Определяем экономическую эффективность производства европоддона
Особенности учета тары
Вопросам регулярного анализа и снижения себестоимости продукции вспомогательных цехов производственного предприятия обычно уделяется мало внимания. В первую очередь это касается деревообрабатывающих цехов, которые, как правило, производят деревянную тару для упаковки, транспортировки, хранения и реализации на сторону продукции основных цехов. Чтобы понять, почему так происходит, кратко рассмотрим особенности учета тары, производимой в деревообрабатывающих цехах производственного предприятия.
К деревянной таре относятся деревянные бочки, контейнеры, ящики и поддоны. Как деревянная, так и прочая тара может быть невозвратной и возвратной (оборотной).
Если тара невозвратная, ее стоимость должна быть включена в общую стоимость реализуемого товара с выделением или без выделения в отгрузочных документах количества и стоимости тары в отдельной строке.
В случае если в договоре предусмотрено, что тара возвратная, покупатель должен ее вернуть. Однако на практике заказчики по разным причинам тару возвращают не всегда.
Самые частые причины невозврата тары — существенные транспортные расходы, связанные с организацией доставки тары обратно поставщику, или длительное хранение на складах покупателя закупленного товара вместе с предоставленной ему в залог тарой. Поэтому большинство предприятий-поставщиков взимают залоговую стоимость возвратной тары при реализации товара.
Стоимость залога, как правило, соответствует рыночной стоимости тары. Но если сумма залога очень высока, покупатель может отказаться не только от тары, но и от покупки товара.
Важно!
Себестоимость производимой на предприятии тары и ее цена (как в случае ее возвратности, так и при продаже невозвратной тары) не должны быть выше ее рыночной стоимости.
При этом на предприятиях, устанавливая цену реализации или залоговую стоимость в пределах рыночной цены, чтобы избежать нареканий и отказов покупателей, не всегда контролируют рентабельность реализации тары:
- во-первых, потому, что если тара возвратная, считается что она поступит обратно на склад предприятия-поставщика и никаких убытков предприятие не понесет;
- во-вторых, не рассчитывается фактическая себестоимость тары, а ее учет осуществляется по плановой себестоимости, которая не отражает реальных фактических затрат.
Рассмотрим, как обычно на практике осуществляется учет и контроль себестоимости и уровня рентабельности изготовления тары на предприятии по отношению к рыночной цене.
Бухгалтерский учет тары внутри организации-поставщика и производителя тары ведется в соответствии с Методическими указаниями по бухгалтерскому учету материально-производственных запасов, утвержденными Приказом Минфина России от 28.12.2001 № 119н (в ред. от 24.12.2010; далее — Методические указания).
В соответствии с п. 176 Методических указаний полученная возвратная тара учитывается у поставщика по дебету счета «Материалы» (субсчет «Тара и тарные материалы») по фактической себестоимости или учетной цене в корреспонденции с кредитом счета учета расчетов.
Вместе с тем в целях бухгалтерского учета внутри организации на тару в большинстве случаев устанавливаются либо утвержденная стоимость (цена реализации тары), либо плановая себестоимость. Это связано с тем, что при большом ассортименте изделий, выпускаемых деревообрабатывающим цехом, ежемесячный расчет фактической себестоимости каждого изделия — длительный и трудоемкий процесс.
К сведению
Под расчетом фактических затрат на изготовление одного вида изделия подразумевается полный учет фактического расхода каждой из разновидностей пиломатериалов с корректным распределением на продукцию фактических отходов производства, используемой фурнитуры, метизов и пр. на каждое изделие, а также учет фактических затрат труда и энергоносителей и пр.
При закрытии отчетного периода в бухгалтерской программе формируется фактическая себестоимость изделий. Однако в целях контроля уровня рентабельности производства и реализации тары эти данные используются крайне редко, прежде всего в связи с их неактуальностью.
Нередко фактическая себестоимость, сформированная по данным бухгалтерского учета, не совсем корректная в связи с неправильным отнесением затрат и отходов на конкретную продукцию.
