Π’Π΅Ρ Π½ΠΎΠ»ΠΎΠ³ΠΈΡ ΠΏΡΠΎΠΈΠ·Π²ΠΎΠ΄ΡΡΠ²Π° Π³ΠΈΠΏΡΠΎΠ²ΠΎΠΉ Π»Π΅ΠΏΠ½ΠΈΠ½Ρ | ΠΠ΅ΡΡΠΎΠ‘ΡΠ°Ρ
ΠΠ³ΡΠ°Π½ΠΈΡΠ΅Π½Π½ΠΎΠ΅ ΠΈΡΠΏΠΎΠ»ΡΠ·ΠΎΠ²Π°Π½ΠΈΠ΅ Π² ΠΈΠ½ΡΠ΅ΡΡΠ΅ΡΠ΅ ΠΈ ΡΡΡΠ΄ΠΎΠ΅ΠΌΠΊΠΈΠΉ ΠΏΡΠΎΡΠ΅ΡΡ ΠΏΡΠΎΠΈΠ·Π²ΠΎΠ΄ΡΡΠ²Π° Π³ΠΈΠΏΡΠΎΠ²ΠΎΠΉ Π»Π΅ΠΏΠ½ΠΈΠ½Ρ, ΡΠΎΡΡΠΎΠΈΡ ΠΈΠ· ΡΡΠ΅Ρ ΡΡΠ°ΠΏΠΎΠ²:
- ΠΠΎΠ΄Π΅Π»ΠΈΡΠΎΠ²Π°Π½ΠΈΠ΅
- Π’ΠΈΡΠ°ΠΆΠΈΡΠΎΠ²Π°Π½ΠΈΠ΅ ΠΈ ΡΠΎΡΠΌΠΎΠ²ΠΊΠ°
- ΠΠΎΠ½ΡΠ°ΠΆ Ρ ΠΏΠΎΡΠ»Π΅Π΄ΡΡΡΠ΅ΠΉ ΠΏΡΠ΅Π΄ΠΏΠΎΠΊΡΠ°ΡΠΎΡΠ½ΠΎΠΉ ΠΎΠ±ΡΠ°Π±ΠΎΡΠΊΠΎΠΉ.
ΠΠΎΠ΄Π΅Π»ΠΈΡΠΎΠ²Π°Π½ΠΈΠ΅ Π³ΠΈΠΏΡΠΎΠ²ΠΎΠΉ Π»Π΅ΠΏΠ½ΠΈΠ½Ρ
ΠΠ° Π΄Π°Π½Π½ΠΎΠΌ ΡΡΠ°ΠΏΠ΅ ΠΏΡΠΎΠΈΡΡ ΠΎΠ΄ΠΈΡ ΠΏΡΠΎΡΠ΅ΡΡ ΡΠΎΠ·Π΄Π°Π½ΠΈΡ ΠΌΠΎΠ΄Π΅Π»ΠΈ ΠΈΠ·Π΄Π΅Π»ΠΈΡ ΠΈΠ· Π³ΠΈΠΏΡΠ°. ΠΠΎΠ΄Π΅Π»Ρ ΡΠ²Π»ΡΠ΅ΡΡΡ ΠΎΠ±ΡΠ°Π·ΡΠΎΠΌ Π΄Π΅ΠΊΠΎΡΠ°ΡΠΈΠ²Π½ΠΎΠ³ΠΎ ΡΠ»Π΅ΠΌΠ΅Π½ΡΠ°, ΠΊΠΎΡΠΎΡΡΠΉ Π²ΡΠΏΠΎΠ»Π½ΡΠ΅ΡΡΡ ΠΈΠ· ΡΠ°Π·Π»ΠΈΡΠ½ΡΡ ΠΌΠ°ΡΠ΅ΡΠΈΠ°Π»ΠΎΠ² ΠΏΠΎ ΡΡΠΊΠΈΠ·Π°ΠΌ, ΡΠ΅ΡΡΠ΅ΠΆΠ°ΠΌ, Π»ΠΈΠ±ΠΎ ΡΠΎΡΠΎΠ³ΡΠ°ΡΠΈΡΠΌ. ΠΠΎΡΠ»Π΅ ΠΈΠ·Π³ΠΎΡΠΎΠ²Π»Π΅Π½ΠΈΡ ΠΌΠΎΠ΄Π΅Π»ΠΈ Ρ Π½Π΅Π΅ ΡΠ½ΠΈΠΌΠ°Π΅ΡΡΡ ΡΠΎΡΠΌΠ°, Ρ ΠΏΠΎΠΌΠΎΡΡΡ ΠΊΠΎΡΠΎΡΠΎΠΉ ΠΎΡΠ»ΠΈΠ²Π°ΡΡ Π½Π΅ΠΎΠ±Ρ ΠΎΠ΄ΠΈΠΌΠΎΠ΅ ΠΊΠΎΠ»ΠΈΡΠ΅ΡΡΠ²ΠΎ Π΄Π°Π½Π½ΡΡ ΡΠ»Π΅ΠΌΠ΅Π½ΡΠΎΠ². ΠΠ°Π½Π½ΡΠΌ ΠΏΡΠΎΡΠ΅ΡΡΠΎΠΌ Π·Π°Π½ΠΈΠΌΠ°Π΅ΡΡΡ ΠΌΠ°ΡΡΠ΅Ρ-ΠΌΠΎΠ΄Π΅Π»ΡΡΠΈΠΊ.
ΠΡΠ΅ ΠΌΠΎΠ΄Π΅Π»ΠΈ ΡΠ°Π·Π»ΠΈΡΠ°ΡΡΡΡ ΠΏΠΎ ΠΌΠ°ΡΠ΅ΡΠΈΠ°Π»Ρ ΠΈΠ· ΠΊΠΎΡΠΎΡΠΎΠ³ΠΎ ΠΎΠ½ΠΈ ΠΈΠ·Π³ΠΎΡΠ°Π²Π»ΠΈΠ²Π°ΡΡΡΡ, Π² ΠΎΡΠ½ΠΎΠ²Π½ΠΎΠΌ ΠΏΡΠΈΠΌΠ΅Π½ΡΠ΅ΡΡΡ ΡΠ²Π΅ΡΠ΄ΡΠ΅ β Π³ΠΈΠΏΡ, ΠΈΠ»ΠΈ ΠΌΡΠ³ΠΊΠΈΠ΅ β ΠΏΠ»Π°ΡΡΠΈΠ»ΠΈΠ½, Π³Π»ΠΈΠ½Π°, Π²ΠΎΡΠΊ. Π ΠΈΠ½ΡΠ΅ΡΡΠ΅ΡΠ½ΠΎΠΉ Π»Π΅ΠΏΠ½ΠΈΠ½Π΅ ΠΈΡΠΏΠΎΠ»ΡΠ·ΡΠ΅ΡΡΡ Π³ΠΈΠΏΡ, Π² ΡΠΊΡΡΠ΅ΡΡΠ΅ΡΠ½ΠΎΠΉ β Π³Π»ΠΈΠ½Π°, ΠΏΠ»Π°ΡΡΠΈΠ»ΠΈΠ½.
ΠΠΎ ΡΡΠ½ΠΊΡΠΈΠΎΠ½Π°Π»ΡΠ½ΠΎΡΡΠΈ ΠΌΠΎΠ΄Π΅Π»ΠΈ Π΄Π΅Π»ΡΡΡΡ Π½Π° ΠΏΠ»ΠΎΡΠΊΠΈΠ΅ ΠΈ ΠΎΠ±ΡΠ΅ΠΌΠ½ΡΠ΅. Π ΠΏΠΎ Π²Π½Π΅ΡΠ½Π΅ΠΌΡ Π²ΠΈΠ΄Ρ β ΠΎΡΠ½Π°ΠΌΠ΅Π½ΡΠ½ΡΠ΅ ΠΈ Π³Π»Π°Π΄ΠΊΠΈΠ΅.
Π’ΠΈΡΠ°ΠΆΠΈΡΠΎΠ²Π°Π½ΠΈΠ΅ ΠΈ ΡΠΎΡΠΌΠΎΠ²ΠΊΠ°
Π€ΠΎΡΠΌΠΎΠ²ΠΊΠ°, ΡΡΠΎ ΠΏΡΠΎΡΠ΅ΡΡ ΠΏΠΎΠ»ΡΡΠ΅Π½ΠΈΡ Π½Π΅ΠΎΠ±Ρ ΠΎΠ΄ΠΈΠΌΠΎΠ³ΠΎ ΡΠ΅Π»ΡΠ΅ΡΠ° Ρ ΠΌΠΎΠ΄Π΅Π»ΠΈ, ΠΊΠΎΡΠΎΡΠ°Ρ ΠΈΠ·Π³ΠΎΡΠΎΠ²Π»Π΅Π½Π° Π½Π° ΠΏΡΠ΅Π΄ΡΠ΄ΡΡΠ΅ΠΉ ΡΡΠ°Π΄ΠΈΠΈ ΠΏΡΠΎΠΈΠ·Π²ΠΎΠ΄ΡΡΠ²Π°. Π‘ ΠΏΠΎΠΌΠΎΡΡΡ ΠΏΠΎΠ»ΡΡΠ΅Π½Π½ΠΎΠΉ ΡΠΎΡΠΌΡ ΠΏΡΠΎΠΈΠ·Π²ΠΎΠ΄ΠΈΡΡΡ ΠΈΠ·Π³ΠΎΡΠΎΠ²Π»Π΅Π½ΠΈΠ΅ Π½ΡΠΆΠ½ΠΎΠ³ΠΎ ΠΊΠΎΠ»ΠΈΡΠ΅ΡΡΠ²Π° Π½Π΅ΠΎΠ±Ρ ΠΎΠ΄ΠΈΠΌΡΡ ΠΊΠΎΠΏΠΈΠΉ ΠΊΠΎΠ½ΠΊΡΠ΅ΡΠ½ΠΎΠΉ Π΄Π΅ΡΠ°Π»ΠΈ. Π‘Π»ΠΎΠΆΠ½ΠΎΡΡΡ ΡΠΎΡΠΌΡ ΠΈ Π²Π½Π΅ΡΠ½ΠΈΠΉ Π²ΠΈΠ΄ ΠΎΠΏΡΠ΅Π΄Π΅Π»ΡΡΡΡΡ Π½Π΅ΠΏΠΎΡΡΠ΅Π΄ΡΡΠ²Π΅Π½Π½ΠΎ ΠΌΠ°ΡΠ΅ΡΠΈΠ°Π»ΠΎΠΌ ΠΌΠΎΠ΄Π΅Π»ΠΈ, ΠΊΠΎΠ»ΠΈΡΠ΅ΡΡΠ²ΠΎΠΌ Π΄Π΅ΡΠ°Π»Π΅ΠΉ ΠΈ ΡΠΏΠΎΡΠΎΠ±ΠΎΠΌ ΡΠΎΡΠΌΠΎΠ²ΠΊΠΈ.
ΠΠΎΠ½ΡΠ°ΠΆ Ρ ΠΏΠΎΡΠ»Π΅Π΄ΡΡΡΠ΅ΠΉ ΠΏΡΠ΅Π΄ΠΏΠΎΠΊΡΠ°ΡΠΎΡΠ½ΠΎΠΉ ΠΎΠ±ΡΠ°Π±ΠΎΡΠΊΠΎΠΉ
ΠΠ΅ΡΠ΅Π΄ Π²ΡΠΏΠΎΠ»Π½Π΅Π½ΠΈΠ΅ΠΌ ΠΌΠΎΠ½ΡΠ°ΠΆΠ½ΡΡ ΡΠ°Π±ΠΎΡ Π»Π΅ΠΏΠ½ΠΈΠ½Π° ΠΏΠΎΠ΄Π²Π΅ΡΠ³Π°Π΅ΡΡΡ ΠΎΠ±ΡΠ°Π±ΠΎΡΠΊΠ΅ Π²ΠΎΠ΄ΠΎΠΉ Π΄Π»Ρ ΠΏΡΠΎΠΏΠΈΡΡΠ²Π°Π½ΠΈΡ. ΠΠ΅Π»ΠΊΠΈΠ΅ ΡΠ°ΡΡΠΈ ΠΎΠΏΡΡΠΊΠ°ΡΡ Π² Π΅ΠΌΠΊΠΎΡΡΡ Ρ Π²ΠΎΠ΄ΠΎΠΉ, Π° ΠΊΡΡΠΏΠ½ΡΠ΅ β ΡΠΌΠ°ΡΠΈΠ²Π°ΡΡ Ρ Π΄Π²ΡΡ ΡΡΠΎΡΠΎΠ½ ΠΏΡΠΈ ΠΏΠΎΠΌΠΎΡΠΈ ΠΊΠΈΡΡΠΈ Π»ΠΈΠ±ΠΎ ΠΏΡΠ»ΡΠ²Π΅ΡΠΈΠ·Π°ΡΠΎΡΠ°. ΠΠ°Π»Π΅Π΅ Π½Π΅ΠΎΠ±Ρ ΠΎΠ΄ΠΈΠΌΠΎ ΡΠΌΠΎΡΠΈΡΡ ΠΏΠΎΠ²Π΅ΡΡ Π½ΠΎΡΡΡ ΡΡΠ΅Π½, Π½Π° ΠΊΠΎΡΠΎΡΡΠ΅ Π±ΡΠ΄Π΅Ρ ΠΏΡΠΎΠΈΠ·Π²ΠΎΠ΄ΠΈΡΡΡ ΠΌΠΎΠ½ΡΠ°ΠΆΠ° Π»Π΅ΠΏΠ½ΠΈΠ½Ρ (ΡΠΌ. ΡΠ»Π΅ΠΌΠ΅Π½Ρ ΠΊΠ°ΡΠ½ΠΈΠ·Ρ ΠΈΠ· Π³ΠΈΠΏΡΠ°).
ΠΠΎΡΠ»Π΅ ΡΠΌΠ°ΡΠΈΠ²Π°Π½ΠΈΡ Π²ΠΎΠ΄ΠΎΠΉ Π»Π΅ΠΏΠ½ΠΈΠ½Ρ ΠΈ ΠΏΠΎΠ²Π΅ΡΡ
Π½ΠΎΡΡΠΈ ΡΡΠ΅Π½, Π½Π°ΡΠΈΠ½Π°Π΅ΡΡΡ ΠΏΡΠΎΡΠ΅ΡΡ ΠΏΠΎΠ΄Π³ΠΎΡΠΎΠ²ΠΊΠΈ Π³ΠΈΠΏΡΠΎΠ²ΠΎΠ³ΠΎ ΡΠ°ΡΡΠ²ΠΎΡΠ°. ΠΠΈΠΏΡΠΎΠ²ΡΠΉ ΡΠ°ΡΡΠ²ΠΎΡ ΡΠΎΡΡΠΎΠΈΡ ΠΈΠ· Π³ΠΈΠΏΡΠ°, ΠΏΡΡΠ°ΡΠ° ΠΈ ΠΠΠ ΠΊΠ»Π΅Ρ. ΠΠΈΠΏΡΠΎΠ²ΡΠΉ ΡΠ°ΡΡΠ²ΠΎΡ Π΄ΠΎΠ»ΠΆΠ΅Π½ ΠΏΡΠ΅Π΄ΡΡΠ°Π²Π»ΡΡΡ ΡΠΎΠ±ΠΎΠΉ ΠΎΠ΄Π½ΠΎΡΠΎΠ΄Π½ΡΡ ΠΌΠ°ΡΡΡ, ΠΈΡΠΊΠ»ΡΡΠ°ΡΡΡΡ Π½Π°Π»ΠΈΡΠΈΡ ΠΊΠΎΠΌΠΊΠΎΠ², ΠΊΠΎΠ½ΡΠΈΡΡΠ΅Π½ΡΠΈΡ ΡΠ°ΡΡΠ²ΠΎΡΠ° Π΄ΠΎΠ»ΠΆΠ½Π° Π½Π°ΠΏΠΎΠΌΠΈΠ½Π°ΡΡ ΡΠΌΠ΅ΡΠ°Π½Ρ. Π’ΠΎΠ»ΡΠΊΠΎ ΡΠΎΠ±Π»ΡΠ΄Π΅Π½ΠΈΠ΅ Π΄Π°Π½Π½ΡΡ
Π½ΠΎΡΠΌ, ΠΏΠΎΠ·Π²ΠΎΠ»ΠΈΡ Π΄ΠΎΠ±ΠΈΡΡΡΡ Π½Π΅ΠΎΠ±Ρ
ΠΎΠ΄ΠΈΠΌΠΎΠ³ΠΎ ΡΡΠ΅ΠΏΠ»Π΅Π½ΠΈΡ Π»Π΅ΠΏΠ½ΠΈΠ½Ρ ΡΠΎ ΡΡΠ΅Π½ΠΎΠΉ, ΠΈ ΠΏΡΠ΅Π΄ΠΎΡΠ²ΡΠ°ΡΠ΅Π½ΠΈΠ΅ ΡΡΠ΅ΠΊΠ°Π½ΠΈΡ Π΅Π³ΠΎ Ρ Π½Π°ΠΊΠ»ΠΎΠ½Π½ΡΡ
Β ΠΈ Π³ΠΎΡΠΈΠ·ΠΎΠ½ΡΠ°Π»ΡΠ½ΡΡ
ΠΏΠΎΠ²Π΅ΡΡ
Π½ΠΎΡΡΠ΅ΠΉ.
ΠΠ° Π΄Π΅ΡΠ°Π»Ρ ΡΠ°ΡΡΠ²ΠΎΡ Π½Π°Π½ΠΎΡΠΈΡΡΡ Ρ ΠΏΠΎΠΌΠΎΡΡΡ ΡΠΏΠ΅ΡΠΈΠ°Π»ΡΠ½ΠΎΠΉ Π»ΠΎΠΏΠ°ΡΠΊΠΈ, Π»ΠΈΠ±ΠΎ ΡΠΏΠ°ΡΠ΅Π»Ρ, ΠΏΠΎΡΠ»Π΅ ΡΡΠΎΠ³ΠΎ Π΄Π΅ΡΠ°Π»Ρ ΠΊΡΠ΅ΠΏΠΊΠΎ ΠΏΡΠΈΠΆΠΈΠΌΠ°Π΅ΡΡΡ ΠΊ ΠΏΠΎΠ²Π΅ΡΡ Π½ΠΎΡΡΠΈ ΠΈ ΠΏΡΠΈΡΠΈΡΠ°Π΅ΡΡΡ. ΠΡΠΈΡΠΈΡΠΊΠ° ΠΏΡΠΎΠΈΠ·Π²ΠΎΠ΄ΠΈΡΡΡ ΡΠ»Π΅Π΄ΡΡΡΠΈΠΌ ΠΎΠ±ΡΠ°Π·ΠΎΠΌ β Π΄Π΅ΡΠ°Π»Ρ ΠΏΠ»ΠΎΡΠ½ΠΎ ΠΏΡΠΈΠΆΠΈΠΌΠ°Π΅ΡΡΡ ΠΊ ΡΡΠ΅Π½Π΅ ΠΈ Π΄Π²ΠΈΠ³Π°Π΅ΡΡΡ ΠΏΡΠΈΠΆΠΈΠΌΠ°Ρ ΠΈΠ· ΡΡΠΎΡΠΎΠ½Ρ Π² ΡΡΠΎΡΠΎΠ½Ρ Π½Π° Π½Π΅ΡΠΊΠΎΠ»ΡΠΊΠΎ ΠΌΠΈΠ»Π»ΠΈΠΌΠ΅ΡΡΠΎΠ². Π‘ ΠΏΠΎΠΌΠΎΡΡΡ ΠΏΡΠΈΡΠΈΡΠΊΠΈ ΡΠ΄Π°Π»ΡΡΡΡΡ ΠΈΠ·Π»ΠΈΡΠΊΠΈ ΡΠ°ΡΡΠ²ΠΎΡΠ° ΠΈΠ· ΠΏΠΎΠ΄ Π΄Π΅ΡΠ°Π»ΠΈ.Β ΠΠ·Π»ΠΈΡΠΊΠΈ ΡΠ±ΠΈΡΠ°ΡΡΡΡ ΡΠΏΠ°ΡΠ΅Π»Π΅ΠΌ, ΠΈΠ»ΠΈ ΡΡΡΠΏΠΊΠΎΠΉ, Π° ΡΠ΅Π»ΡΠ΅ΡΠ½ΡΠ΅ ΠΌΠ΅ΡΡΠ° ΠΎΠ±ΡΠ°Π±Π°ΡΡΠ²Π°ΡΡΡΡ ΠΊΠΈΡΡΠΎΡΠΊΠΎΠΉ.
ΠΠ»Ρ ΠΌΠΎΠ½ΡΠ°ΠΆΠ° Π»Π΅ΠΏΠ½ΠΈΠ½Ρ ΠΊ ΠΏΠΎΡΠΎΠ»ΠΊΠ°ΠΌ, ΠΈΠ»ΠΈ ΠΌΠΎΠ½ΡΠ°ΠΆΠ° ΡΡΠΆΠ΅Π»ΡΡ ΡΠ»Π΅ΠΌΠ΅Π½ΡΠΎΠ² Π»Π΅ΠΏΠ½ΠΈΠ½Ρ ΠΏΡΠΈΠΌΠ΅Π½ΡΡΡΡΡ Π΄ΠΎΠΏΠΎΠ»Π½ΠΈΡΠ΅Π»ΡΠ½ΡΠ΅ ΠΊΡΠ΅ΠΏΠ΅ΠΆΠ½ΡΠ΅ ΡΠ»Π΅ΠΌΠ΅Π½ΡΡ.
ΠΡΠΎΠΈΠ·Π²ΠΎΠ΄ΡΡΠ²ΠΎ Π³ΠΈΠΏΡΠΎΠ²ΠΎΠΉ Π»Π΅ΠΏΠ½ΠΈΠ½Ρ, ΠΈΠ·Π³ΠΎΡΠΎΠ²Π»Π΅Π½ΠΈΠ΅ Π»Π΅ΠΏΠ½ΠΈΠ½Ρ ΠΈΠ· Π³ΠΈΠΏΡΠ°
ΠΡ ΠΈΠΌΠ΅Π΅ΠΌ ΡΠΎΠ±ΡΡΠ²Π΅Π½Π½ΠΎΠ΅ ΠΏΡΠΎΠΈΠ·Π²ΠΎΠ΄ΡΡΠ²ΠΎ Π³ΠΈΠΏΡΠΎΠ²ΠΎΠΉ Π»Π΅ΠΏΠ½ΠΈΠ½Ρ
ΠΠ΄Π½ΠΈΠΌ ΠΈΠ· ΡΠ°ΡΠΏΡΠΎΡΡΡΠ°Π½Π΅Π½Π½ΡΡ
Π²Π°ΡΠΈΠ°Π½ΡΠΎΠ² Π΄Π΅ΠΊΠΎΡΠΈΡΠΎΠ²Π°Π½ΠΈΡ Π²Π½ΡΡΡΠ΅Π½Π½Π΅Π³ΠΎ ΠΏΡΠΎΡΡΡΠ°Π½ΡΡΠ²Π° ΠΏΠΎΠΌΠ΅ΡΠ΅Π½ΠΈΡ ΡΠ²Π»ΡΠ΅ΡΡΡ ΠΎΡΠ΄Π΅Π»ΠΊΠ° Π»Π΅ΠΏΠ½ΠΈΠ½ΠΎΠΉ ΠΈΠ· Π³ΠΈΠΏΡΠ°. ΠΠ·Π΄Π°Π²Π½Π° ΡΠ»Π΅ΠΌΠ΅Π½ΡΡ Π»Π΅ΠΏΠ½ΠΎΠ³ΠΎ Π΄Π΅ΠΊΠΎΡΠ° Π² ΠΏΠΎΠΌΠ΅ΡΠ΅Π½ΠΈΠΈ ΡΡΠΈΡΠ°ΡΡΡΡ ΠΏΡΠΈΠ·Π½Π°ΠΊΠΎΠΌ ΡΠΎΡΠΊΠΎΡΠΈ, Π±ΠΎΠ³Π°ΡΡΡΠ²Π°, ΡΠΊΡΠΊΠ»ΡΠ·ΠΈΠ²Π½ΠΎΡΡΠΈ ΠΈ ΠΎΡΠ»ΠΈΡΠ½ΠΎΠ³ΠΎ Π²ΠΊΡΡΠ°. ΠΡΡΠΎΡΠΈΡΠ΅ΡΠΊΠΈ ΡΠ΅Π»ΡΠ΅ΡΠ½ΡΡ Π»Π΅ΠΏΠ½ΠΈΠ½Ρ ΠΈΠ· Π³ΠΈΠΏΡΠ° ΠΈΡΠΏΠΎΠ»ΡΠ·ΠΎΠ²Π°Π»ΠΈ Π΄Π»Ρ Π΄Π΅ΠΊΠΎΡΠΈΡΠΎΠ²Π°Π½ΠΈΡ ΠΎΠΊΠΎΠ½Π½ΡΡ
ΠΈ Π΄Π²Π΅ΡΠ½ΡΡ
ΠΏΡΠΎΠ΅ΠΌΠΎΠ², ΡΡΠ΅Π½ ΠΈ ΠΏΠΎΡΠΎΠ»ΠΊΠΎΠ², Π²ΡΡΡΠΎΠ΅Π½Π½ΡΡ
Π½ΠΈΡ ΠΈ Π΄ΡΡΠ³ΠΈΡ
ΡΠ»Π΅ΠΌΠ΅Π½ΡΠΎΠ² ΡΠΎΡΠΊΠΎΡΠ½ΡΡ
ΠΎΡΠΎΠ±Π½ΡΠΊΠΎΠ² ΠΈ ΠΈΠΌΠ΅Π½ΠΈΠΉ. Π‘ΠΎΠ²ΡΠ΅ΠΌΠ΅Π½Π½ΡΠ΅ ΠΆΠ΅ ΡΠ΅Ρ
Π½ΠΎΠ»ΠΎΠ³ΠΈΠΈ ΠΈΠ·Π³ΠΎΡΠΎΠ²Π»Π΅Π½ΠΈΡ Π»Π΅ΠΏΠ½ΠΈΠ½Ρ ΠΈΠ· Π³ΠΈΠΏΡΠ° ΠΎΠ±Π΅ΡΠΏΠ΅ΡΠΈΠ²Π°ΡΡ Π΅Π΅ Π΄ΠΎΡΡΡΠΏΠ½ΠΎΡΡΡ Π΄Π»Ρ Π»ΡΠ±ΠΎΠ³ΠΎ ΠΏΠΎΠΊΡΠΏΠ°ΡΠ΅Π»Ρ.
Π£Π½ΠΈΠΊΠ°Π»ΡΠ½ΡΠ΅ ΡΠ²ΠΎΠΉΡΡΠ²Π° Π»Π΅ΠΏΠ½ΠΎΠ³ΠΎ Π΄Π΅ΠΊΠΎΡΠ°
ΠΠ΅ΠΊΠΎΡΠ°ΡΠΈΠ²Π½ΡΠ΅ Π»Π΅ΠΏΠ½ΡΠ΅ ΡΠ»Π΅ΠΌΠ΅Π½ΡΡ ΠΈΠ· Π³ΠΈΠΏΡΠ° ΠΎΡΠ»ΠΈΡΠ°ΡΡΡΡ Π½Π΅ ΡΠΎΠ»ΡΠΊΠΎ ΠΊΡΠ°ΡΠΎΡΠΎΠΉ, ΡΡΡΠ΅ΡΠΈΠΊΠΎΠΉ ΠΈ ΠΈΠ·ΡΡΠΊΠ°Π½Π½ΠΎΡΡΡΡ, Π½ΠΎ ΠΈ ΠΏΡΠ°ΠΊΡΠΈΡΠ½ΠΎΡΡΡΡ. Π‘ ΠΎΠ΄Π½ΠΎΠΉ ΡΡΠΎΡΠΎΠ½Ρ ΠΏΡΠ°Π²ΠΈΠ»ΡΠ½ΠΎ ΠΏΠΎΠ΄ΠΎΠ±ΡΠ°Π½Π½ΡΠΉ Π»Π΅ΠΏΠ½ΠΎΠΉ Π΄Π΅ΠΊΠΎΡ ΠΏΠΎΠ΄ΡΠ΅ΡΠΊΠ½Π΅Ρ ΠΎΡΠΎΠ±Π΅Π½Π½ΠΎΡΡΠΈ ΠΈ Π΄ΠΎΡΡΠΎΠΈΠ½ΡΡΠ²Π° ΠΈΠ½ΡΠ΅ΡΡΠ΅ΡΠ° ΠΏΠΎΠΌΠ΅ΡΠ΅Π½ΠΈΡ, Π° Ρ Π΄ΡΡΠ³ΠΎΠΉ β ΠΏΠΎΠ·Π²ΠΎΠ»ΠΈΡ ΡΠΊΡΡΡΡ Π½Π΅Π΄ΠΎΡΡΠ°ΡΠΊΠΈ ΠΈΠ»ΠΈ ΠΎΡΠΈΠ±ΠΊΠΈ ΠΏΡΠΈ ΡΡΡΠΎΠΈΡΠ΅Π»ΡΡΡΠ²Π΅ ΠΈ ΠΎΡΠ΄Π΅Π»ΠΊΠ΅ ΠΊΠΎΠΌΠ½Π°ΡΡ, Π° ΡΠ°ΠΊΠΆΠ΅ Π½Π΅ ΡΡΡΠ΅ΡΠΈΡΠ½ΡΠ΅ ΡΠ»Π΅ΠΌΠ΅Π½ΡΡ ΡΠΈΡΡΠ΅ΠΌ ΡΠ΅ΠΏΠ»ΠΎ- ΠΈ Π²ΠΎΠ΄ΠΎΡΠ½Π°Π±ΠΆΠ΅Π½ΠΈΡ (Π½Π°ΠΏΡΠΈΠΌΠ΅Ρ, ΡΠ΅Π»ΠΈ, ΡΡΡΠΊΠΈ, ΡΡΡΠ±Ρ, Π±Π°ΡΠ°ΡΠ΅ΠΈ, Π²Π΅Π½ΡΠΈΠ»ΡΡΠΈΠΎΠ½Π½ΡΠ΅ ΡΠ΅ΡΠ΅ΡΠΊΠΈ ΠΈ Ρ.Π΄.). ΠΡΠΎΠΌΠ΅ ΡΠΎΠ³ΠΎ, ΠΌΠ°ΡΡΠΈΠ²Π½ΡΠ΅ ΡΠ»Π΅ΠΌΠ΅Π½ΡΡ Π»Π΅ΠΏΠ½ΠΎΠ³ΠΎ Π΄Π΅ΠΊΠΎΡΠ° (Π½Π°ΠΏΡΠΈΠΌΠ΅Ρ, ΠΊΠΎΠ»ΠΎΠ½Π½Ρ) ΠΏΠΎΠΌΠΎΠ³ΡΡ ΡΠ°Π·Π΄Π΅Π»ΠΈΡΡ ΠΏΠΎΠΌΠ΅ΡΠ΅Π½ΠΈΡ Π½Π° Π½Π΅ΡΠΊΠΎΠ»ΡΠΊΠΎ ΡΡΠ½ΠΊΡΠΈΠΎΠ½Π°Π»ΡΠ½ΡΡ
Π·ΠΎΠ½, Π²ΠΈΠ·ΡΠ°Π»ΡΠ½ΠΎ ΡΠ²Π΅Π»ΠΈΡΠΈΡΡ, ΡΠ°ΡΡΠΈΡΠΈΡΡ ΠΈΠ»ΠΈ ΡΡΠ·ΠΈΡΡ Π²Π½ΡΡΡΠ΅Π½Π½Π΅Π΅ ΠΏΡΠΎΡΡΡΠ°Π½ΡΡΠ²ΠΎ, ΡΠ΄Π΅Π»Π°ΡΡ Π΅Π³ΠΎ Π±ΠΎΠ»Π΅Π΅ ΠΎΠ±ΡΠ΅ΠΌΠ½ΡΠΌ ΠΈ ΡΠ΅Π»ΡΠ΅ΡΠ½ΡΠΌ.
Β
Π‘ΠΎΠ²ΡΠ΅ΠΌΠ΅Π½Π½ΡΠΉ Π°ΡΡΠΎΡΡΠΈΠΌΠ΅Π½Ρ Π»Π΅ΠΏΠ½ΡΡ Π΄Π΅ΠΊΠΎΡΠ°ΡΠΈΠ²Π½ΡΡ ΡΠ»Π΅ΠΌΠ΅Π½ΡΠΎΠ² ΠΏΠΎΠ·Π²ΠΎΠ»ΡΠ΅Ρ ΠΈΡΠΏΠΎΠ»ΡΠ·ΠΎΠ²Π°ΡΡ ΠΈΡ Π΄Π»Ρ Π΄ΠΈΠ·Π°ΠΉΠ½Π΅ΡΡΠΊΠΎΠ³ΠΎ ΠΎΡΠΎΡΠΌΠ»Π΅Π½ΠΈΡ ΡΡΠ΅Π½, ΡΠ³Π»ΠΎΠ², ΠΏΠΎΡΠΎΠ»ΠΊΠΎΠ², Π²Π½ΡΡΡΠ΅Π½Π½ΠΈΡ Π΄Π²Π΅ΡΠ½ΡΡ ΠΈ ΠΎΠΊΠΎΠ½Π½ΡΡ ΠΏΡΠΎΠ΅ΠΌΠΎΠ², ΠΎΡΠ΄Π΅Π»ΡΠ½ΡΡ Π½ΠΈΡ ΠΈ ΠΏΡΡΡΡΡΡΠ΅Π³ΠΎ ΠΏΡΠΎΡΡΡΠ°Π½ΡΡΠ²Π°, Π΄ΠΎΠΏΠΎΠ»Π½ΠΈΡΠ΅Π»ΡΠ½ΠΎΠ³ΠΎ ΡΠΊΡΠ°ΡΠ΅Π½ΠΈΡ ΡΠ»Π΅ΠΌΠ΅Π½ΡΠΎΠ² ΠΎΡΠ²Π΅ΡΠΈΡΠ΅Π»ΡΠ½ΠΎΠΉ ΡΠΈΡΡΠ΅ΠΌΡ (ΡΠΎΠ·Π΅ΡΠΊΠΈ, ΠΏΠ»Π°ΡΠΎΠ½Ρ, Π»ΡΡΡΡΡ, Π²ΡΠΊΠ»ΡΡΠ°ΡΠ΅Π»ΠΈ ΠΈ Ρ.Π΄.). ΠΡΡΠΎΠΊΠΎΠΉ ΠΏΠΎΠΏΡΠ»ΡΡΠ½ΠΎΡΡΡΡ Π² ΡΡΠ΅ΡΠ΅ Π΄ΠΈΠ·Π°ΠΉΠ½Π° ΠΈΠ½ΡΠ΅ΡΡΠ΅ΡΠ° Π»Π΅ΠΏΠ½ΠΎΠΉ Π΄Π΅ΠΊΠΎΡ ΠΈΠ· Π³ΠΈΠΏΡΠ° ΠΏΠΎΠ»ΡΠ·ΡΠ΅ΡΡΡ Π±Π»Π°Π³ΠΎΠ΄Π°ΡΡ ΡΠ»Π΅Π΄ΡΡΡΠΈΠΌ ΠΎΡΠ½ΠΎΠ²Π½ΡΠΌ ΡΠ°ΠΊΡΠΎΡΠ°ΠΌ:
- ΠΠΊΠΎΠ»ΠΎΠ³ΠΈΡΠ΅ΡΠΊΠ°Ρ ΡΠΈΡΡΠΎΡΠ°. ΠΠΈΠΏΡ ΡΠ²Π»ΡΠ΅ΡΡΡ ΠΏΡΠΈΡΠΎΠ΄Π½ΡΠΌ ΠΌΠ°ΡΠ΅ΡΠΈΠ°Π»ΠΎΠΌ, ΡΠΎΠΎΡΠ²Π΅ΡΡΡΠ²Π΅Π½Π½ΠΎ Π½Π΅ ΡΠΎΠ΄Π΅ΡΠΆΠΈΡ ΡΠΎΠΊΡΠΈΡΠ½ΡΡ ΠΈ Π°Π»Π»Π΅ΡΠ³ΠΈΡΠ΅ΡΠΊΠΈΡ ΡΠΎΠ΅Π΄ΠΈΠ½Π΅Π½ΠΈΠΉ, ΠΊΠ°ΠΊ, Π½Π°ΠΏΡΠΈΠΌΠ΅Ρ, ΡΠΈΠ½ΡΠ΅ΡΠΈΡΠ΅ΡΠΊΠΈΠΉ Π΄Π΅ΠΊΠΎΡ. ΠΠ»Π°Π³ΠΎΠ΄Π°ΡΡ ΠΏΡΠΈΡΠΎΠ΄Π½ΠΎΠΌΡ Ρ ΠΈΠΌΠΈΡΠ΅ΡΠΊΠΎΠΌΡ ΡΠΎΡΡΠ°Π²Ρ Π³ΠΈΠΏΡ ΠΏΡΠΎΠΏΡΡΠΊΠ°Π΅Ρ Π²ΠΎΠ·Π΄ΡΡ ΠΈ Π²Π»Π°Π³Ρ, ΠΎΠ±Π΅ΡΠΏΠ΅ΡΠΈΠ²Π°Ρ ΡΠ΅ΠΌ ΡΠ°ΠΌΡΠΌ Π΅ΡΡΠ΅ΡΡΠ²Π΅Π½Π½ΡΡ Π²Π΅Π½ΡΠΈΠ»ΡΡΠΈΡ, ΡΡΠΎ ΠΏΠΎΠ·ΠΈΡΠΈΠ²Π½ΠΎ ΡΠΊΠ°Π·ΡΠ²Π°Π΅ΡΡΡ Π½Π° ΠΏΡΠΈΡ ΠΎΠ»ΠΎΠ³ΠΈΡΠ΅ΡΠΊΠΎΠΌ ΠΈ ΡΠΈΠ·ΠΈΡΠ΅ΡΠΊΠΎΠΌ ΡΠΎΡΡΠΎΡΠ½ΠΈΠΈ ΡΠ΅Π»ΠΎΠ²Π΅ΠΊΠ°.
- ΠΠΎΠ»Π³ΠΎΠ²Π΅ΡΠ½ΠΎΡΡΡ. ΠΠ΅ΠΏΠ½ΠΈΠ½Π° ΠΈΠ· Π³ΠΈΠΏΡΠ° ΠΏΡΠ°ΠΊΡΠΈΡΠ΅ΡΠΊΠΈ Π½Π΅ ΠΏΠΎΠ΄Π²Π΅ΡΠΆΠ΅Π½Π° ΠΈΠ·Π½ΠΎΡΡ, Π° ΠΏΡΠΈ ΠΏΡΠ°Π²ΠΈΠ»ΡΠ½ΠΎΠΌ ΡΡ
ΠΎΠ΄Π΅ ΠΈ ΡΠ²ΠΎΠ΅Π²ΡΠ΅ΠΌΠ΅Π½Π½ΠΎΠΉ ΡΠ΅ΡΡΠ°Π²ΡΠ°ΡΠΈΠΈ ΠΏΡΠΎΡΠ»ΡΠΆΠΈΡ Π΄ΠΎ ΡΠΎΡΠ½ΠΈ Π»Π΅Ρ.
ΠΠΈΠΏΡΠΎΠ²ΡΠΉ Π»Π΅ΠΏΠ½ΠΎΠΉ Π΄Π΅ΠΊΠΎΡ ΠΏΡΠ΅ΠΊΡΠ°ΡΠ½ΠΎ ΠΏΠ΅ΡΠ΅Π½ΠΎΡΠΈΡ ΠΈΠ·ΠΌΠ΅Π½Π΅Π½ΠΈΡ ΡΠ΅ΠΌΠΏΠ΅ΡΠ°ΡΡΡΡ, ΠΏΡΠ°ΠΊΡΠΈΡΠ΅ΡΠΊΠΈ Π½Π΅ ΡΠ΅ΡΡΠ΅Ρ ΠΏΡΠΎΡΠ½ΠΎΡΡΡ ΠΈ Π½Π΅ Π΄Π°Π΅Ρ ΡΡΠ°Π΄ΠΊΠΈ ΡΠΎΡΡΠ°Π²Π°.
- ΠΠΈΠ·ΠΊΠΈΠΉ ΡΡΠΎΠ²Π΅Π½Ρ ΠΏΠΎΠΆΠ°ΡΠΎΠΎΠΏΠ°ΡΠ½ΠΎΡΡΠΈ. ΠΠ»Π°Π³ΠΎΠ΄Π°ΡΡ ΡΠ²ΠΎΠ΅ΠΌΡ Ρ ΠΈΠΌΠΈΡΠ΅ΡΠΊΠΎΠΌΡ ΡΠΎΡΡΠ°Π²Ρ ΠΈ ΠΎΡΠ½ΠΎΡΠΈΡΠ΅Π»ΡΠ½ΠΎ ΠΏΠΎΠ»ΠΎΠΉ ΡΡΡΡΠΊΡΡΡΠ΅ Π³ΠΈΠΏΡ ΠΏΡΠ°ΠΊΡΠΈΡΠ΅ΡΠΊΠΈ Π½Π΅ ΠΏΡΠΎΠ²ΠΎΠ΄ΠΈΡ ΡΠ΅ΠΏΠ»ΠΎ, Π° ΡΠΎΠΎΡΠ²Π΅ΡΡΡΠ²Π΅Π½Π½ΠΎ β Π½Π΅ Π³ΠΎΡΠΈΡ.
- ΠΠΈΠ·Π°ΠΉΠ½Π΅ΡΡΠΊΠ°Ρ Π²Π°ΡΠΈΠ°ΡΠΈΠ²Π½ΠΎΡΡΡ. ΠΠΈΠΏΡΠΎΠ²ΡΠ΅ Π΄Π΅ΠΊΠΎΡΠ°ΡΠΈΠ²Π½ΡΠ΅ ΠΈΠ·Π΄Π΅Π»ΠΈΡ β ΠΎΠ³ΡΠΎΠΌΠ½ΠΎΠ΅ ΠΏΠΎΠ»Π΅ Π΄Π»Ρ ΡΠ²ΠΎΡΡΠ΅ΡΡΠ²Π°, Π²Π΅Π΄Ρ Π»Π΅ΠΏΠ½ΠΎΠΉ Π΄Π΅ΠΊΠΎΡ ΠΌΠΎΠΆΠ΅Ρ ΠΈΠΌΠ΅ΡΡ Π°Π±ΡΠΎΠ»ΡΡΠ½ΠΎ Π»ΡΠ±ΠΎΠΉ ΡΠ°Π·ΠΌΠ΅Ρ ΠΈ ΡΠΎΡΠΌΡ, Π΄Π°ΠΆΠ΅ ΡΠ°ΠΌΡΡ ΠΏΡΠΈΡΡΠ΄Π»ΠΈΠ²ΡΡ (ΠΎΡ ΠΏΡΠ°Π²ΠΈΠ»ΡΠ½ΡΡ Π³Π΅ΠΎΠΌΠ΅ΡΡΠΈΡΠ΅ΡΠΊΠΈΡ ΡΠΈΠ³ΡΡ Π΄ΠΎ Π²ΠΈΠ½ΠΎΠ³ΡΠ°Π΄Π½ΡΡ Π»ΠΎΠ·, ΠΌΠΎΡΡΠΊΠΈΡ ΡΠ°ΠΊΠΎΠ²ΠΈΠ½, ΡΠΎΠ³ΠΎΠ² ΠΈΠ·ΠΎΠ±ΠΈΠ»ΠΈΡ ΠΈ Ρ.Π΄.). ΠΡΠΈ ΡΡΠΎΠΌ Β«ΠΎΠΆΠΈΠ²ΠΈΡΡΒ», ΠΏΡΠΈΠ΄Π°ΡΡ ΡΡΠΊΠΈΡ ΠΎΡΡΠ΅Π½ΠΊΠΎΠ² Π»Π΅ΠΏΠ½ΠΈΠ½Π΅ ΠΎΡΠ΅Π½Ρ Π»Π΅Π³ΠΊΠΎ Ρ ΠΏΠΎΠΌΠΎΡΡΡ Π»Π°ΠΊΠΎΠΊΡΠ°ΡΠΎΡΠ½ΡΡ ΠΌΠ°ΡΠ΅ΡΠΈΠ°Π»ΠΎΠ², ΡΠ΅Ρ Π½ΠΎΠ»ΠΎΠ³ΠΈΠΈ Π·ΠΎΠ»ΠΎΡΠ΅Π½ΠΈΡ ΠΈ Ρ.Π΄.
Π ΡΠ΅ΡΠ΅Π½ΠΈΠ΅ ΠΌΠ½ΠΎΠ³ΠΈΡ
ΡΡΠΎΠ»Π΅ΡΠΈΠΉ ΠΈΡΠΏΠΎΠ»ΡΠ·ΠΎΠ²Π°Π½ΠΈΡ Π΄Π΅ΠΊΠΎΡΠ°ΡΠΈΠ²Π½ΡΠ΅ Π³ΠΈΠΏΡΠΎΠ²ΡΠ΅ Π»Π΅ΠΏΠ½ΡΠ΅ ΡΠ»Π΅ΠΌΠ΅Π½ΡΡ Π·Π°ΡΠ΅ΠΊΠΎΠΌΠ΅Π½Π΄ΠΎΠ²Π°Π»ΠΈ ΡΠ΅Π±Ρ ΠΊΠ°ΠΊ Π½Π°Π΄Π΅ΠΆΠ½ΠΎΠ΅, ΠΎΡΠΈΠ³ΠΈΠ½Π°Π»ΡΠ½ΠΎΠ΅ ΠΈ ΡΠ»Π΅Π³Π°Π½ΡΠ½ΠΎΠ΅ Π΄ΠΈΠ·Π°ΠΉΠ½Π΅ΡΡΠΊΠΎΠ΅ ΡΠΊΡΠ°ΡΠ΅Π½ΠΈΠ΅ ΠΏΠΎΠΌΠ΅ΡΠ΅Π½ΠΈΡ. ΠΠ°ΠΊ ΠΏΡΠ°Π²ΠΈΠ»ΠΎ, Π΄Π΅ΠΊΠΎΡΠ°ΡΠΈΠ²Π½Π°Ρ Π»Π΅ΠΏΠ½ΠΈΠ½Π° ΠΈΠ· Π³ΠΈΠΏΡΠ° ΠΈΡΠΏΠΎΠ»ΡΠ·ΡΠ΅ΡΡΡ Π΄Π»Ρ ΡΠΊΡΠ°ΡΠ΅Π½ΠΈΡ ΠΈΠ½ΡΠ΅ΡΡΠ΅ΡΠΎΠ² Π² ΠΊΠ»Π°ΡΡΠΈΡΠ΅ΡΠΊΠΎΠΌ ΡΡΠΈΠ»Π΅. ΠΡΠΈ ΡΡΠΎΠΌ Π΄Π΅ΠΊΠΎΡΠ°ΡΠΈΠ²Π½Π°Ρ Π»Π΅ΠΏΠ½ΠΈΠ½Π° ΠΏΠΎΠ·Π²ΠΎΠ»ΡΠ΅Ρ ΡΠΎΠ·Π΄Π°Π²Π°ΡΡ Π²ΠΏΠ΅ΡΠ°ΡΠ»Π΅Π½ΠΈΠ΅ ΡΡΠΈΠ»ΠΈΠ·Π°ΡΠΈΠΈ ΠΏΠΎΠΌΠ΅ΡΠ΅Π½ΠΈΡ ΠΏΠΎΠ΄ ΠΈΡΡΠΎΡΠΈΡΠ΅ΡΠΊΠΈΠ΅ ΡΠΏΠΎΡ
ΠΈ, ΠΏΡΠΈΠ½ΠΎΡΡ Π²ΠΎ Π²Π½ΡΡΡΠ΅Π½Π½Π΅Π΅ ΠΏΡΠΎΡΡΡΠ°Π½ΡΡΠ²ΠΎ ΡΡΠ²ΡΡΠ²ΠΎ Π³Π°ΡΠΌΠΎΠ½ΠΈΠΈ, ΠΈΠ·ΡΡΠΊΠ°Π½Π½ΠΎΡΡΠΈ, Π±ΠΎΠ³Π°ΡΡΡΠ²Π°. ΠΠ΄Π½Π°ΠΊΠΎ, ΡΠ΅ΠΉΡΠ°Ρ ΠΌΠ½ΠΎΠ³ΠΈΠ΅ Π΄ΠΈΠ·Π°ΠΉΠ½Π΅ΡΡ ΠΈΡΠΏΠΎΠ»ΡΠ·ΡΡΡ Π»Π΅ΠΏΠ½ΡΠ΅ Π³ΠΈΠΏΡΠΎΠ²ΡΠ΅ ΡΠ»Π΅ΠΌΠ΅Π½ΡΡ ΠΏΡΠΈ ΠΎΡΠΎΡΠΌΠ»Π΅Π½ΠΈΠΈ ΠΏΠΎΠΌΠ΅ΡΠ΅Π½ΠΈΡ Π² ΡΡΠΈΠ»ΡΡ
, ΠΌΠΎΠ΄Π΅ΡΠ½, Ρ
Π°ΠΉ-ΡΠ΅ΠΊ, ΠΌΠΈΠ½ΠΈΠΌΠ°Π»ΠΈΠ·ΠΌ, Π°ΡΡ-Π΄Π΅ΠΊΠΎ, ΠΏΠΎΠΏ-Π°ΡΡ, Π° ΡΠ°ΠΊΠΆΠ΅ ΠΈΡ
ΠΊΠΎΠΌΠ±ΠΈΠ½ΠΈΡΠΎΠ²Π°Π½ΠΈΡ, ΡΡΠΎ ΠΏΡΠΈΠ΄Π°Π΅Ρ ΠΏΡΠΎΡΡΡΠ°Π½ΡΡΠ²Ρ ΠΎΡΠΈΠ³ΠΈΠ½Π°Π»ΡΠ½ΠΎΡΡΡ, ΡΠΊΡΡΡΠ°Π²Π°Π³Π°Π½ΡΠ½ΠΎΡΡΡ, Π½Π΅ΠΎΡΠ΄ΠΈΠ½Π°ΡΠ½ΠΎΡΡΡ.
ΠΡΠ°ΠΏΡ ΠΈΠ·Π³ΠΎΡΠΎΠ²Π»Π΅Π½ΠΈΡ Π³ΠΈΠΏΡΠΎΠ²ΠΎΠΉ Π»Π΅ΠΏΠ½ΠΈΠ½Ρ
ΠΠΈΠ·Π°ΠΉΠ½ ΠΏΡΠΎΠ΅ΠΊΡ
ΠΏΠ΅ΡΠ΅ΠΏΠ»Π°Π½ΠΈΡΠΎΠ²ΠΊΠ°, Π²ΠΈΠ·ΡΠ°Π»ΠΈΠ·Π°ΡΠΈΡ Π² 3D, ΡΠΏΠΈΡΠΎΠΊ Π³ΠΈΠΏΡΠΎΠ²ΡΡ ΠΈΠ·Π΄Π΅Π»ΠΈΠΉ, Π½Π°ΡΠΈΠ½Π°Ρ ΠΎΡ ΠΊΠΎΠ»ΠΎΠ½Π½ ΠΈ Π·Π°ΠΊΠ°Π½ΡΠΈΠ²Π°Ρ ΡΡΠΈΠ·Π°ΠΌΠΈ. ΠΠΈΠ·Π°ΠΉΠ½ Π»Π΅ΠΏΠ½ΠΈΠ½Ρ Π² ΠΈΠ½ΡΠ΅ΡΡΠ΅ΡΠ΅.
Π₯ΡΠ΄ΠΎΠΆΠ΅ΡΡΠ²Π΅Π½Π½ΡΠ΅ ΡΠ°Π±ΠΎΡΡ
Π΅ΡΠ»ΠΈ Π²ΠΎΠ·Π½ΠΈΠΊΠ½Π΅Ρ ΠΆΠ΅Π»Π°Π½ΠΈΠ΅ Β«ΠΎΠΆΠΈΠ²ΠΈΡΡΒ» Π»Π΅ΠΏΠ½ΠΈΠ½Ρ ΠΊΡΠ°ΡΠΊΠ°ΠΌΠΈ, Π½Π°ΡΠΈ Ρ ΡΠ΄ΠΎΠΆΠ½ΠΈΠΊΠΈ Π²ΡΠΏΠΎΠ»Π½ΡΡ Π΄Π΅ΠΊΠΎΡΠ°ΡΠΈΠ²Π½ΡΠ΅ ΡΠΎΡΠΏΠΈΡΠΈ ΠΈΠ»ΠΈ Π²Π΅Π½Π΅ΡΠΈΠ°Π½ΡΠΊΡΡ ΡΡΡΠΊΠ°ΡΡΡΠΊΡ.
Β
Π’Π΅Ρ Π½ΠΎΠ»ΠΎΠ³ΠΈΡ ΠΏΡΠΎΠΈΠ·Π²ΠΎΠ΄ΡΡΠ²Π° Π»Π΅ΠΏΠ½ΡΡ Π΄Π΅ΠΊΠΎΡΠ°ΡΠΈΠ²Π½ΡΡ ΡΠ»Π΅ΠΌΠ΅Π½ΡΠΎΠ²
ΠΠ° ΡΠΎΠ²ΡΠ΅ΠΌΠ΅Π½Π½ΠΎΠΌ ΡΡΠ½ΠΊΠ΅ Π΄Π΅ΠΊΠΎΡΠ° Π³ΠΈΠΏΡΠΎΠ²Π°Ρ Π»Π΅ΠΏΠ½ΠΈΠ½Π°, ΠΊΠ°ΠΊ ΠΏΡΠ°Π²ΠΈΠ»ΠΎ, ΠΏΡΠ΅Π΄ΡΡΠ°Π²Π»ΡΠ΅Ρ ΡΠΎΠ±ΠΎΠΉ Π°ΡΡ
ΠΈΡΠ΅ΠΊΡΡΡΠ½ΡΠ΅ ΡΠΎΡΠΌΡ ΡΠ»Π΅Π΄ΡΡΡΠ΅Π³ΠΎ Π²ΠΈΠ΄Π°: ΠΊΠ°ΡΠ½ΠΈΠ·Ρ, ΡΡΠ³ΠΈ, ΡΠΎΠ·Π΅ΡΠΊΠΈ, ΡΠ³Π»Ρ, ΠΌΠΎΠ»Π΄ΠΈΠ½Π³ΠΈ, ΡΡΠΈΠ·Ρ, ΠΊΠ°ΠΌΠΈΠ½Ρ, ΠΊΡΠΎΠ½ΡΡΠ΅ΠΉΠ½Ρ, Π°ΡΠΊΠΈ, ΠΊΠ°ΠΏΠΈΡΠ΅Π»ΠΈ, ΠΏΠΈΠ»ΡΡΡΡΡ, ΠΊΠΎΠ»ΠΎΠ½Π½Ρ, ΠΎΡΠ½Π°ΠΌΠ΅Π½ΡΡ ΠΈ Π΄Ρ. Π’Π΅Ρ
Π½ΠΎΠ»ΠΎΠ³ΠΈΡ ΠΏΡΠΎΠΈΠ·Π²ΠΎΠ΄ΡΡΠ²Π° Π΄Π°Π½Π½ΠΎΠ³ΠΎ Π»Π΅ΠΏΠ½ΠΎΠ³ΠΎ Π΄Π΅ΠΊΠΎΡΠ° ΠΏΡΠ΅Π΄ΠΏΠΎΠ»Π°Π³Π°Π΅Ρ ΡΠ»Π΅Π΄ΡΡΡΠΈΠ΅ ΡΡΠ°Π½Π΄Π°ΡΡΠ½ΡΠ΅ ΡΡΠ°ΠΏΡ ΡΠ°Π±ΠΎΡΡ:
- ΡΠ°Π·ΡΠ°Π±ΠΎΡΠΊΠ° ΠΌΠΎΠ΄Π΅Π»ΠΈ Π±ΡΠ΄ΡΡΠ΅Π³ΠΎ Π΄Π΅ΠΊΠΎΡΠ°ΡΠΈΠ²Π½ΠΎΠ³ΠΎ ΡΠ»Π΅ΠΌΠ΅Π½ΡΠ° Π² ΡΡΠ΅Ρ ΠΌΠ΅ΡΠ½ΠΎΠΉ Π³ΡΠ°ΡΠΈΠΊΠ΅;
- Π»Π΅ΠΏΠΊΠ° ΠΏΡΠΎΠ΅ΠΊΡΠ½ΠΎΠΉ ΠΌΠΎΠ΄Π΅Π»ΠΈ ΠΈΠ· ΠΏΠ»Π°ΡΡΠΈΠ»ΠΈΠ½Π°;
- ΠΏΡΠΎΠΈΠ·Π²ΠΎΠ΄ΡΡΠ²ΠΎ (Π½Π° ΠΎΡΠ½ΠΎΠ²Π΅ ΠΏΡΠΎΠ΅ΠΊΡΠ½ΠΎΠΉ ΠΌΠΎΠ΄Π΅Π»ΠΈ) ΡΠΎΡΠΌΡ Π΄Π»Ρ ΠΎΡΠ»ΠΈΠ²Π° Π΄Π΅ΠΊΠΎΡΠ°ΡΠΈΠ²Π½ΠΎΠ³ΠΎ ΡΠ»Π΅ΠΌΠ΅Π½ΡΠ°;
- ΠΎΡΠ»ΠΈΠ² Π΄Π΅ΠΊΠΎΡΠ°ΡΠΈΠ²Π½ΠΎΠ³ΠΎ ΡΠ»Π΅ΠΌΠ΅Π½ΡΠ°.
ΠΡΠΊΠ»ΡΡΠ΅Π½ΠΈΠ΅ΠΌ ΠΈΠ· Π΄Π°Π½Π½ΠΎΠΉ ΠΏΠΎΡΠ»Π΅Π΄ΠΎΠ²Π°ΡΠ΅Π»ΡΠ½ΠΎΡΡΠΈ ΠΏΡΠΎΠΈΠ·Π²ΠΎΠ΄ΡΡΠ²Π° Π»Π΅ΠΏΠ½ΠΈΠ½Ρ ΡΠ²Π»ΡΠ΅ΡΡΡ Π»Π΅ΠΏΠ½ΠΎΠΉ Π΄Π΅ΠΊΠΎΡ ΡΡΡΠ½ΠΎΠΉ ΡΠ°Π±ΠΎΡΡ. Π ΡΡΠ½ΡΠ΅ Π»Π΅ΠΏΠ½ΡΠ΅ ΡΠ»Π΅ΠΌΠ΅Π½ΡΡ Π²ΡΠΏΠΎΠ»Π½ΡΡΡΡΡ Π½Π΅ΠΏΠΎΡΡΠ΅Π΄ΡΡΠ²Π΅Π½Π½ΠΎ Π½Π° Π΄Π΅ΠΊΠΎΡΠΈΡΡΠ΅ΠΌΠΎΠΉ ΠΏΠΎΠ²Π΅ΡΡ Π½ΠΎΡΡΠΈ Ρ ΠΈΡΠΏΠΎΠ»ΡΠ·ΠΎΠ²Π°Π½ΠΈΠ΅ΠΌ ΡΠ΅Ρ Π½ΠΎΠ»ΠΎΠ³ΠΈΠΈ ΡΠ΅Π·ΡΠ±Ρ. ΠΠΎΠ»Π΅Π΅ ΠΌΠ°ΡΡΠΈΠ²Π½ΡΠ΅ ΠΈ Π΄ΡΡΠ³ΠΈΠ΅ ΡΡΠ°Π½Π΄Π°ΡΡΠ½ΡΠ΅ ΡΠ»Π΅ΠΌΠ΅Π½ΡΡ Π»Π΅ΠΏΠ½ΠΈΠ½Ρ ΠΎΡΠ»ΠΈΠ²Π°ΡΡΡΡ ΠΎΡΠ΄Π΅Π»ΡΠ½ΠΎ Π² ΡΠΏΠ΅ΡΠΈΠ°Π»ΡΠ½ΡΡ Π·Π°Π³ΠΎΡΠΎΠ²ΠΊΠ°Ρ (ΠΌΠ΅ΡΠ°Π»Π»ΠΈΡΠ΅ΡΠΊΠΈΠ΅ ΠΈΠ»ΠΈ ΡΠΈΠ»ΠΈΠΊΠΎΠ½ΠΎΠ²ΡΠ΅). ΠΠ΅ΠΏΠ½ΠΎΠΉ Π΄Π΅ΠΊΠΎΡ ΡΡΡΠ½ΠΎΠΉ ΡΠ°Π±ΠΎΡΡ ΠΈΠ·Π³ΠΎΡΠ°Π²Π»ΠΈΠ²Π°Π΅ΡΡΡ Π² ΠΎΡΠ½ΠΎΠ²Π½ΠΎΠΌ Π½Π° Π·Π°ΠΊΠ°Π·, Π° Π΅Π³ΠΎ ΡΠΎΡΠΌΠ°, ΡΠ°Π·ΠΌΠ΅Ρ, ΡΠ΅ΠΊΡΡΡΡΠ° ΠΈ Π΄ΡΡΠ³ΠΈΠ΅ Ρ Π°ΡΠ°ΠΊΡΠ΅ΡΠΈΡΡΠΈΠΊΠΈ Π·Π°Π²ΠΈΡΡΡ ΠΈΡΠΊΠ»ΡΡΠΈΡΠ΅Π»ΡΠ½ΠΎ ΠΎΡ ΠΏΠΎΠΆΠ΅Π»Π°Π½ΠΈΠΉ Π·Π°ΠΊΠ°Π·ΡΠΈΠΊΠ°.
ΠΠ°ΠΏΡΠΈΠΌΠ΅Ρ, Π»Π΅ΠΏΠ½ΡΠ΅ ΡΠ»Π΅ΠΌΠ΅Π½ΡΡ ΠΌΠΎΠ³ΡΡ Π±ΡΡΡ ΡΡΠΈΠ»ΠΈΠ·ΠΈΡΠΎΠ²Π°Π½Ρ ΠΏΠΎΠ΄ ΠΌΡΠ°ΠΌΠΎΡ, ΡΡΠ°ΡΠΈΠ½Ρ, ΠΏΠΎΠ²ΡΠΎΡΡΡΡ Π°Π±ΡΠΎΠ»ΡΡΠ½ΠΎ Π»ΡΠ±ΡΠ΅ ΡΠ°ΠΊΡΡΡΡ. Π Π»ΡΠ±ΠΎΠΌ Π²Π°ΡΠΈΠ°Π½ΡΠ΅ ΡΡΡΠ½Π°Ρ Π΄Π΅ΠΊΠΎΡΠ°ΡΠΈΠ²Π½Π°Ρ Π»Π΅ΠΏΠΊΠ° ΠΏΡΠΈΠ΄Π°ΡΡ ΡΠ»Π΅Π³Π°Π½ΡΠ½ΡΠΉ, ΡΠΎΡΠΊΠΎΡΠ½ΡΠΉ ΠΈ ΡΠ΅ΡΠΏΠ΅ΠΊΡΠ°Π±Π΅Π»ΡΠ½ΡΠΉ Π²ΠΈΠ΄, ΠΊΠ°ΠΊ Π²Π½Π΅ΡΠ½Π΅ΠΌΡ, ΡΠ°ΠΊ ΠΈ Π²Π½ΡΡΡΠ΅Π½Π½Π΅ΠΌΡ ΠΏΡΠΎΡΡΡΠ°Π½ΡΡΠ²Ρ ΠΏΠΎΠΌΠ΅ΡΠ΅Π½ΠΈΡ.
Π£ΡΡΠ°Π½ΠΎΠ²ΠΊΠ° Π»Π΅ΠΏΠ½ΠΈΠ½Ρ ΠΈΠ· Π³ΠΈΠΏΡΠ°
ΠΡΠΎΠ±Π΅Π½Π½ΠΎΡΡΠΈ ΡΠ΅Ρ Π½ΠΎΠ»ΠΎΠ³ΠΈΠΈ ΠΌΠΎΠ½ΡΠ°ΠΆΠ° Π΄Π΅ΠΊΠΎΡΠ°ΡΠΈΠ²Π½ΡΡ Π»Π΅ΠΏΠ½ΡΡ ΡΠ»Π΅ΠΌΠ΅Π½ΡΠΎΠ² ΠΎΠ±ΡΡΠ»Π°Π²Π»ΠΈΠ²Π°ΡΡΡΡ ΡΠΎΡΠΌΠΎΠΉ ΠΈ Π²Π΅ΡΠΎΠΌ ΠΏΠΎΡΠ»Π΅Π΄Π½ΠΈΡ :
- ΠΠ°Π»ΠΎΠ³Π°Π±Π°ΡΠΈΡΠ½ΡΠ΅ Π΄Π΅ΠΊΠΎΡΠ°ΡΠΈΠ²Π½ΡΠ΅ ΠΈΠ·Π΄Π΅Π»ΠΈΡ ΠΈΠ· Π³ΠΈΠΏΡΠ° β ΠΌΠΎΠ½ΡΠΈΡΡΡΡΡΡ ΠΏΡΠΈ ΠΏΠΎΠΌΠΎΡΠΈ ΠΊΠ»Π΅Π΅Π²ΡΡ ΠΎΡΠ½ΠΎΠ² (Π½Π°ΠΏΡΠΈΠΌΠ΅Ρ, ΠΊΠ»Π΅ΠΉ ΠΠΠ). ΠΡΠ΅Π΄Π²Π°ΡΠΈΡΠ΅Π»ΡΠ½ΠΎ Π΄ΠΎ Π½Π°Π½Π΅ΡΠ΅Π½ΠΈΡ ΠΊΠ»Π΅Ρ ΠΎΠ±ΡΠ°ΡΠ½Π°Ρ ΠΏΠΎΠ²Π΅ΡΡ Π½ΠΎΡΡΡ Π»Π΅ΠΏΠ½ΠΎΠ³ΠΎ ΡΠ»Π΅ΠΌΠ΅Π½ΡΠ° Π΄ΠΎΠ»ΠΆΠ½Π° Π±ΡΡΡ ΠΎΡΡΠ»ΠΈΡΠΎΠ²Π°Π½Π° Ρ ΠΏΠΎΠΌΠΎΡΡΡ Π½Π°ΠΆΠ΄Π°ΡΠ½ΠΎΠΉ Π±ΡΠΌΠ°Π³ΠΈ. Π’ΠΎΠ»ΡΠΊΠΎ ΠΏΠΎΡΠ»Π΅ ΡΠ»ΠΈΡΠΎΠ²ΠΊΠΈ Π½Π° ΠΎΠ±ΡΠ°ΡΠ½ΡΡ ΠΏΠΎΠ²Π΅ΡΡ Π½ΠΎΡΡΡ Π½Π°Π½ΠΎΡΡΡ ΠΊΠ»Π΅ΠΉ ΠΈ ΠΏΡΠΈΠΊΠ»Π°Π΄ΡΠ²Π°ΡΡ ΠΊ ΠΌΠ΅ΡΡΡ ΠΌΠΎΠ½ΡΠ°ΠΆΠ°, ΠΏΡΠΈΠ΄Π΅ΡΠΆΠΈΠ²Π°Ρ 2-3 ΠΌΠΈΠ½ΡΡΡ.
