Производство фанеры. Описание технологии производства фанеры.
Процесс производства фанеры выглядит следующим образом. Бревна древесины, из которой будет производиться фанера, разделяются на чураки, длина которых равна длине шпона для будущей фанеры. Чураки нарезаются на круглопильных станках. Далее чураки распаривают в специальных емкостях с горячей водой для придания древесине достаточной мягкости. Если лущить холодную и сухую древесину, то шпон может разрушаться. Затем чураки проходят окорку.
Биржа сырья. |
|
Распаривание чураков в специальных бассейнах. |

Шпон на лущильной линии. |
Для изготовления фанеры допускается шпон с влажностью около 6%. Для достижения такой влажности шпон сушат в газовых или паровых сушках, а потом разделяют на сорта, в зависимости от наличия сучков и других дефектов.
Для повышения качества фанерного листа необходимо нормализовать размеры и качество шпона. Выпавшие сучки и другие дефекты вырубаются из шпона, а отверстия заделываются шпоновыми заплатками. Все это выполняется с помощью шпонопочиночных станков. Иногда дефекты убираются с помощью вырезки из шпона по всей ширине ленты дефектной области. Затем в месте разрыва лента шпона сшивается стеклонитью, которая обработана полиамидной смолой. Эти операции выполняются на ребросклеивающих станках. Существуют станки, в которые шпон подается поперек или вдоль. Процесс ребросклеивания шпона положительно сказывается на качестве фанерного листа и позволяет механизировать движение ленты шпона во время формирования стопок для последующей склейки фанеры.
Линия сращивания шпона |
После этого шпон подвергается кондиционированию, а затем поступает в цех для склеивания. Сегодняшние цеха по склеиванию фанеры оборудованы 30-40 этажными горячими прессами, в которые автоматически загружаются пакеты и также автоматически выгружается
фанера. Также цеха оборудованы станками, наносящими клей, агрегатами, укладывающими шпон в пакеты и прессами для подпрессовки пакетов, когда они собраны в пачки, а также транспортировочными агрегатами.
Пакеты, из которых будет сделана фанера, состоят из нечетного числа листов шпона. Клеем обрабатываются четные листы. При изготовлении влагостойкой фанеры или фанеры фк используется карбамидный клей, при изготовлении фанеры фсф — фенолформальдегидный. При составлении пакетов попеременно кладутся листы шпона обработанные клеем и без клея. Стопы транспортируются к станку, где происходит подпрессовка, которая улучшает качество склеивания и позволяет добиться компактности пакетов. Затем пакеты подаются в горячий пресс.
После склеивания фанера подвергается кондиционированию и обрезке по размерам на круглопильных станках.
Высокие сорта фанеры шлифуют на широколенточном шлифовальном оборудовании. Фанера, которая подверглась обработке на шлифовальном станке, обладает высокой точностью по толщине. Такая фанера называется калиброванной. Затем фанера сортируется, получает маркировку и упаковывается в пачки для доставки потребителю.
Производство фанеры | Изготовление фанеры
Производство фанеры в настоящее время довольно трудоемкий технологический процесс. История фанеры берет свой отсчет с 15 века до нашей эры. Первые же механические станки для
Изготовление фанеры состоит из нескольких этапов
Выбор древесины
Этот этап характеризуется подбором и подготовкой бревен древесины. Бревна предназначенные для изготовления фанеры называют фанерным кряжом. Доставляют их до места обработки чаще всего железнодорожным транспортом. Для производства могут применяться как лиственные породы древесины – береза, липа, ольха, так и использоваться хвойные породы. Из лиственных пород наиболее часто используется береза. Обусловлено это во многом определенным расположением годовых колец в строении ствола дерева, а также малым количеством сучков. Кроме того, березу отличает средняя плотность порядка 650 кг/м
Подготовка древесины

Происходит этот процесс следующим образом. Деревянные бревна помещают в такие бассейны и потом закрывают их крышкой. В зависимости от периода (летний или зимний) выдерживается необходимое время. При этом в бассейн добавляется горячая вода для поддержания нужной температуры. Благодаря данной операции при дальнейшем получении шпона он стремиться вернуться в форму цилиндра.
Предварительная обработка древесины
Предварительная обработка древесины называется окоркой бревен. Из названия понятно, что с бревен удаляют кору. Получившиеся при окорке бревен отходы перемалывают в измельчительных машинах и уже после используют для изготовления ДСП. Камера металлоискателя позволяет определять инородные металлические включения в бревне. Затем оно поступает на распиловочный станок. На этом станке бревна нарезают в чураки. Чурак – кусок бревна длиной от 1,3 до 1,6 метра. При нарезке чураков также удаляют негодные части древесины. Далее такие куски отправляются на участок получения шпона.
Процесс получения шпона
К следующему этапу изготовления фанеры относится процесс получения шпона. Всего насчитывают три основных способа получения шпона. Это лущение чураков на специальном круговом станке, пиление чураков на полосы, а также строгание чураков. Получение шпона процессами пиления и строгания характеризуются низкой экономичностью и малой производительностью, а потому в настоящее время практически не используются.
На лущильных станках чураки режутся в поперечном сечении. Заготовка устанавливается на круговой станок и вращается вокруг своей оси. Путем подведения специального лущильного ножа срезается тонкая часть древесины. Так и нарезается лента шпона. Длина и ширина такой ленты зависят от габаритов чурака и от необходимой толщины самой ленты шпона. Далее такая лента нарезается в стандартные размеры 1,3 или 1,6 м. Листы шпона укладывают стопками и передают на сушку. Некондиционный же шпон поступает на измельчение и дальнейшую переработку.
Наглядное видео по лущению березового шпона
Сушка и ремонт шпона
Сушка шпона осуществляется на специальном конвейере. На нем шпон подвергается обработке теплым воздухом. Затем при помощи специального сканера и влагомера происходит его сортировка. Некондиционные и влажные листы отбраковываются и отправляются на ремонт или досушку.
Починка шпона осуществляется путем вырезания некондиционных фрагментов. Вместо них вставляются куски нового шпона, который подбирается по цвету и фактуре. Толщина нового куска шпона должна полностью соответствовать толщине начального листа. При этом минимально допустимая ширина не должна быть меньше 450 мм. При этом влажность новой части должна быть меньше на 2-4% изначального листа.
Прошедший проверку сканером и влагомером шпон выдерживают на специальном складе хранения в течении суток. Этого времени достаточно, чтобы влажность всех листов стала одинаковой. Ремонтированные листы выдерживают не более 8 часов. Далее шпон передается на участки склейки.
Склейка шпона
Полосы шпона, имеющие различные дефекты отправляются на ребросклейку. Благодаря этой операции получается полотно из склеенных полос шпона. Далее такие полосы стыкуются и склеиваются. Готовая лента полос режется в стандартные размеры.
Стоит отметить, что готовые листы шпона имеют поперечное направление волокон. Однако, необходимая прочность цельных листов фанеры достигается путем попеременного расположения волокон в листах шпона. Достигается это следующим способом. Листы шпона разрезаются пополам, затем в каждом листе формируется специальный выступ и паз для усового соединения.
Видео по нанесению клея на листы шпона
На паз одного из листов наносится специальный клей и отправляется в пресс. В специальном прессе под действием высокой температуры и большом давлении происходит склейка листов шпона. Количество листов шпона в фанерном листе должно быть нечетным. После того, как готовые листы просохнут, их нарезают в нужные размеры.
Дополнительная обработка листов фанеры
В зависимости от марки и степени обработки может производиться дополнительная обработка листов. Часто листы подвергают дополнительной шлифовке. При этом могут быть отшлифованы как обе стороны фанеры, так и только одна.
Также листы для придания более высокой износоустойчивости могут пройти процесс ламинирования. Для этого листы покрывают специальной пленкой. Такая пленка дополнительно защищает фанеру от воздействия влаги. Ламинированная фанера очень часто используется в опалубке, где необходимо многократное использование листов.
Упаковка готовых листов
На этапе упаковки листы укладываются в пачки нужного количества и передаются на отгрузку или склады хранения.
В целом процесс изготовления фанеры можно представить в виде схемы:
Заключение
Изготовление фанеры длительный и трудоемкий процесс. В настоящее время в России качество фанеры регламентируется ГОСТ 3916.1-96. Четкое следование всем технологическим процессам производства фанеры позволяет получать готовый материал высокого качества. Такой материал можно эксплуатировать длительное время.
технология и видео основных этапов процесса
Фанера – это необычный листовой материал, со свойствами, которые столь уникальны, что использовать его можно и для любительских поделок и для обшивки морских судов. При производстве фанеры технология, которая используется для получения материала с особыми качествами, имеет свою специфику. Но есть общая последовательность операций, которые повторяются при изготовлении фанеры любого назначения.
Из чего состоит фанера
Технология производства фанеры разработана так, чтобы получить определенную структуру, которая представляет собой слои древесины, число которых может доходить до 21, склеенные между собой клеевыми составами. Причем самыми популярными сортами древесины, которые применяют для изготовления фанеры, являются сосна и береза, которые придают особые свойства материалу. Клеевые составы для соединения древесных слоев, изготавливаются на основе смол, которые влияют на свойства фанеры не меньше, чем древесина.
Фанера из березы
Технология производства фанеры
Технология производства фанеры из березового шпона это сложный многоэтапный процесс, который требует точного соблюдения методик, чтобы получить качественный листовой материал.
Основные этапы изготовления фанеры:
- Подготовка древесины. Стволы березы подбирают по размеру. То есть для получения листовую фанеру размером 1,2 м на 2,4 м, нужны стволы длиной 5,20 м с диаметром от 20 до 40 см, которые распиливают на чурки от 1,3 м до 2,6 м. После этого березовые чурки проваривают в бассейне в течение суток. Это значит, что вода должна иметь температуру около 40оС;
Проваривание березовых стволов в бассейне
Важно! Если на этапе проваривания стволов будет нарушено время нахождения в бассейне или температура воды будет слишком горячей, то качество шпона будет низким.
- Окорка и распиловка. На окорочном станке со специальными ножами снимается кора, которую используют для того, чтобы отапливать фанерный комбинат. После этого металодетектором обследуют древесину, чтобы обнаружить гвозди или проволоку, которые могут повредить оборудование;
Окорочный станок
- Распиловка и лущение.
Бревна распиливаются, и на специальных станках начинается лущение, то есть срезается тонкая лента шпона. Из березы получается очень тонкий шпон толщиной около 1,5 мм, который лучше чем шпон других сортов древесины. Во время лущения происходит контроль качества шпона, и лущильные станки подстраивают под каждую партию;
Лущильный станок
- Рубка шпона. Шпон режется на форматные листы автоматическими ножницами. Чтобы получить фанеру размером 1,2 м на 2,4 м шпон должен быть разрезан на листы размером 1,3 м на 2,6 м.
- Просушивание шпона. В сушилке листы шпона обдувают прогретым воздухом в течение 10 мин. За это время 90% влажности уходит из древесины.
- Сортировка шпона. При сортировке выявляют листы, которые имеют повреждения, например, трещины, выпавшие сучки. Кроме того отбраковывают недосушенный шпон, который отправляют на повторную сушку.
