Оборудование для производства газобетона — АлтайСтройМаш
Оборудование для производства газоблоков
Компания «АлтайСтройМаш» с 2000 года выпускает профессиональное оборудование для изготовления газоблоков, которое имеет сертификат государственного образца. Более двадцати лет опыта в сфере машиностроения, технология бережливого производства «Toyota», использование немецкой лазерной резки «Trumpf» для идеально точной обработки каждой детали являются гарантией качества оборудования по производству неавтоклавного газобетона.
Наши установки позволяют изготавливать газобетонные блоки высокой прочности и безупречной геометрии, которые имеют единый стандарт с автоклавным газобетоном, в соответствии с ГОСТом от 1989 года.
Мы поставляем производственные линии по всему миру и даем гарантию 2 года на все комплектующие, т.к. контролируем качество на всех этапах производства и продажи оборудования.
Приобретая линию, вы получаете бесплатную техническую поддержку,
которая включает в себя:
- Инструкции по монтажу оборудования;
- Обучение персонала;
- Профессиональную поддержку наших инженеров-технологов на протяжении всего вашего бизнеса;
- Актуальную информацию по поставщикам сырья в вашем регионе;
- Готовую рецептуру газобетонной смеси, в зависимости от характеристик сырья;
- Маркетинговые материалы для продвижения готовой продукции на рынок;
Цена на газобетон
и оборудование для его производства
Неавтоклавный газобетон используют для строительства коттеджей, домов, школ, больниц, высотных домов, торговых центров. За последние 8 лет спрос на газоблоки вырос в 14 раз и среди других строительных материалов газобетон занимает долю на рынке 43%. Рыночная цена на газобетонные блоки, независимо от области, превышает их себестоимость не менее чем на 30%.
Популярность материала зависит от географической территории, например, в Казахстане цена газобетонных блоков на рынке выше, чем в странах, где газобетон только начинает приобретать известность. Но уже и там количество клиентов, желающих купить газоблоки, выросло на 27% по сравнению с 2017 годом. Это связано с активным развитием строительства и государственной поддержкой малого и среднего бизнеса.
Линии для производства газобетона — АлтайСтройМаш
Компания “АлтайСтройМаш” предлагает широкую линейку заводов по производству неавтоклавного газобетона: более 200 комплектаций.
В нашем каталоге вы найдете оборудование для производства газоблоков с разной степенью автоматизации: конвейерного и стационарного типа.
В чем разница между типами заводов по производству газоблоков?
Конвейерные линии по производству газобетона и их преимущества
Конвейерные линии: формы катятся по рельсам, а смеситель стоит неподвижно.
Преимущества:
-
легко автоматизировать;
-
экономится площадь помещения, т.к. формы располагаются близко друг к другу;
-
высокая производительность т.к. после заливки все блоки оказываются в одном месте, и не нужно тратить время и силы на их сбор.
Особенности стационарных линий по производству газобетона
Стационарные линии: формы не двигаются, и заливка происходит с перемещением смесителя по рельсам.
Преимущества:
-
очень простой монтаж ;
-
Все линии, и стационарные, и линии конвейерного типа, бывают в мини-формате. Количество форм и объем смесителя в таких мини-линиях меньше.
Каждая линия имеет свою производительность (от 2 до 200 м3/сут).
По желанию клиента любая модель может быть оснащена дополнительными элементами, которые улучшают технологию изготовления газоблоков: они облегчают работу и повышают производительность.
Как увеличить производительность оборудования для газобетона?
-
добавить формы (увеличивается производительность),
-
установить автоматическую резку (безупречная форма газоблока),
-
наладить автоматическую подачу песка и цемента (скорость выше, работников нужно меньше).
Сравните производительность разных моделей:
Тип линии |
Автоматизированная конвейерная линия |
Неавтоматизированная конвейерная линия |
Стационарная линия |
---|---|---|---|
Площадь помещения |
200 м2 | ||
Число рабочих на производстве |
2-4 чел.![]() |
2-6 чел. | 2-4 чел. |
Объем м3/сутки |
До 40 м3/сут. | До 40 м3/сут. | 20м3/сут. |
Какую модель вы выберете для производства газобетонных блоков? Мини-линию или полностью автоматизированный завод с большой производительностью? В любом случае мы бесплатно окажем вам помощь на всех этапах:
-
помогаем с монтажом и выезжаем на пусконаладку, если необходимо;
-
оказываем техподдержку на протяжении всей работы оборудования;
-
предоставляем рецептуру и маркетинговые материалы для продвижения ваших блоков.
Газобетонные блоки, изготовленные на оборудовании от “АлтайСтройМаш”, сделают ваш бизнес узнаваемым и эффективным!
Оборудование для производства полистиролбетона — АлтайСтройМаш
Большинство строительных объектов сегодня возводят из стройматериалов, созданных новейшими технологиями. Доступная стоимость и высокая прочность делают эти материалы более привлекательными по сравнению с традиционными.
Большую популярность приобрел полистиролбетон — один из видов лёгкого бетона (к этой категории относят также газобетон и пенобетон). В его составе, в качестве наполнителя используются гранулы полистирола. Как показывает европейский опыт, использование полистиролбетона позволяет значительно экономить энергоресурсы. Он легкий, хорошо сохраняет тепло и обеспечивает высокую звукоизоляцию.
Структура полистиролбетонного блока.
Для приготовления, перемещения и заливки смеси необходима мобильная установка для полистиролбетона, которая позволяет изготавливать штучные изделия (блоки, плиты), а также монолитную заливку при тепло- и звукоизоляции крыш; заливке полов; монолитной заливке самонесущих стен.
Технология производства полистиролбетона
Технологические операции изготовления полистрилбетонной смеси достаточно просты: в смеситель для полистиролбетона подается вода, затем цемент и химические компоненты.
Транспортирование и укладка монолитного полистиролбетона и формование блоков.
Укладка полистиролбетона в несъемную опалубку при возведении наружных стен осуществляется после сборки опалубки и установки всех необходимых связей. Шланг опускается в нижнюю часть опалубки и постепенно по мере заполнения ее перемещается вдоль опалубки и поднимается вверх (аналогично происходит формовка сборных конструкций). Такой способ укладки при отсутствии виброуплотнения позволяет существенно уменьшить образование воздушных пустот.
При устройстве монолитной теплоизоляции перекрытий над холодными подвалами и проездами укладка полистиролбетона осуществляется в один слой. Разравнивание и уплотнение поверхности уложенного полистиролбетона осуществляется при помощи рейки.
При формовании блоков нужно опустить сливной шланг в форму и сливать смесь до полного заполнения объема ячейки.
Как купить оборудование для производства полистиролбетона?
Чтобы купить полистиролбетонную установку, достаточно связаться с нами любым удобным для вас способом: позвонить, написать или заполнить заявку на сайте. Цена оборудования одинакова для всех клиентов России, Узбекистана, Казахстана, Киргизии и др. Мы осуществляем доставку по всему миру и даем гарантию 2 года на все установки. Кроме того, вы получаете полное техническое сопровождение наших специалистов на весь период эксплуатации оборудования.
Мы на You TubeУслуги предприятияСамое популярноеНовости
|
youtube.com/embed/2P6W-w2PEfs» frameborder=»0″ allow=»accelerometer; autoplay; encrypted-media; gyroscope; picture-in-picture» allowfullscreen=»»/> Газобетон (строительный материал) – популярный в строительной сфере материал, прочный, но достаточно легкий. Для его изготовления требовались промышленные мощности, но сегодня технологии меняются. Появляется модернизированное оборудование для производства газобетона, которое позволяет производить его в рамках небольших производств, а некоторые модели – в домашних условиях. Оборудование для изготовления газобетона можно условно разделить на 5 основных категорий:
Купить оборудование для производства блоков можно на нашем сайте. Мы являемся производителями, поэтому готовы при необходимости предоставить вам сертификаты качества и гарантии. Если вам требуется подробная консультация по техническим вопросам, помощь при выборе модели – звоните нам по телефону, у наших сотрудников есть ответы на все вопросы. |
обзор типов линий и установок
Производство блоков из газобетона
Еще не так давно, производство популярного материала в виде строительного камня было возможно лишь в условиях завода. Но с усовершенствованием технологий такая возможность появилась не только у мелких предпринимателей, но и у самих застройщиков.
На данный момент существует большое количество различного оборудования, предназначенного для изготовления данного представителя ячеистых бетонов. Комплекты отличаются между собой по ряду признаков, а в первую очередь ценовой категорией и объемом выпуска.
В данной статье мы будем рассматривать оборудование для производства газобетонных блоков разного типа, и проанализируем сам процесс изготовления изделий. А также сравним материал, произведенный в домашних и заводских условиях.
Содержание статьи
Общая технология производства газобетона
Предварительно, пожалуй, рассмотрим общий принцип технологического процесса. Ведь для полноценного обзора линий оборудования, нам нужно иметь представление о том, как именно изготавливается газобетонный блок.
Необходимое сырье
Для приготовления газобетонной смеси, понадобится наличие следующего сырья:
- Цемент марки не менее М400;
- Вода;
- Известь негашеная;
- Гипс;
- Песок кварцевый;
- Алюминиевая пудра.
Алюминиевая пудра
Также не помешает добавить в раствор пластификатор. Основное его предназначение – повышение пластичности раствора, что предотвращает растрескивание изделий на стадии сушки и твердения.
Пластификатор
Другие химические добавки также используются. Как правило, они добавляются с целью повышения качеств готовых изделий.
Пропорции сырья вместе с добавками
Обратите внимание! Вышеуказанный состав является классическим. Многие компоненты могут заменяться. В этом случае набор числовые значения свойств также будут варьироваться.
- Кремнеземистый компонент может быть представлен в виде: песка, золы и иных вторичных продуктов промышленности;
- Тип вяжущего также может быть разным: цементным, шлаковым, известковым, смешанным, зольным.
Примерное содержание пропорций – следующее:
- 50-60% — цемент;
- 20-40% — песок;
- 1-10% — известь;
- До 1% — вода.
На заметку! При желании повысить плотность изделий, следует увеличить количество цемента. В этом случае также изменится и масса готового материала, и коэффициент теплопроводности.
Пропорции в зависимости от желаемой плотности
Основные этапы
Краткая инструкция выглядит следующим образом:
- Первым делом взвешиваются компоненты и смешиваются в необходимых пропорциях.
При изготовлении своими руками это делается вручную, в заводских условиях, как правило, в автоматическом режиме.
- Все ингредиенты попадают в смеситель, где и происходит смешивание.
- Следующим этапом станет формовка. Формы наполняются примерно на 1/3, так как при порообразовании смесь попросту может вытечь.
- Следом, после завершения процесса вспучивания, выжидается некоторое время до частичного застывания.
- Далее производят резку единого пласта или просто распалубку, если формы используются уже готовых типоразмеров.
- Последним этапом станет автоклавирование либо отправление блоков на сушку при неавтоклавном способе производства.
Обратите внимание! Ход процесса может несколько отличаться в зависимости от того, какое оборудование для изготовления газобетонных блоков используется. Однако в целом, общий принцип будет аналогичным.
Типы установок и линий
Теперь перейдём непосредственно к обзору типов оборудования.
Конвейерный тип
Оборудование для газобетона конвейерного типа отличается:
- Максимальной автоматизацией производства;
- Минимальным участием работников;
- Высокой стоимостью;
- Большими объемами производства;
- Полной комплектацией;
- И, как правило, наибольшей рентабельностью.
Большая конвейерная линия
Рассмотрим подробнее комплектацию и возможности такого газобетонного оборудования на примере линии популярного китайского производителя, являющегося дилером компании Премиум Кирпич Плюс.