- ΠΡΡΠΏΠ½ΠΎΠ³Π°Π±Π°ΡΠΈΡΠ½ΡΠ΅ Π»Π΅ΠΏΠ½ΡΠ΅ ΠΈΠ·Π΄Π΅Π»ΠΈΡ β ΠΌΠΎΠ½ΡΠΈΡΡΡΡΡΡ Ρ ΠΈΡΠΏΠΎΠ»ΡΠ·ΠΎΠ²Π°Π½ΠΈΠ΅ΠΌ ΠΊΠ»Π΅Π΅Π²ΡΡ
ΡΠΌΠ΅ΡΠ΅ΠΉ (Π³ΠΎΡΠΎΠ²ΠΈΡΡΡ ΡΠΏΠ΅ΡΠΈΠ°Π»ΠΈΡΡΠ°ΠΌΠΈ Π½Π΅ΠΏΠΎΡΡΠ΅Π΄ΡΡΠ²Π΅Π½Π½ΠΎ ΠΏΠ΅ΡΠ΅Π΄ ΠΌΠΎΠ½ΡΠ°ΠΆΠΎΠΌ) ΠΈ ΠΎΡΠΈΠ½ΠΊΠΎΠ²Π°Π½Π½ΡΡ
ΡΡΡΡΠΏΠΎΠ² (ΠΏΡΠ΅Π΄ΠΎΡΠ²ΡΠ°ΡΠ°Π΅Ρ ΠΏΠΎΡΠ²Π»Π΅Π½ΠΈΠ΅ ΡΠΆΠ°Π²ΡΠΈΠ½Ρ). ΠΠ΅ΡΠ΅Π΄ ΠΌΠΎΠ½ΡΠ°ΠΆΠΎΠΌ Π³ΠΈΠΏΡΠΎΠ²ΠΎΠΉ Π»Π΅ΠΏΠ½ΠΈΠ½Ρ ΠΎΠ±ΡΠ°ΡΠ½Π°Ρ ΡΡΠΎΡΠΎΠ½Π° ΠΈΠ·Π΄Π΅Π»ΠΈΡ ΠΈ ΠΏΠΎΠ²Π΅ΡΡ
Π½ΠΎΡΡΡ, Π½Π° ΠΊΠΎΡΠΎΡΡΡ Π±ΡΠ΄Π΅Ρ ΠΏΡΠΎΠΈΠ·Π²ΠΎΠ΄ΠΈΡΡΡΡ ΠΊΡΠ΅ΠΏΠ΅ΠΆ Π΄ΠΎΠ»ΠΆΠ½Ρ Π±ΡΡΡ Π²Π»Π°ΠΆΠ½ΡΠΌΠΈ ΠΈ ΠΎΠ±ΡΠ°Π±ΠΎΡΠ°Π½Π½ΡΠΌΠΈ ΠΊΠ»Π΅Π΅ΠΌ ΠΠΠ. ΠΠΎΡΠ»Π΅ ΠΏΠΎΡΠ°Π΄ΠΊΠΈ Π΄Π΅ΠΊΠΎΡΠ°ΡΠΈΠ²Π½ΠΎΠ³ΠΎ ΡΠ»Π΅ΠΌΠ΅Π½ΡΠ° Π½Π° ΠΊΠ»Π΅ΠΉ ΠΎΡΡΡΠ΅ΡΡΠ²Π»ΡΠ΅ΡΡΡ Π΅Π³ΠΎ Π·Π°ΠΊΡΠ΅ΠΏΠ»Π΅Π½ΠΈΠ΅ Ρ ΠΏΠΎΠΌΠΎΡΡΡ ΠΎΡΠΈΠ½ΠΊΠΎΠ²Π°Π½Π½ΡΡ
ΡΡΡΡΠΏΠΎΠ², ΠΊΠ°ΠΆΠ΄ΡΠΉ ΠΈΠ· ΠΊΠΎΡΠΎΡΡΡ
Π²ΠΊΡΡΡΠΈΠ²Π°Π΅ΡΡΡ Π½Π° ΡΠ°ΡΡΡΠΎΡΠ½ΠΈΠΈ 20-25 ΡΠ°Π½ΡΠΈΠΌΠ΅ΡΡΠΎΠ².
- ΠΠΎΠ½ΡΠ°ΠΆ ΠΊΠΎΠ»ΠΎΠ½Π½ ΠΈ ΠΏΠΈΠ»ΡΡΡΡΠΎΠ² β Π½Π°ΠΈΠ±ΠΎΠ»Π΅Π΅ ΡΡΡΠ΄ΠΎΠ΅ΠΌΠΊΠΈΠΉ ΠΈ ΡΠ΅Ρ Π½ΠΎΠ»ΠΎΠ³ΠΈΡΠ΅ΡΠΊΠΈ ΡΠ»ΠΎΠΆΠ½ΡΠΉ ΠΏΡΠΎΡΠ΅ΡΡ, ΠΊΠΎΡΠΎΡΡΠΉ Π΄ΠΎΠ»ΠΆΠ½Ρ Π²ΡΠΏΠΎΠ»Π½ΡΡΡ ΠΌΠΈΠ½ΠΈΠΌΡΠΌ Π΄Π²Π° ΡΠΏΠ΅ΡΠΈΠ°Π»ΠΈΡΡΠ°-ΠΌΠΎΠ½ΡΠ°ΠΆΠ½ΠΈΠΊΠ°. ΠΠΎΠ½ΡΠΈΡΡΠ΅ΡΡΡ ΠΊΠΎΠ»ΠΎΠ½Π½Π° ΠΈΠ· Π΄Π²ΡΡ ΡΠ°ΡΡΠ΅ΠΉ, ΠΊΠΎΡΠΎΡΡΠ΅ ΡΠΊΠ»Π΅ΠΈΠ²Π°ΡΡΡΡ ΠΌΠ΅ΠΆΠ΄Ρ ΡΠΎΠ±ΠΎΠΉ ΠΌΠ°Π»ΡΡΠ½ΡΠΌ ΡΠΊΠΎΡΡΠ΅ΠΌ. ΠΠ°Π»Π΅Π΅ ΠΎΡΡΡΠ΅ΡΡΠ²Π»ΡΠ΅ΡΡΡ Π½Π°ΠΏΠΎΠ»Π½Π΅Π½ΠΈΠ΅ ΠΏΠΎΠ»ΠΎΡΡΠΈ Π³ΠΎΡΠΎΠ²ΠΎΠΉ ΠΊΠΎΠ»ΠΎΠ½Π½Ρ Π³ΠΈΠΏΡΠΎΠ²ΠΎΠΉ ΡΡΡΡΠΆΠΊΠΎΠΉ. ΠΠ°ΠΏΠΎΠ»Π½Π΅Π½ΠΈΠ΅ Π΄ΠΎΠ»ΠΆΠ½ΠΎ ΠΏΡΠΎΠΈΡΡ ΠΎΠ΄ΠΈΡΡ ΠΏΠΎΡΡΠ°ΠΏΠ½ΠΎ (ΡΡΠΎΠ²Π΅Π½Ρ Π½Π°ΠΏΠΎΠ»Π½Π΅Π½ΠΈΡ Π½Π΅ Π±ΠΎΠ»Π΅Π΅ 20ΡΠ°Π½ΡΠΈΠΌΠ΅ΡΡΠΎΠ² Π·Π° ΠΎΠ΄ΠΈΠ½ ΡΠ°Π·) Π΄Π»Ρ ΡΠΎΠ³ΠΎ ΡΡΠΎΠ±Ρ Π³ΠΈΠΏΡΠΎΠ²Π°Ρ ΠΊΠΎΠ½ΡΡΡΡΠΊΡΠΈΡ Π½Π΅ ΡΡΠ΅ΡΠ½ΡΠ»Π° ΠΈΠ»ΠΈ ΡΠ΄Π²ΠΈΠ½ΡΠ»Π°ΡΡ.
- ΠΠΊΠΎΠ½ΡΠ°ΡΠ΅Π»ΡΠ½ΡΡ ΠΎΡΠ΄Π΅Π»ΠΊΡ ΠΈ Π·Π°ΡΠΈΡΠΊΡ ΡΠ²ΠΎΠ² ΠΌΠΎΠΆΠ½ΠΎ ΠΎΡΡΡΠ΅ΡΡΠ²Π»ΡΡΡ ΡΠ΅ΡΠ΅Π· 2 ΡΡΡΠΎΠΊ ΠΏΠΎΡΠ»Π΅ ΠΎΡΠ½ΠΎΠ²Π½ΠΎΠ³ΠΎ ΡΡΠ°ΠΏΠ° ΠΌΠΎΠ½ΡΠ°ΠΆΠ°. ΠΡΠ»ΠΈ ΠΡ ΠΏΠ»Π°Π½ΠΈΡΡΠ΅ΡΠ΅ Π΄Π°Π»ΡΠ½Π΅ΠΉΡΠ΅Π΅ Π΄Π΅ΠΊΠΎΡΠΈΡΠΎΠ²Π°Π½ΠΈΠ΅ Π³ΠΈΠΏΡΠΎΠ²ΠΎΠΉ Π»Π΅ΠΏΠ½ΠΈΠ½Ρ, ΡΠΎ ΡΠ΅ΡΠ΅Π· ΡΡΡΠΊΠΈ ΠΏΠΎΡΠ»Π΅ ΠΌΠΎΠ½ΡΠ°ΠΆΠ°, ΠΈΠ·Π΄Π΅Π»ΠΈΡ Π½Π΅ΠΎΠ±Ρ ΠΎΠ΄ΠΈΠΌΠΎ ΠΎΠ±ΡΠ°Π±ΠΎΡΠ°ΡΡ ΡΠΏΠ΅ΡΠΈΠ°Π»ΡΠ½ΠΎΠΉ Π°ΠΊΡΠΈΠ»ΠΎΠ²ΠΎΠΉ Π³ΡΡΠ½ΡΠΎΠ²ΠΊΠΎΠΉ. ΠΠΊΡΠΈΠ»ΠΎΠ²Π°Ρ Π³ΡΡΠ½ΡΠΎΠ²ΠΊΠ° Π½Π΅ ΡΠΎΠ»ΡΠΊΠΎ ΠΎΠ±Π»Π΅Π³ΡΠΈΡ ΠΏΡΠΎΡΠ΅ΡΡ ΠΏΠΎΠΊΡΡΡΠΈΡ ΠΈΠ·Π΄Π΅Π»ΠΈΡ Π»Π°ΠΊΠΎΠΊΡΠ°ΡΠΎΡΠ½ΡΠΌΠΈ ΠΌΠ°ΡΠ΅ΡΠΈΠ°Π»Π°ΠΌΠΈ, Π½ΠΎ ΠΈ Π·Π°ΡΠΈΡΠΈΡ Π΅Π³ΠΎ ΠΎΡ ΠΏΠΎΠ²ΡΠ΅ΠΆΠ΄Π΅Π½ΠΈΠΉ.
ΠΠ΅ΠΊΠΎΡΠ°ΡΠΈΠ²Π½ΠΎΠ΅ ΠΎΡΠΎΡΠΌΠ»Π΅Π½ΠΈΠ΅ Π»Π΅ΠΏΠ½ΠΈΠ½Ρ
ΠΠ΅ΠΊΠΎΡΠ°ΡΠΈΠ²Π½Π°Ρ Π³ΠΈΠΏΡΠΎΠ²Π°Ρ Π»Π΅ΠΏΠ½ΠΈΠ½Π° ΡΠ°ΠΌΠ° ΠΏΠΎ ΡΠ΅Π±Π΅ ΠΎΡΠ΅Π½Ρ ΠΊΡΠ°ΡΠΈΠ²ΡΠΉ ΠΈ ΡΡΠ°ΡΡΡΠ½ΡΠΉ ΡΠ»Π΅ΠΌΠ΅Π½Ρ Π΄ΠΈΠ·Π°ΠΉΠ½Π° ΠΈΠ½ΡΠ΅ΡΡΠ΅ΡΠ°. ΠΠ΄Π½Π°ΠΊΠΎ ΡΠΎΠ²ΡΠ΅ΠΌΠ΅Π½Π½Π°Ρ ΡΡΠ΅ΡΠ° Ρ
ΡΠ΄ΠΎΠΆΠ΅ΡΡΠ²Π΅Π½Π½ΠΎΠ³ΠΎ ΠΎΡΠΎΡΠΌΠ»Π΅Π½ΠΈΡ ΠΏΠΎΠ·Π²ΠΎΠ»ΡΠ΅Ρ ΠΎΡΡΡΠ΅ΡΡΠ²Π»ΡΡΡ Π΄Π°Π»ΡΠ½Π΅ΠΉΡΠ΅Π΅ Π΄Π΅ΠΊΠΎΡΠΈΡΠΎΠ²Π°Π½ΠΈΠ΅ Π»Π΅ΠΏΠ½ΡΡ
Π³ΠΈΠΏΡΠΎΠ²ΡΡ
ΡΠ»Π΅ΠΌΠ΅Π½ΡΠΎΠ². Π₯ΡΠ΄ΠΎΠΆΠ΅ΡΡΠ²Π΅Π½Π½ΠΎΠ΅ Π΄Π΅ΠΊΠΎΡΠΈΡΠΎΠ²Π°Π½ΠΈΠ΅ Π³ΠΈΠΏΡΠΎΠ²ΠΎΠΉ Π»Π΅ΠΏΠ½ΠΈΠ½Ρ ΠΎΡΡΡΠ΅ΡΡΠ²Π»ΡΠ΅ΡΡΡ Ρ ΠΏΠΎΠΌΠΎΡΡΡ ΡΠ»Π΅Π΄ΡΡΡΠΈΡ
ΡΠ΅Ρ
Π½ΠΎΠ»ΠΎΠ³ΠΈΠΉ:
- Π’ΠΎΠ½ΠΈΡΠΎΠ²Π°Π½ΠΈΠ΅ β ΠΏΡΠ΅Π΄ΠΏΠΎΠ»Π°Π³Π°Π΅Ρ ΠΏΡΠΈΠ΄Π°Π½ΠΈΠ΅ ΠΎΠΏΡΠ΅Π΄Π΅Π»Π΅Π½Π½ΠΎΠ³ΠΎ ΠΎΡΡΠ΅Π½ΠΊΠ° Π»Π΅ΠΏΠ½ΠΈΠ½Π΅, ΠΊΠΎΡΠΎΡΡΠΉ Π±ΡΠ΄Π΅Ρ Π³Π°ΡΠΌΠΎΠ½ΠΈΡΠΎΠ²Π°ΡΡ Ρ ΠΎΠ±ΡΠΈΠΌ ΠΈΠ½ΡΠ΅ΡΡΠ΅ΡΠΎΠΌ.
- ΠΠ΄Π½ΠΎ- ΠΈ ΠΌΠ½ΠΎΠ³ΠΎΡΠ²Π΅ΡΠ½Π°Ρ ΠΏΠΎΠΊΡΠ°ΡΠΊΠ°, Π² ΡΠΎΠΌ ΡΠΈΡΠ»Π΅ Π·ΠΎΠ»ΠΎΡΠ΅Π½ΠΈΠ΅ ΠΈ ΡΠ΅ΡΠ΅Π±ΡΠ΅Π½ΠΈΠ΅, Π²Π΄ΠΎΡ Π½Π΅Ρ Β«ΠΆΠΈΠ·Π½ΡΒ» Π² Π»Π΅ΠΏΠ½ΠΎΠΉ Π΄Π΅ΠΊΠΎΡ. ΠΠΈΠΏΡΠΎΠ²Π°Ρ Π»Π΅ΠΏΠΊΠ° Π·Π°ΠΈΠ³ΡΠ°Π΅Ρ ΠΊΡΠ°ΡΠΎΡΠ½ΡΠΌΠΈ ΠΏΠ΅ΡΠ΅Π»ΠΈΠ²Π°ΠΌΠΈ ΠΈ Π·Π°Π³Π°Π΄ΠΎΡΠ½ΡΠΌΠΈ, ΠΏΡΠΈΠ²Π»Π΅ΠΊΠ°ΡΡΠΈΠΌΠΈ Π²Π½ΠΈΠΌΠ°Π½ΠΈΠ΅ ΠΎΡΡΠ΅Π½ΠΊΠ°ΠΌΠΈ.
- Π₯ΡΠ΄ΠΎΠΆΠ΅ΡΡΠ²Π΅Π½Π½Π°Ρ ΡΠΎΡΠΏΠΈΡΡ β ΡΠΌΠΎΡΡΠΈΡΡΡ Π½Π° Π³ΠΈΠΏΡΠΎΠ²ΠΎΠΉ Π»Π΅ΠΏΠ½ΠΈΠ½Π΅ ΠΎΡΠΎΠ±Π΅Π½Π½ΠΎ ΡΠ»Π΅Π³Π°Π½ΡΠ½ΠΎ. Π Π·Π°Π²ΠΈΡΠΈΠΌΠΎΡΡΠΈ ΠΎΡ ΡΠ΅ΠΌΠ°ΡΠΈΠΊΠΈ, Π² ΠΊΠΎΡΠΎΡΠΎΠΉ Π²ΡΠΏΠΎΠ»Π½Π΅Π½ Π»Π΅ΠΏΠ½ΠΎΠΉ Π΄Π΅ΠΊΠΎΡ ΠΈ ΠΎΠ±ΡΠ΅Π³ΠΎ ΠΈΠ½ΡΠ΅ΡΡΠ΅ΡΠ°, ΠΎΠ½ ΠΌΠΎΠΆΠ΅Ρ Π±ΡΡΡ ΡΠΊΡΠ°ΡΠ΅Π½ Π³Π΅ΠΎΠΌΠ΅ΡΡΠΈΡΠ΅ΡΠΊΠΈΠΌΠΈ ΡΠΈΠ³ΡΡΠ°ΠΌΠΈ, ΠΏΠ΅ΠΉΠ·Π°ΠΆΠ°ΠΌΠΈ, Π½Π°ΡΡΡΠΌΠΎΡΡΠ°ΠΌΠΈ ΠΈ Ρ.Π΄.
- ΠΡΠΊΡΡΡΡΠ²Π΅Π½Π½ΠΎΠ΅ ΠΏΡΠΈΠ΄Π°Π½ΠΈΠ΅ ΡΡΡΠ΅ΠΊΡΠ° Β«ΡΠΎΡΡΠ°ΡΠΈΠ²Π°Π½ΠΈΡΒ» β ΠΎΡΠ΅Π½Ρ ΡΡΡΠ΅ΠΊΡΠ½ΠΎ ΡΠΌΠΎΡΡΠΈΡΡΡ Π² ΠΊΠ»Π°ΡΡΠΈΡΠ΅ΡΠΊΠΎΠΌ ΠΎΡΠΎΡΠΌΠ»Π΅Π½ΠΈΠΈ ΠΏΠΎΠΌΠ΅ΡΠ΅Π½ΠΈΡ. ΠΠΈΠ·ΡΠ°Π»ΡΠ½ΠΎ ΠΏΠΎΡΠ΅ΡΡΡΠ΅ Π»Π΅ΠΏΠ½ΡΠ΅ ΡΠ»Π΅ΠΌΠ΅Π½ΡΡ ΠΏΡΠΈΠ΄Π°ΡΡ Π°ΡΠΈΡΡΠΎΠΊΡΠ°ΡΠΈΡΠ΅ΡΠΊΠΎΠ΅ Π±Π»Π°Π³ΠΎΡΠΎΠ΄ΡΡΠ²ΠΎ Π²Π½ΡΡΡΠ΅Π½Π½Π΅ΠΌΡ ΡΠ±ΡΠ°Π½ΡΡΠ²Ρ ΠΏΠΎΠΌΠ΅ΡΠ΅Π½ΠΈΡ.
- ΠΡΠΈΠ΄Π°Π½ΠΈΠ΅ Π·Π°Π΄Π°Π½Π½ΠΎΠΉ ΡΠ΅ΠΊΡΡΡΡΡ (ΠΌΡΠ°ΠΌΠΎΡ, ΠΊΠ°ΠΌΠ΅Π½Ρ, ΡΠ°ΡΡΠΎΡ, ΠΌΠ΅ΡΠ°Π»Π» ΠΈ Ρ.Π΄.) ΡΠ°ΠΊΠΆΠ΅ Π½Π°ΠΏΡΠ°Π²Π»Π΅Π½Π½ΠΎ Π½Π° Π³Π°ΡΠΌΠΎΠ½ΠΈΠ·Π°ΡΠΈΡ Π»Π΅ΠΏΠΊΠΈ Ρ ΠΎΠ±ΡΠΈΠΌ ΠΈΠ½ΡΠ΅ΡΡΠ΅ΡΠΎΠΌ.
- ΠΠ°ΠΏΡΠΈΠΌΠ΅Ρ, Π΅ΡΠ»ΠΈ Π² ΠΏΡΠΎΡΡΡΠ°Π½ΡΡΠ²Π΅ ΠΏΠΎΠΌΠ΅ΡΠ΅Π½ΠΈΡ ΠΏΡΠΈΡΡΡΡΡΠ²ΡΡΡ ΠΌΡΠ°ΠΌΠΎΡΠ½ΡΠ΅ ΡΠ»Π΅ΠΌΠ΅Π½ΡΡ, ΡΠΎ ΠΎΡΠ΄Π΅Π»ΠΊΠ° Π»Π΅ΠΏΠ½ΡΠΌ Π΄Π΅ΠΊΠΎΡΠΎΠΌ Ρ ΠΌΡΠ°ΠΌΠΎΡΠ½ΠΎΠΉ ΡΠ΅ΠΊΡΡΡΡΠΎΠΉ ΠΏΡΠΈΠ΄Π°ΡΡ Π·Π°ΠΊΠΎΠ½ΡΠ΅Π½Π½ΡΠΉ Π²Π½Π΅ΡΠ½ΠΈΠΉ Π²ΠΈΠ΄ ΡΡΠΈΠ»ΠΈΡΡΠΈΡΠ΅ΡΠΊΠΎΠΉ ΠΊΠΎΠ½ΡΠ΅ΠΏΡΠΈΠΈ.
ΠΠ³ΡΠΎΠΌΠ½ΠΎΠ΅ ΠΊΠΎΠ»ΠΈΡΠ΅ΡΡΠ²ΠΎ ΡΠΎΠ²ΡΠ΅ΠΌΠ΅Π½Π½ΡΡ Π»Π°ΠΊΠΎΠΊΡΠ°ΡΠΎΡΠ½ΡΡ ΡΡΠ΅Π΄ΡΡΠ² (Π»Π°ΠΊΠΈ, ΠΊΡΠ°ΡΠΊΠΈ, ΡΠΎΠ½Π΅ΡΡ, Π²ΠΎΡΠΊΠΈ ΠΈ Ρ.Π΄.) ΠΏΠΎΠ·Π²ΠΎΠ»ΡΠ΅Ρ Ρ ΡΠ΄ΠΎΠΆΠ½ΠΈΠΊΠ°ΠΌ ΠΈ ΠΌΠ°ΡΡΠ΅ΡΠ°ΠΌ Π΄Π΅ΠΊΠΎΡΠΈΡΠΎΠ²Π°ΡΡ ΠΊΠΎΠΌΠΏΠΎΠ·ΠΈΡΠΈΠΈ ΠΈΠ· ΡΠ»Π΅ΠΌΠ΅Π½ΡΠΎΠ² Π»Π΅ΠΏΠ½ΠΎΠ³ΠΎ Π΄Π΅ΠΊΠΎΡΠ° ΡΠ°Π·Π»ΠΈΡΠ½ΡΠΌΠΈ ΠΎΡΡΠ΅Π½ΠΊΠ°ΠΌΠΈ ΡΠ²Π΅ΡΠΎΠ² ΠΈ ΡΠ΅Ρ Π½ΠΈΠΊΠ°ΠΌΠΈ Π½Π°Π½Π΅ΡΠ΅Π½ΠΈΡ. ΠΡΠΎΠΌΠ΅ ΡΠΎΠ³ΠΎ, ΠΎΠΊΡΠ°ΡΠ΅Π½Π½ΡΠ΅ ΠΈΠ»ΠΈ Π·Π°ΡΠΎΠ½ΠΈΡΠΎΠ²Π°Π½Π½ΡΠ΅ Π»Π΅ΠΏΠ½ΡΠ΅ ΡΠ»Π΅ΠΌΠ΅Π½ΡΡ ΠΌΠΎΠ³ΡΡ ΠΈΠ·ΠΌΠ΅Π½ΡΡΡ ΠΎΡΡΠ΅Π½ΠΊΠΈ Π² Π·Π°Π²ΠΈΡΠΈΠΌΠΎΡΡΠΈ ΠΎΡ ΡΠ³Π»Π° ΠΎΡΠ²Π΅ΡΠ΅Π½ΠΈΡ Π² ΠΏΠΎΠΌΠ΅ΡΠ΅Π½ΠΈΠΈ, ΡΡΠΎ ΠΏΠΎΠ·Π²ΠΎΠ»ΡΠ΅Ρ ΡΠΎΠ·Π΄Π°Π²Π°ΡΡ ΠΏΠΎΠΈΡΡΠΈΠ½Π΅ ΡΠΊΡΠΊΠ»ΡΠ·ΠΈΠ²Π½ΡΠ΅ ΠΈΠ½ΡΠ΅ΡΡΠ΅ΡΡ, ΠΊΠΎΡΠΎΡΡΠ΅ ΠΎΡΡΠ°ΠΆΠ°ΡΡ Π°ΡΠΌΠΎΡΡΠ΅ΡΡ ΠΈ Π½Π°ΡΡΡΠΎΠ΅Π½ΠΈΠ΅ Π²Π»Π°Π΄Π΅Π»ΡΡΠ΅Π².
Π‘ΡΡΠ΄ΠΈΡ Π»Π΅ΠΏΠ½ΠΎΠ³ΠΎ Π΄Π΅ΠΊΠΎΡΠ° ΠΠ΅ΡΡΠΎΠ‘ΡΠ°Ρ ΠΏΡΠ΅Π΄Π»Π°Π³Π°Π΅Ρ ΠΊΠΎΠΌΠΏΠ»Π΅ΠΊΡ ΡΡΠ»ΡΠ³ ΠΏΠΎ ΠΈΠ·Π³ΠΎΡΠΎΠ²Π»Π΅Π½ΠΈΡ ΠΈ ΡΡΡΠ°Π½ΠΎΠ²ΠΊΠ΅ Π΄Π΅ΠΊΠΎΡΠ°ΡΠΈΠ²Π½ΡΡ
Π³ΠΈΠΏΡΠΎΠ²ΡΡ
Π»Π΅ΠΏΠ½ΡΡ
ΠΈΠ·Π΄Π΅Π»ΠΈΠΉ. Π Π°ΡΡΠΎΡΡΠΈΠΌΠ΅Π½ΡΠ΅ Π½Π°ΡΠ΅Π³ΠΎ ΠΊΠ°ΡΠ°Π»ΠΎΠ³Π° ΡΠ°Π±ΠΎΡ ΠΈΠΌΠ΅ΡΡΡΡ Π³ΠΎΡΠΎΠ²ΡΠ΅ Π΄Π΅ΠΊΠΎΡΠ°ΡΠΈΠ²Π½ΡΠ΅ Π»Π΅ΠΏΠ½ΡΠ΅ ΠΈΠ·Π΄Π΅Π»ΠΈΡ ΠΈΠ· Π³ΠΈΠΏΡΠ° (ΠΊΠ°ΡΠ½ΠΈΠ·Ρ, ΡΠΎΠ·Π΅ΡΠΊΠΈ, Π²Π΅Π½ΡΠΈΠ»ΡΡΠΈΠΎΠ½Π½ΡΠ΅ ΡΠ΅ΡΠ΅ΡΠΊΠΈ, ΠΊΠΎΠ»ΠΎΠ½Π½Ρ, ΡΠ³Π»Ρ ΠΈ Π΄Ρ. ). ΠΡΠΎΠΌΠ΅ ΡΠΎΠ³ΠΎ, Ρ Π½Π°Ρ ΠΡ ΠΌΠΎΠΆΠ΅ΡΠ΅ Π·Π°ΠΊΠ°Π·Π°ΡΡ Π΄Π΅ΠΊΠΎΡΠ°ΡΠΈΠ²Π½ΡΠ΅ ΠΏΠ°Π½Π½ΠΎ, ΡΠΊΡΠ°ΡΠ΅Π½ΠΈΡ Π΄Π»Ρ ΠΊΠ°ΠΌΠΈΠ½ΠΎΠ² ΠΈ Π΄ΡΡΠ³ΠΈΠ΅ Π»Π΅ΠΏΠ½ΡΠ΅ ΡΠ»Π΅ΠΌΠ΅Π½ΡΡ Π² Π°Π²ΡΠΎΡΡΠΊΠΎΠΌ ΠΈΡΠΏΠΎΠ»Π½Π΅Π½ΠΈΠΈ (ΡΡΠΊΠΈΠ·Ρ ΠΌΠΎΠ³ΡΡ Π±ΡΡΡ Π²ΡΠΏΠΎΠ»Π½Π΅Π½Ρ ΠΊΠ°ΠΊ ΡΠΏΠ΅ΡΠΈΠ°Π»ΠΈΡΡΠ°ΠΌΠΈ ΠΊΠΎΠΌΠΏΠ°Π½ΠΈΠΈ, ΡΠ°ΠΊ ΠΈ ΠΏΡΠΈΠ½Π°Π΄Π»Π΅ΠΆΠ°ΡΡ ΠΊΠ»ΠΈΠ΅Π½ΡΡ).
Π‘ΠΏΠ΅ΡΠΈΠ°Π»ΠΈΡΡΡ ΠΊΠΎΠΌΠΏΠ°Π½ΠΈΠΈ ΠΠ΅ΡΡΠΎΠ‘ΡΠ°Ρ Π·Π½Π°ΠΊΠΎΠΌΡ Ρ ΡΠ°Π·Π»ΠΈΡΠ½ΡΠΌΠΈ ΡΠ΅Ρ Π½ΠΈΠΊΠ°ΠΌΠΈ ΡΡΡΠ½ΠΎΠΉ Π»Π΅ΠΏΠΊΠΈ ΠΈ Π΄Π΅ΠΊΠΎΡΠΈΡΠΎΠ²Π°Π½ΠΈΡ, Π² ΡΠ²ΠΎΠ΅ΠΉ ΡΠ°Π±ΠΎΡΠ΅ ΠΏΡΠΈΠΌΠ΅Π½ΡΡΡ ΡΠ°Π·Π½ΠΎΠΎΠ±ΡΠ°Π·Π½ΡΠ΅ Π²ΠΈΠ΄Ρ ΡΠΏΠ°ΠΊΠ»Π΅Π²ΠΊΠΈ ΠΈ Π»Π°ΠΊΠΎΠΊΡΠ°ΡΠΎΡΠ½ΡΡ ΠΌΠ°ΡΠ΅ΡΠΈΠ°Π»ΠΎΠ². ΠΠ°ΡΠΈ ΠΏΡΠΎΡΠ΅ΡΡΠΈΠΎΠ½Π°Π»Ρ ΡΡΡΠ½ΠΎΠΉ Π»Π΅ΠΏΠΊΠΈ ΠΈΠ· Π³ΠΈΠΏΡΠ° ΠΎΡΠΎΡΠΌΡΡ ΡΠ°ΡΠ°Π΄ ΠΈ Π²Π½ΡΡΡΠ΅Π½Π½Π΅Π΅ ΠΏΡΠΎΡΡΡΠ°Π½ΡΡΠ²ΠΎ Π»ΡΠ±ΠΎΠ³ΠΎ ΠΏΠΎΠΌΠ΅ΡΠ΅Π½ΠΈΡ ΡΠΊΡΠΊΠ»ΡΠ·ΠΈΠ²Π½ΡΠΌΠΈ Π»Π΅ΠΏΠ½ΡΠΌΠΈ ΠΎΡΠ½Π°ΠΌΠ΅Π½ΡΠ°ΠΌΠΈ, ΠΏΡΠΈΠ²Π½ΠΎΡΡ Π½ΠΎΡΠΊΠΈ ΠΈΠ½Π΄ΠΈΠ²ΠΈΠ΄ΡΠ°Π»ΡΠ½ΠΎΡΡΠΈ ΠΈ ΠΈΠ·ΡΡΠΊΠ°Π½Π½ΠΎΡΡΠΈ.
Π‘ΡΡΠ΄ΠΈΡ ΠΠ΅ΡΡΠΎΠ‘ΡΠ°Ρ ΠΊΡΠΎΠΌΠ΅ ΠΈΠ·Π³ΠΎΡΠΎΠ²Π»Π΅Π½ΠΈΡ Π»Π΅ΠΏΠ½ΡΡ
Π΄Π΅ΠΊΠΎΡΠ°ΡΠΈΠ²Π½ΡΡ
ΡΠ»Π΅ΠΌΠ΅Π½ΡΠΎΠ² ΡΠ°ΠΊΠΆΠ΅ Π·Π°Π½ΠΈΠΌΠ°Π΅ΡΡΡ ΠΈΡ
ΠΌΠΎΠ½ΡΠ°ΠΆΠΎΠΌ. Π‘ΡΡΠΎΠΈΡΠ΅Π»ΠΈ ΠΈΠ· Π½Π°ΡΠ΅ΠΉ ΠΊΠΎΠΌΠΏΠ°Π½ΠΈΠΈ ΡΠΏΠ΅ΡΠΈΠ°Π»ΠΈΠ·ΠΈΡΡΡΡΡΡ Π½Π° ΠΌΠΎΠ½ΡΠ°ΠΆΠ΅ Π³ΠΈΠΏΡΠΎΠ²ΠΎΠΉ Π»Π΅ΠΏΠ½ΠΈΠ½Ρ, Π·Π½Π°ΠΊΠΎΠΌΡ ΡΠΎ Π²ΡΠ΅ΠΌΠΈ ΠΎΡΠΎΠ±Π΅Π½Π½ΠΎΡΡΡΠΌΠΈ Π΅Π΅ ΡΡΡΠ°Π½ΠΎΠ²ΠΊΠΈ ΠΈ ΠΏΠΎΠ΄Π³ΠΎΡΠΎΠ²ΠΊΠΈ ΠΏΠΎΠ²Π΅ΡΡ
Π½ΠΎΡΡΠΈ Π΄Π»Ρ ΠΊΡΠ΅ΠΏΠ΅ΠΆΠ° Π»Π΅ΠΏΠ½ΠΎΠ³ΠΎ Π΄Π΅ΠΊΠΎΡΠ°. ΠΠΈΡΡΠ΅ ΠΈ ΡΡΡΠ°Π½ΠΎΠ²ΠΊΠ° Π³ΠΈΠΏΡΠΎΠ²ΠΎΠΉ Π»Π΅ΠΏΠ½ΠΈΠ½Ρ Π±ΡΠ΅Π½Π΄Π° ΠΠ΅ΡΡΠΎΠ‘ΡΠ°Ρ ΠΎΡΡΡΠ΅ΡΡΠ²Π»ΡΠ΅ΡΡΡ ΠΌΠ°ΡΡΠ΅ΡΠ°ΠΌΠΈ Ρ ΠΌΠ½ΠΎΠ³ΠΎΠ»Π΅ΡΠ½ΠΈΠΌ ΡΡΠΏΠ΅ΡΠ½ΡΠΌ ΠΎΠΏΡΡΠΎΠΌ ΡΠ°Π±ΠΎΡΡ, ΡΡΠΎ Π³Π°ΡΠ°Π½ΡΠΈΡΡΠ΅Ρ Π²ΡΡΠΎΠΊΠΎΠ΅ ΠΊΠ°ΡΠ΅ΡΡΠ²ΠΎ Π³ΠΎΡΠΎΠ²ΠΎΠ³ΠΎ ΠΈΠ·Π΄Π΅Π»ΠΈΡ.
Π’Π°ΠΊΠΆΠ΅ ΠΊΠΎΠΌΠΏΠ°Π½ΠΈΡ ΠΠ΅ΡΡΠΎΠ‘ΡΠ°Ρ Π²ΡΠΏΠΎΠ»Π½ΡΠ΅Ρ ΡΠ°Π±ΠΎΡΡ ΠΏΠΎ Ρ ΡΠ΄ΠΎΠΆΠ΅ΡΡΠ²Π΅Π½Π½ΠΎΠΌΡ Π΄Π΅ΠΊΠΎΡΠΈΡΠΎΠ²Π°Π½ΠΈΡ Π³ΠΈΠΏΡΠΎΠ²ΠΎΠΉ Π»Π΅ΠΏΠ½ΠΈΠ½Ρ β ΡΠΎΠ½ΠΈΡΠΎΠ²Π°Π½ΠΈΠ΅, Π·ΠΎΠ»ΠΎΡΠ΅Π½ΠΈΠ΅, ΠΏΠΎΠΊΡΠ°ΡΠΊΠ°, ΠΈΡΠΊΡΡΡΡΠ²Π΅Π½Π½ΠΎΠ΅ ΡΠΎΡΡΠ°ΡΠΈΠ²Π°Π½ΠΈΠ΅, ΡΡΠΈΠ»ΠΈΠ·Π°ΡΠΈΡ ΠΏΠΎΠ΄ Π·Π°Π΄Π°Π½Π½ΡΡ ΡΠ΅ΠΊΡΡΡΡΡ ΠΈ Π΄Ρ. ΠΠ°ΡΠΈ ΡΠΏΠ΅ΡΠΈΠ°Π»ΠΈΡΡΡ ΠΏΠΎΠ΄Π±Π΅ΡΡΡ ΠΎΡΡΠ΅Π½ΠΊΠΈ ΠΈ ΡΡΡΡΠΊΡΡΡΡ Π»Π΅ΠΏΠ½ΠΎΠ³ΠΎ Π΄Π΅ΠΊΠΎΡΠ°, ΠΊΠΎΡΠΎΡΡΠ΅ ΠΈΠ΄Π΅Π°Π»ΡΠ½ΠΎ Π²ΠΏΠΈΡΡΡΡΡ Π² ΠΠ°Ρ ΠΈΠ½ΡΠ΅ΡΡΠ΅Ρ ΠΈ ΠΏΠΎΠ΄ΡΠ΅ΡΠΊΠ½ΡΡ Π΅Π³ΠΎ ΠΈΠ½Π΄ΠΈΠ²ΠΈΠ΄ΡΠ°Π»ΡΠ½ΠΎΡΡΡ ΠΈ ΡΠΎΡΠΊΠΎΡΠ½ΠΎΡΡΡ.
Π‘ΡΡΠ΄ΠΈΡ Π»Π΅ΠΏΠ½ΠΎΠ³ΠΎ Π΄Π΅ΠΊΠΎΡΠ° ΠΠ΅ΡΡΠΎΠ‘ΡΠ°Ρ ΠΏΡΠ΅Π΄Π»Π°Π³Π°Π΅Ρ ΠΠ°ΠΌ ΡΠΊΡΠΊΠ»ΡΠ·ΠΈΠ²Π½ΡΠ΅ ΠΈΠ΄Π΅ΠΈ Π΄Π»Ρ ΠΎΡΠΎΡΠΌΠ»Π΅Π½ΠΈΡ ΠΏΠΎΠΌΠ΅ΡΠ΅Π½ΠΈΠΉ Π½Π° ΠΎΡΠ½ΠΎΠ²Π΅ Π΄Π΅ΠΊΠΎΡΠΈΡΠΎΠ²Π°Π½ΠΈΡ ΡΠΎΡΠΊΠΎΡΠ½ΡΠΌΠΈ ΠΈ ΠΎΠ΄Π½ΠΎΠ²ΡΠ΅ΠΌΠ΅Π½Π½ΠΎ ΠΏΡΠ°ΠΊΡΠΈΡΠ½ΡΠΌΠΈ Π»Π΅ΠΏΠ½ΡΠΌΠΈ ΡΠ»Π΅ΠΌΠ΅Π½ΡΠ°ΠΌΠΈ ΠΈΠ· Π³ΠΈΠΏΡΠ°.
ΠΠ°ΡΠ΅ ΠΏΡΠ΅Π΄Π»ΠΎΠΆΠ΅Π½ΠΈΠ΅
- ΠΏΠΎΠ»Π½ΡΠΉ ΠΊΠΎΠΌΠΏΠ»Π΅ΠΊΡ ΡΠ°Π±ΠΎΡ ΠΏΠΎ ΡΠ°Π·ΡΠ°Π±ΠΎΡΠΊΠ΅,Β ΠΏΡΠΎΠΈΠ·Π²ΠΎΠ΄ΡΡΠ²Ρ ΠΈ ΠΌΠΎΠ½ΡΠ°ΠΆΡ Π³ΠΈΠΏΡΠΎΠ²ΡΡ ΡΠ»Π΅ΠΌΠ΅Π½ΡΠΎΠ²;
- Π°ΡΡ ΠΈΡΠ΅ΠΊΡΡΡΠ½ΡΠΉ Π»Π΅ΠΏΠ½ΠΎΠΉ Π³ΠΈΠΏΡΠΎΠ²ΡΠΉ Π΄Π΅ΠΊΠΎΡ Π΄Π»Ρ Π»ΡΠ±ΡΡ ΠΏΠΎΠΌΠ΅ΡΠ΅Π½ΠΈΠΉ;
- ΠΈΠ·Π³ΠΎΡΠΎΠ²Π»Π΅Π½ΠΈΠ΅Β Π»Π΅ΠΏΠ½ΠΈΠ½Ρ ΠΈΠ· Π³ΠΈΠΏΡΠ°Β ΠΏΠΎ ΠΊΠ°ΡΠ°Π»ΠΎΠ³Ρ Π½Π°ΡΠ΅ΠΉ ΠΊΠΎΠΌΠΏΠ°Π½ΠΈΠΈ, Π° ΡΠ°ΠΊΠΆΠ΅ ΠΏΠΎ ΡΡΠΊΠΈΠ·Π°ΠΌ Π·Π°ΠΊΠ°Π·ΡΠΈΠΊΠ°;
- Π² Π½Π°Π»ΠΈΡΠΈΠΈ Π°ΡΡΠΎΡΡΠΈΠΌΠ΅Π½ΡΒ Π³ΠΈΠΏΡΠΎΠ²ΡΡ Π»Π΅ΠΏΠ½ΡΡ Β ΠΊΠ°ΡΠ½ΠΈΠ·ΠΎΠ², ΠΈΠ·Π³ΠΎΡΠΎΠ²Π»Π΅Π½ΠΈΠ΅ ΠΊΠΎΠ»ΠΎΠ½Π½, ΠΏΠ°Π½Π½ΠΎ, Π±Π°Π»ΡΡΠΈΠ½, ΡΠΊΡΠ°ΡΠ΅Π½ΠΈΠ΅ ΠΊΠ°ΠΌΠΈΠ½ΠΎΠ², Π²Π΅Π½ΡΠΈΠ»ΡΡΠΈΠΎΠ½Π½ΡΡ ΡΠ΅ΡΠ΅ΡΠΎΠΊ, ΠΈ ΠΌΠ½ΠΎΠ³ΠΎΠ΅ Π΄ΡΡΠ³ΠΎΠ΅;
- Π΄Π΅ΠΊΠΎΡΠ°ΡΠΈΠ²Π½Π°ΡΒ ΠΏΠΎΠΊΡΠ°ΡΠΊΠ° Π»Π΅ΠΏΠ½ΠΈΠ½ΡΒ (ΠΏΠ°ΡΠΈΠ½Π°, Π·ΠΎΠ»ΠΎΡΠ΅Π½ΠΈΠ΅, ΠΈΠΌΠΈΡΠ°ΡΠΈΡ Β«ΠΏΠΎΠ΄ ΠΌΡΠ°ΠΌΠΎΡΒ», Β«ΠΏΠΎΠ΄ Π΄Π΅ΡΠ΅Π²ΠΎΒ») ΠΈ ΠΈΡΠΊΡΡΡΡΠ²Π΅Π½Π½ΠΎΠ΅ Β«ΡΡΠ°ΡΠ΅Π½ΠΈΠ΅Β» ΠΏΠΎΠ²Π΅ΡΡ Π½ΠΎΡΡΠΈ;
ΠΠ²Π°Π»ΠΈΡΠΈΡΠΈΡΠΎΠ²Π°Π½Π½ΡΠΉ Π΄ΠΈΠ·Π°ΠΉΠ½ ΠΈ ΠΌΠ°ΡΡΠ΅ΡΡΡΠ²ΠΎ Π»ΠΈΡΡΡ Π½Π° ΠΎΡΠ½ΠΎΠ²Π΅ ΠΌΠ½ΠΎΠ³ΠΎΠ»Π΅ΡΠ½Π΅Π³ΠΎ ΠΎΠΏΡΡΠ° ΠΏΠΎΠ·Π²ΠΎΠ»ΡΡΡ Π½Π°ΠΌ ΠΏΡΠΎΠΈΠ·Π²ΠΎΠ΄ΠΈΡΡ Π³ΠΈΠΏΡΠΎΠ²ΡΠ΅ ΡΠ»Π΅ΠΌΠ΅Π½ΡΡ, ΠΊΠΎΡΠΎΡΡΠ΅ ΠΏΡΠΎΡ
ΠΎΠ΄ΡΡ ΡΡΡΠΎΠ³ΠΈΠΉ ΠΊΠΎΠ½ΡΡΠΎΠ»Ρ ΠΊΠ°ΡΠ΅ΡΡΠ²Π° Π½Π° Π²ΡΠ΅Ρ
ΡΡΠ°ΠΏΠ°Ρ
ΠΈΠ·Π³ΠΎΡΠΎΠ²Π»Π΅Π½ΠΈΡ.
ΠΠ°ΡΠ° ΠΊΠΎΠΌΠΏΠ°Π½ΠΈΡ ΠΈΠΌΠ΅Π΅Ρ Π±ΠΎΠ»ΡΡΠΎΠΉ ΠΎΠΏΡΡ ΡΠ΅Π°Π»ΠΈΠ·Π°ΡΠΈΠΈ ΠΏΡΠΎΠ΅ΠΊΡΠΎΠ² Π»ΡΠ±ΠΎΠ³ΠΎ ΡΡΠΎΠ²Π½Ρ ΡΠ»ΠΎΠΆΠ½ΠΎΡΡΠΈ, ΡΡΠΎ ΠΏΠΎΠ·Π²ΠΎΠ»ΡΠ΅Ρ Π½Π°ΠΌ ΡΠΎΠΎΡΠ²Π΅ΡΡΡΠ²ΠΎΠ²Π°ΡΡ ΡΠ°ΠΌΡΠΌ Π²Π·ΡΡΠΊΠ°ΡΠ΅Π»ΡΠ½ΡΠΌ ΡΡΠ΅Π±ΠΎΠ²Π°Π½ΠΈΡΠΌ ΠΈ ΠΏΠΎΠΆΠ΅Π»Π°Π½ΠΈΡΠΌ Π·Π°ΠΊΠ°Π·ΡΠΈΠΊΠ°. Π£ΡΡΠ°Π½ΠΎΠ²ΠΊΠ°Β Π»Π΅ΠΏΠ½ΠΎΠ³ΠΎ Π³ΠΈΠΏΡΠΎΠ²ΠΎΠ³ΠΎ Π΄Π΅ΠΊΠΎΡΠ°Β Π²ΡΠΏΠΎΠ»Π½ΡΠ΅ΡΡΡ ΠΌΠ°ΡΡΠ΅ΡΠ°ΠΌΠΈ Ρ ΠΌΠ½ΠΎΠ³ΠΎΠ»Π΅ΡΠ½ΠΈΠΌ ΠΎΠΏΡΡΠΎΠΌ, Π³Π°ΡΠ°Π½ΡΠΈΡΡΡ Π²ΡΡΠΎΠΊΠΎΠ΅ ΠΊΠ°ΡΠ΅ΡΡΠ²ΠΎ ΠΈΡΠΏΠΎΠ»Π½Π΅Π½ΠΈΡ ΡΠ°Π±ΠΎΡ.
ΠΡΡΠ°Π»ΠΈΡΡ Π²ΠΎΠΏΡΠΎΡΡ? Π₯ΠΎΡΠΈΡΠ΅ ΡΠ΄Π΅Π»Π°ΡΡ Π·Π°ΠΊΠ°Π·?
Π’Π΅Ρ Π½ΠΎΠ»ΠΎΠ³ΠΈΡ ΠΏΡΠΎΠΈΠ·Π²ΠΎΠ΄ΡΡΠ²Π° Π³ΠΈΠΏΡΠΎΠ²ΠΎΠΉ Π»Π΅ΠΏΠ½ΠΈΠ½Ρ
Π ΡΠΎΠ²ΡΠ΅ΠΌΠ΅Π½Π½ΠΎΠΌ Π΄ΠΈΠ·Π°ΠΉΠ½Π΅ Π³ΠΈΠΏΡΠΎΠ²Π°Ρ Π»Π΅ΠΏΠ½ΠΈΠ½Π° Π²ΡΡΡΠ΅ΡΠ°Π΅ΡΡΡ ΡΠ°ΡΡΠΎ. ΠΠ°ΡΠ΅ΡΠΈΠ°Π» Π°ΠΊΡΠΈΠ²Π½ΠΎ ΠΈΡΠΏΠΎΠ»ΡΠ·ΡΡΡ Π΄Π»Ρ Π΄Π΅ΠΊΠΎΡΠ°ΡΠΈΠΈ ΠΏΠΎΠΌΠ΅ΡΠ΅Π½ΠΈΠΉ Π² ΡΠ°Π·Π½ΡΡ ΡΡΠΈΠ»ΡΡ . ΠΡΠΎΠΈΠ·Π²ΠΎΠ΄ΡΡ Π΄Π΅ΠΊΠΎΡΠ°ΡΠΈΠ²Π½ΡΠ΅ ΡΠ»Π΅ΠΌΠ΅Π½ΡΡ ΠΈΡΠΏΠΎΠ»ΡΠ·ΡΡ Π³ΠΈΠΏΡ, ΡΡΡΠΊΠ°ΡΡΡΠΊΡ, ΡΠ΅ΠΌΠ΅Π½Ρ, ΠΏΠΎΠ»ΠΈΡΡΠ΅ΡΠ°Π½, ΡΡΠ΅ΠΊΠ»ΠΎΠ²ΠΎΠ»ΠΎΠΊΠ½ΠΎ ΠΈ ΠΏΠ°ΠΏΡΠ΅-ΠΌΠ°ΡΠ΅. ΠΠΎ ΠΈΠ· Π²ΡΠ΅Π³ΠΎ ΡΡΠΎΠ³ΠΎ ΠΈΠ·ΠΎΠ±ΠΈΠ»ΠΈΡ ΡΠΎΠ»ΡΠΊΠΎ Π³ΠΈΠΏΡΠΎΠ²Π°Ρ Π»Π΅ΠΏΠ½ΠΈΠ½Π° ΠΈΠΌΠ΅Π΅Ρ ΠΌΠ°ΠΊΡΠΈΠΌΠ°Π»ΡΠ½ΠΎ ΠΏΡΠΈΡΠΎΠ΄Π½ΡΠΉ ΠΈ ΡΡΡΠ΅ΠΊΡΠ½ΡΠΉ Π²Π½Π΅ΡΠ½ΠΈΠΉ Π²ΠΈΠ΄. Π§Π΅ΠΌ Π³ΠΈΠΏΡ Π»ΡΡΡΠ΅ Π°Π½Π°Π»ΠΎΠ³ΠΎΠ² ΠΈ ΠΊΠ°ΠΊ Π΄Π΅Π»Π°ΡΡ Π³ΠΈΠΏΡΠΎΠ²ΡΡ Π»Π΅ΠΏΠ½ΠΈΠ½Ρ, Π΄Π°Π»Π΅Π΅ ΡΠ°ΡΡΠΌΠΎΡΡΠΈΠΌ Π±ΠΎΠ»Π΅Π΅ ΠΏΠΎΠ΄ΡΠΎΠ±Π½ΠΎ.
ΠΡΡΠΎΡΠΈΡ ΠΏΡΠΎΠΈΠ·Π²ΠΎΠ΄ΡΡΠ²Π° Π³ΠΈΠΏΡΠ°ΠΠ΅ΡΠ²ΡΠ΅ Π³ΠΈΠΏΡΠΎΠ²ΡΠ΅ ΡΠΊΡΠ°ΡΠ΅Π½ΠΈΡ ΠΏΠΎΡΠ²ΠΈΠ»ΠΈΡΡ Π² ΠΡΠ΅Π²Π½Π΅ΠΌ ΠΠ³ΠΈΠΏΡΠ΅ Π΅ΡΡ Π²3700 Π³ΠΎΠ΄Ρ Π΄ΠΎ Π½Π°ΡΠ΅ΠΉ ΡΡΡ. Π ΠΠ²ΡΠΎΠΏΠ΅ ΠΌΠ°ΡΠ΅ΡΠΈΠ°Π» Π½Π°ΡΠ°Π»ΠΈ ΠΏΡΠΈΠΌΠ΅Π½ΡΡΡ Π½Π°ΠΌΠ½ΠΎΠ³ΠΎ ΠΏΠΎΠ·ΠΆΠ΅, Π½Π°ΡΠΈΠ½Π°Ρ Ρ 15 Π²Π΅ΠΊΠ°. Π’ΠΎΠ³Π΄Π° Π³ΠΈΠΏΡ Π²ΠΏΠ΅ΡΠ²ΡΠ΅ Π½Π°ΡΠ°Π»ΠΈ ΠΈΡΠΏΠΎΠ»ΡΠ·ΠΎΠ²Π°ΡΡ ΠΊΠ°ΠΊ ΠΎΡΠ΄Π΅Π»ΠΎΡΠ½ΡΠΉ ΠΌΠ°ΡΠ΅ΡΠΈΠ°Π», Π΄Π»Ρ ΡΠΊΡΠ°ΡΠ΅Π½ΠΈΡ ΡΡΠ΅Π½ Π·Π΄Π°Π½ΠΈΠΉ ΠΈ ΠΏΠΎΠΌΠ΅ΡΠ΅Π½ΠΈΠΉ.
ΠΠΈΠΏΡ β ΡΡΠΎ ΠΌΡΠ³ΠΊΠΈΠΉ, ΠΏΠ»Π°ΡΡΠΈΠ½ΡΠ°ΡΡΠΉ ΠΌΠΈΠ½Π΅ΡΠ°Π», ΠΊΠΎΡΠΎΡΡΠΉ ΠΎΡΠ½ΠΎΡΡΡ ΠΊ ΠΊΠ»Π°ΡΡΡ ΡΡΠ»ΡΡΠ°ΡΠΎΠ². ΠΠΈΠ½Π΅ΡΠ°Π» ΠΌΠΎΠΆΠ΅Ρ ΠΈΠΌΠ΅ΡΡ Π²ΠΎΠ»ΠΎΠΊΠ½ΠΈΡΡΡΡ ΠΈΠ»ΠΈ Π·Π΅ΡΠ½ΠΈΡΡΡΡ ΡΡΡΡΠΊΡΡΡΡ, Ρ ΠΏΠ»ΠΎΡΠ½ΠΎΡΡΡΡ Π΄ΠΎ 2330 ΠΊΠ³ Π½Π° ΠΌΠ΅ΡΡ ΠΊΡΠ±ΠΈΡΠ΅ΡΠΊΠΈΠΉ. ΠΠ±ΡΠ°Π·ΡΠ΅ΡΡΡ Π³ΠΈΠΏΡ Π² ΡΠ΅Π·ΡΠ»ΡΡΠ°ΡΠ΅ ΠΈΡΠΏΠ°ΡΠ΅Π½ΠΈΡ ΠΎΠΊΠ΅Π°Π½Π°, ΠΊΠ°ΠΊ Ρ ΠΈΠΌΠΈΡΠ΅ΡΠΊΠΈΠΉ ΠΎΡΠ°Π΄ΠΎΠΊ.
Π ΠΎΡΠ»ΠΈΡΠΈΠ΅ ΠΎΡ ΡΠ°Π·Π»ΠΈΡΠ½ΡΡ ΡΠΈΠ½ΡΠ΅ΡΠΈΡΠ΅ΡΠΊΠΈΡ Π°Π½Π°Π»ΠΎΠ³ΠΎΠ² Π³ΠΈΠΏΡ ΠΈΠΌΠ΅Π΅Ρ Π½Π΅ΠΌΠ°Π»ΠΎ Π²Π΅ΡΠΎΠΌΡΡ ΠΏΡΠ΅ΠΈΠΌΡΡΠ΅ΡΡΠ², ΠΌΠΈΠ½Π΅ΡΠ°Π»:
- ΠΠ°ΡΡΡΠ°Π»ΡΠ½ΡΠΉ ΠΈ Π±Π΅Π·ΠΎΠΏΠ°ΡΠ½ΡΠΉ Π΄Π»Ρ ΠΎΡΠ³Π°Π½ΠΈΠ·ΠΌΠ°. ΠΠΈΠΏΡ ΠΎΡΠ½ΠΎΡΡΡ ΠΊ ΡΠΊΠΎΠ»ΠΎΠ³ΠΈΡΠ΅ΡΠΊΠΈ ΡΠΈΡΡΡΠΌ ΠΌΠ°ΡΠ΅ΡΠΈΠ°Π»Π°ΠΌ. ΠΠΈΠΊΠ°ΠΊΠΈΡ Π²ΡΠ΅Π΄Π½ΡΡ ΠΈΡΠΏΠ°ΡΠ΅Π½ΠΈΠΉ ΠΈ ΡΠΎΠΊΡΠΈΠ½ΠΎΠ² Π³ΠΈΠΏΡ Π½Π΅ Π²ΡΠ΄Π΅Π»ΡΠ΅Ρ, ΠΏΠΎΡΡΠΎΠΌΡ ΠΌΠΎΠΆΠ΅Ρ ΠΈΡΠΏΠΎΠ»ΡΠ·ΠΎΠ²Π°ΡΡΡΡ Π΄Π»Ρ Π΄Π΅ΠΊΠΎΡΠ°ΡΠΈΠ²Π½ΠΎΠΉ ΠΎΡΠ΄Π΅Π»ΠΊΠΈ ΠΆΠΈΠ»ΡΡ ΠΏΠΎΠΌΠ΅ΡΠ΅Π½ΠΈΠΉ.
- ΠΠ΅Π³ΠΊΠΎ ΠΏΠΎΠ΄Π΄Π°ΡΡΡΡ ΠΎΠ±ΡΠ°Π±ΠΎΡΠΊΠ΅. ΠΡΠ»ΠΈ ΡΡΠ°Π²Π½ΠΈΠ²Π°ΡΡ Π»Π΅ΠΏΠ½ΠΈΠ½Ρ ΠΈΠ· ΡΠ°Π·Π½ΡΡ
ΠΌΠ°ΡΠ΅ΡΠΈΠ°Π»ΠΎΠ², Π³ΠΈΠΏΡ ΠΌΠ°ΠΊΡΠΈΠΌΠ°Π»ΡΠ½ΠΎ ΡΠΎΡΠ½ΠΎ ΠΏΠ΅ΡΠ΅Π΄Π°ΡΡ ΠΈΠ·ΠΎΠ±ΡΠ°ΠΆΠ΅Π½ΠΈΠ΅. ΠΠΎΡΠΎΠ²ΡΠ΅ Π³ΠΈΠΏΡΠΎΠ²ΡΠ΅ ΠΈΠ·Π΄Π΅Π»ΠΈΡ ΠΎΡΠ»ΠΈΡΠ°ΡΡΡΡ ΠΏΡΠ°Π²ΠΈΠ»ΡΠ½ΡΠΌΠΈ, Π³Π΅ΡΠΌΠ΅ΡΠΈΡΠ½ΡΠΌΠΈ ΡΠΎΡΠΌΠ°ΠΌΠΈ ΠΈ ΠΏΡΠΈΠ²Π»Π΅ΠΊΠ°ΡΠ΅Π»ΡΠ½ΡΠΌ Π΄ΠΈΠ·Π°ΠΉΠ½ΠΎΠΌ.
- ΠΠΌΠ΅Π΅Ρ Π΄Π»ΠΈΡΠ΅Π»ΡΠ½ΡΠ΅ ΡΡΠΎΠΊΠΈ ΡΠΊΡΠΏΠ»ΡΠ°ΡΠ°ΡΠΈΠΈ. ΠΡΠΎΡΠ»ΡΠΆΠ°Ρ Π³ΠΈΠΏΡΠΎΠ²ΡΠ΅ ΡΠΊΡΠ°ΡΠ΅Π½ΠΈΡ ΡΠΎΡΠ½ΠΈ Π»Π΅Ρ, ΡΡΠΎ Π³Π»Π°Π²Π½ΡΠΉ ΠΏΠ»ΡΡ Π³ΠΈΠΏΡΠΎΠ²ΠΎΠΉ Π»Π΅ΠΏΠ½ΠΈΠ½Ρ. ΠΡΡΠ°Π»ΡΠ½ΡΠ΅ ΠΌΠ°ΡΠ΅ΡΠΈΠ°Π»Ρ Π½Π΅ ΠΌΠΎΠ³ΡΡ ΠΏΠΎΡ Π²Π°ΡΡΠ°ΡΡΡΡ ΡΠ°ΠΊΠΎΠΉ ΠΏΡΠΎΡΠ½ΠΎΡΡΡΡ ΠΈ ΠΎΡΠ΅Π½Ρ Π±ΡΡΡΡΠΎ ΡΠ΅ΡΡΡΡ ΡΠ²ΠΎΡ ΠΏΡΠΈΠ²Π»Π΅ΠΊΠ°ΡΠ΅Π»ΡΠ½ΠΎΡΡΡ.
- ΠΠ΅ Π±ΠΎΠΈΡΡΡ Π²Π»Π°ΠΆΠ½ΠΎΡΡΠΈ ΠΈ Π΄ΡΡΠ³ΠΈΡ Π½Π΅Π±Π»Π°Π³ΠΎΠΏΡΠΈΡΡΠ½ΡΡ Π²ΠΎΠ·Π΄Π΅ΠΉΡΡΠ²ΠΈΠΉ. ΠΠΈΠΏΡΠΎΠ²ΡΠ΅ ΠΈΠ·Π΄Π΅Π»ΠΈΡ ΡΡΠΎΠΉΠΊΠΎ ΠΏΠ΅ΡΠ΅Π½ΠΎΡΡΡ Π²ΡΡΠΎΠΊΡΡ ΡΠ΅ΠΌΠΏΠ΅ΡΠ°ΡΡΡΡ, Π²Π»Π°Π³Ρ ΠΈ ΠΎΠ±Π΅ΡΠΏΠ΅ΡΠΈΠ²Π°ΡΡ Π΄ΠΎΠΏΠΎΠ»Π½ΠΈΡΠ΅Π»ΡΠ½ΡΡ Π·Π²ΡΠΊΠΎΠΈΠ·ΠΎΠ»ΡΡΠΈΡ ΠΏΠΎΠΌΠ΅ΡΠ΅Π½ΠΈΠΉ.
ΠΠ»Π°Π³ΠΎΠ΄Π°ΡΡ Π²ΡΠ΅ΠΌ Π²ΡΡΠ΅ΠΏΠ΅ΡΠ΅ΡΠΈΡΠ»Π΅Π½Π½ΡΠΌ ΡΠ²ΠΎΠΉΡΡΠ²Π°ΠΌ Π³ΠΈΠΏΡΠΎΠ²Π°Ρ Π»Π΅ΠΏΠ½ΠΈΠ½Π° ΠΈΡΠΏΠΎΠ»ΡΠ·ΡΠ΅ΡΡΡ ΡΠΆΠ΅ ΡΠΎΡΠ½ΠΈ Π»Π΅Ρ Π΄Π»Ρ ΡΠΊΡΠ°ΡΠ΅Π½ΠΈΡ ΠΈ ΠΎΡΠ΄Π΅Π»ΠΊΠΈ ΠΏΠΎΠΌΠ΅ΡΠ΅Π½ΠΈΠΉ.
ΠΡΠΎΡΠ΅ΡΡ ΠΈΠ·Π³ΠΎΡΠΎΠ²Π»Π΅Π½ΠΈΡ Π»Π΅ΠΏΠ½ΠΈΠ½ΡΠΠΈΠΏΡΠΎΠ²Π°Ρ Π»Π΅ΠΏΠ½ΠΈΠ½Π° ΠΏΡΠ΅Π΄ΡΡΠ°Π²Π»Π΅Π½Π½Π°Ρ Π½Π° ΡΠ°ΠΉΡΠ΅ lepart.su β ΡΡΠΎ Π½Π°ΡΡΠΎΡΡΠ΅Π΅ ΠΈΡΠΊΡΡΡΡΠ²ΠΎ, ΡΡΠ΅Π±ΡΡΡΠ΅Π΅ Π²ΡΡΠΎΠΊΠΎΠ³ΠΎ ΠΏΡΠΎΡΠ΅ΡΡΠΈΠΎΠ½Π°Π»ΠΈΠ·ΠΌΠ° ΠΈ Π²ΡΠ΅ΠΌΠ΅Π½ΠΈ. ΠΠ»Ρ ΡΠΎΠ·Π΄Π°Π½ΠΈΡ Π³ΠΈΠΏΡΠΎΠ²ΠΎΠΉ Π»Π΅ΠΏΠ½ΠΈΠ½Ρ ΡΠΏΠ΅ΡΠΈΠ°Π»ΠΈΡΡΡ:
- ΠΠΎΠ΄Π΅Π»ΠΈΡΡΡΡ ΠΈΠ·Π΄Π΅Π»ΠΈΠ΅.
- ΠΠΎΠ΄Π³ΠΎΡΠ°Π²Π»ΠΈΠ²Π°ΡΡ ΡΠΎΡΠΌΡ.
- ΠΡΠ»ΠΈΠ²Π°ΡΡ, ΠΈΠ»ΠΈ ΡΠΈΡΠ°ΠΆΠΈΡΡΡΡ Π»Π΅ΠΏΠ½ΠΈΠ½Ρ.
Π‘Π½Π°ΡΠ°Π»Π° ΡΠΏΠ΅ΡΠΈΠ°Π»ΠΈΡΡΡ ΡΠΎΠ·Π΄Π°ΡΡ ΡΠ΅ΡΡΡΠΆ, ΠΏΠΎ ΠΊΠΎΡΠΎΡΠΎΠΌΡ ΡΠΎΠ·Π΄Π°ΡΡΡΡ ΠΌΠΎΠ΄Π΅Π»Ρ Π±ΡΠ΄ΡΡΠ΅Π³ΠΎ ΠΈΠ·Π΄Π΅Π»ΠΈΡ. Π§Π΅ΠΌ ΠΊΠ°ΡΠ΅ΡΡΠ²Π΅Π½Π½Π΅ΠΉ Π²ΡΠΏΠΎΠ»Π½Π΅Π½ ΡΠ΅ΡΡΡΠΆ, ΡΠ΅ΠΌ ΠΌΠ΅Π½ΡΡΠ΅ ΠΎΡΠΈΠ±ΠΎΠΊ Π²ΠΎΠ·Π½ΠΈΠΊΠ°Π΅Ρ ΠΏΡΠΈ ΠΈΠ·Π³ΠΎΡΠΎΠ²Π»Π΅Π½ΠΈΠΈ ΠΌΠ°ΠΊΠ΅ΡΠ°. ΠΠ»Ρ ΠΈΠ·Π³ΠΎΡΠΎΠ²Π»Π΅Π½ΠΈΡ ΠΌΠΎΠ΄Π΅Π»ΠΈ ΡΠ°ΠΊΠΆΠ΅ ΠΈΡΠΏΠΎΠ»ΡΠ·ΡΡΡ Π³ΠΈΠΏΡ, ΠΏΠ»Π°ΡΡΠΈΠ»ΠΈΠ½ ΠΈ Π΄ΡΡΠ³ΠΈΠ΅ ΠΏΠΎΠ΄ΡΡΡΠ½ΡΠ΅ ΠΌΠ°ΡΠ΅ΡΠΈΠ°Π»Ρ.
ΠΠΎΠ³Π΄Π° ΠΌΠ°ΠΊΠ΅Ρ Π³ΠΎΡΠΎΠ², ΡΠΏΠ΅ΡΠΈΠ°Π»ΠΈΡΡΡ Π΅ΡΡ ΡΠ°Π· ΠΏΡΠΎΠ²Π΅ΡΡΡΡ Π΅Π³ΠΎ ΡΠΎΠΎΡΠ²Π΅ΡΡΡΠ²ΠΈΠ΅ ΡΠΎΡΡΠ°Π²Π»Π΅Π½Π½ΡΠΌ ΡΠ°Π½Π΅Π΅ ΡΠ΅ΡΡΠ΅ΠΆΠ°ΠΌ ΠΈ Π½Π°ΡΠΈΠ½Π°ΡΡ ΡΠΎΡΠΌΠΎΠ²ΠΊΡ Π»Π΅ΠΏΠ½ΠΈΠ½Ρ ΠΈΠ· Π³ΠΈΠΏΡΠ°. ΠΠ»Ρ ΡΠΎΡΠΌΠΎΠ²ΠΊΠΈ ΠΈΡΠΏΠΎΠ»ΡΠ·ΡΡΡ ΠΎΠ΄Π½ΠΎΡΠ°Π·ΠΎΠ²ΡΠ΅ ΠΈ ΠΌΠ½ΠΎΠ³ΠΎΡΠ°Π·ΠΎΠ²ΡΠ΅ ΡΠΎΡΠΌΡ, Π²ΡΠ±ΠΎΡ Π·Π°Π²ΠΈΡΠΈΡ ΠΎΡ ΡΠ»ΠΎΠΆΠ½ΠΎΡΡΠΈ ΠΌΠΎΠ΄Π΅Π»ΠΈ ΠΈ Π½Π΅ΠΎΠ±Ρ ΠΎΠ΄ΠΈΠΌΠΎΠ³ΠΎ ΠΊΠΎΠ»ΠΈΡΠ΅ΡΡΠ²Π° ΠΊΠΎΠΏΠΈΠΉ. ΠΠ»Ρ ΡΠ΅ΡΠΈΠΉΠ½ΠΎΠ³ΠΎ ΠΏΡΠΎΠΈΠ·Π²ΠΎΠ΄ΡΡΠ²Π° Π»Π΅ΠΏΠ½ΠΈΠ½Ρ ΠΈΡΠΏΠΎΠ»ΡΠ·ΡΡΡ ΡΠΏΠ΅ΡΠΈΠ°Π»ΡΠ½ΡΠ΅ Π±Π΅ΡΠΎΠ½Π½ΡΠ΅ ΡΠΎΡΠΌΡ. Π‘Π΄Π΅Π»Π°ΡΡ ΡΠΎΡΠΌΡ ΠΌΠΎΠΆΠ½ΠΎ ΠΈ ΠΈΠ· Π΄ΡΡΠ³ΠΈΡ ΠΌΠ°ΡΠ΅ΡΠΈΠ°Π»ΠΎΠ², Π½Π°ΠΏΡΠΈΠΌΠ΅Ρ, ΠΈΠ· Π΄Π΅ΡΠ΅Π²Π° ΠΈΠ»ΠΈ ΠΏΠ»Π°ΡΡΠΈΠΊΠ°.