Обратите внимание! Качество сортировки во многом зависит от оборудования, которое используется на комбинате.
Наибольшее количество дефектов выявляют там, где есть автоматизированное оборудование, которое сканирует поверхность шпона.
- Вальцовка и склеивание шпона. На этом этапе происходит создание структуры фанеры, прочность которой достигается тем, что шпон складывается так, чтобы направление волокон одного листа шпона было перпендикулярно направлению волокон в соседних слоях. После того как последовательность слоев определена, шпон укладывают в наборный пакет, причем листы чередуются так, чтобы сухой шпон чередовался с листами шпона, прошедшими вальцовку, во время которой с обеих сторон наносится клей;
Сборка пакетов
- Холодная подпрессовка в течение 10 мин проводится для того, чтобы получить пакет шпона, удобный для транспортировки;
- Горячее прессование проводят при температуре 130 оС на специальном прессе.
Более подробно расскажет технологию производства фанеры видео:
com/embed/7xdQiyIaNuM?feature=oembed» frameborder=»0″ allowfullscreen=»»/>
Сюжет демонстрирует, что качественная фанера – это результат сложного процесса, который повторить в кустарных условиях невозможно без специального оборудования.
Вконтакте
Google+
1. Технология производства фанеры. Технология производства фанеры
Похожие главы из других работ:
Автоматизация редукционно–охладительной установки
2.1 Технология производства. Описание технологического процесса участка производства
Редукционно-охладительная установка (РОУ) служит для понижения давления и температуры острого пара, вырабатываемого котлоагрегатами. С помощью РОУ резервируются промышленные и теплофикационные отборы паровых турбин…
Анализ организации и технологии отрасли Волгоградского филиала ООО «Омсктехуглерод»
4. Технология производства
Важный элемент, без которого не может существовать ни одно предприятие, — его структура, отражающая вертикали управления, подчиненность отделов, служб, цехов (Рисунок 4). ..
Влияние эмульсии из свиной шкурки на качество колбас
2. Технология производства
…
Консервная промышленность
1.1 Технология производства
Сбор, доставка и хранение сырья. Механизированную уборку томатов начинают при созревании на кусте 70-80% плодов, используя комплекс машин из самоходного комбайна СКТ-2 и тракторной платформы ПТ-3…
ОАО «Марийский Целлюлозно–бумажный Комбинат»
2. Технология производства
…
Обоснование выбора оборудования для организации производственного процесса производства полукопчёной колбасы «Польская»
Технология производства
К полукопчёным колбасам относятся изделия, готовые к употреблению в пищу после варки, копчения и сушки. В процессе изготовления полукопчёные колбасы теряют влагу, поэтому совершенно нецелесообразно насыщать фарш влагой, т. е…
Особенности производства асбестовермикулитовых изделий
3.
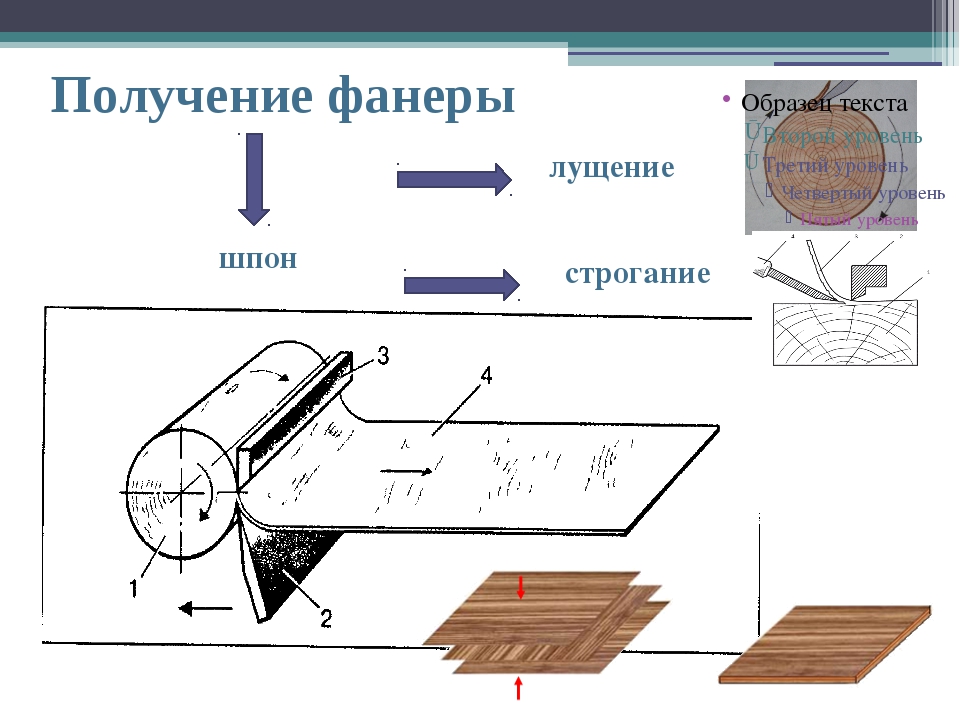
…
Проектирование предприятий по производству игристых вин
1.4 Технология производства шампанских вин
Существует два способа производства шампанского: бутылочный способ и резервуарный. Технология шампанского бутылочным способом отличается трудоемкостью, требует больших затрат ручного труда…
Производство звукопоглощающих и звукоизоляционных материалов
2.3 Технология производства
Рис…
Процесс прокатки шаров на станах
3. Технология производства
…
Разработка композиционного решения интерьера помещения и технологии изготовления художественного изделия в стиле «модерн» с элементами витража
3.3 Технология производства
…
Разработка робототехнического комплекса по производству фанеры
· Анализ технологического процесса производства фанеры.
…
Расчет и технология изготовления ригелей на линейных стендах
2.
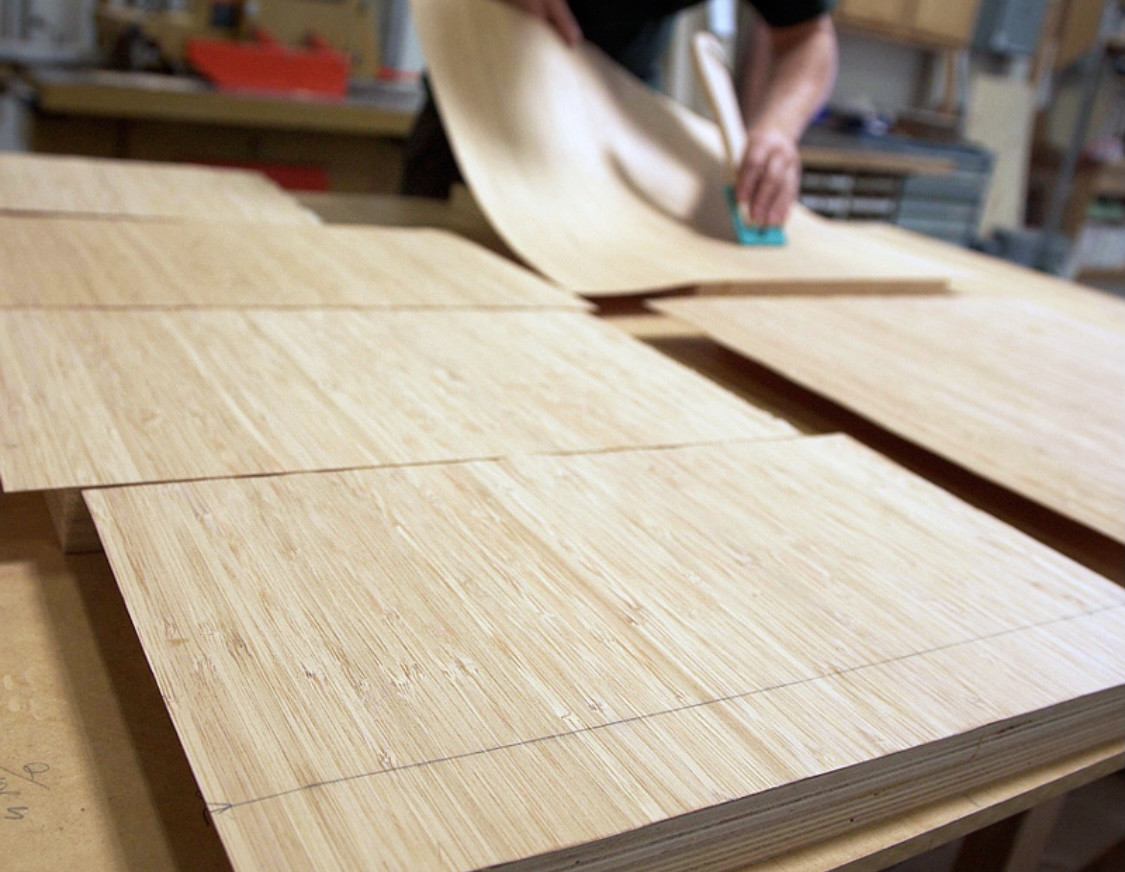
Наиболее оптимальным способом производства ригелей является стендовый, позволяющий максимально автоматизировать и механизировать процесс производства и получивший широкое распространение за рубежом…
Технологический процесс переработки мяса, производство и реализация продукции общественного питания
2. Технология производства продукта
Технология производства колбас представлена на технологической схеме (рис.1). Рис.1. Технологическая схема производства колбас Разделка, обвалка…
Цех по производству минераловатных (жёстких) акустических плит
1.3 Технология производства
акустический плита цех сырье Пояснительная записка к технологической схеме производства. Технологическая поточная линия производства плит повышенной жесткости по способу «мокрого» формования работает следующим образом…
Процесс производства фанеры
Производство фанеры — это сложный технологический процесс, который начинается с прихода сырья на завод.
Фанерное сырье – это кряж (бревна определенной длины). Фанерный кряж может быть разных пород дерева – основное в нашей стране это береза, но может быть осина, сосна, ель, а так же др. породы древесины. Принимается сырье на «биржу сырья», где укладывается в штабеля и в таком виде хранится. Перед началом переработки фанерный кряж поступает в пропарочные бассейны, чтобы затем его было легко разлущивать, это особенно важно в зимний период, когда древесина замерзшая.
Пропаренный фанерный кряж поступает на торцовку в нужный размер по длине и затем на лущильный станок, где получают лущеный шпон нужной толщины в виде листов в размер будущей фанеры в зависимости от ее формата. Затем шпон сушится до определенной влажности, для того чтобы его можно было склеивать между собой, сортируется по качеству и определяется куда он пойдет (на лицевые стороны или на внутренние слои).
Для повышения сортности такого листа шпона, у которого есть выпадающий сучек, лист отправляют на «шпонопочинку» где на специальном оборудовании вставляется эллипсообразная вставка из такого же шпона. Подготовленный шпон поступает на оборудование, где на него наносится клей и формируется лист фанеры нужной толщины и сортности. Затем набранный пакет поступает в многопрофильный пресс, где и склеивается при высокой температуре. После склеивания полученный лист обрезается в размер, шлифуется по необходимости и окончательно сортируется и маркируется. По завершению процесса производства фанера упаковывается и отправляется на склад готовой продукции.