Планово-экономический отдел, в свою очередь, формирует для бухгалтерского учета плановую себестоимость тары, основанную на единожды утвержденных нормах расхода, нормативах и расценках.
Плановая себестоимость тары рассчитывается на основании норм, выданных в планово-экономический отдел при отсутствии технолога, как правило, мастером или начальником деревообрабатывающего цеха. Нормы зачастую не предусматривают постоянного изменения параметров входящего пиломатериала.
Кроме того, цены на пиломатериал также не стоят на месте.
Несмотря на это, плановая себестоимость тарной продукции может не пересматриваться на предприятии достаточно долго. Соответственно, не предпринимаются и меры к снижению себестоимости.
Снизить себестоимость изготавливаемых в деревообрабатывающем цехе изделий, в том числе тары, и сделать их производство рентабельным можно: всегда есть резервы экономии — за счет рационального использования материалов, снижения трудоемкости продукции и, конечно, за счет сокращения накладных расходов, которые прямо пропорционально зависят от производительности и объемов выпуска продукции в цехе.
Расчет себестоимости европоддона
На примере производства европоддонов, выпускаемых по ГОСТ 9557-87 (рис. 1), рассмотрим, насколько выгодно их производство в небольшом деревообрабатывающем цехе.
Почему европоддон? На крупном производственном предприятии заказывают тару для упаковки и транспортировки своей продукции основные цеха и отдел логистики, которые мало интересуются разновидностями всевозможных поддонов, себестоимостью тары и особенностями ее производства и в большинстве случаев заказывают европоддоны как самую известную на рынке тару.
Л. И. Киюцен,
начальник ПЭО ООО «Корпорация Маяк»
www.profiz.ru
оборудование, технология, рентабельность. Европоддон :: SYL.ru
Поддоны (паллеты) являются незаменимыми на любом складе. С их помощью перемещается и хранится груз, разгружаются товары, облегчается их учет и многое другое. Как осуществляется производство поддонов, на каком оборудовании, какова технология их изготовления и рентабельность, читайте в статье.
Общие сведения
Поддоны впервые были изготовлены в Соединенных штатах Америки в начале 20 века. На них складировали груз при его перевозке в вагонах, поэтому размеры поддонов соответствовали их габаритам. На сегодняшний день эти размеры считают стандартными, но область применения паллет намного расширилась.
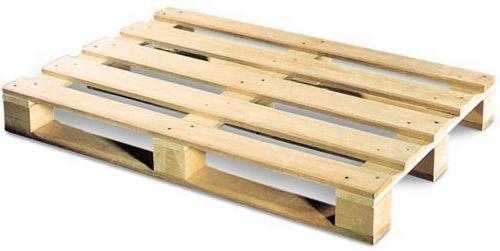
В нашей стране большую популярность приобрели поддоны, размеры которых соответствуют европейским стандартам: 120х80 сантиметров. В настоящее время освоено производство поддонов разного типа и размера в зависимости от параметров груза.
Классификация
В зависимости от способов погрузки и расположения грузов различают:
- Двухзаходные поддоны и четырехзаходные. Это зависит от того, как вилы автопогрузчика вводятся под дно паллет: с двух сторон или с четырех.
- Однонастильные поддоны (одностороннее размещение груза) и двухнастильные (груз размещается по обеим сторонам).

- Поддоны с однократным и многократным использованием. Первые используются при транспортировке груза в отдаленные районы или другие страны. Возвращать их оттуда проблематично или нерентабельно.
- Складные поддоны и неразборные.
Производство поддонов
Технология зависит от способа изготовления паллет, который бывает ручным, частично автоматизированным (используется вспомогательное оборудование) и с применением автоматической производственной линии.
Любой способ будет рентабельней при наличии собственной пилорамы. Стартовый капитал для приобретения материала и необходимого оборудования очень скоро окупится. Уже через несколько месяцев производство поддонов начинает приносить прибыль. Оборудование, к которому относится ленточная рама, кромкообрезной и торцовочный станок, обычно используется при выполнении других работ, связанных с обработкой дерева.