ΠΠ»Ρ ΠΈΠ·Π³ΠΎΡΠΎΠ²Π»Π΅Π½ΠΈΡ ΠΏΡΠΎΡΠ½ΠΎΠΉ ΠΈ ΡΡΡΠ΅ΡΠΈΡΠ½ΠΎΠΉ ΡΠ°ΡΠ°Π΄Π½ΠΎΠΉ Π»Π΅ΠΏΠ½ΠΈΠ½Ρ ΡΠΏΠ΅ΡΠΈΠ°Π»ΠΈΡΡΡ ΠΈΡΠΏΠΎΠ»ΡΠ·ΡΡΡ ΡΠΎΠ²ΡΠ΅ΠΌΠ΅Π½Π½ΡΠ΅ ΡΠ΅Ρ Π½ΠΎΠ»ΠΎΠ³ΠΈΠΈ ΠΈ ΠΊΠ°ΡΠ΅ΡΡΠ²Π΅Π½Π½ΡΠ΅ ΠΌΠ°ΡΠ΅ΡΠΈΠ°Π»Ρ. ΠΠ΅ΠΏΠ½ΠΈΠ½Ρ Π΄Π΅Π»Π°ΡΡ ΠΈΠ· ΡΠΏΠ΅ΡΠΈΠ°Π»ΡΠ½ΠΎΠ³ΠΎ Π°ΡΠΌΠΈΡΠΎΠ²Π°Π½Π½ΠΎΠ³ΠΎ ΠΏΠ΅Π½ΠΎΠΏΠΎΠ»ΠΈΡΡΠΈΡΠΎΠ»Π°, ΠΊΠΎΡΠΎΡΡΠΉ ΠΏΠΎΠΊΡΡΠ²Π°ΡΡ ΡΠ΅ΠΌΠ΅Π½ΡΠΎΠΌ.
Π€Π°ΡΠ°Π΄Π½Π°Ρ Π»Π΅ΠΏΠ½ΠΈΠ½Π°, Π±Π»Π°Π³ΠΎΠ΄Π°ΡΡ ΡΠ²ΠΎΠΈΠΌ ΠΌΠ½ΠΎΠ³ΠΎΡΠΈΡΠ»Π΅Π½Π½ΡΠΌ ΠΏΡΠ΅ΠΈΠΌΡΡΠ΅ΡΡΠ²Π°ΠΌ, ΡΡΠ°Π»Π° Π΄ΠΎΡΡΠΎΠΉΠ½ΡΠΌ Π°Π½Π°Π»ΠΎΠ³ΠΎΠΌ Π΄ΡΡΠ³ΠΈΠΌ ΠΎΡΠ΄Π΅Π»ΠΎΡΠ½ΡΠΌ ΠΌΠ°ΡΠ΅ΡΠΈΠ°Π»Π°ΠΌ, Π½Π°Π³ΡΡΠΆΠ°ΡΡΠΈΠΌ ΠΊΠΎΠ½ΡΡΡΡΠΊΡΠΈΡ. ΠΠ΅ΠΏΠ½ΠΈΠ½Π° Π»ΡΠ³ΠΊΠ°Ρ ΠΈ Π΄ΠΎΠ»Π³ΠΎΠ²Π΅ΡΠ½Π°Ρ, ΠΏΠΎΠ²Π΅ΡΡ
Π½ΠΎΡΡΡ ΠΌΠΎΠΆΠ½ΠΎ ΠΎΠΊΡΠ°ΡΠΈΠ²Π°ΡΡ Π² Π»ΡΠ±ΠΎΠΉ ΡΠ²Π΅Ρ, ΡΠΎΠ·Π΄Π°Π²Π°Ρ Π½Π΅ΠΎΠ±ΡΡΠ½ΡΠ΅ ΡΡΡΠ΅ΠΊΡΡ, ΠΏΠΎΡΡΠΎΠΌΡ ΠΌΠ°ΡΠ΅ΡΠΈΠ°Π» Π°ΠΊΡΠΈΠ²Π½ΠΎ ΠΈΡΠΏΠΎΠ»ΡΠ·ΡΡΡ Π΄Π»Ρ ΡΠΊΡΠ°ΡΠ΅Π½ΠΈΡ ΡΠ°ΡΠ°Π΄ΠΎΠ² Π·Π΄Π°Π½ΠΈΠΉ.
Β
Π’Π΅Ρ Π½ΠΎΠ»ΠΎΠ³ΠΈΡ
Π ΡΡΠΎΠΌ ΡΠ°Π·Π΄Π΅Π»Π΅ ΠΌΡ ΠΏΡΠΈΠΎΡΠΊΡΠΎΠ΅ΠΌ Π½Π΅ΠΊΠΎΡΠΎΡΡΠ΅ ΡΠ΅ΠΊΡΠ΅ΡΡ ΠΏΡΠΎΠΈΠ·Π²ΠΎΠ΄ΡΡΠ²Π°Β Π³ΠΈΠΏΡΠΎΠ²ΠΎΠΉ Π»Π΅ΠΏΠ½ΠΈΠ½Ρ, ΡΠ°ΡΡΠΊΠ°ΠΆΠ΅ΠΌ ΠΎ ΡΠ΅Ρ Π½ΠΎΠ»ΠΎΠ³ΠΈΠΈ ΠΈΠ·Π³ΠΎΡΠΎΠ²Π»Π΅Π½ΠΈΡ ΠΈ ΡΡΡΠ°Π½ΠΎΠ²ΠΊΠΈ ΠΈΠ·Π΄Π΅Π»ΠΈΠΉ ΠΈΠ· Π³ΠΈΠΏΡΠ°.
ΠΠ° ΡΠ΅Π³ΠΎΠ΄Π½ΡΡΠ½ΠΈΠΉ Π΄Π΅Π½Ρ ΠΌΠ°ΡΠ΅ΡΠΈΠ°Π»ΠΎΠ² Π΄Π»Ρ ΠΏΡΠΎΠΈΠ·Π²ΠΎΠ΄ΡΡΠ²Π° Π³ΠΈΠΏΡΠΎΠ²ΠΎΠ³ΠΎ Π΄Π΅ΠΊΠΎΡΠ° ΠΎΡΠ΅Π½Ρ ΠΌΠ½ΠΎΠ³ΠΎ β ΡΡΠΎ Π³ΠΈΠΏΡ, ΡΠ΅ΠΌΠ΅Π½Ρ, ΡΡΡΠΊΠ°ΡΡΡΠΊΠ°, ΡΡΠ΅ΠΊΠ»ΠΎΠ²ΠΎΠ»ΠΎΠΊΠ½ΠΎ, ΠΏΠ°ΠΏΡΠ΅-ΠΌΠ°ΡΠ΅ ΠΈ ΠΏΠΎΠΏΡΠ»ΡΡΠ½ΡΠΉ ΡΠ΅Π³ΠΎΠ΄Π½Ρ ΠΏΠΎΠ»ΠΈΡΡΠ΅ΡΠ°Π½. ΠΠ΅ ΡΠΌΠΎΡΡΡ Π½Π° ΠΈΠ·ΠΎΠ±ΠΈΠ»ΠΈΠ΅ ΠΌΠ°ΡΠ΅ΡΠΈΠ°Π»ΠΎΠ², Π½Π°ΠΈΠ±ΠΎΠ»Π΅Π΅ Π΅ΡΡΠ΅ΡΡΠ²Π΅Π½Π½Π°Ρ, ΠΊΠ°ΡΠ΅ΡΡΠ²Π΅Π½Π½Π°Ρ ΠΈ ΡΠ΅Π»ΡΠ΅ΡΠ½Π°Ρ Π»Π΅ΠΏΠ½ΠΈΠ½Π° ΠΏΠΎΠ»ΡΡΠ°Π΅ΡΡΡ ΠΈΠ· Π³ΠΈΠΏΡΠ°.
ΠΠ΅ΠΊΠΎΡΠΎΡΡΠ΅ ΡΠ°ΠΊΡΡ ΠΎ Π³ΠΈΠΏΡΠ΅
β Π‘Π°ΠΌΡΠΉ Π΄ΡΠ΅Π²Π½ΠΈΠΉ ΠΌΠ°ΡΠ΅ΡΠΈΠ°Π» Π΄Π»Ρ ΠΈΠ·Π³ΠΎΡΠΎΠ²Π»Π΅Π½ΠΈΡ Π»Π΅ΠΏΠ½ΠΈΠ½Ρ. ΠΠΏΠ΅ΡΠ²ΡΠ΅ ΡΡΠΎΡ ΠΌΠ°ΡΠ΅ΡΠΈΠ°Π» Π±ΡΠ» ΠΏΡΠΈΠΌΠ΅Π½ΡΠ½ Π² 3700 Π³ΠΎΠ΄Ρ Π΄ΠΎ Π½.Ρ. Π² ΠΡΠ΅Π²Π½Π΅ΠΌ ΠΠ³ΠΈΠΏΡΠ΅. ΠΠ΄Π½Π°ΠΊΠΎ Π² ΠΠ²ΡΠΎΠΏΠ΅ Π½Π°ΡΠ°Π» ΠΏΡΠΈΠΌΠ΅Π½ΡΡΡΡΡ ΡΠΎΠ»ΡΠΊΠΎ Π² XV Π²Π΅ΠΊΠ΅. Π£ΠΆΠ΅ ΡΠΎΠ³Π΄Π° Π³ΠΈΠΏΡ ΠΏΡΠΈΠΌΠ΅Π½ΡΠ»ΠΈ Π΄Π»Ρ Π²Π½Π΅ΡΠ½Π΅ΠΉ ΠΎΡΠ΄Π΅Π»ΠΊΠΈ Π·Π΄Π°Π½ΠΈΠΉ ΠΈ ΠΊΠ°ΠΊ ΡΠ»Π΅ΠΌΠ΅Π½Ρ Π²Π½ΡΡΡΠ΅Π½Π½Π΅Π³ΠΎ Π΄Π΅ΠΊΠΎΡΠΈΡΠΎΠ²Π°Π½ΠΈΡ.Β
β ΠΠΈΠ½Π΅ΡΠ°Π»Β ΠΈΠ· ΠΊΠ»Π°ΡΡΠ° ΡΡΠ»ΡΡΠ°ΡΠΎΠ²:Β ΠΌΡΠ³ΠΊΠΈΠΉ,Β ΠΏΠ»Π°ΡΡΠΈΠ½ΡΠ°ΡΠΎΠΉ, Π²ΠΎΠ»ΠΎΠΊΠ½ΠΈΡΡΠΎΠΉ ΠΈΠ»ΠΈ Π·Π΅ΡΠ½ΠΈΡΡΠΎΠΉ ΠΊΠΎΠ½ΡΠΈΡΡΠ΅Π½ΡΠΈΠΈ, ΠΏΠ»ΠΎΡΠ½ΠΎΡΡΡΡ 2310-2330 ΠΊΠ³/ΠΌ3.
β Π’ΠΈΠΏΠΈΡΠ½ΡΠΉ ΠΎΡΠ°Π΄ΠΎΡΠ½ΡΠΉ ΠΌΠΈΠ½Π΅ΡΠ°Π», ΠΊΠΎΡΠΎΡΡΠΉ ΠΎΠ±ΡΠ°Π·ΠΎΠ²Π°Π½ ΠΊΠ°ΠΊ Ρ
ΠΈΠΌΠΈΡΠ΅ΡΠΊΠΈΠ΅ ΠΎΡΠ°Π΄ΠΊΠΈ Π² ΡΠ΅Π·ΡΠ»ΡΡΠ°ΡΠ΅ ΠΈΡΠΏΠ°ΡΠ΅Π½ΠΈΡ Π΄ΡΠ΅Π²Π½Π΅Π³ΠΎ ΠΎΠΊΠ΅Π°Π½Π°.
ΠΡΠ΅ΠΈΠΌΡΡΠ΅ΡΡΠ²Π° Π³ΠΈΠΏΡΠ°
1.Β ΠΠ΅Π·Π²ΡΠ΅Π΄Π½ΠΎΡΡΡ ΠΈ ΡΠΊΠΎΠ»ΠΎΠ³ΠΈΡΠ½ΠΎΡΡΡ.Β ΠΠΈΠΏΡ βΒ ΡΡΠΎ ΡΠΊΠΎΠ»ΠΎΠ³ΠΈΡΠ΅ΡΠΊΠΈ ΡΠΈΡΡΡΠΉ, Π½Π°ΡΡΡΠ°Π»ΡΠ½ΡΠΉ, ΠΆΠΈΠ²ΠΎΠΉ ΠΌΠ°ΡΠ΅ΡΠΈΠ°Π», ΠΊΠΎΡΠΎΡΡΠΉ Π½Π΅ Π²ΡΠ΄Π΅Π»ΡΠ΅Ρ Π²ΡΠ΅Π΄Π½ΡΡ Π΄Π»Ρ ΡΠ΅Π»ΠΎΠ²Π΅ΠΊΠ° Π²Π΅ΡΠ΅ΡΡΠ² ΠΈ Π½Π΅ ΠΈΠΌΠ΅Π΅Ρ Π·Π°ΠΏΠ°Ρ Π°.
2.Β Π’ΠΎΡΠ½ΠΎΡΡΡ ΠΏΠ΅ΡΠ΅Π΄Π°ΡΠΈ ΡΠΈΡΡΠ½ΠΊΠ°.Β ΠΠΈΠΏΡΠΎΠ²ΡΠ΅ ΠΈΠ·Π΄Π΅Π»ΠΈΡ ΡΠ΅Π»ΡΠ΅ΡΠ½Ρ, ΠΈΠ·ΡΡΠ½Ρ, ΡΠΎ ΡΡΡΠΎΠ³ΠΈΠΌΠΈ Π³Π΅ΠΎΠΌΠ΅ΡΡΠΈΡΠ΅ΡΠΊΠΈΠΌΠΈ ΡΠΎΡΠΌΠ°ΠΌΠΈ.Β
3.Β ΠΠΎΠ»Π³ΠΎΠ²Π΅ΡΠ½ΠΎΡΡΡ.Β ΠΠΈΠΏΡ ΡΠ΅Π½ΠΈΡΡΡ Π·Π° ΡΠ²ΠΎΡ ΠΏΡΠΎΡΠ½ΠΎΡΡΡ.Β ΠΠΈΠΏΡΠΎΠ²Π°Ρ Π»Π΅ΠΏΠ½ΠΈΠ½Π°Β ΠΌΠΎΠΆΠ΅Ρ ΠΏΡΠΎΡΠ»ΡΠΆΠΈΡΡ Π΄ΠΎ 100 Π»Π΅Ρ ΠΈ Π±ΠΎΠ»ΡΡΠ΅. Π ΡΠΎ Π²ΡΠ΅ΠΌΡ ΠΊΠ°ΠΊ ΠΏΠΎΠ»ΠΈΡΡΠ΅ΡΠ°Π½ΠΎΠ²ΡΠΉ Π΄Π΅ΠΊΠΎΡ ΡΠΆΠ΅ ΡΠ΅ΡΠ΅Π· Π½Π΅ΡΠΊΠΎΠ»ΡΠΊΠΎ Π»Π΅Ρ Π½Π°ΡΠΈΠ½Π°Π΅Ρ ΡΠ΅ΡΡΡΡ ΡΠ²ΠΎΠΈ ΠΊΠ°ΡΠ΅ΡΡΠ²Π°. ΠΠΈΠΏΡ ΡΠ²Π»ΡΠ΅ΡΡΡ Π΅ΡΠ΅ ΠΈ Ρ ΠΎΡΠΎΡΠΈΠΌ ΡΡΠ΅ΠΏΠ»ΠΈΡΠ΅Π»Π΅ΠΌ Π΄Π»Ρ ΠΏΠΎΠΌΠ΅ΡΠ΅Π½ΠΈΠΉ.
4.Β ΠΠΎΠ΄ΠΎΡΡΠΎΠΉΠΊΠΎΡΡΡ, ΠΏΠΎΠΆΠ°ΡΠΎΠ±Π΅Π·ΠΎΠΏΠ°ΡΠ½ΠΎΡΡΡ, Π·Π²ΡΠΊΠΎΠΈΠ·ΠΎΠ»ΡΡΠΈΡ.Β ΠΠΈΠΏΡΠΎΠ²ΡΠ΅ ΠΈΠ·Π΄Π΅Π»ΠΈΡ Π½Π΅ Π³ΠΎΡΡΡ, ΡΡΠΎΠΉΠΊΠΈΠ΅ ΠΊ Π²ΠΎΠ·Π΄Π΅ΠΉΡΡΠ²ΠΈΡ Π²Π»Π°Π³ΠΈ ΠΈ ΠΎΠ±Π΅ΡΠΏΠ΅ΡΠΈΠ²Π°ΡΡ ΠΏΠΎΠΌΠ΅ΡΠ΅Π½ΠΈΡ Π·Π²ΡΠΊΠΎΠΈΠ·ΠΎΠ»ΡΡΠΈΡ.
ΠΠ·Π³ΠΎΡΠΎΠ²Π»Π΅Π½ΠΈΠ΅ Π³ΠΈΠΏΡΠΎΠ²ΠΎΠΉ Π»Π΅ΠΏΠ½ΠΈΠ½Ρ
ΠΡΠΎΠΈΠ·Π²ΠΎΠ΄ΡΡΠ²ΠΎ Π»Π΅ΠΏΠ½ΠΈΠ½Ρ ΠΈΠ· Π³ΠΈΠΏΡΠ°Β βΒ ΡΠ΅Ρ Π½ΠΎΠ»ΠΎΠ³ΠΈΡΠ΅ΡΠΊΠΈ ΡΠ»ΠΎΠΆΠ½ΡΠΉ ΠΈ ΡΡΡΠ΄ΠΎΡΠΌΠΊΠΈΠΉ ΠΏΡΠΎΡΠ΅ΡΡ, Π²ΠΊΠ»ΡΡΠ°ΡΡΠΈΠΉ Π² ΡΠ΅Π±Ρ ΡΡΠΈ ΠΏΠΎΡΠ»Π΅Π΄ΠΎΠ²Π°ΡΠ΅Π»ΡΠ½ΡΡ ΡΡΠ°ΠΏΠ°:
- ΠΠΎΠ΄Π΅Π»ΠΈΡΠΎΠ²Π°Π½ΠΈΠ΅
- Π€ΠΎΡΠΌΠΎΠ²ΠΊΠ°
- ΠΡΠ»ΠΈΠ²ΠΊΠ° ΠΈΠ»ΠΈ ΡΠΈΡΠ°ΠΆΠΈΡΠΎΠ²Π°Π½ΠΈΠ΅
ΠΠ΅ΡΠ²ΡΠΉ ΡΡΠ°ΠΏ ΠΏΡΠΎΠΈΠ·Π²ΠΎΠ΄ΡΡΠ²Π° Π»Π΅ΠΏΠ½ΠΈΠ½Ρ β ΡΡΠΎ ΠΈΠ·Π³ΠΎΡΠΎΠ²Π»Π΅Π½ΠΈΠ΅ ΠΏΠΎ ΡΠΎΠ·Π΄Π°Π½Π½ΠΎΠΌΡ Π°ΡΡ
ΠΈΡΠ΅ΠΊΡΠΎΡΠΎΠΌ ΡΠ΅ΡΡΠ΅ΠΆΡ ΠΌΠΎΠ΄Π΅Π»ΠΈ Π±ΡΠ΄ΡΡΠ΅Π³ΠΎ ΡΠ»Π΅ΠΌΠ΅Π½ΡΠ° Π΄Π΅ΠΊΠΎΡΠ°. ΠΠ°ΡΠ΅ΡΡΠ²ΠΎ ΠΌΠΎΠ΄Π΅Π»ΠΈ Π²ΠΎ ΠΌΠ½ΠΎΠ³ΠΎΠΌ Π·Π°Π²ΠΈΡΠΈΡ ΠΎΡ ΠΊΠ°ΡΠ΅ΡΡΠ²Π° Π²ΡΠΏΠΎΠ»Π½Π΅Π½Π½ΠΎΠ³ΠΎ ΡΠ΅ΡΡΠ΅ΠΆΠ°. ΠΠΎΠ΄Π΅Π»ΠΈ ΠΎΠ±ΡΡΠ½ΠΎ Π΄Π΅Π»Π°ΡΡΡΡ ΠΈΠ· ΠΏΠ»Π°ΡΡΠΈΠ»ΠΈΠ½Π°, Π³Π»ΠΈΠ½Ρ, Π³ΠΈΠΏΡΠ° ΠΈΠ»ΠΈ Π΄ΡΡΠ³ΠΎΠ³ΠΎ ΠΌΠ°ΡΠ΅ΡΠΈΠ°Π»Π°. ΠΡΠΏΠΎΠ»Π½Π΅Π½Π½ΡΡ ΠΌΠ°ΡΡΠ΅ΡΠΎΠΌ ΠΌΠΎΠ΄Π΅Π»Ρ ΠΎΡΠΌΠ°ΡΡΠΈΠ²Π°ΡΡ ΠΈ, Π΅ΡΠ»ΠΈ ΠΎΠ½Π° ΡΠΎΠΎΡΠ²Π΅ΡΡΡΠ²ΡΠ΅Ρ ΡΠ΅ΡΡΠ΅ΠΆΡ, ΡΠΎ ΠΏΡΠΈΡΡΡΠΏΠ°ΡΡ ΠΊ ΡΠ»Π΅Π΄ΡΡΡΠ΅ΠΌΡ ΡΡΠ°ΠΏΡ β ΡΠΎΡΠΌΠΎΠ²ΠΊΠ΅ ΠΌΠΎΠ΄Π΅Π»ΠΈ Π² Π³ΠΈΠΏΡΠ΅.
Π€ΠΎΡΠΌΡ ΠΈΠ·Π³ΠΎΡΠ°Π²Π»ΠΈΠ²Π°ΡΡΡΡ ΠΈΠ· ΡΠ°Π·Π»ΠΈΡΠ½ΡΡ ΠΌΠ°ΡΠ΅ΡΠΈΠ°Π»ΠΎΠ², Π° Π²ΡΠ±ΠΎΡ ΠΌΠ°ΡΠ΅ΡΠΈΠ°Π»Π° Π·Π°Π²ΠΈΡΠΈΡ ΠΎΡ Π½Π΅ΠΎΠ±Ρ ΠΎΠ΄ΠΈΠΌΠΎΠ³ΠΎ ΡΠΈΡΠ»Π° ΠΊΠΎΠΏΠΈΠΉ ΠΈ ΡΠ°Π·Π΄Π΅Π»ΡΡΡΡΡ Π½Π° Π²ΠΈΠ΄Ρ:
- ΠΠ΄Π½ΠΎΡΠ°Π·ΠΎΠ²ΡΠ΅: Π³ΠΈΠΏΡΠΎΠ²Π°Ρ ΡΠ΅ΡΠ½ΠΎΠ²Π°Ρ
- ΠΠ½ΠΎΠ³ΠΎΡΠ°Π·ΠΎΠ²ΡΠ΅: Π³ΠΈΠΏΡΠΎΠ²Π°Ρ ΡΠΈΡΡΠ°Ρ ΠΊΡΡΠΊΠΎΠ²Π°Ρ, ΠΊΠ»Π΅Π΅Π²Π°Ρ ΠΈ ΡΠΎΡΠΌΠΎΠΏΠ»Π°ΡΡΠΎΠ²Π°Ρ
- ΠΠ»Ρ ΠΌΠ°ΡΡΠΎΠ²ΠΎΠ³ΠΎ ΠΏΡΠΎΠΈΠ·Π²ΠΎΠ΄ΡΡΠ²Π°: ΡΠ΅ΠΌΠ΅Π½ΡΠ½Π°Ρ (Π±Π΅ΡΠΎΠ½Π½Π°Ρ)
ΠΡΠΎΠΌΠ΅ ΡΠΎΠ³ΠΎ, ΡΠΎΡΠΌΡ ΡΠ°ΠΊΠΆΠ΅ Π±ΡΠ²Π°ΡΡ Π΄Π΅ΡΠ΅Π²ΡΠ½Π½ΡΠ΅, ΠΌΠ΅ΡΠ°Π»Π»ΠΈΡΠ΅ΡΠΊΠΈΠ΅ ΠΈ ΠΈΠ·Π³ΠΎΡΠΎΠ²Π»Π΅Π½Π½ΡΠ΅ ΠΈΠ· Π΄ΡΡΠ³ΠΈΡ ΠΌΠ°ΡΠ΅ΡΠΈΠ°Π»ΠΎΠ². ΠΡΠΈ ΠΏΠΎΠΌΠΎΡΠΈ ΠΏΠΎΠ»ΡΡΠ΅Π½Π½ΠΎΠΉ ΡΠΎΡΠΌΡ ΠΎΡΠ»ΠΈΠ²Π°ΡΡ ΠΈΠ»ΠΈ ΠΎΡΠ±ΠΈΠ²Π°ΡΡ (ΡΠΈΡΠ°ΠΆΠΈΡΡΡΡ) Π½Π΅ΠΎΠ±Ρ ΠΎΠ΄ΠΈΠΌΠΎΠ΅ ΡΠΈΡΠ»ΠΎ ΠΈΠ·Π΄Π΅Π»ΠΈΠΉ.
Π‘ΠΎΠ²ΡΠ΅ΠΌΠ΅Π½Π½Π°Ρ ΡΠ°ΡΠ°Π΄Π½Π°Ρ Π»Π΅ΠΏΠ½ΠΈΠ½Π°, ΠΌΠ°ΡΠ΅ΡΠΈΠ°Π»Ρ ΠΈ ΡΠ΅Ρ Π½ΠΎΠ»ΠΎΠ³ΠΈΡ ΠΈΠ·Π³ΠΎΡΠΎΠ²Π»Π΅Π½ΠΈΡ
Π€Π°ΡΠ°Π΄Π½Π°Ρ Π»Π΅ΠΏΠ½ΠΈΠ½Π° ΠΎΡ ΠΡΠΌΠΈΡΠ°ΠΆΒ β ΡΡΠΎ ΡΠΊΡΠΊΠ»ΡΠ·ΠΈΠ²Π½ΡΠΉ ΡΠ°ΡΠ°Π΄Π½ΡΠΉ Π΄Π΅ΠΊΠΎΡ, Π°Π½Π°Π»ΠΎΠ³ΠΎΠ² ΠΊΠΎΡΠΎΡΠΎΠΉ ΡΠ΅Π³ΠΎΠ΄Π½Ρ Π½ΠΈ Π² Π£ΠΊΡΠ°ΠΈΠ½Π΅, Π½ΠΈ Π² Π ΠΎΡΡΠΈΠΈ Π½Π΅Ρ.
ΠΠ΅ΠΏΠ½ΠΎΠΉ Π΄Π΅ΠΊΠΎΡ Π΄Π»Ρ ΡΠ°ΡΠ°Π΄ΠΎΠ² ΠΈΠ· ΠΏΠ΅Π½ΠΎΠΏΠΎΠ»ΠΈΡΡΠΈΡΠΎΠ»Π° Ρ ΡΠ΅ΠΌΠ΅Π½ΡΠ½ΠΎΠΊΠ»Π΅Π΅Π²ΡΠΌ Π°ΡΠΌΠΈΡΡΡΡΠΈΠΌ ΠΏΠΎΠΊΡΡΡΠΈΠ΅ΠΌ βΒ Π΄ΠΎΡΡΠΎΠΉΠ½Π°Ρ Π°Π»ΡΡΠ΅ΡΠ½Π°ΡΠΈΠ²Π° ΠΏΡΠ΅ΠΆΠ½ΠΈΠΌ ΡΡΠΆΡΠ»ΡΠΌ ΠΌΠ°ΡΠ΅ΡΠΈΠ°Π»Π°ΠΌ. ΠΠΎΡΠΎΠ²ΡΠ΅ ΠΈΠ·Π΄Π΅Π»ΠΈΡ ΠΈΠ· ΠΏΠ΅Π½ΠΎΠΏΠ»Π°ΡΡΠ° ΠΏΠΎΠΊΡΡΠ²Π°ΡΡΡΡ ΡΠΏΠ΅ΡΠΈΠ°Π»ΡΠ½ΠΎΠΉ ΡΠ΅ΡΠΊΠΎΠΉ, Π½Π° ΠΊΠΎΡΠΎΡΡΡ Π½Π°Π½ΠΎΡΡΡ ΠΊΠ»Π΅ΠΉ ΠΈ ΡΠ΅ΠΌΠ΅Π½Ρ. ΠΠΎΡΠ»Π΅ ΡΡΠΎΠ³ΠΎ ΠΈΠ·Π΄Π΅Π»ΠΈΡ ΠΎΠΊΡΠ°ΡΠΈΠ²Π°ΡΡΡΡ ΠΏΡΠΈ ΠΏΠΎΠΌΠΎΡΠΈ ΠΊΠΈΡΡΠΈ ΠΈΠ»ΠΈ ΠΈΠ· ΠΊΡΠ°ΡΠΊΠΎΠΏΡΠ»ΡΡΠ° ΠΈ ΠΌΠΎΠ½ΡΠΈΡΡΡΡΡΡ Π½Π° Π·Π΄Π°Π½ΠΈΠ΅.Β
Π‘ΡΠΎΠΊ Π²ΡΠΏΠΎΠ»Π½Π΅Π½ΠΈΡ Π·Π°ΠΊΠ°Π·Π° Π·Π°Π²ΠΈΡΠΈΡ ΠΎΡ ΠΎΠ±ΡΡΠΌΠ° ΠΈ ΡΡΠΎΠ²Π½Ρ Π΅Π³ΠΎ ΡΠ»ΠΎΠΆΠ½ΠΎΡΡΠΈ, Π½ΠΎ Π² ΡΡΠ΅Π΄Π½Π΅ΠΌ ΡΠΎΡΡΠ°Π²Π»ΡΠ΅Ρ ΠΎΡ 3 Π΄ΠΎ 7 Π΄Π½Π΅ΠΉ.Β ΠΠ»Π°Π³ΠΎΠ΄Π°ΡΡ Π½Π°ΡΠ΅ΠΌΡ ΠΎΠΏΡΡΡ, ΡΠΎΠ²ΡΠ΅ΠΌΠ΅Π½Π½ΠΎΠΌΡ ΠΎΠ±ΠΎΡΡΠ΄ΠΎΠ²Π°Π½ΠΈΡ ΠΈ Π±ΠΎΠ»ΡΡΠΎΠΉ ΠΊΠΎΠΌΠ°Π½Π΄Π΅ Π²ΡΡΠΎΠΊΠΎΠΊΠ»Π°ΡΡΠ½ΡΡ ΡΠΏΠ΅ΡΠΈΠ°Π»ΠΈΡΡΠΎΠ², ΠΌΡ ΡΠ΅Π°Π»ΠΈΠ·ΠΎΠ²ΡΠ²Π°Π΅ΠΌ ΠΏΡΠΎΠ΅ΠΊΡΡ Π»ΡΠ±ΠΎΠ³ΠΎ ΠΎΠ±ΡΡΠΌΠ° ΠΈ ΡΡΠ΅ΠΏΠ΅Π½ΠΈ ΡΠ»ΠΎΠΆΠ½ΠΎΡΡΠΈ.
ΠΠ°ΠΊΠΎΠ²Π° ΠΏΡΠ°Π²ΠΈΠ»ΡΠ½Π°Ρ ΡΠ΅Ρ Π½ΠΎΠ»ΠΎΠ³ΠΈΡ Π΄Π»Ρ ΠΈΠ·Π³ΠΎΡΠΎΠ²Π»Π΅Π½ΠΈΡ Π³ΠΈΠΏΡΠΎΠ²ΠΎΠΉ Π»Π΅ΠΏΠ½ΠΈΠ½Ρ Π² Π΄ΠΎΠΌΠ°ΡΠ½ΠΈΡ ΡΡΠ»ΠΎΠ²ΠΈΡΡ ?
ΠΠ΅ΠΏΠ½ΠΈΠ½Π° — ΠΎΡΠ»ΠΈΡΠ½ΡΠΉ Π²ΡΠ±ΠΎΡ ΠΏΡΠ°ΠΊΡΠΈΡΠ΅ΡΠΊΠΈ Π΄Π»Ρ Π»ΡΠ±ΠΎΠ³ΠΎ ΠΈΠ½ΡΠ΅ΡΡΠ΅ΡΠ°. ΠΡΠ΅ Π±ΠΎΠ»ΡΡΠ΅ Π»ΡΠ΄Π΅ΠΉ ΠΎΡΠ΄Π°ΡΡ ΠΏΡΠ΅Π΄ΠΏΠΎΡΡΠ΅Π½ΠΈΠ΅ Π»Π΅ΠΏΠ½ΡΠΌ ΡΠ»Π΅ΠΌΠ΅Π½ΡΠ°ΠΌ, Π²Π΅Π΄Ρ ΡΠΌΠΎΡΡΡΡΡΡ ΠΎΠ½ΠΈ ΠΎΡΠ΅Π½Ρ Π±ΠΎΠ³Π°ΡΠΎ ΠΈ ΠΏΡΠΈΠ΄Π°ΡΡ ΠΏΠΎΠΌΠ΅ΡΠ΅Π½ΠΈΡ Π±Π»Π°Π³ΠΎΡΠΎΠ΄Π½ΡΠΉ Π²ΠΈΠ΄. ΠΡΠ΄Π° ΠΏΡΠΈΡΡΠ½Π΅Π΅ Π½Π°Ρ
ΠΎΠ΄ΠΈΡΡΡΡ Π² ΠΊΠΎΠΌΠ½Π°ΡΠ΅ Ρ Π½Π΅ΠΎΠ±ΡΡΠ°ΠΉΠ½ΠΎΠΉ ΠΊΡΠ°ΡΠΎΡΡ Π»Π΅ΠΏΠ½ΡΠΌΠΈ ΠΈΠ·Π΄Π΅Π»ΠΈΡΠΌΠΈ, ΠΊΠΎΡΠΎΡΡΠ΅ ΠΏΡΠΎΡΡΠΎ ΠΏΡΠΈΡΡΠ½ΠΎ ΡΠ°ΡΡΠΌΠ°ΡΡΠΈΠ²Π°ΡΡ, Π½Π°ΠΏΡΠΈΠΌΠ΅Ρ, ΠΏΠΎΠΊΠ° ΡΠ΅Π³ΠΎ-ΡΠΎ ΠΆΠ΄Π΅ΡΡ, ΡΠ΅ΠΌ Π² ΠΏΠΎΠΌΠ΅ΡΠ΅Π½ΠΈΠΈ Π² ΡΡΠΈΠ»Π΅ ΠΌΠΈΠ½ΠΈΠΌΠ°Π»ΠΈΠ·ΠΌΠ° ΠΈ ΠΌΠΎΠ΄Π΅ΡΠ½Π°.
ΠΠ·Π³ΠΎΡΠΎΠ²Π»Π΅Π½ΠΈΠ΅ Π³ΠΈΠΏΡΠΎΠ²ΠΎΠΉ Π»Π΅ΠΏΠ½ΠΈΠ½Ρ Π² Π΄ΠΎΠΌΠ°ΡΠ½ΠΈΡ ΡΡΠ»ΠΎΠ²ΠΈΡΡ Π½Π΅ ΡΠ²Π»ΡΠ΅ΡΡΡ ΡΠ°ΠΊΠΈΠΌ ΡΠΆ ΡΠ»ΠΎΠΆΠ½ΡΠΌ Π΄Π΅Π»ΠΎΠΌ. Π― Π½Π΅ Ρ ΠΎΡΡ ΡΠΊΠ°Π·Π°ΡΡ, ΡΡΠΎ Π²ΡΠ΅ ΠΏΡΠΎΡΡΠΎ, Π½ΠΎ Π΅ΡΠ»ΠΈ ΡΠΎΠ±Π»ΡΠ΄Π°ΡΡ ΡΠ΅Ρ Π½ΠΎΠ»ΠΎΠ³ΠΈΡ, ΡΠΎ Ρ ΠΏΡΠΈΡ ΠΎΠ΄ΠΎΠΌ ΠΎΠΏΡΡΠ° ΠΡ Π½Π΅ Π±ΡΠ΄Π΅ΡΠ΅ Π² ΡΡΠΎΠΌ Π·Π°Π½ΡΡΠΈΠΈ Π²ΠΈΠ΄Π΅ΡΡ ΠΊΠ°ΠΊΠΈΡ -Π»ΠΈΠ±ΠΎ ΡΡΡΠ΄Π½ΠΎΡΡΠ΅ΠΉ.
ΠΠ°Π²Π°ΠΉΡΠ΅ Π½Π°ΡΠ½Π΅ΠΌ Ρ ΡΠΎΠ³ΠΎ, ΡΡΠΎ Π±ΡΠ²Π°ΡΡ ΡΠ°Π·Π»ΠΈΡΠ½ΡΠ΅ Π»Π΅ΠΏΠ½ΡΠ΅ ΡΠ»Π΅ΠΌΠ΅Π½ΡΡ: ΠΌΠΎΠ»Π΄ΠΈΠ½Π³, Π·Π°ΠΌΠΎΠΊ, ΠΊΠ°ΡΠ½ΠΈΠ·, ΠΊΠ°ΠΏΠΈΡΠ΅Π»Ρ, Π±Π°Π»ΡΡΡΡΠ°Π΄Π°, ΡΠΎΠ·Π΅ΡΠΊΠ° ΠΈ ΡΠ°ΠΊ Π΄Π°Π»Π΅Π΅. Π’Π°ΠΊ Π²ΠΎΡ, ΡΠ΅Ρ
Π½ΠΎΠ»ΠΎΠ³ΠΈΡ ΠΈΠ·Π³ΠΎΡΠΎΠ²Π»Π΅Π½ΠΈΡ ΡΠ°Π·Π»ΠΈΡΠ½ΡΡ
ΡΠ»Π΅ΠΌΠ΅Π½ΡΠΎΠ² ΡΠ°Π·Π½ΠΈΡΡΡ. Π’Π°ΠΊ, Π½Π°ΠΏΡΠΈΠΌΠ΅Ρ, Π΄Π»Ρ ΠΈΠ·Π³ΠΎΡΠΎΠ²Π»Π΅Π½ΠΈΡ ΠΊΠ°ΠΏΠΈΡΠ΅Π»ΠΈ ΠΈΠ»ΠΈ ΡΠΎΠ·Π΅ΡΠΊΠΈ ΠΌΠΎΠΆΠ½ΠΎ ΠΈΡΠΏΠΎΠ»ΡΠ·ΠΎΠ²Π°ΡΡ ΡΠΎΡΠΌΡ, ΠΎΠ½ΠΈ ΠΈΠ·Π³ΠΎΡΠ°Π²Π»ΠΈΠ²Π°ΡΡΡΡ ΠΈΠ· ΡΠΈΠ»ΠΈΠΊΠΎΠ½Π° (Π½Π° ΠΌΠΎΠΉ Π²Π·Π³Π»ΡΠ΄ ΡΡΠΎ Π½Π°ΠΈΠ»ΡΡΡΠΈΠΉ Π²Π°ΡΠΈΠ°Π½Ρ). Π Π²ΠΎΡ, ΡΡΠΎ ΠΊΠ°ΡΠ°Π΅ΡΡΡ Π±ΠΎΠ»Π΅Π΅ ΠΎΠ΄Π½ΠΎΠΎΠ±ΡΠ°Π·Π½ΡΡ
ΡΠ»Π΅ΠΌΠ΅Π½ΡΠΎΠ², ΡΠΎΠ²Π½Π°Ρ ΠΊΠΎΠ»ΠΎΠ½Π½Π° ΠΈΠ»ΠΈ ΠΌΠΎΠ»Π΄ΠΈΠ½Π³ Π±Π΅Π· ΡΠ΅Π·Π½ΡΡ
ΡΠ·ΠΎΡΠΎΠ², ΡΠΎ Π·Π΄Π΅ΡΡ Π΅ΡΠ΅ ΠΏΡΠΎΡΠ΅ — Π΄ΠΎΡΡΠ°ΡΠΎΡΠ½ΠΎ ΡΠΎΠΎΡΡΠ΄ΠΈΡΡ ΠΈΠ· ΠΊΡΡΠΊΠ° ΠΏΠ»Π°ΡΡΠΈΠΊΠ° ΠΈΠ»ΠΈ ΡΠ°Π½Π΅ΡΠΊΠΈ ΡΠ°Π±Π»ΠΎΠ½ΡΠΈΠΊ ΠΈ ΡΠ°Π±ΠΎΡΠ°ΡΡ Ρ Π½ΠΈΠΌ.
ΠΡΠ»ΠΈ ΠΡ Π²ΡΠ΅ΡΡΠ΅Π· Ρ ΠΎΡΠΈΡΠ΅ Π·Π°Π½ΡΡΡΡΡ ΠΈΠ·Π³ΠΎΡΠΎΠ²Π»Π΅Π½ΠΈΠ΅ΠΌ Π»Π΅ΠΏΠ½ΡΡ ΡΠ»Π΅ΠΌΠ΅Π½ΡΠΎΠ² ΠΈΠ· Π³ΠΈΠΏΡΠ°, Π΄ΡΠΌΠ°Ρ, ΡΡΠΎ Π½Π΅ Π»ΠΈΡΠ½ΠΈΠΌ Π΄Π»Ρ ΠΠ°Ρ Π±ΡΠ΄Π΅Ρ ΠΏΠΎΡΠΌΠΎΡΡΠ΅ΡΡ ΡΡΠΎ Π²ΠΈΠ΄Π΅ΠΎ, Ρ Π½Π΅Π³ΠΎ ΠΌΠΎΠΆΠ½ΠΎ ΠΏΠΎΡΠ΅ΡΠΏΠ½ΡΡΡ Π΄ΠΎΠ²ΠΎΠ»ΡΠ½ΠΎ ΠΌΠ½ΠΎΠ³ΠΎ ΠΈΠ½ΡΠ΅ΡΠ΅ΡΠ½ΠΎΠΉ ΠΈΠ½ΡΠΎΡΠΌΠ°ΡΠΈΠΈ:
Π§ΡΠΎ ΠΊΠ°ΡΠ°Π΅ΡΡΡ ΠΈΠ·Π³ΠΎΡΠΎΠ²Π»Π΅Π½ΠΈΡ ΡΠΎΡΠΌ ΠΈΠ· Π³ΠΈΠΏΡΠ°, ΡΠΎ Π·Π΄Π΅ΡΡ Π²ΡΠ΅ ΡΠΎΠ²Π΅ΡΡΠ΅Π½Π½ΠΎ ΠΈΠ½Π°ΡΠ΅. ΠΠ»Ρ ΠΈΠ·Π³ΠΎΡΠΎΠ²Π»Π΅Π½ΠΈΡ ΡΠΎΡΠΌΡ Π΄Π»Ρ ΠΏΠΎΡΠ»Π΅Π΄ΡΡΡΠ΅Π³ΠΎ ΠΈΡΠΏΠΎΠ»ΡΠ·ΠΎΠ²Π°Π½ΠΈΡ Π΅Π΅ ΠΏΡΠΈ ΠΈΠ·Π³ΠΎΡΠΎΠ²Π»Π΅Π½ΠΈΠΈ Π»Π΅ΠΏΠ½ΠΈΠ½Ρ ΠΈΠ· Π³ΠΈΠΏΡΠ° Π½Π°ΠΌ ΠΏΠΎΡΡΠ΅Π±ΡΠ΅ΡΡΡ:
- ΡΠΈΠ»ΠΈΠΊΠΎΠ½ Π½Π° ΠΎΡΠ½ΠΎΠ²Π΅ Π°ΠΊΡΠΈΠ»Π° ΠΈΠ»ΠΈ Π΅ΠΌΡ ΠΏΠΎΠ΄ΠΎΠ±Π½ΡΠΉ;
- ΡΠΈΠ»ΠΈΠΊΠΎΠ½ΠΎΠ²ΠΎΠ΅ ΠΌΠ°ΡΠ»ΠΎ;
- ΡΠ°Π·Π΄Π΅Π»ΠΈΡΠ΅Π»ΡΠ½Π°Ρ ΡΠΌΠ°Π·ΠΎΡΠ½Π°Ρ ΡΠΌΠ΅ΡΡ ΠΈΠ»ΠΈ Π°Π½Π°Π»ΠΎΠ³;
- ΡΡΡΠΎΠΈΡΠ΅Π»ΡΠ½ΡΠΉ Π³ΠΈΠΏΡ;
- ΠΌΠ°ΡΠ»Ρ;
Π‘ ΠΌΠ°ΡΠ΅ΡΠΈΠ°Π»Π°ΠΌΠΈ ΠΎΠΏΡΠ΅Π΄Π΅Π»ΠΈΠ»ΠΈΡΡ, Ρ ΠΎΡΡ Π² ΡΠ°Π·Π»ΠΈΡΠ½ΡΡ ΡΠ»ΡΡΠ°ΡΡ ΠΌΠΎΠΆΠ½ΠΎ ΠΈΡΠΏΠΎΠ»ΡΠ·ΠΎΠ²Π°ΡΡ ΠΈ Π΄ΡΡΠ³ΠΎΠΉ Π½Π°Π±ΠΎΡ, ΡΡΡ ΡΠΆ ΠΊΡΠΎ ΠΊ ΡΠ΅ΠΌΡ ΠΏΡΠΈΠ²ΡΠΊ. Π’Π΅ΠΏΠ΅ΡΡ ΠΈΠ½ΡΡΡΡΠΌΠ΅Π½Ρ:
- ΡΠΏΠ°ΡΠ΅Π»ΠΈ;
- ΠΊΠΈΡΡΠΈ;
- ΡΡΠ°ΠΊΠ°Π½ Ρ ΠΌΠ΅ΡΠ½ΡΠΌ Π΄Π΅Π»Π΅Π½ΠΈΠ΅ΠΌ Π»ΠΈΡΠ½ΠΈΠΌ Π½Π΅ Π±ΡΠ΄Π΅Ρ;
- ΡΠΎΠ²Π½Π°Ρ ΠΏΠΎΠ²Π΅ΡΡ Π½ΠΎΡΡΡ Π½Π΅ΠΎΠ±Ρ ΠΎΠ΄ΠΈΠΌΠΎΠ³ΠΎ ΡΠ°Π·ΠΌΠ΅ΡΠ° (Π½Π° Π½Π΅ΠΉ Π±ΡΠ΄Π΅Ρ Π·Π°ΡΡΡΠ²Π°ΡΡ ΡΠΎΡΠΌΠ°, Π΄Π»Ρ ΡΡΠΈΡ ΡΠ΅Π»Π΅ΠΉ ΠΏΠΎΠ΄ΠΎΠΉΠ΄Π΅Ρ ΡΠ°Π½Π΅ΡΠ°, ΡΡΠΎΠ»Π΅ΡΠ½ΠΈΡΠ° ΠΈ ΡΠΏ)
ΠΡΠ½ΠΎΠ²Π½ΡΠΌ, Π½Π° Π΄Π°Π½Π½ΡΠΉ ΠΌΠΎΠΌΠ΅Π½Ρ, ΡΠΎΡΡΠ°Π²Π»ΡΡΡΠΈΠΌ ΡΡΠΏΠ΅ΡΠ½ΠΎΠΉ ΡΠ°Π±ΠΎΡΡ ΡΠ²Π»ΡΠ΅ΡΡΡ ΠΎΠ±ΡΠ°Π·Π΅Ρ. ΠΠ±ΡΠ°Π·Π΅Ρ, ΠΏΠΎ ΠΊΠΎΡΠΎΡΠΎΠΌΡ Π±ΡΠ΄Π΅ΠΌ ΠΎΡΠ»ΠΈΠ²Π°ΡΡ ΡΠΎΡΠΌΡ, ΠΌΠΎΠΆΠ½ΠΎ ΠΏΡΠΈΠΎΠ±ΡΠ΅ΡΡΠΈ Π½Π° ΡΡΠ½ΠΊΠ΅, ΡΡΠΎ ΠΌΠΎΠΆΠ΅Ρ Π±ΡΡΡ Π»Π΅ΠΏΠ½ΠΈΠ½Π° ΠΈΠ· ΠΏΠΎΠ»ΠΈΡΡΠ΅ΡΠ°Π½Π° ΠΈΠ»ΠΈ Π³ΠΈΠΏΡΠ°. Π’Π°ΠΊΠΆΠ΅ ΠΌΠΎΠΆΠ½ΠΎ ΠΎΠ±ΡΠ°Π·Π΅Ρ ΠΈΠ·Π³ΠΎΡΠΎΠ²ΠΈΡΡ ΡΠ°ΠΌΠΎΡΡΠΎΡΡΠ΅Π»ΡΠ½ΠΎ, Π½ΠΎ Π² ΡΡΠΎΠΌ ΡΠ»ΡΡΠ°Π΅ Π½ΡΠΆΠ½ΠΎ ΠΈΠΌΠ΅ΡΡ ΡΠ°Π»Π°Π½Ρ ΠΈ ΠΎΠΏΡΡ ΡΠ°Π±ΠΎΡΡ Ρ Π³ΠΈΠΏΡΠΎΠΌ (ΠΈΠ»ΠΈ ΠΏΠΎΠ΄ΠΎΠ±Π½ΡΠΌΠΈ ΠΌΠ°ΡΠ΅ΡΠΈΠ°Π»Π°ΠΌΠΈ).
ΠΠ»Ρ ΠΏΡΠΈΠ³ΠΎΡΠΎΠ²Π»Π΅Π½ΠΈΡ ΡΠΌΠ΅ΡΠΈ Π½Π΅ΠΎΠ±Ρ ΠΎΠ΄ΠΈΠΌΠΎ ΡΠΌΠ΅ΡΠ°ΡΡ ΡΠΈΠ»ΠΈΠΊΠΎΠ½ Ρ ΡΠΈΠ»ΠΈΠΊΠΎΠ½ΠΎΠ²ΡΠΌ ΠΌΠ°ΡΠ»ΠΎΠΌ. Π‘ΡΠΎΠΈΡ ΠΎΡΠΌΠ΅ΡΠΈΡΡ, ΡΡΠΎ ΡΠΈΠ»ΠΈΠΊΠΎΠ½ΠΎΠ²ΠΎΠ΅ ΠΌΠ°ΡΠ»ΠΎ ΠΈΡΠΏΠΎΠ»ΡΠ·ΡΠ΅ΡΡΡ Π΄Π»Ρ ΠΏΡΠΈΠ΄Π°Π½ΠΈΡ ΡΠΌΠ΅ΡΠΈ ΡΠ»Π°ΡΡΠΈΡΠ½ΠΎΡΡΠΈ, ΠΏΠΎΡΡΠΎΠΌΡ, Π΅ΡΠ»ΠΈ ΡΠΎΡΠΌΠ° Π½Π΅ ΠΎΠ±Π»Π°Π΄Π°Π΅Ρ ΠΊΠ°ΠΊΠΈΠΌΠΈ-Π»ΠΈΠ±ΠΎ ΡΠ»ΠΎΠΆΠ½ΡΠΌΠΈ ΠΎΡΠ΅ΡΡΠ°Π½ΠΈΡΠΌΠΈ, ΠΌΠΎΠΆΠ½ΠΎ ΠΎΠ±ΠΎΠΉΡΠΈΡΡ ΠΈ Π±Π΅Π· ΡΡΠΎΠ³ΠΎ ΠΌΠ°ΡΠ΅ΡΠΈΠ°Π»Π°. ΠΠΎΠ½ΡΠΈΡΡΠ΅Π½ΡΠΈΡ ΡΠΌΠ΅ΡΠΈ Π΄ΠΎΠ»ΠΆΠ½Π° Π±ΡΡΡ ΠΎΠ΄Π½ΠΎΡΠΎΠ΄Π½ΠΎΠΉ, ΡΡΠΎ ΠΎΠ±ΡΠ·Π°ΡΠ΅Π»ΡΠ½ΠΎΠ΅ ΡΡΠ»ΠΎΠ²ΠΈΠ΅.
ΠΠ΅ΡΠ΅Ρ ΠΎΠ΄ΠΈΠΌ ΠΊ ΡΠ°Π±ΠΎΡΠ΅ΠΌΡ ΠΌΠ΅ΡΡΡ, Π³Π΄Π΅ ΡΠΆΠ΅ Π»Π΅ΠΆΠΈΡ Π½Π°Ρ ΠΎΠ±ΡΠ°Π·Π΅Ρ. ΠΠ³ΠΎ, ΠΊΡΡΠ°ΡΠΈ, ΠΆΠ΅Π»Π°ΡΠ΅Π»ΡΠ½ΠΎ ΠΎΠ³ΡΠ°Π΄ΠΈΡΡ, ΡΠ΄Π΅Π»Π°ΡΡ Π±ΠΎΡΡΠΈΠΊΠΈ, ΡΡΠΎΠ±Ρ ΡΠΎΡΠΌΠ° Π±ΡΠ»Π° ΡΠΎΠ²Π½ΠΎΠΉ ΠΈ ΡΠΌΠ΅ΡΡ Π½ΠΈΠΊΡΠ΄Π° Π½Π΅ ΡΡΠ΅ΠΊΠ»Π°.
ΠΠ»Ρ ΠΈΠ·Π³ΠΎΡΠΎΠ²Π»Π΅Π½ΠΈΡ ΡΠΎΡΠΌΡ Π½Π°Π½ΠΎΡΠΈΠΌ ΡΠ°Π·Π΄Π΅Π»ΠΈΡΠ΅Π»ΡΠ½ΡΡ ΡΠΌΠ°Π·ΠΎΡΠ½ΡΡ ΡΠΌΠ΅ΡΡ Π½Π° ΠΎΠ±ΡΠ°Π·Π΅Ρ, ΠΏΠΎΡΠ»Π΅ ΡΡΠΎΠ³ΠΎ ΠΊΠΈΡΡΡΡ Π½Π°Π½ΠΎΡΠΈΠΌ ΡΠΈΠ»ΠΈΠΊΠΎΠ½ΠΎΠ²ΡΡ ΡΠΌΠ΅ΡΡ. ΠΠ° ΠΏΠ΅ΡΠ²ΠΎΠΌ ΡΡΠ°ΠΏΠ΅ ΠΌΡ ΡΠ°Π±ΠΎΡΠ°Π΅ΠΌ ΠΊΠΈΡΡΡΡ, ΡΡΠΎΠ±Ρ Π½Π° ΡΠΎΡΠΌΠ΅ Π½Π΅ Π±ΡΠ»ΠΎ ΠΏΡΠ·ΡΡΡΠΊΠΎΠ² (Π½Π΅Π»ΡΠ·Ρ Π΄ΠΎΠΏΡΡΡΠΈΡΡ ΠΎΠ±ΡΠ°Π·ΠΎΠ²Π°Π½ΠΈΠ΅ ΠΏΡΠ·ΡΡΡΠΊΠΎΠ², ΡΠ°ΠΊ ΠΊΠ°ΠΊ Π²ΡΠ΅ Π΄Π΅ΡΠ°Π»ΠΈ, ΠΈΠ·Π³ΠΎΡΠΎΠ²Π»Π΅Π½Π½ΡΠ΅ Π² ΡΠ°ΠΊΠΎΠΉ ΡΠΎΡΠΌΠ΅ Π±ΡΠ΄ΡΡ Π±ΡΠ°ΠΊΠΎΠ²Π°Π½Π½ΡΠΌΠΈ).
Π‘Π»Π΅Π΄ΡΡΡΠΈΠΉ ΡΡΠ°ΠΏ ΠΏΠΎΠ΄ΡΠ°Π·ΡΠΌΠ΅Π²Π°Π΅Ρ Π°ΡΠΌΠΈΡΠΎΠ²Π°Π½ΠΈΠ΅ ΡΠΎΡΠΌΡ, ΡΡΠΎΠ±Ρ ΠΏΡΠΈΠ΄Π°ΡΡ Π΅ΠΉ ΠΏΡΠΎΡΠ½ΠΎΡΡΠΈ. ΠΠ° Π΅ΡΠ΅ Π½Π΅ Π·Π°ΡΡΡΠ²ΡΠΈΠΉ ΡΠΈΠ»ΠΈΠΊΠΎΠ½ ΡΠΊΠ»Π°Π΄ΡΠ²Π°Π΅ΠΌ ΠΌΠ°ΡΠ»Ρ, Π΄Π΅Π»Π°Π΅ΠΌ ΡΡΠΎ ΠΏΡΠ΅Π΄Π΅Π»ΡΠ½ΠΎ ΠΎΡΡΠΎΡΠΎΠΆΠ½ΠΎ. ΠΠ°Π»ΠΈΠ²Π°Π΅ΠΌ ΡΠΈΠ»ΠΈΠΊΠΎΠ½ΠΎΠΌ Π΅ΡΠ΅ Π½Π΅ΡΠΊΠΎΠ»ΡΠΊΠΎ ΡΠ»ΠΎΠ΅Π². Π‘ΠΊΠΎΠ»ΡΠΊΠΎ ΠΎΠ½ Π±ΡΠ΄Π΅Ρ ΠΏΠΎΠ΄ΡΡΡ Π°ΡΡ ΡΠΈΡΠ°Π΅ΠΌ Π² ΠΈΠ½ΡΡΡΡΠΊΡΠΈΠΈ.
ΠΡΠ»ΠΈ ΡΠΎΡΠΌΠ° Π±ΠΎΠ»ΡΡΠ°Ρ, ΠΌΠΎΠΆΠ½ΠΎ Π΄Π»Ρ Π½Π΅Π΅ ΠΈΠ·Π³ΠΎΡΠΎΠ²ΠΈΡΡ ΠΎΡΠ½ΠΎΠ²Π°Π½ΠΈΠ΅ ΠΈΠ· Π³ΠΈΠΏΡΠ°. ΠΠ»Ρ ΡΡΠΎΠ³ΠΎ Π±ΠΎΡΡΠΈΠΊΠΈ Π·Π°Π±Π»Π°Π³ΠΎΠ²ΡΠ΅ΠΌΠ΅Π½Π½ΠΎ Π΄Π΅Π»Π°Π΅ΠΌ Π±ΠΎΠ»ΡΡΠ΅Π³ΠΎ ΡΠ°Π·ΠΌΠ΅ΡΠ° ΠΈ ΠΏΠΎΠ²Π΅ΡΡ ΡΠΈΠ»ΠΈΠΊΠΎΠ½Π° Π·Π°Π»ΠΈΠ²Π°Π΅ΠΌ Π΅ΡΠ΅ ΠΈ Π³ΠΈΠΏΡ (ΡΠΌΠ΅ΡΡ Π³ΠΈΠΏΡΠ°, ΠΊΠ»Π΅Ρ ΠΠΠ ΠΈ ΡΠ΅ΠΌΠ΅Π½ΡΠ°).
Π’Π΅Ρ Ρ Π½ΠΎΠ»ΠΎΠ³ΠΈΡ ΠΈΠ·Π³ΠΎΡΠΎΠ²Π»Π΅Π½ΠΈΡ Π»Π΅ΠΏΠ½ΠΈΠ½Ρ ΠΈΠ· ΠΏΠΎΠ»ΠΈΡΡΠ΅ΡΠ°Π½Π°…
Π€Π°ΡΠ°Π΄Π½ΡΠΉ ΠΈ ΠΈΠ½ΡΠ΅ΡΡΠ΅ΡΠ½ΡΠΉ Π»Π΅ΠΏΠ½ΠΎΠΉ Π΄Π΅ΠΊΠΎΡ, ΠΏΡΠ΅Π΄Π»Π°Π³Π°Π΅ΠΌΡΠΉ Π½Π°ΡΠ΅ΠΉ ΠΊΠΎΠΌΠΏΠ°Π½ΠΈΠ΅ΠΉ, ΠΏΡΠΎΠΈΠ·Π²ΠΎΠ΄ΠΈΡΡΡ ΠΈΠ· Π²ΡΡΠΎΠΊΠΎΠΊΠ°ΡΠ΅ΡΡΠ²Π΅Π½Π½ΠΎΠ³ΠΎ ΠΏΠΎΠ»ΠΈΠΌΠ΅ΡΠ° β ΠΏΠ΅Π½ΠΎΠΏΠΎΠ»ΠΈΡΡΠ΅ΡΠ°Π½Π° (ΠΠΠ£).
Π’Π΅Ρ
Π½ΠΎΠ»ΠΎΠ³ΠΈΡ ΠΏΡΠΎΠΈΠ·Π²ΠΎΠ΄ΡΡΠ²Π° Π»Π΅ΠΏΠ½ΠΈΠ½Ρ ΠΈΠ· ΠΏΠΎΠ»ΠΈΡΡΠ΅ΡΠ°Π½Π° Π±ΡΠ»Π° ΡΠ°Π·ΡΠ°Π±ΠΎΡΠ°Π½Π° Π² Π‘Π¨Π Π² 70Ρ
Π³ΠΎΠ΄Π°Ρ
, Π±ΡΡΡΡΠΎ ΠΏΡΠΈΠΎΠ±ΡΠ΅Π»Π° ΠΏΠΎΠΏΡΠ»ΡΡΠ½ΠΎΡΡΡ ΠΈ ΡΠ°ΡΠΏΡΠΎΡΡΡΠ°Π½ΠΈΠ»Π°ΡΡ ΠΊΠ°ΠΊ Π² Π‘Π¨Π, ΡΠ°ΠΊ ΠΈ Π² ΠΠ²ΡΠΎΠΏΠ΅. ΠΠ»ΠΎΡΠ½Π°Ρ ΠΏΠΎΠ»ΠΈΡΡΠ΅ΡΠ°Π½ΠΎΠ²Π°Ρ ΠΏΠ΅Π½Π° ΠΎΠ±ΡΠ°Π·ΡΠ΅ΡΡΡ ΠΈΠ· Π΄Π²ΡΡ
ΠΊΠΎΠΌΠΏΠΎΠ½Π΅Π½ΡΠΎΠ², ΠΊΠΎΡΠΎΡΡΠ΅ Π² ΠΏΡΠΎΡΠ΅ΡΡΠ΅ ΡΠ΅Π°ΠΊΡΠΈΠΈ Π²ΡΠ΄Π΅Π»ΡΡΡ ΡΠ΅ΠΏΠ»ΠΎ. ΠΠ΄ΠΈΠ½ ΠΊΠΎΠΌΠΏΠΎΠ½Π΅Π½Ρ ΡΠΎΠ΄Π΅ΡΠΆΠΈΡ Π²ΠΎΠ΄Ρ, Π΄ΡΡΠ³ΠΎΠΉ Ρ Π²ΠΎΠ΄ΠΎΠΉ ΡΠ΅Π°Π³ΠΈΡΡΠ΅Ρ. ΠΠΈΡΠ»ΠΎΡΠΎΠ΄ Π²ΠΎΠ΄Ρ Π·Π°ΠΏΡΡΠΊΠ°Π΅Ρ ΡΠΊΠ·ΠΎΡΠ΅ΡΠΌΠΈΡΠ΅ΡΠΊΡΡ ΡΠ΅Π°ΠΊΡΠΈΡ, Π² ΠΏΡΠΎΡΠ΅ΡΡΠ΅ ΠΊΠΎΡΠΎΡΠΎΠΉ ΡΠΎΡΠΌΠΈΡΡΡΡΡΡ ΠΏΡΠ·ΡΡΡΠΊΠΈ Π²ΠΎΠ΄ΠΎΡΠΎΠ΄Π° β ΠΏΡΠΎΠΈΡΡ
ΠΎΠ΄ΠΈΡ Π²ΡΠΏΠ΅Π½ΠΈΠ²Π°Π½ΠΈΠ΅. ΠΡΠ»ΠΈ ΡΡΠΎΡ ΠΏΡΠΎΡΠ΅ΡΡ ΠΈΠ΄ΡΡ ΡΠ²ΠΎΠ±ΠΎΠ΄Π½ΠΎ, Π½Π΅ ΠΏΠΎΠ΄ ΠΏΡΠ΅ΡΡΠΎΠΌ ΡΠΎΡΠΌΡ β ΠΏΠ΅Π½Π° ΠΏΠΎΠ΄Π½ΠΈΠΌΠ°Π΅ΡΡΡ ΠΏΠΎ ΠΌΠ΅ΡΠ΅ Ρ
ΠΎΠ΄Π° Ρ
ΠΈΠΌΠΈΡΠ΅ΡΠΊΠΎΠΉ ΡΠ΅Π°ΠΊΡΠΈΠΈ ΠΈ ΡΠΎΡΠΌΠΈΡΡΠ΅Ρ Π½Π΅ΠΏΠ»ΠΎΡΠ½ΡΡ ΡΠ°ΠΏΠΊΡ. ΠΠ½Π°Ρ ΠΏΡΠΎΠΏΠΎΡΡΠΈΠΈ Π΄Π²ΡΡ
ΠΊΠΎΠΌΠΏΠΎΠ½Π΅Π½ΡΠΎΠ², ΠΌΠΎΠΆΠ½ΠΎ ΡΠ°ΡΡΡΠΈΡΠ°ΡΡ, ΠΊΠ°ΠΊΠΎΠ΅ ΠΈΡ
ΠΊΠΎΠ»ΠΈΡΠ΅ΡΡΠ²ΠΎ Π½Π΅ΠΎΠ±Ρ
ΠΎΠ΄ΠΈΠΌΠΎ Π΄Π»Ρ ΠΎΠ±ΡΠ°Π·ΠΎΠ²Π°Π½ΠΈΡ Π½ΡΠΆΠ½ΠΎΠ³ΠΎ ΠΎΠ±ΡΡΠΌΠ° ΠΏΠ΅Π½Ρ.Β ΠΠΎ Π΅ΡΡ Π±ΠΎΠ»Π΅Π΅ Π²Π°ΠΆΠ½ΠΎ ΡΠΎ, ΡΡΠΎ Π²ΠΎΠ·ΠΌΠΎΠΆΠ½ΠΎ ΠΏΡΠΎΠΈΠ·Π²ΠΎΠ΄ΠΈΡΡ ΠΈΠ·Π΄Π΅Π»ΠΈΡ Π²ΡΡΠΎΠΊΠΎΠΉ ΠΏΠ»ΠΎΡΠ½ΠΎΡΡΠΈ, Π·Π°Π»ΠΈΠ²Π°Ρ ΡΠ°ΡΡΡΠΈΡΠ°Π½Π½ΠΎΠ΅ ΠΊΠΎΠ»ΠΈΡΠ΅ΡΡΠ²ΠΎ ΠΊΠΎΠΌΠΏΠΎΠ½Π΅Π½ΡΠΎΠ² Π² Π·Π°ΠΌΠΊΠ½ΡΡΡΡ ΡΠΎΡΠΌΡ ΠΏΠΎΠ΄ Π΄Π°Π²Π»Π΅Π½ΠΈΠ΅ΠΌ.
Π’Π°ΠΊΠΈΠ΅ ΠΈΠ·Π΄Π΅Π»ΠΈΡ ΠΈΠ· ΠΏΠΎΠ»ΠΈΡΡΠ΅ΡΠ°Π½Π° ΠΏΠΎ ΡΡΠ΅ΠΏΠ΅Π½ΠΈ ΠΏΠ»ΠΎΡΠ½ΠΎΡΡΠΈ ΡΠΎΠΏΠΎΡΡΠ°Π²ΠΈΠΌΡ Ρ ΠΈΠ·Π΄Π΅Π»ΠΈΡΠΌΠΈ ΠΈΠ· Ρ Π²ΠΎΠΉΠ½ΡΡ ΠΏΠΎΡΠΎΠ΄ Π΄Π΅ΡΠ΅Π²Π°.
Π ΡΠ°ΡΡΠ½ΠΎΡΡΠΈ, ΠΏΠΎΡΡΠΎΠΌΡ ΠΎΠ½ΠΈ Π»Π΅Π³ΠΊΠΎ ΠΏΠΎΠ΄Π΄Π°ΡΡΡΡ ΠΎΠ±ΡΠ°Π±ΠΎΡΠΊΠ΅ — ΠΈΡ ΠΌΠΎΠΆΠ½ΠΎ ΡΠ°ΡΠΏΠΈΠ»ΠΈΠ²Π°ΡΡ, Π·Π°ΡΠΊΡΡΠΈΠ²Π°ΡΡ, Π²Π±ΠΈΠ²Π°ΡΡ Π² Π½ΠΈΡ Π³Π²ΠΎΠ·Π΄ΠΈ β ΡΠ°ΠΊ ΠΆΠ΅, ΠΊΠ°ΠΊ Π² Π΄Π΅ΡΠ΅Π²ΠΎ.Β ΠΠΎ, Π² ΠΎΡΠ»ΠΈΡΠΈΠ΅ ΠΎΡ Π΄Π΅ΡΠ΅Π²Π°, ΠΏΠΎΠ»ΠΈΠΌΠ΅ΡΠ½ΡΠΉ ΠΌΠ°ΡΠ΅ΡΠΈΠ°Π» Π½Π΅ Π±ΡΠ΄Π΅Ρ Π³Π½ΠΈΡΡ, ΡΠ°ΡΡΡΠ΅ΡΠΊΠΈΠ²Π°ΡΡΡΡ ΠΈ ΠΏΠΎΠ΅Π΄Π°ΡΡΡΡ Π½Π°ΡΠ΅ΠΊΠΎΠΌΡΠΌΠΈ.