Остались вопросы? Задайте их в разделе Вопрос-Ответ
Вся фанера на этом видео предоставлена нашей компанией. Использовалась высокосортная березовая фанера 10-20 мм.
Технология изготовления изделий из фанеры
Технология изготовления изделий из фанеры
Перед началом работы со всякого вида материалами нужно знать правила его первоначальной обработки. Без таких знаний будущее изделие не будет выглядеть достаточно красиво. Правила обработки обязательно нужно знать и о фанере. Данный материал не является массивом дерева, это всего лишь тонкие листы из шпона. Они склеены между собой специфическим образом. В итоге склейки волокна шпона в одном слое становятся в перпендикулярное положение относительно волокон другого слоя. Благодаря этому листы из этого материала гнутся в любом направлении при необходимости создания сложных форм. В то же самое время процесс распиливания верхнего слоя в поперечном направлении от волокон может стать причиной повреждения листа. Итак, правила работы с фанерой фсф таковы:
— чтобы её поверхность не треснула из-за поперечной резьбы по волокнам, нужно надрезать ножом саму линию распила;
— нужно обязательно просверливать отверстия под гвозди или саморезы;
— пространство под шляпками крепёжных элементов требует помещения шайб;
— перед склейкой поверхностей их следует зачистить с помощью шкурки, клей наносить равномерно и также равномерно сжимать все соединяемые поверхности;
— если элементы нужно подвергнуть сгибанию, то их перед работой стоит смочить или распарить, положить в необходимый шаблон и выдержать в нём сутки;
— для резки тонкой фанеры (до 1,5 мм) нужно использовать острый нож, лобзик подходит для листов фанеры до 6 мм, а самые толстые листы режутся только дисковой пилой;
— края деталей стоит обязательно обработать напильником или любым шлифовальным инструментом для устранения заусенцев.
Для производства любого фанерного изделия требуется совсем небольшой столярный набор:
— очень острый нож, а также электролобзик с полным набором пилочек к нему;
— шуруповёрт, дрель, бит с набором свёрл;
— подходящий для дерева клей, например, простой столярный;
— наждачная шкурка и напильник;
— карандаш и любой удобный измерительный инструмент
— элементы для крепежа деталей.
Фанера – это поистине уникальный и универсальный материал для талантливых мастеров с развитой фантазией. Это ценное сырьё для использовании его как в большом налаженном производстве, так и самостоятельно. Древесная фактура, экологичность, доступность и натуральность известна каждому. Умелые руки человека, его воображение и терпение помогут превращению обыкновенного листа фанеры в изделие, которое не будет иметь аналогов в мире.
Технология производства фанеры
Ниже будет показана пошаговая инструкция технологии производства фанеры. Фанера Караганда.
1. Резка бревен
Бревна нарезаются на небольшие отрезки, подходящие для нарезки шпона.
2. Пилинг и резка шпона
Шпон снимается с обрезанных бревен. После пилинга виниры классифицируются. Из соображений стоимости при производстве фанеры используются два вида шпона. Толстый и низкосортный шпон для фанерного сердечника. Шпон тонких и высших сортов для облицовки фанеры
3. Сушка шпона
Недавно очищенные свежие виниры имеют высокий уровень влажности от 35% до 45%. Чтобы клей хорошо впитался, их необходимо тщательно высушить в сушилке или в машине для горячего прессования. После высыхания шпон дает усадку на 4-10%. Процесс сушки шпона улучшает характеристики фанеры, делая ее более прочной.
4. Нанесение клея
Следует приклеить только половину шпона, чтобы сухой шпон был покрыт клееным шпоном. Типы клея зависят от требований к качеству фанеры.
5. Укладка шпона
Клееные виниры складываются по типу конструкции. Конструкционная фанера и неконструкционная фанера имеют совершенно разную структуру.
В отличие от фанерных фабрик в Европе или США, китайские производители фанеры используют в этом процессе в основном рабочую силу.
6. Холодный пресс
Холодный пресс — это предварительный пресс для экономии энергии. Это может сэкономить время на горячее прессование и снизить производственные затраты.
7. Крепление
Трещины на шпоне сверху фиксируются шпатлевкой или кусочком шпона. Перед шлифовкой все швы шпона заполняются шпаклевкой, чтобы убедиться в хорошем состоянии поверхности.
8. Горячий пресс
Это ключевой процесс производства фанеры. Клей затвердевает под давлением и нагреванием. Шпон склеивают вместе, чтобы получилась прочная доска. Фанера без этого процесса называется фанерой одноразового прессования, которая по качеству ниже, чем фанера двухкратного прессования.
9. Резка
Панель разрезается на квадратные листы. При этом образуется большое количество остатков фанеры. После обрезки кромки рабочие произведут необходимую фиксацию на кромке фанеры. Крепление включает ручную полировку и заполнение отверстий.
(PDF) Инновационная система укладки фанеры
56 Eur. J. Wood Prod. (2009) 67: 55–62
производителей увеличили производство фанеры за последние два
лет до момента написания (Baodong et al. 2006, Dieter
and Englert 2007).
В этом сценарии снижение производственных затрат является важным фактором повышения рентабельности компаний по производству фанеры
. Технологические инновации в процессе производства
особенно важны не только для снижения затрат
, но и для повышения качества существующей ресурсной базы древесины
.
Традиционный процесс производства фанеры обычно состоит из подготовки фанеры, операции укладки, прессования и, в заключение, процесса отделки.
Операция по укладке, которая составляет основу производства фанеры
, требует большого количества ручных операндов
и оказывает сильное влияние на качество продукции. Его цель
— получить сборку виниров. После этого
собранный шпон отправляется на горячий пресс, где
уплотняет его под действием тепла и давления.Время и температура варьируются в зависимости от используемой породы древесины, используемой смолы,
и конструкции пресса.
Возрастающая конкуренция на рынке фанеры
вынуждает компании улучшать производственные показатели. Большой объем работы связан с разработкой клея, процессом отслаивания
и процессом сушки. Потребность в гибкости
обычно требует использования большого количества рабочей силы
человек, а большое количество конечных продуктов
различных размеров препятствовало разработке на решающем этапе укладки
.К сожалению, на момент написания эта ситуация
существенно повлияла на производительность производственной системы
, особенно на стоимость производства, качество и безопасность операторов
в нескольких случаях.
В этой статье предлагается инновационная система укладки
, основанная на новой идее создания панели, обеспечивающей интенсивное использование
гибкой автоматизации ресурсов. Сообщается как о теоретическом решении, так и о реальном применении.
Эта статья организована следующим образом. В разделе 2 дается обзор литературы
, относящейся к предложенной проблеме. Детали
традиционной системы укладки обсуждаются в Разд. 3 в то время как
разд. 4 представляет новую идею, а метод, разработанный как
, является результатом. Реальное применение инновационной системы
на крупном производителе фанеры из тополя представлено
в разд. 5. Наконец, в разд.6.
2 Обзор литературы
Процесс укладки фанерных панелей — область, мало изученная в литературе. Спелтер (1989) изучил стоимость производства
фанеры без учета сырья. Он подтверждает значительное влияние существующей системы на этап укладки
, от 18 до 26% от общей стоимости производства
в зависимости от конкретной используемой породы древесины.
Существующий процесс укладки ясно представлен
Болдуином (1981) и Шраммом (2003). Последний из этих
двух авторов описывает существующую технологию изготовления фанеры, а
, прежде всего, он пытается описать дополнительные технологические инновации и прорывные технологические инновации
в нескольких направлениях, особенно в отношении лущения, сушки.
Инженерные и полимерные разработки.
В других исследованиях немного обсуждается проблема укладки, но
не посвящены ее улучшению. Например, Bekhta и
Marutzky (2007) оценивают снижение расхода клея —
на этапе укладки за счет использования предварительно спрессованных виниров
.Завала и Хамфри (1996) обсуждают связь между процессом укладки и горячего прессования. Айдын и Колакоглу
(2005) исследуют влияние условий сушки на производительность укладки и прессования
. Айдын (2004) предлагает
процесс механической предварительной обработки перед укладкой на поверхности тиватного шпона ac-
для улучшения склеивания клея.
Однако все исследования учитывают существующую систему резервирования
(см. Разд.3) разложить виниры для этапа прессования.
Никаких значительных исследований в области инноваций процесса укладки
не проводилось.
3 Традиционная система укладки
Система укладки подготавливает группу виниров путем выравнивания и правильного наложения их внахлест (т. Е. Чередование направления волокон шпона
), а затем их помещения в
система прессования для изготовления панели. Свойства фанеры
с точки зрения размера, толщины и количества перекрывающихся слоев
зависят от желаемого конечного продукта.Более того, все фанерные панели
требуют облицовки лицевой и тыльной сторон,
, и, будучи единственными видимыми слоями фанеры, они должны соответствовать спецификациям заказчика
. Внутри панели есть два вида волокон
: длинные волокна, т.е. волокна
идут в одном направлении на лицевой и обратной стороне, и поперечные волокна
, где волокна перпендикулярны.
Из-за широкого ассортимента продуктов гибкость системы укладки
должна быть высокой, на существующем оборудовании задействовано
большое количество операторов, а автоматизация существует только до
в небольшой степени. Система укладки обычно требует укладки шпона четырех типов на поддоны: лицевого, заднего,
длиннозернистого и поперечного шпона. Изделие готовят два оператора
, работающие за сборочным столом. Основная стратегия
традиционного подхода заключается в поставке нескольких групп, состоящих из
пар фанеры, предварительно подготовленных с помощью ролика
и системы с несколькими ленточными конвейерами. Смола наносится на две стороны
одного из листов в паре, в частности, на шпон с поперечным зерном
, образующий верхний лист пары.
Разбрасыватель обычно представляет собой валковую машину, которая имеет серию из
покрытых резиной валков с канавками для нанесения. Первая пара
состоит из задней части и поперечно-клееного шпона. Для второй пары
требуется шпон с длинными волокнами, уложенный на крест.
13
Как производится фанера — оборудование и производственный процесс
В этой статье описывается непрерывный процесс и машины, необходимые для производства фанеры. Выполните следующие десять шагов, чтобы понять, как обычно производят фанеру:
Шаг 1: Распиливание бревен
Большие деревянные бревна, обычно хранящиеся под водой, разрезаются на куски в соответствии с производственными требованиями.
Необходимые инструменты / оборудование : Большая ручная пила или механическая пила (лесопильный завод).
Siep-2: Обработка журналов
Затем куски бревен нагревают при температуре около 70-90 градусов C в течение 12-14 часов либо под горячей водой, либо в паровой камере.
Необходимые инструменты / оборудование : Паровая камера или баня с горячей водой.
Этап 3: окорка
Кора или толстая пленка вокруг бревна удаляются ручными инструментами или окорочным станком.
Необходимые инструменты / оборудование : большое долото и молоток или окорочный станок.
Шаг 4: Изготовление шпона
Шпон — это слои древесины толщиной в несколько миллиметров. Виниры могут быть изготовлены путем лущения или нарезки.Бревно загружается на токарно-лущильный станок или на строгальный станок для изготовления из него фанеры.