В стандартный комплект входят:
- Емкости и бункеры для сырья;
Бункер для сырья
- Ленточные конвейеры для транспортировки компонентов;
Ленточный конвейер
- Узел растворосмесительный;
Узел бетоно-растворный
Автоклавы
Сборная форма для блоков
- Резательный комплекс;
- Транспортер перемешивающий;
- Дробилки;
- Тележки;
- Узел для автоматического управления линией;
- Погрузчик вилочный.
Такое оборудование для производства стоит около 55 000 000. Согласитесь, сумма, не маленькая. Однако при этом, производительность составляет около 300 тысяч метров кубических в год. Площадь, необходимая для размещения такой линии должна быть около 4000 м2.
В качестве альтернативы, можно рассмотреть возможность приобретения конвейерной линии в бывшем употреблении. Это – своеобразный риск, однако стоимость ее значительно ниже.
Также стоит обратить внимание на мини линию конвейерного типа «Иннтех-100». Ее производительность значительно ниже и составляет 100 м3 в сутки. Цена ее – около 3 000 000.
Мини конвейерная линия
Данная линия характеризуется неподвижным смесителем. Формы передвигаются по рельсовому транспортеру как тележка. Компоненты подаются и дозируются в автоматическом режиме. Резательный комплекс – механический.
Больше всего среди производителей ценятся линии известных немецких производителей оборудования. Они отличаются высокой продуктивностью, долговечность в использовании. С их помощью можно изготавливать блоки самого высокого качества.
Немецкое оборудование для изготовления газоблока
Видео в этой статье продемонстрирует принцип работы оборудования для изготовления газобетона.
Производство газобетона Поревит
Стационарный тип
- Такой тип оборудования гораздо менее дорогостоящий. Однако и производительность ее гораздо ниже и составляет около 50 м3 в сутки.
- Как правило, в комплект таких линий входят дозаторы компонентов и ленточный транспортер, который и подает ингредиенты в смеситель.
- Однако полностью автоматизированным такой комплект назвать уже нельзя. Для полноценной работы требуется наличие как минимум нескольких человек.
- Необходимая квадратура для размещения производства и склада составляет около 500 м2.
Линия стационарного типа для производства газобетонного блока
В качестве примера, кратко рассмотрим комплектацию и возможности линии АСМ-1МС.
- Производительность составляет около 60 м3;
- Для работы потребуется привлечение 3-4-х человек;
- Песок и цемент подаются в автоматизированном режиме.
Комплектация:
- Смеситель для вяжущего и иных компонентов;
- Конструкция для резки блочного массива с пилами;
- Формы и поддоны;
- Транспортер.
Мобильные установки и мини-линии
Такое оборудование для производства блоков газобетонных идеально подойдет для начинающих предпринимателей либо застройщиков, желающих изготовить изделия для собственных нужд.
При помощи мобильной установки можно произвести исключительно только газоблок неавтоклавного твердения. Ниже мы рассмотрим основные его отличия от основного конкурента.
Такой оборудование требует наличия сети в 220 Вт, в то время как другие типы машин требуют подключения к сети в 360 Вт. Объем производства составляет около 2-10 м3 в сутки.
Установка мобильная для изготовления газобетона
Рассмотрим характеристики установки на примере комплекта Газобетон 500Б.
Установка газобетон 500 Б
- В комплект входит: смеситель, соединительные рукава и компрессор. Для производства необходимо участие нескольких человек.
- Практически весь процесс работ происходит с участие человека. В автоматическом режиме производится только смешивание.
- Дозирование также придется производить самостоятельно.
- Объем выпуска 3 м3 пористой смеси.
- Емкость для смешивания- 500 литров.
Мини-линии более производительны. С их помощью возможно изготовление вплоть до 25 м3 в сутки. Для мелких предпринимателей – отличный вариант начать свое дело.
Принцип их устройства – аналогичен мобильным установка, больше – мощность и объем смесителя.
Подробнее об автоклавировании
Теперь давайте более подробно поговорим об автоклавной обработке газоблока и разберемся, в чем заключаются основные различия между изделиями самостоятельного производства и материалом, выпущенным в условиях завода.
Что представляет собой автоклавная обработка?
При помощи автоклавной обработки удается повысить качества готовых изделий.
- Разрезанные на типоразмеры блоки помещаются в автоклав и обрабатываются под действием давления выше атмосферного водяным паром, при этом преобладает высокая температура.
- Обработка длится в течение 12-ти часов.
- По окончании обработки, блоки практически сразу можно использовать в строительстве, ведь марочной прочности они уже достигнут.
- Неавтоклав же набирает прочность в течение 4-х недель.
- При автоклавной обработке повышаются такие качества как: прочность, плотность, долговечность. Изделия становятся менее хрупкими
Стоит отметить, что изготовление блоков автоклавного твердения возможно только в заводских условиях.
Процесс автоклавирования
Сравнение автоклавного и неавтоклавного газоблока
А теперь сравним свойства автоклавного газобетона и изделий, достигающий прочности естественным способом.
Характеристика | Сравнительный анализ |
Сочетание плотности и теплопроводности | За счет специализированной обработки в автоклаве, изделия синтезного твердения отличаются лучшим сочетанием показателей плотности и теплопроводности. |
Морозостойкость и долговечность | В соответствии с ГОСТ, требования к марке по морозостойкости к неавтоклавному блоку несколько ниже. Точные сроки долговечности обоих изделий не установлены опытным путем, в силу недостаточного времени существования материала на рынке строительных материалов. |
Внешний вид и геометрия изделия | Автоклав имеет практически идеальную геометрию. Неавтоклавный блок, изготовленный в домашних условиях в данном отношении серьезно ему уступает. |
Требования к оборудованию и сложность производства | Оборудование для газобетона автоклавного, в целом, отличается лишь наличием автоклавов.![]() |
Хрупкость | Неавтоклавные блоки больше уязвимы к механическому воздействию, они более хрупкие. |
Стоимость | Автоклавные изделия дороже примерно на 10%. |
Усадка | Неавтоклавные блоки больше подвержены усадке. Показатель составляет до 1 мм/м2. |
В заключение
На современном рынке существует большое количество различных комплектов оборудования для производства газобетонных блоков, начиная от дорогостоящих крупномасштабных конвейерных линий и заканчивая бюджетными мобильными установками. Именно поэтому производство данного материала стало еще более популярным.
ИННТЕХГРУПП — оборудование для производства газобетона.
Производственная Компания — ИННТЕХГРУПП
Мы рады приветствовать Вас на нашем сайте! Здесь вы можете узнать что такое неавтоклавный газобетон,
где и как он применяется, чем отличается от других строительных материалов, каким образом выглядит
его производство. Так же нашем сайте Вы можете выбрать и купить оборудование для производства
газобетона и сам неавтоклавный газобетон. Если у Вас остались сомнения или вопросы Вы всегда можете
их задать специалистам компании по телефону или электронной почте.
Обладая значительным опытом в таких областях как, эксплуатация и продажа строительного оборудования, производство строительных материалов (в том числе и производство газобетона), организация процессов прямых продаж и продаж в сети Интернет, мы постарались сделать для Вас этот сайт как можно проще и доступнее.
Если Вас интересует Оборудование для производства газобетона, его характеристики и возможности, ресурсы необходимые для производства, подробные комплектации с описаниями каждого элемента оборудования, стоимость базовых линий – переходите в раздел Основное оборудование.
Если Вас интересует Технология производства газоблока, подробное описание и требования к сырью,
описание основных технологических процессов, особенности эксплуатации оборудования, варианты
автоматизации – просмотрите раздел Технология производства.
Если Вас интересует приобретение оборудование для производства газоблока, условия поставки, способы оплаты, способы доставки, условия гарантии – переходите в раздел Как купить.
Если Вас интересует общая информация о газобетоне, перспективах и тенденциях рынка, об оборудование для газобетона и его отличиях от оборудования для пенобетона, о способах строительства из газобетона – Вы можете перейти в раздел Статьи.
Если Вам интересна информация о нас, о том какие компании входят в ИННТЕХГРУПП, и каков профиль их деятельности — переходите в раздел О компании.
Презентационный мини-видео ролик о работе линии для производства газобетона по конвейерной технологии Иннтех ПРОФИ
Перейти на наш канал в YouTube
Необходимое оборудование для производства газобетона
Мини-завод по производству неавтоклавного газобетона
Раньше изготовление газобетонных изделий было только на заводах. Теперь оборудование для производства газобетона может устанавливаться на небольших площадках или даже во дворе собственного дома.
В зависимости от количества необходимых блоков можно приобрести оборудование в виде мини-завода, поставить мобильную установку для получения блоков различной плотности.
Технология получения газобетона
Газобетон относится к разряду ячеистых бетонов. Состоит он из смеси нескольких компонентов:
- песок — 20-40%;
- известь — 1-5%;
- цемент — 50-70%;
- вода чистая — 0,25-0,8%;
- пудра алюминиевая — 0,04-0,09%.
Песок используется просеянный, его фракции не превышают 2,1 мм. Глины в нем должно содержаться не больше 7%. Цемент нужен качественный — марки М400 или М500. Алюминиевая пудра применяется в качестве газообразователя. В состав могут включаться еще некоторые компоненты: пластификаторы, ускорители твердения. Для изменения свойств газоблоков в смесь добавляют шлак, гипс или опилки. Этими добавками можно изменить плотность блоков. Ведь материал для изготовления фундамента должен быть прочнее, чем для перегородок. Теплоизоляционные блоки желательно делать более легкими и пористыми. Для этого можно полностью исключить из его состава песок.
Производство газобетонных изделий бывает автоклавное и неавтоклавное. Второй вариант производится гораздо проще, но имеет низкую прочность, недостаточную точность геометрических размеров. Автоклавные изделия бывают обычно более однородной структуры и низкой теплоемкости. Такие блоки используются в условиях России для возведения стен толщиной до 400 мм.
Изготовление блоков
Для производства газоблоков не требуются особо сложные установки. Нужно лишь точное выполнение технологических циклов. Изготовление может выполняться в следующем порядке:
- подготовка компонентов;
- введение газообразователя;
- укладка раствора в формы;
- разрезание блоков;
- созревание изделий;
- автоклавирование.
Все необходимые компоненты взвешиваются и всыпаются для перемешивания в смеситель. Минут через 10-15 к ним добавляют алюминиевую пудру, которая сразу же вступает в химическую реакцию с находящейся в смеси известью. В результате реакции смесь наполняется газом в виде пузырьков по всему объему. Это является сигналом к выкладке раствора в формы для газобетона или на специальный лоток толстым слоем. На лотке производят разрезку массы на блоки особыми пилами. Созревают полуготовые блоки в течение 10-18 часов. После этого блоки помещаются в автоклав. Это особая печь, состоящая из герметичной камеры с температурой 190°C. В ней материал обрабатывается горячим паром под высоким давлением. Далее готовый материал вынимается из автоклава и раскладывается для просушки.
Неавтоклавный строительный материал просушивается в течение 3-7 суток естественным образом. Далее блоки складируются в помещение для набора полной прочности. Происходит это обычно 30 суток. Только по истечении этого срока можно перевозить газобетон к потребителю, упаковав его в специальную термоусадочную пленку.
Оборудование для изготовления блоков
Для газобетонных блоков обычно комплектуется технологическая линия, состоящая из:
- смесителя;
- активатора;
- дозатора;
- режущего приспособления;
- автоклава;
- форм.
Все это оборудование бывает разной мощности. Она обычно варьируется в пределах 10-150 м³ в сутки. Самое дорогое в этом наборе — автоклав. От него и зависит стоимость готового продукта. В домашних условиях это производство чаще всего становится нерентабельным.
Оборудование можно разделить на такие виды:
- стационарная линия;
- конвейерная линия;
- мини-линия;
- мини-завод;
- мобильная линия.