ΠΠ»Ρ ΡΠΎΠ³ΠΎ, ΡΡΠΎΠ±Ρ ΠΏΠΎΠ»ΡΡΠΈΡΡ Π»ΡΠ³ΠΊΠΈΠΉ ΠΏΠΎΠ»ΠΈΠΌΠ΅Ρ ΠΏΠ»ΠΎΡΠ½ΠΎΡΡΡΡ ΠΊΠ°ΠΊ Π΄Π΅ΡΠ΅Π²ΠΎ, Π½Π΅ΠΎΠ±Ρ
ΠΎΠ΄ΠΈΠΌΠ° ΠΎΠ³ΡΠΎΠΌΠ½Π°Ρ ΠΊΠΎΠΌΠΏΡΠ΅ΡΡΠΈΡ. ΠΡΠΎΠΌΠ΅ ΡΠΎΠ³ΠΎ, ΠΏΠΎΠ²Π΅ΡΡ
Π½ΠΎΡΡΡ ΠΈΠ·Π΄Π΅Π»ΠΈΡ Π΄ΠΎΠ»ΠΆΠ½Π° Π±ΡΡΡ ΠΊΠ°ΡΠ΅ΡΡΠ²Π΅Π½Π½ΠΎΠΉ. ΠΡΠΎ ΠΎΠ·Π½Π°ΡΠ°Π΅Ρ, ΡΡΠΎ ΡΠΎΡΠΌΠ° Π΄ΠΎΠ»ΠΆΠ½Π° Π±ΡΡΡ Π΄ΠΎΡΡΠ°ΡΠΎΡΠ½ΠΎ ΠΊΡΠ΅ΠΏΠΊΠΎΠΉ, ΡΡΠΎΠ±Ρ Π²ΡΠ΄Π΅ΡΠΆΠ°ΡΡ Π΄Π°Π²Π»Π΅Π½ΠΈΠ΅ ΡΠ°ΡΡΠΈΡΡΡΡΠ΅ΠΉΡΡ ΠΏΠ΅Π½Ρ, ΠΈ Π²ΡΡΠΎΠΊΠΎΠΊΠ°ΡΠ΅ΡΡΠ²Π΅Π½Π½ΠΎΠΉ β ΡΡΠΎΠ±Ρ Π΄Π΅ΠΊΠΎΡΠ°ΡΠΈΠ²Π½ΡΠΉ ΡΠ»Π΅ΠΌΠ΅Π½Ρ ΠΌΠΎΠ³ ΠΈΠΌΠ΅ΡΡ ΡΠΎΡΠ½ΡΡ Π΄Π΅ΡΠ°Π»ΠΈΠ·Π°ΡΠΈΡ.
Π’Π°ΠΊΠΈΠΌ ΠΎΠ±ΡΠ°Π·ΠΎΠΌ, Ρ ΠΎΡΡ Π΄Π΅ΠΊΠΎΡΠ°ΡΠΈΠ²Π½ΡΠ΅ ΡΠ»Π΅ΠΌΠ΅Π½ΡΡ ΠΈΠ· ΠΏΠ»ΠΎΡΠ½ΠΎΠ³ΠΎ ΠΏΠΎΠ»ΠΈΡΡΠ΅ΡΠ°Π½Π° ΠΊΡΠ΅ΠΏΠΊΠΈΠ΅ ΠΈ Π»ΡΠ³ΠΊΠΈΠ΅, ΡΠΎΡΠΌΡ, Π² ΠΊΠΎΡΠΎΡΡΡ ΠΎΠ½ΠΈ ΠΈΠ·Π³ΠΎΡΠ°Π²Π»ΠΈΠ²Π°ΡΡΡΡ, ΠΎΡΠ΅Π½Ρ ΡΡΠΆΡΠ»ΡΠ΅ β ΡΠ°ΡΡΠΎ ΠΌΠ΅ΡΠ°Π»Π»ΠΈΡΠ΅ΡΠΊΠΈΠ΅. ΠΡΡ ΡΡΠΎ ΡΠΎΠ·Π΄Π°ΡΡ ΠΏΡΠΎΠΈΠ·Π²ΠΎΠ΄ΡΡΠ²Π΅Π½Π½ΡΡ ΡΠΏΠ΅ΡΠΈΡΠΈΠΊΡ ΡΠ΅Ρ Π½ΠΎΠ»ΠΎΠ³ΠΈΡΠ΅ΡΠΊΠΎΠ³ΠΎ ΠΏΡΠΎΡΠ΅ΡΡΠ°: ΠΈΠ·Π³ΠΎΡΠΎΠ²Π»Π΅Π½ΠΈΠ΅ Π»Π΅ΠΏΠ½ΠΈΠ½Ρ ΠΈΠ· ΠΏΠΎΠ»ΠΈΡΡΠ΅ΡΠ°Π½Π° Π΄Π»Ρ ΡΠ°ΡΠ°Π΄Π½ΠΎΠ³ΠΎ ΠΈ ΠΈΠ½ΡΠ΅ΡΡΠ΅ΡΠ½ΠΎΠ³ΠΎ Π΄Π΅ΠΊΠΎΡΠ° ΡΡΠ΅Π±ΡΠ΅Ρ ΡΡΡΠ΄ ΠΊΠ²Π°Π»ΠΈΡΠΈΡΠΈΡΠΎΠ²Π°Π½Π½ΡΡ ΡΠ΅Ρ Π½ΠΈΡΠ΅ΡΠΊΠΈΡ ΡΠΏΠ΅ΡΠΈΠ°Π»ΠΈΡΡΠΎΠ². Π ΡΡΡΠ΅ΠΌΠ»Π΅Π½ΠΈΠ΅ ΠΊ ΠΈΠ΄Π΅Π°Π»ΡΠ½ΠΎΠΌΡ ΠΈΡΠΏΠΎΠ»Π½Π΅Π½ΠΈΡ Π»Π΅ΠΏΠ½ΡΡ ΡΠ°ΡΠ°Π΄Π½ΡΡ ΠΈ ΠΈΠ½ΡΠ΅ΡΡΠ΅ΡΠ½ΡΡ ΡΠ»Π΅ΠΌΠ΅Π½ΡΠΎΠ² (Π½Π°ΠΏΡΠΈΠΌΠ΅Ρ, ΠΌΠΎΠ»Π΄ΠΈΠ½Π³ΠΎΠ², ΠΊΠ°ΡΠ½ΠΈΠ·ΠΎΠ² ΠΈ Π±Π°Π»ΡΡΠΈΠ½) Π²Π΅Π΄ΡΡ ΠΊ ΡΡΡΠΎΠ³ΠΎΠΌΡ ΠΊΠΎΠ½ΡΡΠΎΠ»Ρ ΠΊΠ°ΡΠ΅ΡΡΠ²Π° Π½Π° Π²ΡΠ΅Ρ ΡΡΠ°ΡΡΠΊΠ°Ρ ΠΏΡΠΎΠΈΠ·Π²ΠΎΠ΄ΡΡΠ²Π΅Π½Π½ΠΎΠ³ΠΎ ΠΏΡΠΎΡΠ΅ΡΡΠ°.
ΠΠ°ΡΠ΅ ΠΏΡΠΎΠΈΠ·Π²ΠΎΠ΄ΡΡΠ²ΠΎ ΠΏΠΎΠ·Π²ΠΎΠ»ΡΠ΅Ρ Π½Π°ΠΌ Π²ΡΠΏΠΎΠ»Π½ΡΡΡ ΠΈΠ½Π΄ΠΈΠ²ΠΈΠ΄ΡΠ°Π»ΡΠ½ΡΠ΅ Π·Π°ΠΊΠ°Π·Ρ Π½Π° ΠΈΠ·Π³ΠΎΡΠΎΠ²Π»Π΅Π½ΠΈΠ΅ Π»Π΅ΠΏΠ½ΠΈΠ½Ρ ΠΈΠ· ΠΏΠΎΠ»ΠΈΡΡΠ΅ΡΠ°Π½Π°.
ΠΡ ΠΌΠΎΠΆΠ΅ΡΠ΅ Π·Π°ΠΊΠ°Π·Π°ΡΡ ΠΈΠ·Π³ΠΎΡΠΎΠ²Π»Π΅Π½ΠΈΠ΅ ΠΈΠ½Π΄ΠΈΠ²ΠΈΠ΄ΡΠ°Π»ΡΠ½ΠΎΠ³ΠΎ Π΄Π΅ΠΊΠΎΡΠ°ΡΠΈΠ²Π½ΠΎΠ³ΠΎ ΠΈΠ·Π΄Π΅Π»ΠΈΡ ΠΈΠ· ΠΏΠΎΠ»ΠΈΡΡΠ΅ΡΠ°Π½Π° ΠΏΠΎ ΡΠ²ΠΎΠΈΠΌ ΡΠ΅ΡΡΠ΅ΠΆΠ°ΠΌ, ΡΡΠΊΠΈΠ·Π°ΠΌ ΠΈΠ»ΠΈ ΠΏΡΠΎΡΡΠΎ ΡΠ°ΡΡΠΊΠ°Π·Π°Π² Π½Π°ΡΠΈΠΌ ΡΠΏΠ΅ΡΠΈΠ°Π»ΠΈΡΡΠ°ΠΌ ΡΠ²ΠΎΠΈ ΠΏΠΎΠΆΠ΅Π»Π°Π½ΠΈΡ.
ΠΠΎΡΡΡΠ°Ρ ΡΠ°Π·ΡΠ°Π±ΠΎΡΠΊΡ ΠΈ ΠΈΠ·Π³ΠΎΡΠΎΠ²Π»Π΅Π½ΠΈΠ΅ ΠΏΠΎΠ»ΠΈΡΡΠ΅ΡΠ°Π½ΠΎΠ²ΠΎΠΉ Π»Π΅ΠΏΠ½ΠΈΠ½Ρ Π½Π°ΡΠ΅ΠΉ ΠΊΠΎΠΌΠΏΠ°Π½ΠΈΠΈ, ΠΡ ΠΏΠΎΠ»ΡΡΠ°Π΅ΡΠ΅ Π²ΠΎΠ·ΠΌΠΎΠΆΠ½ΠΎΡΡΡ ΠΎΡΡΠ»Π΅ΠΆΠΈΠ²Π°ΡΡ ΠΏΡΠΎΡΠ΅ΡΡ ΡΠΎΠ·Π΄Π°Π½ΠΈΡ ΠΈΠ·Π΄Π΅Π»ΠΈΠΉ, ΠΊΠΎΠ½ΡΡΠ»ΡΡΠΈΡΠΎΠ²Π°ΡΡΡΡ Ρ Π½Π°ΡΠΈΠΌΠΈ Π»ΡΡΡΠΈΠΌΠΈ ΡΠΏΠ΅ΡΠΈΠ°Π»ΠΈΡΡΠ°ΠΌΠΈ ΠΈ ΠΏΡΠΈ Π½Π΅ΠΎΠ±Ρ
ΠΎΠ΄ΠΈΠΌΠΎΡΡΠΈ Π²Π½ΠΎΡΠΈΡΡ ΠΊΠΎΡΡΠ΅ΠΊΡΠΈΡΠΎΠ²ΠΊΠΈ.
ΠΡ Π³ΠΎΡΠΎΠ²Ρ ΠΈΠ·Π³ΠΎΡΠ°Π²Π»ΠΈΠ²Π°ΡΡ ΡΠ»Π΅ΠΌΠ΅Π½ΡΡΒ Π»Π΅ΠΏΠ½ΠΎΠ³ΠΎ Π΄Π΅ΠΊΠΎΡΠ° Π΄Π»Ρ ΠΎΠ±Π»ΠΈΡΠΎΠ²ΠΊΠΈ ΡΠ°ΡΠ°Π΄Π° ΠΈ Π΄Π΅ΠΊΠΎΡΠΈΡΠΎΠ²Π°Π½ΠΈΡ ΠΈΠ½ΡΠ΅ΡΡΠ΅ΡΠ° Π΄Π°ΠΆΠ΅ Π² Π΅Π΄ΠΈΠ½ΠΈΡΠ½ΠΎΠΌ ΡΠΊΠ·Π΅ΠΌΠΏΠ»ΡΡΠ΅.
ΠΠ·Π³ΠΎΡΠΎΠ²Π»Π΅Π½ΠΈΠ΅ ΡΠΎΡΠΌ Π΄Π»Ρ Π»Π΅ΠΏΠ½ΠΈΠ½Ρ ΠΈΒ Π΄Π΅ΠΊΠΎΡΠ°ΡΠΈΠ²Π½ΡΡ ΡΠ»Π΅ΠΌΠ΅Π½ΡΠΎΠ² ΠΈΠ· ΠΏΠΎΠ»ΠΈΡΡΠ΅ΡΠ°Π½Π°, ΠΈΠ·Π³ΠΎΡΠΎΠ²Π»Π΅Π½ΠΈΠ΅ Π»Π΅ΠΏΠ½ΠΎΠ³ΠΎ Π΄Π΅ΠΊΠΎΡΠ°.
ΠΡΠΎΠΈΠ·Π²ΠΎΠ΄ΡΡΠ²ΠΎ ΡΠΎΡΠΌ Π΄Π»Ρ ΠΈΠ·Π³ΠΎΡΠΎΠ²Π»Π΅Π½ΠΈΡ Π»Π΅ΠΏΠ½ΠΈΠ½Ρ ΠΈΠ· ΠΏΠΎΠ»ΠΈΡΡΠ΅ΡΠ°Π½Π°. ΠΠΎΡΠ»Π΅ ΠΈΠ·Π³ΠΎΡΠΎΠ²Π»Π΅Π½ΠΈΡ ΠΏΡΠΎΡΠΈΠ»Ρ ΡΠΎΡΠΌΡ ΠΎΠ½Π° ΠΏΡΠΎΡ ΠΎΠ΄ΠΈΡ ΠΏΠΎΠ΄Π³ΠΎΡΠΎΠ²ΠΊΡ Π΄Π»Ρ ΠΏΡΡΠΊΠ° Π² ΠΏΡΠΎΠΈΠ·Π²ΠΎΠ΄ΡΡΠ²ΠΎ. Π ΡΠ»ΡΡΠ°Π΅ ΠΈΠ·Π³ΠΎΡΠΎΠ²Π»Π΅Π½ΠΈΡ ΡΠ΅Ρ Π½ΠΎΠ»ΠΎΠ³ΠΈΡΠ΅ΡΠΊΠΈ ΡΠ»ΠΎΠΆΠ½ΡΡ ΠΈΠ·Π΄Π΅Π»ΠΈΠΉ ΡΠΏΠ΅ΡΠ²Π° ΡΠΎΠ·Π΄Π°ΡΡΡΡ ΠΌΠΎΠ΄Π΅Π»Ρ ΠΈΠ·Π΄Π΅Π»ΠΈΡ, ΠΏΠΎΡΠΎΠΌ β ΡΠΎΡΠΌΠ°. Π’Π°ΠΊΠΆΠ΅, Π΅ΡΠ»ΠΈ Π½Π΅ΠΎΠ±Ρ ΠΎΠ΄ΠΈΠΌΠΎ ΠΈΠ·Π³ΠΎΡΠΎΠ²ΠΈΡΡ Ρ ΡΠ΄ΠΎΠΆΠ΅ΡΡΠ²Π΅Π½Π½ΠΎΠ΅ ΠΈΠ·Π΄Π΅Π»ΠΈΠ΅ (ΠΊ ΠΏΡΠΈΠΌΠ΅ΡΡ, ΡΠΈΠ³ΡΡΠ½ΡΠΉ Π±Π°ΡΠ΅Π»ΡΠ΅Ρ), Π² Π³ΠΈΠΏΡΠΎΠ²ΠΎΠΉ ΠΌΠ°ΡΡΠ΅ΡΡΠΊΠΎΠΉ ΡΠΊΡΠ»ΡΠΏΡΠΎΡΡ ΠΈΠ·Π³ΠΎΡΠ°Π²Π»ΠΈΠ²Π°ΡΡ ΠΏΡΠΎΡΠΎΡΠΈΠΏ ΠΈΠ·Π΄Π΅Π»ΠΈΡ.
Β
Β
ΠΠΎΠΊΡΠ°ΡΠΊΠ° ΡΠΎΡΠΌΡ ΠΈ Π·Π°Π»ΠΈΠ²ΠΊΠ° ΠΏΠ΅Π½ΠΎΠΏΠΎΠ»ΠΈΡΡΠ΅ΡΠ°Π½Π° (ΠΠΠ£). ΠΠ΅ΡΠ΅Π΄ Π½Π°ΡΠ°Π»ΠΎΠΌ ΠΏΡΠΎΠΈΠ·Π²ΠΎΠ΄ΡΡΠ²Π΅Π½Π½ΠΎΠ³ΠΎ ΠΏΡΠΎΡΠ΅ΡΡΠ° ΡΠΎΡΠΌΠ° ΠΎΠ±ΡΠ°Π±Π°ΡΡΠ²Π°Π΅ΡΡΡ. ΠΠ°Π»Π΅Π΅ Π·Π°Π»ΠΈΠ²Π°Π΅ΡΡΡ ΡΠΌΠ΅ΡΡ ΠΏΠΎΠ»ΠΈΠΎΠ»Π° ΠΈ ΠΈΠ·ΠΎΡΠΈΠ°Π½Π°ΡΠ°, ΡΠΎΡΠΌΠ° Π·Π°ΠΊΡΡΠ²Π°Π΅ΡΡΡ ΠΈ Π² Π½Π΅ΠΉ ΠΏΡΠΎΠΈΡΡ ΠΎΠ΄ΠΈΡ ΡΠ΅Π°ΠΊΡΠΈΡ Π²ΡΠΏΠ΅Π½ΠΈΠ²Π°Π½ΠΈΡ, Π²ΡΠ»Π΅Π΄ΡΡΠ²ΠΈΠ΅ ΠΊΠΎΡΠΎΡΠΎΠΉ ΠΎΠ±ΡΠ°Π·ΡΠ΅ΡΡΡ ΠΏΠ΅Π½ΠΎΠΏΠΎΠ»ΠΈΡΡΠ΅ΡΠ°Π½ (ΠΠΠ£).
Β
ΠΠ°Π»Π΅Π΅ ΠΊΠ°ΠΆΠ΄ΠΎΠ΅ ΠΈΠ·Π΄Π΅Π»ΠΈΠ΅ ΠΏΡΠΎΡ
ΠΎΠ΄ΠΈΡ Π΄ΠΎΠΏΠΎΠ»Π½ΠΈΡΠ΅Π»ΡΠ½ΡΡ ΠΎΠ±ΡΠ°Π±ΠΎΡΠΊΡ β ΡΠ»ΠΈΡΠΎΠ²ΠΊΡ ΠΈ ΠΏΠΎΠΊΡΠ°ΡΠΊΡ. Π¨Π»ΠΈΡΠΎΠ²ΠΊΠ° Π½Π΅ΠΎΠ±Ρ
ΠΎΠ΄ΠΈΠΌΠ° Π΄Π»Ρ ΡΠΎΠ³ΠΎ, ΡΡΠΎΠ±Ρ ΡΡΡΡΠ°Π½ΠΈΡΡ ΠΌΠ΅Π»ΠΊΠΈΠ΅ Π½Π΅ΡΠΎΡΠ½ΠΎΡΡΠΈ, ΠΏΡΠ°ΠΊΡΠΈΡΠ΅ΡΠΊΠΈ Π½Π΅ΠΈΠ·Π±Π΅ΠΆΠ½ΡΠ΅ Π² ΠΏΠΎΠ»ΠΈΡΡΠ΅ΡΠ°Π½ΠΎΠ²ΠΎΠΌ ΠΏΡΠΎΠΈΠ·Π²ΠΎΠ΄ΡΡΠ²Π΅. ΠΠ»Ρ ΠΊΠ»ΠΈΠ΅Π½ΡΠ° ΡΡΠΎ Π·Π½Π°ΡΠΈΡ, ΡΡΠΎ ΠΊΠ°ΠΆΠ΄ΠΎΠ΅ ΠΈΠ·Π΄Π΅Π»ΠΈΠ΅ Π±ΡΠ»ΠΎ ΡΡΠ°ΡΠ΅Π»ΡΠ½ΠΎ ΠΏΡΠΎΠ²Π΅ΡΠ΅Π½ΠΎ Π²ΡΡΡΠ½ΡΡ.
Β
ΠΠΎΠΊΡΠ°ΡΠΊΠ° ΠΈΠ·Π΄Π΅Π»ΠΈΡ ΡΠ°ΠΊΠΆΠ΅ Π²ΠΊΠ»ΡΡΠ°Π΅Ρ Π² ΡΠ΅Π±Ρ Π½Π°Π½Π΅ΡΠ΅Π½ΠΈΠ΅ Π·Π°ΡΠΈΡΠ½ΠΎΠ³ΠΎ ΠΏΠΎΠΊΡΡΡΠΈΡ, ΠΏΡΠ΅ΠΏΡΡΡΡΠ²ΡΡΡΠ΅Π³ΠΎ Π½Π΅Π±Π»Π°Π³ΠΎΠΏΡΠΈΡΡΠ½ΠΎΠΌΡ Π²ΠΎΠ·Π΄Π΅ΠΉΡΡΠ²ΠΈΡ ΡΠ»ΡΡΡΠ°ΡΠΈΠΎΠ»Π΅ΡΠΎΠ²ΡΡ (Π£Π€) Π»ΡΡΠ΅ΠΉ Π½Π° ΡΠ»Π΅ΠΌΠ΅Π½ΡΡ ΡΠ°ΡΠ°Π΄Π½ΠΎΠ³ΠΎ Π΄Π΅ΠΊΠΎΡΠ°. Π’Π°ΠΊΠΈΠΌ ΠΎΠ±ΡΠ°Π·ΠΎΠΌ ΠΈΠ·Π΄Π΅Π»ΠΈΠ΅ Π±ΡΠ΄Π΅Ρ ΡΠ»ΡΠΆΠΈΡΡ Π΄ΠΎΠ»ΡΡΠ΅ ΠΈ Π½Π΅ ΡΡΠ΅Π±ΠΎΠ²Π°ΡΡ ΡΠ΅ΠΌΠΎΠ½ΡΠ° ΠΌΠ½ΠΎΠ³ΠΎ Π»Π΅Ρ.
Β
Π₯ΡΠ°Π½ΡΡΡΡ ΠΈΠ·Π΄Π΅Π»ΠΈΡ Π½Π° ΠΎΠ±ΡΠΈΡΠ½ΡΡ ΡΠΊΠ»Π°Π΄Π°Ρ ΠΏΡΠΈ ΠΏΡΠΎΠΈΠ·Π²ΠΎΠ΄ΡΡΠ²Π΅. ΠΠ°Π»ΠΈΡΠΈΠ΅ ΡΠΊΠ»Π°Π΄ΠΎΠ² ΠΈ ΠΏΠΎΡΡΠΎΡΠ½Π½ΠΎ ΠΏΠΎΠ΄Π΄Π΅ΡΠΆΠΈΠ²Π°Π΅ΠΌΡΡ Π·Π°ΠΏΠ°ΡΠΎΠ² ΠΈΠ·Π΄Π΅Π»ΠΈΠΉ ΠΏΠΎΠ·Π²ΠΎΠ»ΡΠ΅Ρ Π½Π°ΠΌ Π±ΡΡΡΡΠ΅Π΅ Π²ΡΠΏΠΎΠ»Π½ΡΡΡ Π·Π°ΠΊΠ°Π·Ρ Π½Π°ΡΠΈΡ ΠΊΠ»ΠΈΠ΅Π½ΡΠΎΠ². Π‘ΠΊΠ»Π°Π΄Ρ ΠΏΠΎΡΡΠΎΡΠ½Π½ΠΎ ΠΌΠΎΠ΄Π΅ΡΠ½ΠΈΠ·ΠΈΡΡΡΡΡΡ ΠΈ ΡΠ°ΡΡΠΈΡΡΡΡΡΡ.
Β
Β
ΠΡΡ ΠΈΡΠ΅ΠΊΡΡΡΠ½ΡΠ΅ ΡΠ»Π΅ΠΌΠ΅Π½ΡΡ ΠΊΠΎΠ»Π»Π΅ΠΊΡΠΈΠΈ Π Π΅Π³Π΅Π½Ρ ΠΠ΅ΠΊΠΎΡ ΡΠ½Π°Π±ΠΆΠ΅Π½Ρ ΡΠΈΡΠΌΠ΅Π½Π½ΠΎΠΉ ΠΌΠ°ΡΠΊΠΈΡΠΎΠ²ΠΊΠΎΠΉ Π½Π° Π²Π½ΡΡΡΠ΅Π½Π½Π΅ΠΉ ΡΠ°ΡΡΠΈ ΠΈΠ·Π΄Π΅Π»ΠΈΠΉ.
ΠΠ·Π³ΠΎΡΠΎΠ²Π»Π΅Π½ΠΈΠ΅ Π»Π΅ΠΏΠ½ΠΈΠ½Ρ ΠΈΠ· Π³ΠΈΠΏΡΠ° Π½Π° Π·Π°ΠΊΠ°Π· Π² Π‘ΠΠ± ΠΈ ΠΠΎΡΠΊΠ²Π΅ ΠΏΠΎ Π½ΠΈΠ·ΠΊΠΈΠΌ ΡΠ΅Π½Π°ΠΌ
ΠΠ·Π³ΠΎΡΠΎΠ²Π»Π΅Π½ΠΈΠ΅ Π³ΠΈΠΏΡΠΎΠ²ΠΎΠΉ Π»Π΅ΠΏΠ½ΠΈΠ½Ρ Π² Π½Π°ΡΠ΅ΠΉ ΠΊΠΎΠΌΠΏΠ°Π½ΠΈΠΈ Π²Π΅Π΄Π΅ΡΡΡ Π½Π° ΡΠΎΠ²ΡΠ΅ΠΌΠ΅Π½Π½ΠΎΠΌ ΠΎΠ±ΠΎΡΡΠ΄ΠΎΠ²Π°Π½ΠΈΠΈ. Π ΡΠ°Π±ΠΎΡΠ΅ Π·Π°Π΄Π΅ΠΉΡΡΠ²ΠΎΠ²Π°Π½Ρ ΠΎΠΏΡΡΠ½ΡΠ΅ ΠΈ ΡΠΌΠ΅Π»ΡΠ΅ ΠΌΠ°ΡΡΠ΅ΡΠ°, ΡΠΏΠΎΡΠΎΠ±Π½ΡΠ΅ Π²ΠΎΠΏΠ»ΠΎΡΠΈΡΡ Π² ΠΆΠΈΠ·Π½Ρ ΡΠ»ΠΎΠΆΠ½Π΅ΠΉΡΠΈΠ΅ ΠΏΡΠΎΠ΅ΠΊΡΡ. Π£Π΄ΠΈΠ²ΠΈΡΠ΅Π»ΡΠ½ΡΠ΅ ΡΠ²ΠΎΡΠ΅Π½ΠΈΡ, ΡΠΎΠ·Π΄Π°Π½Π½ΡΠ΅ ΡΡΠΊΠ°ΠΌΠΈ Π½Π°ΡΠΈΡ
Π΄ΠΈΠ·Π°ΠΉΠ½Π΅ΡΠΎΠ², ΠΎΠ»ΠΈΡΠ΅ΡΠ²ΠΎΡΡΡΡ Π³Π°ΡΠΌΠΎΠ½ΠΈΡ ΡΡΠΈΠ»Ρ ΠΈ ΡΠΎΡΠΌΠΈΡΡΡΡ ΡΠ΅Π»ΠΎΡΡΠ½ΠΎΡΡΡ Π°ΡΡ
ΠΈΡΠ΅ΠΊΡΡΡΠ½ΠΎΠ³ΠΎ ΠΏΡΠΎΠΈΠ·Π²Π΅Π΄Π΅Π½ΠΈΡ. ΠΡΠΈΠ²Π»Π΅ΠΊΠ°ΡΠ΅Π»ΡΠ½ΡΠ΅, ΠΈΠ·ΡΡΠ½ΡΠ΅ ΠΈ Π½Π΅ΠΏΠΎΠ²ΡΠΎΡΠΈΠΌΠΎ ΡΡΡΠ½ΡΠ΅ ΡΠ»Π΅ΠΌΠ΅Π½ΡΡ Π΅ΡΠ΅ ΠΈ ΠΏΡΠ°ΠΊΡΠΈΡΠ½Ρ.
- ΠΡΠ»ΠΈ ΠΏΡΠ°Π²ΠΈΠ»ΡΠ½ΠΎ ΡΠΎΠ±Π»ΡΡΡΠΈ ΠΏΡΠΈΠ½ΡΠΈΠΏ ΠΎΡΠΎΡΠΌΠ»Π΅Π½ΠΈΡ ΠΏΡΠΎΡΡΡΠ°Π½ΡΡΠ²Π°, ΠΏΠΎΠ»ΠΎΠΆΠΈΠ² Π² ΠΎΡΠ½ΠΎΠ²Ρ Π°ΠΊΡΡΠ°Π»ΡΠ½ΡΠ΅ ΡΠ΅Π½Π΄Π΅Π½ΡΠΈΠΈ ΠΈ Π½Π°ΡΠ»Π΅Π΄ΠΈΠ΅ ΠΏΡΠΎΡΠ»ΠΎΠ³ΠΎ, ΠΏΠΎΠ»ΡΡΠΈΡΡΡ ΡΠ΅Π°Π»ΠΈΠ·ΠΎΠ²Π°ΡΡ ΡΠ½ΠΈΠΊΠ°Π»ΡΠ½ΡΠΉ ΠΎΠ±ΡΠ°Π·, ΡΠ΅ΠΌ ΡΠ°ΠΌΡΠΌ ΡΠΊΡΡΠ² Π½Π΅Π΄ΠΎΡΡΠ°ΡΠΊΠΈ ΠΏΠΎΠΌΠ΅ΡΠ΅Π½ΠΈΡ.
- Π£Π½ΠΈΠΊΠ°Π»ΡΠ½ΡΠ΅ Ρ Π°ΡΠ°ΠΊΡΠ΅ΡΠΈΡΡΠΈΠΊΠΈ ΠΌΠ°ΡΠ΅ΡΠΈΠ°Π»Π° ΠΈ ΡΠ΅Ρ Π½ΠΎΠ»ΠΎΠ³ΠΈΡ ΠΈΠ·Π³ΠΎΡΠΎΠ²Π»Π΅Π½ΠΈΡ Π»Π΅ΠΏΠ½ΠΈΠ½Ρ ΠΈΠ· Π³ΠΈΠΏΡΠ° ΠΏΠΎΠ·Π²ΠΎΠ»ΡΠ΅Ρ ΡΠΎΠ·Π΄Π°Π²Π°ΡΡ ΠΈΠ·Π΄Π΅Π»ΠΈΡ Π»ΡΠ±ΡΡ ΡΠΎΡΠΌ ΠΈ ΡΠ°Π·ΠΌΠ΅ΡΠΎΠ².
- ΠΠ΅ΠΏΠ½ΠΎΠΉ Π΄Π΅ΠΊΠΎΡ ΠΈΠ· ΡΡΠΎΠ³ΠΎ ΡΠ½ΠΈΠ²Π΅ΡΡΠ°Π»ΡΠ½ΠΎΠ³ΠΎ ΠΈ ΠΏΠΎΠ΄Π°ΡΠ»ΠΈΠ²ΠΎΠ³ΠΎ ΠΌΠ°ΡΠ΅ΡΠΈΠ°Π»Π° ΠΈΠ·Π³ΠΎΡΠ°Π²Π»ΠΈΠ²Π°ΡΡ ΠΏΠΎ ΠΈΠ½Π΄ΠΈΠ²ΠΈΠ΄ΡΠ°Π»ΡΠ½ΡΠΌ ΡΡΠΊΠΈΠ·Π°ΠΌ Π΄Π»Ρ ΡΠΎΡΠΌΠΈΡΠΎΠ²Π°Π½ΠΈΡ Π½Π΅ΠΏΠΎΠ²ΡΠΎΡΠΈΠΌΡΡ ΠΎΡΠ΅ΡΡΠ°Π½ΠΈΠΉ ΠΈΠ½ΡΠ΅ΡΡΠ΅ΡΠ°.
- ΠΠ΅ΠΏΠ½ΠΈΠ½Π° ΡΠ°Π±ΠΎΡΠ°Π΅Ρ ΠΈ Π½Π° ΡΡΠ½ΠΊΡΠΈΠΎΠ½Π°Π»ΡΠ½ΠΎΡΡΡ ΠΏΠΎΠΌΠ΅ΡΠ΅Π½ΠΈΡ, ΡΠΎΠ·Π΄Π°Π²Π°Ρ Π³Π°ΡΠΌΠΎΠ½ΠΈΡΠ½ΠΎΠ΅ Π²ΠΈΠ΄Π΅Π½ΠΈΠ΅ Π²Π½ΡΡΡΠ΅Π½Π½Π΅Π³ΠΎ ΠΏΡΠΎΡΡΡΠ°Π½ΡΡΠ²Π°.
ΠΠΎΠ½Π΅ΡΠ½ΠΎ, ΡΡΡΠ΅ΡΠΈΡΠ΅ΡΠΊΠ°Ρ ΡΠΎΡΡΠ°Π²Π»ΡΡΡΠ°Ρ ΠΎΡΠ΅Π½Ρ Π²Π°ΠΆΠ½Π° ΠΏΡΠΈ ΠΏΡΠΎΠΈΠ·Π²ΠΎΠ΄ΡΡΠ²Π΅ Π»Π΅ΠΏΠ½ΠΈΠ½Ρ, ΠΎΠ΄Π½Π°ΠΊΠΎ Π½Π΅ ΠΌΠ΅Π½ΡΡΡΡ Π·Π½Π°ΡΠΈΠΌΠΎΡΡΡ ΠΈΠΌΠ΅Π΅Ρ ΠΏΡΠ°ΠΊΡΠΈΡΠ΅ΡΠΊΠ°Ρ ΡΡΠΎΡΠΎΠ½Π°. ΠΠ°Π΄Π΅ΠΊΠΎΡΠΈΡΠΎΠ²Π°Π² ΡΡΠ΅Π½Ρ ΠΈ ΠΏΠΎΡΠΎΠ»ΠΎΠΊ Π³ΠΈΠΏΡΠΎΠ²ΡΠΌΠΈ ΠΈΠ·Π΄Π΅Π»ΠΈΡΠΌΠΈ, ΠΌΠΎΠΆΠ½ΠΎ Ρ Π»Π΅Π³ΠΊΠΎΡΡΡΡ ΡΠ°Π·Π΄Π΅Π»ΠΈΡΡ ΠΏΠΎΠΌΠ΅ΡΠ΅Π½ΠΈΠ΅ Π½Π° Π½Π΅ΡΠΊΠΎΠ»ΡΠΊΠΎ ΡΡΠ½ΠΊΡΠΈΠΎΠ½Π°Π»ΡΠ½ΡΡ
Π·ΠΎΠ½. Π’Π°ΠΊΠΆΠ΅ Ρ ΠΈΡ
ΠΏΠΎΠΌΠΎΡΡΡ ΡΠΊΡΡΠ²Π°ΡΡΡΡ ΠΎΠ³ΡΠ΅Ρ
ΠΈ ΡΡΡΠΎΠΈΡΠ΅Π»Π΅ΠΉ ΠΈΠ»ΠΈ ΡΠ°Π·Π»ΠΈΡΠ½ΡΠ΅ ΠΊΠΎΠ½ΡΡΡΡΠΊΡΠΈΠ²Π½ΡΠ΅ ΡΠ»Π΅ΠΌΠ΅Π½ΡΡ ΠΊΠΎΠΌΠ½Π°ΡΡ.
Π£ΡΠΏΠ΅ΡΠ½ΠΎΠ΅ ΠΏΡΠΎΠΈΠ·Π²ΠΎΠ΄ΡΡΠ²ΠΎ Π³ΠΈΠΏΡΠΎΠ²ΠΎΠΉ Π»Π΅ΠΏΠ½ΠΈΠ½Ρ Π² ΡΠ΅ΡΠ΅Π½ΠΈΠ΅ 20 Π»Π΅Ρ
ΠΠΎΠΌΠΏΠ°Π½ΠΈΡ Β«ΠΠ‘Π’ΠΠΠΒ» ΠΎΡΡΡΠ΅ΡΡΠ²Π»ΡΠ΅Ρ ΠΈΠ·Π³ΠΎΡΠΎΠ²Π»Π΅Π½ΠΈΠ΅ Π»Π΅ΠΏΠ½ΠΎΠ³ΠΎ Π΄Π΅ΠΊΠΎΡΠ° ΠΈΠ· Π³ΠΈΠΏΡΠ° Π² Π‘Π°Π½ΠΊΡ-ΠΠ΅ΡΠ΅ΡΠ±ΡΡΠ³Π΅ Π½Π° ΠΏΡΠΎΡΡΠΆΠ΅Π½ΠΈΠΈ ΠΏΠΎΡΠ»Π΅Π΄Π½ΠΈΡ Π΄Π²Π°Π΄ΡΠ°ΡΠΈ Π»Π΅Ρ. Π ΠΊΠ°ΠΆΠ΄ΠΎΠΉ ΡΠ°Π±ΠΎΡΠ΅ ΠΌΡ ΡΡΠ°ΡΠ°Π΅ΠΌΡΡ ΡΠΉΡΠΈ ΠΎΡ Π±Π΅Π·Π»ΠΈΠΊΠΈΡ ΠΈ ΡΠΈΠΏΠΎΠ²ΡΡ Π²ΠΈΠ΄ΠΎΠ² Π³ΠΎΡΠΎΠ΄ΡΠΊΠΎΠΉ Π·Π°ΡΡΡΠΎΠΉΠΊΠΈ, Π΄ΠΎΠΏΠΎΠ»Π½ΠΈΠ² ΠΈΡ ΡΡΠΎΠ½ΡΠ΅Π½Π½ΠΎΡΡΡΡ ΠΈ ΠΈΠ·ΡΡΠΊΠΎΠΌ.
ΠΠ° Π΄ΠΎΠ»Π³ΠΈΠ΅ Π³ΠΎΠ΄Ρ Π½Π°ΠΌ ΡΠ΄Π°Π»ΠΎΡΡ Π½Π°ΡΠ°Π±ΠΎΡΠ°ΡΡ ΠΎΠΏΡΡ, ΠΏΠΎΠ·Π²ΠΎΠ»ΡΡΡΠΈΠΉ ΠΈΠ·Π±Π΅ΠΆΠ°ΡΡ Π΄Π΅ΡΠ΅ΠΊΡΠΎΠ² (ΡΠΊΠΎΠ»ΠΎΠ², ΡΡΠ΅ΡΠΈΠ½ ΠΈ Ρ.Π΄.) ΠΏΡΠΈ ΡΠΎΠ·Π΄Π°Π½ΠΈΠΈ ΠΈΠ·Π΄Π΅Π»ΠΈΠΉ. ΠΡΠΎΠΌΠ΅ ΡΠΎΠ³ΠΎ, ΠΌΡ ΡΠΌΠΎΠ³Π»ΠΈ Π΄ΠΎΠ±ΠΈΡΡΡΡ ΠΈΠ΄Π΅Π°Π»ΡΠ½ΠΎΠΉ ΡΡΡΠΊΠΎΠ²ΠΊΠΈ Π΄Π΅ΡΠ°Π»Π΅ΠΉ. ΠΡΠΎΠΈΠ·Π²ΠΎΠ΄ΡΡΠ²ΠΎ Π΄Π΅ΠΊΠΎΡΠ°ΡΠΈΠ²Π½ΡΡ ΡΠ»Π΅ΠΌΠ΅Π½ΡΠΎΠ² ΠΈΠ· Π³ΠΈΠΏΡΠ° ΡΠ΅ΡΠΊΠΎ Π½Π°Π»Π°ΠΆΠ΅Π½ΠΎ, ΠΏΠΎΡΡΠΎΡΠ½Π½ΠΎ ΠΎΠ±Π½ΠΎΠ²Π»ΡΠ΅ΡΡΡ ΠΈ ΠΏΠΎΠΏΠΎΠ»Π½ΡΠ΅ΡΡΡ ΠΏΠ°ΡΠΊ ΡΠΎΡΠΌ. ΠΠ°ΠΆΠ΅ Π΅ΡΠ»ΠΈ Π²Ρ Π½Π΅ Π½Π°ΡΠ»ΠΈ ΠΏΠΎΠ΄Ρ ΠΎΠ΄ΡΡΠΈΠΉ ΡΠΎΠ²Π°Ρ, ΠΌΡ ΠΈΠ·Π³ΠΎΡΠΎΠ²ΠΈΠΌ Π΅Π³ΠΎ ΠΏΠΎ ΠΈΠ½Π΄ΠΈΠ²ΠΈΠ΄ΡΠ°Π»ΡΠ½ΠΎΠΌΡ ΠΏΡΠΎΠ΅ΠΊΡΡ.
ΠΡΠ΅ΠΈΠΌΡΡΠ΅ΡΡΠ²Π°
Π ΠΎΡΠ»ΠΈΡΠΈΠ΅ ΠΎΡ ΠΏΠ»Π°ΡΡΠΈΠΊΠΎΠ²ΡΡ
ΠΈΠ·Π΄Π΅Π»ΠΈΠΉ, Π²ΡΠ΅Π³ΠΎ Π»ΠΈΡΡ ΠΈΠΌΠΈΡΠΈΡΡΡΡΠΈΡ
Π³ΠΈΠΏΡ, Π½Π°ΡΠ° ΠΏΡΠΎΠ΄ΡΠΊΡΠΈΡ ΡΠΊΠΎΠ»ΠΎΠ³ΠΈΡΠ΅ΡΠΊΠΈ Π±Π΅Π·ΠΎΠΏΠ°ΡΠ½Π°Ρ ΠΈ Π°Π±ΡΠΎΠ»ΡΡΠ½ΠΎ Π½Π΅Π³ΠΎΡΡΡΠ°Ρ.
- ΠΠ½Π΄ΠΈΠ²ΠΈΠ΄ΡΠ°Π»ΡΠ½ΠΎΡΡΡ
ΠΡΠΎΠΈΠ·Π²ΠΎΠ΄ΡΡΠ²ΠΎ Π»Π΅ΠΏΠ½ΠΎΠ³ΠΎ Π΄Π΅ΠΊΠΎΡΠ° ΠΈΠ· Π³ΠΈΠΏΡΠ°, Π² ΡΡΠ°Π²Π½Π΅Π½ΠΈΠΈ Ρ ΠΏΠΎΠ»ΠΈΡΡΠ΅ΡΠ°Π½ΠΎΠ²ΡΠΌΠΈ ΠΌΠΎΠ΄Π΅Π»ΡΠΌΠΈ, Π²Π΅Π΄Π΅ΡΡΡ ΠΏΠΎ ΠΈΠ½Π΄ΠΈΠ²ΠΈΠ΄ΡΠ°Π»ΡΠ½ΡΠΌ ΠΏΡΠΎΠ΅ΠΊΡΠ°ΠΌ, Ρ ΡΡΠ΅ΡΠΎΠΌ Π²ΡΠ΅Ρ ΠΏΠΎΠΆΠ΅Π»Π°Π½ΠΈΠΉ Π·Π°ΠΊΠ°Π·ΡΠΈΠΊΠ°. Π ΡΠ°ΠΊΠΆΠ΅ Ρ Π½Π°Ρ ΠΈΠΌΠ΅ΡΡΡΡ ΠΈ Π³ΠΎΡΠΎΠ²ΡΠ΅ Π΄Π΅ΡΠ°Π»ΠΈ.
- ΠΡΡΠΎΠΊΠΎΠ΅ ΠΊΠ°ΡΠ΅ΡΡΠ²ΠΎ
ΠΠΎΠΌΠΈΠΌΠΎ ΠΏΡΠΈΡΠΎΠ΄Π½ΡΡ ΡΠ²ΠΎΠΉΡΡΠ² ΠΌΠ°ΡΠ΅ΡΠΈΠ°Π»Π°, ΠΌΡ Π·Π°ΠΊΠ»Π°Π΄ΡΠ²Π°Π΅ΠΌ Π΄ΠΎΠΏΠΎΠ»Π½ΠΈΡΠ΅Π»ΡΠ½ΡΠΉ Π·Π°ΠΏΠ°Ρ ΠΏΡΠΎΡΠ½ΠΎΡΡΠΈ Π² Ρ ΠΎΠ΄Π΅ ΠΈΠ·Π³ΠΎΡΠΎΠ²Π»Π΅Π½ΠΈΡ Π»Π΅ΠΏΠ½ΠΈΠ½Ρ. ΠΠΈΠΏΡ Π½Π΅ Π΄Π°Π΅Ρ ΡΡΠ°Π΄ΠΊΠΈ, Π° Π·Π½Π°ΡΠΈΡ, ΠΈ ΡΠ΅ΡΠ΅Π· Π΄Π΅ΡΡΡΠΈΠ»Π΅ΡΠΈΡ ΠΎΠ½ Π½Π΅ ΠΏΠΎΡΠ΅ΡΡΠ΅Ρ ΠΏΡΠΈΠ²Π»Π΅ΠΊΠ°ΡΠ΅Π»ΡΠ½ΠΎΡΡΠΈ, ΡΡΠ°Π² Π² ΠΎΠ΄ΠΈΠ½ ΡΡΠ΄ Ρ ΠΏΠΎΡΠ°Π·ΠΈΡΠ΅Π»ΡΠ½ΠΎΠΉ Π°ΡΡ ΠΈΡΠ΅ΠΊΡΡΡΠΎΠΉ Π΄Π²ΠΎΡΡΠΎΠ² ΠΈ ΡΡΠ°Π΄Π΅Π± ΠΠ΅ΡΠ΅ΡΠ±ΡΡΠ³Π° ΠΏΡΠΎΡΠ»ΠΎΠ³ΠΎ.
- ΠΠΎΡΡΡΠΏΠ½Π°Ρ ΡΡΠΎΠΈΠΌΠΎΡΡΡ
ΠΠ·Π³ΠΎΡΠΎΠ²Π»Π΅Π½ΠΈΠ΅ Π΄Π΅ΠΊΠΎΡΠ°ΡΠΈΠ²Π½ΡΡ ΡΠ»Π΅ΠΌΠ΅Π½ΡΠΎΠ² ΠΈΠ· Π³ΠΈΠΏΡΠ° Π²Π΅Π΄Π΅ΡΡΡ ΠΏΠΎ ΡΠΎΠ²ΡΠ΅ΠΌΠ΅Π½Π½ΠΎΠΉ ΡΠ΅Ρ Π½ΠΎΠ»ΠΎΠ³ΠΈΠΈ, ΡΡΠΎ ΠΏΠΎΠ·Π²ΠΎΠ»ΡΠ΅Ρ ΡΠ΄Π΅ΡΠΆΠΈΠ²Π°ΡΡ ΡΠ΅Π½Ρ Π½Π° Π΄ΠΎΡΡΡΠΏΠ½ΠΎΠΌ ΡΡΠΎΠ²Π½Π΅. Π ΡΡΠΎΠΈΠΌΠΎΡΡΡ ΡΠΎΠ²Π°ΡΠ° ΠΌΡ Π½Π΅ Π²ΠΊΠ»ΡΡΠ°Π΅ΠΌ ΡΠΊΠ»Π°Π΄ΡΠΊΠΈΠ΅ ΠΈΠ·Π΄Π΅ΡΠΆΠΊΠΈ ΠΈ Π΄ΡΡΠ³ΠΈΠ΅ ΡΠ°ΡΡ ΠΎΠ΄Ρ, ΠΊΠΎΡΠΎΡΡΠΌΠΈ ΠΎΠ±ΡΠ΅ΠΌΠ΅Π½Π΅Π½Ρ ΠΏΠΎΡΡΠ΅Π΄Π½ΠΈΠΊΠΈ.
- ΠΠΎΠ·ΠΌΠΎΠΆΠ½ΠΎΡΡΡ ΡΠ΅ΡΡΠ°Π²ΡΠ°ΡΠΈΠΈ
ΠΠΎΠ²ΡΠ΅ΠΆΠ΄Π΅Π½Π½ΡΠ΅ Π³ΠΈΠΏΡΠΎΠ²ΡΠ΅ ΠΈΠ·Π΄Π΅Π»ΠΈΡ ΠΌΠΎΠΆΠ½ΠΎ Π»Π΅Π³ΠΊΠΎ Π²ΠΎΡΡΡΠ°Π½ΠΎΠ²ΠΈΡΡ. ΠΡΠ°ΠΊΡΠΈΡΠ΅ΡΠΊΠΈ Π»ΡΠ±ΠΎΠΉ ΡΠΊΠΎΠ» ΠΈΠ»ΠΈ ΡΡΠ΅ΡΠΈΠ½Π° Π½Π΅Π·Π°ΠΌΠ΅ΡΠ½ΠΎ ΠΈΡΠΏΡΠ°Π²Π»ΡΠ΅ΡΡΡ ΡΠΌΠ΅Π»ΡΠΌΠΈ ΡΡΠΊΠ°ΠΌΠΈ ΠΌΠ°ΡΡΠ΅ΡΠ°.
- ΠΡΡΡΡΡΠΉ ΠΌΠΎΠ½ΡΠ°ΠΆ
Π£ΡΡΠ°Π½ΠΎΠ²ΠΊΠ° Π»Π΅ΠΏΠ½ΠΎΠ³ΠΎ Π΄Π΅ΠΊΠΎΡΠ° ΠΏΡΠΎΠ²ΠΎΠ΄ΠΈΡΡΡ ΡΠΏΠ΅ΡΠΈΠ°Π»ΠΈΡΡΠ°ΠΌΠΈ Π²ΡΡΠΎΠΊΠΎΠ³ΠΎ ΡΡΠΎΠ²Π½Ρ, ΡΡΠΎ Π² ΡΠ°Π·Ρ ΡΠΎΠΊΡΠ°ΡΠ°Π΅Ρ ΡΡΠΎΠΊΠΈ ΡΠ°Π±ΠΎΡ Π±Π΅Π· ΠΏΠΎΡΠ΅ΡΠΈ ΠΊΠ°ΡΠ΅ΡΡΠ²Π°.
PMT | ΠΡΡΠΎΠΊΠΎΠΊΠ°ΡΠ΅ΡΡΠ²Π΅Π½Π½ΠΎΠ΅ Π»ΠΈΡΡΠ΅ ΠΏΠ»Π°ΡΡΠΌΠ°ΡΡ ΠΏΠΎΠ΄ Π΄Π°Π²Π»Π΅Π½ΠΈΠ΅ΠΌ Π±ΠΎΠ»Π΅Π΅ 40 Π»Π΅Ρ | ΠΠ»Π°ΡΡΠΈΠΊΠΎΠ²ΡΠ΅ Π’Π΅Ρ Π½ΠΎΠ»ΠΎΠ³ΠΈΠΈ Π€ΠΎΡΠΌΠΎΠ²ΠΊΠΈ, ΠΠ½ΠΊ | ΠΠ»Ρ-ΠΠ°ΡΠΎ, Π’Π΅Ρ Π°Ρ, Π’Π΅Ρ Π°Ρ
ΠΠ°ΡΠ΅ΡΡΠ²ΠΎ — ΡΡΠΎ Π½Π°Ρ ΠΊΠΎΠΌΠΏΠ°Ρ — Π½Π°Ρ ΠΈΡΡΠΈΠ½Π½ΡΠΉ ΡΠ΅Π²Π΅Ρ.
ΠΠΎΠΌΠΏΠ°Π½ΠΈΡ Plastic Molding Technology, Inc. ΡΡΡΠ΅ΠΌΠΈΡΡΡ ΠΎΠ±Π΅ΡΠΏΠ΅ΡΠΈΠ²Π°ΡΡ Π²ΡΡΠΎΡΠ°ΠΉΡΠΈΠΉ ΡΡΠΎΠ²Π΅Π½Ρ ΠΊΠ°ΡΠ΅ΡΡΠ²Π° Π²ΠΎ Π²ΡΠ΅ΠΌ, ΡΡΠΎ ΠΌΡ Π΄Π΅Π»Π°Π΅ΠΌ.
ΠΡΡΡΡΡΡΠ²ΠΈΠ΅ Π΄Π΅ΡΠ΅ΠΊΡΠΎΠ² ΠΈ 100% ΡΠ²ΠΎΠ΅Π²ΡΠ΅ΠΌΠ΅Π½Π½ΡΠ΅ ΠΏΠΎΡΡΠ°Π²ΠΊΠΈ — Π½Π°ΡΠΈ ΠΏΠΎΡΡΠΎΡΠ½Π½ΡΠ΅ ΡΠ΅Π»ΠΈ. ΠΠ΅ΠΏΡΠ΅ΡΡΠ²Π½ΠΎΠ΅ ΡΠΎΠ²Π΅ΡΡΠ΅Π½ΡΡΠ²ΠΎΠ²Π°Π½ΠΈΠ΅ — Π½Π°ΡΠ° ΠΌΠ°Π½ΡΡΠ°.
ΠΠ° ΠΏΡΠΎΡΡΠΆΠ΅Π½ΠΈΠΈ Π½Π°ΡΠ΅ΠΉ ΠΏΡΡΠΈΠ΄Π΅ΡΡΡΠΈΠ»Π΅ΡΠ½Π΅ΠΉ ΠΈΡΡΠΎΡΠΈΠΈ ΠΌΡ Π²ΡΠ΅Π³Π΄Π° Π±ΡΠ»ΠΈ ΠΈ Π²ΡΠ΅Π³Π΄Π° Π±ΡΠ΄Π΅ΠΌ ΡΡΡΠ΅ΠΌΠΈΡΡΡΡ ΠΊ ΠΏΠΎΠ»Π½ΠΎΠΌΡ ΡΠ΄ΠΎΠ²Π»Π΅ΡΠ²ΠΎΡΠ΅Π½ΠΈΡ ΠΏΠΎΡΡΠ΅Π±Π½ΠΎΡΡΠ΅ΠΉ ΠΊΠ»ΠΈΠ΅Π½ΡΠΎΠ², ΠΎΡ ΠΏΡΠΎΠ΅ΠΊΡΠΈΡΠΎΠ²Π°Π½ΠΈΡ ΠΈ ΠΏΡΠΎΠ΅ΠΊΡΠΈΡΠΎΠ²Π°Π½ΠΈΡ Π΄ΠΎ ΡΠΎΡΠΌΠΎΠ²Π°Π½ΠΈΡ ΠΈ ΠΎΠ±ΡΠ»ΡΠΆΠΈΠ²Π°Π½ΠΈΡ ΠΊΠ»ΠΈΠ΅Π½ΡΠΎΠ².ΠΠ°ΡΠ° Π½Π΅ΠΏΠΎΠΊΠΎΠ»Π΅Π±ΠΈΠΌΠ°Ρ ΠΏΡΠΈΠ²Π΅ΡΠΆΠ΅Π½Π½ΠΎΡΡΡ ΠΊΠ°ΡΠ΅ΡΡΠ²Ρ ΠΊΠ°ΠΊ ΠΏΡΠΎΠ΄ΡΠΊΡΠΎΠ², ΡΠ°ΠΊ ΠΈ ΠΎΠ±ΡΠ»ΡΠΆΠΈΠ²Π°Π½ΠΈΡ ΠΊΠ»ΠΈΠ΅Π½ΡΠΎΠ², Π° ΡΠ°ΠΊΠΆΠ΅ Π½Π°ΡΠ° ΠΏΠΎΡΡΠΎΡΠ½Π½Π°Ρ ΠΎΡΠΈΠ΅Π½ΡΠ°ΡΠΈΡ Π½Π° ΠΏΠΎΡΡΠΎΡΠ½Π½ΠΎΠ΅ ΡΠΎΠ²Π΅ΡΡΠ΅Π½ΡΡΠ²ΠΎΠ²Π°Π½ΠΈΠ΅ ΠΏΠΎΠΌΠΎΠ³Π»ΠΈ Π½Π°ΠΌ ΠΏΠΎΡΡΡΠΎΠΈΡΡ Π΄ΠΎΠ»Π³ΠΎΡΡΠΎΡΠ½ΡΠ΅ ΠΎΡΠ½ΠΎΡΠ΅Π½ΠΈΡ Ρ ΠΊΠ»ΠΈΠ΅Π½ΡΠ°ΠΌΠΈ ΠΈ Π΄ΠΎΡΡΠΈΡΡ Π²ΡΡΠΎΠΊΠΎΠ³ΠΎ ΡΡΠΎΠ²Π½Ρ ΠΏΠΎΠ²ΡΠΎΡΠ½ΡΡ
Π·Π°ΠΊΠ°Π·ΠΎΠ².
ΠΠ°ΡΠΈ ΡΠ΅Π»ΠΈ Π² ΠΎΠ±Π»Π°ΡΡΠΈ ΠΊΠ°ΡΠ΅ΡΡΠ²Π° Π΄ΠΎΡΡΠΈΠ³Π°ΡΡΡΡ Π·Π° ΡΡΠ΅Ρ ΡΠΎΡΠ΅ΡΠ°Π½ΠΈΡ ΡΠΎΠ²ΡΠ΅ΠΌΠ΅Π½Π½ΠΎΠ³ΠΎ ΠΎΠ±ΠΎΡΡΠ΄ΠΎΠ²Π°Π½ΠΈΡ, ΡΠ΅ΡΠΊΠΎ ΠΎΠΏΡΠ΅Π΄Π΅Π»Π΅Π½Π½ΡΡ ΠΏΡΠΎΡΠ΅ΡΡΠΎΠ², ΡΡΡΠΎΠ³ΠΎΠ³ΠΎ ΠΊΠΎΠ½ΡΡΠΎΠ»Ρ ΠΊΠ°ΡΠ΅ΡΡΠ²Π°, ΠΏΡΠ°ΠΊΡΠΈΡΠ΅ΡΠΊΠΎΠ³ΠΎ ΡΠΏΡΠ°Π²Π»Π΅Π½ΠΈΡ, Π½Π΅ΠΏΡΠ΅ΡΡΠ²Π½ΠΎΠ³ΠΎ ΠΎΠ±ΡΡΠ΅Π½ΠΈΡ ΠΈ ΠΊΠ²Π°Π»ΠΈΡΠΈΡΠΈΡΠΎΠ²Π°Π½Π½ΡΡ , ΠΏΡΠ΅Π΄Π°Π½Π½ΡΡ ΡΠ²ΠΎΠ΅ΠΌΡ Π΄Π΅Π»Ρ ΡΠΎΡΡΡΠ΄Π½ΠΈΠΊΠΎΠ². ΠΡ ΠΈΡΠΏΠΎΠ»ΡΠ·ΡΠ΅ΠΌ eDART System β’, ΠΌΠΎΡΠ½ΡΡ ΡΠΈΡΡΠ΅ΠΌΡ ΠΌΠΎΠ½ΠΈΡΠΎΡΠΈΠ½Π³Π° ΠΈ ΡΠΏΡΠ°Π²Π»Π΅Π½ΠΈΡ ΠΏΡΠΎΠΈΠ·Π²ΠΎΠ΄ΡΡΠ²Π΅Π½Π½ΡΠΌ ΠΏΡΠΎΡΠ΅ΡΡΠΎΠΌ Ρ ΠΌΠ½ΠΎΠΆΠ΅ΡΡΠ²ΠΎΠΌ ΡΡΠ½ΠΊΡΠΈΠΉ ΠΈ ΡΡΠ½ΠΊΡΠΈΠΉ, ΠΏΡΠ΅Π΄Π½Π°Π·Π½Π°ΡΠ΅Π½Π½ΡΡ Π΄Π»Ρ ΡΠ»ΡΡΡΠ΅Π½ΠΈΡ ΠΊΠΎΠ½ΡΡΠΎΠ»Ρ ΠΊΠ°ΡΠ΅ΡΡΠ²Π° Π½Π° ΠΏΡΠΎΡΡΠΆΠ΅Π½ΠΈΠΈ Π²ΡΠ΅Π³ΠΎ ΠΏΡΠΎΠΈΠ·Π²ΠΎΠ΄ΡΡΠ²Π΅Π½Π½ΠΎΠ³ΠΎ ΠΏΡΠΎΡΠ΅ΡΡΠ°.
ΠΠ°ΠΆΠ΄Π°Ρ ΠΈΠ·Π³ΠΎΡΠΎΠ²Π»Π΅Π½Π½Π°Ρ Π΄Π΅ΡΠ°Π»Ρ ΠΏΠΎΠ΄Π»Π΅ΠΆΠΈΡ Π°Π²ΡΠΎΠΌΠ°ΡΠΈΡΠ΅ΡΠΊΠΎΠΌΡ ΠΈ / ΠΈΠ»ΠΈ Π²ΠΈΠ·ΡΠ°Π»ΡΠ½ΠΎΠΌΡ ΠΊΠΎΠ½ΡΡΠΎΠ»Ρ. ΠΠ½ΠΎΠ³ΠΈΠ΅ ΠΈΠ· Π½Π°ΡΠΈΡ ΠΏΡΠΎΠΈΠ·Π²ΠΎΠ΄ΡΡΠ²Π΅Π½Π½ΡΡ ΡΠ΅Ρ ΠΎΠ² ΠΈΡΠΏΠΎΠ»ΡΠ·ΡΡΡ ΡΠΎΠ±ΠΎΡΡ ΠΈ ΡΠΈΡΡΠ΅ΠΌΡ ΡΠ΅Ρ Π½ΠΈΡΠ΅ΡΠΊΠΎΠ³ΠΎ Π·ΡΠ΅Π½ΠΈΡ Π΄Π»Ρ Π΄ΠΎΡΡΠΈΠΆΠ΅Π½ΠΈΡ ΠΌΠ°ΠΊΡΠΈΠΌΠ°Π»ΡΠ½ΠΎΠ³ΠΎ ΡΡΠΎΠ²Π½Ρ ΡΠΎΠ³Π»Π°ΡΠΎΠ²Π°Π½Π½ΠΎΡΡΠΈ Π² ΡΠΏΡΠ°Π²Π»Π΅Π½ΠΈΠΈ ΡΠ΅Ρ Π½ΠΎΠ»ΠΎΠ³ΠΈΡΠ΅ΡΠΊΠΈΠΌ ΠΏΡΠΎΡΠ΅ΡΡΠΎΠΌ ΠΈ ΠΎΠ±Π΅ΡΠΏΠ΅ΡΠ΅Π½ΠΈΡ ΠΏΡΠ΅Π²ΠΎΡΡ ΠΎΠ΄Π½ΠΎΠ³ΠΎ ΠΊΠ°ΡΠ΅ΡΡΠ²Π° Π΄Π΅ΡΠ°Π»Π΅ΠΉ.
Π‘Π΅ΡΡΠΈΡΠΈΠΊΠ°Ρ ΠΊΠ°ΡΠ΅ΡΡΠ²Π°
PMT ΡΠ²Π»ΡΠ΅ΡΡΡ Π·Π°ΡΠ΅Π³ΠΈΡΡΡΠΈΡΠΎΠ²Π°Π½Π½ΡΠΌ ΠΏΠΎΠ»ΡΡΠ°ΡΠ΅Π»Π΅ΠΌ ΡΠ΅ΡΡΠΈΡΠΈΠΊΠ°ΡΠΎΠ² ΠΊΠ°ΡΠ΅ΡΡΠ²Π° ISO 9001: 2015 ΠΈ IATF 16949: 2016, ΠΏΠΎΡΠ»Π΅Π΄Π½ΠΈΠΉ ΠΈΠ· ΠΊΠΎΡΠΎΡΡΡ
ΠΎΡΠ½ΠΎΠ²Π°Π½ Π½Π° ΡΡΠ°Π½Π΄Π°ΡΡΠ°Ρ
, ΡΡΡΠ°Π½ΠΎΠ²Π»Π΅Π½Π½ΡΡ
ΠΠ΅ΠΆΠ΄ΡΠ½Π°ΡΠΎΠ΄Π½ΠΎΠΉ Π°Π²ΡΠΎΠΌΠΎΠ±ΠΈΠ»ΡΠ½ΠΎΠΉ ΡΠ΅Π»Π΅Π²ΠΎΠΉ Π³ΡΡΠΏΠΏΠΎΠΉ (IATF). ΠΡ ΡΠ°ΠΊΠΆΠ΅ ΡΠ²Π»ΡΠ΅ΠΌΡΡ Π·Π°ΡΠ΅Π³ΠΈΡΡΡΠΈΡΠΎΠ²Π°Π½Π½ΡΠΌ ΡΠΎΡΠΌΠΎΠ²ΡΠΈΠΊΠΎΠΌ Underwriters Laboratory (UL) Ρ Π²ΠΎΠ·ΠΌΠΎΠΆΠ½ΠΎΡΡΡΡ ΠΎΡΡΠ»Π΅ΠΆΠΈΠ²Π°Π½ΠΈΡ ΠΏΠ°ΡΡΠΈΠΈ ΠΌΠ°ΡΠ΅ΡΠΈΠ°Π»Π°.
ΠΠ°ΠΊ Π²Π΅Π΄ΡΡΠΈΠΉ ΠΏΠΎΡΡΠ°Π²ΡΠΈΠΊ ΠΏΡΠΎΠΈΠ·Π²ΠΎΠ΄ΠΈΡΠ΅Π»Π΅ΠΉ Π°Π²ΡΠΎΠΌΠΎΠ±ΠΈΠ»Π΅ΠΉ ΡΡΠΎΠ²Π½Ρ 1 ΠΈ 2, ΠΌΡ ΡΠ°ΠΊΠΆΠ΅ ΠΈΡΠΏΠΎΠ»ΡΠ·ΡΠ΅ΠΌ ΡΡΡΠΎΠ³ΠΈΠΉ ΠΏΡΠΎΡΠ΅ΡΡ ΡΡΠ²Π΅ΡΠΆΠ΄Π΅Π½ΠΈΡ ΠΏΡΠΎΠΈΠ·Π²ΠΎΠ΄ΡΡΠ²Π΅Π½Π½ΡΡ Π΄Π΅ΡΠ°Π»Π΅ΠΉ (PPAP) Π² Π°Π²ΡΠΎΠΌΠΎΠ±ΠΈΠ»ΡΠ½ΠΎΠΉ ΠΏΡΠΎΠΌΡΡΠ»Π΅Π½Π½ΠΎΡΡΠΈ Π΄Π»Ρ ΠΎΠ±Π΅ΡΠΏΠ΅ΡΠ΅Π½ΠΈΡ ΡΠ²Π΅ΡΠ΅Π½Π½ΠΎΡΡΠΈ, Π½Π°Π΄Π΅ΠΆΠ½ΠΎΡΡΠΈ ΠΈ ΡΠΎΠ³Π»Π°ΡΠΎΠ²Π°Π½Π½ΠΎΡΡΠΈ ΠΏΡΠΎΠΈΠ·Π²ΠΎΠ΄ΡΡΠ²Π΅Π½Π½ΡΡ ΠΏΡΠΎΡΠ΅ΡΡΠΎΠ² ΠΊΠΎΠΌΠΏΠ°Π½ΠΈΠΈ.
ΠΡΡΠ³ΠΈΠ΅ ΠΏΡΠΎΡΠ΅ΡΡΡ ΠΈ ΠΌΠ΅ΡΠΎΠ΄Ρ, ΠΎΡΠΈΠ΅Π½ΡΠΈΡΠΎΠ²Π°Π½Π½ΡΠ΅ Π½Π° ΠΊΠ°ΡΠ΅ΡΡΠ²ΠΎ, ΠΊΠΎΡΠΎΡΡΠ΅ ΠΌΡ ΠΈΡΠΏΠΎΠ»ΡΠ·ΡΠ΅ΠΌ, Π²ΠΊΠ»ΡΡΠ°ΡΡ Β«Π±Π΅ΡΠ΅ΠΆΠ»ΠΈΠ²ΠΎΠ΅Β» ΠΏΡΠΎΠΈΠ·Π²ΠΎΠ΄ΡΡΠ²ΠΎ, 5-S, Six Sigma, ΡΡΠ°ΡΠΈΡΡΠΈΡΠ΅ΡΠΊΠΈΠΉ ΠΊΠΎΠ½ΡΡΠΎΠ»Ρ ΠΏΡΠΎΡΠ΅ΡΡΠ° (SPC) ΠΈ Π°Π½Π°Π»ΠΈΠ· ΡΡΡΠ΅ΠΊΡΠΎΠ² ΡΠ΅ΠΆΠΈΠΌΠ° ΠΎΡΠΊΠ°Π·Π° ΠΏΡΠΎΡΠ΅ΡΡΠ° (PFMEA).ΠΠ°ΡΠ° ΠΌΠΎΠ΄Π΅Π»Ρ ΡΡΠ»ΡΠ³ ΠΏΠΎ ΡΠΏΡΠ°Π²Π»Π΅Π½ΠΈΡ ΠΏΡΠΎΠ΅ΠΊΡΠ°ΠΌΠΈ ΡΠ°ΠΊΠΆΠ΅ ΠΏΠΎΠΌΠΎΠ³Π°Π΅Ρ ΠΏΡΠ΅Π΄ΠΎΡΡΠ°Π²ΠΈΡΡ ΠΊΠ»ΠΈΠ΅Π½ΡΠ°ΠΌ ΠΏΠΎΠ»Π½ΡΡ Π³Π°ΡΠ°Π½ΡΠΈΡ ΠΊΠ°ΡΠ΅ΡΡΠ²Π° ΠΎΡ Π½Π°ΡΠ°Π»Π° Π΄ΠΎ ΠΊΠΎΠ½ΡΠ°.