Изображение предоставлено: доктор П.Д. Эванс
Необходимые инструменты / оборудование : Станок для лущения древесины или станок для нарезки шпона.
Шаг 5: Мокрая клипсация Затем шпон разрезают на кусочки необходимого размера с помощью клипсатора. Клипса работает как большие ножницы. Необходимые инструменты / оборудование : Станок для обрезки шпона. Шаг 5: Сушка Затем виниры частично сушат солнечным светом и частично сушильным аппаратом. Поддержание необходимого количества влаги в фанере очень важно для производства фанеры хорошего качества.
Рис.2: Схема сушилки для шпона Необходимые инструменты / оборудование : Сушилка для шпона, измеритель влажности шпона.
Шаг 6: Сухая клипсация После повторной сушки виниры обрезаются с помощью клипсатора. Этот шаг необходим, чтобы обрезать виниры с жесткими допусками и удалить дефекты высыхания.
Необходимые инструменты / оборудование : Станок для обрезки шпона.
Шаг 7: Приготовление смолы Для изготовления клея используются жидкие или порошковые смолы. Формальдегид мочевины (UF) и фенилформальдегид (PF) — два наиболее распространенных типа смол, используемых в производстве фанеры. В случае жидкой смолы, смола обычно производится в доме с использованием реактора для смолы или завода по производству смолы.
Необходимые инструменты / оборудование : Завод по производству смолы или котел.
Шаг 7: Склеивание и сборка Затем виниры правильного размера склеиваются обычным способом с помощью клеильного станка. Шпон пропускается между двумя роликами клеильного станка. Ролики клеильного станка смачиваются непрерывной подачей клея. Нечетное количество слоев шпона собирают таким образом, чтобы направления волокон следующих друг за другом слоев были перпендикулярны друг другу.
Необходимые инструменты / оборудование : Машина для склеивания шпона.
Шаг 8: Горячее прессование Собранные слои фанеры переносятся внутри горячего гидравлического пресса, который прикладывает определенное давление и температуру в течение определенного времени к сборке фанеры и превращает ее в фанеру путем отверждения смол.
Рис.3: Гидравлический пресс для горячей фанерыИзображение предоставлено Wiki
Необходимые инструменты / оборудование : Гидравлический горячий пресс
Шаг 9: Обрезка Циркулярная электрическая пила используется для обрезки фанерных досок до необходимого размера.
Необходимые инструменты / оборудование : Циркулярная пилорама
Шаг 10: Инспекция, маркировка и отправка Осмотр выполняется для выявления бракованных и подлежащих ремонту частей среди хороших частей. Ремонтопригодные детали ремонтируются шпаклевкой и цветными пастами вручную. Наконец, маркировка и отправка завершены.
Необходимые инструменты / оборудование : Этикетировочная машина.
Это типичный процесс производства фанеры и оборудование. Если у вас есть что рассказать по этому поводу, не стесняйтесь комментировать.
Привет, я Шибашис, блоггер по страсти и инженер по профессии. Я написал большинство статей для mechGuru.com. Более десяти лет я тесно связан с технологиями инженерного проектирования и моделирования производства. Я занимаюсь программированием-самоучкой, сейчас влюблен в Python (Open CV / ML / Data Science / AWS -3000+ строк, 400+ часов)
1. Описание производственных процессов
1. Описание производственных процессов.1.1 Введение
1.2 Лесопильное
1.3 Производство фанеры
1.4 Производство ДСП
В связи с принятием мер по энергосбережению возникла необходимость в детальном анализе процесса и оборудования, используемого в этом процессе. Этот анализ должен был определить количество, тип и качество необходимой энергии, чтобы определить возможную экономию энергии, совместимую с соответствующим анализом затрат и выгод.
Следующие ниже описания процессов производства пиломатериалов, фанеры и ДСП носят общий характер и должны дать читателю общее представление о производственных процессах, задействованных в механической деревообрабатывающей промышленности, и о роли, в которой энергия играет важную роль. часть.
1.2.1 Сортировка бревен и окорка
1.2.2 Распиловка или дробление бревен
1.2.3 Сортировка и сортировка
1.2.4 Сушка
1.2.5 Повторная сортировка и наплавка
Лесопильное производство — менее сложная отрасль механической лесной промышленности. Он подразумевает выполнение определенного количества операций от обработки и транспортировки бревен до сушки, сортировки и классификации древесины, требующих различных видов энергии. В то время как в развивающихся странах большинство процессов являются высокомеханизированными, и потребности в энергии удовлетворяются в основном за счет выработки нескольких кВт для привода основных пил. Остальные процессы выполняются с использованием энергии животных и дешевой рабочей силы.
Тем не менее, независимо от характера задействованных процессов и действий, все действия, направленные на экономию энергии, требуют подробного анализа существующих процессов и возможных решений.
На рисунке 1 представлена схема типичного предприятия и описание основных процессов для ознакомления читателя.
1.2.1 Сортировка бревен и окорка
По прибытии на склад комбината бревна сортируются и хранятся по видам, диаметру, длине, конечному использованию и т. Д.Складывается достаточное количество древесины для обеспечения непрерывной работы лесопильного завода, особенно в неблагоприятных погодных условиях, когда вывоз и поставка бревен из леса могут оказаться под угрозой.
Транспортировка и обработка бревен различаются от лесопильного завода к другому и в значительной степени зависят от производительности лесопильного завода и размера полученных потерь. Ручной и животный привод, который может использоваться в небольших переносных лесопильных станциях, до фронтальных погрузчиков для перевозки бревен и мостовых кранов, свидетельствует о большом разнообразии используемого в настоящее время погрузочно-разгрузочного оборудования.
Рисунок 1. Лесопильное производство — упрощенный технологический процесс
Окорка бревен вручную или механическими окорочными станками в лесу или на заводе становится общепринятой практикой. Окорка предназначена для защиты пил и другого оборудования от чрезмерного износа и повреждений, которые в противном случае могли бы возникнуть в результате попадания в кору камней, металла и других подобных предметов; окорка также помогает главному пилораму оценить древесину.Шайбы для бревен также можно использовать для удаления оставшегося песка или грязи, которые могут приставать к поверхности бревен.
1.2.2 Распил или распил бревна
Перед тем, как бревно подано на головную опору для разрушения, оно обрезается до максимально допустимой прямой длины с помощью отрезной пилы, после чего оно загружается на тележку головной пилы и размещается таким образом, чтобы позволить оператору достичь максимальной длины. рисунок распиловки, который приведет к оптимальному производству пиломатериалов с минимумом отходов.Схема распила во многом определяется размером и состоянием бревна, а также требованиями рынка к ширине и толщине пиломатериалов.
Распиловка бревна осуществляется с помощью ленточной пилы или циркулярной пилы со второй пилой, установленной вертикально над первой, в случае распиловки бревен большого диаметра. Тележка для бревен перемещает бревно через головную пилу, на которой бревно может быть зажато и повернуто, чтобы его можно было поднести к головной пиле для достижения наилучшего рисунка пиления.
Следом за головной опорой на перекладке происходит дальнейшая разбивка плит, обрезков и брусьев, что позволяет улучшить древесину; толстые плиты распиливают на доски, а брус и брус распиливают на доски и доски. Неровные закругленные края деталей, выходящих из передней стойки и повторных пил, удаляются либо циркулярной пилой, либо кромкообрезным станком, чтобы получить стандартную ширину по мере необходимости.
При выходе из шпинделя, пилы или обрезного станка пиломатериалы разрезаются на стандартизованную длину, кромки берутся в квадрат и дефекты устраняются с помощью одной или нескольких фиксированных или подвижных обрезных пил, после чего пиломатериалы подвергаются сортировке и сортировке.
1.2.3 Сортировка и сортировка
Пиломатериалы и обрезки сортируются по толщине, ширине, длине, качеству, сорту и породе в зависимости от требований рынка; такая деятельность может выполняться вручную или, в случае заводов, где нет дешевой рабочей силы, механизированными сортировщиками. Сортировка — это способ разделения пиломатериалов по общему качеству, направлению волокон, наличию сучков и дефектов, а также по общему виду и т. Д.
Для защиты пиломатериалов от поражения грибами и насекомыми, а также для предотвращения склонности высушенных на воздухе пиломатериалов расслаиваться и раскалываться концы пиломатериалов можно чистить щеткой вручную или механически, погружая их в подготовленный химический раствор. Воск или краска наносится на торцевую часть древесины, подлежащую сушке на воздухе, кистью или распылением, чтобы действовать как герметик, чтобы вызвать более медленное высыхание конечностей и, следовательно, вызвать более сильное высыхание. равномерное высыхание пиломатериалов.
1.2.4 Сушка
Пиломатериал, который не продается в зеленом виде, сушится воздухом или в печи, что улучшает его товарный вид. При сушке и снижении содержания влаги до приемлемого уровня его ценность повышается благодаря тому, что древесина стабилизируется по размерам, а ее прочность и цвет улучшаются; Кроме того, снижение веса снижает транспортные расходы.
Сушка на воздухе включает укладку пиломатериалов штабелями на открытом воздухе или под навесами на подготовленном грунте таким образом, чтобы они подвергались хорошему потоку воздуха до тех пор, пока не будет достигнута требуемая влажность.
Хотя воздушная сушка требует минимальных капитальных и эксплуатационных затрат, она требует большого количества земли, включает в себя большие запасы, которые представляют опасность пожара, а условия и скорость сушки находятся вне контроля оператора верфи.
Сушка в печи, с другой стороны, позволяет пиломатериалам сушиться в закрытой и контролируемой среде, где можно регулировать температуру, циркуляцию воздуха и влажность, чтобы достичь наиболее экономичных условий сушки без ухудшения качества. Две наиболее распространенные печи — это печи периодического и прогрессивного типа. Первый сушит древесину в камерах в качестве загрузки партии, тогда как второй сушит древесину, пока она перемещается по длине печи на грузовиках.
Поскольку на сушку пиломатериалов в печи приходится около 70-90 процентов всей энергии, потребляемой в процессе лесопиления, в настоящее время в лесопильной промышленности становится широко распространенной практикой использовать отходы пиломатериалов в качестве источника топлива, энергетическая ценность которых составляет что может даже быть избыточным для нужд комбината.
1.2.5 Восстановление и наплавка
Перед тем, как складывать пиломатериал на хранение, его обычно проверяют на предмет каких-либо дефектов, которые могли возникнуть в процессе сушки, таких как секущиеся концы, незакрепленные сучки и т. Д., Которые можно удалить путем обрезки и, следовательно, повышения его стоимости.
Дальнейшее улучшение может быть выполнено путем строгания поверхности с использованием строгальных станков с вращающимся ножом или абразивных лент в соответствии с потребностями рынка.
1.3.1 Журнал сортировка, кондиционирование и окорка
1.3.2 Очистка, наматывание и обрезка
1.3.3 Сушка шпона
1.3.4 Сборка
1.3.5 Прессование
1.3.6 Чистовая обработка
На Рисунке 2 представлена типичная схема завода, чтобы проиллюстрировать читателям задействованные процессы.