Ручной способ
Производство деревянных поддонов таким способом не отвечает высокому качеству, поэтому крупные компании приобретают их не охотно. Но невысокая цена и отсутствие информации о способе производства, которую умышленно скрывают изготовители, привлекает покупателей и поддоны быстро раскупаются.
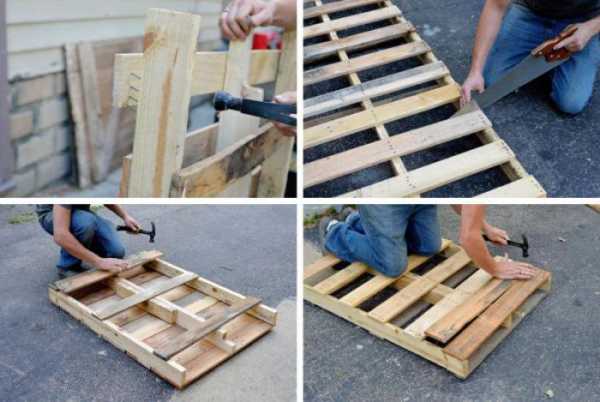
Мастеру для работы нужно немного: пиломатериалы, гвозди и молоток. Производительность труда при таком способе небольшая, 80-150 единиц продукции за 8 часов работы.
Полуавтоматический способ
Изготавливая поддоны с привлечением вспомогательного оборудования, повышается производительность труда. За одну рабочую смену, равную восьми часам, можно изготовить 300-600 поддонов. Такой способ производства паллет является самым распространенным. Используется следующее оборудование:
- Пистолеты гвоздезабивные (нейлеры), которые бывают пневматическими, электрическими и газовыми.
- Стол монтажный для сборки паллет.
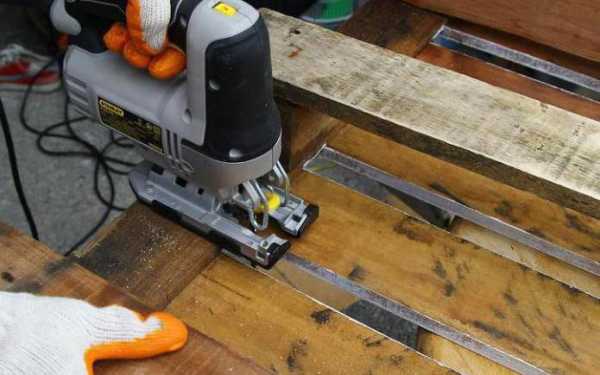
- Станок, на котором обрезаются углы поддонов.
- Линия комплексной сборки. В ее состав входит несколько станин, каждая из которых осуществляет определенную операцию с поддоном.
Автоматический способ
Линиями, оснащенными станками и агрегатами, может располагать завод по производству поддонов, который выпускает большой объем продукции или небольшой цех. Выбор отечественных и зарубежных автоматических линий в настоящее время очень большой, но наиболее привлекательными являются два типа:
- В основу первого входит гвоздезабивная машина СНФ-02. Такая линия за одну минуту производит полтора поддона. Обслуживают линию два оператора и один погрузчик.
- Второй тип автоматической линии основан на использовании двух гвоздезабивных машин. Производительность составляет 5-7 паллет за минуту. Преимущество такой линии в переключении станка на изготовление поддонов с другими размерами.
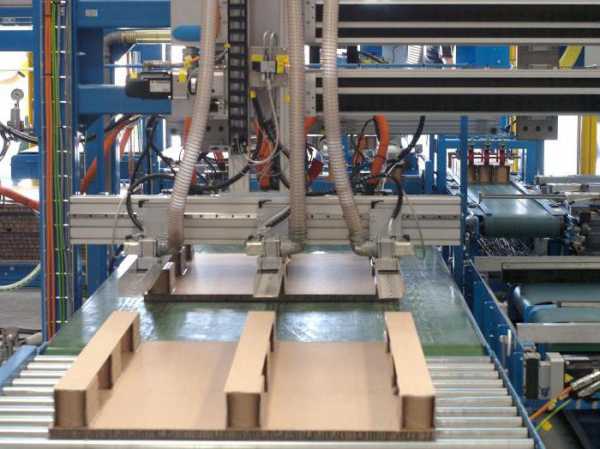
Технология производства паллет из дерева такова:
- Сначала в шаблоны гвоздезабивной машины закладывается пиломатериал в виде брусков или досок.