ΠΠ΅Π·Π°Π²ΠΈΡΠΈΠΌΠΎ ΠΎΡ ΡΠΎΠ³ΠΎ, ΡΡΠ΅Π±ΡΡΡΡΡ Π»ΠΈ Π²Π°ΡΠ΅ΠΌΡ ΠΏΡΠΎΠ΅ΠΊΡΡ ΠΌΠΈΠ»Π»ΠΈΠΎΠ½Ρ Π΅Π΄ΠΈΠ½ΠΈΡ ΠΈΠ»ΠΈ Π½Π΅Π±ΠΎΠ»ΡΡΠΈΠ΅ ΠΏΡΠ΅Π΄Π²Π°ΡΠΈΡΠ΅Π»ΡΠ½ΡΠ΅ ΠΏΠ°ΡΡΠΈΠΈ, Π²Π°ΡΠ° ΡΠ°Π±ΠΎΡΠ° Π±ΡΠ΄Π΅Ρ Π²ΡΠΏΠΎΠ»Π½ΡΡΡΡΡ Ρ ΡΠ°ΠΊΠΈΠΌ ΠΆΠ΅ ΠΏΠΎΡΡΠΎΡΠ½Π½ΡΠΌ Π²Π½ΠΈΠΌΠ°Π½ΠΈΠ΅ΠΌ ΠΊ Π΄Π΅ΡΠ°Π»ΡΠΌ, ΠΊΠΎΡΠΎΡΠΎΠ³ΠΎ Π²Ρ Π·Π°ΡΠ»ΡΠΆΠΈΠ²Π°Π΅ΡΠ΅.
ΠΠΎΠ²ΡΠΉ ΡΠΏΠΎΡΠΎΠ± ΡΠΎΡΠΌΠΎΠ²Π°ΡΡ Π±ΠΎΠ»Π΅Π΅ ΠΊΠ°ΡΠ΅ΡΡΠ²Π΅Π½Π½ΡΠ΅ Π΄Π΅ΡΠ°Π»ΠΈ, Π±ΡΡΡΡΠ΅Π΅ ΠΈ ΠΏΡΠΎΡΠ΅
Procter & Gamble ΡΠΈΡΠΎΠΊΠΎ ΠΈΠ·Π²Π΅ΡΡΠ½Π° ΠΊΠ°ΠΊ ΠΊΠΎΠΌΠΏΠ°Π½ΠΈΡ, Π·Π°Π½ΠΈΠΌΠ°ΡΡΠ°ΡΡΡ ΠΏΡΠΎΠΈΠ·Π²ΠΎΠ΄ΡΡΠ²ΠΎΠΌ ΠΏΠΎΡΡΠ΅Π±ΠΈΡΠ΅Π»ΡΡΠΊΠΈΡ
ΡΠΎΠ²Π°ΡΠΎΠ², Π½ΠΎ, Π²ΠΎΠ·ΠΌΠΎΠΆΠ½ΠΎ, ΠΌΠ΅Π½Π΅Π΅ ΠΈΠ·Π²Π΅ΡΡΠ½Π° ΡΠ²ΠΎΠΈΠΌΠΈ ΠΈΡΡΠ»Π΅Π΄ΠΎΠ²Π°Π½ΠΈΡΠΌΠΈ ΠΈ ΡΠ°Π·ΡΠ°Π±ΠΎΡΠΊΠ°ΠΌΠΈ ΠΏΠΎ ΡΠΎΠ²Π΅ΡΡΠ΅Π½ΡΡΠ²ΠΎΠ²Π°Π½ΠΈΡ ΡΠ΅Ρ
Π½ΠΎΠ»ΠΎΠ³ΠΈΠΈ ΠΏΠ΅ΡΠ΅ΡΠ°Π±ΠΎΡΠΊΠΈ ΠΏΠ»Π°ΡΡΠΌΠ°ΡΡ. Π‘Π°ΠΌΠ° ΠΊΠΎΠΌΠΏΠ°Π½ΠΈΡ P&G ΡΠ²Π»ΡΠ΅ΡΡΡ ΠΊΡΡΠΏΠ½ΡΠΌ ΠΏΠΎΡΡΠ΅Π±ΠΈΡΠ΅Π»Π΅ΠΌ ΠΊΠΎΠΌΠΏΠΎΠ½Π΅Π½ΡΠΎΠ² Π΄Π»Ρ ΡΠΏΠ°ΠΊΠΎΠ²ΠΊΠΈ, ΡΠΎΠ²Π°ΡΠΎΠ² ΠΆΠ΅Π½ΡΠΊΠΎΠΉ Π³ΠΈΠ³ΠΈΠ΅Π½Ρ, Π·ΡΠ±Π½ΡΡ
ΡΠ΅ΡΠΎΠΊ, ΠΊΠΎΠΌΠΏΠΎΠ½Π΅Π½ΡΠΎΠ² Π΄Π»Ρ Π±ΡΠΈΡΠ² ΠΈ Π΄ΡΡΠ³ΠΈΡ
ΡΠΎΠ²Π°ΡΠΎΠ², ΠΈΠ·Π³ΠΎΡΠΎΠ²Π»Π΅Π½Π½ΡΡ
ΠΌΠ΅ΡΠΎΠ΄ΠΎΠΌ Π»ΠΈΡΡΡ ΠΏΠΎΠ΄ Π΄Π°Π²Π»Π΅Π½ΠΈΠ΅ΠΌ.
P&G Π·Π°ΠΊΡΠΏΠ°Π΅Ρ ΠΌΠ½ΠΎΠ³ΠΈΠ΅ ΠΊΠΎΠΌΠΏΠΎΠ½Π΅Π½ΡΡ Ρ ΡΠΎΡΠΌΠΎΠ²ΡΠΈΠΊΠΎΠ² ΠΏΠΎ ΠΈΠ½Π΄ΠΈΠ²ΠΈΠ΄ΡΠ°Π»ΡΠ½ΠΎΠΌΡ Π·Π°ΠΊΠ°Π·Ρ, Π° ΡΠ°ΠΊΠΆΠ΅ ΠΏΡΠΎΠΈΠ·Π²ΠΎΠ΄ΠΈΡ Π²Π½ΡΡΡΠΈ ΠΊΠΎΠΌΠΏΠ°Π½ΠΈΠΈ Π·ΡΠ±Π½ΡΡ ΡΠ΅ΡΠΎΠΊ Oral B ΠΈ Π»Π΅Π·Π²ΠΈΠΉ ΠΈ Π±ΡΠΈΡΠ² Gillette. P&G ΠΏΠΎΡΡΠΎΡΠ½Π½ΠΎ Π²Π²ΠΎΠ΄ΠΈΡ Π½ΠΎΠ²ΡΠ΅ΡΡΠ²Π° Π² ΡΡΠΎΠΉ ΠΎΠ±Π»Π°ΡΡΠΈ, ΡΡΠΎΠ±Ρ ΠΎΠ±Π΅ΡΠΏΠ΅ΡΠΈΡΡ ΠΏΠΎΠ²ΡΡΠ΅Π½ΠΈΠ΅ ΡΠΊΠΎΡΠΎΡΡΠΈ, ΡΡΠΎΠΈΠΌΠΎΡΡΠΈ ΠΈ Π΄ΠΈΠ·Π°ΠΉΠ½Π°.
ΠΠ΅ΡΠΊΠΎΠ»ΡΠΊΠΎ Π»Π΅Ρ Π½Π°Π·Π°Π΄ ΠΊΠΎΠΌΠΏΠ°Π½ΠΈΡ P&G ΠΎΡΠΎΠ·Π½Π°Π»Π° Π½Π΅ΠΎΠ±Ρ
ΠΎΠ΄ΠΈΠΌΠΎΡΡΡ ΡΠ½ΠΈΠΆΠ΅Π½ΠΈΡ ΡΡΠΎΠΈΠΌΠΎΡΡΠΈ ΠΈ ΡΠΎΠΊΡΠ°ΡΠ΅Π½ΠΈΡ ΡΡΠΎΠΊΠΎΠ² Π²ΡΠΏΡΡΠΊΠ° Π½ΠΎΠ²ΡΡ
ΠΊΠΎΠ½ΡΡΡΡΠΊΡΠΈΠΉ ΠΏΠ»Π°ΡΡΠΈΠΊΠΎΠ²ΡΡ
Π΄Π΅ΡΠ°Π»Π΅ΠΉ.Π¦Π΅Π»Ρ ΡΠΎΡΡΠΎΡΠ»Π° Π² ΡΠΎΠΌ, ΡΡΠΎΠ±Ρ ΠΏΠΎΠ»Π½ΠΎΡΡΡΡ ΠΏΠ΅ΡΠ΅ΠΎΡΠΌΡΡΠ»ΠΈΡΡ ΠΏΡΠΎΡΠ΅ΡΡ ΠΈΠ·Π³ΠΎΡΠΎΠ²Π»Π΅Π½ΠΈΡ Π΄Π΅ΡΠ°Π»Π΅ΠΉ, ΠΈΠ·Π³ΠΎΡΠΎΠ²Π»Π΅Π½Π½ΡΡ
Π»ΠΈΡΡΠ΅ΠΌ ΠΏΠΎΠ΄ Π΄Π°Π²Π»Π΅Π½ΠΈΠ΅ΠΌ, ΡΡΠΎΠ±Ρ ΠΎΠ±Π΅ΡΠΏΠ΅ΡΠΈΡΡ ΠΏΡΠΎΡΡΠ² Π² ΡΠΊΠΎΡΠΎΡΡΠΈ, ΡΡΠΎΠΈΠΌΠΎΡΡΠΈ ΠΈ ΠΊΠ°ΡΠ΅ΡΡΠ²Π΅. ΠΡΠ»ΠΎ Π½Π°ΡΠ°ΡΠΎ ΠΎΠ±ΡΠ΅ΠΊΠΎΡΠΏΠΎΡΠ°ΡΠΈΠ²Π½ΠΎΠ΅ ΠΈΡΡΠ»Π΅Π΄ΠΎΠ²Π°Π½ΠΈΠ΅, Π² ΠΊΠΎΡΠΎΡΠΎΠΌ ΡΡΠ°ΡΡΠ²ΠΎΠ²Π°Π»ΠΈ ΡΠΏΠ΅ΡΠΈΠ°Π»ΠΈΡΡΡ ΠΏΠΎ ΡΠ΅Ρ
Π½ΠΎΠ»ΠΎΠ³ΠΈΠΈ Π»ΠΈΡΡΡ ΠΏΠΎΠ΄ Π΄Π°Π²Π»Π΅Π½ΠΈΠ΅ΠΌ. ΠΠΎΡΠ»Π΅ ΠΈΡΡΠ΅ΡΠΏΡΠ²Π°ΡΡΠΈΡ
ΠΈΡΡΠ»Π΅Π΄ΠΎΠ²Π°Π½ΠΈΠΉ, ΠΈΡΠΏΡΡΠ°Π½ΠΈΠΉ ΠΈ Π΄Π΅ΠΌΠΎΠ½ΡΡΡΠ°ΡΠΈΠΈ Π² ΠΏΠΈΠ»ΠΎΡΠ½ΠΎΠΌ ΠΌΠ°ΡΡΡΠ°Π±Π΅ ΠΊΠΎΠΌΠ°Π½Π΄Π° ΡΠ°Π·ΡΠ°Π±ΠΎΡΠ°Π»Π° ΡΠ΅Π²ΠΎΠ»ΡΡΠΈΠΎΠ½Π½ΡΡ Π½ΠΎΠ²ΡΡ ΡΠ΅Ρ
Π½ΠΎΠ»ΠΎΠ³ΠΈΡ, ΠΈΡΠΏΠΎΠ»ΡΠ·ΡΡΡΡΡ Π½ΠΈΠ·ΠΊΠΎΠ΅ ΠΏΠΎΡΡΠΎΡΠ½Π½ΠΎΠ΅ Π΄Π°Π²Π»Π΅Π½ΠΈΠ΅ Π½Π°Π³Π½Π΅ΡΠ°Π½ΠΈΡ. ΠΡΠΎΡ Π½ΠΎΠ²ΡΠΉ ΠΏΡΠΎΡΠ΅ΡΡ ΠΏΠΎΠ·Π²ΠΎΠ»ΡΠ΅Ρ ΠΏΠΎ-Π΄ΡΡΠ³ΠΎΠΌΡ Π΄ΡΠΌΠ°ΡΡ ΠΎ ΡΠΎΠΌ, ΠΊΠ°ΠΊ ΠΌΠΎΠΆΠ½ΠΎ ΠΏΡΠΎΠ΅ΠΊΡΠΈΡΠΎΠ²Π°ΡΡ Π΄Π΅ΡΠ°Π»ΠΈ ΠΈ ΡΠΎΡΠΌΡ. Π‘ ΡΡΠΈΠΌ Π½ΠΎΠ²ΡΠΌ ΠΎΡΠΊΡΡΡΠΈΠ΅ΠΌ P&G ΡΠ΅ΡΠΈΠ»Π° Π·Π°ΠΏΡΡΡΠΈΡΡ iMFLUX Inc.ΠΊΠ°ΠΊ ΠΎΡΠ΄Π΅Π»ΡΠ½Π°Ρ Π΄ΠΎΡΠ΅ΡΠ½ΡΡ ΠΊΠΎΠΌΠΏΠ°Π½ΠΈΡ, Π½Π°Ρ
ΠΎΠ΄ΡΡΠ°ΡΡΡ Π² ΠΏΠΎΠ»Π½ΠΎΠΉ ΡΠΎΠ±ΡΡΠ²Π΅Π½Π½ΠΎΡΡΠΈ.
ΠΠΎΠ²ΡΠΉ ΠΏΡΠΎΡΠ΅ΡΡ Π»ΠΈΡΡΡ ΠΏΠΎΠ΄ Π΄Π°Π²Π»Π΅Π½ΠΈΠ΅ΠΌ iMFLUX Π²ΠΊΠ»ΡΡΠ°Π΅Ρ Π² ΡΠ΅Π±Ρ ΡΠΏΠ΅ΡΠΈΠ°Π»ΠΈΠ·ΠΈΡΠΎΠ²Π°Π½Π½ΡΠΉ ΠΊΠΎΠ½ΡΡΠΎΠ»Π»Π΅Ρ, ΠΊΠΎΡΠΎΡΡΠΉ ΠΏΠΎΠ·Π²ΠΎΠ»ΡΠ΅Ρ Π·Π°ΠΏΠΎΠ»Π½ΡΡΡ ΠΏΡΠ΅ΡΡ-ΡΠΎΡΠΌΡ ΠΏΡΠΈ Π±ΠΎΠ»Π΅Π΅ Π½ΠΈΠ·ΠΊΠΎΠΌ Π·Π°Π΄Π°Π½Π½ΠΎΠΌ ΠΏΡΠΎΡΠΈΠ»Π΅ Π΄Π°Π²Π»Π΅Π½ΠΈΡ ΡΠ°ΡΠΏΠ»Π°Π²Π°, ΠΎΠ±Π΅ΡΠΏΠ΅ΡΠΈΠ²Π°Ρ ΠΏΠ΅ΡΠ΅ΠΌΠ΅Π½Π½ΡΡ ΡΠΊΠΎΡΠΎΡΡΡ Π·Π°ΠΏΠΎΠ»Π½Π΅Π½ΠΈΡ, ΠΊΠΎΡΠΎΡΠ°Ρ Π°Π²ΡΠΎΠΌΠ°ΡΠΈΡΠ΅ΡΠΊΠΈ Π°Π΄Π°ΠΏΡΠΈΡΡΠ΅ΡΡΡ ΠΊ Π³Π΅ΠΎΠΌΠ΅ΡΡΠΈΠΈ Π΄Π΅ΡΠ°Π»ΠΈ. Π ΠΏΡΠ΅ΠΈΠΌΡΡΠ΅ΡΡΠ²Π°ΠΌ ΠΎΡΠ½ΠΎΡΡΡΡΡ ΡΠ»ΡΡΡΠ΅Π½Π½ΠΎΠ΅ ΠΊΠ°ΡΠ΅ΡΡΠ²ΠΎ Π΄Π΅ΡΠ°Π»Π΅ΠΉ, Π²ΠΎΠ·ΠΌΠΎΠΆΠ½ΠΎΡΡΠΈ ΠΏΡΠΎΠ΅ΠΊΡΠΈΡΠΎΠ²Π°Π½ΠΈΡ Π½ΠΎΠ²ΡΡ Π΄Π΅ΡΠ°Π»Π΅ΠΉ ΠΈ ΠΏΡΠ΅ΡΡ-ΡΠΎΡΠΌ, ΠΏΠΎΠ²ΡΡΠ΅Π½ΠΈΠ΅ ΡΠΊΠΎΠ»ΠΎΠ³ΠΈΡΠ½ΠΎΡΡΠΈ ΠΈ ΡΠ½ΠΈΠΆΠ΅Π½ΠΈΠ΅ ΠΊΠ°ΠΏΠΈΡΠ°Π»ΡΠ½ΡΡ Π·Π°ΡΡΠ°Ρ.
Π‘Π°ΠΌΡΠΌ Π±ΠΎΠ»ΡΡΠΈΠΌ ΠΏΡΠΎΡΡΠ²ΠΎΠΌ, Π½Π΅ΠΎΠΆΠΈΠ΄Π°Π½Π½ΡΠΌ ΠΈ Π²Π΅ΡΡΠΌΠ° ΠΏΡΠΎΡΠΈΠ²ΠΎΡΠ΅ΡΠ°ΡΠΈΠΌ Π·Π΄ΡΠ°Π²ΠΎΠΌΡ ΡΠΌΡΡΠ»Ρ, ΡΡΠ°Π»ΠΎ ΠΎΡΠΊΡΡΡΠΈΠ΅ ΡΠΎΠ³ΠΎ, ΡΡΠΎ ΠΌΠ΅Π΄Π»Π΅Π½Π½ΠΎΠ΅ Π½Π°ΠΏΠΎΠ»Π½Π΅Π½ΠΈΠ΅ ΠΏΡΠΈΠ²ΠΎΠ΄ΠΈΡ ΠΊ ΡΠΎΠΊΡΠ°ΡΠ΅Π½ΠΈΡ ΠΏΡΠΎΠ΄ΠΎΠ»ΠΆΠΈΡΠ΅Π»ΡΠ½ΠΎΡΡΠΈ ΡΠΈΠΊΠ»Π°.
ΠΠΠ ΠΠ‘Π ΠΠΠ«Π§ΠΠ«Π₯ ΠΠ ΠΠΠΠΠ Π€ΠΠ ΠΠΠΠΠΠΠ―
ΠΡΠΎΡΠ΅ΡΡ iMFLUX ΡΠ΅ΡΠ°Π΅Ρ Π½Π΅ΡΠΊΠΎΠ»ΡΠΊΠΎ ΠΏΡΠΎΠ±Π»Π΅ΠΌ, ΡΠ²ΡΠ·Π°Π½Π½ΡΡ
Ρ ΡΡΠ°Π΄ΠΈΡΠΈΠΎΠ½Π½ΠΎΠΉ ΡΠΈΠ»ΠΎΡΠΎΡΠΈΠ΅ΠΉ ΠΎΠ±ΡΠ°Π±ΠΎΡΠΊΠΈ, Π·Π°ΠΊΠ»ΡΡΠ°ΡΡΠ΅ΠΉΡΡ Π² ΠΈΡΠΏΠΎΠ»ΡΠ·ΠΎΠ²Π°Π½ΠΈΠΈ ΠΊΡΠΈΠ²ΠΎΠΉ ΡΠ΅ΠΎΠ»ΠΎΠ³ΠΈΠΈ Π΄Π»Ρ ΡΡΡΠ°Π½ΠΎΠ²Π»Π΅Π½ΠΈΡ ΠΎΠΏΡΠΈΠΌΠ°Π»ΡΠ½ΠΎΠΉ ΡΠΊΠΎΡΠΎΡΡΠΈ Π½Π°ΠΏΠΎΠ»Π½Π΅Π½ΠΈΡ. ΠΡΠ° ΠΎΠ±ΡΠ΅ΠΏΡΠΈΠ½ΡΡΠ°Ρ ΡΠΈΠ»ΠΎΡΠΎΡΠΈΡ ΠΎΠ±ΡΡΠ½ΠΎ ΠΏΡΠΈΠ²ΠΎΠ΄ΠΈΡ ΠΊ ΠΎΡΠ΅Π½Ρ Π±ΡΡΡΡΠΎΠΌΡ Π·Π°ΠΏΠΎΠ»Π½Π΅Π½ΠΈΡ ΡΠΎΡΠΌΡ, ΡΡΠΎ ΠΏΠΎΠ·Π²ΠΎΠ»ΡΠ΅Ρ ΠΈΡΠΏΠΎΠ»ΡΠ·ΠΎΠ²Π°ΡΡ ΡΠ²ΠΎΠΉΡΡΠ²Π° ΠΏΠΎΠ»ΠΈΠΌΠ΅ΡΠΎΠ² ΡΠ°Π·ΠΆΠΈΠΆΠ°ΡΡΡΡ ΠΏΡΠΈ ΡΠ΄Π²ΠΈΠ³Π΅.
ΠΠ΄Π½Π°ΠΊΠΎ Ρ ΡΡΠΎΠ³ΠΎ ΠΏΠΎΠ΄Ρ ΠΎΠ΄Π° Π΅ΡΡΡ Π½Π΅ΡΠΊΠΎΠ»ΡΠΊΠΎ Π½Π΅Π΄ΠΎΡΡΠ°ΡΠΊΠΎΠ², ΠΏΠΎΡΠΊΠΎΠ»ΡΠΊΡ ΠΎΠ½ ΠΎΠ±ΡΡΠ½ΠΎ ΠΏΡΠΈΠ²ΠΎΠ΄ΠΈΡ ΠΊ ΠΎΡΠ΅Π½Ρ Π²ΡΡΠΎΠΊΠΈΠΌ Π΄Π°Π²Π»Π΅Π½ΠΈΡΠΌ ΡΠΎΡΠΌΠΎΠ²Π°Π½ΠΈΡ. ΠΠΎΡΠΊΠΎΠ»ΡΠΊΡ Π² ΠΏΡΠΎΡΠ΅ΡΡΠ΅ ΠΈΡΠΏΠΎΠ»ΡΠ·ΡΠ΅ΡΡΡ ΠΊΠΎΠ½ΡΡΠΎΠ»ΠΈΡΡΠ΅ΠΌΠ°Ρ ΡΠΊΠΎΡΠΎΡΡΡ Π·Π°ΠΏΠΎΠ»Π½Π΅Π½ΠΈΡ, ΡΠ΅Π·ΡΠ»ΡΡΠΈΡΡΡΡΠ΅Π΅ Π΄Π°Π²Π»Π΅Π½ΠΈΠ΅ ΡΠ°ΡΠΏΠ»Π°Π²Π° ΡΠΈΠ»ΡΠ½ΠΎ Π²Π°ΡΡΠΈΡΡΠ΅ΡΡΡ Π² ΡΠ°Π·Π½ΡΡ ΠΎΠ±Π»Π°ΡΡΡΡ ΠΎΡΡΠΎΡΠΌΠΎΠ²Π°Π½Π½ΠΎΠΉ Π΄Π΅ΡΠ°Π»ΠΈ.ΠΠ° ΡΠΈΡΡΠ½ΠΊΠ΅ 1 ΠΏΠΎΠΊΠ°Π·Π°Π½ΠΎ, ΠΊΠ°ΠΊ ΠΈΠ·ΠΌΠ΅Π½ΡΠ΅ΡΡΡ Π΄Π°Π²Π»Π΅Π½ΠΈΠ΅ Π² ΡΠΈΠΏΠΈΡΠ½ΠΎΠΉ Π΄Π΅ΡΠ°Π»ΠΈ, ΠΎΡΠ»ΠΈΡΠΎΠΉ ΠΏΠΎΠ΄ Π΄Π°Π²Π»Π΅Π½ΠΈΠ΅ΠΌ ΠΎΠ±ΡΡΠ½ΡΠΌ ΡΠΏΠΎΡΠΎΠ±ΠΎΠΌ.
ΠΡΠΈ ΠΏΠ΅ΡΠ΅ΠΏΠ°Π΄Ρ Π΄Π°Π²Π»Π΅Π½ΠΈΡ, ΠΏΡΠΈΡΡΡΠΈΠ΅ ΡΡΠ°Π΄ΠΈΡΠΈΠΎΠ½Π½ΠΎΠΌΡ ΠΏΠΎΠ΄Ρ ΠΎΠ΄Ρ ΠΊ ΡΠΎΡΠΌΠΎΠ²Π°Π½ΠΈΡ, ΠΏΡΠΈΠ²ΠΎΠ΄ΡΡ ΠΊ ΠΌΠ½ΠΎΠΆΠ΅ΡΡΠ²Ρ ΠΏΡΠΎΠ±Π»Π΅ΠΌ, Π²ΠΊΠ»ΡΡΠ°Ρ Π΄ΠΈΡΡΠ΅ΡΠ΅Π½ΡΠΈΠ°Π»ΡΠ½ΡΡ ΡΡΠ°Π΄ΠΊΡ (ΠΈΠ»ΠΈ Π΄Π΅ΡΠΎΡΠΌΠ°ΡΠΈΡ), ΠΈΠ·ΠΌΠ΅Π½Π΅Π½ΠΈΡ ΡΠ°Π·ΠΌΠ΅ΡΠΎΠ², Π·Π°ΡΡΠ΅Π½ΡΠ΅Π² ΠΈ Π½Π΅ΡΠΏΠΎΡΠΎΠ±Π½ΠΎΡΡΡ ΠΏΡΠΈΡΠΏΠΎΡΠΎΠ±ΠΈΡΡΡΡ ΠΊ ΠΏΠ΅ΡΠ΅Ρ ΠΎΠ΄Π°ΠΌ ΠΌΠ΅ΠΆΠ΄Ρ ΡΠΎΠ»ΡΠΈΠ½ΠΎΠΉ ΡΡΠ΅Π½ΠΊΠΈ ΠΈ Π³Π΅ΠΎΠΌΠ΅ΡΡΠΈΠΈ Π΄Π΅ΡΠ°Π»ΠΈ.
ΠΡΠΎΡΠ΅ΡΡ iMFLUX ΡΠ΅ΡΠ°Π΅Ρ ΡΡΠΈ ΠΏΡΠΎΠ±Π»Π΅ΠΌΡ Π·Π° ΡΡΠ΅Ρ ΠΈΡΠΏΠΎΠ»ΡΠ·ΠΎΠ²Π°Π½ΠΈΡ ΠΏΠΎΡΡΠΎΡΠ½Π½ΠΎΠ³ΠΎ Π½ΠΈΠ·ΠΊΠΎΠ³ΠΎ Π΄Π°Π²Π»Π΅Π½ΠΈΡ Π½Π°ΠΏΠΎΠ»Π½Π΅Π½ΠΈΡ, ΡΡΠΎ ΠΏΡΠΈΠ²ΠΎΠ΄ΠΈΡ ΠΊ ΡΠ°Π²Π½ΠΎΠΌΠ΅ΡΠ½ΠΎΠΌΡ Π΄Π°Π²Π»Π΅Π½ΠΈΡ Π² ΠΎΡΡΠΎΡΠΌΠΎΠ²Π°Π½Π½ΠΎΠΉ Π΄Π΅ΡΠ°Π»ΠΈ.ΠΠΌΠ΅ΡΡΠΎ ΠΈΡΠΏΠΎΠ»ΡΠ·ΠΎΠ²Π°Π½ΠΈΡ ΠΏΠΎΡΡΠΎΡΠ½Π½ΠΎΠΉ ΡΠΊΠΎΡΠΎΡΡΠΈ Π²ΠΏΡΡΡΠΊΠ°, ΡΠΊΠΎΡΠΎΡΡΡ ΠΌΠΎΠΆΠ΅Ρ ΠΈΠ·ΠΌΠ΅Π½ΡΡΡΡΡ Π΄Π»Ρ ΠΏΠΎΠ΄Π΄Π΅ΡΠΆΠ°Π½ΠΈΡ ΠΏΠΎΡΡΠΎΡΠ½Π½ΠΎΠ³ΠΎ ΠΏΠ»Π°ΡΡΠΈΡΠ΅ΡΠΊΠΎΠ³ΠΎ Π΄Π°Π²Π»Π΅Π½ΠΈΡ. ΠΠ° ΡΠΈΡΡΠ½ΠΊΠ΅ 2 ΠΏΠΎΠΊΠ°Π·Π°Π½ΠΎ, ΠΊΠ°ΠΊ ΠΈΠ·ΠΌΠ΅Π½ΡΠ΅ΡΡΡ ΡΠΊΠΎΡΠΎΡΡΡ Π² ΠΏΡΠΎΡΠ΅ΡΡΠ΅ iMFLUX.
ΠΠΠΠΠΠΠΠΠΠ Π‘ΠΠΠΠΠΠΠ― Π£Π ΠΠΠΠΠΠΠ‘Π’Π ΠΠ«Π‘Π’Π Π«Π₯ Π¦ΠΠΠΠΠ
Π’Π΅Ρ Π½ΠΎΠ»ΠΎΠ³ΠΈΡ iMFLUX ΡΠΏΡΠ°Π²Π»ΡΠ΅Ρ ΠΏΡΠΎΡΠ΅ΡΡΠΎΠΌ ΡΠΎΡΠΌΠΎΠ²Π°Π½ΠΈΡ Ρ ΠΏΠΎΠΌΠΎΡΡΡ ΠΏΠ»Π°ΡΡΠΈΡΠ΅ΡΠΊΠΎΠ³ΠΎ Π΄Π°Π²Π»Π΅Π½ΠΈΡ, Π° Π½Π΅ ΡΡΠ°Π΄ΠΈΡΠΈΠΎΠ½Π½ΡΠΌ ΠΌΠ΅ΡΠΎΠ΄ΠΎΠΌ Π·Π°ΠΏΠΎΠ»Π½Π΅Π½ΠΈΡ ΡΠΎΡΠΌΡ Π² ΡΠΎΠΎΡΠ²Π΅ΡΡΡΠ²ΠΈΠΈ Ρ ΠΎΠ±ΡΠ΅ΠΌΠ½ΡΠΌ ΡΠ°ΡΡ ΠΎΠ΄ΠΎΠΌ (ΡΠ°ΠΊΠΆΠ΅ Π½Π°Π·ΡΠ²Π°Π΅ΠΌΡΠΌ Π·Π°ΠΏΠΎΠ»Π½Π΅Π½ΠΈΠ΅ΠΌ ΠΏΠΎ ΡΠΊΠΎΡΠΎΡΡΠΈ). Π£ΠΏΡΠ°Π²Π»Π΅Π½ΠΈΠ΅ ΠΏΡΠΎΡΠ΅ΡΡΠΎΠΌ Ρ ΠΏΠΎΠΌΠΎΡΡΡ Π΄Π°Π²Π»Π΅Π½ΠΈΡ ΡΠ°ΡΠΏΠ»Π°Π²Π° ΠΏΠ»Π°ΡΡΠΈΠΊΠ° ΠΏΠΎΠ·Π²ΠΎΠ»ΡΠ΅Ρ ΡΠ°ΡΠΏΠ»Π°Π²Ρ ΡΠ΅ΡΡ ΡΠ΅ΡΠ΅Π· ΡΠΈΡΡΠ΅ΠΌΡ ΠΏΠΎΠ΄Π°ΡΠΈ ΡΠ°ΡΠΏΠ»Π°Π²Π° ΠΈ ΠΏΠΎΠ»ΠΎΡΡΡ ΡΠΎΡΠΌΡ Π±Π΅Π· Π²ΠΎΠ·ΠΌΠΎΠΆΠ½ΠΎΡΡΠΈ ΠΎΡΡΠ°Π½ΠΎΠ²ΠΊΠΈ ΠΈΠ»ΠΈ ΠΊΠΎΠ»Π΅Π±Π°Π½ΠΈΠΉ.ΠΠΎΡΡΠΎΡΠ½Π½ΠΎΠ΅, Π½Π΅ ΠΊΠΎΠ»Π΅Π±Π»ΡΡΠ΅Π΅ΡΡ Π΄Π°Π²Π»Π΅Π½ΠΈΠ΅ Π½Π΅ΠΏΡΠ΅ΡΡΠ²Π½ΠΎ ΠΏΡΠΎΠ΄Π²ΠΈΠ³Π°Π΅Ρ ΡΡΠΎΠ½Ρ ΠΏΠΎΡΠΎΠΊΠ° Π² ΠΊΠ°ΠΆΠ΄ΠΎΠΉ ΡΠΎΡΠΊΠ΅, Π΄Π°ΠΆΠ΅ ΡΠ°ΠΌ, Π³Π΄Π΅ ΠΎΠ½ Π²ΡΡΡΠ΅ΡΠ°Π΅ΡΡΡ Ρ ΡΠ΅Π±ΡΠ°ΠΌΠΈ, Π²ΡΡΡΡΠΏΠ°ΠΌΠΈ ΠΈΠ»ΠΈ Π΄ΡΡΠ³ΠΈΠΌΠΈ ΡΠ»Π΅ΠΌΠ΅Π½ΡΠ°ΠΌΠΈ.
ΠΡΠΎΡΠ΅ΡΡ ΠΎΡΠ½ΠΎΠ²Π°Π½ Π½Π° ΠΎΡ
Π»Π°ΠΆΠ΄Π΅Π½ΠΈΠΈ ΡΠ°ΡΠΏΠ»Π°Π²Π° Π² ΠΊΡΠΈΡΡΠ°Π»Π»ΠΈΠ·Π°ΡΠΎΡΠ΅ Π΄Π»Ρ ΡΠΎΠ·Π΄Π°Π½ΠΈΡ ΡΠΎΠΏΡΠΎΡΠΈΠ²Π»Π΅Π½ΠΈΡ ΠΏΠΎΡΠΎΠΊΡ, ΡΡΠΎ, Π² ΡΠ²ΠΎΡ ΠΎΡΠ΅ΡΠ΅Π΄Ρ, ΠΏΠΎΠ·Π²ΠΎΠ»ΡΠ΅Ρ Π΄Π°Π²Π»Π΅Π½ΠΈΡ ΡΡΠ°Π±ΠΈΠ»ΠΈΠ·ΠΈΡΠΎΠ²Π°ΡΡΡΡ ΠΈ ΠΎΡΡΠ°Π²Π°ΡΡΡΡ ΠΏΠΎΡΡΠΎΡΠ½Π½ΡΠΌ Π²Π½ΡΡΡΠΈ ΠΏΡΡΠΈ ΠΏΠΎΡΠΎΠΊΠ° ΠΈ Π½Π° ΡΡΠΎΠ½ΡΠ΅ ΠΏΠΎΡΠΎΠΊΠ°. ΠΠΎΡΠΊΠΎΠ»ΡΠΊΡ ΡΠΎΡΠΌΠ° Π·Π°ΠΏΠΎΠ»Π½ΡΠ΅ΡΡΡ ΠΎΡΠ΅Π½Ρ ΠΌΠ΅Π΄Π»Π΅Π½Π½ΠΎ, ΠΏΠΎΠ»ΠΈΠΌΠ΅Ρ ΠΏΠΎΡΡΠΎΡΠ½Π½ΠΎ ΠΎΡ
Π»Π°ΠΆΠ΄Π°Π΅ΡΡΡ ΠΈ ΡΠΏΠ»ΠΎΡΠ½ΡΠ΅ΡΡΡ, ΠΏΠΎΠΊΠ° ΡΠΎΡΠΌΠ° Π·Π°ΠΏΠΎΠ»Π½ΡΠ΅ΡΡΡ. ΠΠ΅ΡΠ°Π»Ρ Π½Π° ΡΠ°ΠΌΠΎΠΌ Π΄Π΅Π»Π΅ Β«ΡΠΏΠ°ΠΊΠΎΠ²ΡΠ²Π°Π΅ΡΡΡ ΠΏΠΎ ΠΌΠ΅ΡΠ΅ Π·Π°ΠΏΠΎΠ»Π½Π΅Π½ΠΈΡΒ».β
ΠΠ° ΡΠΈΡ. 3 ΠΏΠΎΠΊΠ°Π·Π°Π½Ρ ΠΊΠΎΡΠΎΡΠΊΠΈΠ΅ ΡΠ½ΠΈΠΌΠΊΠΈ ΠΏΡΠΎΡΠ΅ΡΡΠ° iMFLUX ΠΈ ΡΠΈΠΏΠΈΡΠ½ΠΎΠ³ΠΎ ΠΎΠ±ΡΡΠ½ΠΎΠ³ΠΎ ΠΏΡΠΎΡΠ΅ΡΡΠ°. ΠΠ°ΠΊ Π²ΠΈΠ΄ΠΈΡΠ΅, ΠΊΠΎΡΠΎΡΠΊΠΈΠ΅ ΠΊΠ°Π΄ΡΡ iMFLUX ΠΏΠΎΠ»Π½ΠΎΡΡΡΡ ΡΠΏΠ°ΠΊΠΎΠ²Π°Π½Ρ Π½Π΅Π·Π°Π²ΠΈΡΠΈΠΌΠΎ ΠΎΡ ΡΠΎΠ³ΠΎ, Π³Π΄Π΅ ΠΎΡΡΠ°Π½ΠΎΠ²ΠΈΠ»ΡΡ ΡΡΠΎΠ½Ρ ΠΏΠΎΡΠΎΠΊΠ°, Π² ΡΠΎ Π²ΡΠ΅ΠΌΡ ΠΊΠ°ΠΊ ΠΎΠ±ΡΡΠ½ΡΠ΅ Π΄Π΅ΡΠ°Π»ΠΈ Π½Π΅ ΡΠΏΠ°ΠΊΠΎΠ²Π°Π½Ρ ΠΈ ΠΏΡΠΎΠ΄ΠΎΠ»ΠΆΠ°ΡΡ ΡΠΏΠ»ΠΎΡΠ½ΡΡΡΡΡ Π·Π° ΡΡΠΎΠ½ΡΠΎΠΌ ΠΏΠΎΡΠΎΠΊΠ°.
ΠΡΠΎΡΠ΅ΡΡ iMFLUX Π·Π°ΠΏΠΎΠ»Π½ΡΠ΅ΡΡΡ ΠΌΠ΅Π΄Π»Π΅Π½Π½Π΅Π΅, Π½ΠΎ ΠΏΡΠΈΠ²ΠΎΠ΄ΠΈΡ ΠΊ Π±ΠΎΠ»Π΅Π΅ Π±ΡΡΡΡΠΎΠΌΡ ΡΠΈΠΊΠ»Ρ ΡΠΎΡΠΌΠΎΠ²Π°Π½ΠΈΡ. ΠΡΡΡ Π½Π΅ΡΠΊΠΎΠ»ΡΠΊΠΎ ΡΠ°ΠΊΡΠΎΡΠΎΠ²:
- ΠΠΎΠ»Π΅Π΅ Π½ΠΈΠ·ΠΊΠ°Ρ ΡΠΊΠΎΡΠΎΡΡΡ Π½Π°ΠΏΠΎΠ»Π½Π΅Π½ΠΈΡ ΠΏΡΠΈΠ²ΠΎΠ΄ΠΈΡ ΠΊ ΠΌΠ΅Π½ΡΡΠ΅ΠΌΡ Π½Π°Π³ΡΠ΅Π²Ρ ΠΏΡΠΈ ΡΠ΄Π²ΠΈΠ³Π΅, ΡΡΠΎ ΡΡΠ΅Π±ΡΠ΅Ρ ΠΌΠ΅Π½ΡΡΠ΅ Π²ΡΠ΅ΠΌΠ΅Π½ΠΈ Π½Π° ΠΎΡ Π»Π°ΠΆΠ΄Π΅Π½ΠΈΠ΅.
- Π€ΠΎΡΠΌΠ° Π·Π°ΠΏΠΎΠ»Π½ΡΠ΅ΡΡΡ ΡΠ°ΠΊ ΠΌΠ΅Π΄Π»Π΅Π½Π½ΠΎ, ΡΡΠΎ ΠΎΠ½Π° Β«ΡΠΏΠ»ΠΎΡΠ½ΡΠ΅ΡΡΡ ΠΏΠΎ ΠΌΠ΅ΡΠ΅ Π·Π°ΠΏΠΎΠ»Π½Π΅Π½ΠΈΡΒ», ΡΠ°ΠΊΠΈΠΌ ΠΎΠ±ΡΠ°Π·ΠΎΠΌ, ΠΌΠ°ΡΠ΅ΡΠΈΠ°Π» ΠΏΠΎΡΡΠΎΡΠ½Π½ΠΎ ΠΊΠΎΠ½ΡΠ°ΠΊΡΠΈΡΡΠ΅Ρ ΡΠΎ ΡΡΠ΅Π½ΠΊΠ°ΠΌΠΈ ΡΠΎΡΠΌΡ, ΠΎΠ±Π΅ΡΠΏΠ΅ΡΠΈΠ²Π°Ρ ΡΡΡΠ΅ΠΊΡΠΈΠ²Π½ΠΎΠ΅ ΠΎΡ Π»Π°ΠΆΠ΄Π΅Π½ΠΈΠ΅.
- ΠΠΎΠ³Π΄Π° ΡΠΎΡΠΌΠ° ΠΏΠΎΠ»Π½ΠΎΡΡΡΡ Π·Π°ΠΏΠΎΠ»Π½Π΅Π½Π°, Π΄Π΅ΡΠ°Π»Ρ ΡΠΆΠ΅ ΡΠΏΠ°ΠΊΠΎΠ²Π°Π½Π°, ΡΡΠΎ ΠΏΠΎ ΡΡΡΠ΅ΡΡΠ²Ρ ΠΈΡΠΊΠ»ΡΡΠ°Π΅Ρ ΡΠ°Π·Ρ ΡΠΏΠ°ΠΊΠΎΠ²ΠΊΠΈ ΠΈ ΡΠΎΠΊΡΠ°ΡΠ°Π΅Ρ ΡΠ°ΡΡΡ ΡΠΈΠΊΠ»Π° ΠΎΡ
Π»Π°ΠΆΠ΄Π΅Π½ΠΈΡ. ΠΠΎΠΌΠ±ΠΈΠ½ΠΈΡΠΎΠ²Π°Π½Π½ΡΠΉ ΡΡΡΠ΅ΠΊΡ ΠΏΡΠΈΠ²ΠΎΠ΄ΠΈΡ ΠΊ ΡΠΎΠΊΡΠ°ΡΠ΅Π½ΠΈΡ Π²ΡΠ΅ΠΌΠ΅Π½ΠΈ ΡΠΈΠΊΠ»Π°, ΠΊΠ°ΠΊ ΠΏΠΎΠΊΠ°Π·Π°Π½ΠΎ Π½Π° ΡΠΈΡ.
4.
ΠΠΠ Π ΠΠΠΠΠΠΠΠΠ’Π¬ ΠΠΠΠ«Π ΠΠ ΠΠ¦ΠΠ‘Π‘
iMFLUX Inc., ΡΠΎΠ·Π΄Π°Π½Π½Π°Ρ Π² 2013 Π³ΠΎΠ΄Ρ, ΠΏΡΠ΅Π΄Π»Π°Π³Π°Π΅Ρ ΡΡΡ Π·Π°ΠΏΠ°ΡΠ΅Π½ΡΠΎΠ²Π°Π½Π½ΡΡ ΡΠ΅Ρ Π½ΠΎΠ»ΠΎΠ³ΠΈΡ, Π΄ΠΎΡΡΡΠΏΠ½ΡΡ ΠΏΠΎ Π»ΠΈΡΠ΅Π½Π·ΠΈΠΈ. Π’Π΅Ρ Π½ΠΎΠ»ΠΎΠ³ΠΈΡ Π°ΠΏΡΠΎΠ±ΠΈΡΠΎΠ²Π°Π½Π° Π² ΠΏΠΎΠ»Π½ΠΎΠΌ ΠΎΠ±ΡΠ΅ΠΌΠ΅ Π² ΡΠΎΡΠ½ΡΡ ΠΊΠΎΠΌΠΌΠ΅ΡΡΠ΅ΡΠΊΠΈΡ ΠΏΡΠΈΠ»ΠΎΠΆΠ΅Π½ΠΈΠΉ. ΠΠ½ ΡΠΊΡΠΊΠ»ΡΠ·ΠΈΠ²Π½ΠΎ ΠΏΠΎΡΡΠ°Π²Π»ΡΠ΅ΡΡΡ ΠΊΠΎΠΌΠΏΠ°Π½ΠΈΠ΅ΠΉ iMFLUX Inc., ΡΠ°ΡΠΏΠΎΠ»ΠΎΠΆΠ΅Π½Π½ΠΎΠΉ Π² ΠΠ°ΠΌΠΈΠ»ΡΡΠΎΠ½Π΅, ΡΡΠ°Ρ ΠΠ³Π°ΠΉΠΎ.
ΠΠ»Ρ ΠΌΠ°ΡΠΈΠ½Ρ Π΄Π»Ρ Π»ΠΈΡΡΡ ΠΏΠΎΠ΄ Π΄Π°Π²Π»Π΅Π½ΠΈΠ΅ΠΌ Π½Π΅ΠΎΠ±Ρ ΠΎΠ΄ΠΈΠΌ ΡΠΏΠ΅ΡΠΈΠ°Π»ΠΈΠ·ΠΈΡΠΎΠ²Π°Π½Π½ΡΠΉ ΠΊΠΎΠ½ΡΡΠΎΠ»Π»Π΅Ρ, ΠΏΠΎΠ·Π²ΠΎΠ»ΡΡΡΠΈΠΉ ΡΠΏΡΠ°Π²Π»ΡΡΡ ΠΏΡΠΎΡΠ΅ΡΡΠΎΠΌ ΠΏΠ»Π°ΡΡΠΈΡΠ΅ΡΠΊΠΈΠΌ Π΄Π°Π²Π»Π΅Π½ΠΈΠ΅ΠΌ, Π° Π½Π΅ ΡΠΊΠΎΡΠΎΡΡΡΡ ΠΈ Π΄Π°Π²Π»Π΅Π½ΠΈΠ΅ΠΌ Π²ΡΠ΄Π΅ΡΠΆΠΊΠΈ. ΠΠ°ΡΡΠΈΠΊ Π΄Π°Π²Π»Π΅Π½ΠΈΡ Π΄ΠΎΠ±Π°Π²Π»Π΅Π½ ΠΊ ΡΠΎΠΏΠ»Ρ ΠΌΠ°ΡΠΈΠ½Ρ, ΡΡΠΎΠ±Ρ ΠΎΠ±Π΅ΡΠΏΠ΅ΡΠΈΡΡ ΠΈΠ·ΠΌΠ΅ΡΠ΅Π½ΠΈΠ΅ Π΄Π°Π²Π»Π΅Π½ΠΈΡ ΠΏΠ»Π°ΡΡΠΈΠΊΠ°, ΠΏΠΎΡΡΡΠΏΠ°ΡΡΠ΅Π³ΠΎ Π² ΡΠΈΡΡΠ΅ΠΌΡ ΠΏΠΎΠ΄Π°ΡΠΈ ΠΌΠ°ΡΠ΅ΡΠΈΠ°Π»Π°, Π² ΡΠ΅Π°Π»ΡΠ½ΠΎΠΌ Π²ΡΠ΅ΠΌΠ΅Π½ΠΈ.ΠΠΎΠ½ΡΡΠΎΠ»Π»Π΅Ρ ΠΈΡΠΏΠΎΠ»ΡΠ·ΡΠ΅Ρ Π΄Π°Π²Π»Π΅Π½ΠΈΠ΅ ΠΏΠ»Π°ΡΡΠΈΠΊΠ° Π² ΠΊΠ°ΡΠ΅ΡΡΠ²Π΅ ΠΎΡΠ½ΠΎΠ²Π½ΠΎΠ³ΠΎ ΡΠΏΡΠ°Π²Π»ΡΡΡΠ΅Π³ΠΎ ΡΠΈΠ³Π½Π°Π»Π° Π½Π° ΠΏΡΠΎΡΡΠΆΠ΅Π½ΠΈΠΈ Π²ΡΠ΅Π³ΠΎ Π·Π°ΠΏΠΎΠ»Π½Π΅Π½ΠΈΡ ΡΠΎΡΠΌΡ. Π ΡΠΎΡΠΌΠ΅ Π΄ΠΎΠ±Π°Π²Π»ΡΡΡΡΡ Π΄Π°ΡΡΠΈΠΊΠΈ, ΠΎΠ±Π΅ΡΠΏΠ΅ΡΠΈΠ²Π°ΡΡΠΈΠ΅ ΠΈΠ½Π΄ΠΈΠΊΠ°ΡΠΈΡ Π΄Π°Π²Π»Π΅Π½ΠΈΡ Π² ΡΠΎΡΠΌΠ΅ ΠΈ ΠΏΡΠΎΠ΄Π²ΠΈΠΆΠ΅Π½ΠΈΠ΅ ΡΡΠΎΠ½ΡΠ° ΠΏΠΎΡΠΎΠΊΠ°.
ΠΠ±ΡΠ°ΡΠ½Π°Ρ ΡΠ²ΡΠ·Ρ ΠΎΡ Π΄Π°ΡΡΠΈΠΊΠΎΠ² ΠΏΡΠ΅ΡΡ-ΡΠΎΡΠΌΡ Π½Π΅ΠΎΠ±Ρ
ΠΎΠ΄ΠΈΠΌΠ° Π΄Π»Ρ ΠΎΠ±Π΅ΡΠΏΠ΅ΡΠ΅Π½ΠΈΡ ΠΎΠΏΡΠΈΠΌΠ°Π»ΡΠ½ΠΎΠ³ΠΎ Π΄Π°Π²Π»Π΅Π½ΠΈΡ Π² ΠΏΡΠ΅ΡΡ-ΡΠΎΡΠΌΠ΅ ΠΈ Π²Π½Π΅ΡΠ΅Π½ΠΈΡ ΠΈΠ·ΠΌΠ΅Π½Π΅Π½ΠΈΠΉ Π² Π΄Π°Π²Π»Π΅Π½ΠΈΠ΅ Π²ΠΏΡΡΡΠΊΠ° Π² ΡΠ΅Π°Π»ΡΠ½ΠΎΠΌ Π²ΡΠ΅ΠΌΠ΅Π½ΠΈ Π² ΡΠ΅Π·ΡΠ»ΡΡΠ°ΡΠ΅ ΠΈΠ·ΠΌΠ΅Π½Π΅Π½ΠΈΠΉ ΠΌΠ°ΡΠ΅ΡΠΈΠ°Π»Π°, ΠΏΡΠ΅ΡΡ-ΡΠΎΡΠΌΡ ΠΈΠ»ΠΈ ΠΏΡΠΎΡΠ΅ΡΡΠ°. ΠΡΠ΅Π΄ΠΎΡΡΠ°Π²Π»ΡΠ΅ΡΡΡ ΠΏΠΎΠ»ΡΠ·ΠΎΠ²Π°ΡΠ΅Π»ΡΡΠΊΠΈΠΉ ΠΈΠ½ΡΠ΅ΡΡΠ΅ΠΉΡ, ΠΏΠΎΠ·Π²ΠΎΠ»ΡΡΡΠΈΠΉ Π²Π²ΠΎΠ΄ΠΈΡΡ ΠΏΠ°ΡΠ°ΠΌΠ΅ΡΡΡ ΠΏΡΠΎΡΠ΅ΡΡΠ° ΠΈ ΠΊΠΎΠ½ΡΡΠΎΠ»ΠΈΡΠΎΠ²Π°ΡΡ ΠΏΡΠΎΡΠ΅ΡΡ.ΠΠ° ΡΠΈΡΡΠ½ΠΊΠ΅ 5 ΠΏΠΎΠΊΠ°Π·Π°Π½Ρ ΡΠ»Π΅ΠΌΠ΅Π½ΡΡ ΡΠΈΡΠΌΠ΅Π½Π½ΠΎΠΉ ΡΠΈΡΡΠ΅ΠΌΡ ΡΠΏΡΠ°Π²Π»Π΅Π½ΠΈΡ.
ΠΡΠΎΡΠ΅ΡΡ iMFLUX ΠΌΠΎΠΆΠ΅Ρ Π±ΡΡΡ ΠΈΠ½ΡΠ΅Π³ΡΠΈΡΠΎΠ²Π°Π½ Ρ Π±ΠΎΠ»ΡΡΠΈΠ½ΡΡΠ²ΠΎΠΌ ΡΠΈΠΏΠΎΠ² ΠΌΠ°ΡΠΈΠ½, Π²ΠΊΠ»ΡΡΠ°Ρ Π³ΠΈΠ΄ΡΠ°Π²Π»ΠΈΡΠ΅ΡΠΊΠΈΠ΅, ΠΏΠΎΠ»Π½ΠΎΡΡΡΡ ΡΠ»Π΅ΠΊΡΡΠΈΡΠ΅ΡΠΊΠΈΠ΅ ΠΈ Π³ΠΈΠ±ΡΠΈΠ΄Π½ΡΠ΅ Π»ΠΈΡΡΠ΅Π²ΡΠ΅ ΠΌΠ°ΡΠΈΠ½Ρ. ΠΠ»Ρ ΡΡΠΎΠΉ ΡΠ΅Ρ Π½ΠΎΠ»ΠΎΠ³ΠΈΠΈ Π΄ΠΎΡΡΡΠΏΠ½ΠΎ ΠΌΠ½ΠΎΠΆΠ΅ΡΡΠ²ΠΎ OEM-ΠΊΠΎΠΌΠΏΠ»Π΅ΠΊΡΠΎΠ² Π΄Π»Ρ Π½ΠΎΠ²ΡΡ ΠΏΡΠ΅ΡΡΠΎΠ² ΠΎΡ Π½Π΅ΡΠΊΠΎΠ»ΡΠΊΠΈΡ ΠΊΡΡΠΏΠ½ΡΡ ΠΏΡΠΎΠΈΠ·Π²ΠΎΠ΄ΠΈΡΠ΅Π»Π΅ΠΉ ΠΎΠ±ΠΎΡΡΠ΄ΠΎΠ²Π°Π½ΠΈΡ, ΠΊΠΎΡΠΎΡΡΠ΅ ΠΎΠ±Π΅ΡΠΏΠ΅ΡΠΈΠ²Π°ΡΡ Π±ΡΡΡΡΡΡ ΠΈ ΠΏΡΠΎΡΡΡΡ ΠΈΠ½ΡΠ΅Π³ΡΠ°ΡΠΈΡ. ΠΠ΄Π½Π°ΠΊΠΎ iMFLUX ΠΌΠΎΠΆΠ½ΠΎ ΠΈΠ½ΡΠ΅Π³ΡΠΈΡΠΎΠ²Π°ΡΡ ΠΈ Ρ ΡΡΡΠ΅ΡΡΠ²ΡΡΡΠΈΠΌΠΈ ΠΌΠ°ΡΠΈΠ½Π°ΠΌΠΈ. ΠΡΠΎΡΠ΅ΡΡ ΡΡΡΠ΅ΠΊΡΠΈΠ²Π½ΠΎ ΡΠ°Π±ΠΎΡΠ°Π΅Ρ Ρ ΠΏΡΠ΅ΡΡ-ΡΠΎΡΠΌΠ°ΠΌΠΈ, ΡΠ°Π·ΡΠ°Π±ΠΎΡΠ°Π½Π½ΡΠΌΠΈ ΡΠΏΠ΅ΡΠΈΠ°Π»ΡΠ½ΠΎ Π΄Π»Ρ iMFLUX, Π° ΡΠ°ΠΊΠΆΠ΅ Ρ ΠΌΠΎΠ΄Π΅ΡΠ½ΠΈΠ·ΠΈΡΠΎΠ²Π°Π½Π½ΡΠΌΠΈ ΠΊΠΎΠΌΠ±ΠΈΠ½Π°ΡΠΈΡΠΌΠΈ ΠΏΡΠ΅ΡΡ-ΡΠΎΡΠΌ ΠΈ ΠΏΡΠ΅ΡΡΠΎΠ².
ΠΡΠ° ΡΠΈΡΡΠ΅ΠΌΠ° ΠΈΡΠΏΠΎΠ»ΡΠ·ΡΠ΅ΡΡΡ Π² ΡΠ°Π·Π»ΠΈΡΠ½ΡΡ
ΠΎΡΡΠ°ΡΠ»ΡΡ
ΠΏΡΠΎΠΌΡΡΠ»Π΅Π½Π½ΠΎΡΡΠΈ, Π²ΠΊΠ»ΡΡΠ°Ρ Π°Π²ΡΠΎΠΌΠΎΠ±ΠΈΠ»Π΅ΡΡΡΠΎΠ΅Π½ΠΈΠ΅, ΠΌΠ΅Π΄ΠΈΡΠΈΠ½Ρ, ΡΠΏΠ°ΠΊΠΎΠ²ΠΊΡ ΠΈ ΠΏΡΠΎΠΈΠ·Π²ΠΎΠ΄ΡΡΠ²ΠΎ ΠΏΠΎΡΡΠ΅Π±ΠΈΡΠ΅Π»ΡΡΠΊΠΈΡ
ΡΠΎΠ²Π°ΡΠΎΠ². ΠΡΠΏΠΎΠ»Π½Π΅Π½ΠΈΠ΅ ΠΏΡΠΎΡΠ΅ΡΡΠ° Ρ Π·Π°ΠΌΠΊΠ½ΡΡΡΠΌ ΠΊΠΎΠ½ΡΡΡΠΎΠΌ, Π½ΠΈΠ·ΠΊΠΈΠΌ ΠΈ ΠΏΠΎΡΡΠΎΡΠ½Π½ΡΠΌ ΠΊΠΎΠ½ΡΡΠΎΠ»Π΅ΠΌ Π΄Π°Π²Π»Π΅Π½ΠΈΡ ΠΎΠ·Π½Π°ΡΠ°Π΅Ρ, ΡΡΠΎ Π±ΠΎΠ»ΡΡΠΈΠ½ΡΡΠ²ΠΎ ΠΏΠΎΠ»ΠΈΠΌΠ΅ΡΠΎΠ² ΡΠ°Π±ΠΎΡΠ°Π΅Ρ Π»ΡΡΡΠ΅ Ρ iMFLUX, ΡΠ΅ΠΌ Π² ΡΡΠ΅Π΄Π΅ Ρ Π²ΡΡΠΎΠΊΠΈΠΌ ΡΠ΄Π²ΠΈΠ³ΠΎΠΌ ΠΎΠ±ΡΡΠ½ΠΎΠ³ΠΎ ΠΏΡΠΎΡΠ΅ΡΡΠ°.
ΠΠ ΠΠΠΠ£Π©ΠΠ‘Π’ΠΠ ΠΠ ΠΠ¦ΠΠ‘Π‘Π IMFLUX
ΠΡΠ΅ΠΈΠΌΡΡΠ΅ΡΡΠ²Π° ΠΏΡΠΎΡΠ΅ΡΡΠ° iMFLUX ΠΎΠ±ΡΡΠ»ΠΎΠ²Π»Π΅Π½Ρ ΡΠ΅ΡΡΡΡΠΌΡ ΠΊΠ»ΡΡΠ΅Π²ΡΠΌΠΈ ΠΎΡΠ»ΠΈΡΠΈΡΠΌΠΈ ΠΎΡ ΠΎΠ±ΡΡΠ½ΠΎΠ³ΠΎ ΡΠΎΡΠΌΠΎΠ²Π°Π½ΠΈΡ:
- ΠΠ°ΠΏΠΎΠ»Π½Π΅Π½ΠΈΠ΅ ΠΏΠΎΠ΄ Π½ΠΈΠ·ΠΊΠΈΠΌ ΠΏΠΎΡΡΠΎΡΠ½Π½ΡΠΌ Π΄Π°Π²Π»Π΅Π½ΠΈΠ΅ΠΌ;
- Π£ΠΏΠ°ΠΊΠΎΠ²ΠΊΠ° ΠΏΠΎ ΠΌΠ΅ΡΠ΅ Π·Π°ΠΏΠΎΠ»Π½Π΅Π½ΠΈΡ ΡΠΎΡΠΌΡ;
- ΠΠ°ΠΏΠΎΠ»Π½Π΅Π½ΠΈΠ΅ Π±Π΅Π· ΠΊΠΎΠ»Π΅Π±Π°Π½ΠΈΠΉ ΠΏΠΎΡΠΎΠΊΠ°;
- ΠΠ°ΠΊ ΠΎΠ½ ΠΈΡΠΏΠΎΠ»ΡΠ·ΡΠ΅Ρ ΠΎΠ±ΡΠ°ΡΠ½ΡΡ ΡΠ²ΡΠ·Ρ ΠΏΠΎ Π΄Π°Π²Π»Π΅Π½ΠΈΡ Π² ΠΏΠΎΠ»ΠΎΡΡΠΈ ΠΎΡ ΡΠΎΡΠΌΡ.
Π ΡΠ°Π±Π»ΠΈΡΠ΅ Π½Π° ΠΏΡΠ΅Π΄ΡΠ΄ΡΡΠ΅ΠΉ ΡΡΡΠ°Π½ΠΈΡΠ΅ ΠΎΠ±ΠΎΠ±ΡΠ΅Π½Ρ ΡΠΈΠΏΠΈΡΠ½ΡΠ΅ ΠΏΡΠ΅ΠΈΠΌΡΡΠ΅ΡΡΠ²Π° ΡΡΠΈΡ ΡΠ°Π·Π»ΠΈΡΠΈΠΉ.
Π§ΠΠ’Π«Π Π ΠΠ ΠΠΠΠ Π
ΠΡΠΈΠΌΠ΅Ρ 1 : ΠΠ΅Π΄ΠΈΡΠΈΠ½ΡΠΊΠ°Ρ Π΄Π΅ΡΠ°Π»Ρ ΠΈΠ· ΠΏΠΎΠ»ΠΈΠΊΠ°ΡΠ±ΠΎΠ½Π°ΡΠ° Π±ΡΠ»Π° ΠΏΠ΅ΡΠ΅Π²Π΅Π΄Π΅Π½Π° Π½Π° ΡΠ΅Ρ
Π½ΠΎΠ»ΠΎΠ³ΠΈΡ iMFLUX. ΠΠ°ΠΊΠ°Π·ΡΠΈΠΊ ΡΡΠΎΠ»ΠΊΠ½ΡΠ»ΡΡ Ρ Π²ΡΡΠΎΠΊΠΈΠΌΠΈ ΠΏΠΎΠΊΠ°Π·Π°ΡΠ΅Π»ΡΠΌΠΈ Π±ΡΠ°ΠΊΠ° ΠΈΠ·-Π·Π° Π½Π΅ΡΠ±Π°Π»Π°Π½ΡΠΈΡΠΎΠ²Π°Π½Π½ΠΎΠΉ ΡΠΎΡΠΌΡ Ρ 16 Π³Π½Π΅Π·Π΄Π°ΠΌΠΈ ΠΈ Π·Π°ΡΠ»ΠΎΠ½ΠΊΠ°ΠΌΠΈ Π³ΠΎΡΡΡΠ΅ΠΊΠ°Π½Π°Π»ΡΠ½ΡΡ
ΠΊΠ»Π°ΠΏΠ°Π½ΠΎΠ², ΡΡΠΎ ΠΏΡΠΈΠ²ΠΎΠ΄ΠΈΠ»ΠΎ ΠΊ ΠΏΡΠ΅ΡΡΠ²ΠΈΡΡΡΠΌ ΠΊΠΎΡΠΎΡΠΊΠΈΠΌ Π²ΡΡΡΡΠ΅Π»Π°ΠΌ. iMFLUX ΡΠ½ΠΈΠ·ΠΈΠ» ΠΏΡΠΎΡΠ΅Π½Ρ Π±ΡΠ°ΠΊΠ° Ρ Π±ΠΎΠ»Π΅Π΅ ΡΠ΅ΠΌ 10% Π΄ΠΎ ΠΌΠ΅Π½Π΅Π΅ ΡΠ΅ΠΌ 0,2% Π·Π° ΡΡΠ΅Ρ ΡΠ»ΡΡΡΠ΅Π½ΠΈΡ Π±Π°Π»Π°Π½ΡΠ° ΠΎΡ Π΄Π΅ΡΠ°Π»ΠΈ ΠΊ Π΄Π΅ΡΠ°Π»ΠΈ.ΠΡΠΎ ΡΠ²ΡΠ·Π°Π½ΠΎ Ρ Π½Π°ΠΏΠΎΠ»Π½Π΅Π½ΠΈΠ΅ΠΌ ΠΏΠΎΠ΄ ΠΏΠΎΡΡΠΎΡΠ½Π½ΡΠΌ Π΄Π°Π²Π»Π΅Π½ΠΈΠ΅ΠΌ. ΠΠ°ΠΆΠ΄Π°Ρ Π΄Π΅ΡΠ°Π»Ρ ΠΈΡΠΏΡΡΡΠ²Π°Π΅Ρ ΠΎΠ΄ΠΈΠ½Π°ΠΊΠΎΠ²ΠΎΠ΅ Π΄Π°Π²Π»Π΅Π½ΠΈΠ΅, ΠΈ Π³Π΅ΠΎΠΌΠ΅ΡΡΠΈΡ Π΄Π΅ΡΠ°Π»ΠΈ ΡΠΎΠΎΠ±ΡΠ°Π΅Ρ ΠΌΠ°ΡΠΈΠ½Π΅, ΠΊΠ°ΠΊ Π½Π΅ΠΏΡΠ΅ΡΡΠ²Π½ΠΎ ΠΏΡΠΎΡΠΈΠ»ΠΈΡΠΎΠ²Π°ΡΡ ΡΠΊΠΎΡΠΎΡΡΡ, ΡΡΠΎ ΠΏΡΠΈΠ²ΠΎΠ΄ΠΈΡ ΠΊ ΠΏΠΎΡΡΠΎΡΠ½Π½ΡΠΌ ΡΡΠ»ΠΎΠ²ΠΈΡΠΌ ΡΠΏΠ°ΠΊΠΎΠ²ΠΊΠΈ. ΠΠΎΠΌΠΈΠΌΠΎ ΠΈΡΠΊΠ»ΡΡΠ΅Π½ΠΈΡ ΠΊΠΎΡΠΎΡΠΊΠΈΡ
ΠΊΠ°Π΄ΡΠΎΠ² ΠΈ ΡΠ»ΡΡΡΠ΅Π½ΠΈΡ Π±Π°Π»Π°Π½ΡΠ° ΠΏΠΎΠ»ΠΎΡΡΠΈ Π½Π° 48%, Π²ΡΠ΅ΠΌΡ ΡΠΈΠΊΠ»Π° Π±ΡΠ»ΠΎ ΡΠΎΠΊΡΠ°ΡΠ΅Π½ΠΎ Π½Π° 30%. Π ΡΡΠΎΠΌ ΠΏΡΠΈΠΌΠ΅ΡΠ΅ ΡΡΡΠ΅ΡΡΠ²ΡΡΡΠ°Ρ ΠΏΠΎΠ»Π½ΠΎΡΡΡΡ ΡΠ»Π΅ΠΊΡΡΠΈΡΠ΅ΡΠΊΠ°Ρ ΠΈΠ½ΡΠ΅ΠΊΡΠΈΠΎΠ½Π½Π°Ρ ΠΌΠ°ΡΠΈΠ½Π° Π±ΡΠ»Π° ΠΌΠΎΠ΄Π΅ΡΠ½ΠΈΠ·ΠΈΡΠΎΠ²Π°Π½Π° Π΄Π»Ρ ΡΠ°Π±ΠΎΡΡ Ρ ΡΠΈΡΡΠ΅ΠΌΠΎΠΉ iMFLUX.