1.3.1 Сортировка, кондиционирование и окорка бревен
Бревна подходящего размера и качества для резки и очистки обычно сортируются на складе по прибытии по размеру и виду.Погрузочно-разгрузочные работы могут осуществляться с помощью тяжелых погрузчиков, буровых вышек или кранов, размеры которых соответствуют размерам и весу бревен.
Рисунок 2. Производство фанеры — упрощенный технологический процесс
Перед лущением большинство пиломатериалов необходимо кондиционировать, чтобы смягчить древесину, чтобы облегчить лущение и получить шпон приемлемого качества. Кондиционирование включает в себя воздействие тепла и влаги на блоки овощечистки путем замачивания в чанах с горячей водой или воздействия острого пара или струй горячей воды.
Затем происходит окорка бревен для облегчения работы оператора токарного станка и удаления грязи и мусора, которые в противном случае могут нанести вред ножу токарного станка, после чего бревна разрезаются на длину, подходящую для токарного станка, которая обычно составляет 240 -270 см.
1.3.2 Очистка, наматывание и клипсование
В настоящее время почти во всех случаях фанерный шпон разрезается ротационным способом, при этом ножевой блок вращается вокруг своей оси на токарном станке, в то время как сплошной лист шпона разрезается ножом, установленным параллельно оси блока.
Затем лист шпона наматывают на катушки или направляют в систему с несколькими лотками, чтобы обеспечить хранение и перенапряжение в случае колебаний подачи шпона с токарного станка; скорости обеих систем хранения обычно синхронизируются со скоростью токарного станка.
Затем зеленый шпон обрезается по размеру вручную или с помощью высокоскоростных ножей, сортируется и складывается в стопки для сушки. Затем из листа вырезаются любые дефекты, такие как сучки и трещины.
1.3.3 Сушка шпона
Сушка шпона до содержания влаги от двух до десяти процентов предназначена для облегчения процесса склеивания во время производства фанеры. В зависимости от расположения и сложности фанерного завода листы шпона можно оставить для сушки на воздухе или в печи. Сушка в печи включает сушку штабелированного шпона партиями или непрерывную сушку листов, которые механически транспортируются либо на непрерывной ленте, либо на роликовой системе по всей длине сушилки.Очевидно, что контролируемая среда сушки при минимальном обращении приведет к более равномерной сушке шпона с наименьшим количеством повреждений.
На сушку шпона приходится около 70 процентов тепловой энергии, потребляемой при производстве фанеры, и примерно 60 процентов от общей потребности комбината в энергии. По этой причине постоянно разрабатываются новые и улучшенные сушильные системы, а также способы их нагрева.
Нагрев сушилки может осуществляться за счет непрямого использования пара или термического масла или прямого сжигания, при этом температура регулируется регулировкой подпитки свежим воздухом.Хотя температуры сушки от 90 до 160 ° C можно считать нормальными, для некоторых видов используются повышенные температуры примерно до 175 ° C, чтобы сократить общее время сушки.
1.3.4 Сборка
Сборка фанеры перед прессованием заключается в стыковке узких полос шпона, которые склеиваются по кромке с получением листов необходимого размера. Затем клей наносится на внутренние слои или сердцевину, которые, в свою очередь, укладываются между внешними слоями фанеры, готовыми к склеиванию.На эту операцию приходится значительная часть ручного труда, используемого в производственном процессе.
Хотя ручные валковые разбрасыватели являются широко используемым методом нанесения клея, разработка альтернативных систем привела к внедрению навесных устройств для нанесения покрытий, экструдеров, окрасочных камер и т. Д., Каждая из которых имеет свои особенности.
1.3.5 Прессование
После укладки фанеры в виде сборочных листов фанеры их подают в гидравлические прессы, чтобы привести фанеру в непосредственный контакт с клеем, где при нагревании клей отверждается.
Переход от холодных прессов с одним открытием к горячим прессам с несколькими открываниями, с дневным светом от 5 до 25 и работающими при температуре плиты порядка 80–180 ° C, значительно сократил общее время цикла прессования и повысил производительность пресса. Плиты обычно нагреваются горячей водой или паром, хотя термическое масло используется при прессовании при более высоких температурах.
Предварительное холодное прессование при сравнительно низком давлении не используется в современных производственных линиях. Во многом это связано с тем, что со склеенным шпоном легче обращаться и загружать его в пресс для горячего прессования, к тому же уменьшенная толщина слоя позволяет использовать меньшие отверстия для дневного света в прессе для горячего прессования, что приводит к общему сокращению времени загрузки и горячего прессования. .
1.3.6 Чистовая
Первичная отделка, которая включает в себя обрезку, шлифовку и обновление фанеры после прессования, проводится с целью повышения товарности продукта. Она выполняется либо на отдельных рабочих местах, либо, в случае современных мельниц, как комбинированная операция на непрерывной полуавтоматической линии.
Обрезные пилы отрезают фанерные плиты до необходимого размера, которые затем шлифуются на станках, оснащенных широколенточными или барабанными шлифовальными машинами, для получения желаемой гладкости поверхности. Повреждения или дефекты лицевых виниров затем устраняются вручную путем закупоривания и наложения пластырей.
Фанера производится в широком диапазоне размеров и толщины, хотя чаще всего производятся размеры 1220 x 2440 мм вместе с панелями размером 1830 x 3050 мм и 915 x 915 мм. Толщина может составлять от 3 до 25 мм, при этом количество слоев составляет от трех для плит толщиной до 7,5 мм до пяти и более слоев для более толстых сортов.
1.4.1 Подготовка частиц
1.4.2 Сушка частиц и просеивание
1.4.3 Смешивание и формование мата
1.4.4 Прессование
1.4.5 Отделка плит
В большинстве случаев производство частиц включает в себя определенное количество операций, как описано ниже (см. Рисунок 3), которые требуют различных количеств и типов энергии.
Рисунок 3. Производство ДСП — упрощенный технологический процесс
1.4.1 Подготовка частиц
Отделка ДСП производится из множества источников, и по мере того, как конкуренция за твердую древесину и ее остатки возрастает, производителям приходится прибегать к использованию низкосортных отходов, таких как измельченные отходы заводов, опилки, стружка строгальных станков и т. Д. а также ранее не рассматриваемые породы древесины.
Ввиду широкого ассортимента целлюлозы, поставляемой на завод, разделение по размеру и, если возможно, по видам должно проводиться до процесса измельчения.Кора удаляется с бревен, если это еще не сделано в лесу, чтобы избежать затупления ножей измельчителя, а наличие камнеуловителей и магнитных сепараторов предохраняет другое оборудование для измельчения от повреждений, которые в противном случае были бы нанесены, если бы с волокном были внесены противоречия. отделка.
Размер и геометрия частиц, необходимые для внутреннего и поверхностного слоев древесно-стружечных плит, достигаются с помощью разнообразного оборудования для измельчения, которое соответствует разнообразию и размеру используемой древесины и древесных остатков.Измельчители, ножевые дробилки, молотковые дробилки, дисковые рафинеры и т. Д., Каждая из которых работает по разному принципу, с использованием ножей, ударных стержней, рифленых дисковых пластин и т. Д., Лишь некоторые из них широко используются в промышленности.
1.4.2 Сушка и просеивание частиц
Большую часть композиции, поставляемой на комбинат, необходимо высушить, чтобы общий уровень влажности частиц составлял порядка трех-восьми процентов с целью связывания с жидкими смолами.
Сушка частиц — это непрерывный процесс, при котором частицы движутся по длине вращающихся горизонтальных сушилок, будучи подвешенными и подвергаемыми воздействию горячих газов или тепла, излучаемого пучками труб, по которым проходит горячая вода, пар или термическое масло.Тепло образуется при сжигании нефти, газа или технологических остатков. В настоящее время мгновенная сушка рассматривается как приемлемая альтернатива ротационным сушилкам и требует несколько более низких температур сушки.
Непосредственно после сушки частицы просеиваются по размеру на вибрационных или вращающихся ситах или путем классификации по воздуху. Просеивание обычно происходит после сушилок, поскольку влажные частицы имеют тенденцию слипаться, забивая пластины сита и снижая общую эффективность процесса просеивания.
Частицы разделяются по размеру с целью сортировки композиции для лицевого и внутреннего слоев плиты. Важно, чтобы частицы слишком большого размера рециркулировали для дальнейшего восстановления и чтобы мелкие частицы отсеивались, чтобы избежать потребления непропорционального количества связующего на основе смолы и обеспечить ценный источник топлива.
1.4.3 Смешивание и формование мата
Клеи в виде мочевины, фенола и меламиноформальдегида обычно используются для связывания смеси частиц, причем первая из используемых смол является наиболее предпочтительной.От трех до десяти процентов по массе смолы вместе с другими добавками, используемыми для придания таких свойств, как огнестойкость и т. Д., Смешивают в контролируемых условиях порциями или в непрерывном режиме. Смешивание может происходить либо в больших чанах с медленной скоростью, либо в небольших блендерах с быстрым смешиванием и более коротким временем смешивания.
На более современных заводах по производству древесно-стружечных плит формование мата является полностью механическим процессом, в то время как более старые формовщики требуют ручного выравнивания. Несмотря на большое разнообразие доступных в настоящее время формовщиков, основные принципы формирования мата в целом схожи в том, что равномерный поток частиц подается к формовщику из сборного бункера, который, в свою очередь, дозирует равномерно распределенный слой частиц в рама на движущейся ленте или уплотнении.
Формирователи могут быть оснащены одной или несколькими формовочными головками, которые могут быть либо неподвижными, либо подвижными, и сконструированы таким образом, что самые мелкие частицы доставляются для формирования поверхностных слоев мата, а более грубые материалы — для формирования сердцевины. Во всех случаях важно, чтобы был сформирован равномерно распределенный мат желаемого веса. Коврики, не соответствующие стандарту, отбраковываются и перерабатываются.
Транспортировка матов к предварительному прессу и горячему прессу осуществляется путем формования матов на металлических пластинах, называемых калами, которые затем вручную или механически катят к прессам, или, в случае систем без уплотнения, с использованием гибкие металлические ленты, пластиковые ленты и лотки, по которым маты транспортируются к прессу горячего прессования.
1.4.4 Прессование
Предварительное прессование матов перед использованием в многопластовых горячих прессах в настоящее время становится обычным явлением в операции прессования из-за уплотнения и уменьшения ширины мата. Это позволяет упростить обращение и использовать более узкие отверстия в горячем прессе, что значительно сокращает время прессования.
В то время как предварительные прессы могут быть горячего или холодного типа, основной пресс всегда нагревается путем пропускания горячей воды, пара или масла через плиты до температуры порядка 140-200 ° C, в зависимости от используемые смолы и тип пресса.
Могут использоваться горячие прессы с одним или несколькими открываниями, при этом загрузка и разгрузка осуществляется вручную или механически с помощью троса, цепных подъемников или гидравлики, в зависимости от возраста и сложности установки. Хотя в более крупных современных установках и время прессования, и давление регулируются автоматически, на многих заводах по-прежнему отдается предпочтение ручному управлению, поскольку оно позволяет вносить корректировки в зависимости от качества мата.