Стационарная линия оборудования для газобетона может производить от 60 м³ продукции в сутки. Для ее складирования требуется примерно 500 м² площади. С управлением линией вполне справятся 2 человека.
Конвейерная линия может выпускать за сутки 75-150 м³ готовой продукции. Размещения оборудования для производства газобетонного блока требует площади более 600 м². Обслуживают его 8 человек.
Мини-линия рассчитана на суточный выпуск около 15 м³ изделий. В состав линии входит смеситель и формы. Для организации производства и установки оборудования требуется 2 человека и 140-160 м² площади.
Установка мини-завода гарантирует выпуск готовых блоков от 25 м³ в сутки. Это немного больше, чем с помощью мини-линии. Отличает мини-завод лишь наличием в его составе поддонов, бака с водой, оборудования для разрезания газобетона.
Мобильные линии часто используются при строительстве личных домов. Они позволяют снизить расходы на треть. Для получения качественного газобетона оборудование подключается к розетке 220 В. В составе линии может быть:
- неподвижный смеситель;
- передвижные формы для заливки раствора;
- установка для разрезания блоков.
Производительность линии достигает 100 м³ в сутки.
Заключение по теме
На протяжении многих тысячелетий человек строит для себя жилье. За эти годы значительно изменились технологии и материалы для строительства. В наше время актуальным стало строительство с использованием газобетона в виде блоков. Раньше блоки выпускались только на заводах, сегодня их производство можно наладить дома. Для этого нужно иметь желание, приобрести оборудование и установить все это на подготовленной площадке. Для выпуска газобетона нужно иметь чистую теплую воду, кварцевый песок, алюминиевую пудру марки ПАП-1, известь, портландцемент М400 или М500 и еще несколько добавок для улучшения качества продукции. Получив все это, можно начинать собственный бизнес по выпуску стройматериалов, имеющих большой спрос. При строительстве собственного дома материал сократит расходы примерно на треть.
Для собственного производства лучше всего приобрести небольшую стационарную линию, с помощью которой можно делать неавтоклавный газобетон. Обслуживать установку могут 2 человека. При таких силах можно ежесуточно выпускать около 60 м³ отличных блоков. Каждый такой искусственный камень весит примерно 30 кг и заменяет собой около 30 стандартных кирпичей. Газоблок весит в несколько раз легче кирпича, поэтому не требует строительства капитального фундамента и использования грузоподъемной техники. Материал отлично обрабатывается ручными инструментами: пилой, стамеской, сверлом. В наше время газобетон занимает ведущее место среди других строительных материалов.
6485_Wehrhahn_Folder_PB_GB_RZ.indd