- Затем ножки и основная часть поддона сбиваются за один проход машины по 2-м шаблонам.
- После того, как гвозди забиты, шаблон вместе с ножками возвращается оператором назад, а ножки помещаются в шаблон основной.
Европоддоны
Они предназначены для того, чтобы на них складировать товар. Благодаря паллетам повышается технологичность всех процессов при перевозке любых товаров. На строительные объекты кирпич, бетон, цемент и прочие материалы доставляют на европоддонах.
Они изготавливаются их ольхи, осины, ели, сосны, влажность которых должна быть не меньше 24%. Европоддон, размеры которого соответствуют европейским стандартам (800х1200 миллиметров), состоит из строганных досок. Не следует путать эти поддоны с американским аналогом, размеры которого больше – 100х100 сантиметров.
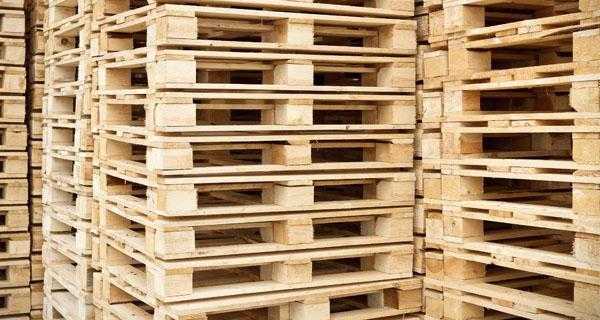
Все элементы скрепляются ершенными гвоздями, которые обеспечивают высокую прочность. Европоддон, размеры досок которого неодинаковые, состоит из 20 элементов. Общий вес паллета небольшой (10 килограммов), но на нем перевозятся грузы массой до 2,5 тонн. Это достигается за счет того, что шашки размещены, а доски по ширине чередуются правильно.
Оборудование
Если деревянные паллеты производятся для собственных нужд, небольшими партиями, используется универсальное оборудование для производства поддонов. Раскрой бревен поперек производится цепной ручной пилой. Выпилить брус и раскроить его на доски можно на лесопильной раме или распиловочном горизонтальном станке. На торцовочном агрегате, пилы которого расположены снизу и сверху, раскраивают брус на шашки и торцуют доски в размер.
При образовании на заготовках дырок от выпавших сучков их заделывают пробками. Специальных станков для таких операций в нашей стране не производят, а на импортное оборудование цена очень высокая. Поэтому пробки изготавливают на сверлильных станках, которые оснащены полыми сверлами.
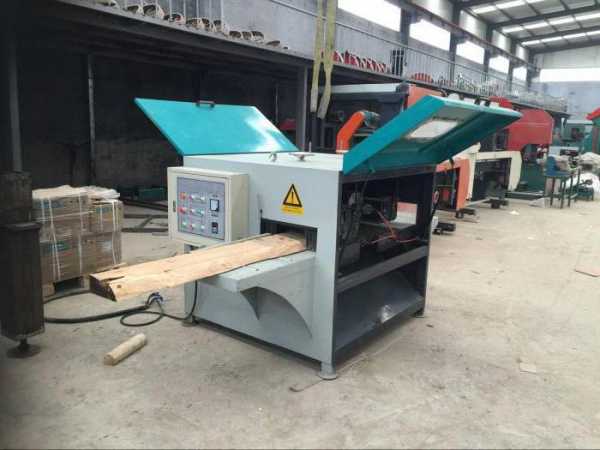
Для крупного предприятия, которое специализируется на производстве деревянных поддонов, этого оборудования недостаточно. Для обеспечения нужной мощности нужна специальная техника и станки.