ΠΡΠΈΠΌΠ΅Ρ 2 : iMFLUX Π±ΡΠ» ΠΈΡΠΏΠΎΠ»ΡΠ·ΠΎΠ²Π°Π½ Π½Π° ΡΡΠ°ΠΏΠ΅ ΠΏΡΠΎΠ΅ΠΊΡΠΈΡΠΎΠ²Π°Π½ΠΈΡ Π½ΠΎΠ²ΡΡ
ΠΏΡΠ΅ΡΡ-ΡΠΎΡΠΌ ΠΈ ΠΏΡΠ΅ΡΡΠΎΠ² Π΄Π»Ρ Π±ΡΡΠΎΠ²ΠΎΠΉ ΡΠΈΡΡΡΡΠ΅ΠΉ ΠΌΠ°ΡΠΈΠ½Ρ ΠΈΠ· ΠΏΠΎΠ»ΠΈΠΏΡΠΎΠΏΠΈΠ»Π΅Π½Π°.ΠΠ½Π°Ρ ΠΎ ΠΏΡΠ΅ΠΈΠΌΡΡΠ΅ΡΡΠ²Π°Ρ
ΡΠ½ΠΈΠΆΠ΅Π½ΠΈΡ Π΄Π°Π²Π»Π΅Π½ΠΈΡ, ΠΏΡΠ΅ΡΡ-ΡΠΎΡΠΌΠ° Π±ΡΠ»Π° ΡΠΏΡΠΎΠ΅ΠΊΡΠΈΡΠΎΠ²Π°Π½Π° ΡΠ°ΠΊ, ΡΡΠΎΠ±Ρ ΠΌΠ°ΠΊΡΠΈΠΌΠ°Π»ΡΠ½ΠΎ ΠΈΡΠΏΠΎΠ»ΡΠ·ΠΎΠ²Π°ΡΡ Π²ΠΎΠ·ΠΌΠΎΠΆΠ½ΠΎΡΡΠΈ ΡΠ΅Ρ
Π½ΠΎΠ»ΠΎΠ³ΠΈΠΈ. ΠΠ΅ΡΠ°Π»Ρ ΡΠ°Π½Π΅Π΅ ΡΠ°Π±ΠΎΡΠ°Π»Π° Π½Π° ΡΠ΅ΡΠ²ΠΎΠ³ΠΈΠ΄ΡΠ°Π²Π»ΠΈΡΠ΅ΡΠΊΠΎΠΉ 500-ΡΠΎΠ½Π½ΠΎΠΉ ΠΌΠ°ΡΠΈΠ½Π΅ Ρ Π²ΠΎΡΠ΅ΠΌΡΡ ΠΏΠΎΠ»ΠΎΡΡΡΠΌΠΈ ΠΈ 52-ΡΠ΅ΠΊΡΠ½Π΄Π½ΡΠΌ ΡΠΈΠΊΠ»ΠΎΠΌ. ΠΠΎΠ²Π°Ρ ΡΠΎΡΠΌΠ° ΠΈ ΡΠΈΡΡΠ΅ΠΌΠ° iMFLUX ΠΏΠΎΠ·Π²ΠΎΠ»ΠΈΠ»ΠΈ ΠΈΡΠΏΠΎΠ»ΡΠ·ΠΎΠ²Π°ΡΡ ΠΎΠ±ΡΡΠ½ΡΡ Π³ΠΈΠ΄ΡΠ°Π²Π»ΠΈΡΠ΅ΡΠΊΡΡ 400-ΡΠΎΠ½Π½ΡΡ ΠΌΠ°ΡΠΈΠ½Ρ, ΡΠ°ΡΡΠΈΡΠΈΠ² ΠΊΠ°Π²ΠΈΡΠ°ΡΠΈΡ Π½Π° 50% Π΄ΠΎ 12 ΠΏΠΎΠ»ΠΎΡΡΠ΅ΠΉ ΠΈ ΡΠΎΠΊΡΠ°ΡΠΈΠ² ΡΠΈΠΊΠ» Π½Π° 21%. Π ΡΠΎΠ²ΠΎΠΊΡΠΏΠ½ΠΎΡΡΠΈ ΡΡΠΎ ΠΏΡΠΈΠ²Π΅Π»ΠΎ ΠΊ ΡΠ²Π΅Π»ΠΈΡΠ΅Π½ΠΈΡ ΠΏΡΠΎΠΏΡΡΠΊΠ½ΠΎΠΉ ΡΠΏΠΎΡΠΎΠ±Π½ΠΎΡΡΠΈ Π½Π° 91%. ΠΠ°ΠΆΠ΅ Ρ Π΄ΠΎΠ±Π°Π²Π»Π΅Π½ΠΈΠ΅ΠΌ ΡΠ΅ΡΡΡΠ΅Ρ
ΠΏΠΎΠ»ΠΎΡΡΠ΅ΠΉ ΠΈ ΡΠΎΠΊΡΠ°ΡΠ΅Π½ΠΈΠ΅ΠΌ Π²ΡΠ΅ΠΌΠ΅Π½ΠΈ ΡΠΈΠΊΠ»Π° ΠΎΠ±ΡΠ΅Π΅ ΠΏΠΈΠΊΠΎΠ²ΠΎΠ΅ Π΄Π°Π²Π»Π΅Π½ΠΈΠ΅ Π²ΠΏΡΡΡΠΊΠ° Π±ΡΠ»ΠΎ Π½Π° 30% Π½ΠΈΠΆΠ΅, ΡΠ΅ΠΌ ΠΏΡΠΈ ΠΎΠ±ΡΡΠ½ΠΎΠΌ ΠΏΡΠΎΡΠ΅ΡΡΠ΅.Π₯ΠΎΡΡ iMFLUX ΡΡΡΠ΅ΠΊΡΠΈΠ²Π΅Π½ Π½Π° ΠΌΠΎΠ΄Π΅ΡΠ½ΠΈΠ·ΠΈΡΠΎΠ²Π°Π½Π½ΡΡ
ΠΌΠ°ΡΠΈΠ½Π°Ρ
Ρ ΡΡΡΠ΅ΡΡΠ²ΡΡΡΠΈΠΌ ΠΈΠ½ΡΡΡΡΠΌΠ΅Π½ΡΠΎΠΌ, ΡΡΠΎΡ ΡΠ»ΡΡΠ°ΠΉ ΠΏΠΎΠΊΠ°Π·ΡΠ²Π°Π΅Ρ, ΡΡΠΎ ΡΠ°Π·ΡΠ°Π±ΠΎΡΠΊΠ° Π½ΠΎΠ²ΡΡ
ΡΠΎΡΠΌ ΡΠΏΠ΅ΡΠΈΠ°Π»ΡΠ½ΠΎ Π΄Π»Ρ ΠΏΡΠΎΡΠ΅ΡΡΠ° iMFLUX Π΄Π°Π΅Ρ ΡΡΡΠ΅ΡΡΠ²Π΅Π½Π½ΡΠ΅ ΠΏΡΠ΅ΠΈΠΌΡΡΠ΅ΡΡΠ²Π°.
ΠΡΠΈΠΌΠ΅Ρ 3 : ΠΠΎΠΌΠΏΠΎΠ½Π΅Π½Ρ ΡΠΏΠ°ΠΊΠΎΠ²ΠΊΠΈ ΠΈΠ· ΠΠΠ’ Π±ΡΠ» Π·Π°ΠΏΡΡΠ΅Π½ Π² ΡΠ΅ΡΡΡΠ΅Ρ Π³Π½Π΅Π·Π΄Π½ΠΎΠΉ ΠΏΡΠ΅ΡΡ-ΡΠΎΡΠΌΠ΅ Π½Π° Π³ΠΈΠ΄ΡΠ°Π²Π»ΠΈΡΠ΅ΡΠΊΠΎΠΌ ΠΏΡΠ΅ΡΡΠ΅, ΠΎΡΠ½Π°ΡΠ΅Π½Π½ΠΎΠΌ ΡΠ΅Ρ Π½ΠΎΠ»ΠΎΠ³ΠΈΠ΅ΠΉ iMFLUX. ΠΡΠΎΠΈΠ·Π²ΠΎΠ΄ΠΈΡΠ΅Π»ΡΠ½ΠΎΡΡΡ Π½ΠΎΠ²ΠΎΠ³ΠΎ ΠΏΡΠΎΡΠ΅ΡΡΠ° ΡΠ²Π΅Π»ΠΈΡΠΈΠ»Π°ΡΡ Π½Π° 16% ΠΏΠΎ ΡΡΠ°Π²Π½Π΅Π½ΠΈΡ Ρ ΠΎΠ±ΡΡΠ½ΡΠΌ ΠΏΡΠΎΡΠ΅ΡΡΠΎΠΌ. Π ΡΡΠ΅Π΄Π½Π΅ΠΌ ΠΌΠΎΠ΄Π΅ΡΠ½ΠΈΠ·ΠΈΡΠΎΠ²Π°Π½Π½ΡΠ΅ ΠΌΠ°ΡΠΈΠ½Ρ Ρ ΡΡΡΠ΅ΡΡΠ²ΡΡΡΠΈΠΌΠΈ ΠΏΡΠ΅ΡΡ-ΡΠΎΡΠΌΠ°ΠΌΠΈ ΠΏΠΎΠ·Π²ΠΎΠ»ΡΡΡ ΠΏΠΎΠ²ΡΡΠΈΡΡ ΠΏΡΠΎΠΈΠ·Π²ΠΎΠ΄ΠΈΡΠ΅Π»ΡΠ½ΠΎΡΡΡ Π½Π° 15-25%.ΠΠ΄Π½Π°ΠΊΠΎ ΠΏΡΠΎΡΠ΅ΡΡ iMFLUX ΡΠ°ΠΊΠΆΠ΅ ΡΠ½ΠΈΠ·ΠΈΠ» Π΄ΠΈΡΠ±Π°Π»Π°Π½Ρ ΠΏΠΎΠ»ΠΎΡΡΠΈ Ρ 6% Π΄ΠΎ 0,8%, ΠΏΠΎΡΡΠΈ Π²Π΄Π²ΠΎΠ΅ ΡΠΌΠ΅Π½ΡΡΠΈΠ» Π΄Π°Π²Π»Π΅Π½ΠΈΠ΅, Π½Π΅ΠΎΠ±Ρ ΠΎΠ΄ΠΈΠΌΠΎΠ΅ Π΄Π»Ρ Π·Π°ΠΏΠΎΠ»Π½Π΅Π½ΠΈΡ Π΄Π΅ΡΠ°Π»ΠΈ (Ρ 1079 Π±Π°Ρ Π΄ΠΎ 622 Π±Π°Ρ), ΠΈ ΡΠ½ΠΈΠ·ΠΈΠ» ΡΡΠ΅Π΄Π½ΠΈΠΉ Π²Π΅Ρ Π΄Π΅ΡΠ°Π»ΠΈ Π½Π° 0,48% ΠΏΡΠΈ ΡΠΎΡ ΡΠ°Π½Π΅Π½ΠΈΠΈ Π²ΡΠ΅Ρ Π³Π°Π±Π°ΡΠΈΡΠ½ΡΡ ΡΠ°Π·ΠΌΠ΅ΡΠΎΠ². ΡΠ΅Ρ Π½ΠΈΡΠ΅ΡΠΊΠΈΠ΅ Ρ Π°ΡΠ°ΠΊΡΠ΅ΡΠΈΡΡΠΈΠΊΠΈ. ΠΡΡΠ΅ΠΌ ΡΠΏΠ°ΠΊΠΎΠ²ΠΊΠΈ Π²ΠΎ Π²ΡΠ΅ΠΌΡ Π·Π°ΠΏΠΎΠ»Π½Π΅Π½ΠΈΡ Π΄Π΅ΡΠ°Π»ΠΈ ΠΌΠΎΠΆΠ½ΠΎ ΡΠ½ΠΈΠ·ΠΈΡΡ Π΄Π°Π²Π»Π΅Π½ΠΈΠ΅. ΠΡΠΎΠΌΠ΅ ΡΠΎΠ³ΠΎ, Π² ΡΠΎ Π²ΡΠ΅ΠΌΡ ΠΊΠ°ΠΊ ΠΏΡΠΈ ΠΎΠ±ΡΡΠ½ΠΎΠΌ ΠΏΡΠΎΡΠ΅ΡΡΠ΅ Π·Π°ΠΏΠΎΠ»Π½Π΅Π½ΠΈΠ΅ ΠΏΡΠΎΠΈΡΡ ΠΎΠ΄ΠΈΡ Ρ Π²ΡΡΠΎΠΊΠΎΠΉ ΡΠΊΠΎΡΠΎΡΡΡΡ, Π° Π·Π°ΡΠ΅ΠΌ Π΄Π΅ΡΠ°Π»Ρ ΡΠΏΠ°ΠΊΠΎΠ²ΡΠ²Π°Π΅ΡΡΡ, ΡΠΏΠΎΡΠΎΠ±Π½ΠΎΡΡΡ iMFLUX ΡΠΏΠ°ΠΊΠΎΠ²ΡΠ²Π°ΡΡ Π²ΠΎ Π²ΡΠ΅ΠΌΡ Π·Π°ΠΏΠΎΠ»Π½Π΅Π½ΠΈΡ ΠΈΡΠΊΠ»ΡΡΠ°Π΅Ρ Π½Π΅Π½ΡΠΆΠ½ΡΠΉ ΠΌΠ°ΡΠ΅ΡΠΈΠ°Π», ΡΠ½ΠΈΠΆΠ°Ρ Π²Π΅Ρ Π΄Π΅ΡΠ°Π»ΠΈ.ΠΡΠ΅ΠΌΡ ΡΠΈΠΊΠ»Π° ΡΠΎΠΊΡΠ°ΡΠΈΠ»ΠΎΡΡ Π½Π° 13%.
ΠΡΠΈΠΌΠ΅Ρ 4 : ΠΠ²ΡΠΎΠΌΠΎΠ±ΠΈΠ»ΡΠ½ΡΠΉ ΠΊΠΎΠΌΠΏΠΎΠ½Π΅Π½Ρ ΠΈΠ· ΠΏΠΎΠ»ΠΈΠΏΡΠΎΠΏΠΈΠ»Π΅Π½Π° Π±ΡΠ» ΡΠΏΡΡΠ΅Π½ Π² ΠΈΠ½ΡΡΡΡΠΌΠ΅Π½Ρ Ρ Π²ΠΎΡΠ΅ΠΌΡΡ Π³Π½Π΅Π·Π΄Π°ΠΌΠΈ Π½Π° 550-ΡΠΎΠ½Π½ΠΎΠΉ Π³ΠΈΠ΄ΡΠ°Π²Π»ΠΈΡΠ΅ΡΠΊΠΎΠΉ ΠΌΠ°ΡΠΈΠ½Π΅. Π Π°Π½Π΅Π΅ ΠΎΠ½ ΡΠ°Π±ΠΎΡΠ°Π» Ρ 50-ΡΠ΅ΠΊΡΠ½Π΄Π½ΡΠΌ ΡΠΈΠΊΠ»ΠΎΠΌ, Π½ΠΎ ΠΏΠΎΡΠ»Π΅ ΡΠΎΠ³ΠΎ, ΠΊΠ°ΠΊ ΠΏΡΠΎΡΠ΅ΡΡ iMFLUX Π±ΡΠ» ΠΈΠ½ΡΠ΅Π³ΡΠΈΡΠΎΠ²Π°Π½ Π² ΠΏΡΠ΅ΡΡ, Π²ΡΠ΅ΠΌΡ ΡΠΈΠΊΠ»Π° Π±ΡΠ»ΠΎ ΡΠΎΠΊΡΠ°ΡΠ΅Π½ΠΎ Π½Π° 8 ΡΠ΅ΠΊΡΠ½Π΄, ΡΡΠΎ ΠΏΡΠΈΠ²Π΅Π»ΠΎ ΠΊ ΡΠ²Π΅Π»ΠΈΡΠ΅Π½ΠΈΡ ΠΏΡΠΎΠΈΠ·Π²ΠΎΠ΄ΠΈΡΠ΅Π»ΡΠ½ΠΎΡΡΠΈ Π½Π° 20%. ΠΠ°ΠΊ ΠΎΠΏΠΈΡΠ°Π½ΠΎ Π² ΡΠ΅ΠΌΠ°ΡΠΈΡΠ΅ΡΠΊΠΎΠΌ ΠΈΡΡΠ»Π΅Π΄ΠΎΠ²Π°Π½ΠΈΠΈ β 3, ΠΎΠ΄Π½ΠΎΠ²ΡΠ΅ΠΌΠ΅Π½Π½Π°Ρ ΡΠΏΠ°ΠΊΠΎΠ²ΠΊΠ° ΠΈ Π½Π°ΠΏΠΎΠ»Π½Π΅Π½ΠΈΠ΅ ΠΏΡΠΈΠ²Π΅Π»ΠΈ ΠΊ ΡΠ½ΠΈΠΆΠ΅Π½ΠΈΡ Π΄Π°Π²Π»Π΅Π½ΠΈΡ Π½Π° 14% ΠΈ ΡΠΌΠ΅Π½ΡΡΠ΅Π½ΠΈΡ ΡΠ°ΡΡΠΈΡΠ½ΠΎΠ³ΠΎ Π²Π΅ΡΠ° Π½Π° 1%. ΠΠ΄ΠΎΠ±Π°Π²ΠΎΠΊ ΠΊ ΡΡΠΎΠΌΡ, ΡΠΏΠΎΡΠΎΠ±Π½ΠΎΡΡΡ iMFLUX Π΄ΠΈΠ½Π°ΠΌΠΈΡΠ΅ΡΠΊΠΈ ΠΏΠΎΠ³Π»ΠΎΡΠ°ΡΡ ΠΈΠ·ΠΌΠ΅Π½Π΅Π½ΠΈΡ Π²ΡΠ·ΠΊΠΎΡΡΠΈ ΡΠ½ΠΈΠ·ΠΈΠ»Π° ΠΏΡΠΎΡΠ΅Π½Ρ Π±ΡΠ°ΠΊΠ° Ρ 18% Π΄ΠΎ 0.2%.
ΠΡΠ΅ΠΈΠΌΡΡΠ΅ΡΡΠ²Π° ΠΏΡΠΎΡΠ΅ΡΡΠ° iMFLUX
ΠΠΠΠΠΠ ΠΠΠ‘Π’ΠΠ―ΠΠΠΠ ΠΠΠΠΠΠΠΠ
- Π£ΡΠΈΠ»ΠΈΠ΅ Π½ΠΈΠΆΠ½Π΅Π³ΠΎ Π·Π°ΠΆΠΈΠΌΠ°
- ΠΠ΅Π½ΡΡΠ΅ ΠΎΡΡΠ°ΡΠΎΡΠ½ΠΎΠ³ΠΎ Π½Π°ΠΏΡΡΠΆΠ΅Π½ΠΈΡ
- Π Π°Π²Π½ΠΎΠΌΠ΅ΡΠ½ΠΎΠ΅ Π½Π°ΠΏΡΡΠΆΠ΅Π½ΠΈΠ΅ (Π±Π΅Π· Π΄Π΅ΡΠΎΡΠΌΠ°ΡΠΈΠΈ)
- ΠΠΎΠ»Π΅Π΅ Π½ΠΈΠ·ΠΊΠΈΠ΅ ΡΠ΅ΠΌΠΏΠ΅ΡΠ°ΡΡΡΡ ΠΏΠ»Π°Π²Π»Π΅Π½ΠΈΡ
- ΠΠ΅Π½ΡΡΠ΅ ΡΡΠΌΡΠ½
- ΠΠ΅Π½ΡΡΠ΅ Π²ΡΠΏΡΡΠΊΠΈ
- ΠΠ΅Π½ΡΡΠ΅ Π²Π°ΡΠΈΠ°ΡΠΈΠΉ ΠΎΡ ΠΏΠΎΠ»ΠΎΡΡΠΈ ΠΊ ΠΏΠΎΠ»ΠΎΡΡΠΈ Π² ΠΌΠ½ΠΎΠ³ΠΎΠ³Π½Π΅Π·Π΄Π½ΡΡ ΠΈ ΡΠ΅ΠΌΠ΅ΠΉΠ½ΡΡ ΠΏΡΠ΅ΡΡ-ΡΠΎΡΠΌΠ°Ρ
- ΠΠ΅Π½ΡΡΠ΅ ΡΠ°Π·ΡΡΡΠ΅Π½ΠΈΡ ΠΌΠ°ΡΠ΅ΡΠΈΠ°Π»Π°
PACK-AS-IT-FILLS
- ΠΠΎΠ»Π΅Π΅ Π±ΡΡΡΡΡΠ΅ ΡΠΈΠΊΠ»Ρ
- ΠΠ΅Π½ΡΡΠ΅ ΡΠ°ΠΊΠΎΠ²ΠΈΠ½
- ΠΠΎΠ»Π΅Π΅ ΠΏΡΠΎΡΠ½ΡΠ΅ Π»ΠΈΠ½ΠΈΠΈ ΡΠ²Π°ΡΠΊΠΈ
- Π£Π»ΡΡΡΠ΅Π½Π½Π°Ρ ΠΎΠ±ΡΠ°Π±ΠΎΡΠΊΠ° ΠΏΠΎΠ²Π΅ΡΡ Π½ΠΎΡΡΠΈ
ΠΠΠ ΠΠΠΠΠΠΠΠΠ
- ΠΠΈΠ½ΠΈΠΈ ΡΠ΅Π΄ΡΡΠΈΡΠΎΠ²Π°Π½Π½ΠΎΠ³ΠΎ ΠΏΠΎΡΠΎΠΊΠ°
- Π’ΠΎΠ½ΠΊΠΎΡΡΠ΅Π½Π½Π°Ρ ΡΡΠ΅Π½ΠΊΠ° ΡΠ»ΡΡΡΠ΅Π½Π½Π°Ρ
- ΠΠΎΠ»Π΅Π΅ Π²ΡΡΠΎΠΊΠ°Ρ ΠΏΡΠΎΠΏΡΡΠΊΠ½Π°Ρ ΡΠΏΠΎΡΠΎΠ±Π½ΠΎΡΡΡ L / T
- ΠΠ°Π»ΡΠ΅ Ρ ΠΎΠ»ΠΎΠ΄ΠΈΠ»ΡΠ½ΡΠ΅ Π±Π΅Π³ΡΠ½Ρ
ΠΠΠΠΠ‘Π’Π¬-ΠΠΠΠΠΠΠΠ
- ΠΠΎΠ»Π΅Π΅ Π»Π΅Π³ΠΊΠΈΠ΅ Π΄Π΅ΡΠ°Π»ΠΈ (1-3%)
- Π£ΠΌΠ΅Π½ΡΡΠ΅Π½Π½Π°Ρ Π²ΡΠΏΡΡΠΊΠ°
- ΠΠ²ΡΠΎΠΌΠ°ΡΠΈΡΠ΅ΡΠΊΠ°Ρ ΡΠ΅Π³ΡΠ»ΠΈΡΠΎΠ²ΠΊΠ° Π²ΡΠ·ΠΊΠΎΡΡΠΈ
- Π Π΅Π³ΡΠ»ΠΈΡΠΎΠ²ΠΊΠ° Π·Π°Π±Π»ΠΎΠΊΠΈΡΠΎΠ²Π°Π½Π½ΡΡ ΠΏΠΎΠ»ΠΎΡΡΠ΅ΠΉ Π² ΡΠ΅Π°Π»ΡΠ½ΠΎΠΌ Π²ΡΠ΅ΠΌΠ΅Π½ΠΈ
- ΠΠΎΡΠ»Π΅Π΄ΠΎΠ²Π°ΡΠ΅Π»ΡΠ½ΡΠΉ ΠΏΡΠΈΠ²ΠΎΠ΄ Π·Π°ΡΠ»ΠΎΠ½ΠΎΠΊ
- ΠΠ΅ Π·Π°Π²ΠΈΡΠΈΡ ΠΎΡ Π²ΡΡΠ΅ΠΊΠ°ΡΡΠ΅Π³ΠΎ ΡΡΠΎΠΏΠΎΡΠ½ΠΎΠ³ΠΎ ΠΊΠΎΠ»ΡΡΠ°
- ΠΠ΅ Π²Π»ΠΈΡΠ΅Ρ ΠΈΠ·Π½ΠΎΡΠ΅Π½Π½ΡΠΉ ΡΡΠ²ΠΎΠ»
ΠΠ ΠΠΠ’ΠΠ Π : ΠΠΆΠΈΠ½ ΠΠ»ΡΡΠΎΠ½Π΅Π½ Π±ΡΠ» ΡΠ΅Ρ
Π½ΠΈΡΠ΅ΡΠΊΠΈΠΌ Π΄ΠΈΡΠ΅ΠΊΡΠΎΡΠΎΠΌ iMFLUX Π² ΠΠ°ΠΌΠΈΠ»ΡΡΠΎΠ½Π΅, ΡΡΠ°Ρ ΠΠ³Π°ΠΉΠΎ, Ρ 2015 Π³ΠΎΠ΄Π°. ΠΠ½ ΡΠ²Π»ΡΠ΅ΡΡΡ ΠΈΠ·ΠΎΠ±ΡΠ΅ΡΠ°ΡΠ΅Π»Π΅ΠΌ Π±Π°Π·ΠΎΠ²ΠΎΠΉ ΡΠ΅Ρ
Π½ΠΎΠ»ΠΎΠ³ΠΈΠΈ iMFLUX ΠΈ ΡΡΠΊΠΎΠ²ΠΎΠ΄ΠΈΡ Π½Π°ΡΡΠ½ΠΎ-ΠΈΡΡΠ»Π΅Π΄ΠΎΠ²Π°ΡΠ΅Π»ΡΡΠΊΠΎΠΉ ΠΎΡΠ³Π°Π½ΠΈΠ·Π°ΡΠΈΠ΅ΠΉ iMFLUX. ΠΠΆΠΈΠ½ ΠΏΠΎΡΡΠ°ΡΠΈΠ» Π²ΡΡ ΡΠ²ΠΎΡ 27-Π»Π΅ΡΠ½ΡΡ ΠΊΠ°ΡΡΠ΅ΡΡ Π² Procter & Gamble Π½Π° ΡΠ°Π·ΡΠ°Π±ΠΎΡΠΊΡ Π½ΠΎΠ²ΡΡ
ΡΠΏΠ°ΠΊΠΎΠ²ΠΎΡΠ½ΡΡ
ΡΠ΅ΡΠ΅Π½ΠΈΠΉ, Π²ΠΊΠ»ΡΡΠ°Ρ ΠΌΠ½ΠΎΠ³ΠΎΡΠΈΡΠ»Π΅Π½Π½ΡΠ΅ ΠΈΠ½Π½ΠΎΠ²Π°ΡΠΈΠΈ Π² ΡΠ΅Ρ
Π½ΠΎΠ»ΠΎΠ³ΠΈΡΡ
Π»ΠΈΡΡΡ ΠΏΠΎΠ΄ Π΄Π°Π²Π»Π΅Π½ΠΈΠ΅ΠΌ. ΠΠΎ Π·Π°ΠΏΡΡΠΊΠ° iMFLUX ΠΠΆΠΈΠ½ Π±ΡΠ» Π½Π°ΡΡΠ½ΡΠΌ ΡΠΎΡΡΡΠ΄Π½ΠΈΠΊΠΎΠΌ ΠΈ ΡΡΠΊΠΎΠ²ΠΎΠ΄ΠΈΠ» ΠΎΡΠ½ΠΎΠ²Π½ΡΠΌΠΈ ΡΠ°Π·ΡΠ°Π±ΠΎΡΠΊΠ°ΠΌΠΈ Π² ΠΎΠ±Π»Π°ΡΡΠΈ ΡΠ΅Ρ
Π½ΠΎΠ»ΠΎΠ³ΠΈΠΉ Π»ΠΈΡΡΡ ΠΏΠΎΠ΄ Π΄Π°Π²Π»Π΅Π½ΠΈΠ΅ΠΌ Π² ΠΊΠΎΠΌΠΏΠ°Π½ΠΈΠΈ P&G. Π£ Π½Π΅Π³ΠΎ Π±ΠΎΠ»Π΅Π΅ 50 ΠΏΠ°ΡΠ΅Π½ΡΠΎΠ² ΠΈ Π½Π΅ ΠΌΠ΅Π½Π΅Π΅ 35 Π·Π°ΡΠ²ΠΎΠΊ Π½Π° ΠΏΠ°ΡΠ΅Π½ΡΡ Π½Π° ΡΠ°ΡΡΠΌΠΎΡΡΠ΅Π½ΠΈΠΈ. ΠΠ»Ρ ΠΏΠΎΠ»ΡΡΠ΅Π½ΠΈΡ Π΄ΠΎΠΏΠΎΠ»Π½ΠΈΡΠ΅Π»ΡΠ½ΠΎΠΉ ΠΈΠ½ΡΠΎΡΠΌΠ°ΡΠΈΠΈ ΠΎΠ± iMFLUX ΠΎΠ±ΡΠ°ΡΠ°ΠΉΡΠ΅ΡΡ Π½Π° @ imflux.com; imflux.com.
6 ΡΠΈΠΏΠΎΠ² ΡΠ΅Ρ Π½ΠΎΠ»ΠΎΠ³ΠΈΠΉ Π»ΠΈΡΡΡ ΠΏΠΎΠ΄ Π΄Π°Π²Π»Π΅Π½ΠΈΠ΅ΠΌ
ΠΡ Π΄ΠΎΡΡΠΈΠΆΠ΅Π½ΠΈΠΉ, ΠΊΠΎΡΠΎΡΡΠ΅ ΠΏΠΎΠΌΠΎΠ³Π°Π»ΠΈ ΠΎΡΡΠ°ΡΠ»ΠΈ Π½Π° ΠΏΡΠΎΡΡΠΆΠ΅Π½ΠΈΠΈ Π±ΠΎΠ»Π΅Π΅ 40 Π»Π΅Ρ, Π΄ΠΎ ΠΏΠΎΡΠ»Π΅Π΄Π½ΠΈΡ ΠΏΠ΅ΡΠ΅Π΄ΠΎΠ²ΡΡ ΠΈΠ½Π½ΠΎΠ²Π°ΡΠΈΠΉ, ΡΡΡΠ΅ΡΡΠ²ΡΠ΅Ρ ΡΡΠ΄ ΠΈΠ½ΡΠ΅ΡΠ΅ΡΠ½ΡΡ ΡΠ΅Ρ Π½ΠΎΠ»ΠΎΠ³ΠΈΠΉ Π»ΠΈΡΡΡ ΠΏΠ»Π°ΡΡΠΌΠ°ΡΡ ΠΏΠΎΠ΄ Π΄Π°Π²Π»Π΅Π½ΠΈΠ΅ΠΌ, ΠΊΠΎΡΠΎΡΡΠ΅ ΠΌΠΎΠΆΠ½ΠΎ ΠΈΡΠΏΠΎΠ»ΡΠ·ΠΎΠ²Π°ΡΡ Π΄Π»Ρ Π·Π°ΠΏΡΡΠΊΠ° Π²Π°ΡΠ΅Π³ΠΎ ΠΏΡΠΎΡΠΎΡΠΈΠΏΠ° Π² ΠΏΡΠΎΠΈΠ·Π²ΠΎΠ΄ΡΡΠ²ΠΎ.
ΠΠΈΠΆΠ΅ ΠΏΡΠΈΠ²Π΅Π΄Π΅Π½Ρ ΡΠ΅ΡΡΡ ΡΠ΅Ρ
Π½ΠΎΠ»ΠΎΠ³ΠΈΠΉ, ΠΊΠΎΡΠΎΡΡΠ΅ ΠΏΠΎΠΌΠΎΠ³Π°ΡΡ ΡΠ΅Π³ΠΎΠ΄Π½ΡΡΠ½ΠΈΠΌ ΠΊΠΎΠΌΠΏΠ°Π½ΠΈΡΠΌ, Π·Π°Π½ΠΈΠΌΠ°ΡΡΠΈΠΌΡΡ Π»ΠΈΡΡΠ΅ΠΌ ΠΏΠΎΠ΄ Π΄Π°Π²Π»Π΅Π½ΠΈΠ΅ΠΌ, ΠΏΡΠΎΠΈΠ·Π²ΠΎΠ΄ΠΈΡΡ Π΄Π΅ΡΠ°Π»ΠΈ Π±ΡΡΡΡΠ΅Π΅ ΠΈ Ρ Π±ΠΎΠ»Π΅Π΅ Π²ΡΡΠΎΠΊΠΈΠΌ ΠΊΠ°ΡΠ΅ΡΡΠ²ΠΎΠΌ. Π§Π΅ΠΌ Π±ΠΎΠ»ΡΡΠ΅ Π²Ρ Π·Π½Π°Π΅ΡΠ΅, ΡΠ΅ΠΌ Π»ΡΡΡΠ΅ Π±ΡΠ΄Π΅ΡΠ΅ Π³ΠΎΡΠΎΠ²Ρ Π·Π°ΠΏΡΠΎΡΠΈΡΡ ΡΠ°ΠΊΡΡ ββΡΠ΅Ρ
Π½ΠΎΠ»ΠΎΠ³ΠΈΡ, ΠΊΠΎΠ³Π΄Π° ΠΏΡΠΈΠ΄Π΅Ρ Π²ΡΠ΅ΠΌΡ Π²ΡΠ±ΠΈΡΠ°ΡΡ ΠΏΠ°ΡΡΠ½Π΅ΡΠ° Π΄Π»Ρ Π»ΠΈΡΡΡ ΠΏΠΎΠ΄ Π΄Π°Π²Π»Π΅Π½ΠΈΠ΅ΠΌ!
6 ΡΠΈΠΏΠΎΠ² ΡΠ΅Ρ Π½ΠΎΠ»ΠΎΠ³ΠΈΠΉ Π»ΠΈΡΡΡ ΠΏΠΎΠ΄ Π΄Π°Π²Π»Π΅Π½ΠΈΠ΅ΠΌ
1. Π’ΠΎΠ½ΠΊΠΎΡΡΠ΅Π½Π½ΡΠΉ ΠΏΡΠΎΡΠΈΠ»Ρ
ΠΠΈΡΡΠ΅ Ρ ΡΠΎΠ½ΠΊΠΈΠΌΠΈ ΡΡΠ΅Π½ΠΊΠ°ΠΌΠΈ — ΡΡΠΎ ΡΠ΅Ρ Π½ΠΎΠ»ΠΎΠ³ΠΈΡ Π»ΠΈΡΡΡ ΠΏΠΎΠ΄ Π΄Π°Π²Π»Π΅Π½ΠΈΠ΅ΠΌ, ΠΏΠΎΠ·Π²ΠΎΠ»ΡΡΡΠ°Ρ ΠΏΠΎΠ»ΡΡΠΈΡΡ ΠΏΠ»Π°ΡΡΠΌΠ°ΡΡΠΎΠ²ΡΡ Π΄Π΅ΡΠ°Π»Ρ Ρ ΠΎΡΠ΅Π½Ρ ΡΠΎΠ½ΠΊΠΈΠΌΠΈ ΡΡΠ΅Π½ΠΊΠ°ΠΌΠΈ. ΠΠ½ ΡΠ°ΡΡΠΎ ΠΈΡΠΏΠΎΠ»ΡΠ·ΡΠ΅ΡΡΡ Π² ΡΠ΅ΡΡΠΎΠ²ΡΡ ΠΏΡΠΈΠ±ΠΎΡΠ°Ρ , ΡΠ»Π΅ΠΊΡΡΠΎΠ½ΠΈΠΊΠ΅, ΡΠΎΡΡΠ΄Π°Ρ , ΡΡΡΠ±ΠΊΠ°Ρ ΠΈ Π΄ΡΡΠ³ΠΈΡ ΠΊΠΎΡΠΏΡΡΠ°Ρ . ΠΠΈΡΠ°, Π·Π°Π½ΠΈΠΌΠ°ΡΡΠΈΠ΅ΡΡ Π»ΠΈΡΡΠ΅ΠΌ ΠΏΠ»Π°ΡΡΠΌΠ°ΡΡ ΠΏΠΎΠ΄ Π΄Π°Π²Π»Π΅Π½ΠΈΠ΅ΠΌ, ΠΊΠΎΡΠΎΡΡΠ΅ Π·Π°Π½ΠΈΠΌΠ°ΡΡΡΡ ΡΠΎΡΠΌΠΎΠ²Π°Π½ΠΈΠ΅ΠΌ ΡΠΎΠ½ΠΊΠΈΡ ΡΡΠ΅Π½ΠΎΠΊ, Π΄ΠΎΠ»ΠΆΠ½Ρ ΡΡΠ°ΡΠ΅Π»ΡΠ½ΠΎ ΠΏΡΠΎΠ΄ΡΠΌΡΠ²Π°ΡΡ Π²ΡΠ΅ Π°ΡΠΏΠ΅ΠΊΡΡ ΠΊΠΎΠ½ΡΡΡΡΠΊΡΠΈΠΈ Π΄Π΅ΡΠ°Π»ΠΈ, ΠΊΠΎΠ½ΡΡΡΡΠΊΡΠΈΠΈ ΠΏΡΠ΅ΡΡ-ΡΠΎΡΠΌΡ ΠΈ ΠΎΠ±ΡΠ°Π±ΠΎΡΠΊΠΈ, ΡΡΠΎΠ±Ρ Π³Π°ΡΠ°Π½ΡΠΈΡΠΎΠ²Π°ΡΡ, ΡΡΠΎ Π³Π΅ΠΎΠΌΠ΅ΡΡΠΈΡ ΡΠΎΠ½ΠΊΠΈΡ ΡΡΠ΅Π½ΠΎΠΊ ΡΠΎΡ ΡΠ°Π½ΠΈΡΡΡ Π±Π΅Π· ΠΏΡΠΎΠ±Π»Π΅ΠΌ Ρ ΠΊΠ°ΡΠ΅ΡΡΠ²ΠΎΠΌ.ΠΠ΄Π΅ΡΡ, Π² Micron, ΠΌΡ ΠΈΡΠΏΠΎΠ»ΡΠ·ΡΠ΅ΠΌ ΡΠ»ΠΎΠΆΠ½ΡΡ ΡΠΈΡΡΠ΅ΠΌΡ ΡΠ΅Ρ Π½ΠΈΡΠ΅ΡΠΊΠΎΠ³ΠΎ Π·ΡΠ΅Π½ΠΈΡ Π΄Π»Ρ ΠΏΡΠΎΠ²Π΅ΡΠΊΠΈ ΠΊΠ°ΠΆΠ΄ΠΎΠΉ Π³ΠΎΡΠΎΠ²ΠΎΠΉ Π΄Π΅ΡΠ°Π»ΠΈ, ΡΡΠΎΠ±Ρ ΡΠ±Π΅Π΄ΠΈΡΡΡΡ, ΡΡΠΎ Π½Π° Π½Π΅ΠΉ Π½Π΅Ρ ΡΡΠ΅ΡΠΈΠ½.
2. ΠΠ°Π·ΠΎΠ²ΠΎΠ΅ Π»ΠΈΡΡΠ΅ ΠΏΠΎΠ΄ Π΄Π°Π²Π»Π΅Π½ΠΈΠ΅ΠΌ
ΠΡΠΎΠ±Π»Π΅ΠΌΠ° Ρ Π»ΡΠ±ΠΎΠΉ ΡΠΎΠ»ΡΡΠΎΠΉ ΠΏΠ»Π°ΡΡΠΈΠΊΠΎΠ²ΠΎΠΉ Π΄Π΅ΡΠ°Π»ΡΡ, ΠΏΠΎΠ»ΡΡΠ΅Π½Π½ΠΎΠΉ Π»ΠΈΡΡΠ΅ΠΌ ΠΏΠΎΠ΄ Π΄Π°Π²Π»Π΅Π½ΠΈΠ΅ΠΌ, Π·Π°ΠΊΠ»ΡΡΠ°Π΅ΡΡΡ Π² ΡΠΎΠΌ, ΡΡΠΎ ΠΎΠ½Π° ΠΏΠΎΠ΄Π²Π΅ΡΠΆΠ΅Π½Π° ΡΠΈΡΠΊΡ Π΄Π΅ΡΠΎΡΠΌΠ°ΡΠΈΠΈ ΠΏΡΠΈ ΠΎΡ
Π»Π°ΠΆΠ΄Π΅Π½ΠΈΠΈ. ΠΠΈΡΡΠ΅ ΠΏΠΎΠ΄ Π΄Π°Π²Π»Π΅Π½ΠΈΠ΅ΠΌ Ρ ΠΏΠΎΠΌΠΎΡΡΡ Π³Π°Π·Π° ΠΏΠΎΠΌΠΎΠ³Π°Π΅Ρ ΡΠ΅ΡΠΈΡΡ ΡΡΡ ΠΏΡΠΎΠ±Π»Π΅ΠΌΡ Π·Π° ΡΡΠ΅Ρ ΠΏΠΎΠ΄Π°ΡΠΈ Π³Π°Π·Π° Π² ΡΠΎΡΠΌΡ Π΄Π»Ρ Π»ΠΈΡΡΡ ΠΏΠΎΠ΄ Π΄Π°Π²Π»Π΅Π½ΠΈΠ΅ΠΌ, Π·Π°ΠΏΠΎΠ»Π½Π΅Π½Π½ΡΡ ΠΏΠ»Π°ΡΡΠΈΠΊΠΎΠ²ΡΠΌ ΠΌΠ°ΡΠ΅ΡΠΈΠ°Π»ΠΎΠΌ. ΠΡΠΎ ΠΏΠΎΠ·Π²ΠΎΠ»ΡΠ΅Ρ ΠΏΠ»Π°ΡΡΠΈΠΊΡ Π½Π° Π²Π½Π΅ΡΠ½Π΅ΠΉ ΡΡΠΎΡΠΎΠ½Π΅ ΡΠΎΡΠΌΡ ΡΠΎΡ
ΡΠ°Π½ΡΡΡ Π³Π»Π°Π΄ΠΊΠΈΠΉ ΠΈ Π·Π°ΠΊΠΎΠ½ΡΠ΅Π½Π½ΡΠΉ Π²ΠΈΠ΄, Π² ΡΠΎ Π²ΡΠ΅ΠΌΡ ΠΊΠ°ΠΊ Π²Π½ΡΡΡΠ΅Π½Π½ΡΡ ΡΠ°ΡΡΡ ΠΎΡΡΠ°Π΅ΡΡΡ ΠΏΠΎΡΠΈΡΡΠΎΠΉ ΠΈΠ»ΠΈ ΠΏΠΎΠ»ΠΎΠΉ.ΠΡΠΎ Π½Π΅ ΡΠΎΠ»ΡΠΊΠΎ ΠΏΡΠ΅Π΄ΠΎΡ
ΡΠ°Π½ΡΠ΅Ρ Π΄Π΅ΡΠ°Π»Ρ ΠΎΡ Π΄Π΅ΡΠΎΡΠΌΠ°ΡΠΈΠΈ Π²ΠΎ Π²ΡΠ΅ΠΌΡ ΡΡΠ°Π΄ΠΈΠΈ ΠΎΡ
Π»Π°ΠΆΠ΄Π΅Π½ΠΈΡ, Π½ΠΎ ΠΈ ΡΠ½ΠΈΠΆΠ°Π΅Ρ ΡΡΠΎΠΈΠΌΠΎΡΡΡ Π΄Π΅ΡΠ°Π»ΠΈ (ΠΏΠΎΡΠΊΠΎΠ»ΡΠΊΡ Π²Ρ ΠΈΡΠΏΠΎΠ»ΡΠ·ΡΠ΅ΡΠ΅ ΠΌΠ΅Π½ΡΡΠ΅ ΠΌΠ°ΡΠ΅ΡΠΈΠ°Π»Π°).
3. ΠΠΈΡΡΠ΅ ΠΌΠ΅ΡΠ°Π»Π»Π° ΠΏΠΎΠ΄ Π΄Π°Π²Π»Π΅Π½ΠΈΠ΅ΠΌ
ΠΠ»Π°ΡΡΠΌΠ°ΡΡΠ° — ΡΡΠΎ Π½Π΅ Π΅Π΄ΠΈΠ½ΡΡΠ²Π΅Π½Π½ΠΎΠ΅, ΡΡΠΎ ΠΌΠΎΠΆΠ½ΠΎ Π»ΠΈΡΡ ΠΏΠΎΠ΄ Π΄Π°Π²Π»Π΅Π½ΠΈΠ΅ΠΌ, ΠΌΠΎΠΆΠ½ΠΎ ΠΈ ΠΌΠ΅ΡΠ°Π»Π». ΠΡΠ° Π½ΠΎΠ²Π°Ρ ΡΠ΅Ρ Π½ΠΎΠ»ΠΎΠ³ΠΈΡ Π·Π½Π°ΡΠΈΡΠ΅Π»ΡΠ½ΠΎ Π΄ΠΎΡΠΎΠΆΠ΅, ΡΠ΅ΠΌ Π»ΠΈΡΡΠ΅ ΠΏΠ»Π°ΡΡΠΌΠ°ΡΡ ΠΏΠΎΠ΄ Π΄Π°Π²Π»Π΅Π½ΠΈΠ΅ΠΌ, ΠΈ ΠΎΠ±ΡΡΠ½ΠΎ ΠΈΡΠΏΠΎΠ»ΡΠ·ΡΠ΅ΡΡΡ Π½Π° Π½ΠΈΡΠ΅Π²ΠΎΠΌ ΡΡΠ½ΠΊΠ΅. ΠΠ°ΠΏΡΠΈΠΌΠ΅Ρ, ΡΡΠ½ΠΎΠΊ ΡΠΎΡΠΎΠ²ΡΡ ΡΠ΅Π»Π΅ΡΠΎΠ½ΠΎΠ² ΠΈΠ½ΠΎΠ³Π΄Π° ΠΈΡΠΏΠΎΠ»ΡΠ·ΡΠ΅Ρ Π»ΠΈΡΡΠ΅ ΠΌΠ΅ΡΠ°Π»Π»Π° ΠΏΠΎΠ΄ Π΄Π°Π²Π»Π΅Π½ΠΈΠ΅ΠΌ Π΄Π»Ρ Π·Π°ΡΠΈΡΡ ΡΠΎΡΠΎΠ²ΠΎΠΉ ΡΠ»Π΅ΠΊΡΡΠΎΠ½ΠΈΠΊΠΈ ΠΎΡ ΡΠ°Π΄ΠΈΠΎ ΠΈΠ»ΠΈ ΠΌΠΈΠΊΡΠΎΠ²ΠΎΠ»Π½.
4. ΠΠΈΡΡΠ΅ ΠΆΠΈΠ΄ΠΊΠΎΠ³ΠΎ ΡΠΈΠ»ΠΈΠΊΠΎΠ½Π° ΠΏΠΎΠ΄ Π΄Π°Π²Π»Π΅Π½ΠΈΠ΅ΠΌ
ΠΠΎΠ»ΡΡΠ°Ρ ΡΠ°ΡΡΡ ΠΏΠ»Π°ΡΡΠΌΠ°ΡΡ Π΄Π»Ρ Π»ΠΈΡΡΡ ΠΏΠΎΠ΄ Π΄Π°Π²Π»Π΅Π½ΠΈΠ΅ΠΌ — ΡΡΠΎ ΡΠ΅ΡΠΌΠΎΡΠ΅Π°ΠΊΡΠΈΠ²Π½ΡΠΉ ΠΌΠ°ΡΠ΅ΡΠΈΠ°Π» , ΡΡΠΎ ΠΎΠ·Π½Π°ΡΠ°Π΅Ρ, ΡΡΠΎ Ρ
ΠΎΠ»ΠΎΠ΄Π½ΡΠΉ ΠΌΠ°ΡΠ΅ΡΠΈΠ°Π» Π²ΠΏΡΡΡΠΊΠΈΠ²Π°Π΅ΡΡΡ Π² ΡΡΠ΅Π·Π²ΡΡΠ°ΠΉΠ½ΠΎ Π³ΠΎΡΡΡΡΡ ΡΠΎΡΠΌΡ Π΄Π»Ρ ΡΠΎΠ·Π΄Π°Π½ΠΈΡ Π΄Π΅ΡΠ°Π»ΠΈ. ΠΡΠΎΡ ΠΏΡΠΎΡΠ΅ΡΡ ΠΎΡΠ²Π΅ΡΠΆΠ΄Π°Π΅Ρ Π΄Π΅ΡΠ°Π»Ρ, ΡΡΠΎΠ±Ρ Π΅Π΅ Π±ΠΎΠ»ΡΡΠ΅ Π½Π΅Π»ΡΠ·Ρ Π±ΡΠ»ΠΎ ΡΠ°ΡΠΏΠ»Π°Π²ΠΈΡΡ. ΠΠΎ Π΅ΡΠ»ΠΈ Π²Π°ΠΌ Π½ΡΠΆΠ½Π° Π΄Π΅ΡΠ°Π»Ρ, ΡΠΏΠΎΡΠΎΠ±Π½Π°Ρ Π²ΡΠ΄Π΅ΡΠΆΠΈΠ²Π°ΡΡ ΠΎΡΠ΅Π½Ρ Π²ΡΡΠΎΠΊΠΈΠ΅ ΡΠ΅ΠΌΠΏΠ΅ΡΠ°ΡΡΡΡ ΠΈΠ»ΠΈ Ρ
ΠΈΠΌΠΈΡΠ΅ΡΠΊΠΈΠ΅ Π²ΠΎΠ·Π΄Π΅ΠΉΡΡΠ²ΠΈΡ — ΠΊΠ°ΠΊ, Π½Π°ΠΏΡΠΈΠΌΠ΅Ρ, Π½Π΅ΠΊΠΎΡΠΎΡΡΠ΅ ΠΌΠ΅Π΄ΠΈΡΠΈΠ½ΡΠΊΠΈΠ΅ ΡΡΡΡΠΎΠΉΡΡΠ²Π° ΠΈΠ»ΠΈ Π°Π²ΡΠΎΠΌΠΎΠ±ΠΈΠ»ΡΠ½ΡΠ΅ Π΄Π΅ΡΠ°Π»ΠΈ — Π²Π°ΠΌ ΠΌΠΎΠΆΠ΅Ρ ΠΏΠΎΡΡΠ΅Π±ΠΎΠ²Π°ΡΡΡΡ Π»ΠΈΡΡΠ΅ ΠΏΠΎΠ΄ Π΄Π°Π²Π»Π΅Π½ΠΈΠ΅ΠΌ ΠΈΠ· ΡΠ΅ΡΠΌΠΎΠΏΠ»Π°ΡΡΠ° , Π² ΠΊΠΎΡΠΎΡΠΎΠΌ ΡΠ°ΡΡΠΎ ΠΈΡΠΏΠΎΠ»ΡΠ·ΡΠ΅ΡΡΡ ΠΆΠΈΠ΄ΠΊΠΈΠΉ ΡΠΈΠ»ΠΈΠΊΠΎΠ½.
5. 3D-ΠΏΠ΅ΡΠ°ΡΡ
3D-ΠΏΠ΅ΡΠ°ΡΡ — ΠΈΠ·Π²Π΅ΡΡΠ½Π°Ρ ΡΠ΅Ρ
Π½ΠΎΠ»ΠΎΠ³ΠΈΡ Π»ΠΈΡΡΡ ΠΏΠΎΠ΄ Π΄Π°Π²Π»Π΅Π½ΠΈΠ΅ΠΌ ΠΈΠ·-Π·Π° ΡΠΎΠΉ ΡΠΎΠ»ΠΈ, ΠΊΠΎΡΠΎΡΡΡ ΠΎΠ½Π° ΠΈΠ³ΡΠ°Π΅Ρ Π² ΡΠΎΠ·Π΄Π°Π½ΠΈΠΈ ΠΏΡΠΎΡΠΎΡΠΈΠΏΠΎΠ² Π΄Π΅ΡΠ°Π»Π΅ΠΉ, ΠΏΠΎΠ»ΡΡΠ΅Π½Π½ΡΡ
Π»ΠΈΡΡΠ΅ΠΌ ΠΏΠΎΠ΄ Π΄Π°Π²Π»Π΅Π½ΠΈΠ΅ΠΌ. ΠΠ΄Π΅ΡΡ, Π² Micron, ΠΌΡ ΡΠΎΠ·Π΄Π°Π΅ΠΌ 3D-ΠΏΠ΅ΡΠ°ΡΠ½ΡΠΉ ΠΏΡΠΎΡΠΎΡΠΈΠΏ Π΄Π΅ΡΠ°Π»ΠΈ ΠΊΠ»ΠΈΠ΅Π½ΡΠ°, ΠΏΡΠ΅ΠΆΠ΄Π΅ ΡΠ΅ΠΌ ΠΏΡΠΈΡΡΡΠΏΠΈΡΡ ΠΊ ΠΏΡΠΎΠΈΠ·Π²ΠΎΠ΄ΡΡΠ²Ρ. ΠΡΠΎ ΠΏΠΎΠ·Π²ΠΎΠ»ΡΠ΅Ρ Π½Π°ΠΌ ΠΎΠ±ΡΡΠΆΠ΄Π°ΡΡ ΠΏΠΎΡΠ΅Π½ΡΠΈΠ°Π»ΡΠ½ΡΠ΅ ΡΠ»ΡΡΡΠ΅Π½ΠΈΡ Π±ΠΎΠ»Π΅Π΅ ΠΏΠΎΠ΄ΡΠΎΠ±Π½ΠΎ, ΡΠ΅ΠΌ, Π½Π°ΠΏΡΠΈΠΌΠ΅Ρ, ΠΏΡΠΈ ΠΏΡΠΎΡΠΌΠΎΡΡΠ΅ ΠΎΠ½Π»Π°ΠΉΠ½-ΡΠ΅Π½Π΄Π΅ΡΠΈΠ½Π³Π°. Π’Π°ΠΊΠΆΠ΅ ΡΡΠΎΠΈΡ ΠΎΡΠΌΠ΅ΡΠΈΡΡ, ΡΡΠΎ 3D-ΠΏΠ΅ΡΠ°ΡΡ ΠΌΠΎΠΆΠ΅Ρ ΠΈΡΠΏΠΎΠ»ΡΠ·ΠΎΠ²Π°ΡΡΡΡ Π΄Π»Ρ ΠΏΠ΅ΡΠ°ΡΠΈ ΡΠ΅Π°Π»ΡΠ½ΡΡ
ΡΠΎΡΠΌ Π΄Π»Ρ Π»ΠΈΡΡΡ ΠΏΠΎΠ΄ Π΄Π°Π²Π»Π΅Π½ΠΈΠ΅ΠΌ ΠΈΠ· ΠΏΠ»Π°ΡΡΠΈΠΊΠ° ΠΈΠ»ΠΈ ΠΌΠ΅ΡΠ°Π»Π»Π°.Π Π½Π°ΡΡΠΎΡΡΠ΅Π΅ Π²ΡΠ΅ΠΌΡ Π΄ΠΎΡΡΡΠΏΠ½Π°Ρ ΡΠ΅Ρ
Π½ΠΎΠ»ΠΎΠ³ΠΈΡ 3D-ΠΏΠ΅ΡΠ°ΡΠΈ Π½Π΅ ΠΏΠΎΠ·Π²ΠΎΠ»ΡΠ΅Ρ Π½Π°ΠΌ ΠΏΠ΅ΡΠ°ΡΠ°ΡΡ Π΄Π΅ΡΠ°Π»ΠΈ Ρ ΡΠ·ΠΊΠΈΠΌΠΈ Π΄ΠΎΠΏΡΡΠΊΠ°ΠΌΠΈ, Π½Π΅ΠΎΠ±Ρ
ΠΎΠ΄ΠΈΠΌΡΠΌΠΈ Π΄Π»Ρ Π»ΠΈΡΡΠ΅Π²ΡΡ
ΡΠΎΡΠΌ, Π½ΠΎ ΠΌΡ ΠΏΡΠ΅Π΄ΠΏΠΎΠ»Π°Π³Π°Π΅ΠΌ, ΡΡΠΎ ΡΡΠΎ Π²ΠΎΠ·ΠΌΠΎΠΆΠ½ΠΎ Π² Π±ΡΠ΄ΡΡΠ΅ΠΌ.
6. Π£Π½ΠΈΠΊΠ°Π»ΡΠ½ΡΠ΅ ΡΠΎΡΡΠ°Π²Ρ ΠΌΠ°ΡΠ΅ΡΠΈΠ°Π»ΠΎΠ²
Π₯ΠΎΡΡ ΡΡΠΎ Π½Π΅ Β«ΡΠ΅Ρ Π½ΠΎΠ»ΠΎΠ³ΠΈΡΒ» Π²ΠΏΡΡΡΠΊΠ° ΠΏΠ»Π°ΡΡΠΈΠΊΠ° Π² ΡΡΠ°Π΄ΠΈΡΠΈΠΎΠ½Π½ΠΎΠΌ ΠΏΠΎΠ½ΠΈΠΌΠ°Π½ΠΈΠΈ, ΠΈΡΠΏΠΎΠ»ΡΠ·ΠΎΠ²Π°Π½ΠΈΠ΅ ΡΠ½ΠΈΠΊΠ°Π»ΡΠ½ΡΡ ΡΠΎΡΡΠ°Π²ΠΎΠ² ΠΌΠ°ΡΠ΅ΡΠΈΠ°Π»ΠΎΠ² Π΄Π΅ΠΉΡΡΠ²ΠΈΡΠ΅Π»ΡΠ½ΠΎ ΡΠ°ΡΡΠΈΡΡΠ΅Ρ Π²ΠΎΠ·ΠΌΠΎΠΆΠ½ΠΎΡΡΠΈ ΡΠΎΡΠΌΠΎΠ²Π°Π½ΠΈΡ. ΠΠΎΠΌΠΏΠ°Π½ΠΈΠΈ, Π·Π°Π½ΠΈΠΌΠ°ΡΡΠΈΠ΅ΡΡ Π»ΠΈΡΡΠ΅ΠΌ ΠΏΠΎΠ΄ Π΄Π°Π²Π»Π΅Π½ΠΈΠ΅ΠΌ, ΠΌΠΎΠ³ΡΡ, Π½Π°ΠΏΡΠΈΠΌΠ΅Ρ, ΠΈΡΠΏΠΎΠ»ΡΠ·ΠΎΠ²Π°ΡΡ ΡΠ³Π»Π΅ΡΠΎΠ΄Π½ΡΠΉ ΠΈΠ»ΠΈ ΠΌΠΈΠ½Π΅ΡΠ°Π»ΡΠ½ΡΠΉ Π½Π°ΠΏΠΎΠ»Π½ΠΈΡΠ΅Π»Ρ, ΠΏΠ΅Π½ΠΎΠΎΠ±ΡΠ°Π·ΠΎΠ²Π°ΡΠ΅Π»Ρ ΠΈ ΡΠΌΠ°Π·ΠΎΡΠ½ΡΡ Π΄ΠΎΠ±Π°Π²ΠΊΡ Π΄Π»Ρ ΠΏΡΠΈΠ΄Π°Π½ΠΈΡ Π΄Π΅ΡΠ°Π»ΡΠΌ ΠΎΠΏΡΠ΅Π΄Π΅Π»Π΅Π½Π½ΡΡ ΡΠ²ΠΎΠΉΡΡΠ².ΠΠ°ΠΏΡΠΈΠΌΠ΅Ρ, Π·Π΄Π΅ΡΡ, Π² Micron, ΠΌΡ ΠΈΡΠΏΠΎΠ»ΡΠ·ΠΎΠ²Π°Π»ΠΈ ΠΠΠ‘-ΠΏΠ»Π°ΡΡΠΈΠΊ Ρ 40% -Π½ΡΠΌ ΡΠ³Π»Π΅ΡΠΎΠ΄Π½ΡΠΌ Π½Π°ΠΏΠΎΠ»Π½Π΅Π½ΠΈΠ΅ΠΌ (Π°ΠΊΡΠΈΠ»ΠΎΠ½ΠΈΡΡΠΈΠ»-Π±ΡΡΠ°Π΄ΠΈΠ΅Π½-ΡΡΠΈΡΠΎΠ») Π΄Π»Ρ Π΄ΠΎΡΡΠΈΠΆΠ΅Π½ΠΈΡ ΠΎΠΏΡΠ΅Π΄Π΅Π»Π΅Π½Π½ΠΎΠΉ ΡΡΠ΅ΠΏΠ΅Π½ΠΈ ΡΠ»Π΅ΠΊΡΡΠΎΠΏΡΠΎΠ²ΠΎΠ΄Π½ΠΎΡΡΠΈ Π² ΠΏΠ»Π°ΡΡΠΌΠ°ΡΡΠΎΠ²ΠΎΠΌ ΡΡΠ΅ΡΠΆΠ½Π΅ ΠΈΠ»ΠΈ Π΄Π°ΡΡΠΈΠΊΠ΅. Π’Π΅ΠΌΠΏΠ΅ΡΠ°ΡΡΡΠ° ΡΠΎΡΠΌΡ ΠΈ ΠΏΠ»Π°ΡΡΠΈΠΊΠ° Π²Π°ΠΆΠ½Ρ ΠΏΡΠΈ Π΄ΠΎΠ±Π°Π²Π»Π΅Π½ΠΈΠΈ Π½Π°ΠΏΠΎΠ»Π½ΠΈΡΠ΅Π»Ρ, Π΄ΠΎΠ±Π°Π²ΠΊΠΈ ΠΈ Π²ΡΠΏΠ΅Π½ΠΈΠ²Π°ΡΠ΅Π»Ρ, ΠΏΠΎΡΡΠΎΠΌΡ ΠΌΡ ΠΏΠΎΡΡΠΎΡΠ½Π½ΠΎ ΡΠΎΠ²Π΅ΡΡΠ΅Π½ΡΡΠ²ΡΠ΅ΠΌ Π½Π°Ρ ΠΏΡΠΎΡΠ΅ΡΡ, ΡΡΠΎΠ±Ρ Π΄ΠΎΠ±ΠΈΡΡΡΡ Π½Π°ΠΈΠ»ΡΡΡΠΈΡ ΠΏΡΠ΅ΠΈΠΌΡΡΠ΅ΡΡΠ² Π΄Π»Ρ ΡΡΠΈΡ ΡΠ½ΠΈΠΊΠ°Π»ΡΠ½ΡΡ ΠΌΠ°ΡΠ΅ΡΠΈΠ°Π»ΠΎΠ².
ΠΡΠ»ΠΈ Ρ Π²Π°Ρ Π΅ΡΡΡ Π΄ΠΎΠΏΠΎΠ»Π½ΠΈΡΠ΅Π»ΡΠ½ΡΠ΅ Π²ΠΎΠΏΡΠΎΡΡ ΠΎ ΡΠΎΠΌ, ΠΊΠ°ΠΊΠ°Ρ ΡΠ΅Ρ Π½ΠΎΠ»ΠΎΠ³ΠΈΡ Π»ΠΈΡΡΡ ΠΏΠΎΠ΄ Π΄Π°Π²Π»Π΅Π½ΠΈΠ΅ΠΌ ΠΌΠΎΠΆΠ΅Ρ ΠΏΠΎΡΡΠ΅Π±ΠΎΠ²Π°ΡΡΡΡ Π΄Π»Ρ Π²Π°ΡΠ΅ΠΉ Π΄Π΅ΡΠ°Π»ΠΈ, ΠΌΡ Π±ΡΠ΄Π΅ΠΌ ΡΠ°Π΄Ρ Π²Π°ΠΌ ΠΏΠΎΠΌΠΎΡΡ.
ΠΡΠΎΡΡΠΎ Π·Π°ΠΏΠΎΠ»Π½ΠΈΡΠ΅ ΡΠΎΡΠΌΡ Π½ΠΈΠΆΠ΅ ΠΈΠ»ΠΈ ΡΠ²ΡΠΆΠΈΡΠ΅ΡΡ Ρ Π½Π°ΠΌΠΈ, ΠΈ ΠΌΡ ΡΠ²ΡΠΆΠ΅ΠΌΡΡ Ρ Π²Π°ΠΌΠΈ!
ΠΠ²ΠΎΠ»ΡΡΠΈΡ Π»ΠΈΡΡΡ ΠΏΠ»Π°ΡΡΠΌΠ°ΡΡ ΠΏΠΎΠ΄ Π΄Π°Π²Π»Π΅Π½ΠΈΠ΅ΠΌ: ΡΡΠΎ Π΄Π°Π»ΡΡΠ΅?
ΠΠ΅ΡΠΌΠΎΡΡΡ Π½Π° ΡΠΎ, ΡΡΠΎ Π»ΠΈΡΡΠ΅ ΠΏΠ»Π°ΡΡΠΌΠ°ΡΡ ΠΏΠΎΠ΄ Π΄Π°Π²Π»Π΅Π½ΠΈΠ΅ΠΌ Π·Π½Π°ΡΠΈΡΠ΅Π»ΡΠ½ΠΎ ΠΏΡΠΎΠ΄Π²ΠΈΠ½ΡΠ»ΠΎΡΡ Π·Π° ΡΡΠΈ Π³ΠΎΠ΄Ρ, ΠΎΠ½ΠΎ ΠΏΠΎ-ΠΏΡΠ΅ΠΆΠ½Π΅ΠΌΡ ΠΎΡΠ½ΠΎΠ²Π°Π½ΠΎ Π½Π° ΡΠ΅Ρ
ΠΆΠ΅ ΡΡΠ°Π½Π΄Π°ΡΡΠ½ΡΡ
ΠΏΡΠΈΠ½ΡΠΈΠΏΠ°Ρ
, ΡΡΠΎ ΠΈ ΠΌΠ½ΠΎΠ³ΠΎ Π»Π΅Ρ Π½Π°Π·Π°Π΄; ΡΠΎΠ²ΡΠ΅ΠΌΠ΅Π½Π½ΡΠ΅ ΡΠ΅Ρ
Π½ΠΎΠ»ΠΎΠ³ΠΈΡΠ΅ΡΠΊΠΈΠ΅ ΡΠ°Π·ΡΠ°Π±ΠΎΡΠΊΠΈ ΡΠΎΠ»ΡΠΊΠΎ Π΅ΡΠ΅ Π±ΠΎΠ»ΡΡΠ΅ ΠΏΠΎΠ²ΡΡΠΈΠ»ΠΈ Π΅Π³ΠΎ ΡΠ½ΠΈΠ²Π΅ΡΡΠ°Π»ΡΠ½ΠΎΡΡΡ ΠΈ Π½Π°Π΄Π΅ΠΆΠ½ΠΎΡΡΡ.
ΠΠΎ Π²ΡΠ΅ΠΌΡ Π»ΠΈΡΡΡ ΠΏΠ»Π°ΡΡΠΌΠ°ΡΡ ΠΏΠΎΠ΄ Π΄Π°Π²Π»Π΅Π½ΠΈΠ΅ΠΌ ΡΠ°ΡΡΠΈΡΡ ΠΏΠ»Π°ΡΡΠΈΠΊΠ° ΠΏΠ»Π°Π²ΡΡΡΡ ΠΈ Π²ΠΏΡΡΡΠΊΠΈΠ²Π°ΡΡΡΡ Π² ΡΠΎΡΠΌΡ, ΠΊΠΎΡΠΎΡΡΠ΅ ΠΎΡ Π»Π°ΠΆΠ΄Π°ΡΡΡΡ Π²ΠΎΠ΄ΠΎΠΉ ΠΈΠ»ΠΈ ΠΎΡ Π»Π°ΠΆΠ΄Π°ΡΡΠ΅ΠΉ ΠΆΠΈΠ΄ΠΊΠΎΡΡΡΡ, ΠΏΠΎΠ·Π²ΠΎΠ»ΡΡΡΠ΅ΠΉ ΠΏΠ»Π°ΡΡΠΈΠΊΡ Π·Π°ΡΠ²Π΅ΡΠ΄Π΅ΡΡ.ΠΠΎΡΠ»Π΅ ΡΠΎΠ³ΠΎ, ΠΊΠ°ΠΊ ΠΎΠ½ Π·Π°ΡΠ²Π΅ΡΠ΄Π΅Π΅Ρ, ΠΎΠ½ Π²ΡΡΠ°Π»ΠΊΠΈΠ²Π°Π΅ΡΡΡ ΠΈΠ· ΡΠΎΡΠΌΡ ΠΈ Π³ΠΎΡΠΎΠ² ΠΊ ΠΈΡΠΏΠΎΠ»ΡΠ·ΠΎΠ²Π°Π½ΠΈΡ.
ΠΠ»Π°ΡΡΠΈΠΊΠΎΠ²ΡΠ΅ ΠΌΠ°ΡΠ΅ΡΠΈΠ°Π»Ρ Π΄Π»Ρ Π»ΠΈΡΡΡ ΠΏΠΎΠ΄ Π΄Π°Π²Π»Π΅Π½ΠΈΠ΅ΠΌ
ΠΠ·ΠΎΠ±ΡΠ΅ΡΠ΅Π½Π½ΡΠ΅ Π² 1850-Ρ Π³ΠΎΠ΄Π°Ρ , Ρ ΡΠ°Π½Π½ΠΈΠΌΠΈ ΠΏΠ»Π°ΡΡΠΈΠΊΠΎΠ²ΡΠΌΠΈ ΡΠΎΡΠΌΠ°ΠΌΠΈ Π±ΡΠ»ΠΎ ΡΡΠ΅Π·Π²ΡΡΠ°ΠΉΠ½ΠΎ ΡΡΡΠ΄Π½ΠΎ ΡΠ°Π±ΠΎΡΠ°ΡΡ, Π½ΠΎ Π² 1870-Ρ Π³ΠΎΠ΄Π°Ρ Π±ΡΠ»ΠΈ ΡΠ°Π·ΡΠ°Π±ΠΎΡΠ°Π½Ρ Π±ΠΎΠ»Π΅Π΅ ΠΏΠΎΠ΄Π°ΡΠ»ΠΈΠ²ΡΠ΅ ΡΠΎΡΠΌΡ, ΠΊΠ°ΠΊ ΠΈ ΠΏΡΠΎΡΠ΅ΡΡ Π»ΠΈΡΡΡ ΠΏΠ»Π°ΡΡΠΌΠ°ΡΡ ΠΏΠΎΠ΄ Π΄Π°Π²Π»Π΅Π½ΠΈΠ΅ΠΌ, ΠΊΠΎΡΠΎΡΡΠΉ ΠΏΠΎΠ·Π²ΠΎΠ»ΠΈΠ» Π±ΡΡΡΡΠΎ ΠΈ ΡΡΡΠ΅ΠΊΡΠΈΠ²Π½ΠΎ ΡΠΎΡΠΌΠΎΠ²Π°ΡΡ Ρ ΡΡΠ΅ΡΠΎΠΌ ΠΊΠΎΠ½ΠΊΡΠ΅ΡΠ½ΡΡ ΠΏΠΎΡΡΠ΅Π±Π½ΠΎΡΡΠ΅ΠΉ ΠΏΡΠΈΠΌΠ΅Π½Π΅Π½ΠΈΡ.