% PDF-1.3 % 79 0 объект >] / Pages 74 0 R / Type / Catalog / ViewerPreferences >>> эндобдж 75 0 объект > поток 2016-11-25T15: 07: 37 + 01: 002017-05-23T13: 09: 03 + 02: 002017-05-23T13: 09: 03 + 02: 00Adobe InDesign CS5 (7.0.1)
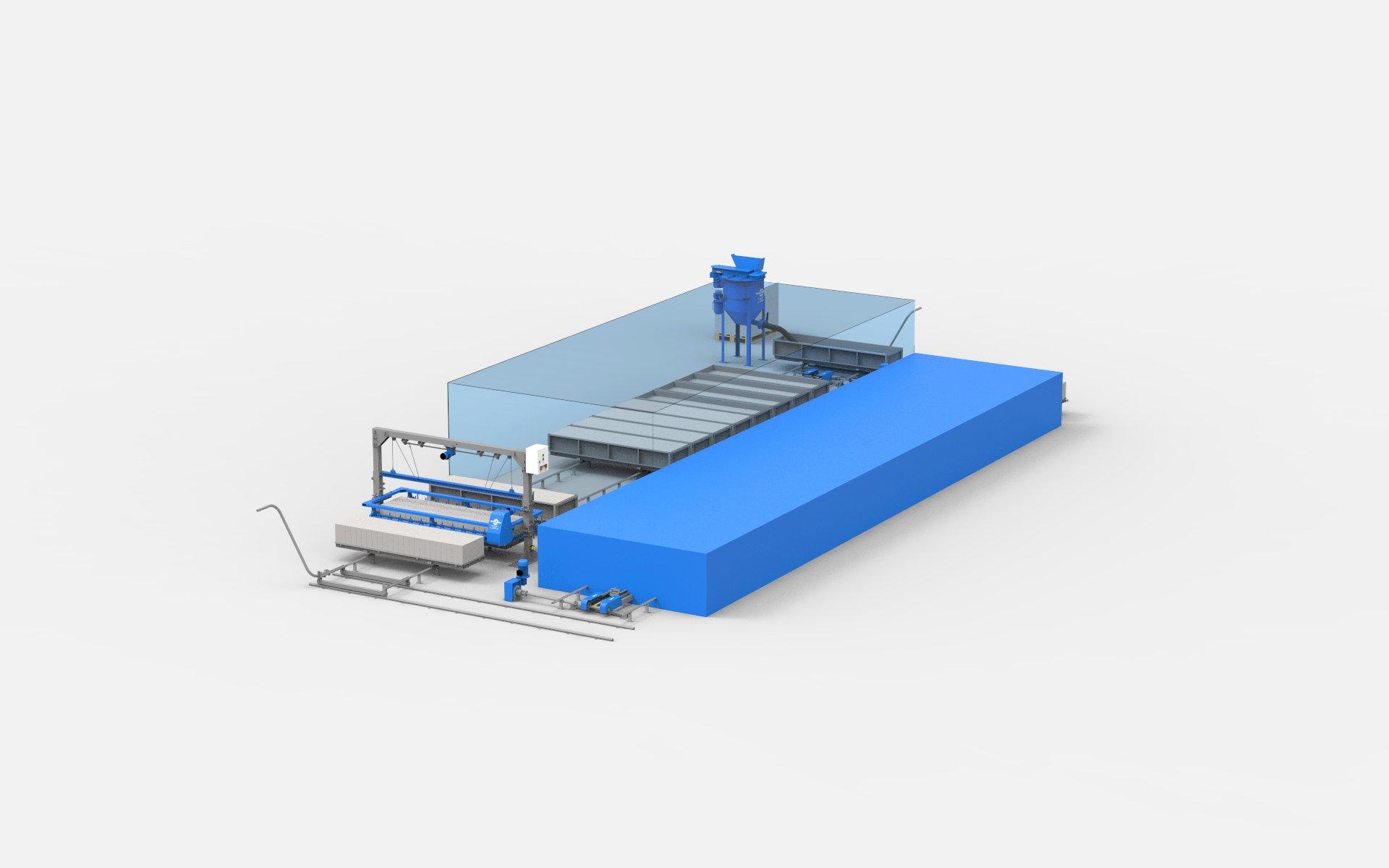

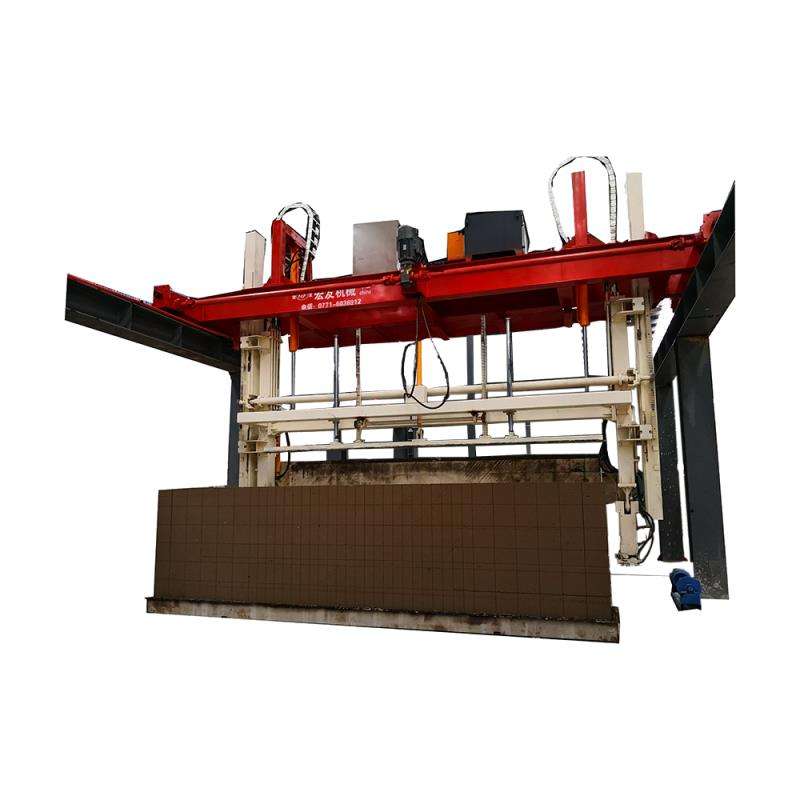



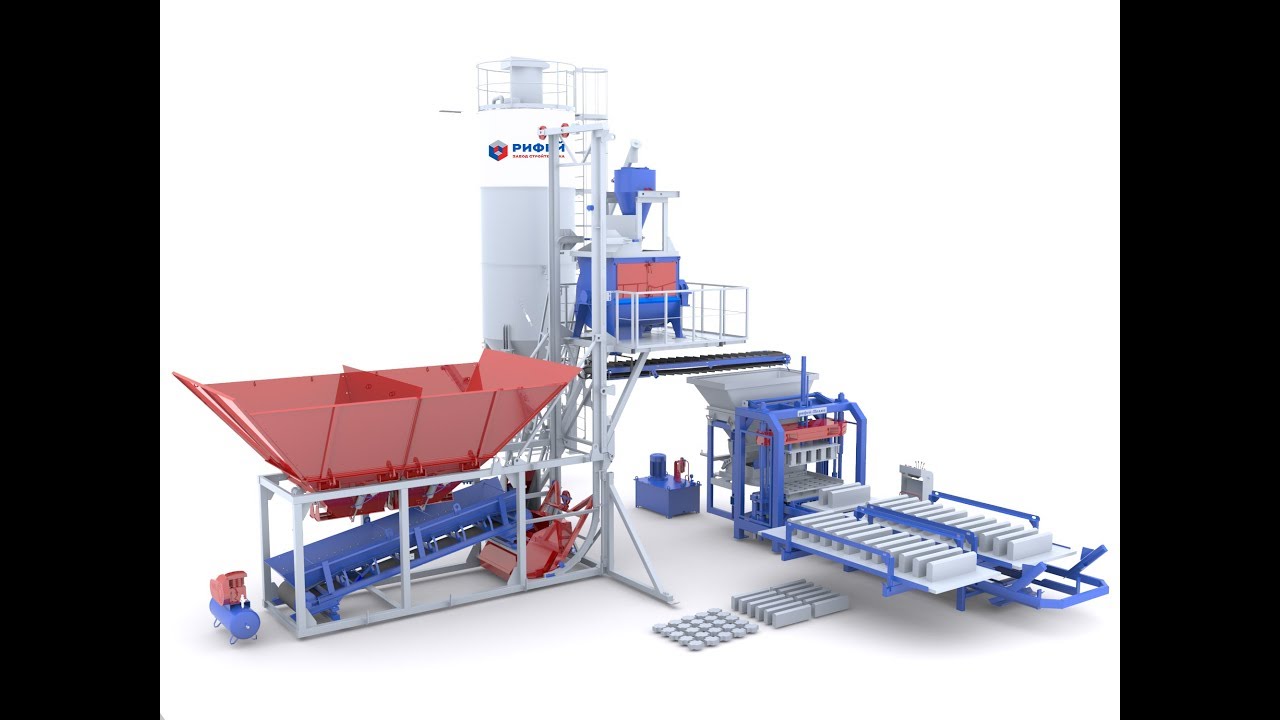



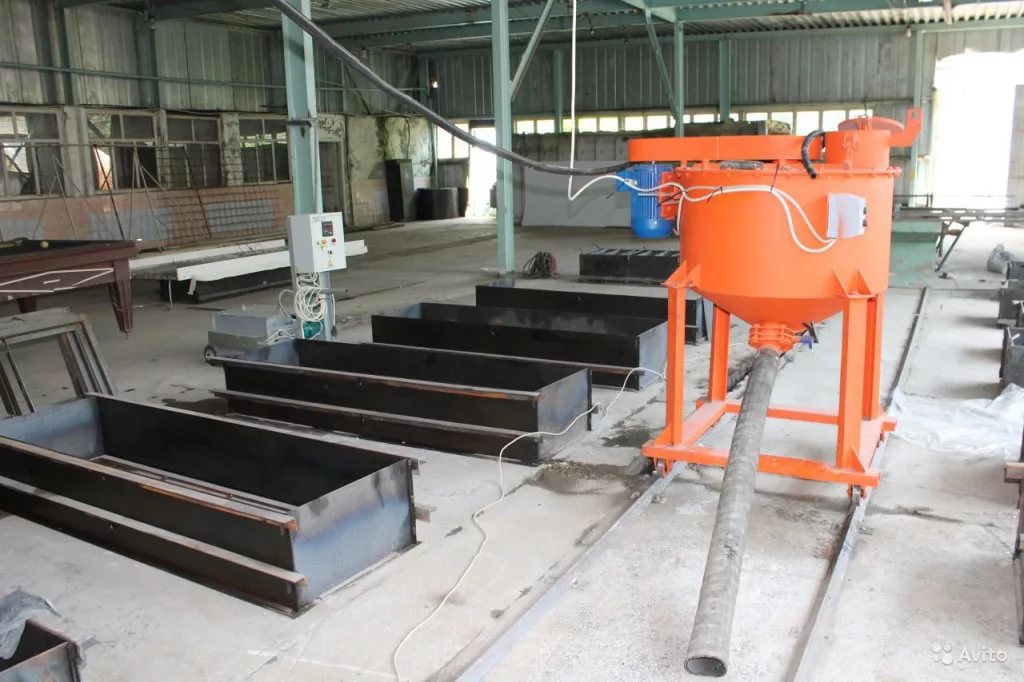
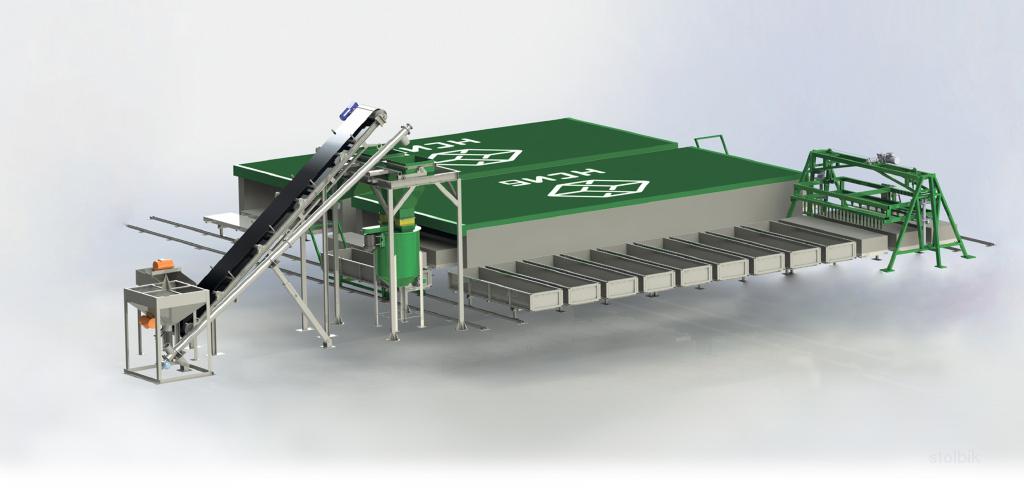
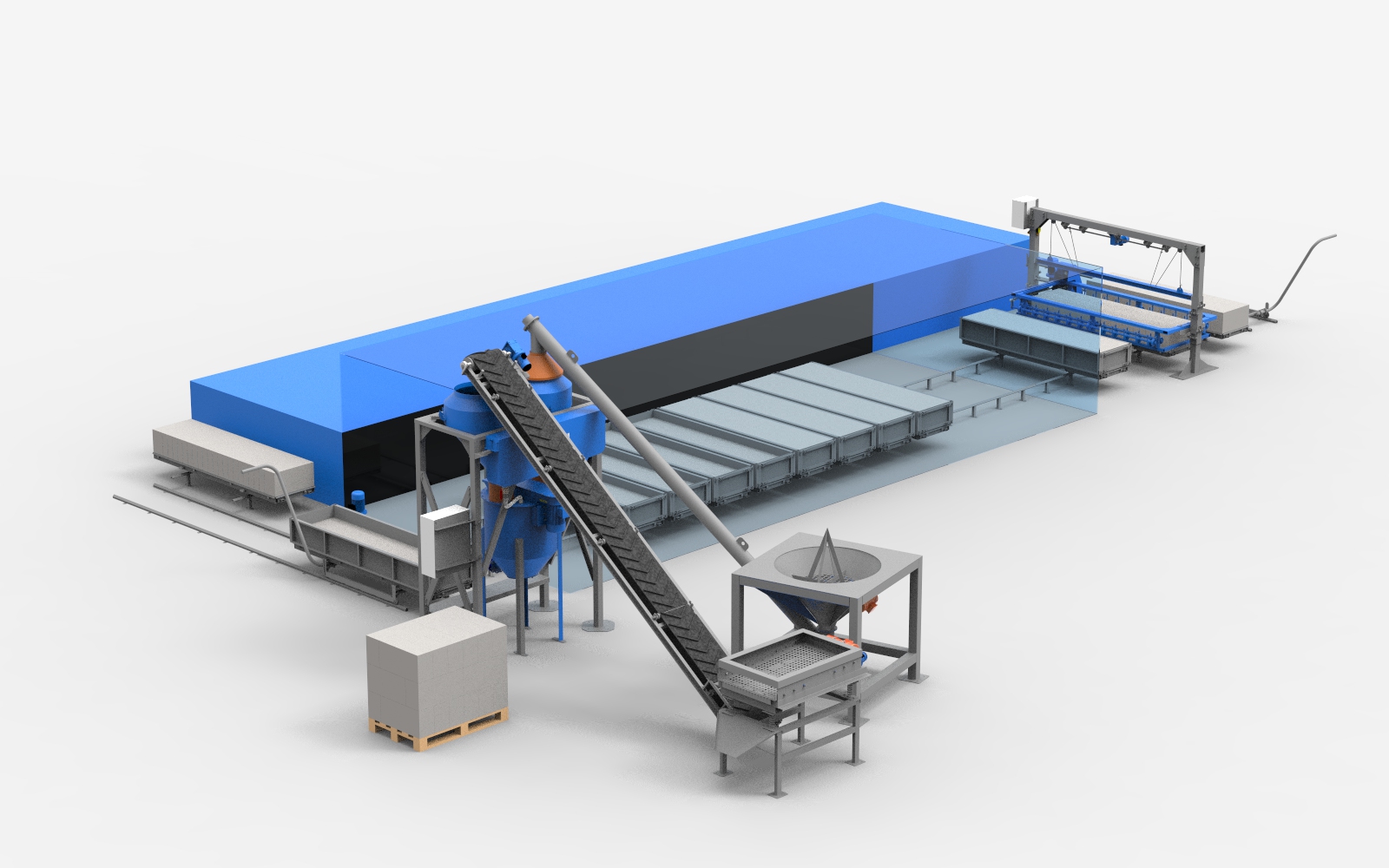
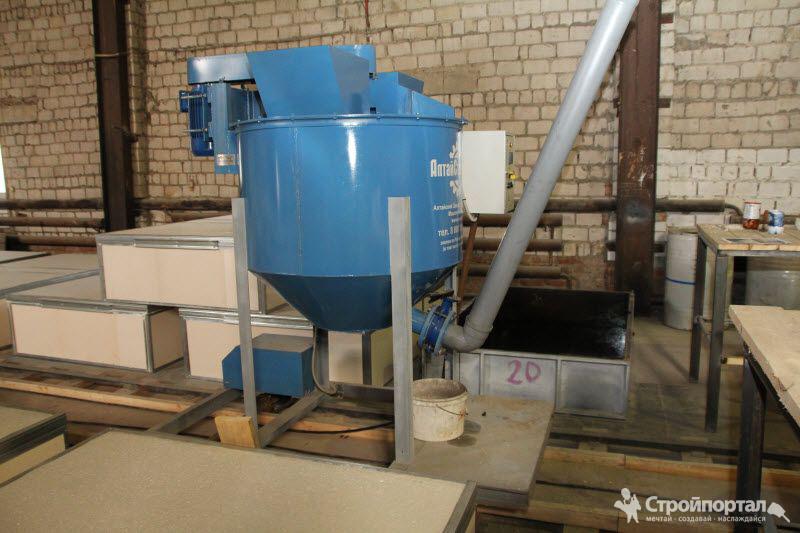


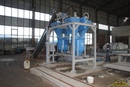
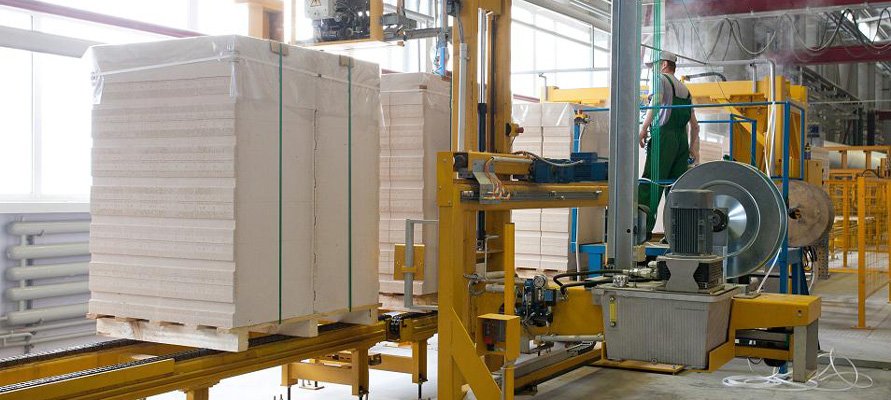

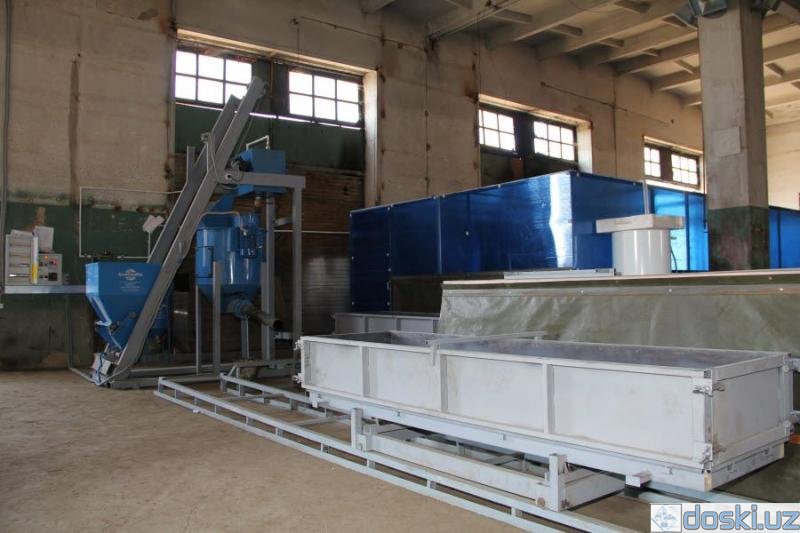
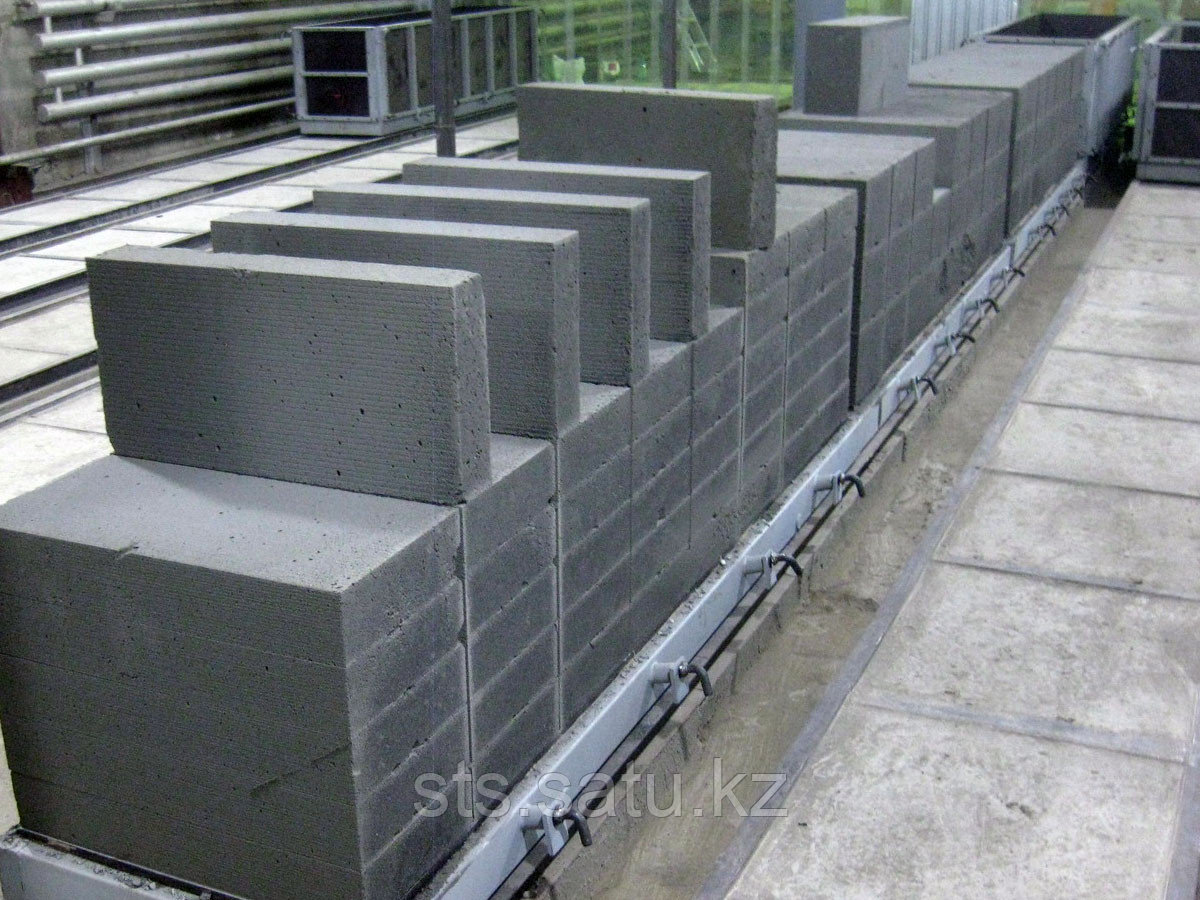



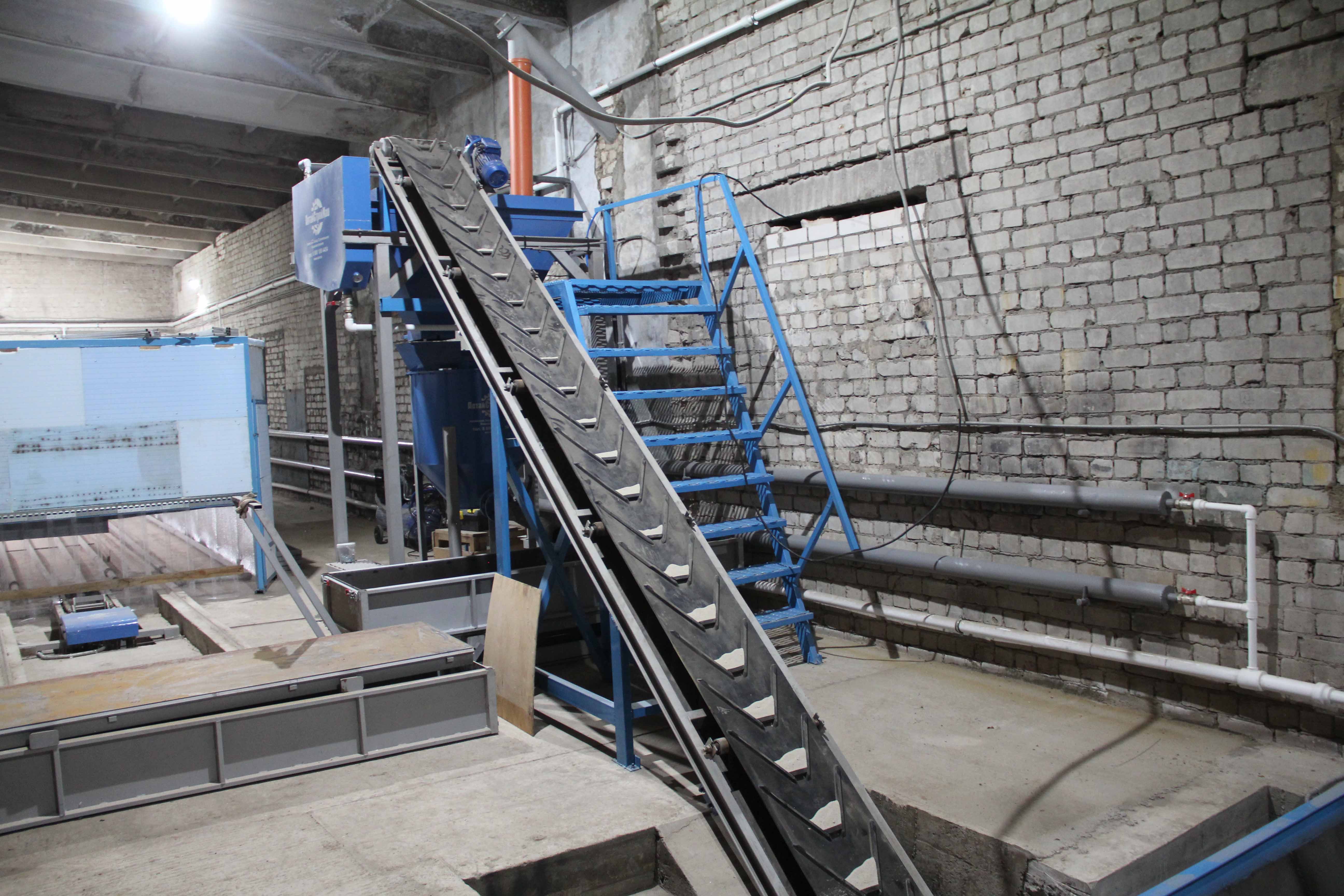
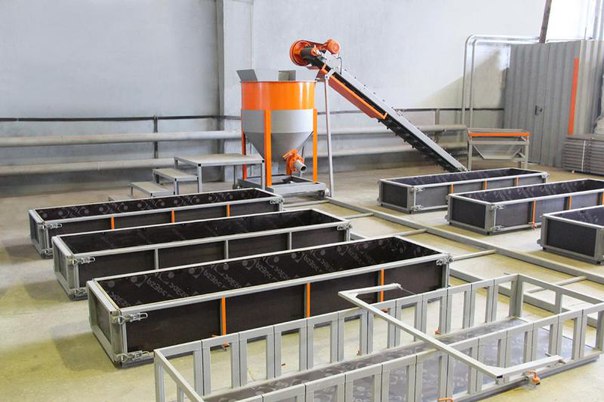


68118083B8CAB4DA62CD2013-04-05T11: 19: 34 + 02: 00Adobe InDesign 7.0 /; / метаданные

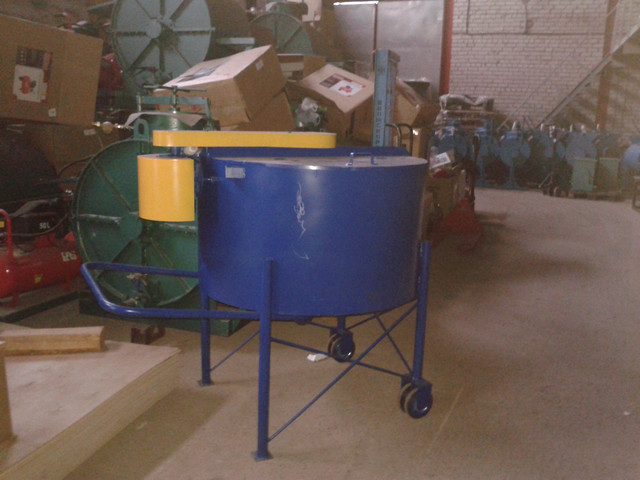
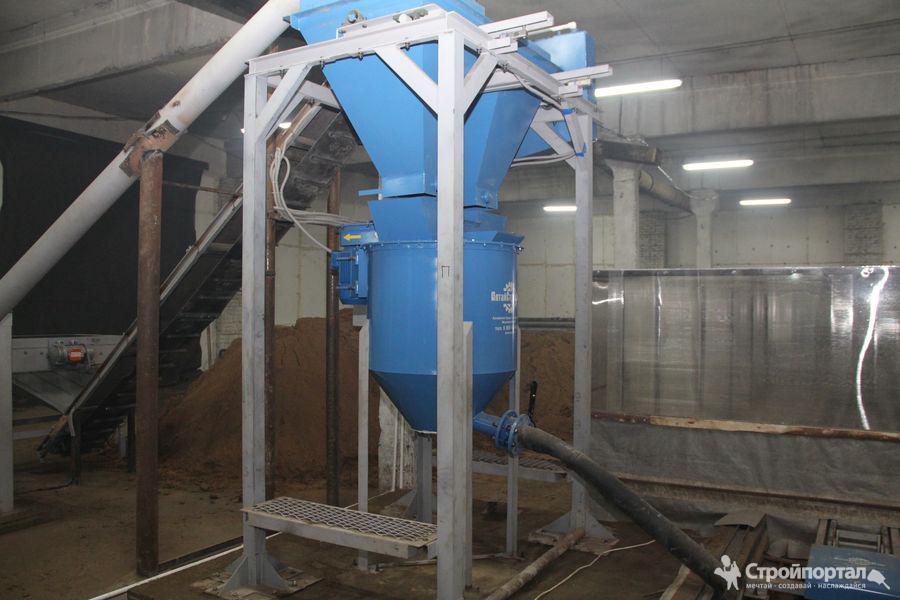



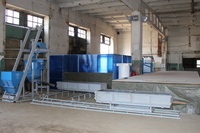
Оборудование для производства пенобетона
Современные технологии позволяют изготавливать газобетонные блоки как на крупных производственных площадках, так и в домашних условиях, при этом легко просчитать и оценить объем продукции, технологические характеристики, а также необходимые финансовые затраты. для запуска производства.В зависимости от того, как вы налаживаете производство, вы можете выбрать стационарное оборудование, мини-завод или компактный мобильный завод по производству газобетонных блоков разной плотности.