Предъявляемые требования
Производство поддонов осуществляется из древесины мягких лиственных и хвойных пород деревьев, а также березы. Для изготовления паллет используется низкосортный пиломатериал. Его влажность не должна быть больше 25 процентов.
Пороки на древесине не допустимы: чужеродные включения, рак, острые или тупые обзолы, повреждения механического характера и трещины, идущие от торцов в глубину на 5 сантиметров и больше.
Заготовки для поддонов должны быть цельными, сращивать их запрещается. В местах установки крепежных деталей и на ребрах крайних досок настила снизу не допускается присутствие сучков. Если они во время обработки досок отпали, образовавшиеся отверстия заделываются пробками из дерева той же породы. Поддоны должны быть обязательно промаркированы.
Обработка паллет
На каждом поддоне обязательно ставится клеймо, подтверждающее прохождение фитосанитарной обработки согласно действующим стандартам с указанием названия партии, страны-изготовителя, метода обработки. На европоддонах дополнительно указывается, под каким номером выпущена партия и год ее изготовления. Обработку поддонов производят тремя способами:
- Фумигацией – когда для обработки используется бромистый метил, нейтрализующий всех вредителей и болезни. Этот способ не пользуется популярностью у производителей, так как после санитарной обработки свойства древесины изменяются: поверхность поддона покрывается тонким слоем состава. На таких паллетах хранить продукты нельзя.
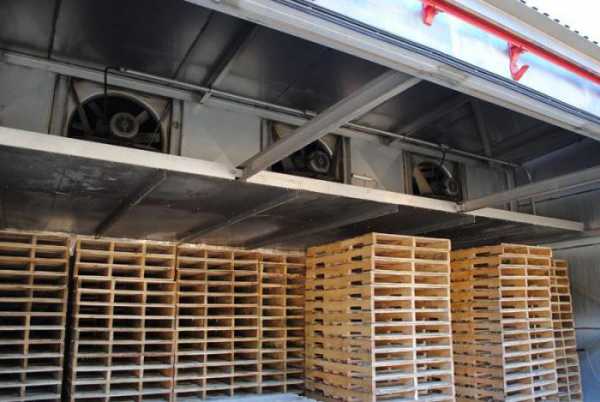
- Тепловой обработкой, которая заключается в том, что поддоны на длительный срок помещаются в камеры с высокой температурой. Вредоносные бактерии в таких условиях нейтрализуются. Недостатком обработки является дороговизна оборудования.
- Камерной сушкой, которая является распространенным и наиболее эффективным способом. Заключается он в следующем: пиломатериалы для производства поддонов помещают в камеру с определенной температурой и влажностью и выдерживают какое-то время. Технология автоматизирована, камера оснащена датчиками. Как только значения температуры и влажности достигнут необходимой величины, приборы автоматически выключаются.
Кто покупает поддоны?
Продажа поддонов в розницу не имеет смысла. Нужно искать оптовых покупателей среди крупных компаний. Потенциальными приобретателями паллет могут быть:
- Компании, перевозящие грузы во все страны мира.
- Предприятия, производящие товар: станки, мебель, бытовую технику и прочее.
- Тепличные и фермерские хозяйства, сбывающие продукцию.
- Центры торговли и крупные рынки.
- Компании, специализирующиеся на оказании складских услуг, которые берут на хранение различные товары.
Рентабельность
Бизнес по производству паллет — очень выгодное дело. Рентабельность производства поддонов зависит от того, какова стоимость сырья. Поэтому начинать такой бизнес предпочтительней в регионах с развитой индустрией деревообработки. Здесь сырье можно приобрести по выгодной цене.