1.4.5 Доска отделочная
На выходе из горячего пресса доски отделяются от герметиков вручную или механически с помощью цепей или поворотных устройств.Уплотнения укладываются в стопку, дают остыть, а затем возвращаются на станцию формования на толкающих тележках или механически транспортируются по фиксированной возвратной линии. Плиты, в свою очередь, охлаждаются и кондиционируются, чтобы избежать разложения смол мочевины.
Обрезные пилы используются для обрезки досок по размеру, при этом обрезки кромок либо перерабатываются, либо используются в качестве топлива. Чтобы соответствовать установленным стандартам в отношении толщины и качества поверхности, можно использовать комбинацию ножевых строгальных станков и ленточных или барабанных шлифовальных машин.
После обработки поверхности досок их разрезают на размер по длине и ширине с помощью комбинации пил в соответствии с требованиями рынка. ДСП обычно выпускается в виде панелей размером 1220 x 2440 мм и толщиной от 3 до 35 мм, из которых 19 мм являются наиболее распространенными. Обычно плиты производятся в диапазоне средней плотности 400-800 кг на кубический метр, хотя в качестве основного материала используется плита высокой плотности 800-1120 кг на кубический метр.
UPM Plywood начинает использовать новый экологически чистый WISA BioBond
(UPM Plywood, Лахти, Финляндия, 2 октября 2017 г., 13:00 EET) — UPM Plywood начинает использовать новую экологически безопасную технологию склеивания WISA BioBond на основе лигнина при производстве фанеры.В новой технологии 50% фенола на основе ископаемых заменено лигнином, полученным как побочный продукт производства крафовой целлюлозы.
«Наша долгосрочная цель заключалась в разработке технологии склеивания с использованием лигнина в качестве сырья. Достигнутый сейчас технологический прорыв является наиболее значительным нововведением в склеивании фанеры за пять десятилетий», — говорит Сюзанна Ринне , вице-президент, Развитие бизнеса в UPM Plywood.
UPM Plywood планирует постепенно внедрять новую технологию склеивания на всех своих фанерных заводах.
Фанера, изготовленная по новой технологии склеивания, по своим техническим характеристикам не уступает традиционным. Поэтому продукты WISA BioBond напрямую заменяют старые продукты. Смена технологии склейки не оказывает практического влияния на конечных пользователей и не требует каких-либо действий с их стороны. Клиенты смогут использовать устойчивость нового WISA BioBond в своем собственном бизнесе постепенно по мере внедрения технологии.
«Устойчивое и эффективное использование сырья — один из краеугольных камней стратегии UPM Biofore.WISA BioBond — яркий пример этой стратегии на практике. Благодаря межотраслевому сотрудничеству мы разработали технологию склеивания, которая делает нашу фанерную продукцию WISA самой экологичной на рынке », — говорит Мика Силланпяя, , исполнительный вице-президент UPM Plywood.
Возможность использовать облицовку, полученную в результате -продукт получения крафт-целлюлозы при склеивании древесины изучается давно, WISA BioBond основан на запатентованной технологии лигнина UPM BioPiva, разработанной UPM Biochemicals. UPM Plywood теперь выводит на рынок первую продукцию из фанеры, на которую подана заявка на патент, в которой используется эта технология.
Более подробная информация о технологии WISA BioBond доступна на сайте www.wisabiobond.com.
За дополнительной информацией обращайтесь:
Сюзанна Ринне, вице-президент по развитию бизнеса, UPM Plywood, тел. +358 40 574 1270
Юусо Конттинен, вице-президент UPM Biochemicals, тел. +358 40 531 7405
UPM Plywood, по связям с заинтересованными сторонами
пн-пт 9.00-16.00 EET
тел. +358 204 151 13
[email protected]
UPM Plywood производит высококачественную фанеру и шпон WISA ® , в основном для строительной и транспортной промышленности, а также новый термоформованный древесный материал UPM Grada ® . для формовочной промышленности. Продажи UPM Plywood в 2016 году составили 444 миллиона евро, в компании работает около 2400 сотрудников. UPM Plywood владеет шестью фанерными и фанерными заводами в Финляндии, а также фанерными заводами в России и Эстонии — www. wisaplywood.com, www.upmgrada.com
Следите за новостями UPM Plywood в Twitter | LinkedIn | Facebook | YouTube | Instagram
UPM Biochemicals предлагает устойчивые и конкурентоспособные биохимические продукты на основе древесины для различных промышленных целей без ущерба для характеристик продукта. Основным сырьем для нашей продукции является сертифицированная древесина из устойчиво управляемых лесов. Мы разрабатываем новые биологические материалы для биомедицинской и других отраслей.Мы стремимся ускорить разработку новых решений благодаря нашему сотрудничеству с рядом различных партнеров — www.upmbiochemicals.com
UPM
Посредством обновления био- и лесной промышленности UPM строит устойчивое будущее в шести сферах деятельности. : UPM Biorefining, UPM Energy, UPM Raflatac, UPM Specialty Papers, UPM Paper ENA и UPM Plywood. Наша продукция изготовлена из возобновляемого сырья и подлежит вторичной переработке. Мы обслуживаем клиентов по всему миру. В группе работает около 19 300 человек, а ее годовой объем продаж составляет около 10 миллиардов евро.Акции UPM котируются на NASDAQ OMX Helsinki. UPM — Компания Biofore — www.upm.com
Следите за новостями UPM в Twitter | LinkedIn | Facebook | YouTube | Instagram | upmbiofore.com
История производства APA, фанеры и конструкционной древесины
APA — The Engineered Wood Association — это некоммерческая торговая ассоциация индустрии конструкционных изделий из дерева США и Канады. Базирующаяся в Такоме, штат Вашингтон, Ассоциация состоит из производителей конструкционной фанеры, ориентированно-стружечных плит (OSB), поперечно-клееной древесины, клееного бруса (клееного бруса), деревянных двутавровых балок и клееного бруса (LVL).
APA была основана в 1933 году как Ассоциация фанеры из пихты Дугласа с целью продвижения интересов растущей фанерной промышленности северо-западного Тихоокеанского региона. Улучшения клея и технологии в конечном итоге привели к производству структурной фанеры из южной сосны и других пород, и в 1964 году Ассоциация изменила свое название на Американская фанерная ассоциация (APA), чтобы отразить национальный масштаб ее растущего членства.
Состав Ассоциации снова расширился в начале 1980-х годов с введением ориентированно-стружечных плит (OSB), продукта, который Ассоциация помогла вывести на рынок путем разработки новых стандартов производительности панелей.Десять лет спустя APA приняла производителей изделий из древесины без панелей, таких как клееный брус, деревянные двутавровые балки и клееный брус.
Чтобы лучше отразить расширяющийся ассортимент продукции и географический диапазон своего членства, Ассоциация снова изменила свое название в 1994 году на APA — The Engineered Wood Association . Сокращение «APA» было сохранено в названии, потому что оно было широко известно и уважаемо на рынке.
История фанеры
Древнее происхождение фанеры
Археологи обнаружили следы клееного дерева в гробницах египетских фараонов. Тысячу лет назад китайцы стригли дерево и склеивали его для изготовления мебели. Сообщается, что англичане и французы обрабатывали дерево по общему принципу фанеры в 17 и 18 веках. И историки считают, что царская Россия изготавливала формы из фанеры еще до 20 века. Фанера ранней современной эпохи обычно изготавливалась из декоративных твердых пород дерева и чаще всего использовалась в производстве предметов домашнего обихода, таких как шкафы, сундуки, столешницы и двери. Строительная фанера из хвойных пород не появлялась на рынке до 20 века.
Фанера запатентована, а потом забыта
Первый патент на то, что можно назвать фанерой, был выдан 26 декабря 1865 года Джону К. Мэйо из Нью-Йорка. В переиздании этого патента, датированном 18 августа 1868 года, разработка Мэйо описывалась следующим образом: «Изобретение состоит в цементировании или другом скреплении вместе ряда этих чешуек листов с зернистостью следующих друг за другом частей или некоторых из них. , идущий поперек или иначе, чем у других… »У Мэйо могло быть видение, но, очевидно, не было большого делового чутья, поскольку история не свидетельствует о том, что он когда-либо извлекал выгоду из своих патентов.
В 1905 году город Портленд, штат Орегон, готовился к проведению Всемирной выставки в рамках празднования 100-летия экспедиции Льюиса и Кларка. Несколько местных предприятий попросили подготовить экспонаты для мероприятия, в том числе Portland Manufacturing Company, небольшую фабрику по производству деревянных ящиков в районе Сент-Джонс города. Совладелец и директор завода Густав Карлсон решил ламинировать древесные панели из различных хвойных пород Северо-Запада Тихоокеанского региона.Используя кисти для нанесения клея и домкраты в качестве прессов, несколько панелей были выставлены для демонстрации. Продукт, получивший название «3-слойный шпон», вызвал значительный интерес у посетителей выставки, в том числе у нескольких производителей дверей, шкафов и сундуков, которые затем разместили заказы. К 1907 году компания Portland Manufacturing установила автоматический разбрасыватель клея и ручной секционный пресс. Производство выросло до 420 панелей в день. Так родилась индустрия.
От дверей до подножек: первые рынки фанеры
В течение первых 15 лет производство фанеры хвойных пород в основном полагалось на единственный рынок — дверные панели.Но в 1920 году «супер-продавец» Гас Бартеллс из компании Elliott Bay Plywood в Сиэтле начал привлекать клиентов в автомобильную промышленность. Ранее Bartells основал первые представительства по продаже фанеры по всей стране и не менее успешно убедил производителей автомобилей использовать фанеру для подножек. В эпоху джаза рынок начал расти, и отрасль стабильно росла. К 1929 году на Тихоокеанском Северо-Западе насчитывалось 17 фанерных фабрик, а объем производства достиг рекордных 358 миллионов квадратных футов (3/8-дюймовая основа).
Технологический прорыв: водостойкий клей
Отсутствие водостойкого клея, которое могло бы сделать фанеру пригодной для наружного воздействия, в конечном итоге привело к тому, что производители автомобилей перешли с фанеры на более прочные металлические подножки. Прорыв произошел в 1934 году, когда доктор Джеймс Невин, химик из Harbour Plywood Corporation в Абердине, штат Вашингтон, наконец, разработал полностью водостойкий клей. Этот технологический прогресс мог открыть новые важные рынки.Но отрасль оставалась фрагментированной. Качество продукции и системы сортировки сильно различались от фабрики к фабрике. У отдельных компаний не было технических или, в большинстве случаев, маркетинговых ресурсов для исследования, разработки и продвижения новых видов использования фанеры. Промышленность обратилась за помощью к недавно созданной торговой ассоциации Douglas Fir Plywood Association.