Оборудование подбирается под предполагаемую пропускную способность: можно установить оборудование производительностью от 20 до 200 куб. М газобетона в сутки — это параметр (а также степень автоматизации процесса), от которого будет зависеть окончательная цена вашей производственной единицы.
Автоматизированные линии по производству газобетона
Газобетон — прекрасный строительный материал, который активно используется во многих сферах строительства.Газобетонные блоки легкие, прочные и достаточно удобные в строительстве. Запуск линии по производству газобетона в небольшом городке может принести неплохой доход. С помощью этого общего калькулятора вы можете рассчитать окупаемость оборудования для вашего региона. поможет разработать бизнес-план и организовать свой бизнес по производству пенобетона.Для принятия окончательного решения заказчик может сначала посетить малые предприятия и автоматизированные заводы различной производительности, которые успешно эксплуатируют технику Строительных технологий Сибири за счет государства -современные технологии производства газобетона.
Сумма начальных вложений, необходимых для запуска производства газоблоков, зависит от ресурсов заказчика, а если вам необходимо получить оборудование для производства газобетона с минимальными начальными вложениями, есть возможность оформить лизинг или кредит.
По оценкам профессионалов, спрос на газобетонные блоки неуклонно растет. За последние пять лет объемы производства и продаж газобетонных блоков выросли в десять раз.Это связано с ростом строительства малоэтажных и промышленных зданий. А это говорит о том, что грамотно организованный бизнес по производству газоблоков способен приносить стабильно высокую прибыль. Наша компания ориентирована на долгосрочное беспроигрышное партнерство: мы гарантируем высокое качество, отличный сервис, индивидуальный подход, консультации, а также помощь в оформлении таможенных документов и организации доставки в любой регион.
Китайский производитель завода по производству блоков AAC, машина для производства блоков AAC, поставщик производственной линии блоков AAC
Линия для производства блоков из автоклавного пенобетона
Цена FOB: 40 000–80 000 долларов США / Кусок
Мин. Заказ:
1 кусок
Видео
Цена FOB: 1 800 000–3 000 000 долларов США / Набор
Мин.Заказ: 1 комплект
Связаться сейчасВидео
Цена FOB: 500 000–2 000 000 долларов США / Кусок
Мин.Заказ: 1 кусок
Связаться сейчасВидео
Цена FOB: 1 000 000–1 950 000 долларов США / Набор
Мин. Заказ:
1 комплект
Видео
Цена FOB: 750 000–1500 000 долларов США / Кусок
Мин.Заказ: 1 кусок
Связаться сейчасВидео
Цена FOB: 500 000–1500 000 долларов США / Набор
Мин.Заказ: 1 комплект
Связаться сейчасВидео
Цена FOB: 500 000–1500 000 долларов США / Набор
Мин. Заказ:
1 комплект
Видео
Цена FOB: 300 000–1 000 000 долларов США / Набор
Мин.Заказ: 1 комплект
Связаться сейчасЦена FOB: 40 000–70 000 долларов США / Кусок
Мин.Заказ: 1 кусок
Связаться сейчасРекомендовано для вас
Видео
Цена FOB: 10 000–150 000 долларов США / Набор
Мин. Заказ:
1 комплект
Видео
Цена FOB: 10 000–150 000 долларов США / Набор
Мин.Заказ: 1 комплект
Связаться сейчасГорячие продукты
Видео
Цена FOB: 50 000–2 000 000 долларов США / Кусок
Мин. Заказ:
1 кусок
Цена FOB: 500 000–1500 000 долларов США / Кусок
Мин.Заказ: 1 кусок
Связаться сейчасЦена FOB: 45 000–75 000 долларов США / Кусок
Мин.Заказ: 1 кусок
Связаться сейчасВидео
Цена FOB: 10 000–150 000 долларов США / Набор
Мин. Заказ:
1 комплект
Видео
Цена FOB: 750 000–1500 000 долларов США / Кусок
Мин.Заказ: 1 кусок
Связаться сейчасПрофиль компании
{{util.each (imageUrls, function (imageUrl) {}} {{})}} {{if (imageUrls.длина> 1) {}} {{}}}Тип бизнеса: | Производитель / Завод и торговая компания | |
Основные продукты: | Блок-машина AAC | |
Количество работников: | 104 | |
Год основания: | 2004-10-15 | |
Сертификация системы менеджмента: | ISO9001: 2008 | |
Среднее время выполнения: | Время выполнения заказа в пиковый сезон: 3-6 месяцев Время выполнения заказа в межсезонье: 3-6 месяцев |
Компания по производству оборудования для строительных материалов Чанчжоу Mingjie, Ltd, расположенная в зоне развития zhonglou в Чанчжоу, была дочерней компанией Changzhou Diesel Group более 30 лет. Благодаря богатому опыту в области механической обработки, сильной экономической прочности и значительной технической базе, Mingjie является лидером в производстве автоклавного пенобетона. оборудование обрабатывающей промышленности.
В последние годы, в связи с большим изменением времен и быстрым развитием науки и техники, настаивая на духе …
Что такое автоклавный газобетон?
Ячеистый бетон — это растущий строительный материал, особенно для зданий, которым требуется сертификация LEED.
Этот тип сборного железобетона, состоящего из натурального сырья, является строительным стандартом с середины 1920-х годов.
Предлагая его в качестве строительного материала, вы можете увеличить ваш доход — если у вас есть подходящее оборудование для его эффективного производства.
Давайте подробнее рассмотрим, как производится автоклавный газобетон и преимущества его использования.
Производство газобетона автоклавного типа
Этот материал, изобретенный шведским архитектором Йоханом Эрикссоном, стал побочным продуктом продолжающейся индустриализации, которую мир наблюдал с начала до середины 1900-х годов.
Первоначально он был изготовлен с использованием процесса, включающего квасцы сланца; однако позже было обнаружено, что радиоактивный газ был побочным продуктом материала.
Начиная с 1975 года, в качестве заменителей использовались более безопасные связующие (песок, известь, алюминиевый порошок).
Материал требует производства промышленного оборудования.
В автоклавных системах используется процесс парового давления для упрочнения пенобетона после его формирования.
Кварцевый песок в смеси реагирует с гидроксидом кальция из-за огромного давления.
В результате этой реакции образуется гидрат силиката кальция, который является веществом, придающим газобетону его уникальные свойства.
Преимущества автоклавного газобетона
Материал обладает несколькими уникальными характеристиками, которые дают ему преимущество перед традиционным бетоном, в том числе:
- Огнестойкость.
- Уменьшенный вес.
- Эффективность нагрева и охлаждения.
- Долговечный.
- Экологичность и возможны баллы LEED.
- Изоляция (которая со временем экономит деньги ваших клиентов).
Автоклавный газобетон более хрупкий, поэтому рабочим следует обращаться с ним с особой осторожностью.
Автоклавы по индивидуальному заказу из пенобетона
Ваши потребности и технические характеристики — это план, который мы используем при проектировании и создании вашей автоклавной системы.
У индивидуальной автоклавной системы для газобетона есть несколько преимуществ, в том числе:
- Произведено в США.. Многие автоклавы, используемые для производства автоклавного ячеистого бетона в США, были произведены в европейских странах. Производство вашей автоклавной системы здесь, в США, резко сокращает время производства и расходы на доставку, связанные с доставкой автоклава на ваш объект.
- Повышенная производительность. Если производство автоклавных систем отвечает вашим уникальным потребностям, то в дальнейшем сводится к минимуму необходимость адаптировать или настраивать стандартную систему в соответствии с вашими требованиями, что может увеличить ваши общие расходы.
- Специализированный ремонт. Нет никого лучше подходящего для обслуживания и / или ремонта вашего автоклава, чем те, кто построил его с нуля.
Вы можете получить все необходимое для вашей автоклавной системы для газобетона в нашем универсальном центре — от проектирования самой системы до трубопроводов, автоматизации и погрузочно-разгрузочных работ — для перемещения вашего газобетона на протяжении всего производственного процесса.
Мы производим каждый компонент вашего автоклава.Это также означает, что вы в надежных руках при ремонте, который потребуется вашей системе в будущем.
Требуется ли обновление вашей системы автоклавного газобетона?
Автор: Джеффри Липпинкотт
Процесс производства бетонных блоков / панелей — TEEYER
Производственный процесс
(1) Зона разгрузки автоклава (2) Зона защиты от давления пара (3) Блок упорядочивания (4) Нет.1 фрезерный машинный зал (5) Конвейер (6) Бак для смешивания № 1 (7) Бак для смешивания № 2 (8) Смесительный бак для вторичного материала (9) Контейнер для порошка извести (10) Известковый склад (11) Помещение дробления известковых блоков (12) Аппаратная для машинных залов помола извести (13) №2 Фрезерный машинный зал | (14) Емкость для гипса (15) Бетонный контейнер (16) Бетонный цех (17) Переходная зона для процесса заливки (18) Площадь предварительного отверждения (19) Линия извлечения пресс-формы (20) Станок поперечной резки (21) Станок продольной резки (22) Парораспределительная (23) Линия возврата тележки (24) Разделитель (25) Упаковочная линия (26) Зарезервированная зона для обработки стальной арматуры |
Схема нашего оборудования для производства блоков / панелей из автоклавного газобетона представлена на рисунке.Вы можете проверить подробную информацию о производственном процессе и задействованных машинах для бетонных блоков ниже.
1. Взвешивание и дозирование сырья.
2. Загрузите сырье в разливочную машину, чтобы приготовить суспензию.
3. После тщательного перемешивания суспензия выливается в форму.
4. После предварительного отверждения при определенной температуре в течение определенного периода времени лепешки станут достаточно твердыми, чтобы их можно было разрезать.
5. Наклоните подъемник, чтобы повернуть форму более чем на 90 градусов.
6. Затем извлеките торт из формы и поместите торт вместе с боковой пластиной на машину для резки.
7. Две вертикальные стороны блока будут разрезаны перпендикулярно.
8. Затем продольная резка будет производиться в горизонтальном направлении.
9. Наконец, горизонтальная резка будет выполняться в продольном направлении.
10. После нарезки жмых с помощью подъемника для полуфабрикатов подвешивается к тележке с боковыми пластинами.
11. Хорошо разложите кексы и поместите их в автоклав.
12. Закалка коржей при определенной температуре и давлении.
13. Вынуть готовую продукцию из автоклава.
14. Подъемник поднимет готовый продукт в штабель.
15. Продукция упакована для транспортировки.
16. Боковые пластины возвращаются роликом боковой пластины.
17. Боковая пластина и пустая форма будут реорганизованы.
18. Очистите форму и подготовьтесь к следующей заливке.
1.Хранение и транспортировка сырья
Сырье — песок: (1) Хвостовой песок (или кварцевый песок), гипс
Транспортируйте хвостовой песок на завод для хранения. При производстве используйте погрузчик, чтобы загрузить их в бункер, после подачи и дозирования они будут транспортироваться конвейерной лентой на мельницу мокрого помола для тонкого помола и превращения в целлюлозу; При варке следует добавить воду в количестве, это поможет при первоначальном приготовлении суспензии соответствующей концентрации.Тонко измельченная пульпа поступает в смесительный бункер через мельницу, здесь добавляется определенное количество воды для приготовления суспензии с концентрацией, подходящей для производства, а затем с помощью погружного шламового насоса закачивается суспензия в резервуар (100 м3) в резерве. Хвостовой песок соответствующей крупности также может быть добавлен непосредственно в бункер барабанного сита, промыт водой в смесительный бункер для варки целлюлозы. Во время производства существует два метода добавления гипса или фосфогипса: во-первых, в определенном соотношении для добавления вместе с хвостовым песком в машину для мокрого измельчения для измельчения и варки целлюлозы; во-вторых, добавьте гипс в определенном количестве непосредственно в смесительный резервуар для варки целлюлозы, а затем закачивайте в гипсовый резервуар (10 м3) в резерве.