Рентабельность обсчитывается следующим образом. Зная стоимость одного кубометра доски можно высчитать себестоимость готового поддона. При продаже цена на него увеличивается. Производительность линии по изготовлению паллет известна. Легко высчитать количество выпускаемых поддонов за час, день, месяц, год. Из суммы годового дохода вычитаются расходы на налоги, оплату коммунальных платежей, заработную плату всему персоналу предприятия. Оставшаяся сумма и будет чистой прибылью.
www.syl.ru
производство, виды и стоимость европаллет
История использования и производства деревянных поддонов для перевоза грузов начинается в начале XX века в США. Первоначально паллеты использовали для перевозки грузов в вагонах поездов, от чего их габариты были сопряжены с габаритами вагонов. Сегодня этот размер паллет считается стандартным, хотя сами поддоны стали использовать не только при железнодорожных перевозках.
В России популярностью пользуются поддоны размерами 120х80 и 120х100 см, основанные на европейских железнодорожных стандартах. Размер и тип паллет зависит от параметров перевозимого груза: массы, размера и его других характеристик.
Масштабы производства и виды деревянных поддонов
В США ежегодно на изготовление деревянных поддонов уходит 14 млн м3 древесины. За последние десять лет на западном рынке появилось несколько десятков новых видов поддонов. Связано это с тем, что для каждой задачи и предприятия стали изготавливать отдельный вид поддонов. К примеру, существуют такие виды:
- для химического сырья;
- для пивных бочек;
- с «ушами» и «без ушей».
В России такая практика не ведётся, и современный отечественный рынок насчитывает всего десять стандартов поддонов.
Конструкция
Вне зависимости от размеров поддонов, их конструкция примерно одинаковая: нижние доски («лыжи»), установленные на деревянные кубики, и поперечные доски, на которые монтируется настил. Кубики оставляют пространство для вил погрузочной техники. А на настил укладывается груз.
Доски настила и их число зависят от габаритов груза, однако это не влияет на общую конструкцию. Она предусмотрена таким образом, чтобы погрузчик мог захватить поддон со всех сторон.
В зависимости от типа груза и его размеров, приобретаются поддоны разных габаритов и толщиной настила и несущих досок, высотой кубиков. Поддоны большей грузоподъёмности требуют большего количества древесины, а потому и их стоимость намного больше, чем у обычных.
Совет: для придания большей жёсткости деревянному паллету можно сделать нижнюю обвязку по её периметру.
Производство
Для производства поддонов сегодня используют как автоматические, так и полуавтоматические линии. Из-за высокой стоимости физического труда и для снижения нагрузки на работников в Европе чаще всего используют автоматические линии.
В России физический труд обходится дешевле автоматизированного производства, поэтому не редка ситуация, когда на заводах поддоны собираются рабочими и сколачиваются вручную. Естественно, качество поддона при ручной сборке гораздо ниже, чем при автоматическом изготовлении.
Факт: поддоны, собранные автоматически, легко отличить от ручного труда по забитым гвоздям. При ручном труде шляпка гвоздя остаётся заподлицо с поверхностью доски, а при автоматическом производстве – она утапливается. К слову, именно автоматический вариант соответствует с нормами ГОСТ.
Для производства паллет используются навивные гвозди (ещё называются ершоны). По конструкции они напоминают что-то среднее между саморезом и гвоздем: имеется особая шляпка, большая толщина и специальные насечки. Последнее сделано для того, чтобы крепёжные элементы держались прочнее на доске.
Благодаря этому, деревянные поддоны не разваливаются при грубом использовании, что важно, поскольку на производстве их часто роняют и толкают. Обычные строительные гвозди при таком обращении попросту бы вылетели из конструкции.
Четыре способа производства
Существует четыре основных способа изготовления поддонов:
- Первый. Наиболее простой и дешёвый. Представляет собой следующую технологию: из кругляка делается деловой лес и отправляется по назначению. В итоге остаётся 25-30% отходов, требующих утилизации. И, как раз, самый простой способ – это создание паллет. Делается это с помощью молотков и гвоздей, поэтому цена такого деревянного поддона невысокая, но и качество не соответствует требованиям многих предприятий.
