0) года, путем измерения инвестиций в денежный поток (Hakizimana and Kim, 2016).
Текущая стоимость долларов, заработанных или выплаченных в будущем, получается путем умножения денежного потока на коэффициент дисконтирования текущей стоимости, как показано в уравнении. (16) ((Short et al., 1995) и Satyasai (2014)).
NPV = −TCI + ∑ (CF (1 + i) n)
(16)
TCI — общие капитальные вложения, CF — денежный поток в n -м -м году, n — год, и 1 / (1 + i) n — коэффициент дисконтирования.
3.2.7. Норма возврата инвестиций
Норма возврата инвестиций, основанная на дисконтированном денежном потоке, представляет собой процентную ставку, при которой все доходы покрывают капитальные затраты с использованием пробной цены.Следовательно, он выполняет следующее по формуле. (17).
CF — денежный поток за n -й -год, n — год, а 1 / (1 + i) n — коэффициент дисконтирования (см.).
Таблица 6
Дисконтированный денежный поток для значения i.
n -е -год | Чистый денежный поток (CF) | Пробная i = текущая стоимость | ||
---|---|---|---|---|
1 | 86,677 | 86,677 | ||
3 | 97,922 | 97,922 | ||
4 | 79,805 | 79,805 | ||
5 | ||||
5 | 65,037 | 65,037 9057 9057 9057 9057 9057 9057 8 | 43,188 | 43,188 |
8 | 35,192 | 35,192 | ||
9 | 28,675 | 28,675 | ||
10 | ||||
10 |
(Peters and Timmerhaus, 2003)
Соотношение = 611,2306 11 426 = 1.0
(19)
Правильная процентная ставка (i) определяется путем сопоставления общей приведенной стоимости с начальными инвестициями и угадывания процентной ставки (i). Для получения правильной процентной ставки по проекту коэффициент должен быть равен 1,0 (Peters and Timmerhaus, 2003). На основании приведенного выше расчета получается цена 23,55% в год, что больше, чем капитальные ссуды банков под 5,5%. Проект / инвестиция выполняется при условии, что норма возврата превышает значение ROI. Тем не менее, это исследование — это ROI Хакизиманы и Ким (2016) в 24 года.94% показали, что фабрика заслуживает дальнейшего развития (Hakizimana, Kim, 2016).
3.2.8. Время выплаты (POT)
POT — это быстрая оценка, используемая для определения времени, в течение которого капиталовложения являются рискованными (Short et al., 1995). POT рассчитывается как.
Таблица 7
Совокупный денежный поток (долл. США).
n th -год | Чистый денежный поток | Накопленные денежные средства | |||||||||||||||||||||||||||||||||||||||||||||||||||||||||||
---|---|---|---|---|---|---|---|---|---|---|---|---|---|---|---|---|---|---|---|---|---|---|---|---|---|---|---|---|---|---|---|---|---|---|---|---|---|---|---|---|---|---|---|---|---|---|---|---|---|---|---|---|---|---|---|---|---|---|---|---|---|
1 | 107,061 | 107,061 | |||||||||||||||||||||||||||||||||||||||||||||||||||||||||||
9057 9057 9057 9057 9057 | 9057 9057 | 184528 | 442741 | ||||||||||||||||||||||||||||||||||||||||||||||||||||||||||
4 | 185754 | 628495 | |||||||||||||||||||||||||||||||||||||||||||||||||||||||||||
5 | 186980 | 815475 | |||||||||||||||||||||||||||||||||||||||||||||||||||||||||||
6 | 188206 | 1003681 | |||||||||||||||||||||||||||||||||||||||||||||||||||||||||||
7 | 189432 | 1193113 | |||||||||||||||||||||||||||||||||||||||||||||||||||||||||||
8 | 190,659 | 1,383,772 | |||||||||||||||||||||||||||||||||||||||||||||||||||||||||||
9 | 191,885 | 1,575,656 | |||||||||||||||||||||||||||||||||||||||||||||||||||||||||||
10 | 193,111 | 1,768,767 | получено в 3.42 года при стоимости FCI 519 712 долларов США. POT этого исследования короче, чем POT Хакизиманы и Кима (2016), который составляет 5–6 лет (Hakizimana and Kim, 2016) и Maroušek et al. (2019), что составляет 4–6 лет (Maroušek et al., 2019). Без вычета налогов максимально допустимый POT для промышленных химикатов составляет пять лет для низкого риска и два года для высокого риска (Aries and Newton, 1955).3.2.9. Точка безубыточности (BEP)Исследование BEP используется для оценки суммы производственных мощностей, где общие затраты эквивалентны показателям продаж.Стоимость сделки равна начисленным расходам. Точка разделения, фиксированные затраты и полувариантная производственная деятельность должны определяться с использованием графической формы (Aries and Newton, 1955) (см.). BEP = FC + 0,3⋅SVCS − 0,7⋅SVC − VC⋅100% (20) Таблица 8Фиксированные затраты, переменные затраты, полупеременные затраты и продажи.
Предположим, домашнему хозяйству требуется сжиженный нефтяной газ до 1 кг / день, где теплотворная способность сжиженного нефтяного газа составляет 44.00 МДж / кг, а теплотворная способность керосина составляет 42,00 МДж (Surange et al., 2014). Например, если взять стоимость сжиженного нефтяного газа для приготовления пищи в качестве справочной цены (0,01072 долларов США / МДж), а стоимость электроэнергии для домашних хозяйств сжиженного нефтяного газа составляет 0,47718 долларов США в день. Если текущая цена на керосин составляет 0,60840 долларов США / кг, одной семье требуется стоимость энергии в размере 0,81265 долларов США в день. |