Сырье — зола уноса:
(1) летучая зола, гипс
Принять смешанный процесс варки золы и гипса. При производстве добавьте зольную пыль и гипс в определенном соотношении в ванну для взбивания, чтобы приготовить смешанную суспензию. При варке целлюлозы добавьте воды в количестве, чтобы образовалась суспензия подходящей концентрации. Затем перекачивается шламовым насосом в резервуар для шлама в резерве.
(2) Известь негашеная
Блок негашеной извести доставляется на причал, а затем на грузовиках доставляется на завод для разгрузки и хранения.После дробления на щековой дробилке, подается ковшовым элеватором в бункер для негашеной извести. Затем подается ленточным конвейером закрытого типа в мельницу для измельчения. Порошок негашеной извести после тонкого измельчения транспортируется шнековым конвейером в ковшовый элеватор и, наконец, транспортируется в бункер для порошка негашеной извести.
(3) Цемент
Рассмотрите возможность использования наливного цемента. Цемент навалом доставляется на завод цементовозом, а затем перекачивается прямо в бункер для цементного порошка в резерве.
(4) Алюминиевый порошок
Храните бочки с алюминиевой порошковой пастой на складе.Транспортируется с помощью электрической лебедки на третий этаж бетонного цеха, вручную помещается в смеситель для алюминиевого порошка для перемешивания до 5% суспензии в запасе. Затем с помощью водомера добавьте воды к алюминиевому порошку.
(5) Стальная катанка и нержавеющая краска
Храните стальную катанку и антикоррозионную краску в резерве на соответствующем складе.
(6) Лом и шлам
Лом, нарезанный режущей линией до дна желоба, промывается водой до дна ванны для шлама резательного станка, после постоянной промывки и перемешивания, для чего шлам достигает определенной концентрации, перекачивается погружным шламовым насосом в отходы. резервуар для жидкого навоза (50м3) в резерве.Сточная вода из баков для пульпы, шламов и литейного смесителя падает по трубопроводу в резервуар для сточных вод смесителя, затем закачивается погружным шламовым насосом в резервуар для шлама режущей машины для перемешивания и варки целлюлозы вместе со сточной водой.
2. Дозирование, смешивание, разливка и предварительное отверждение
Известь и цемент подаются с помощью одинарного спирального трубчатого питателя днища силоса в порошковые электронные измерительные весы, после накопленных дозировок выгружаются одиночным спиралевидным трубчатым питателем днища измерительной шкалы в разливочный смеситель.
После открытия клапана каждого резервуара для пульпы (100 м3 и 50 м3) пульпа из хвостового песка и суспензия отходов соответственно выгружаются в смесительный резервуар рядом с резервуаром. Затем закачивают в пульпу электронные измерительные весы замочного цеха для учета накопленных запасов. Когда вес навозной жижи достигает необходимого для дозирования, система автоматического управления закрывает выпускной клапан. Отмеренная суспензия будет залита в миксер в соответствии с инструкциями.
После ручного взвешивания алюминиевой пудры вылейте ее в алюминиевый миксер (1.5м3) для подготовки суспензии в запасе. Смешанная суспензия подается непосредственно в алюминиевую измерительную шкалу, после дозирования выливается в смеситель.
Перед заливкой суспензии температура должна соответствовать технологическим требованиям. Если температуры не хватает, можно нагреть паром. При заливке форма на специальном транспорте доставляется к литейному смесителю.
Разлитая форма транспортируется транспортным средством для предварительного отверждения в камеру предварительного отверждения для статического предварительного отверждения около 1.5ч-3ч.
3. Раскрой и группировка
После статического предварительного отверждения и достижения прочности резания, заготовка будет транспортирована специальным транспортным средством из камеры предварительного отверждения к линии производства отливки — прецизионного цикла резания для обработки с пятисторонней резкой. Весь процесс резки контролируется консолью PLC станка для резки, что обеспечивает автоматическое управление одним касанием.
Обрезанная заготовка транспортируется на станцию перегрузки на земле, где ее переворачивают на 90 ° для очистки дна заготовки.После завершения заготовка транспортируется в машину для паровой полимеризации, каждая тележка с тремя формами, каждый рельсовый путь автоклава с шестью паровыми машинами для полимеризации.
4. Автоклав и готовая продукция
Сгруппированная заготовка транспортируется в автоклав тяговым механизмом каждой дорожки для отверждения паром. Время отверждения заготовки паром при постоянном давлении в автоклаве составляет около 6 часов, давление пара — 1,2 МПа, температура — около 183 ℃. После автоклавирования и обработки продукты будут извлечены из автоклава лебедкой.
5. Разделка и готовая продукция
Ролики транспортируют готовую продукцию (с боковыми пластинами) на отрезную машину для отделения блока или пластины. Отделенные готовые изделия роликами транспортируются к крану для подъема готовых изделий. В том числе плиты поднимаются в зону перехода и транспортируются вилочными погрузчиками в зону ремонта для осмотра и ремонта, отремонтированные плиты транспортируются вилочными погрузчиками на площадку хранения.Блоки поднимаются на линию упаковки блоков, после ручной упаковки транспортируются вилочными погрузчиками на склад.
6. Возврат боковых пластин, сборка пресс-формы и масляное покрытие
После завершения подъема готовой продукции пустая боковая пластина продолжает движение по ролику к оборотной системе автоклава, затем оборотный распределитель поднимает раму формы и боковую пластину, которые должны быть объединены в форму, и поворачивается на 90 °, чтобы быть поднимается на линию возврата формы.Здесь форма будет очищена и покрыта маслом, а затем проведена циркуляционная заливка.
7. Производство арматуры и сушка покрытий
Арматура обрабатывается правильным и отрезным станком на различные размеры и длину и укладывается на полки.
При производстве стальной сетки поместите несколько длинных и коротких арматурных стержней в арматурный ящик автоматического многоточечного сварочного аппарата, а затем в соответствии с производственными потребностями сварите лист с одной сеткой с помощью автоматического многоточечного сварочного аппарата, каждый раз по две штуки.
После того, как будет сформирован единый сетчатый лист, возьмите верхний и нижний сетчатый лист и несколько фитингов, которые необходимо приварить в стальном сетчатом каркасе с помощью сварочного аппарата для одиночной точечной сварки подвесного типа, а затем транспортировать их к переднему концу сушильного бокса для покрытия.
Транспортировать антикоррозионную краску в бочках в переднюю часть сушильного бокса зоны обработки стали, после того, как она будет перемешана с жидкостью с помощью смесителя консервирующей жидкости, залита в резервуар для антикоррозионной погружной мешалки в резерве.
Каркас из стальной сетки под подъемной балкой поднимают, затем транспортируют однобалочным краном и опускают в антикоррозионную погружную мешалку, после чего поднимают решетку и кладут на конвейерные цепи сушильной печи.Скорость транспортировки цепей составляет 1,7 м / мин, клетка будет перемещаться от переднего конца к заднему концу сушильного бокса, при этом сетчатое покрытие высохло. Если толщина покрытия не может соответствовать производственным требованиям, можно повторить процесс погружения и сушки. Высушенная клетка из стальной сетки будет подниматься и транспортироваться однобалочным краном на полку из листовой сетки в резерве.
8. Сборка сетчатого листа, установка и извлечение стержня
При производстве готовая клетка транспортируется в сторону подъемной рамы сетки камеры предварительного отверждения, а затем поднимается на второй этаж камеры предварительного отверждения.Имеются два ряда полок для размещения сетчатого каркаса, один ряд используется для размещения пустой рамки после извлечения стержня (ряд A), другой ряд используется для размещения собранной рамки (ряд B). Рабочие собирают сетку в ряду B, после того как закончили, чтобы транспортировать в ряд A для вставки стержня в форму. После литья под давлением выполните установку стержня, затем, после предварительного отверждения заготовки формы, выполните извлечение стержня. Готовая заготовка будет перенесена на режущую сторону отрезного станка.
Если вам нужна дополнительная информация о процессе производства нашего оборудования для производства бетонных блоков / панелей, свяжитесь с нами в любое время. Приглашаем вас также лично посетить нашу компанию.
Производство автоклавного газобетона | Группа Маса
Газобетон изготавливается из сырья: кварцевого песка, извести, цемента, гипса (ангидрита), алюминиевого порошка или пасты и воды.
В шаровой мельнице с мокрым покрытием (01) сырой песок перерабатывается в песчаную суспензию, которая хранится в резервуарах для песчаной суспензии.Затем песчаная суспензия вместе с другим сырьем транспортируется на дозирующую и смесительную установку Masa (02).
Когда процесс смешивания завершен, смесь подается в литейную форму. Литейную форму перемещают в зону предварительного затвердевания, чтобы пройти процесс ферментации (03), в ходе которого лепешка из пенобетона, наконец, достигает заданной прочности на резку. В этот момент лепешка из газобетона извлекается из формы (04) в два этапа, сначала удаляются боковые стороны. Затем пустую литейную форму собирают, смазывают маслом (05) и возвращают в производственный цикл.
Пирог из газобетона проходит через различные станции линии резки (06) и после этого помещается на решетку для твердения с помощью транспортной установки / поворотного стола (07).
Три кека на решетках для закалки укладываются друг на друга на тележку для закалки и транспортируются в зону ожидания (08) с помощью транспортной платформы. Отсюда лепешки загружаются в автоклавы (09). Внутри автоклавов лепешки из пенобетона затвердевают под давлением пара и создают свою окончательную прочность.
Кексы из затвердевшего газобетона затем транспортируются к наклоняющемуся столу (10) и, при необходимости, к разделительной машине (11).
После этого газобетонные блоки транспортируются к устройству передачи блоков (12) и укладываются на деревянные поддоны. Отсюда готовая продукция фасуется (13).
Использованные закалочные решетки и закалочные машины возвращаются в производственный цикл через устройство транспортировки закалочной решетки и устройство возврата закалочной тележки (10).
Завод может быть расширен оборудованием для производства изделий со стальной арматурой (14).
Автоклавный газобетон
Автоклавный газобетон (AAC) состоит из мелких заполнителей, цемента и расширителя, который заставляет свежую смесь подниматься, как тесто для хлеба. Фактически, этот вид бетона на 80 процентов содержит воздух. На заводе, где он изготавливается, материал формуют и разрезают на детали с точными размерами.
Затвердевшие блоки или панели из автоклавного газобетона соединяются тонким слоем раствора.Компоненты можно использовать для стен, полов и крыш. Легкий материал обеспечивает отличную звуко- и теплоизоляцию и, как и все материалы на основе цемента, является прочным и огнестойким. Чтобы быть долговечным, AAC требует некоторого вида отделки, например, модифицированной полимером штукатурки, природного или искусственного камня или сайдинга.Ключевые аспекты AAC, будь то проектирование или строительство с его помощью, описаны ниже:
Преимущества
- Автоклавный газобетон сочетает в себе изоляционные и структурные возможности в одном материале для стен, полов и крыш.Его легкий вес / ячеистые свойства позволяют легко резать, брить и придавать форму, легко принимать гвозди и винты, а также позволяют направлять его для создания пазов для электрических каналов и трубопроводов меньшего диаметра. Это дает ему гибкость при проектировании и изготовлении, а также дает возможность легко регулировать в полевых условиях.
- Прочность и стабильность размеров. Материал на основе цемента, AAC устойчив к воде, гниению, плесени, плесени и насекомым. Установки имеют точную форму и соответствуют жестким допускам.
- Огнестойкость отличная, AAC толщиной восемь дюймов достигает четырехчасового рейтинга (фактическая производительность превышает это значение и соответствует требованиям испытаний до восьми часов). А поскольку он негорючий, он не горит и не выделяет токсичных паров.