- Второй. Ручное производство при помощи пневматических инструментов. При данной технологии поддоны также собираются вручную, однако вместо обычных молотков используются пневматические. Это позволяет ускорить производство и немного повысить качество изделий. Стоимость деревянного поддона, изготовленного посредством пневмомолотка немного выше, чем при первом варианте. Из минусов можно отметить низкое качество из-за плохого соблюдения размеров и человеческий фактор, который может привести к некачественной сборке продукта, а в следствии – к повреждению груза при перевозке.
- Третий. В-основном применяется в странах Европы. Представляет собой использование станков полуавтоматического типа. Действуют они следующим образом: автомат забивает гвозди в доски, которые укладываются в металлические клише. Клише наполняются вручную. С помощью полуавтоматов получаются качественные поддоны со всеми допусками по габаритам.
- Четвертый. Наиболее дорогой и качественный способ – это полностью автоматическая линия производства. Работникам требуется только загрузить деревянные заготовки в машину, а далее она обрабатывает поддон на всех этапах:
- нарезка;
- сколачивание;
- складирование;
- заматывание лентой или плёнкой;
- выкатывание готового поддона на погрузку.
Наиболее производительная автоматическая машина по производству поддонов в России изготавливает более 65 000 паллет ежемесячно. В Европе таких автоматических линий не так много. К примеру, среди 18 производств, недавно посещённых отечественными компаниями, не нашлось ни одного, где бы действовала автоматическая линия. Однако при этом предприятия эффективно работали.
Качество полуфабрикатов
Исходные материалы для производства поддонов требуют внимательного обращения. Доски должны быть тщательно просушены, поэтому поставляются в брикетах, в которых имеется небольшое пространство между досками. Если деревянные заготовки не будут иметь доступа к воздуху и будут влажными, то через неделю они посинеют, что приведёт их к негодности для производства.
Для производства используются хвойные и лиственные породы древесины. Обе породы быстро выцветают, что хоть и не влияет на их качество, но лишает древесину товарного вида. Поэтому для хранения древесины необходимо защитить её от солнечных лучей и дождя.
Стандарты производства деревянных поддонов: ГОСТ 9557 87 и другие
В России при изготовлении поддонов руководствуются двумя основополагающими документами: ГОСТом 9557-87 и ГОСТом 9078-84. При этом последний ГОСТ описывает лишь самое очевидное: поддоны должны быть сделаны из дерева и в соответствии с установленными размерами (120х80 и 120х100 см).
Что касается ГОСТа 9557-87, то он на 95% схож с европейским стандартом UIC 435-2: толщина, допуски, припуски, гвозди, фаски. Единственное отличие – это отсутствие в российских нормах клейм EPALи EUR, т.к. отечественное производство пока не прошло сертификацию. При соблюдении этого ГОСТа получаются аналоги европоддонов, называющиеся БК – то есть без клейма.
Фитосанитарная обработка
На поверхности поддона ставится ещё одно клеймо, которое подтверждает, что поддон прошёл фитосанитарную обработку по стандарту ISPM 15. На поддоне печатается название партии, метод обработки и страна-изготовитель. Европейские поддоны ещё содержат год производства и номер партии.
Фитосанитарная обработка может быть произведена тремя способами:
- Фумигация. Обработка бромистым метилом – это состав, который нейтрализует все бактерии и вредителей. Не очень популярный способ из-за изменения свойств древесины после обработки: на поверхности поддона остаётся небольшое количество состава, что не подходит для хранения продуктов питания на таких поддонах.
- Тепловая обработка. Поддоны длительное время находятся в камере с повышенной температурой, что нейтрализует вредные бактерии. Из минусов можно отметить высокую стоимость оборудования, что мешает наладить массовое производство, и невозможность обеспечения равномерной температуры в камере.
- Камерная сушка. Наиболее распространённый и эффективный метод. Пиломатериалы, использующиеся для поддонов, загружаются в специальную камеру. Затем материалы выдерживаются в ней под действием температуре 600С и более, а также необходимой влажности. Технология полностью автоматизирована: в камере имеются датчики, которые производят замеры температуры и влажности, и при достижении необходимого значения, они автоматически завершают процесс.