Основание Ассоциации фанеры из пихты Дугласа
В первые годы существования отрасли было предпринято несколько неудачных попыток создать фанерную ассоциацию.Наконец, 16 мая 1933 года несколько производителей еловой фанеры встретились в старом отеле Портленд, чтобы обсудить целесообразность принятия определенных торговых практик, прежде чем промышленность будет вынуждена сделать это в соответствии с Законом о национальном восстановлении эпохи депрессии. Позже этот закон был объявлен неконституционным, но на какое-то время заставил фанерную промышленность организовать свою деятельность. Последовал месяц переговоров, и 13 июня 1933 года Ассоциация фанеры из пихты Дугласа провела свое первое регулярное собрание в отеле Winthrop в Такоме, штат Вашингтон.Новая ассоциация боролась, пока в 1938 году она не наняла легендарного гуру по развитию бизнеса У. Э. «Диффа» Диффорда.
Стандартизация и улучшенное тестирование качества увеличивают продажи
Ассоциация фанеры из пихты Дугласа была одной из первых, кто воспользовался преимуществом закона 1938 года, разрешившего регистрацию товарных знаков в масштабах всей отрасли, что позволило продвигать фанеру как стандартизированный товар, а не под отдельными торговыми марками. В том же году FHA приняла наружную фанеру, частично основываясь на новом коммерческом стандарте, который включал тесты производительности как внутренней, так и внешней фанеры.Эти разработки помогли открыть путь к более успешному продвижению преимуществ фанеры в строительной отрасли. «Dri-Bilt With Plywood» стал привычным рекламным слоганом. Было построено более миллиона недорогих домов Dri-Bilt с черным полом и обшивкой PlyScord под торговой маркой DFPA, потолками и стенами PlyWall, встроенными панелями PlyPanel и сайдингом PlyShield. В 1940 году ассоциация спонсировала «Дом под солнцем», первый из многих демонстрационных домов из фанеры. Растущая репутация фанеры как прочного и долговечного строительного материала вскоре подверглась суровому испытанию войной.
Фанера идет на войну
Вторая мировая война была испытательным полигоном для фанеры. Этот продукт был объявлен незаменимым военным материалом, а его производство и распространение находились под строгим контролем. Промышленные заводы времен войны — к настоящему времени их насчитывается около 30 — производили от 1,2 до 1,8 миллиарда квадратных футов в год. Повсюду возникли фанерные бараки. Военно-морской флот патрулировал Тихий океан на фанерных катерах. Военно-воздушные силы выполняли разведывательные задания на фанерных планерах. И армия переправилась через Рейн на фанерных штурмовых катерах.Были тысячи военных принадлежностей, сделанных из фанеры — от ящиков для деталей машин, хижин для знаменитых морских обитателей в южной части Тихого океана, до спасательных шлюпок на сотнях кораблей, которые обеспечивали открытые линии снабжения в Атлантическом и Тихом океане.
Послевоенный бум
Когда война закончилась, промышленность была готова удовлетворить растущий спрос в условиях бурно развивающейся послевоенной экономики. В 1944 году 30 заводов отрасли произвели 1,4 миллиарда квадратных футов фанеры. К 1954 году промышленность выросла до 101 завода, а производство приблизилось к 4 миллиардам квадратных футов.В том же году Стэнфордский исследовательский институт предсказал, что спрос на фанеру вырастет до 7 миллиардов футов к 1975 — 21 году в будущем. Хотя некоторые были настроены скептически, добыча выросла до 7,8 миллиарда футов всего за пять лет, а к 1975 году только в США производство превысило 16 миллиардов квадратных футов, что более чем вдвое превысило прогноз.
Фанера идет на север
С ее богатыми лесными ресурсами было вполне естественно, что Канада присоединилась к тому, что в конечном итоге превратилось в настоящую фанерную промышленность Северной Америки.Первая канадская фанера была произведена в 1913 году на заводе Fraser Mills, Нью-Вестминстер, Британская Колумбия, но только в 1935 году был открыт второй завод — компанией H.R. MacMillan. В 1950 году пять канадских компаний основали Ассоциацию производителей фанеры Британской Колумбии (PMBC), которая в конечном итоге превратилась в Канадскую ассоциацию фанеры (CANPLY). Канадская ассоциация стандартов опубликовала первый канадский стандарт на фанеру в 1953 году, основанный на спецификациях, разработанных PMBC.
Возвышение южной сосны
Более полувека производство фанеры хвойных пород располагалось исключительно на северо-западе Тихого океана и в Британской Колумбии, используя обширные запасы пихты Дугласа в этом регионе.До середины века не было известно, как эффективно склеить шпон хвойных пород, произрастающих в других регионах. Но в конце 1950-х — начале 60-х годов исследования и разработки изменили ситуацию, и в 1964 году компания Georgia-Pacific Corporation открыла первый завод по производству фанеры из южной сосны в Фордайсе, штат Арканзас. Ассоциация фанеры из пихты Дугласа изменила свое название в том же году, чтобы отразить тот факт, что фанерная промышленность теперь стала национальной по своему охвату. Сегодня около двух третей всей фанеры в США производится на Юге.
Технологии идут впереди
Фанеру часто называют оригинальным конструктивным деревянным продуктом, потому что она была одной из первых, которая была изготовлена путем соединения вместе вырезанных или переработанных кусков дерева, чтобы сформировать более крупный и цельный композитный блок, более прочный и жесткий, чем сумма его частей. Поперечно-ламинированные слои деревянного шпона фактически улучшают присущие древесине структурные преимущества, распределяя прочность древесины вдоль волокон в обоих направлениях. Эта идея «воссоздания» древесного волокна для производства строительных материалов, превосходящих древесину, в последнее время привела к технологической революции и возникновению совершенно новой отрасли производства изделий из древесины. В конце 1970-х — начале 80-х годов, например, принцип фанеры дал начало тому, что сегодня является мировой отраслью производства стружечных плит или OSB. Вместо сплошных листов шпона OSB изготавливается из небольших деревянных прядей, склеенных между собой слоями перекрестного ламинирования. К другим конструкционным изделиям из дерева сегодня относятся деревянные двутавровые балки, клееный брус, клееный брус и пиломатериалы с ориентированной стружкой. Эти продукты не только обладают превосходными эксплуатационными характеристиками, но и позволяют более эффективно использовать ценные лесные ресурсы.А началось все с фанеры.
История клееного бруса
Клееный брус впервые был использован в Европе в начале 1890-х годов. Патент 1901 года из Швейцарии положил начало строительству из клееного бруса. Одной из первых конструкций из клееного бруса, возведенных в США, была исследовательская лаборатория в лаборатории лесных товаров Министерства сельского хозяйства США в Мэдисоне, штат Висконсин. Сооружение было возведено в 1934 году и эксплуатируется до сих пор.
Значительным достижением в производстве клееной древесины стало введение в 1942 году полностью водостойких фенолрезорциновых клеев.Это позволило использовать клееный брус в открытых внешних средах, не опасаясь деградации клейкого слоя.
Первым производственным стандартом в США для клееной древесины был коммерческий стандарт CS253-63, опубликованный Министерством торговли в 1963 году. Самым последним стандартом является стандарт ANSI A190.1.
Деревянные двутавровые балки и Rim Board®
Первоначально коммерциализированные Trus Joist Corporation (ныне компания Weyerhaeuser) в 1960-х годах, инженерные деревянные двутавровые балки своим началом, по крайней мере частично, обязаны публикации, разработанной Douglas Fir Plywood Association (предшественник APA — The Engineered Wood Association ) в 1959 году под названием DFPA Specification BB-8, Design of Plywood Beams . Эта спецификация, позже опубликованная как Приложение 2 к техническим условиям на проектирование фанеры «Проектирование и изготовление клееных балок из фанеры и пиломатериалов», в общих чертах описывает исходные процедуры проектирования, которые в конечном итоге легли в основу текущих рекомендаций по проектированию.
Первым общепризнанным стандартом для деревянных двутавровых балок был и остается ASTM D5055, Стандартные технические условия для установления и контроля структурной способности сборных деревянных двутавровых балок. Этот консенсусный стандарт содержит рекомендации по оценке механических свойств, физических свойств и качества деревянных двутавровых балок и является текущим общим стандартом испытаний двутавровых балок.Однако, поскольку ASTM D5055 не определяет требуемых уровней производительности, отдельные производители двутавровых балок обычно имеют свои собственные фирменные стандарты, которые регулируют повседневную практику производства их продуктов. Как показала история других строительных материалов, таких как фанера и ориентированно-стружечная плита (OSB), некоторая степень стандартизации отрасли неизбежна. Также неизбежно то, что вместе со стандартизацией произойдет повышение эффективности производства и более широкое использование в строительстве.
Чтобы удовлетворить эту потребность в стандартных уровнях производительности, APA, совместно с несколькими производителями двутавровых балок, разработала стандарты, основанные на характеристиках, для изделий из деревянных двутавровых балок с рейтингом рабочих характеристик. Первый такой стандарт производительности APA предназначен для использования деревянных двутавровых балок в жилых полах и обозначен как PRI-400, хотя кровельные столы и детали также были разработаны для балок PRI-400. Следует отметить, что это добровольный стандарт, и не все производители двутавровых балок решили производить продукцию PRI-400.
Береза в производстве фанеры Технология и производственный процесс — Фанера
Береза в производстве фанеры Технология и производственный процесс
Фанера — это плита, изготовленная из тонких листов строительного шпона , которые соединены слоями для создания прочной и устойчивой плиты. Шпон, используемый для строительства из фанеры, вырезается из бревна для строительных или декоративных целей. Два наиболее распространенных метода, используемых для производства шпона, называются распилом и вращающейся распиловкой .С другой стороны, конструкционные виниры режут с использованием второго метода, называемого ротационной резкой. Лезвие ножа очищает тонкие листы дерева, и это эффективный способ изготовления фанеры, так как их можно разрезать на любую ширину. Чаще всего для изготовления фанеры используют нечетное количество слоев шпона, минимум три. Однако количество используемых шпонов зависит от их толщины и готовой фанерной плиты. Виниры склеены клеем под прямым углом друг к другу, чтобы уменьшить усадку и повысить прочность.
Для производства фанеры могут использоваться разные породы, при этом облицовка и сердцевина могут быть изготовлены из разных пород, или один и тот же вид может использоваться для всей конструкции плиты. Поверхность фанерной доски состоит из шпона, называемого лицевым слоем . В зависимости от качества слой лучшего качества называется лицевой стороной, а другой слой — задней стороной. Для обозначения качества слоев используется буквенный код, обозначающий сорт. В системе оценок используются буквы E, B, BB и C, где оценка E (элита) означает лучшее качество, а оценка C означает самое низкое качество.Марки относятся только к внешнему виду лицевых слоев , и не указывают на структурные характеристики фанерной плиты , . Фанера изготавливается самых разных размеров. Наиболее распространенные размеры (мм): длина — 1525, 2440 и 3010, ширина — 1220, 1525. Толщина фанеры может составлять от 3 до 40 мм в зависимости от области применения.