- Малый вес означает, что значения R для AAC сопоставимы с обычными каркасными стенами, но они имеют более высокую тепловую массу, обеспечивают герметичность и, как только что было отмечено, не горючие.Этот легкий вес также обеспечивает значительное снижение уровня шума для уединения как от внешнего шума, так и от других помещений при использовании в качестве внутренних перегородок.
Но у материала есть некоторые ограничения. Он не так широко доступен, как большинство изделий из бетона, хотя его можно доставить куда угодно. Если он должен быть отправлен, его легкий вес является преимуществом. Поскольку его прочность ниже, чем у большинства бетонных изделий или систем, в несущих приложениях его обычно необходимо армировать. Он также требует защитной отделки, поскольку материал пористый и будет разрушаться, если оставить его незащищенным.
Размеры
Доступны как блоки, так и панели. Блоки укладываются так же, как и обычная кладка, но с тонким слоем раствора, а панели устанавливаются вертикально на всю высоту этажа. Для структурных нужд внутри стеновой секции размещаются залитые, армированные ячейки и балки. (Вогнутые углубления вдоль вертикальных краев могут создать цилиндрическую сердцевину между двумя соседними панелями.) Для обычных применений вертикальная ячейка размещается по углам, по обе стороны от отверстий и на расстоянии от 6 до 8 футов вдоль стены.AAC в среднем составляет около 37 фунтов на кубический фут (pcf), поэтому блоки можно размещать вручную, но панели из-за их размера обычно требуют небольшого крана или другого оборудования.
Панели простираются от пола до верха стены:
- Высота: до 20 футов
- Ширина: 24 дюйма
- Толщина: 6, 8, 10 или 12 дюймов (внутренняя толщина 4 дюйма
Блоки больше и легче традиционной бетонной кладки:
- Высота: обычно 8 дюймов
- Ширина: 24 дюйма в длину
- Толщина: 4, 6, 8, 10 и 12 дюймов
- Стандартные 8 на Блок размером 8 на 24 дюйма весит около 33 фунтов;
Специальные формы:
- U-образная соединительная балка или блоки перемычки доступны толщиной 8, 10 и 12 дюймов.
- Блоки для язычков и пазов доступны от некоторых производителей, и они соединяются с соседними блоками без раствора по вертикальным краям.
- Порошковые блоки для создания вертикальных ячеек с армированным раствором.
Установка, соединения и отделка
Благодаря схожести с традиционной бетонной кладкой, блоки (блоки) из автоклавного газобетона могут быть легко установлены каменщиками. Иногда к монтажу подключаются плотники. Панели тяжелее из-за своего размера и требуют использования крана для установки.Производители предлагают обучающие семинары, и обычно достаточно иметь одного или двух знающих установщиков для небольших проектов. В зависимости от выбранного типа отделки они могут быть приклеены непосредственно или механически к поверхности AAC.
Блок
- Первый слой уложен и выровнен. Блоки укладываются вместе с тонким слоем строительного раствора непрерывным соединением с перекрытием не менее 6 дюймов.
- Стены выровнены, выровнены и выровнены резиновым молотком.
- Отверстия и нестандартные углы вырезаются ножовкой или ленточной пилой.
- Определены места армирования, размещена арматура и выполняется заливка раствора. Затирку необходимо подвергнуть механической вибрации для ее уплотнения.
- Связующие балки размещаются в верхней части стены и могут использоваться для крепления тяжелых приспособлений.
Панели
- Панели размещаются по одной, начиная с угла. Панели устанавливаются в слой тонкослойного раствора, а вертикальная арматура прикрепляется к дюбелям, выступающим от пола, до того, как будет размещена соседняя панель.
- Сплошная соединительная балка создается наверху либо из фанеры и материала AAC, либо с помощью соединительной балки.
- Отверстия можно вырезать заранее или в полевых условиях.
Соединения
- Рама / каркас крыши соединяется с обычной верхней пластиной или ураганными ремнями, встроенными в соединительную балку.
- Каркас пола крепится с помощью стандартных ригелей, закрепленных на стороне узла AAC, рядом с соединительной балкой.
- Напольные системы AAC опираются непосредственно на стены AAC.
- Более крупные конструкционные стальные элементы устанавливаются на приварные пластины или пластины с болтами, вставленные в соединительную балку.
Отделка
- Отделка типа Stucco изготавливается специально для AAC. Эти модифицированные полимером штукатурки герметизируют от проникновения воды, но при этом пропускают пары влаги для воздухопроницаемости.
- Обычные сайдинговые материалы прикрепляются к поверхности стены механически. Если желательна обратная вентиляция сайдингового материала, следует использовать опушку.
- Кладочный шпон можно приклеивать непосредственно к поверхности стены или строить как полую стену. Виниры прямого наложения, как правило, представляют собой легкие материалы, например искусственный камень.
Соображения об устойчивости и энергопотреблении
Автоклавный газобетон с точки зрения устойчивого развития предлагает как материалы, так и характеристики. Что касается материала, он может содержать переработанные материалы, такие как летучая зола и арматура, которые могут способствовать получению баллов в системе LEED® или других экологических рейтинговых системах.Кроме того, он содержит такое большое количество воздуха, что содержит меньше сырья на единицу объема, чем многие другие строительные продукты. С точки зрения производительности система ведет к ограничению ограждающих конструкций здания. Это создает энергоэффективную оболочку и защищает от нежелательных потерь воздуха. Физические испытания демонстрируют экономию на нагреве и охлаждении примерно от 10 до 20 процентов по сравнению с традиционной конструкцией рамы. В постоянно холодном климате экономия может быть несколько меньше, потому что этот материал имеет меньшую тепловую массу, чем другие типы бетона.В зависимости от местоположения производства по отношению к объекту проекта, AAC может также вносить вклад в местные кредиты на материалы в некоторых системах рейтинга экологичного строительства.
Производственные и физические свойства
Сначала в суспензию смешивают несколько ингредиентов: цемент, известь, воду, мелкоизмельченный песок и часто летучую золу. Добавляется расширительный агент, такой как алюминиевый порошок, и жидкая смесь отливается в большую заготовку. Когда суспензия реагирует с расширителем с образованием пузырьков воздуха, смесь расширяется.После первоначального застывания полученный «пирог» разрезается проволокой на блоки или панели точного размера и затем запекается (автоклавируется). Тепло способствует более быстрому отверждению материала, благодаря чему блоки и панели сохраняют свои размеры. Армирование помещается в панели перед отверждением.
В ходе этого производственного процесса производится легкий негорючий материал со следующими свойствами:
Плотность: от 20 до 50 фунтов на кубический фут (pcf) — он достаточно легкий, чтобы плавать в воде
Прочность на сжатие: 300 до 900 фунтов на квадратный дюйм (psi)
Допустимое напряжение сдвига: от 8 до 22 psi
Термическое сопротивление: 0.От 8 до 1,25 на дюйм. толщины
Класс звукопередачи (STC): 40 для толщины 4 дюйма; 45 для толщины 8 дюймов
Автоклавный газобетон
В настоящее время нет торговой ассоциации, представляющей отрасль автоклавного газобетона. Производство AAC все еще существует в Северной Америке. Мы предлагаем вам поискать в Интернете представителей дилеров, которые могут помочь вам с потенциальной доступностью продукта в вашем регионе.
Проекты AAC
История трех городов: универсальность AAC для жилых помещений
Использование газобетона в автоклаве (AAC) дает множество преимуществ.Возможно, в подтверждение универсальности AAC, три описанных здесь жилых проекта совершенно разные, но имеют общую тему безопасности. Большой дом на одну семью в лесу, строительство которого ведет сам хозяин; скромный дом на одну семью на лесистой местности, спроектированный архитектором, стремящимся к экологически безопасному и здоровому образу жизни; и крупная застройка вдоль побережья залива Луизиана, требующая превосходной погодоустойчивости.
Handal Home, Мэриленд: простота и безопасность
Эта большая резиденция (6800 квадратных футов), расположенная в лесу на юге штата Мэриленд, столкнулась с рядом строительных проблем.Таким образом, владелец, который сам управляет строительством, хотел простую систему. Это оказались 12-дюймовые блоки AAC. Ему нужны были их теплоизоляционные и негорючие свойства, чтобы противостоять лесным условиям дома, которые включали низкие температуры и, возможно, опасность пожара. По его словам, простота AAC позволяет ему за один шаг построить конструктивную стену, которая будет изолирована, устойчива к термитам и готова к отделке. Он не хотел прикреплять сайдинг, предпочитая вместо этого прямую отделку: гипсовую штукатурку для интерьера и лепнину для экстерьера.
Дом Додсона: здоровый и безмятежный
Несколько лет назад, когда архитектор Элис Додсон выбрала компанию AAC для строительства собственного дома, это было отчасти из соображений здоровья и окружающей среды. Давний сторонник устойчивого развития, она также уже следила за Bau-biologie. Относительно неизвестный в Соединенных Штатах, но хорошо известный в Европе среди архитекторов и медицинских работников, Bau-biologie занимается биологией строительства или строительством для жизни. Это произошло после того, как быстрое строительство в послевоенной Германии привело к тому, что мы теперь называем синдромом больного здания.Тогда, как и сейчас, она искала здоровые строительные решения. С этой целью она выбрала блоки и панели из AAC, чтобы получить воздухопроницаемые стены из каменной кладки, которые не выделяют летучие органические соединения (ЛОС). Это создает экологически чистое здание со спокойным и тихим интерьером. А поскольку в процессе строительства участвовал ее муж-пожарный, негорючие материалы были необходимы.
Оболочка из AAC также обеспечивает хорошую теплоемкость и изоляцию. Благодаря энергоэффективной оболочке, дополненной солнечными батареями и дровяной печью, счета за газ в течение первого года составляли всего 100 долларов для дома площадью 4000 квадратных футов.В доме может оставаться тепло в течение двух-трех дней даже после отключения электроэнергии. Додсону нравится, как из материала можно вылепить с помощью деревообрабатывающих инструментов различные формы и элементы, такие как колонны и камины, и он продолжает поддерживать AAC с клиентами, которые ценят его универсальность и эстетический потенциал.
Роща на пляже Инлет: безопасность и устойчивость к погодным условиям
Эта история успеха произошла в результате разрушений, вызванных ураганом Катрина. The Grove at Inlet Beach — это первый жилой комплекс с высокой плотностью застройки, построенный компанией Florida Panhandle. Он предназначен для противостояния погодным условиям и безопасности в окружающей среде на побережье Мексиканского залива.Все стены, полы и потолки в этих домах для одной семьи сделаны из панелей и блоков AAC. Превосходная огнестойкость (четыре часа на четыре дюйма) была ключом к утверждению местного зонирования, и в результате не возникло проблем с возгоранием конструкции. Когда прибывают ураганы, эти конструкции готовы противостоять ветрам со скоростью 150 миль в час (категория 4) и с надлежащим усилением могут быть спроектированы так, чтобы противостоять ветрам со скоростью 200 миль в час и более (Категория 5). Дома AAC также не разрушаются наводнениями: они противостоят поднимающимся водам, гниению, плесени и плесени, их можно чистить, перекрашивать и снова открывать для жителей — восстановление не требуется.
Как будто безопасность и устойчивость к погодным условиям не были достаточной причиной для выбора AAC для своего дома, застройщик рассчитывает сэкономить 35 процентов на счетах за коммунальные услуги и 65 процентов на страховых взносах.
Комфорт бетона
Некоторые гости в отеле Джорджии сегодня спят лучше благодаря автоклавному пористому бетону (AAC). Примерно в часе езды от Атланты, на месте Форсайта, штат Джорджия, Comfort Suites, небольшой участок, прилегающий к межштатной автомагистрали, возник несколько проблем.А высокая стоимость земли делает все более распространенным строить на участках, которым присущи такие проблемы, как шум, неровная местность или минимальные препятствия.