При соблюдении указанных требований, поддоны достигают высокого качества и надёжности. Однако в России часто встречаются недобросовестные компании, игнорирующие требования к производству, поэтому выбирая паллеты для складского помещения, необходимо внимательно изучить все сертификационные документы компании-производителя.
skladovoy.ru
Чертеж поддона размеры европоддона вес изделия из дерева
Чертеж поддона размеры европоддона вес изделия из дерева зависит от того, какой материал (дерево) используется для изготовления (осина, ольха, сосна, ель) и его влажность (обычно не менее двадцати четырех процентов). На предложенном примере рассмотрим поддон из сосны.
Поддон состоит из следующих элементов.
1. Доска строганная размером 22х150х1200мм, количество элементов – два.
2. Доска строганная размером 22х100х1200мм, количество элементов – шесть.
3. Доска строганная размером 22х100х800мм, количество элементов – три.
4. Брусок строганный размером 78х100х100мм, количество элементов – девять.
Все перечисленные выше деревянные элементы, крепятся между собой при помощи ершенных гвоздей. Данные гвозди позволяют достичь высокой прочности скрепления деревянных деталей между собой. Они выполнены с круглой плоской шляпкой (головкой) и поперечной насечкой, которая увеличивает в пять раз сопротивление (усилие, приложенное к гвоздю, чтобы его вытащить) по сравнению с обычным, без насечки.
Гвозди используют следующих размеров.
1. L=90мм; кол-во — 27шт; масса – 203г.
2. L=65мм; кол-во — 18шт; масса – 101г.
3. L=40мм; кол-во — 12шт; масса – 43г.
Обший вес гвозлей: триста семь грамм
Схема крепления деталей изделия гвоздями предложена на рисунке
Европоддона вес составит тридцать шесть килограмм (древесина) триста десять грамм (гвозди).
Приступаем к сборке.
Если планируем собирать большое количество изделий, необходимо изготовить под них оснастку. Это значительно ускорит сборку (сократит время) и сохранит размеры европоддона в неизменном виде. Оснастку необходимо надежно закрепить на верстаке, который можно изготовить своими руками. Один из вариантов предложен в статье «Чертеж верстака – массивный стол для гаража или сарая, схема, крепление бруса».
Первый шаг
Устанавливаем в подготовленную оснастку девять брусков 78х100х100, три ряда, по три бруска в каждом
Второй шаг
На каждые три бруска, укладываем доску 22х100х800
Повторяем данную операцию три раза, по разу на ряд
Третий шаг
Поперек, укладываем: две доски 22х150х1200 по краям; одну доску 22х100х1200 по центру. Скрепляем доски между собой гвоздями длиной девяносто миллиметров. Смотрим схему крепления деталей.
Между узкой и широкими досками, по центру укладываем две доски 22х100х1200. Скрепляем доски между собой гвоздями длиной сорок миллиметров. Смотрим схему крепления деталей.
Четвертый шаг
Переворачиваем конструкцию брусками вверх, укладываем на них три доски 22х100х1200. Скрепляем доски между собой гвоздями длиной шестьдесят пять миллиметров. Смотрим схему крепления деталей. Изделие из дерева собрано собственными руками.
По аналогии можно собрать любую модель, с различными геометрическими размерами. И снизу доски можно прибивать не вдоль, а поперек. Все зависит от того, для каких целей вы собираетесь использовать ту, или иную модель. Как видим, организовать сборку, совсем не сложно.
Если захотим срезать фаски в модели (углы под углом сорок пять градусов) по нужному размеру, необходимо использовать дополнительное оборудование. Фаски срезаются со всех наружных торцов и со стороны внутренних брусков. Это делается для удобства попадания и заезда вил погрузочных механизмов. Насколько это оправдано «цена» «удобство» затрудняюсь ответить.
Заказать чертеж
Поделитесь с друзьями!
chertegnik.ru