Обычный клей называется формальдегидом и состоит из углерода, водорода и кислорода.Формальдегид — это химическое вещество, которое существует в природе и вырабатывается растениями и животными, а также промышленное химическое вещество. Важной характеристикой фанеры является количество выделяемого формальдегида. Контакт с формальдегидом может вызвать кратковременное раздражение кожи. Однако длительное воздействие формальдегида может вызвать серьезные проблемы со здоровьем (канцерогенные). Выбросы формальдегида могут быть оценены как E1 (9 мг / 100 г или меньше), E-0
Фанера березовая
Распространенная древесина лиственных пород , порода, используемая для производства фанеры, — береза.Доска из березовой фанеры считается одним из самых популярных видов фанеры благодаря своим превосходным механическим свойствам и красивому внешнему виду. Березовую фанеру можно использовать как для внутренних, так и для наружных работ. В процессе производства фанеры березовые бревна должны быть ровными и иметь определенный размер. В производственном процессе утилизируется только 50% березового полена. Сердцевину березового бревна использовать нельзя, поэтому отходы обычно продают другим деревоперерабатывающим предприятиям.Преимущество березы заключается в ее быстром росте (30-35 лет) по сравнению с другими породами древесины, например, елью. В то же время скорость роста может негативно сказаться на качестве березовых поленьев.
Исторический обзор производства фанеры
Производство фанеры происходило еще в Древнем Египте, где изготавливали изделия из дерева
с использованием пиленого шпона. Тонкие листы шпона высокого качества наклеивались на подложку более низкого качества.Этот процесс был обычным делом из-за отсутствия ценных пород дерева, а высококачественные листы шпона придали дереву красивый внешний вид.
В 18-19 веках производители мебели в Англии использовали шпон для производства мебели высочайшего качества.
Иммануэль Нобель изобрел современную технику вращающейся резки шпона, и первое производственное оборудование было построено в США в 19 веке. «На протяжении десятилетий фанера была одним из самых распространенных строительных материалов.”В начале 19 века Томас Дж. Отцен был владельцем компании Portland Manufacturing Company, США, которая была первым предприятием по производству фанеры. Он внес свой вклад в развитие производства фанеры, сократив процесс сушки и производства. Благодаря его открытиям новая технология сыграла важную роль в «превращении фанеры в один из самых распространенных и доступных строительных продуктов из когда-либо производимых».
Применение фанеры
Как показано на рисунке 11, фанеру можно использовать для самых разных целей (Jackson et.др., , 1990). Внутренняя фанера включает мебель и стеновые панели, в то время как внешняя фанера подходит для кухонных принадлежностей и применений вокруг душевых и ванных комнат. Другой тип фанеры — это конструкционная фанера, которая производится для применений, где прочность и долговечность являются основными факторами. Конструкционная фанера используется в строительстве и строительстве. Чаще всего для опалубки используется фанера из-за ее прочности, устойчивости и устойчивости к изменениям температуры и влажности.Наконец, морская фанера используется там, где требуется влагостойкость. Фанеру также можно использовать для строительства транспортных средств, лодок и упаковки.
Промышленное производство фанеры основано на опыте и ноу-хау нескольких поколений.
Бизнес-модель фанерной промышленности все больше ориентируется на ноу-хау, управление производственными технологиями и обслуживание клиентов. Фанера производится из северной мягкой древесины и березы, которые подходят для изготовления фанеры, требующей долговечности. По словам Мика Силланпяя , исполнительного вице-президента UPM Plywood, успех финской фанеры в требовательных конечных областях применения является результатом многих поколений производственного опыта и ноу-хау.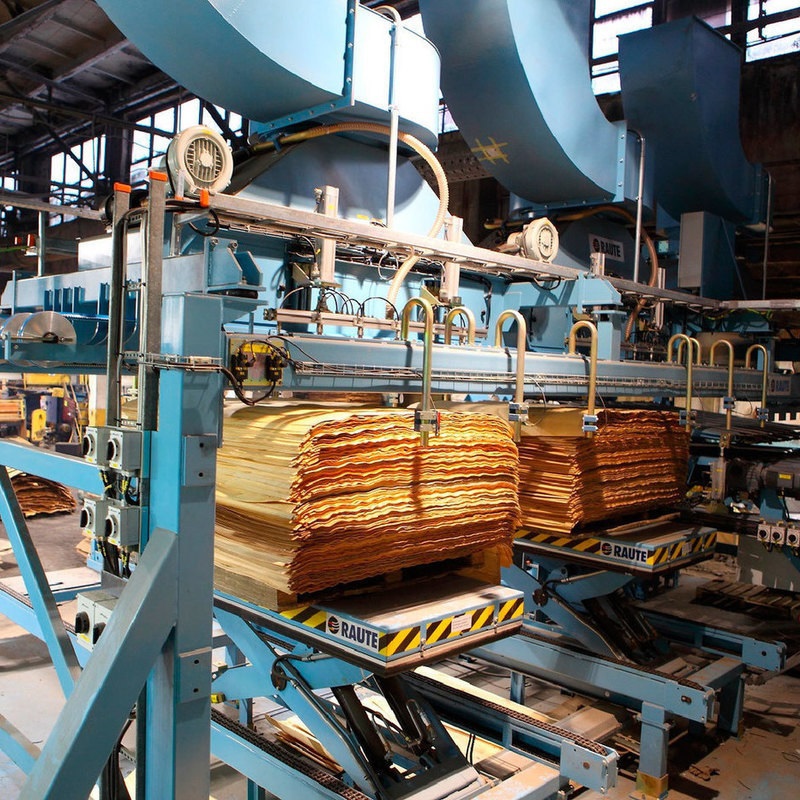
Мировые тенденции благоприятствуют использованию фанеры
По словам Мики Силланпяя, исполнительного вице-президента UPM Plywood, основными глобальными тенденциями развития являются увеличение использования фанеры в нескольких отраслях. «Урбанизация увеличивает количество новых зданий с фанерой, но этот материал также имеет много потенциальных применений при ремонте и расширении. Одновременно с ростом электронной коммерции увеличились грузовые перевозки, где фанера является ключевым материалом для полов при строительстве транспортного оборудования ».
По словам Силланпяя, легкий вес фанеры является важным активом в транспортной отрасли.«Экологические ценности постоянно увеличивают спрос на возобновляемые и более легкие материалы», — говорит Силланпяя.
«Задачи, поставленные в борьбе с изменением климата, увеличивают использование возобновляемых древесных материалов во всем строительстве. Мы также повышаем экологичность, отказываясь от старых фенольных клеев на основе ископаемых, используемых в производстве фанеры, и заменяя их возобновляемыми вариантами на основе лигнина ».
Строительство резервуаров для жидкого азота (СПГ) было стабильным бизнесом в течение трех десятилетий.Успех UPM в отрасли основан, в частности, на изоляционных свойствах березовой фанеры в экстремально холодных условиях. Во время транспортировки температура газа составляет минус 163 градуса, а березовая фанера хорошо сохраняет свою прочность, несмотря на экстремальные минусовые температуры.
«Танкеры СПГ большие, а это значит, что в их конструкции используются большие объемы фанеры. На одну цистерну требуется от одной до трех тысяч кубометров фанеры в зависимости от технологии утепления.Транспортировка СПГ находится на подъеме, что отражается в строительстве подходящих транспортных судов », — заключает Силланпяя.
Помимо строительной индустрии и строительства транспортного оборудования и резервуаров для СПГ, фанера производится для мебельной промышленности, а также для внутренней отделки и производства паркета. «Обычно эти конечные пользователи потребляют высококачественную фанеру в более высоких ценовых диапазонах, и мы инвестировали в развитие производства и сеть обслуживания конечных потребителей, чтобы обслуживать этих клиентов. ”
Новые инвестиции для увеличения производства фанеры
Строительство в Европе растет после длительного спада, и рост значительно увеличил спрос на фанеру. Строительство — это крупнейший сектор конечного использования фанеры. По словам Силланпяя, фанерный бизнес позиционирует себя как производитель материалов в строительной отрасли и не заинтересован в том, чтобы заходить слишком далеко в сферу конечного использования своих клиентов.«Когда мы работаем через дистрибьюторские сети, мы можем продавать продукцию любому оптовику, которого пожелаем.Что касается количества использованной и потребляемой фанеры, для нас не имеет большого значения, будет ли метод строительства бетонным или деревянным. В бетонных конструкциях, среди прочего, используется фанера в литейных формах ».
Большая часть фанеры, используемой в строительстве, — это фанера хвойных пород. Березовая фанера, будучи более прочной и более ценной, используется в промышленной переработке. На один кубометр фанеры нужно два кубометра древесины хвойных пород, а на такое же количество березовой фанеры нужно три кубометра березовой древесины.«Доступность березы будет серьезной проблемой в будущем, так как Финляндия и Россия — единственные регионы, где дерево растет в количестве, необходимом для промышленного использования».
«Расширение завода в Чудово в России — важный шаг в реализации нашей будущей стратегии, которая включает обеспечение поставок сырья. Наша цель — еще больше укрепить наши позиции в наиболее важных областях применения фанеры. Добавленные мощности по производству березовой фанеры являются конкурентоспособными, что улучшает нашу способность удовлетворять растущий спрос на ключевых рынках », — напоминает нам Силланпяя.
По оценке Силланпяя, наличие сырья будет увеличиваться как побочный эффект инвестиций в новый целлюлозный завод. «Поскольку спрос на всю древесину увеличивается, наличие видов древесины, необходимых для деревообрабатывающей промышленности, должно улучшиться вслед за увеличением производства целлюлозы. А поскольку мы покупаем самую дорогую часть бревна, это тоже хорошая новость для лесовладельцев ».
По словам Силланпяя, Финляндия имеет хорошую репутацию в деревообрабатывающей промышленности как поставщик и экспортер.«Мы используем сертифицированную древесину в своей обработке, и у нас нет этических проблем в нашем производстве».
В последние годы UPM инвестировала в увеличение производства в Финляндии и Эстонии, а также в настоящее время расширяет фанерный завод в Чудово, Россия. Общая стоимость инвестиций составляет 50 миллионов евро. Инвестиции увеличат производственную мощность завода на 45 000 кубических метров, увеличивая годовой объем до 155 000 кубических метров, и расширит ассортимент продукции завода. На территории завода также строится новая электростанция, работающая на биомассе.
UPM Plywood — ведущий производитель фанеры в Европе, поставляющий фанеру и шпон, в частности, для нужд строительной и транспортной отраслей. Компания также производит древесный материал UPM Grada, пригодный для компрессионного формования. Компания работает в десяти разных странах, имеет в общей сложности девять заводов и около 2500 сотрудников. Оборот в прошлом году составил 484 миллиона евро.
Эта статья является частью серии статей, написанных Маркку Лаукканеном и Микко Вильякайненом.В серии представлены различные передовые практики и тенденции финской деревообрабатывающей промышленности. Цель состоит в том, чтобы распространять информацию о передовых методах и решениях в финской деревообрабатывающей промышленности для повышения ее конкурентоспособности и более широкого распространения финского опыта. Статьи будут опубликованы на финском и английском языках. Они будут бесплатно доступны для использования в качестве исходного материала и для публикации в том виде, в котором они есть. Статьи будут распространяться в виде информационных бюллетеней Puuinfo, а также будут опубликованы на сайте puuinfo.fi и woodproducts.fi. Данная серия статей финансируется Операционной программой деревянного строительства Министерства окружающей среды.