Π‘Π΅Π³ΠΎΠ΄Π½Ρ Π΄Π»Ρ Π»ΠΈΡΡΡ ΠΏΠΎΠ΄ Π΄Π°Π²Π»Π΅Π½ΠΈΠ΅ΠΌ ΠΌΠΎΠΆΠ½ΠΎ ΠΈΡΠΏΠΎΠ»ΡΠ·ΠΎΠ²Π°ΡΡ ΠΌΠ½ΠΎΠ³ΠΈΠ΅ ΡΠΈΠΏΡ ΠΏΠ»Π°ΡΡΠΈΠΊΠ° — Ρ ΡΠ°Π·Π½ΠΎΠΉ ΡΠ΅ΠΌΠΏΠ΅ΡΠ°ΡΡΡΠΎΠΉ ΠΏΠ»Π°Π²Π»Π΅Π½ΠΈΡ, ΡΡΠΎ Π΄Π΅Π»Π°Π΅Ρ Π΅Π³ΠΎ ΡΠ½ΠΈΠ²Π΅ΡΡΠ°Π»ΡΠ½ΡΠΌ ΡΠ΅ΡΠ΅Π½ΠΈΠ΅ΠΌ Π΄Π»Ρ ΡΠΈΡΠΎΠΊΠΎΠ³ΠΎ ΡΠΏΠ΅ΠΊΡΡΠ° ΠΎΡΡΠ°ΡΠ»Π΅ΠΉ ΠΈ ΡΡΠ΅Ρ ΠΏΡΠΈΠΌΠ΅Π½Π΅Π½ΠΈΡ.Π Π°Π·Π»ΠΈΡΠ½ΡΠ΅ ΡΠΈΠΏΡ ΠΏΠ»Π°ΡΡΠΌΠ°ΡΡ ΠΎΠ±Π»Π°Π΄Π°ΡΡ ΡΠ½ΠΈΠΊΠ°Π»ΡΠ½ΡΠΌΠΈ ΡΠ²ΠΎΠΉΡΡΠ²Π°ΠΌΠΈ ΠΈ ΠΏΡΠ΅ΠΈΠΌΡΡΠ΅ΡΡΠ²Π°ΠΌΠΈ Π΄Π»Ρ ΠΊΠΎΠ½ΠΊΡΠ΅ΡΠ½ΡΡ
ΠΏΡΠΈΠΌΠ΅Π½Π΅Π½ΠΈΠΉ ΠΈ ΠΌΠΎΠ³ΡΡ Π±ΡΡΡ ΠΎΠ±ΡΠ΅Π΄ΠΈΠ½Π΅Π½Ρ Ρ Π΄ΡΡΠ³ΠΈΠΌΠΈ ΡΠΈΠΏΠ°ΠΌΠΈ ΠΌΠ°ΡΠ΅ΡΠΈΠ°Π»ΠΎΠ² ΠΈ Π΄ΠΎΠ±Π°Π²ΠΎΠΊ Π΄Π»Ρ ΠΏΠΎΠ»ΡΡΠ΅Π½ΠΈΡ ΡΠ°Π·Π»ΠΈΡΠ½ΡΡ
Ρ
Π°ΡΠ°ΠΊΡΠ΅ΡΠΈΡΡΠΈΠΊ ΠΈ ΠΎΠΊΡΠ°ΡΠΊΠΈ.
ΠΠ΅ΠΊΠΎΡΠΎΡΡΠ΅ ΠΈΠ· ΡΠ°ΠΌΡΡ ΡΠ½ΠΈΠ²Π΅ΡΡΠ°Π»ΡΠ½ΡΡ ΠΈ ΠΏΠΎΠΏΡΠ»ΡΡΠ½ΡΡ ΡΠ΅Π³ΠΎΠ΄Π½Ρ ΠΏΠ»Π°ΡΡΠΈΠΊΠΎΠ² Π²ΠΊΠ»ΡΡΠ°ΡΡ:
- ΠΠΠ‘
- ΠΠΎΠ»ΠΈΡΡΠΈΠ»Π΅Π½
- ΠΠ΅ΠΉΠ»ΠΎΠ½
- ΠΠΠ₯ ΠΈ ΠΏΠΎΠ»ΠΈΡΡΠ΅ΡΠ°Π½
- ΠΠΎΠ»ΠΈΠΏΡΠΎΠΏΠΈΠ»Π΅Π½
- HIPS
ΠΠ°ΡΠΈΠ°Π½ΡΡ ΠΏΠ»Π°ΡΡΠΈΠΊΠΎΠ²ΡΡ ΡΠΎΡΠΌ Π΄Π»Ρ Π»ΠΈΡΡΡ ΠΏΠΎΠ΄ Π΄Π°Π²Π»Π΅Π½ΠΈΠ΅ΠΌ
Π ΠΏΡΠΎΡΠ»ΠΎΠΌ ΡΠΎΡΠΌΡ ΠΎΠ±ΡΡΠ½ΠΎ ΡΠΎΠ·Π΄Π°Π²Π°Π»ΠΈΡΡ Ρ Π΄Π²ΡΠΌΡ ΡΠ°Π·Π½ΡΠΌΠΈ ΠΏΠ»Π°ΡΡΠΈΠ½Π°ΠΌΠΈ; ΠΎΠ΄Π½Π° ΡΠΎΠ΄Π΅ΡΠΆΠ°Π»Π° ΠΏΠΎΠ»ΠΎΡΡΡ ΡΠΎΡΠΌΡ — Π³Π΄Π΅ ΠΏΡΠΎΠΈΡΡ ΠΎΠ΄ΠΈΡ ΡΠ°ΠΊΡΠΈΡΠ΅ΡΠΊΠΎΠ΅ Π²ΠΏΡΡΡΠΊΠΈΠ²Π°Π½ΠΈΠ΅ ΡΠ°ΡΠΏΠ»Π°Π²Π»Π΅Π½Π½ΠΎΠ³ΠΎ ΠΏΠ»Π°ΡΡΠΈΠΊΠ° — Π° Π΄ΡΡΠ³Π°Ρ ΠΈΡΠΏΠΎΠ»ΡΠ·ΠΎΠ²Π°Π»Π°ΡΡ Π΄Π»Ρ ΡΡΡΠ΅ΠΊΡΠΈΠ²Π½ΠΎΠ³ΠΎ Π²ΡΡΠ°Π»ΠΊΠΈΠ²Π°Π½ΠΈΡ Π³ΠΎΡΠΎΠ²ΠΎΠ³ΠΎ ΠΏΡΠΎΠ΄ΡΠΊΡΠ° ΠΈΠ· ΡΠΎΡΠΌΡ.
Π’Π΅ΠΏΠ΅ΡΡ ΠΏΡΠΎΡΠ΅ΡΡΡ Π°Π²ΡΠΎΠΌΠ°ΡΠΈΠ·ΠΈΡΠΎΠ²Π°Π½Π½ΠΎΠ³ΠΎ ΠΏΡΠΎΠΈΠ·Π²ΠΎΠ΄ΡΡΠ²Π° (CAM) ΠΏΠΎΠ·Π²ΠΎΠ»ΡΡΡ ΡΠΎΠ·Π΄Π°Π²Π°ΡΡ Π³ΠΎΡΠ°Π·Π΄ΠΎ Π±ΠΎΠ»Π΅Π΅ ΡΠ»ΠΎΠΆΠ½ΡΠ΅ ΡΠΎΡΠΌΡ, ΠΊΠΎΡΠΎΡΡΠ΅ ΠΌΠΎΠ³ΡΡ ΡΠΎΠ΄Π΅ΡΠΆΠ°ΡΡ Π½Π΅ΡΠΊΠΎΠ»ΡΠΊΠΎ ΡΠ΅ΠΊΡΠΈΠΉ ΠΈΠ»ΠΈ ΡΠ°ΡΡΠ΅ΠΉ. CAM ΡΠ°ΠΊΠΆΠ΅ ΠΎΠ±Π΅ΡΠΏΠ΅ΡΠΈΠ²Π°Π΅Ρ Π³ΠΎΡΠ°Π·Π΄ΠΎ Π±ΠΎΠ»ΡΡΠ΅ Π΄Π΅ΡΠ°Π»Π΅ΠΉ ΠΈ ΡΠΎΡΠ½ΠΎΡΡΠΈ, Π½ΠΎ ΠΏΠΎΠ»ΠΎΡΡΡ ΡΠΎΡΠΌΡ ΠΈ ΠΏΠ»ΠΈΡΠ° Π²ΡΡΠ°Π»ΠΊΠΈΠ²Π°ΡΠ΅Π»Ρ ΠΎΡΡΠ°ΡΡΡΡ Π΄Π²ΡΠΌΡ Π²Π°ΠΆΠ½ΡΠΌΠΈ, ΠΏΠ΅ΡΠ²ΠΈΡΠ½ΡΠΌΠΈ ΡΠ°ΡΡΡΠΌΠΈ.
ΠΠ±ΠΎΡΡΠ΄ΠΎΠ²Π°Π½ΠΈΠ΅ Π΄Π»Ρ Π»ΠΈΡΡΡ ΠΏΠ»Π°ΡΡΠΌΠ°ΡΡ ΠΏΠΎΠ΄ Π΄Π°Π²Π»Π΅Π½ΠΈΠ΅ΠΌ
ΠΠΈΠ½ΡΠΎΠ²ΡΠ΅ ΡΠ΅ΡΠΌΠΎΠΏΠ»Π°ΡΡΠ°Π²ΡΠΎΠΌΠ°ΡΡ, ΡΠΏΡΠΎΠ΅ΠΊΡΠΈΡΠΎΠ²Π°Π½Π½ΡΠ΅ ΠΈ ΠΏΠΎΡΡΡΠΎΠ΅Π½Π½ΡΠ΅ Π°ΠΌΠ΅ΡΠΈΠΊΠ°Π½ΡΠΊΠΈΠΌ ΠΈΠ·ΠΎΠ±ΡΠ΅ΡΠ°ΡΠ΅Π»Π΅ΠΌ ΠΠΆΠ΅ΠΉΠΌΡΠΎΠΌ Π£ΠΎΡΡΠΎΠ½ΠΎΠΌ Π₯Π΅Π½Π΄ΡΠΈ, Π·Π½Π°ΡΠΈΡΠ΅Π»ΡΠ½ΠΎ ΠΈΠ·ΠΌΠ΅Π½ΠΈΠ»ΠΈ ΠΏΡΠΎΠΈΠ·Π²ΠΎΠ΄ΡΡΠ²Π΅Π½Π½ΡΠΉ Π»Π°Π½Π΄ΡΠ°ΡΡ; ΠΏΠΎΠ·Π²ΠΎΠ»ΡΡ ΡΠΎΡΠ½ΠΎ ΠΊΠΎΠ½ΡΡΠΎΠ»ΠΈΡΠΎΠ²Π°ΡΡ ΡΠΊΠΎΡΠΎΡΡΡ Π²ΠΏΡΡΡΠΊΠ°, ΡΡΠΎΡ ΠΌΠ΅ΡΠΎΠ΄ Π·Π½Π°ΡΠΈΡΠ΅Π»ΡΠ½ΠΎ ΡΠ»ΡΡΡΠΈΠ» ΠΊΠ°ΡΠ΅ΡΡΠ²ΠΎ Π³ΠΎΡΠΎΠ²ΡΡ
ΠΈΠ·Π΄Π΅Π»ΠΈΠΉ. ΠΠΈΠ½ΡΠΎΠ²ΠΎΠ΅ Π»ΠΈΡΡΠ΅ ΠΏΠΎΠ΄ Π΄Π°Π²Π»Π΅Π½ΠΈΠ΅ΠΌ ΡΠ°ΠΊΠΆΠ΅ ΠΏΠΎΠ·Π²ΠΎΠ»ΠΈΠ»ΠΎ ΡΠΌΠ΅ΡΠΈΠ²Π°ΡΡ ΠΌΠ°ΡΠ΅ΡΠΈΠ°Π»Ρ ΠΏΠ΅ΡΠ΅Π΄ Π½Π°ΡΠ°Π»ΠΎΠΌ ΠΏΡΠΎΡΠ΅ΡΡΠ° Π²ΠΏΡΡΡΠΊΠ°; ΡΡΠΎ ΠΎΠ·Π½Π°ΡΠ°Π»ΠΎ, ΡΡΠΎ ΡΠ²Π΅ΡΠ½ΠΎΠΉ ΠΈΠ»ΠΈ ΠΏΠ΅ΡΠ΅ΡΠ°Π±ΠΎΡΠ°Π½Π½ΡΠΉ ΠΏΠ»Π°ΡΡΠΈΠΊ ΡΠ΅ΠΏΠ΅ΡΡ ΠΌΠΎΠΆΠ½ΠΎ Π±ΡΠ»ΠΎ Π΄ΠΎΠ±Π°Π²Π»ΡΡΡ ΠΊ ΠΏΠ΅ΡΠ²ΠΈΡΠ½ΠΎΠΌΡ ΠΌΠ°ΡΠ΅ΡΠΈΠ°Π»Ρ ΠΈ ΡΡΠ°ΡΠ΅Π»ΡΠ½ΠΎ ΠΏΠ΅ΡΠ΅ΠΌΠ΅ΡΠΈΠ²Π°ΡΡ ΠΏΠ΅ΡΠ΅Π΄ ΡΠ΅ΠΌ, ΠΊΠ°ΠΊ Π²ΠΏΡΡΡΠΊΠΈΠ²Π°ΡΡ. Π‘Π΅Π³ΠΎΠ΄Π½Ρ ΠΎΠΊΠΎΠ»ΠΎ 95% Π²ΡΠ΅Ρ
ΡΠ΅ΡΠΌΠΎΠΏΠ»Π°ΡΡΠ°Π²ΡΠΎΠΌΠ°ΡΠΎΠ² ΠΈΡΠΏΠΎΠ»ΡΠ·ΡΡΡ ΡΡΡ ΡΠ½ΠΈΠ²Π΅ΡΡΠ°Π»ΡΠ½ΡΡ ΡΠ½Π΅ΠΊΠΎΠ²ΡΡ ΡΠ΅Ρ
Π½ΠΎΠ»ΠΎΠ³ΠΈΡ.
Hendry ΡΠ°ΠΊΠΆΠ΅ ΡΠ°Π·ΡΠ°Π±ΠΎΡΠ°Π» ΠΏΠ΅ΡΠ²ΡΠΉ Π²ΠΈΠ½ΡΠΎΠ²ΠΎΠΉ ΡΡΠ°Π½ΠΎΠΊ Ρ Π³Π°Π·ΠΎΠ²ΡΠΌ Π΄Π²ΠΈΠ³Π°ΡΠ΅Π»Π΅ΠΌ, ΠΊΠΎΡΠΎΡΡΠΉ ΠΏΠΎΠ·Π²ΠΎΠ»ΠΈΠ» ΠΈΠ·Π³ΠΎΡΠ°Π²Π»ΠΈΠ²Π°ΡΡ ΡΠ»ΠΎΠΆΠ½ΡΠ΅ ΠΏΠΎΠ»ΡΠ΅ Π΄Π΅ΡΠ°Π»ΠΈ, ΡΡΠ΅Π±ΡΡΡΠΈΠ΅ Π½Π΅Π±ΠΎΠ»ΡΡΠΎΠ³ΠΎ Π²ΡΠ΅ΠΌΠ΅Π½ΠΈ Π½Π° ΠΎΡ Π»Π°ΠΆΠ΄Π΅Π½ΠΈΠ΅. ΠΠ±Π΅ΡΠΏΠ΅ΡΠΈΠ²Π°Ρ ΠΏΠΎΠ²ΡΡΠ΅Π½Π½ΡΡ Π³ΠΈΠ±ΠΊΠΎΡΡΡ ΠΏΡΠΎΡΠ΅ΡΡΠ°, Π° ΡΠ°ΠΊΠΆΠ΅ ΠΏΡΠ΅Π²ΠΎΡΡ ΠΎΠ΄Π½ΡΡ ΠΏΡΠΎΡΠ½ΠΎΡΡΡ ΠΈ ΠΊΠ°ΡΠ΅ΡΡΠ²ΠΎ ΠΎΠ±ΡΠ°Π±ΠΎΡΠΊΠΈ, ΡΡΠΎΡ ΠΌΠ΅ΡΠΎΠ΄ ΡΠ½ΠΈΠΆΠ°Π΅Ρ Π·Π°ΡΡΠ°ΡΡ ΠΈ ΡΠΎΠΊΡΠ°ΡΠ°Π΅Ρ Π²ΡΠ΅ΠΌΡ ΠΏΡΠΎΠΈΠ·Π²ΠΎΠ΄ΡΡΠ²Π°, ΠΊΠΎΠ»ΠΈΡΠ΅ΡΡΠ²ΠΎ ΠΎΡΡ ΠΎΠ΄ΠΎΠ² ΠΈ Π²Π΅Ρ ΠΊΠΎΠ½Π΅ΡΠ½ΠΎΠ³ΠΎ ΠΏΡΠΎΠ΄ΡΠΊΡΠ°.
ΠΡΠ΄ΡΡΠ΅Π΅ Π»ΠΈΡΡΡ ΠΏΠ»Π°ΡΡΠΌΠ°ΡΡ ΠΏΠΎΠ΄ Π΄Π°Π²Π»Π΅Π½ΠΈΠ΅ΠΌ
ΠΠΎ ΠΌΠ΅ΡΠ΅ ΡΠΎΠ³ΠΎ ΠΊΠ°ΠΊ ΡΠ΅Ρ
Π½ΠΎΠ»ΠΎΠ³ΠΈΠΈ ΠΈ Π°Π²ΡΠΎΠΌΠ°ΡΠΈΡΠ΅ΡΠΊΠΈΠ΅ Π²ΠΎΠ·ΠΌΠΎΠΆΠ½ΠΎΡΡΠΈ ΠΏΡΠΎΠ΄ΠΎΠ»ΠΆΠ°ΡΡ ΡΠ°Π·Π²ΠΈΠ²Π°ΡΡΡΡ, Π»ΠΈΡΡΠ΅ ΠΏΠ»Π°ΡΡΠΌΠ°ΡΡ ΠΏΠΎΠ΄ Π΄Π°Π²Π»Π΅Π½ΠΈΠ΅ΠΌ — ΠΈ ΠΏΡΠΎΠΌΡΡΠ»Π΅Π½Π½ΠΎΡΡΡ ΠΏΠ»Π°ΡΡΠΌΠ°ΡΡ Π² ΡΠ΅Π»ΠΎΠΌ — ΡΠ°ΠΊΠΆΠ΅ ΠΏΡΠΎΠ΄ΠΎΠ»ΠΆΠ°Π΅Ρ ΡΠ°Π·Π²ΠΈΠ²Π°ΡΡΡΡ. Π‘Π΅Π³ΠΎΠ΄Π½Ρ, Π½Π°ΠΏΡΠΈΠΌΠ΅Ρ, Π²ΡΠ΅ Π±ΠΎΠ»Π΅Π΅ ΠΏΠΎΠΏΡΠ»ΡΡΠ½ΡΠΌΠΈ ΡΡΠ°Π½ΠΎΠ²ΡΡΡΡ Π±ΠΎΠ»Π΅Π΅ Π»Π΅Π³ΠΊΠΈΠ΅ ΠΌΠ°ΡΠ΅ΡΠΈΠ°Π»Ρ, Π° Π°Π²ΡΠΎΠΌΠ°ΡΠΈΠ·Π°ΡΠΈΡ ΡΠΎΠΊΡΠ°ΡΠ°Π΅Ρ ΡΠ°ΡΡ
ΠΎΠ΄Ρ ΠΈ ΡΠΎΠΊΡΠ°ΡΠ°Π΅Ρ ΠΏΠΎΡΡΠ΅Π±Π½ΠΎΡΡΡ Π² ΡΠ°Π±ΠΎΡΠ΅ΠΉ ΡΠΈΠ»Π΅. ΠΠ΅ΠΆΠ΄Ρ ΡΠ΅ΠΌ ΡΠ°ΡΡΠΈΡΠ΅Π½Π½ΡΠ΅ Π²ΠΎΠ·ΠΌΠΎΠΆΠ½ΠΎΡΡΠΈ ΠΈΠ½Π΄ΠΈΠ²ΠΈΠ΄ΡΠ°Π»ΡΠ½ΠΎΠΉ Π½Π°ΡΡΡΠΎΠΉΠΊΠΈ ΠΏΠΎΠ·Π²ΠΎΠ»ΡΡΡ ΡΠΎΠ·Π΄Π°Π²Π°ΡΡ Π±ΠΎΠ»Π΅Π΅ ΠΈΠ½Π΄ΠΈΠ²ΠΈΠ΄ΡΠ°Π»ΡΠ½ΡΠ΅ ΠΏΠ»Π°ΡΡΠΈΠΊΠΎΠ²ΡΠ΅ ΡΠ΅ΡΠ΅Π½ΠΈΡ. Π ΠΏΠΎΡΠΊΠΎΠ»ΡΠΊΡ ΡΠΊΠΎΠ»ΠΎΠ³ΠΈΡΠ΅ΡΠΊΠΈΠ΅ ΠΈΠ½ΠΈΡΠΈΠ°ΡΠΈΠ²Ρ ΠΏΡΠΎΠ΄ΠΎΠ»ΠΆΠ°ΡΡ Π½Π°Π±ΠΈΡΠ°ΡΡ ΠΎΠ±ΠΎΡΠΎΡΡ — ΠΊΠ°ΠΊ ΠΈΠ·-Π·Π° Π½ΠΎΠ²ΡΡ
ΠΏΡΠ°Π²ΠΈΠ», ΡΠ°ΠΊ ΠΈ ΠΈΠ·-Π·Π° ΠΌΠ΅Π½ΡΡΡΠΈΡ
ΡΡ ΠΏΡΠ΅Π΄ΠΏΠΎΡΡΠ΅Π½ΠΈΠΉ ΠΏΠΎΡΡΠ΅Π±ΠΈΡΠ΅Π»Π΅ΠΉ, Π²ΡΠΎΡΠΈΡΠ½ΡΠ΅, ΠΏΠ΅ΡΠ΅ΡΠ°Π±Π°ΡΡΠ²Π°Π΅ΠΌΡΠ΅ ΠΈ Π²ΠΎΠ·ΠΎΠ±Π½ΠΎΠ²Π»ΡΠ΅ΠΌΡΠ΅ ΠΏΠ»Π°ΡΡΠΌΠ°ΡΡΡ ΡΡΠ°Π½ΠΎΠ²ΡΡΡΡ Π²ΡΠ΅ Π±ΠΎΠ»Π΅Π΅ ΠΏΠΎΠΏΡΠ»ΡΡΠ½ΡΠΌΠΈ.
Π Rodon Group Π½Π°ΡΠ° ΠΊΠΎΠΌΠ°Π½Π΄Π° ΡΠΊΡΠΏΠ΅ΡΡΠΎΠ² Ρ ΠΎΡΠΎΡΠΎ ΡΠ°Π·Π±ΠΈΡΠ°Π΅ΡΡΡ Π² Π»ΠΈΡΡΠ΅ ΠΏΠ»Π°ΡΡΠΌΠ°ΡΡ ΠΏΠΎΠ΄ Π΄Π°Π²Π»Π΅Π½ΠΈΠ΅ΠΌ Π±ΠΎΠ»Π΅Π΅ 60 Π»Π΅Ρ, ΠΈ ΠΌΡ ΡΠ°ΠΊΠΆΠ΅ Π³ΠΎΡΠ΄ΠΈΠΌΡΡ ΡΠ΅ΠΌ, ΡΡΠΎ Π½Π°Ρ ΠΎΠ΄ΠΈΠΌΡΡ Π² Π°Π²Π°Π½Π³Π°ΡΠ΄Π΅ ΡΠ΅Π³ΠΎΠ΄Π½ΡΡΠ½Π΅ΠΉ Π·Π°Ρ Π²Π°ΡΡΠ²Π°ΡΡΠ΅ΠΉ ΡΠ²ΠΎΠ»ΡΡΠΈΠΈ Π»ΠΈΡΡΡ ΠΏΠ»Π°ΡΡΠΌΠ°ΡΡ ΠΏΠΎΠ΄ Π΄Π°Π²Π»Π΅Π½ΠΈΠ΅ΠΌ. Π§ΡΠΎΠ±Ρ ΡΠ·Π½Π°ΡΡ Π±ΠΎΠ»ΡΡΠ΅ ΠΎ Π»ΠΈΡΡΠ΅ ΠΏΠ»Π°ΡΡΠΌΠ°ΡΡ ΠΏΠΎΠ΄ Π΄Π°Π²Π»Π΅Π½ΠΈΠ΅ΠΌ ΠΈ Π»ΡΡΡΠ΅ ΠΏΠΎΠ½ΡΡΡ ΡΠ°Π·Π»ΠΈΡΠ½ΡΠ΅ Π΄ΠΎΡΡΡΠΏΠ½ΡΠ΅ ΠΌΠ΅ΡΠΎΠ΄Ρ, Π·Π°Π³ΡΡΠ·ΠΈΡΠ΅ Π±Π΅ΡΠΏΠ»Π°ΡΠ½ΡΡ ΡΠ»Π΅ΠΊΡΡΠΎΠ½Π½ΡΡ ΠΊΠ½ΠΈΠ³Ρ Π ΠΎΠ΄ΠΎΠ½Π° Β«ΠΠΈΡΡΠ΅ ΠΏΠ»Π°ΡΡΠΌΠ°ΡΡ ΠΏΠΎΠ΄ Π΄Π°Π²Π»Π΅Π½ΠΈΠ΅ΠΌ 101Β».
ΠΠΎΠ²ΡΠ΅ ΡΠ΅Ρ Π½ΠΎΠ»ΠΎΠ³ΠΈΠΈ, ΠΈΠ½Π½ΠΎΠ²Π°ΡΠΈΠΈ ΠΈ ΡΠ΅Π½Π΄Π΅Π½ΡΠΈΠΈ Π² Π»ΠΈΡΡΠ΅ ΠΏΠΎΠ΄ Π΄Π°Π²Π»Π΅Π½ΠΈΠ΅ΠΌ
ΠΠΈΡΡΠ΅ ΠΏΠΎΠ΄ Π΄Π°Π²Π»Π΅Π½ΠΈΠ΅ΠΌ — ΡΡΠΎ ΠΏΡΠΎΡΠ΅ΡΡ, ΠΈΡΠΏΠΎΠ»ΡΠ·ΡΠ΅ΠΌΡΠΉ ΠΏΡΠΈ ΠΏΡΠΎΠΈΠ·Π²ΠΎΠ΄ΡΡΠ²Π΅ Π΄Π΅ΡΠ°Π»Π΅ΠΉ ΠΈΠ»ΠΈ ΠΌΠ΅Ρ
Π°Π½ΠΈΡΠ΅ΡΠΊΠΈΡ
ΠΊΠΎΠΌΠΏΠΎΠ½Π΅Π½ΡΠΎΠ² Π² ΠΏΡΠΎΡΠ΅ΡΡΠ΅, ΠΊΠΎΡΠΎΡΡΠΉ Π²ΠΊΠ»ΡΡΠ°Π΅Ρ Π»ΠΈΡΡΠ΅ ΠΌΠ°ΡΠ΅ΡΠΈΠ°Π»Π° Π² ΠΏΡΠ΅ΡΡ-ΡΠΎΡΠΌΡ. ΠΡΠΎ ΡΠ½ΠΈΠ²Π΅ΡΡΠ°Π»ΡΠ½ΡΠΉ ΠΏΡΠΎΡΠ΅ΡΡ, ΠΊΠΎΡΠΎΡΡΠΉ ΡΠΏΡΠΎΡΡΠΈΠ» ΠΏΡΠΎΠΈΠ·Π²ΠΎΠ΄ΡΡΠ²ΠΎ Π½Π΅Π΄ΠΎΡΠΎΠ³ΠΈΡ
ΠΈ Π΄ΠΎΡΠΎΠ³ΠΈΡ
ΠΏΠ»Π°ΡΡΠΌΠ°ΡΡΠΎΠ²ΡΡ
Π΄Π΅ΡΠ°Π»Π΅ΠΉ. Π ΠΌΠΈΡΠ΅ Π»ΠΈΡΡΡ ΠΏΠΎΠ΄ Π΄Π°Π²Π»Π΅Π½ΠΈΠ΅ΠΌ Π±ΡΠ»ΠΈ Π΄ΠΎΡΡΠΈΠ³Π½ΡΡΡ ΡΡΠΏΠ΅Ρ
ΠΈ, ΠΈ ΡΡΠΎ ΡΠΎ, ΡΡΠΎ ΠΌΡ ΡΠΎΠ±ΠΈΡΠ°Π΅ΠΌΡΡ ΡΠ°ΡΡΠΌΠΎΡΡΠ΅ΡΡ Π² ΡΡΠΎΠΉ ΡΡΠ°ΡΡΠ΅. ΠΡΠ°ΠΊ, ΠΊΠ°ΠΊΠΎΠ²Ρ Π½Π΅ΠΊΠΎΡΠΎΡΡΠ΅ ΠΈΠ· Π½ΠΎΠ²ΡΡ
ΡΠ΅Ρ
Π½ΠΎΠ»ΠΎΠ³ΠΈΠΉ Π² ΠΌΠΈΡΠ΅ Π»ΠΈΡΡΡ ΠΏΠΎΠ΄ Π΄Π°Π²Π»Π΅Π½ΠΈΠ΅ΠΌ?
ΠΠΈΡΡΠ΅ ΠΏΠΎΠ΄ Π΄Π°Π²Π»Π΅Π½ΠΈΠ΅ΠΌ Ρ ΠΈΡΠΏΠΎΠ»ΡΠ·ΠΎΠ²Π°Π½ΠΈΠ΅ΠΌ Π³Π°Π·Π°
ΠΠ°ΠΈΠ±ΠΎΠ»Π΅Π΅ ΡΠ°ΡΡΠΎ ΠΈΡΠΏΠΎΠ»ΡΠ·ΡΠ΅ΠΌΡΠΉ Π³Π°Π· Π² ΡΡΠΎΠΌ ΠΏΡΠΎΡΠ΅ΡΡΠ΅ Π»ΠΈΡΡΡ ΠΏΠΎΠ΄ Π΄Π°Π²Π»Π΅Π½ΠΈΠ΅ΠΌ — Π°Π·ΠΎΡ. Π ΡΡΠΎΠΌ ΠΏΡΠΎΡΠ΅ΡΡΠ΅ ΠΏΠ»Π°ΡΡΠΈΠΊ Π²ΠΏΡΡΡΠΊΠΈΠ²Π°Π΅ΡΡΡ Π² ΡΠΎΡΠΌΡ ΠΏΠΎΠ΄ Π΄Π°Π²Π»Π΅Π½ΠΈΠ΅ΠΌ Π³Π°Π·Π°.Π Π°Π·Π»ΠΈΡΠ½ΡΠ΅ ΡΠ°ΡΡΠΈ ΡΠΎΡΠΌΡ Π·Π°ΠΏΠΎΠ»Π½ΡΡΡΡΡ, ΠΊΠΎΠ³Π΄Π° Π΄Π°Π²Π»Π΅Π½ΠΈΠ΅ Π³Π°Π·Π° Π²ΡΡΠ°Π»ΠΊΠΈΠ²Π°Π΅Ρ ΠΏΠ»Π°ΡΡΠΌΠ°ΡΡΠΎΠ²ΠΎΠ΅ ΡΠΎΠ΄Π΅ΡΠΆΠΈΠΌΠΎΠ΅. ΠΠ°Π²Π»Π΅Π½ΠΈΠ΅ ΠΌΠΎΠΆΠ΅Ρ Π±ΡΡΡ Π²Π²Π΅Π΄Π΅Π½ΠΎ Π² ΠΏΠΎΠ»ΠΎΡΡΡ ΡΠΎΡΠΌΡ ΠΈΠ»ΠΈ ΡΠ΅ΡΠ΅Π· ΡΠΎΠΏΠ»ΠΎ, ΡΡΠΎΠ±Ρ ΠΏΡΠΎΡΠΎΠ»ΠΊΠ½ΡΡΡ ΡΠ°ΡΠΏΠ»Π°Π²Π»Π΅Π½Π½ΡΠΉ ΠΏΠ»Π°ΡΡΠΈΠΊ ΡΡΠ΄Π°, Π³Π΄Π΅ ΠΎΠ½ Π΄ΠΎΠ»ΠΆΠ΅Π½ Π±ΡΡΡ. ΠΠ°Π²Π»Π΅Π½ΠΈΠ΅ ΠΌΠΎΠΆΠ΅Ρ ΠΎΠΊΠ°Π·ΡΠ²Π°ΡΡΡΡ Ρ ΡΠ°Π·Π½ΡΡ ΡΠΎΡΠ΅ΠΊ. Π€ΠΎΡΠΌΠΎΠ²Π°Π½ΠΈΠ΅ ΠΏΠΎΠ΄ Π΄Π°Π²Π»Π΅Π½ΠΈΠ΅ΠΌ — ΡΡΠΎ ΠΌΠ΅ΡΠΎΠ΄, ΠΊΠΎΡΠΎΡΡΠΉ Π±Π»Π°Π³ΠΎΠ΄Π°ΡΡ ΡΠ²ΠΎΠ΅ΠΉ ΡΡΡΠ΅ΠΊΡΠΈΠ²Π½ΠΎΡΡΠΈ ΠΏΠΎΠΌΠΎΠ³ ΠΈΠ½Π΄ΡΡΡΡΠΈΠΈ ΠΏΠ»Π°ΡΡΠΌΠ°ΡΡ ΡΠ°Π·Π²ΠΈΠ²Π°ΡΡΡΡ.
ΠΠ½ΡΠ΅ΠΊΡΠΈΡ ΠΏΠ΅Π½ΠΎΠΉ.
ΠΡΠΎ ΠΌΠ΅ΡΠΎΠ΄, ΠΊΠΎΡΠΎΡΡΠΉ ΠΎΡΠ΅Π½Ρ Π²Π°ΠΆΠ΅Π½, ΠΎΡΠΎΠ±Π΅Π½Π½ΠΎ ΠΊΠΎΠ³Π΄Π° ΠΏΡΠΎΠΈΠ·Π²ΠΎΠ΄ΠΈΡΠ΅Π»Ρ Ρ
ΠΎΡΠ΅Ρ Π΄ΠΎΠ±ΠΈΡΡΡΡ Π²ΡΡΠΎΠΊΠΎΠΉ ΡΡΡΡΠΊΡΡΡΠ½ΠΎΠΉ ΠΆΠ΅ΡΡΠΊΠΎΡΡΠΈ ΠΈ ΠΏΡΠΎΡΠ½ΠΎΡΡΠΈ ΠΊΠΎΠ½Π΅ΡΠ½ΠΎΠ³ΠΎ ΠΏΡΠΎΠ΄ΡΠΊΡΠ°. ΠΡΡΠ³ΠΎΠ΅ ΠΏΡΠ΅ΠΈΠΌΡΡΠ΅ΡΡΠ²ΠΎ ΠΈΡΠΏΠΎΠ»ΡΠ·ΠΎΠ²Π°Π½ΠΈΡ ΡΡΠΎΠ³ΠΎ ΠΌΠ΅ΡΠΎΠ΄Π° ΠΏΡΠΈ Π»ΠΈΡΡΠ΅ ΠΏΠΎΠ΄ Π΄Π°Π²Π»Π΅Π½ΠΈΠ΅ΠΌ Π·Π°ΠΊΠ»ΡΡΠ°Π΅ΡΡΡ Π² ΡΠΎΠΌ, ΡΡΠΎ ΠΎΠ½ ΠΎΠ±Π΅ΡΠΏΠ΅ΡΠΈΠ²Π°Π΅Ρ ΠΏΡΠ΅Π²ΠΎΡΡ
ΠΎΠ΄Π½ΡΡ Ρ
ΠΈΠΌΠΈΡΠ΅ΡΠΊΡΡ ΡΡΠΎΠΉΠΊΠΎΡΡΡ ΠΈ ΡΠ΅ΡΠΌΠΈΡΠ΅ΡΠΊΡΡ ΠΈΠ·ΠΎΠ»ΡΡΠΈΡ. ΠΡΠΎΡ ΠΏΡΠΎΡΠ΅ΡΡ Π² ΠΎΡΠ½ΠΎΠ²Π½ΠΎΠΌ ΠΈΡΠΏΠΎΠ»ΡΠ·ΡΠ΅ΡΡΡ ΠΏΡΠΈ ΠΏΡΠΎΠΈΠ·Π²ΠΎΠ΄ΡΡΠ²Π΅ ΠΏΠ°Π½Π΅Π»Π΅ΠΉ Π΄Π»Ρ Π»Π΅Π³ΠΊΠΎΠ²ΡΡ
Π°Π²ΡΠΎΠΌΠΎΠ±ΠΈΠ»Π΅ΠΉ.
ΠΠ΅ΡΠΎΠ΄ ΡΠΎΠ½ΠΊΠΎΡΡΠ΅Π½Π½ΡΡ .
ΠΡΠΎΡ ΠΌΠ΅ΡΠΎΠ΄ Π»ΠΈΡΡΡ ΠΏΠΎΠ΄ Π΄Π°Π²Π»Π΅Π½ΠΈΠ΅ΠΌ ΠΏΠΎΠ»Π΅Π·Π΅Π½ ΠΏΡΠΈ ΠΏΡΠΎΠΈΠ·Π²ΠΎΠ΄ΡΡΠ²Π΅ ΡΠΎΠ½ΠΊΠΎΡΡΠ΅Π½Π½ΡΡ ΠΊΠΎΠ½Π΅ΡΠ½ΡΡ ΠΏΡΠΎΠ΄ΡΠΊΡΠΎΠ². ΠΠ΄Π½Π°ΠΊΠΎ Ρ Π½Π΅Π³ΠΎ Π΅ΡΡΡ Π½Π΅Π΄ΠΎΡΡΠ°ΡΠΎΠΊ, ΠΏΠΎΡΠΊΠΎΠ»ΡΠΊΡ ΡΡΡΠ΄Π½ΠΎ ΠΎΠΏΡΠ΅Π΄Π΅Π»ΠΈΡΡ ΡΠΎΡΠ½ΠΎΠ΅ ΠΈΠ·ΠΌΠ΅ΡΠ΅Π½ΠΈΠ΅, ΡΡΠΎΠ±Ρ ΠΎΠΊΠΎΠ½ΡΠ°ΡΠ΅Π»ΡΠ½Π°Ρ ΡΠΎΡΠΌΠ° ΡΡΠΈΡΠ°Π»Π°ΡΡ ΡΠΎΠ½ΠΊΠΎΡΡΠ΅Π½Π½ΠΎΠΉ.ΠΠ±ΡΠ΅Π΅ ΠΏΡΠ°Π²ΠΈΠ»ΠΎ, ΠΊΠΎΡΠΎΡΠΎΠ΅ Π² ΠΎΡΠ½ΠΎΠ²Π½ΠΎΠΌ ΠΈΡΠΏΠΎΠ»ΡΠ·ΡΠ΅ΡΡΡ Π΄Π»Ρ Π΄Π΅ΡΠ°Π»Π΅ΠΉ, ΠΊΠΎΡΠΎΡΡΠ΅ ΡΡΠΈΡΠ°ΡΡΡΡ ΡΠΎΠ½ΠΊΠΎΡΡΠ΅Π½Π½ΡΠΌΠΈ, — ΡΡΠΎ ΠΊΠΎΠ³Π΄Π° ΠΎΠ½ΠΈ ΠΈΠΌΠ΅ΡΡ ΡΠΈΡΠΈΠ½Ρ ΠΌΠ΅Π½Π΅Π΅ 0,5 ΠΌΠΌ.
ΠΡΠΎΡ ΠΏΡΠΎΡΠ΅ΡΡ Π»ΠΈΡΡΡ ΠΏΠΎΠ΄ Π΄Π°Π²Π»Π΅Π½ΠΈΠ΅ΠΌ Π½Π°ΡΠ°Π»ΡΡ ΠΈΠ·-Π·Π° Π²ΡΡΠΎΠΊΠΎΠ³ΠΎ ΡΠΏΡΠΎΡΠ° Π½Π° ΡΠΎΠ½ΠΊΠΎΡΡΠ΅Π½Π½ΡΠ΅ Π΄Π΅ΡΠ°Π»ΠΈ ΠΈ Π²ΡΡΠΎΠΊΠΎΡΠΎΡΠ½ΠΎΠ³ΠΎ ΡΠΎΠ΅Π΄ΠΈΠ½Π΅Π½ΠΈΡ ΠΏΡΠΈ ΠΈΡ ΠΈΡΠΏΠΎΠ»ΡΠ·ΠΎΠ²Π°Π½ΠΈΠΈ.
ΠΠ½ΠΎΠ³ΠΎΠΊΠΎΠΌΠΏΠΎΠ½Π΅Π½ΡΠ½ΡΠΉ ΠΌΠ΅ΡΠΎΠ΄.
ΠΡΠΎΡ ΠΏΡΠΎΡΠ΅ΡΡ Π²ΠΊΠ»ΡΡΠ°Π΅Ρ ΠΈΡΠΏΠΎΠ»ΡΠ·ΠΎΠ²Π°Π½ΠΈΠ΅ Π±ΠΎΠ»Π΅Π΅ ΠΎΠ΄Π½ΠΎΠ³ΠΎ ΠΌΠ°ΡΠ΅ΡΠΈΠ°Π»Π° ΡΠ°Π·Π½ΡΡ
ΡΠ²Π΅ΡΠΎΠ² Π² ΠΎΠ΄Π½ΠΎΠΉ ΠΈ ΡΠΎΠΉ ΠΆΠ΅ ΡΠΎΡΠΌΠ΅. Π ΡΠ΅Π·ΡΠ»ΡΡΠ°ΡΠ΅ ΠΏΠΎΠ»ΡΡΠ°Π΅ΡΡΡ ΡΠΎΡΠΌΠ° Ρ ΡΠ°Π·Π½ΠΎΠΉ ΡΠ΅ΠΊΡΡΡΡΠΎΠΉ, ΡΠΎΡΠΌΠΎΠΉ ΠΈ ΡΠ²Π΅ΡΠΎΠΌ. ΠΡΠΎΡ ΠΌΠ΅ΡΠΎΠ΄ Π²ΡΠ³ΠΎΠ΄Π΅Π½, ΠΏΠΎΡΠΊΠΎΠ»ΡΠΊΡ ΠΎΠ½ ΠΏΠΎΠ·Π²ΠΎΠ»ΡΠ΅Ρ ΠΏΠΎΠ»ΡΡΠ°ΡΡ Π΄Π΅ΡΠ°Π»ΠΈ Ρ ΠΏΡΠ΅Π²ΠΎΡΡ
ΠΎΠ΄Π½ΠΎΠΉ Ρ
ΠΈΠΌΠΈΡΠ΅ΡΠΊΠΎΠΉ, ΡΠ΅ΡΠΌΠΈΡΠ΅ΡΠΊΠΎΠΉ ΠΈ ΠΌΠ΅Ρ
Π°Π½ΠΈΡΠ΅ΡΠΊΠΎΠΉ ΡΡΠΎΠΉΠΊΠΎΡΡΡΡ.
ΠΡΠΎ ΠΎΡΠ½ΠΎΠ²Π½ΡΠ΅ ΡΠ΅Ρ Π½ΠΎΠ»ΠΎΠ³ΠΈΡΠ΅ΡΠΊΠΈΠ΅ Π΄ΠΎΡΡΠΈΠΆΠ΅Π½ΠΈΡ, ΠΊΠΎΡΠΎΡΡΠ΅ Π±ΡΠ»ΠΈ ΠΎΡΠΌΠ΅ΡΠ΅Π½Ρ Π² ΠΌΠΈΡΠ΅ Π»ΠΈΡΡΡ ΠΏΠΎΠ΄ Π΄Π°Π²Π»Π΅Π½ΠΈΠ΅ΠΌ. ΠΡΠ΄ΡΡΠ΅Π΅ ΠΎΠΏΡΠ΅Π΄Π΅Π»Π΅Π½Π½ΠΎ Π²ΡΠ³Π»ΡΠ΄ΠΈΡ ΡΠ²Π΅ΡΠ»ΡΠΌ, ΠΏΠΎΡΠΊΠΎΠ»ΡΠΊΡ ΡΠΎ Π²ΡΠ΅ΠΌΠ΅Π½Π΅ΠΌ Π² Π»ΠΈΡΡΠ΅ ΠΏΠΎΠ΄ Π΄Π°Π²Π»Π΅Π½ΠΈΠ΅ΠΌ ΠΏΠΎΡΠ²Π»ΡΠ΅ΡΡΡ Π²ΡΠ΅ Π±ΠΎΠ»ΡΡΠ΅ ΠΈΠ΄Π΅ΠΉ ΠΈ ΠΌΡΡΠ»Π΅ΠΉ.
Π€ΠΎΡΠΌΠΎΠ²ΠΎΡΠ½Π°Ρ Π΄ΠΎΠ±Π°Π²ΠΊΠ°
Β«ΠΠ°ΡΡΠΎΠ²ΠΎΠ΅ ΠΏΡΠΎΠΈΠ·Π²ΠΎΠ΄ΡΡΠ²ΠΎΒ» — ΡΡΠΎ ΡΠ΅ΡΠΌΠΈΠ½, ΠΊΠΎΡΠΎΡΡΠΉ ΠΎΠ±ΡΡΠ½ΠΎ Π½Π΅ Π°ΡΡΠΎΡΠΈΠΈΡΡΠ΅ΡΡΡ ΡΠΎ ΡΠ»ΠΎΠΆΠ½ΡΠΌΠΈ ΠΊΠΎΠΌΠΏΠΎΠ·ΠΈΡΠ½ΡΠΌΠΈ ΠΊΠΎΠΌΠΏΠΎΠ½Π΅Π½ΡΠ°ΠΌΠΈ, ΠΊΠΎΡΠΎΡΡΠ΅ ΠΈΠΌΠ΅ΡΡ Π½Π΅ΠΏΡΠ΅ΡΡΠ²Π½ΠΎΠ΅, Π²ΡΡΠΎΠ²Π½Π΅Π½Π½ΠΎΠ΅ Π°ΡΠΌΠΈΡΠΎΠ²Π°Π½ΠΈΠ΅ Π²ΠΎΠ»ΠΎΠΊΠ½ΠΎΠΌ, ΠΎΠ΄Π½Π°ΠΊΠΎ ΡΠ΅Ρ Π½ΠΎΠ»ΠΎΠ³ΠΈ ΠΊΠΎΠΌΠΏΠΎΠ·ΠΈΡΠΎΠ² Π΄ΠΎΠ»Π³ΠΎΠ΅ Π²ΡΠ΅ΠΌΡ ΠΈΡΠΏΠΎΠ»ΡΠ·ΠΎΠ²Π°Π»ΠΈ ΡΡΡ Π½Π΅ΡΠ»ΠΎΠ²ΠΈΠΌΡΡ ΠΊΠΎΠΌΠ±ΠΈΠ½Π°ΡΠΈΡ.Π ΠΊΠΎΠ½ΡΠ΅ ΠΊΠΎΠ½ΡΠΎΠ², ΡΡΠ½ΠΎΡΠ½ΡΠΉ ΠΏΠΎΡΠ΅Π½ΡΠΈΠ°Π» ΠΈΡΠΊΠ»ΡΡΠΈΡΠ΅Π»ΡΠ½ΠΎ Π²Π΅Π»ΠΈΠΊ, ΠΎΡΠΎΠ±Π΅Π½Π½ΠΎ Π² Π°Π²ΡΠΎΠΌΠΎΠ±ΠΈΠ»ΡΠ½ΠΎΠΉ ΠΏΡΠΎΠΌΡΡΠ»Π΅Π½Π½ΠΎΡΡΠΈ, Π΄Π»Ρ ΡΠ΅Π½ΡΠ°Π±Π΅Π»ΡΠ½ΡΡ , ΠΊΡΡΠΏΠ½ΠΎΡΠ΅ΡΠΈΠΉΠ½ΡΡ ΠΈ Π²ΡΡΠΎΠΊΠΎΠΏΡΠΎΠΈΠ·Π²ΠΎΠ΄ΠΈΡΠ΅Π»ΡΠ½ΡΡ ΠΊΠΎΠΌΠΏΠΎΠ·ΠΈΡΠ½ΡΡ ΠΊΠΎΠΌΠΏΠΎΠ½Π΅Π½ΡΠΎΠ².
ΠΠ° ΠΈΡΠΊΠ»ΡΡΠ΅Π½ΠΈΠ΅ΠΌ ΠΊΠΎΠΌΠΏΠΎΠ½Π΅Π½ΡΠΎΠ², ΠΈΠ·Π³ΠΎΡΠΎΠ²Π»Π΅Π½Π½ΡΡ
ΠΏΠΎ ΠΏΡΠ»ΡΡΡΠ·ΠΈΠΈ Π² ΠΎΡΠ΅Π½Ρ ΠΏΡΠΎΡΡΡΠ΅ ΠΏΡΠΎΡΠΈΠ»ΠΈ, ΡΡΠΎΡ ΡΡΠ½ΠΎΡΠ½ΡΠΉ ΠΏΠΎΡΠ΅Π½ΡΠΈΠ°Π» Π½Π΅ Π±ΡΠ» ΡΠ΅Π°Π»ΠΈΠ·ΠΎΠ²Π°Π½ Ρ ΠΏΠΎΠΌΠΎΡΡΡ ΡΠ΅Π³ΠΎΠ΄Π½ΡΡΠ½ΠΈΡ
ΠΏΡΠΎΠΈΠ·Π²ΠΎΠ΄ΡΡΠ²Π΅Π½Π½ΡΡ
ΡΠ΅Ρ
Π½ΠΎΠ»ΠΎΠ³ΠΈΠΉ. ΠΡΠΎΠΈΠ·Π²ΠΎΠ΄ΠΈΡΠ΅Π»ΠΈ ΠΊΠΎΠΌΠΏΠΎΠ·ΠΈΡΠΎΠ² Π»ΠΈΠ±ΠΎ ΠΌΠ°ΡΡΠΎΠ²ΠΎ ΠΏΡΠΎΠΈΠ·Π²ΠΎΠ΄ΡΡ ΡΠ»ΠΎΠΆΠ½ΡΠ΅ ΠΊΠΎΠΌΠΏΠΎΠ·ΠΈΡΠ½ΡΠ΅ ΠΊΠΎΠΌΠΏΠΎΠ½Π΅Π½ΡΡ, ΠΈΠ·Π³ΠΎΡΠΎΠ²Π»Π΅Π½Π½ΡΠ΅ ΠΈΠ· ΡΡΠ±Π»Π΅Π½ΠΎΠ³ΠΎ Π²ΠΎΠ»ΠΎΠΊΠ½Π°, Π»ΠΈΠ±ΠΎ ΠΈΡΠΏΠΎΠ»ΡΠ·ΡΡΡ ΡΠ΅Ρ
Π½ΠΎΠ»ΠΎΠ³ΠΈΠΈ ΠΈΠ·Π³ΠΎΡΠΎΠ²Π»Π΅Π½ΠΈΡ Π² ΠΎΡΠ½ΠΎΡΠΈΡΠ΅Π»ΡΠ½ΠΎ Π½Π΅Π±ΠΎΠ»ΡΡΠΈΡ
ΠΎΠ±ΡΠ΅ΠΌΠ°Ρ
Π΄Π»Ρ ΠΈΠ·Π³ΠΎΡΠΎΠ²Π»Π΅Π½ΠΈΡ ΡΠ°ΠΊΠΈΡ
ΠΊΠΎΠΌΠΏΠΎΠ½Π΅Π½ΡΠΎΠ² Ρ Π½Π΅ΠΏΡΠ΅ΡΡΠ²Π½ΡΠΌ ΠΎΡΠΈΠ΅Π½ΡΠΈΡΠΎΠ²Π°Π½Π½ΡΠΌ Π°ΡΠΌΠΈΡΠΎΠ²Π°Π½ΠΈΠ΅ΠΌ Π²ΠΎΠ»ΠΎΠΊΠ½ΠΎΠΌ.Π₯ΠΎΡΡ ΡΠ°ΠΊΠΈΠ΅ ΡΠ΅Ρ
Π½ΠΎΠ»ΠΎΠ³ΠΈΠΈ ΡΠΎΠ·ΡΠ΅Π²Π°Π½ΠΈΡ, ΠΊΠ°ΠΊ Π°Π²ΡΠΎΠΌΠ°ΡΠΈΡΠ΅ΡΠΊΠΎΠ΅ ΡΠ°Π·ΠΌΠ΅ΡΠ΅Π½ΠΈΠ΅ Π²ΠΎΠ»ΠΎΠΊΠΎΠ½ (AFP) ΠΈ ΡΡΠ΅Ρ
ΠΌΠ΅ΡΠ½Π°Ρ ΠΏΠ΅ΡΠ°ΡΡ Π½Π΅ΠΏΡΠ΅ΡΡΠ²Π½ΡΡ
Π²ΠΎΠ»ΠΎΠΊΠΎΠ½, ΡΠΎΠΊΡΠ°ΡΠ°ΡΡ Π²ΡΠ΅ΠΌΡ ΡΠΈΠΊΠ»Π°, ΠΎΠ½ΠΈ Π½Π΅ Π΄ΠΎΡΡΠΈΠ³Π»ΠΈ ΡΡΠΎΠ²Π½Ρ ΠΌΠ°ΡΡΠΎΠ²ΠΎΠ³ΠΎ ΠΏΡΠΎΠΈΠ·Π²ΠΎΠ΄ΡΡΠ²Π° ΡΠ»ΠΎΠΆΠ½ΡΡ
Π²ΡΡΠΎΠΊΠΎΠΏΡΠΎΠΈΠ·Π²ΠΎΠ΄ΠΈΡΠ΅Π»ΡΠ½ΡΡ
ΠΊΠΎΠΌΠΏΠΎΠ·ΠΈΡΠ½ΡΡ
ΠΊΠΎΠΌΠΏΠΎΠ½Π΅Π½ΡΠΎΠ².
ΠΠ΄Π½Π°ΠΊΠΎ Π½Π΅Π΄Π°Π²Π½ΡΡ ΠΏΠΎΠΏΡΡΠΊΠ° ΠΎΠ±ΡΠ΅Π΄ΠΈΠ½ΠΈΡΡ Π²ΡΡΠΎΠΊΡΡ ΠΏΡΠΎΠΈΠ·Π²ΠΎΠ΄ΠΈΡΠ΅Π»ΡΠ½ΠΎΡΡΡ ΠΈ Π±ΠΎΠ»ΡΡΠΎΠΉ ΠΎΠ±ΡΠ΅ΠΌ Π΄Π°Π΅Ρ Π±ΠΎΠ»ΡΡΠΈΠ΅ Π½Π°Π΄Π΅ΠΆΠ΄Ρ Π½Π° ΡΡΠΏΠ΅ΡΠ½ΠΎΠ΅ ΠΏΡΠ΅ΠΎΠ΄ΠΎΠ»Π΅Π½ΠΈΠ΅ ΡΠ°Π·ΡΡΠ²Π°. ΠΠΎΠ²ΠΈΡΠΎΠΊ Arris Composites (ΠΠ΅ΡΠΊΠ»ΠΈ, ΠΠ°Π»ΠΈΡΠΎΡΠ½ΠΈΡ, Π‘Π¨Π) ΠΏΡΠΈΠ²Π»Π΅ΠΊ Π²Π½ΠΈΠΌΠ°Π½ΠΈΠ΅ ΠΏΡΠΎΠΌΡΡΠ»Π΅Π½Π½ΠΎΠ³ΠΎ ΠΌΠΈΡΠ° Π² ΠΌΠ°Π΅ ΡΡΠΎΠ³ΠΎ Π³ΠΎΠ΄Π°, ΠΊΠΎΠ³Π΄Π° Π² ΡΡΠ°ΡΡΠ΅ Forbes Π±ΡΠ» ΡΠΏΠΎΠΌΡΠ½ΡΡ ΠΎΡΠ½ΠΎΠ²Π°ΡΠ΅Π»Ρ ΠΈ Π³Π΅Π½Π΅ΡΠ°Π»ΡΠ½ΡΠΉ Π΄ΠΈΡΠ΅ΠΊΡΠΎΡ ΠΡΠ°Π½ ΠΡΠΊΠΎΠ²ΠΈΡ.Π ΡΡΠ°ΡΡΠ΅ ΡΠ°ΠΊΠΆΠ΅ Π³ΠΎΠ²ΠΎΡΠΈΠ»ΠΎΡΡ ΠΎΠ± ΠΎΠ±ΡΡΠ²Π»Π΅Π½ΠΈΠΈ ΠΊΠΎΠΌΠΏΠ°Π½ΠΈΠΈ ΠΎ Π·Π°ΠΊΡΡΡΠΈΠΈ ΡΠΈΠ½Π°Π½ΡΠΈΡΠΎΠ²Π°Π½ΠΈΡ ΡΠ΅ΡΠΈΠΈ A Π² ΡΠ°Π·ΠΌΠ΅ΡΠ΅ 10 ΠΌΠΈΠ»Π»ΠΈΠΎΠ½ΠΎΠ² Π΄ΠΎΠ»Π»Π°ΡΠΎΠ², ΡΡΠΎ ΡΠ²Π»ΡΠ΅ΡΡΡ ΡΠ΅ΡΠΈΡΠ΅Π»ΡΠ½ΠΎΠΉ ΠΏΠΎΠ΄Π΄Π΅ΡΠΆΠΊΠΎΠΉ ΠΏΡΠΎΡΠ΅ΡΡΠ° Π°Π΄Π΄ΠΈΡΠΈΠ²Π½ΠΎΠ³ΠΎ ΡΠΎΡΠΌΠΎΠ²Π°Π½ΠΈΡ Arris Ρ ΡΠΎΠ²Π°ΡΠ½ΡΠΌ Π·Π½Π°ΠΊΠΎΠΌ ΠΈ Π·Π°ΡΠ²ΠΊΠΎΠΉ Π½Π° ΠΏΠ°ΡΠ΅Π½Ρ. ΠΠ΅ΡΠ΅Π΄ ΡΡΠΈΠΌ Π·Π½Π°ΠΌΠ΅Π½Π°ΡΠ΅Π»ΡΠ½ΡΠΌ ΡΠΎΠ±ΡΡΠΈΠ΅ΠΌ ΠΡΠΊΠΎΠ²ΠΈΡ ΡΠ°ΠΌ ΠΎΡ
Π°ΡΠ°ΠΊΡΠ΅ΡΠΈΠ·ΠΎΠ²Π°Π» ΠΏΡΠ΅Π΄ΡΠ΄ΡΡΠΈΠ΅ Π΄Π²Π° Π³ΠΎΠ΄Π° ΠΊΠ°ΠΊ Β«ΡΠΊΡΡΡΠ½ΡΡ ΡΠ°Π±ΠΎΡΡΒ», ΠΏΠΎΡΡΠΎΠΌΡ ΡΠΎΠ»ΡΠΊΠΎ Π² ΠΏΠΎΡΠ»Π΅Π΄Π½ΠΈΠ΅ Π½Π΅ΡΠΊΠΎΠ»ΡΠΊΠΎ ΠΌΠ΅ΡΡΡΠ΅Π² ΠΌΠ½ΠΎΠ³ΠΈΠ΅ Π·Π°ΠΈΠ½ΡΠ΅ΡΠ΅ΡΠΎΠ²Π°Π½Π½ΡΠ΅ ΡΡΠΎΡΠΎΠ½Ρ Π² ΠΎΠ±Π»Π°ΡΡΠΈ ΠΊΠΎΠΌΠΏΠΎΠ·ΠΈΡΠ½ΡΡ
ΠΌΠ°ΡΠ΅ΡΠΈΠ°Π»ΠΎΠ² Π½Π°ΡΠ°Π»ΠΈ ΠΈΡΡΠ»Π΅Π΄ΠΎΠ²Π°ΡΡ ΠΈ ΠΎΡΠ΅Π½ΠΈΠ²Π°ΡΡ ΠΏΠΎΡΠ΅Π½ΡΠΈΠ°Π» Π°Π΄Π΄ΠΈΡΠΈΠ²Π½ΠΎΠ³ΠΎ ΡΠΎΡΠΌΠΎΠ²Π°Π½ΠΈΡ.
ΠΠΈΠ΄Π΅Π½ΠΈΠ΅ Π°Π΄Π΄ΠΈΡΠΈΠ²Π½ΠΎΠ³ΠΎ ΡΠΎΡΠΌΠΎΠ²Π°Π½ΠΈΡ Π²ΡΡΠΎΡΠ»ΠΎ ΠΈΠ· ΠΈΠ½Π½ΠΎΠ²Π°ΡΠΈΠΎΠ½Π½ΡΡ
ΠΏΡΠΎΠΈΠ·Π²ΠΎΠ΄ΡΡΠ²Π΅Π½Π½ΡΡ
ΡΡΠΈΠ»ΠΈΠΉ, Π² ΠΊΠΎΡΠΎΡΡΡ
ΠΏΡΠΈΠ½ΡΠ»ΠΈ ΡΡΠ°ΡΡΠΈΠ΅ Π΄Π²Π° ΡΠΎΡΡΡΠ΅Π΄ΠΈΡΠ΅Π»Ρ Arris, ΠΡΠΊΠΎΠ²ΠΈΡ ΠΈ Π Π°ΠΉΠ»ΠΈ Π ΠΈΠ·, ΠΊΠΎΡΠΎΡΠ°Ρ ΡΠ°ΠΊΠΆΠ΅ ΡΠ²Π»ΡΠ΅ΡΡΡ Π³Π»Π°Π²Π½ΡΠΌ ΡΠ΅Ρ
Π½ΠΈΡΠ΅ΡΠΊΠΈΠΌ Π΄ΠΈΡΠ΅ΠΊΡΠΎΡΠΎΠΌ.ΠΡΠΊΠΎΠ²ΠΈΡ ΠΈ Π ΠΈΠ· ΡΠ°Π±ΠΎΡΠ°Π»ΠΈ Π½Π°Π΄ ΠΊΠΎΠΌΠΌΠ΅ΡΡΠΈΠ°Π»ΠΈΠ·Π°ΡΠΈΠ΅ΠΉ Π½ΠΎΠ²ΡΡ
ΠΏΡΠΈΠ»ΠΎΠΆΠ΅Π½ΠΈΠΉ Π΄Π»Ρ 3D-ΠΏΠ΅ΡΠ°ΡΠΈ Π½Π΅ΡΠΊΠΎΠ»ΡΠΊΠΈΠΌΠΈ ΡΠ°Π±ΠΎΡΠΎΠ΄Π°ΡΠ΅Π»ΡΠΌΠΈ. Β«ΠΠ»ΠΈΡΠ½ΠΈΠ΅ 3D-ΠΏΠ΅ΡΠ°ΡΠΈ Π½Π° ΠΊΡΡΠΏΠ½ΠΎΡΠ΅ΡΠΈΠΉΠ½ΠΎΠ΅ ΠΏΡΠΎΠΈΠ·Π²ΠΎΠ΄ΡΡΠ²ΠΎ Π²ΡΠ΅Π³Π΄Π° ΠΏΠ΅ΡΠ΅ΠΎΡΠ΅Π½ΠΈΠ²Π°Π΅ΡΡΡ, — ΡΡΠ²Π΅ΡΠΆΠ΄Π°Π΅Ρ ΠΡΠΊΠΎΠ²ΠΈΡ, — ΠΈ ΡΡΠΎ ΡΠ²ΡΠ·Π°Π½ΠΎ Ρ Π²ΡΡΠΎΠΊΠΈΠΌΠΈ Π·Π°ΡΡΠ°ΡΠ°ΠΌΠΈ Π½Π° ΠΎΠ±ΡΠ°Π±ΠΎΡΠΊΡ ΠΈ ΠΎΡΠ΄Π΅Π»ΠΊΡ Π½Π° Π΅Π΄ΠΈΠ½ΠΈΡΡ ΠΏΡΠΎΠΈΠ·Π²Π΅Π΄Π΅Π½Π½ΠΎΠΉ ΠΏΡΠΎΠ΄ΡΠΊΡΠΈΠΈ, Π° ΡΠ°ΠΊΠΆΠ΅ Ρ Π²ΡΡΠΎΠΊΠΈΠΌΠΈ ΠΌΠ°ΡΠ΅ΡΠΈΠ°Π»ΡΠ½ΡΠΌΠΈ Π·Π°ΡΡΠ°ΡΠ°ΠΌΠΈΒ». (Π₯ΠΎΡΡ Π½Π΅ΠΊΠΎΡΠΎΡΡΠ΅ 3D-ΠΏΡΠΈΠ½ΡΠ΅ΡΡ Π½Π°Ρ
ΠΎΠ΄ΡΡ ΡΠΏΠΎΡΠΎΠ±Ρ ΠΈΡΠΏΠΎΠ»ΡΠ·ΠΎΠ²Π°ΡΡ ΡΡΠ°Π½Π΄Π°ΡΡΠ½ΡΠ΅ ΠΌΠ°ΡΠ΅ΡΠΈΠ°Π»Ρ, ΠΌΠ½ΠΎΠ³ΠΈΠ΅ ΠΈΡΠΏΠΎΠ»ΡΠ·ΡΡΡ Π΄ΠΎΡΠΎΠ³ΠΎΡΡΠΎΡΡΠΈΠ΅ ΡΠΏΠ΅ΡΠΈΠ°Π»ΠΈΠ·ΠΈΡΠΎΠ²Π°Π½Π½ΡΠ΅ ΠΌΠ°ΡΠ΅ΡΠΈΠ°Π»Ρ. ) ΠΠ°ΡΠ° Ρ
ΠΎΡΠ΅Π»Π° Π½Π°ΠΉΡΠΈ ΡΠΏΠΎΡΠΎΠ± ΡΠ²Π΅ΡΡΠΈ Π½Π° Π½Π΅Ρ ΠΏΡΠ΅ΠΈΠΌΡΡΠ΅ΡΡΠ²Π° ΠΏΡΠΎΠΈΠ·Π²ΠΎΠ΄ΠΈΡΠ΅Π»ΡΠ½ΠΎΡΡΠΈ Π½Π°ΠΏΠ΅ΡΠ°ΡΠ°Π½Π½ΡΡ
Π½Π° 3D-ΠΏΡΠΈΠ½ΡΠ΅ΡΠ΅ ΠΊΠΎΠΌΠΏΠΎΠ·ΠΈΡΠΎΠ², Π°ΡΠΌΠΈΡΠΎΠ²Π°Π½Π½ΡΡ
Π½Π΅ΠΏΡΠ΅ΡΡΠ²Π½ΡΠΌ Π²ΠΎΠ»ΠΎΠΊΠ½ΠΎΠΌ, Π·Π° ΡΡΠ΅Ρ ΡΠΊΠΎΡΠΎΡΡΠΈ ΠΈ ΡΠΊΠΎΠ½ΠΎΠΌΠΈΡΠ½ΠΎΡΡΠΈ ΡΠ΅Ρ
Π½ΠΎΠ»ΠΎΠ³ΠΈΠΈ Π»ΠΈΡΡΡ.ΠΡΠΊΠΎΠ²ΠΈΡ ΠΎΠΏΠΈΡΡΠ²Π°Π΅Ρ ΡΡΡ ΠΈΠ΄Π΅Ρ ΠΊΠ°ΠΊ Β«ΡΠΎΠ²ΠΌΠ΅ΡΠ΅Π½Π½ΡΠΉ ΡΠΎΡΠΌΠΎΠ²Π°Π½Π½ΡΠΉ ΡΠ»Π΅ΠΌΠ΅Π½Ρ, Π°ΡΠΌΠΈΡΠΎΠ²Π°Π½Π½ΡΠΉ Π²ΠΎΠ»ΠΎΠΊΠ½ΠΎΠΌΒ».
ΠΠΎΠ»Π°Π³Π°Ρ, ΡΡΠΎ Π³ΠΈΠ±ΡΠΈΠ΄Π½Π°Ρ ΡΠ΅Ρ
Π½ΠΎΠ»ΠΎΠ³ΠΈΡ ΠΌΠΎΠΆΠ΅Ρ Π±ΡΡΡ ΡΠ°Π·ΡΠ°Π±ΠΎΡΠ°Π½Π° Π΄Π»Ρ Π²ΡΡΠΎΠΊΠΎΡΠΊΠΎΡΠΎΡΡΠ½ΠΎΠ³ΠΎ ΡΠΎΡΠΌΠΎΠ²Π°Π½ΠΈΡ Π²ΡΡΠΎΠ²Π½Π΅Π½Π½ΡΡ
, Π°ΡΠΌΠΈΡΠΎΠ²Π°Π½Π½ΡΡ
Π½Π΅ΠΏΡΠ΅ΡΡΠ²Π½ΡΠΌΠΈ Π²ΠΎΠ»ΠΎΠΊΠ½Π°ΠΌΠΈ ΠΊΠΎΠΌΠΏΠΎΠ½Π΅Π½ΡΠΎΠ², ΠΡΠΊΠΎΠ²ΠΈΡ ΠΏΡΠΈΠ½ΡΠ»ΡΡ Π·Π° ΡΠ°Π±ΠΎΡΡ. ΠΠ½ ΡΠ»Π΅Π΄ΠΎΠ²Π°Π» ΠΊΠ»Π°ΡΡΠΈΡΠ΅ΡΠΊΠΎΠΌΡ ΡΠ°ΡΡΠΊΠ°Π·Ρ ΠΈΠ·ΠΎΠ±ΡΠ΅ΡΠ°ΡΠ΅Π»Ρ — Β«Π²ΠΎΠ·ΠΈΠ»ΡΡ Ρ Π½ΠΎΠ²ΡΠΌΠΈ ΡΠ΅Ρ
Π½ΠΎΠ»ΠΎΠ³ΠΈΡΠΌΠΈ Π² ΡΠ²ΠΎΠ΅ΠΌ Π³Π°ΡΠ°ΠΆΠ΅ Π² ΠΠ΅ΡΠΊΠ»ΠΈ, ΡΡΠ°Ρ ΠΠ°Π»ΠΈΡΠΎΡΠ½ΠΈΡΒ», ΠΊΠ°ΠΊ ΠΎΠΏΠΈΡΠ°Π» Π΅Π³ΠΎ ΠΆΡΡΠ½Π°Π» Forbes . ΠΠ½ ΠΎΠΆΠΈΠ΄Π°Π», ΡΡΠΎ ΡΡΠ° ΡΠ΅Ρ
Π½ΠΎΠ»ΠΎΠ³ΠΈΡ ΠΌΠΎΠΆΠ΅Ρ ΠΎΡΠΊΡΡΡΡ ΡΠ»ΡΠ·Ρ Π½Π° Π°Π²ΡΠΎΠΌΠΎΠ±ΠΈΠ»ΡΠ½ΠΎΠΌ ΠΈ ΠΏΠΎΡΡΠ΅Π±ΠΈΡΠ΅Π»ΡΡΠΊΠΎΠΌ ΡΡΠ½ΠΊΠ°Ρ
Π΄Π»Ρ ΡΠΈΡΠΎΠΊΠΎΠ³ΠΎ Π²Π½Π΅Π΄ΡΠ΅Π½ΠΈΡ ΡΠ»ΠΎΠΆΠ½ΡΡ
Π²ΡΡΠΎΠΊΠΎΠΏΡΠΎΠΈΠ·Π²ΠΎΠ΄ΠΈΡΠ΅Π»ΡΠ½ΡΡ
ΠΊΠΎΠΌΠΏΠΎΠ·ΠΈΡΠΎΠ².ΠΠΎΠ½Π΅ΡΠ½ΠΎ, Π΅ΡΠ΅ Π΄ΠΎ ΡΠΎΠ³ΠΎ, ΠΊΠ°ΠΊ ΠΎΠ½ ΡΡΡΠ΅Π΄ΠΈΠ» Arris Composites, ΠΡΠΊΠΎΠ²ΠΈΡ ΠΏΠΎΠ»ΡΡΠΈΠ» Π·Π°ΠΏΡΠΎΡ Π½Π° ΠΏΠΎΠΊΡΠΏΠΊΡ ΠΎΡ Π½Π΅ΠΈΠ·Π²Π΅ΡΡΠ½ΠΎΠ³ΠΎ ΠΏΡΠΎΠΈΠ·Π²ΠΎΠ΄ΠΈΡΠ΅Π»Ρ ΠΏΠΎΡΡΠ΅Π±ΠΈΡΠ΅Π»ΡΡΠΊΠΈΡ
ΡΠΎΠ²Π°ΡΠΎΠ². ΠΠ³ΠΎ ΡΠ°Π±ΠΎΡΠ° ΡΠ°ΠΊΠΆΠ΅ ΠΏΡΠΈΠ²Π»Π΅ΠΊΠ»Π° Π²Π½ΠΈΠΌΠ°Π½ΠΈΠ΅ Π±ΡΠ²ΡΠ΅Π³ΠΎ Π³Π΅Π½Π΅ΡΠ°Π»ΡΠ½ΠΎΠ³ΠΎ Π΄ΠΈΡΠ΅ΠΊΡΠΎΡΠ° Autodesk ΠΠ°ΡΠ»Π° ΠΠ°ΡΡΠ°, ΠΊΠΎΡΠΎΡΡΠΉ ΠΏΡΠ΅Π΄ΠΎΡΡΠ°Π²ΠΈΠ» Π½Π°ΡΠ°Π»ΡΠ½ΡΠΉ ΠΊΠ°ΠΏΠΈΡΠ°Π», ΠΊΠΎΠ½ΡΡΠ»ΡΡΠ°ΡΠΈΠΈ ΠΈ ΠΌΠ΅ΡΡΠΎ Π² ΡΠ²ΠΎΠ΅ΠΌ Π»ΠΈΡΠ½ΠΎΠΌ ΠΏΡΠΎΠΈΠ·Π²ΠΎΠ΄ΡΡΠ²Π΅Π½Π½ΠΎΠΌ ΡΠ΅Ρ
Π΅ Π² ΠΠ΅ΡΠΊΠ»ΠΈ.
ΠΡΠΈΠ²Π»Π΅ΠΊΠ°Ρ Π ΠΈΠ·Π°, Π° ΡΠ°ΠΊΠΆΠ΅ ΠΈΠ½ΠΆΠ΅Π½Π΅ΡΠ°-ΠΌΠ΅Ρ Π°Π½ΠΈΠΊΠ° ΠΈ Π²Π΅ΡΠ΅ΡΠ°Π½Π° ΡΡΠ°ΡΡΠ°ΠΏΠΎΠ² ΠΡΠΈΠΊΠ° ΠΡΠ²ΠΈΠ΄ΡΠΎΠ½Π° (Π½ΡΠ½Π΅ Π³Π»Π°Π²Π½ΡΠΉ ΠΈΠ½ΠΆΠ΅Π½Π΅Ρ ΠΈ ΡΠΎΡΡΡΠ΅Π΄ΠΈΡΠ΅Π»Ρ Arris), ΠΡΠΊΠΎΠ²ΠΈΡ ΠΏΡΠΎΠ΄ΠΎΠ»ΠΆΠ°Π» ΡΠ°Π·Π²ΠΈΠ²Π°ΡΡ ΡΠ΅Ρ Π½ΠΎΠ»ΠΎΠ³ΠΈΡ ΠΈ ΠΏΡΠΈΠ²Π»Π΅ΠΊΠ°ΡΡ Π²Π½ΠΈΠΌΠ°Π½ΠΈΠ΅ Π²ΡΠ΅ Π±ΠΎΠ»ΡΡΠ΅Π³ΠΎ ΡΠΈΡΠ»Π° ΠΏΡΠΎΠΈΠ·Π²ΠΎΠ΄ΠΈΡΠ΅Π»Π΅ΠΉ ΠΈ ΠΊΠ»ΠΈΠ΅Π½ΡΠΎΠ² ΠΊΠΎΠΌΠΏΠΎΠ·ΠΈΡΠΎΠ².Π ΠΏΡΠΎΡΠ΅ΡΡΠ΅ ΠΏΠΎΠ»ΡΡΠ΅Π½ΠΈΡ ΠΈΠ½Π²Π΅ΡΡΠΈΡΠΈΠΉ Π² ΡΠ°Π·ΠΌΠ΅ΡΠ΅ 10 ΠΌΠΈΠ»Π»ΠΈΠΎΠ½ΠΎΠ² Π΄ΠΎΠ»Π»Π°ΡΠΎΠ² ΠΊΠΎΠΌΠΏΠ°Π½ΠΈΡ ΠΈ Π΅Π΅ ΡΠ΅Ρ Π½ΠΎΠ»ΠΎΠ³ΠΈΠΈ Π±ΡΠ»ΠΈ ΠΏΡΠΎΠ²Π΅ΡΠ΅Π½Ρ Π±ΡΠ²ΡΠΈΠΌ Π³Π΅Π½Π΅ΡΠ°Π»ΡΠ½ΡΠΌ Π΄ΠΈΡΠ΅ΠΊΡΠΎΡΠΎΠΌ GE ΠΠΆΠ΅ΡΡΠΎΠΌ ΠΠΌΠΌΠ΅Π»ΡΡΠΎΠΌ, Π½Π° ΠΊΠΎΡΠΎΡΠΎΠ³ΠΎ ΠΏΡΠΎΠΈΠ·Π²Π΅Π»ΠΎ Π΄ΠΎΠ»ΠΆΠ½ΠΎΠ΅ Π²ΠΏΠ΅ΡΠ°ΡΠ»Π΅Π½ΠΈΠ΅. Β«Π’ΠΎ, ΡΡΠΎ ΠΌΡ ΡΠ΄Π΅Π»Π°Π»ΠΈ Π² Π°Π²ΡΠΎΠΌΠΎΠ±ΠΈΠ»Π΅ΡΡΡΠΎΠ΅Π½ΠΈΠΈ Π΄Π»Ρ Π·Π°ΠΌΠ΅Π½Ρ ΠΌΠ΅ΡΠ°Π»Π»Π°, Π½Π΅ ΡΠ²Π»ΡΡΡΠ΅Π³ΠΎΡΡ ΠΊΠΎΠ½ΡΡΡΡΠΊΡΠΈΠΎΠ½Π½ΡΠΌ, Π½Π° Π½Π΅Π΄ΠΎΡΠΎΠ³ΠΈΠ΅ ΠΈ Π»Π΅Π³ΠΊΠΈΠ΅ ΠΊΠΎΠΌΠΏΠΎΠ½Π΅Π½ΡΡ, ΠΏΠΎΠ»ΡΡΠ΅Π½Π½ΡΠ΅ Π»ΠΈΡΡΠ΅ΠΌ ΠΏΠΎΠ΄ Π΄Π°Π²Π»Π΅Π½ΠΈΠ΅ΠΌ Π² 1980-Ρ Π³ΠΎΠ΄Π°Ρ , ΡΠ΅ΠΏΠ΅ΡΡ Arris ΠΏΡΠΈΠΌΠ΅Π½ΠΈΠ»Π° ΠΈ Π΄Π»Ρ ΠΎΡΡΠ°Π»ΡΠ½ΠΎΠΉ ΡΠ°ΡΡΠΈ Π°Π²ΡΠΎΠΌΠΎΠ±ΠΈΠ»ΡΒ», — ΡΡΠΈΡΠ°Π΅Ρ ΠΎΠ½.
ΠΠ°ΠΊ ΡΡΠΎ ΡΠ°Π±ΠΎΡΠ°Π΅Ρ ΠΠ΄Π½ΠΈΠΌ ΠΈΠ· ΠΊΠ»ΡΡΠ΅Π²ΡΡ
ΠΌΠΎΠΌΠ΅Π½ΡΠΎΠ² Π°Π΄Π΄ΠΈΡΠΈΠ²Π½ΠΎΠ³ΠΎ ΡΠΎΡΠΌΠΎΠ²Π°Π½ΠΈΡ ΡΠ²Π»ΡΠ΅ΡΡΡ ΡΠΎ, ΡΡΠΎ ΠΎΠ½ΠΎ Π²Π΅ΡΡΠΈΠΊΠ°Π»ΡΠ½ΠΎ ΠΈΠ½ΡΠ΅Π³ΡΠΈΡΠΎΠ²Π°Π½ΠΎ ΠΎΡ ΡΠΎΡΠΊΠΈ, Π² ΠΊΠΎΡΠΎΡΠΎΠΉ ΡΡΡΡΠ΅ ΠΏΡΠΎΡ
ΠΎΠ΄ΠΈΡ ΡΠ΅ΡΠ΅Π· ΡΠΎΡΠΊΡ, Π² ΠΊΠΎΡΠΎΡΠΎΠΉ Π·Π°ΠΏΠΎΠ»Π½Π΅Π½Π½Π°Ρ ΡΠΎΡΠΌΠ° Π³ΠΎΡΠΎΠ²Π° Π΄Π»Ρ ΠΎΠ±ΡΠ°Π±ΠΎΡΠΊΠΈ, ΠΈ Π΄ΠΎ ΠΈΠ·Π²Π»Π΅ΡΠ΅Π½ΠΈΡ Π³ΠΎΡΠΎΠ²ΡΡ
Π΄Π΅ΡΠ°Π»Π΅ΠΉ, Π³ΠΎΡΠΎΠ²ΡΡ
ΠΊ ΠΈΡΠΏΠΎΠ»ΡΠ·ΠΎΠ²Π°Π½ΠΈΡ. ΠΡΠΎΡΠ΅ΡΡ Π½Π°ΡΠΈΠ½Π°Π΅ΡΡΡ Ρ ΡΡΡ
ΠΎΠ³ΠΎ ΠΆΠ³ΡΡΠ° ΡΠ³Π»Π΅ΡΠΎΠ΄Π½ΠΎΠ³ΠΎ Π²ΠΎΠ»ΠΎΠΊΠ½Π°, ΠΊΠΎΡΠΎΡΡΠΉ ΠΏΡΠ΅Π΄Π²Π°ΡΠΈΡΠ΅Π»ΡΠ½ΠΎ ΠΏΡΠΎΠΏΠΈΡΡΠ²Π°ΡΡ ΠΊΠ°ΠΊ Π»Π΅Π½ΡΡ, ΡΠ°ΠΊ ΠΈ ΠΆΠ³ΡΡ ΠΏΠΎΡΡΠ΅Π΄ΡΡΠ²ΠΎΠΌ ΠΏΡΠΎΡΠ΅ΡΡΠ° ΠΏΡΠΎΠΏΠΈΡΠΊΠΈ. ΠΠ΅Π½ΡΠ° ΠΏΡΠ΅ΠΏΡΠ΅Π³Π° ΠΌΠΎΠΆΠ΅Ρ Π±ΡΡΡ ΠΏΠ»ΠΎΡΠΊΠΎΠΉ ΠΈΠ»ΠΈ Π΅ΠΉ ΠΌΠΎΠΆΠ΅Ρ Π±ΡΡΡ ΠΏΡΠΈΠ΄Π°Π½Π° Π½Π΅ΠΎΠ±Ρ
ΠΎΠ΄ΠΈΠΌΠ°Ρ ΡΠΎΡΠΌΠ° ΠΏΡΠΎΡΠΈΠ»Ρ. Π ΠΈΠ· ΡΠΎΠΎΠ±ΡΠ°Π΅Ρ, ΡΡΠΎ Ρ Arris Π΅ΡΡΡ ΡΠΎΠ±ΡΡΠ²Π΅Π½Π½ΡΠ΅ Π²ΠΎΠ·ΠΌΠΎΠΆΠ½ΠΎΡΡΠΈ Π΄Π»Ρ ΠΏΡΠΎΠΈΠ·Π²ΠΎΠ΄ΡΡΠ²Π° Π»Π΅Π½ΡΡ ΠΈΠ· ΠΏΡΠ΅ΠΏΡΠ΅Π³Π°, ΠΈ ΡΡΠΎ Π±ΡΠ΄ΡΡΠΈΠ΅ ΡΠ°Π·ΡΠ°Π±ΠΎΡΠΊΠΈ ΠΏΠΎΠ·Π²ΠΎΠ»ΡΡ ΠΏΠΎΠ΄Π°Π²Π°ΡΡ Π»Π΅Π½ΡΡ (ΠΈ ΠΏΠ°ΠΊΠ»Ρ) Π½Π΅ΠΏΠΎΡΡΠ΅Π΄ΡΡΠ²Π΅Π½Π½ΠΎ Π½Π° ΡΠ»Π΅Π΄ΡΡΡΠΈΠΉ ΡΡΠ°ΠΏ ΠΏΡΠΎΠΈΠ·Π²ΠΎΠ΄ΡΡΠ²Π°. Π Π½Π°ΡΡΠΎΡΡΠ΅Π΅ Π²ΡΠ΅ΠΌΡ ΠΊΠΎΠΌΠΏΠ°Π½ΠΈΡ ΠΈΡΠΏΠΎΠ»ΡΠ·ΡΠ΅Ρ ΠΈΠΌΠ΅ΡΡΡΡΡΡ Π² ΠΏΡΠΎΠ΄Π°ΠΆΠ΅ ΠΏΡΠ΅ΠΏΡΠ΅Π³Π½ΡΡ Π»Π΅Π½ΡΡ ΡΠΈΡΠΈΠ½ΠΎΠΉ ΠΎΡ ΠΎΠ΄Π½ΠΎΠ³ΠΎ Π΄ΠΎ 24 Π΄ΡΠΉΠΌΠΎΠ² ΠΈ ΠΏΠΎΠ΄Π°Π΅Ρ Π΅Π΅ Π½Π° ΡΠ»Π΅Π΄ΡΡΡΡΡ ΡΡΡΠΏΠ΅Π½ΡΠΊΡ Ρ ΠΊΠ°ΡΡΡΠΊΠΈ.
ΠΠ°ΠΏΠ°ΡΠ΅Π½ΡΠΎΠ²Π°Π½Π½ΠΎΠ΅ ΡΠΎΠ±ΠΎΡΠΈΠ·ΠΈΡΠΎΠ²Π°Π½Π½ΠΎΠ΅ ΠΎΠ±ΠΎΡΡΠ΄ΠΎΠ²Π°Π½ΠΈΠ΅ Π·Π°ΡΠ΅ΠΌ ΡΠΎΡΠΌΠΈΡΡΠ΅Ρ, ΡΠ°Π·ΡΠ΅Π·Π°Π΅Ρ ΠΈ ΠΏΠΎΠΌΠ΅ΡΠ°Π΅Ρ Π΄Π΅ΡΠ°Π»ΠΈ ΠΏΡΠ΅ΠΏΡΠ΅Π³Π° Π² ΠΈΡ
ΠΎΠΊΠΎΠ½ΡΠ°ΡΠ΅Π»ΡΠ½ΡΠ΅ ΠΏΠΎΠ»ΠΎΠΆΠ΅Π½ΠΈΡ Π² ΠΏΠΎΠ»ΠΎΡΡΠΈ ΡΠΎΡΠΌΡ. ΠΠ°ΠΊ ΡΠΎΠ»ΡΠΊΠΎ ΠΏΡΠ΅Π΄ΠΏΠΈΡΠ°Π½Π½ΡΠΉ ΠΏΡΠ΅ΠΏΡΠ΅Π³ ΡΠ°Π·ΠΌΠ΅ΡΠ΅Π½, ΡΠΎΡΠΌΠ° Π·Π°ΠΊΡΡΠ²Π°Π΅ΡΡΡ ΠΈ ΠΏΡΠΈΠΊΠ»Π°Π΄ΡΠ²Π°Π΅Ρ ΡΠ΅ΠΏΠ»ΠΎ ΠΈ Π΄Π°Π²Π»Π΅Π½ΠΈΠ΅ ΠΊ ΠΊΠΎΠΌΠΏΠΎΠ·ΠΈΡΠ½ΡΠΌ ΠΌΠ°ΡΠ΅ΡΠΈΠ°Π»Π°ΠΌ Π΄Π»Ρ ΠΈΡ
ΡΠΏΠ»ΠΎΡΠ½Π΅Π½ΠΈΡ ΠΈ ΠΎΡΠ²Π΅ΡΠΆΠ΄Π΅Π½ΠΈΡ. Β«ΠΠ΅Ρ
Π°Π½ΠΈΠ·ΠΌ ΡΠ°Π·ΠΌΠ΅ΡΠ΅Π½ΠΈΡ ΠΌΠ°ΡΠ΅ΡΠΈΠ°Π»Π° ΠΎΡΠ»ΠΈΡΠ°Π΅ΡΡΡ ΠΎΡ ΠΌΠ΅Ρ
Π°Π½ΠΈΠ·ΠΌΠ°, ΠΈΡΠΏΠΎΠ»ΡΠ·ΡΠ΅ΠΌΠΎΠ³ΠΎ Π² ΠΏΡΠΎΡΠ΅ΡΡΠ°Ρ
Π°Π²ΡΠΎΠΌΠ°ΡΠΈΡΠ΅ΡΠΊΠΎΠΉ ΡΠΊΠ»Π°Π΄ΠΊΠΈ Π»Π΅Π½ΡΡ ΠΈ 3D-ΠΏΠ΅ΡΠ°ΡΠΈΒ», — ΠΎΡΠΌΠ΅ΡΠ°Π΅Ρ Π ΠΈΠ·. Β«ΠΡ ΡΠΎΡΠΌΠΈΡΡΠ΅ΠΌ ΠΏΡΠ΅ΠΏΡΠ΅Π³ΠΈ, Π° Π½Π΅ ΠΊΠΎΠ½ΡΠΎΠ»ΠΈΠ΄ΠΈΡΡΠ΅ΠΌ ΠΈ ΡΠΊΠ»Π΅ΠΈΠ²Π°Π΅ΠΌ ΠΈΡ
Π½Π° ΠΌΠ΅ΡΡΠ΅.Π ΡΠ΅Π·ΡΠ»ΡΡΠ°ΡΠ΅ Π½Π°Ρ ΠΏΡΠΎΡΠ΅ΡΡ ΠΏΡΠ΅Π΄Π²Π°ΡΠΈΡΠ΅Π»ΡΠ½ΠΎΠ³ΠΎ ΡΠΎΡΠΌΠΎΠ²Π°Π½ΠΈΡ ΠΌΠΎΠΆΠ΅Ρ Π²ΡΠΏΠΎΠ»Π½ΡΡΡΡΡ Ρ Π½Π΅Π²Π΅ΡΠΎΡΡΠ½ΠΎΠΉ ΡΠΊΠΎΡΠΎΡΡΡΡ Β».
ΠΠ΄Π½ΠΎ ΠΈΠ· ΠΎΡΠ½ΠΎΠ²Π½ΡΡ ΠΏΡΠ΅ΠΈΠΌΡΡΠ΅ΡΡΠ² 3D-ΠΏΠ΅ΡΠ°ΡΠΈ — Π²ΠΎΠ·ΠΌΠΎΠΆΠ½ΠΎΡΡΡ ΡΠ°Π·ΠΌΠ΅ΡΠ°ΡΡ Π²ΠΎΠ»ΠΎΠΊΠ½Π° Π² Π»ΡΠ±ΠΎΠΉ ΠΎΡΠΈΠ΅Π½ΡΠ°ΡΠΈΠΈ Π² ΡΡΠ΅Ρ ΠΌΠ΅ΡΠ½ΠΎΠΌ ΠΏΡΠΎΡΡΡΠ°Π½ΡΡΠ²Π΅ — ΡΠ°ΠΊΠΆΠ΅ Π²Π΅ΡΠ½ΠΎ ΠΈ Π΄Π»Ρ Π°Π΄Π΄ΠΈΡΠΈΠ²Π½ΠΎΠ³ΠΎ ΡΠΎΡΠΌΠΎΠ²Π°Π½ΠΈΡ. Β«ΠΡ Π²ΠΏΠ΅ΡΠ²ΡΠ΅ ΠΎΠ±ΡΠ΅Π΄ΠΈΠ½ΡΠ΅ΠΌ ΠΏΡΠ΅ΠΈΠΌΡΡΠ΅ΡΡΠ²Π° ΡΡΠ΅Ρ ΡΠ°Π·ΡΠΎΠ·Π½Π΅Π½Π½ΡΡ ΡΠ΅Ρ Π½ΠΎΠ»ΠΎΠ³ΠΈΠΉ, — ΠΎΠ±ΡΡΡΠ½ΡΠ΅Ρ Π ΠΈΠ·, — ΡΠΈΡΠΎΠΊΠΈΠ΅ Π²ΠΎΠ·ΠΌΠΎΠΆΠ½ΠΎΡΡΠΈ 3D-ΠΏΠ΅ΡΠ°ΡΠΈ, Ρ Π°ΡΠ°ΠΊΡΠ΅ΡΠΈΡΡΠΈΠΊΠΈ Π°ΡΡΠΎΠΊΠΎΡΠΌΠΈΡΠ΅ΡΠΊΠΈΡ ΠΊΠΎΠΌΠΏΠΎΠ·ΠΈΡΠΎΠ², Π° ΡΠ°ΠΊΠΆΠ΅ ΡΡΠΎΠΈΠΌΠΎΡΡΡ ΠΈ ΡΠΊΠΎΡΠΎΡΡΡ ΡΠΎΡΠΌΠΎΠ²Π°Π½ΠΈΡΒ».
ΠΡΠΊΠΎΠ²ΠΈΡ ΠΎΠΏΠΈΡΡΠ²Π°Π΅Ρ Π·Π°Π΄Π°ΡΡ, ΠΊΠΎΡΠΎΡΡΡ ΡΠ΅ΡΠ°Π΅Ρ Π°Π΄Π΄ΠΈΡΠΈΠ²Π½ΠΎΠ΅ ΡΠΎΡΠΌΠΎΠ²Π°Π½ΠΈΠ΅, ΠΊΠ°ΠΊ Β«ΠΌΠ°ΡΡΡΠ°Π±ΠΈΡΠΎΠ²Π°Π½ΠΈΠ΅ Π½ΠΎΠ²ΡΡ
Π΄Π΅ΡΠ°Π»Π΅ΠΉ Π±Π΅Π· Π·Π°ΡΡΠ°Ρ Π½Π° ΡΡΠ°Π΄ΠΈΡΠΈΠΎΠ½Π½ΡΠ΅ ΠΊΠΎΠΌΠΏΠΎΠ·ΠΈΡΡ Ρ Π²ΡΡΠΎΠ²Π½Π΅Π½Π½ΡΠΌΠΈ Π²ΠΎΠ»ΠΎΠΊΠ½Π°ΠΌΠΈ.Β«ΠΡΠ° ΡΠ΅Ρ
Π½ΠΎΠ»ΠΎΠ³ΠΈΡ, — ΡΡΠ²Π΅ΡΠΆΠ΄Π°Π΅Ρ ΠΎΠ½, — ΡΠΎΠ·Π΄Π°Π΅Ρ ΡΡΡΡΠΊΡΡΡΡ, Π² ΠΊΠΎΡΠΎΡΡΡ
Β« Π²Π΅ΡΡ ΠΎΠ±ΡΠ΅ΠΌ Π²ΠΎΠ»ΠΎΠΊΠ½Π° ΠΏΡΠΎΡ
ΠΎΠ΄ΠΈΡ ΠΏΠΎ ΠΆΠ΅Π»Π°Π΅ΠΌΡΠΌ ΠΏΡΡΡΠΌ ΠΌΠ΅Ρ
Π°Π½ΠΈΡΠ΅ΡΠΊΠΎΠΉ Π½Π°Π³ΡΡΠ·ΠΊΠΈ ΠΈ ΡΡΠΈΠ»ΠΈΠ²Π°Π΅ΡΡΡ ΡΠ°ΠΌ, Π³Π΄Π΅ ΡΡΠ΅Π±ΡΡΡΡΡ ΡΠ²ΠΎΠΉΡΡΠ²Π° Β». ΠΡ ΠΌΠΎΠΆΠ΅ΠΌ Π²ΡΡΠΎΠ²Π½ΡΡΡ Π²ΠΎΠ»ΠΎΠΊΠ½Π° ΡΠ°ΠΊ, ΠΊΠ°ΠΊ Π½ΠΈΠΊΡΠΎ Π΄ΡΡΠ³ΠΎΠΉ Π½Π΅ ΡΠΌΠΎΠΆΠ΅Ρ ΠΏΡΠΈ Π±ΠΎΠ»ΡΡΠΈΡ
ΠΎΠ±ΡΠ΅ΠΌΠ°Ρ
ΠΏΡΠΎΠΈΠ·Π²ΠΎΠ΄ΡΡΠ²Π° Β». Π‘ΡΠ΄Π° Π²Ρ
ΠΎΠ΄ΡΡ Π½Π΅ΠΊΠΎΡΠΎΡΡΠ΅ ΠΈΠ· Π½Π΅Π΄Π°Π²Π½ΠΎ ΡΠ°Π·ΡΠ°Π±ΠΎΡΠ°Π½Π½ΡΡ
ΠΌΠ΅ΡΠΎΠ΄ΠΎΠ² Π±ΡΡΡΡΠΎΠ³ΠΎ ΠΏΡΠ΅Π΄Π²Π°ΡΠΈΡΠ΅Π»ΡΠ½ΠΎΠ³ΠΎ ΡΠΎΡΠΌΠΎΠ²Π°Π½ΠΈΡ, ΠΊΠΎΡΠΎΡΡΠ΅, ΠΏΠΎ Π΅Π³ΠΎ ΡΠ»ΠΎΠ²Π°ΠΌ, ΡΡΠ΅Π±ΡΡΡ Π±ΠΎΠ»ΡΡΠ΅ ΠΊΠ°ΠΏΠΈΡΠ°Π»ΡΠ½ΠΎΠ³ΠΎ ΠΎΠ±ΠΎΡΡΠ΄ΠΎΠ²Π°Π½ΠΈΡ, ΡΠ΅Π·ΠΊΠΈ ΠΈ ΠΊΠΎΠ½ΡΠΎΠ»ΠΈΠ΄Π°ΡΠΈΠΈ, ΡΠ΅ΠΌ Π°Π΄Π΄ΠΈΡΠΈΠ²Π½ΠΎΠ΅ ΡΠΎΡΠΌΠΎΠ²Π°Π½ΠΈΠ΅, ΠΈ Π½Π΅ ΠΎΠ±Π΅ΡΠΏΠ΅ΡΠΈΠ²Π°ΡΡ ΡΠ°ΠΊΠΎΠΉ ΡΡΠΎΠ²Π΅Π½Ρ Π²ΡΡΠ°Π²Π½ΠΈΠ²Π°Π½ΠΈΡ Π²ΠΎΠ»ΠΎΠΊΠΎΠ½, ΠΊΠ°ΠΊ ΠΏΡΠΎΡΠ΅ΡΡ ΠΡΡΠΈΡΠ°.
Π ΠΈΠ· ΠΏΡΠΎΠ΄ΠΎΠ»ΠΆΠ°Π΅Ρ: Β«Π€ΠΎΡΠΌΠΈΡΡΡ ΡΠΎΡΠΌΡ Π½Π° Π½Π°ΡΠ΅ΠΌ Π°Π΄Π΄ΠΈΡΠΈΠ²Π½ΠΎΠΌ ΡΡΠ°ΠΏΠ΅, ΠΌΡ ΠΏΡΠΎΠΊΠ»Π°Π΄ΡΠ²Π°Π΅ΠΌ ΠΏΡΡΠΈ Π²ΠΎΠ»ΠΎΠΊΠ½Π° Π²ΠΎΠΊΡΡΠ³ ΡΠ»Π΅ΠΌΠ΅Π½ΡΠΎΠ², Π²ΠΌΠ΅ΡΡΠΎ ΡΠΎΠ³ΠΎ, ΡΡΠΎΠ±Ρ Π²ΡΡΠ΅Π·Π°ΡΡ ΠΈΡ , ΡΡΠΎΠ±Ρ ΠΎΠ½ΠΈ ΡΠΎΠΎΡΠ²Π΅ΡΡΡΠ²ΠΎΠ²Π°Π»ΠΈ ΡΡΠΈΠΌ ΡΠ»Π΅ΠΌΠ΅Π½ΡΠ°ΠΌΒ». ΠΠ°ΠΆΠ½ΠΎ ΠΎΡΠΌΠ΅ΡΠΈΡΡ, ΡΡΠΎ Π·Π° ΡΡΠ΅Ρ ΠΈΡΠΊΠ»ΡΡΠ΅Π½ΠΈΡ ΡΡΠΎΠ³ΠΎ ΡΡΠ°ΠΏΠ° ΡΠ΅Π·Π°Π½ΠΈΡ Π°Π΄Π΄ΠΈΡΠΈΠ²Π½ΠΎΠ΅ ΡΠΎΡΠΌΠΎΠ²Π°Π½ΠΈΠ΅ ΠΏΡΠΎΠΈΠ·Π²ΠΎΠ΄ΠΈΡ ΠΌΠ΅Π½ΡΡΠ΅ ΠΎΡΡ ΠΎΠ΄ΠΎΠ², ΡΠ΅ΠΌ ΡΡΠΈ Π΄ΡΡΠ³ΠΈΠ΅ ΠΏΡΠΎΡΠ΅ΡΡΡ, ΡΡΠΎ Π·Π½Π°ΡΠΈΡΠ΅Π»ΡΠ½ΠΎ ΡΠΏΠΎΡΠΎΠ±ΡΡΠ²ΡΠ΅Ρ ΡΠΊΠΎΠ½ΠΎΠΌΠΈΠΈ Π·Π° ΡΡΠ΅Ρ ΠΌΠ°ΡΡΡΠ°Π±ΠΎΠ² ΠΏΡΠΎΠΈΠ·Π²ΠΎΠ΄ΡΡΠ²Π° ΠΏΡΠΈ ΠΊΡΡΠΏΠ½ΠΎΡΠ΅ΡΠΈΠΉΠ½ΠΎΠΌ ΠΏΡΠΎΠΈΠ·Π²ΠΎΠ΄ΡΡΠ²Π΅.
ΠΡΠΊΠΎΠ²ΠΈΡ ΠΈ Π ΠΈΠ· Π½Π΅ ΡΠ΅ΡΠ°ΡΡΡΡ ΡΠΊΠ°Π·Π°ΡΡ, Π½Π°ΡΠΊΠΎΠ»ΡΠΊΠΎ Π±ΠΎΠ»Π΅Π΅ Π±ΡΡΡΡΠΎΠ΅ Π°Π΄Π΄ΠΈΡΠΈΠ²Π½ΠΎΠ΅ ΡΠΎΡΠΌΠΎΠ²Π°Π½ΠΈΠ΅ ΠΏΠΎ ΡΡΠ°Π²Π½Π΅Π½ΠΈΡ Ρ ΡΡΠ°Π΄ΠΈΡΠΈΠΎΠ½Π½ΡΠΌΠΈ ΡΠ΅Ρ
Π½ΠΎΠ»ΠΎΠ³ΠΈΡΠΌΠΈ ΠΈΠ·Π³ΠΎΡΠΎΠ²Π»Π΅Π½ΠΈΡ, Π½ΠΎ ΠΎΠ½ΠΈ ΠΎΠΆΠΈΠ΄Π°ΡΡ, ΡΡΠΎ ΡΡΠ° ΡΠ΅Ρ
Π½ΠΎΠ»ΠΎΠ³ΠΈΡ ΠΎΠ±Π΅ΡΠΏΠ΅ΡΠΈΡ Π΄ΠΎΡΡΠ°Π²ΠΊΡ ΠΊΠΎΠΌΠΏΠΎΠ·ΠΈΡΠ½ΡΡ
ΠΊΠΎΠΌΠΏΠΎΠ½Π΅Π½ΡΠΎΠ² ΠΏΠΎ ΡΠ΅Π½Π΅, ΠΊΠΎΡΠΎΡΠ°Ρ Π½Π° ΠΏΠΎΡΡΠ΄ΠΎΠΊ ΠΌΠ΅Π½ΡΡΠ΅, ΡΠ΅ΠΌ ΠΏΡΠΈ ΡΡΡΠ΅ΡΡΠ²ΡΡΡΠ΅ΠΌ ΠΌΠ΅ΡΠΎΠ΄Π΅ ΠΏΡΠΎΠΈΠ·Π²ΠΎΠ΄ΡΡΠ²Π°. Π ΠΈΠ· ΠΎΡΠΌΠ΅ΡΠ°Π΅Ρ, ΡΡΠΎ Π²ΡΠ΅ΠΌΡ ΡΠΎΡΠΌΠΎΠ²Π°Π½ΠΈΡ ΡΠ²Π»ΡΠ΅ΡΡΡ Π»ΠΈΠΌΠΈΡΠΈΡΡΡΡΠΈΠΌ ΡΡΠ°ΠΏΠΎΠΌ Π² ΠΈΡ
ΠΏΡΠΎΡΠ΅ΡΡΠ΅, Π° Π½Π΅ ΠΏΡΠΎΡΡΠΎΡ. Β«ΠΡ Π½Π°ΡΡΡΠ°ΠΈΠ²Π°Π΅ΠΌ ΠΏΠΎΡΡΠΈΡ Π΄ΠΎΠ±Π°Π²ΠΊΠΈ Π΄Π»Ρ Π΄ΠΎΡΡΠ°Π²ΠΊΠΈ ΡΠΊΠ»Π°Π΄ΠΊΠΈ Π² ΠΎΠΏΡΠΈΠΌΠ°Π»ΡΠ½ΡΠΉ ΠΌΠΎΠΌΠ΅Π½Ρ Π²ΡΠ΅ΠΌΠ΅Π½ΠΈ ΡΠΈΠΊΠ»Π° ΠΏΡΠ΅ΡΡ-ΡΠΎΡΠΌΡΒ», — Π΄ΠΎΠ±Π°Π²Π»ΡΠ΅Ρ ΠΎΠ½.
ΠΡΠΊΠΎΠ²ΠΈΡ ΠΎΡΠΌΠ΅ΡΠ°Π΅Ρ, ΡΡΠΎ ΠΏΡΠΈ ΠΌΠ°ΡΡΠΎΠ²ΠΎΠΌ ΠΏΡΠΈΠΌΠ΅Π½Π΅Π½ΠΈΠΈ Π²ΡΡΠΎΠ²Π½Π΅Π½Π½ΡΡ Π²ΡΡΠΎΠΊΠΎΠΏΡΠΎΠΈΠ·Π²ΠΎΠ΄ΠΈΡΠ΅Π»ΡΠ½ΡΡ ΠΊΠΎΠΌΠΏΠΎΠ·ΠΈΡΠΎΠ² Β«Π΄Π΅Π»ΠΎ Π½Π΅ Π² ΡΡΠΎΠΈΠΌΠΎΡΡΠΈ ΠΌΠ°ΡΠ΅ΡΠΈΠ°Π»Π°; ΡΡΠΎ ΡΠ΅Ρ Π½ΠΎΠ»ΠΎΠ³ΠΈΡΠ΅ΡΠΊΠΈΠ΅ Π·Π°ΡΡΠ°ΡΡ Β», ΠΏΠΎΡΡΠΎΠΌΡ ΡΠ°ΠΊΠΈΠ΅ ΠΊΠΎΠΌΠΏΠΎΠ·ΠΈΡΠ½ΡΠ΅ ΠΌΠ°ΡΠ΅ΡΠΈΠ°Π»Ρ Π½Π΅ ΠΏΡΠΈΠ½ΠΈΠΌΠ°ΡΡΡΡ Π²ΠΎ Π²Π½ΠΈΠΌΠ°Π½ΠΈΠ΅. ΠΠΆΠΈΠ΄Π°Π΅ΡΡΡ, ΡΡΠΎ ΠΊΠ°ΠΏΠΈΡΠ°Π»ΡΠ½ΡΠ΅ Π·Π°ΡΡΠ°ΡΡ Π½Π° Π΅Π΄ΠΈΠ½ΠΈΡΡ Π±ΡΠ΄ΡΡ ΡΡΠ΅Π·Π²ΡΡΠ°ΠΉΠ½ΠΎ Π½ΠΈΠ·ΠΊΠΈΠΌΠΈ Π΄Π»Ρ ΡΠΎΠ²ΠΌΠ΅ΡΠ΅Π½Π½ΡΡ ΠΊΠΎΠΌΠΏΠΎΠ·ΠΈΡΠ½ΡΡ ΡΡΡΡΠΊΡΡΡ, ΠΈΠ·Π³ΠΎΡΠΎΠ²Π»Π΅Π½Π½ΡΡ Ρ ΠΈΡΠΏΠΎΠ»ΡΠ·ΠΎΠ²Π°Π½ΠΈΠ΅ΠΌ Π°Π΄Π΄ΠΈΡΠΈΠ²Π½ΠΎΠ³ΠΎ ΡΠΎΡΠΌΠΎΠ²Π°Π½ΠΈΡ — Π΄ΠΎΡΡΠ°ΡΠΎΡΠ½ΠΎ Π½ΠΈΠ·ΠΊΠΈΠΌΠΈ, ΡΡΠΎΠ±Ρ ΡΠ΄Π΅Π»Π°ΡΡ ΡΡΠΎΠΈΠΌΠΎΡΡΡ Π΄Π΅ΡΠ°Π»Π΅ΠΉ ΠΊΠΎΠ½ΠΊΡΡΠ΅Π½ΡΠΎΡΠΏΠΎΡΠΎΠ±Π½ΡΠΌΠΈ ΠΏΠΎ ΡΡΠ°Π²Π½Π΅Π½ΠΈΡ Ρ Π΄Π΅ΡΠ°Π»ΡΠΌΠΈ, ΠΊΠΎΡΠΎΡΡΠ΅ ΠΎΠ½ΠΈ Π±ΡΠ΄ΡΡ Π·Π°ΠΌΠ΅Π½ΡΡΡ, ΠΈ ΠΏΡΠ΅Π΄Π»ΠΎΠΆΠΈΡΡ Π³ΠΎΡΠ°Π·Π΄ΠΎ Π±ΠΎΠ»Π΅Π΅ Π²ΡΡΠΎΠΊΠΈΠ΅ Ρ Π°ΡΠ°ΠΊΡΠ΅ΡΠΈΡΡΠΈΠΊΠΈ, ΡΠ΅ΠΌ ΡΡΠΈ Π΄Π΅ΡΠ°Π»ΠΈ.
Π’Π΅Ρ Π½ΠΎΠ»ΠΎΠ³ΠΈΡ ΡΠΎΡΠ°ΡΠΈΠΎΠ½Π½ΠΎΠ³ΠΎ ΡΠΎΡΠΌΠΎΠ²Π°Π½ΠΈΡ — 1-Π΅ ΠΈΠ·Π΄Π°Π½ΠΈΠ΅
1.0 ΠΠ²Π΅Π΄Π΅Π½ΠΈΠ΅
1.1 ΠΡΠΎΡΠ΅ΡΡ
1.2 ΠΠ΅ΡΠ²ΡΠ΅ Π΄Π½ΠΈ
1.3 ΠΠ°ΡΠ΅ΡΠΈΠ°Π»Ρ
1. 4 ΠΡΠ΅ΠΈΠΌΡΡΠ΅ΡΡΠ²Π° ΠΈ Π½Π΅Π΄ΠΎΡΡΠ°ΡΠΊΠΈ
1.5 ΠΠ±ΡΠΈΠ΅ ΠΎΡΠ½ΠΎΡΠ΅Π½ΠΈΡ ΠΌΠ΅ΠΆΠ΄Ρ ΡΡΠ»ΠΎΠ²ΠΈΡΠΌΠΈ ΠΎΠ±ΡΠ°Π±ΠΎΡΠΊΠΈ ΠΈ ΡΠ²ΠΎΠΉΡΡΠ²Π°ΠΌΠΈ
2. ΠΠΎΠ»ΠΈΠΌΠ΅ΡΡ Π΄Π»Ρ ΡΠΎΡΠ°ΡΠΈΠΎΠ½Π½ΠΎΠ³ΠΎ ΡΠΎΡΠΌΠΎΠ²Π°Π½ΠΈΡ.
2.0 ΠΠ²Π΅Π΄Π΅Π½ΠΈΠ΅
2.1 ΠΠ±ΡΠΈΠ΅ Ρ
Π°ΡΠ°ΠΊΡΠ΅ΡΠΈΡΡΠΈΠΊΠΈ ΠΏΠΎΠ»ΠΈΠΌΠ΅ΡΠΎΠ²
2.2 ΠΠΎΠ»ΠΈΠΌΠ΅ΡΡ ΠΊΠ°ΠΊ ΠΏΠΎΡΠΎΡΠΊΠΈ ΠΈ ΠΆΠΈΠ΄ΠΊΠΎΡΡΠΈ
2.3 Π’ΠΈΠΏΡ ΠΏΠΎΠ»ΠΈΡΡΠΈΠ»Π΅Π½Π°
2.4 ΠΠΎΠ»ΠΈΠΏΡΠΎΠΏΠΈΠ»Π΅Π½
2.5 ΠΠΠ₯, ΠΏΠ»Π°ΡΡΠΈΠ·ΠΎΠ»ΠΈ, Π΄ΡΠΈΡΠΎΠ»ΠΈ ΠΈ ΠΏΠΎΡΠΎΡΠΊΠΎΠ²ΡΠ΅ ΡΠ»Π°ΡΡΠΈΡΠ½ΡΠ΅ ΠΊΠΎΠΌΠΏΠ°ΡΠ½Π΄Ρ
2.6 Π½Π΅ΠΉΠ»ΠΎΠ½
2.7 ΠΡΡΠ³ΠΈΠ΅ ΠΏΠΎΠ»ΠΈΠΌΠ΅ΡΡ
2.8 ΠΠΈΠ΄ΠΊΠΈΠ΅ ΠΏΠΎΠ»ΠΈΠΌΠ΅ΡΡ
2.9 ΠΡΠ΅Π½ΠΊΠ° Π²Ρ
ΠΎΠ΄ΡΡΠΈΡ
ΠΌΠ°ΡΠ΅ΡΠΈΠ°Π»ΠΎΠ²
2.10 ΠΡΠΎΡΠΎΠΊΠΎΠ»Ρ ΠΈΡΠΏΡΡΠ°Π½ΠΈΠΉ ΠΏΡΠΎΠ΄ΡΠΊΡΠ° ΠΈ ΡΠ²ΡΠ·Ρ Ρ Ρ
Π°ΡΠ°ΠΊΡΠ΅ΡΠΈΡΡΠΈΠΊΠ°ΠΌΠΈ ΠΏΠΎΠ»ΠΈΠΌΠ΅ΡΠ°
2.11 ΠΠ΅Π»Π°ΡΠ΅Π»ΡΠ½ΡΠ΅ Ρ
Π°ΡΠ°ΠΊΡΠ΅ΡΠΈΡΡΠΈΠΊΠΈ ΡΠΌΠΎΠ»Ρ Π΄Π»Ρ ΡΠΎΡΠ°ΡΠΈΠΎΠ½Π½ΠΎΠ³ΠΎ ΡΠΎΡΠΌΠΎΠ²Π°Π½ΠΈΡ
3. Π¨Π»ΠΈΡΠΎΠ²ΠΊΠ° ΠΈ ΠΎΠΊΡΠ°ΡΠΊΠ°
3.0 ΠΠ²Π΅Π΄Π΅Π½ΠΈΠ΅
3.1 ΠΠ±ΡΠΈΠ΅ Π²ΠΎΠΏΡΠΎΡΡ, ΠΊΠ°ΡΠ°ΡΡΠΈΠ΅ΡΡ ΡΠ»ΠΈΡΠΎΠ²Π°Π½ΠΈΡ
3.2 Π Π°ΡΠΏΡΠ΅Π΄Π΅Π»Π΅Π½ΠΈΠ΅ ΡΠ°ΡΡΠΈΡ ΠΏΠΎ ΡΠ°Π·ΠΌΠ΅ΡΠ°ΠΌ
3.3 Π€ΠΎΡΠΌΠ° ΡΠ°ΡΡΠΈΡ
3.4 Π‘ΡΡ
ΠΎΠΉ ΠΏΠΎΡΠΎΠΊ
3.5 ΠΠ°ΡΡΠΏΠ½Π°Ρ ΠΏΠ»ΠΎΡΠ½ΠΎΡΡΡ
3.6 Π€Π°ΠΊΡΠΎΡΡ, Π²Π»ΠΈΡΡΡΠΈΠ΅ Π½Π° ΠΊΠ°ΡΠ΅ΡΡΠ²ΠΎ ΠΏΠΎΡΠΎΡΠΊΠ°
3.7 ΠΠ°ΡΡΠ°ΡΡ Π½Π° ΡΠ»ΠΈΡΠΎΠ²Π°Π½ΠΈΠ΅
3.
8 ΠΠΈΠΊΡΠΎΠΏΠ΅Π»Π»Π΅ΡΠΈΡΠΎΠ²Π°Π½ΠΈΠ΅
3.9 ΠΠΎΠ»ΠΈΠ²ΠΈΠ½ΠΈΠ»Ρ
Π»ΠΎΡΠΈΠ΄
3.10 ΠΠΊΡΠ°ΡΠΊΠ° ΠΏΠ»Π°ΡΡΠΌΠ°ΡΡ Π΄Π»Ρ ΡΠΎΡΠ°ΡΠΈΠΎΠ½Π½ΠΎΠ³ΠΎ ΡΠΎΡΠΌΠΎΠ²Π°Π½ΠΈΡ
4. ΠΠ°ΡΠΈΠ½Ρ ΡΠΎΡΠ°ΡΠΈΠΎΠ½Π½ΠΎΠ³ΠΎ ΡΠΎΡΠΌΠΎΠ²Π°Π½ΠΈΡ.
4.0 ΠΠ²Π΅Π΄Π΅Π½ΠΈΠ΅
4.1 Π’ΠΈΠΏΡ ΡΠΎΡΠ°ΡΠΈΠΎΠ½Π½ΡΡ
ΡΠΎΡΠΌΠΎΠ²ΠΎΡΠ½ΡΡ
ΠΌΠ°ΡΠΈΠ½
4.2 Π‘ΠΎΠΎΠ±ΡΠ°ΠΆΠ΅Π½ΠΈΡ ΠΏΠΎ ΠΊΠΎΠ½ΡΡΡΡΠΊΡΠΈΠΈ ΠΌΠ°ΡΠΈΠ½Ρ
4.3 ΠΡΡ
ΠΎΠ²ΠΊΠ°
4.4 ΠΡ
Π»Π°ΠΆΠ΄Π΅Π½ΠΈΠ΅
4.5 ΠΠΎΠ½ΠΈΡΠΎΡΡ ΠΏΡΠΎΡΠ΅ΡΡΠΎΠ²
4.6 Π‘Π΅ΡΠ²ΠΈΡΠ½ΠΎΠ΅ ΠΎΠ±ΡΠ»ΡΠΆΠΈΠ²Π°Π½ΠΈΠ΅
4.7 Π Π°ΡΡΠΈΡΠ΅Π½Π½ΡΠΉ Π΄ΠΈΠ·Π°ΠΉΠ½ ΠΌΠ°ΡΠΈΠ½Ρ
5. ΠΠΈΠ·Π°ΠΉΠ½ ΠΏΡΠ΅ΡΡ-ΡΠΎΡΠΌ
5.0 ΠΠ²Π΅Π΄Π΅Π½ΠΈΠ΅
5.1 ΠΠ°ΡΠ΅ΡΠΈΠ°Π»Ρ ΠΏΡΠ΅ΡΡ-ΡΠΎΡΠΌΡ
5.2 ΠΠ΅Ρ
Π°Π½ΠΈΡΠ΅ΡΠΊΠΈΠ΅ ΠΈ ΡΠ΅ΡΠΌΠΈΡΠ΅ΡΠΊΠΈΠ΅ Ρ
Π°ΡΠ°ΠΊΡΠ΅ΡΠΈΡΡΠΈΠΊΠΈ ΠΌΠ°ΡΠ΅ΡΠΈΠ°Π»ΠΎΠ² ΠΏΡΠ΅ΡΡ-ΡΠΎΡΠΌΡ
5.3 ΠΠΈΠ·Π°ΠΉΠ½ ΠΏΡΠ΅ΡΡ-ΡΠΎΡΠΌΡ
5.4 Π Π°ΡΡΠ΅Ρ Π²Π΅ΡΠ° Π·Π°ΡΡΠ΄Π°
5.5 ΠΠ΅Π½ΡΠΈΠ»ΡΡΠΈΡ
5.6 ΠΠ±ΡΠ°Π±ΠΎΡΠΊΠ° ΠΏΠΎΠ²Π΅ΡΡ
Π½ΠΎΡΡΠΈ ΠΏΡΠ΅ΡΡ-ΡΠΎΡΠΌΡ
5.7 ΠΡΡΠ°Π»ΠΊΠΈΠ²Π°ΡΠ΅Π»ΠΈ ΠΈΠ· ΠΏΡΠ΅ΡΡ-ΡΠΎΡΠΌΡ
6. ΠΠ±ΡΠ°Π±ΠΎΡΠΊΠ°
6.0 ΠΠ²Π΅Π΄Π΅Π½ΠΈΠ΅ Π² ΠΎΡΠΎΠΏΠ»Π΅Π½ΠΈΠ΅
6.1 ΠΠ±ΡΠ°Ρ Π°Π½Π°ΡΠΎΠΌΠΈΡ ΡΠΈΠΊΠ»Π° ΡΠΎΡΠ°ΡΠΈΠΎΠ½Π½ΠΎΠ³ΠΎ ΡΠΎΡΠΌΠΎΠ²Π°Π½ΠΈΡ
6.2 ΠΠ±ΡΠ΅Π΅ ΠΎΠΏΠΈΡΠ°Π½ΠΈΠ΅ ΠΏΡΠΎΡΠ΅ΡΡΠ°
6.3 ΠΠΎΠ²Π΅Π΄Π΅Π½ΠΈΠ΅ ΠΏΠΎΡΠΎΡΠΊΠ°
6.4 Π₯Π°ΡΠ°ΠΊΡΠ΅ΡΠΈΡΡΠΈΠΊΠΈ ΠΏΠΎΡΠΎΠΊΠ° ΠΏΠΎΡΠΎΡΠΊΠ°
6.
5 Π Π΅ΠΎΠ»ΠΎΠ³ΠΈΡ ΠΏΠΎΡΠΎΠΊΠ° ΠΏΠΎΡΠΎΡΠΊΠ°
6.6 ΠΠΎΠ½ΡΠ΅ΠΏΡΠΈΠΈ ΡΠ΅ΠΏΠ»ΠΎΠΏΠ΅ΡΠ΅Π΄Π°ΡΠΈ ΠΏΡΠΈΠΌΠ΅Π½ΠΈΡΠ΅Π»ΡΠ½ΠΎ ΠΊ ΡΠΎΡΠ°ΡΠΈΠΎΠ½Π½ΠΎΠΌΡ ΡΠΎΡΠΌΠΎΠ²Π°Π½ΠΈΡ
6.7 ΠΠ°Π³ΡΠ΅Π² ΡΠΎΡΠΌΡ
6.8 ΠΠ°Π³ΡΠ΅Π²Π°ΡΠ΅Π»ΡΠ½ΡΠΉ ΠΏΠΎΡΠΎΡΠΎΠΊ
6.9 Π’Π΅ΠΌΠΏΠ΅ΡΠ°ΡΡΡΠ° Π»ΠΈΠΏΠΊΠΎΡΡΠΈ
6.10 ΠΠ°Π³ΡΠ΅Π² Π²ΠΎΠ·Π΄ΡΡ
Π° Π² ΠΏΠΎΠ»ΠΎΡΡΠΈ ΠΏΡΠ΅ΡΡ-ΡΠΎΡΠΌΡ ΠΏΠ΅ΡΠ΅Π΄ Π°Π΄Π³Π΅Π·ΠΈΠ΅ΠΉ ΠΏΠΎΡΠΎΡΠΊΠ° ΠΊ ΠΏΠΎΠ²Π΅ΡΡ
Π½ΠΎΡΡΠΈ ΠΏΡΠ΅ΡΡ-ΡΠΎΡΠΌΡ
6.11 ΠΡΡΠΎΡΠ΅Π½ΠΈΠ΅ ΠΏΠΎΡΡΠ΅Π»ΠΈ
6.12 ΠΠΎΠ°Π»Π΅ΡΡΠ΅Π½ΡΠΈΡ ΡΠ°ΡΡΠΈΡ
6.13 Π£ΠΏΠ»ΠΎΡΠ½Π΅Π½ΠΈΠ΅
6.14 ΠΠ·ΠΌΠ΅Π½Π΅Π½ΠΈΠ΅ ΡΠ°Π·Ρ Π²ΠΎ Π²ΡΠ΅ΠΌΡ Π½Π°Π³ΡΠ΅Π²Π°
6.15 Π ΠΎΠ»Ρ Π΄Π°Π²Π»Π΅Π½ΠΈΡ ΠΈ Π²Π°ΠΊΡΡΠΌΠ°
6.16 ΠΠ°ΡΠ΅ΠΌΠ°ΡΠΈΡΠ΅ΡΠΊΠΎΠ΅ ΠΌΠΎΠ΄Π΅Π»ΠΈΡΠΎΠ²Π°Π½ΠΈΠ΅ ΠΏΡΠΎΡΠ΅ΡΡΠ° Π½Π°Π³ΡΠ΅Π²Π°
6.17 ΠΠ±ΡΠ΅Π΅ Π²ΡΠ΅ΠΌΡ ΡΠΈΠΊΠ»Π° ΠΏΠ΅ΡΠΈ
6.18 ΠΡ
Π»Π°ΠΆΠ΄Π΅Π½ΠΈΠ΅ ΠΈ ΠΎΠΏΡΠΈΠΌΠ°Π»ΡΠ½ΠΎΠ΅ Π²ΡΠ΅ΠΌΡ Π΄Π»Ρ ΠΈΠ·Π²Π»Π΅ΡΠ΅Π½ΠΈΡ ΠΈΠ· ΠΏΠ΅ΡΠΈ
6.19 ΠΠ΅ΠΊΠΎΡΠΎΡΡΠ΅ ΠΊΠΎΠΌΠΌΠ΅Π½ΡΠ°ΡΠΈΠΈ ΠΏΠΎ ΡΠ΅ΠΏΠ»ΠΎΠΏΠ΅ΡΠ΅Π΄Π°ΡΠ΅ ΠΏΡΠΈ ΠΎΡ
Π»Π°ΠΆΠ΄Π΅Π½ΠΈΠΈ
6.20 ΠΠ½Π²Π΅ΡΡΠΈΡ ΡΠ΅ΠΏΠ»ΠΎΠ²ΠΎΠ³ΠΎ ΠΏΡΠΎΡΠΈΠ»Ρ
6.21 ΠΡ
Π»Π°ΠΆΠ΄Π΅Π½ΠΈΠ΅ ΠΈ ΠΏΠ΅ΡΠ΅ΠΊΡΠΈΡΡΠ°Π»Π»ΠΈΠ·Π°ΡΠΈΡ
6.22 ΠΠΎΠ·Π΄ΡΡΠ½ΠΎΠ΅ ΠΎΡ
Π»Π°ΠΆΠ΄Π΅Π½ΠΈΠ΅ Γ» Π‘ΠΊΠΎΡΠΎΡΡΡ ΠΎΡΠ²ΠΎΠ΄Π° ΡΠ΅ΠΏΠ»Π°
6.23 ΠΠΎΠ΄ΡΠ½ΠΎΠ΅ ΠΎΡ
Π»Π°ΠΆΠ΄Π΅Π½ΠΈΠ΅ Γ» Π‘ΠΊΠΎΡΠΎΡΡΡ ΠΎΡΠ²ΠΎΠ΄Π° ΡΠ΅ΠΏΠ»Π°
6.24 ΠΠΎΠ²ΡΡΠ΅Π½ΠΈΠ΅ Π΄Π°Π²Π»Π΅Π½ΠΈΡ
6.25 Π£Π΄Π°Π»Π΅Π½ΠΈΠ΅ Π΄Π΅ΡΠ°Π»ΠΈ
6.
26 ΠΠ»ΠΈΡΠ½ΠΈΠ΅ ΡΠΎΠ»ΡΠΈΠ½Ρ ΡΡΠ΅Π½ΠΊΠΈ Π½Π° ΠΏΡΠΎΠ΄ΠΎΠ»ΠΆΠΈΡΠ΅Π»ΡΠ½ΠΎΡΡΡ ΡΠΈΠΊΠ»Π° ΠΎΡ
Π»Π°ΠΆΠ΄Π΅Π½ΠΈΡ
6.27 ΠΠ±Π·ΠΎΡ ΠΈ ΠΊΡΠ°ΡΠΊΠΎΠ΅ ΠΈΠ·Π»ΠΎΠΆΠ΅Π½ΠΈΠ΅ ΡΠ΅ΡΠΌΠΈΡΠ΅ΡΠΊΠΈΡ
Π°ΡΠΏΠ΅ΠΊΡΠΎΠ² ΠΏΡΠΎΡΠ΅ΡΡΠ° ΡΠΎΡΠ°ΡΠΈΠΎΠ½Π½ΠΎΠ³ΠΎ ΡΠΎΡΠΌΠΎΠ²Π°Π½ΠΈΡ
6.28 ΠΠ²Π΅Π΄Π΅Π½ΠΈΠ΅ Π² ΠΆΠΈΠ΄ΠΊΠΎΡΡΠ½ΠΎΠ΅ ΡΠΎΡΠ°ΡΠΈΠΎΠ½Π½ΠΎΠ΅ ΡΠΎΡΠΌΠΎΠ²Π°Π½ΠΈΠ΅
6.29 ΠΠΈΠ΄ΠΊΠΈΠ΅ ΠΏΠΎΠ»ΠΈΠΌΠ΅ΡΡ
6.30 ΠΡΠΎΡΠ΅ΡΡ ΠΆΠΈΠ΄ΠΊΠΎΡΡΠ½ΠΎΠ³ΠΎ ΡΠΎΡΠ°ΡΠΈΠΎΠ½Π½ΠΎΠ³ΠΎ ΡΠΎΡΠΌΠΎΠ²Π°Π½ΠΈΡ
6.31 Π£ΠΏΡΠ°Π²Π»Π΅Π½ΠΈΠ΅ ΠΏΡΠΎΡΠ΅ΡΡΠΎΠΌ ΠΆΠΈΠ΄ΠΊΠΎΡΡΠ½ΠΎΠ³ΠΎ ΡΠΎΡΠ°ΡΠΈΠΎΠ½Π½ΠΎΠ³ΠΎ ΡΠΎΡΠΌΠΎΠ²Π°Π½ΠΈΡ
6.32 ΠΠ±ΡΠ°Π±ΠΎΡΠΊΠ° ΠΏΠ΅Π½Ρ
7. ΠΠΎΠ½ΡΡΡΡΠΊΡΠΈΡ ΠΌΠ΅Ρ
Π°Π½ΠΈΡΠ΅ΡΠΊΠΎΠΉ ΡΠ°ΡΡΠΈ
7.0 ΠΠ²Π΅Π΄Π΅Π½ΠΈΠ΅
7.1 Π€ΠΈΠ»ΠΎΡΠΎΡΠΈΡ Π΄ΠΈΠ·Π°ΠΉΠ½Π°
7.2 ΠΠ±ΡΠΈΠ΅ ΠΊΠΎΠ½ΡΠ΅ΠΏΡΠΈΠΈ ΠΏΡΠΎΠ΅ΠΊΡΠΈΡΠΎΠ²Π°Π½ΠΈΡ
7.3 ΠΠ΅Ρ
Π°Π½ΠΈΡΠ΅ΡΠΊΠ°Ρ ΠΊΠΎΠ½ΡΡΡΡΠΊΡΠΈΡ
7.4 Π Π°ΡΡΠ΅ΡΠ½ΡΠ΅ ΡΠ²ΠΎΠΉΡΡΠ²Π° ΠΏΠ΅Π½
7.5 ΠΠΎΠΌΠΏΡΡΡΠ΅ΡΠ½ΡΠΉ ΠΈΠ½ΠΆΠΈΠ½ΠΈΡΠΈΠ½Π³ Π² ΡΠΎΡΠ°ΡΠΈΠΎΠ½Π½ΠΎΠΌ ΡΠΎΡΠΌΠΎΠ²Π°Π½ΠΈΠΈ
7.6 ΠΠ΅ΠΊΠΎΡΠΎΡΡΠ΅ ΠΎΠ±ΡΠΈΠ΅ ΡΠΎΠΎΠ±ΡΠ°ΠΆΠ΅Π½ΠΈΡ ΠΏΠΎ ΠΏΡΠΎΠ΅ΠΊΡΠΈΡΠΎΠ²Π°Π½ΠΈΡ
7.7 ΠΠ»ΠΈΡΠ½ΠΈΠ΅ ΠΏΡΠΎΡΠ΅ΡΡΠ° Π½Π° ΠΏΠΎΡΠΈΡΡΠΎΡΡΡ, ΡΠ΄Π°ΡΠ½ΡΡ Π²ΡΠ·ΠΊΠΎΡΡΡ
7.8 ΠΠ±ΡΠ΅Π·ΠΊΠ°
7.9 Π£ΠΊΡΠ°ΡΠ΅Π½ΠΈΠ΅ ΠΏΠΎΠ²Π΅ΡΡ
Π½ΠΎΡΡΠΈ
7.10 Π£ΡΡΡΠ°Π½Π΅Π½ΠΈΠ΅ Π½Π΅ΠΈΡΠΏΡΠ°Π²Π½ΠΎΡΡΠ΅ΠΉ ΠΈ ΠΎΠ±Π΅ΡΠΏΠ΅ΡΠ΅Π½ΠΈΠ΅ ΠΊΠ°ΡΠ΅ΡΡΠ²Π°
ΠΡΠΈΠ»ΠΎΠΆΠ΅Π½ΠΈΡ
ΠΠ½Π΄Π΅ΠΊΡ
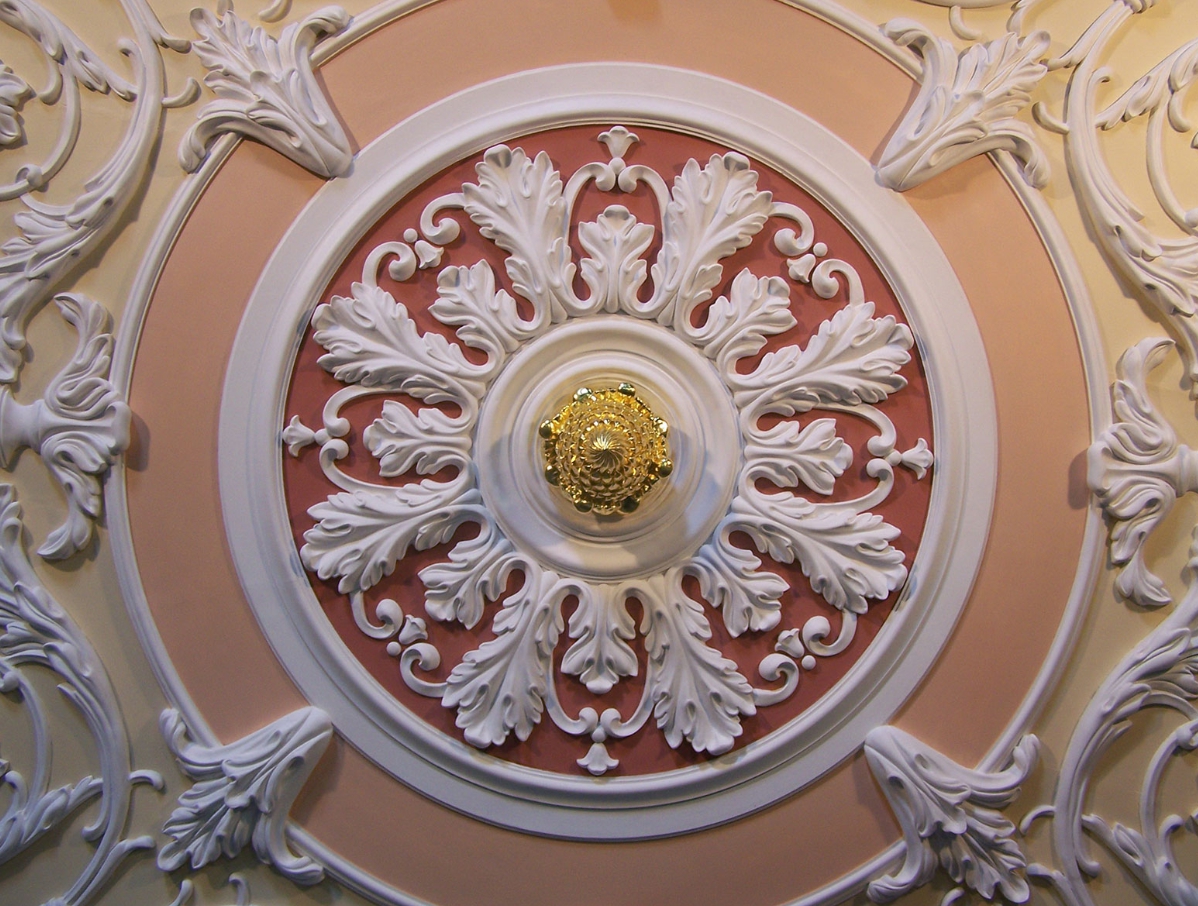