Оборудование для производства автоклавного газобетона
Автоматизированная линия для производства стеновых и перегородочных блоков из автоклавного газобетона по прогрессивной виброударной технологии.
Краткие характеристики оборудования для производства автоклавного газобетона
- Максимальная производительность (по заливке) – до 250 м3 готовой продукции в сутки.
- Расчетная производительность — до 200 м3 готовой продукции в сутки.
- Готовая продукция — блоки стеновые и перегородочные с маркой по средней плотности D400-D600 с прочностью на сжатие В2-В3,5.
- Объем массива – 1 м3 .
- Время заливки одного массива — около 6 минут.
- Время выдержки массива до резки — 3 — 4 часа.
- Время автоклавной обработки — 12 часов.
- Складской запас цемента — 120 т.
- Складской запас наполнителя — 120 т.
- Установленная мощность оборудования — 240 кВт. (без участка помола)
- Потребление воды — 50 т воды в сутки.
- Обслуживающий персонал — 11 человек.
- Площадь цеха не менее 2500м2.
- Высота в зоне заливки 8,5м.
- Высота остального помещения не менее 4,5м.
Отличительные особенности наших линий по производству автоклавного газобетона
Все основное оборудование располагается на площади 2,5 тысячи кв. метров. Это позволяет поставить завод практически в любом месте, где есть коммуникации, например, рядом со строительной площадкой, производством вяжущего или карьером песка.
- МАЛЫЕ КАПИТАЛОВЛОЖЕНИЯ
Относительно небольшая производительность не требует строительства сложной инфраструктуры (железнодорожная станция, разгрузочные терминалы, административные и вспомогательные помещения и т.д.) Все необходимые сырьевые материалы комфортно доставляются автомобильным транспортом.
- БЫСТРАЯ ОКУПАЕМОСТЬ
Небольшие капитальные затраты, короткий срок запуска предприятия и высокое качество продукции позволят сократить срок окупаемости проекта до 1,5 года.
- КАЧЕСТВО ПРОДУКЦИИ
В проектировании оборудования учитывался весь имеющийся мировой опыт производства автоклавного ячеистого бетона. Газобетонные блоки, выпущенные на нашей линии, соответствуют самым жестким мировым стандартам, как по физико-химическим свойствам, так и по геометрии.
- АВТОМАТИЗАЦИЯ
Все элементы оборудования полностью автоматизированы. Главные пульты оснащены сенсорными панелями управления, работают функции учета и контроля. Автоматическая система управления работает на базе промышленной линейки японских контроллеров от мировых лидеров Mitsubishi и Omron.
Сырье для производства блоков из автоклавного газобетона
- ВЯЖУЩИЕ МАТЕРИАЛЫ
— портландцемент по ГОСТ 31108 и ГОСТ 10178 без добавок трепела, глиежа, трассов, глинита, опоки, пеплов, содержащий трехкальциевый алюминат (С3А) не более 8 % по массе.
Сроки схватывания: начало — не ранее 2 ч, конец — не позднее 4 ч;
— высокоосновная зола, содержащая СаО не менее 40 %, в том числе свободный СаО — не менее 16 %, SО3 — не более 6 % и R2О — не более 3,5 %;
— известь негашеная кальциевая по ГОСТ 9179, быстро- и среднегасящаяся, имеющая скорость гашения 5-25 мин и содержащая активные СаО + МgО не менее 70 %, «пережога» — не более 2 %.
- КРЕМНЕЗЕМНИСТЫЕ КОМПОНЕНТЫ
— природные материалы — кварцевый песок, содержащий SiO2 не менее 85 %, илистых и глинистых примесей не более 3 %, монтмориллонитовых глинистых примесей — не более 1,5 %;
— вторичные продукты промышленности и энергетики: золы-унос теплоэлектростанций, продукты обогащения различных руд, продукты собственного производства («горбушки», обрезки).
- ДОБАВКИ ДЛЯ РЕГУЛИРОВАНИЯ И УЛУЧШЕНИЯ СВОЙСТВ АВТОКЛАВНОГО ГАЗОБЕТОНА
— доменные гранулированные шлаки по ГОСТ 3476;
— гипсовый камень по ГОСТ 4013.
- ГАЗООБРАЗОВАТЕЛЬ
— алюминиевая пудра или паста на основе алюминиевой пудры
- ВОДА по ГОСТ 23732.
Подготовка и складирование сырья
ВЯЖУЩИЕ (цемент, известь) из цементовозов или прижелезнодорожного разгрузочного устройства при помощи компрессорной установки пневмо-транспортом загружаются в расходные силосы.
ДОБАВКИ (жидкие) заливаются в специальные емкости, где они перемешиваются с водой и доводятся до необходимой температуры, сухие добавки дозируются в мельницу вместе с песком.
НАПОЛНИТЕЛЬ (песок) подается в шаровую мельницу мокрого помола и после этого поступает в специальный шламовый бассейн. В этот же бассейн поступает подготовленная водная смесь из отходов производства (обрезки, горбушки).
ГАЗООБРАЗОВАТЕЛЬ (алюминиевая пудра или паста) загружается в отделение суспензиатора для приготовления водной суспензии.
Смешивание компонентов
Смешивание всех сухих и жидких компонентов происходит в несколько этапов.
На центральном пульте управления заводом производится контроль, обработка и управление всеми важными функциями установки на всех этапах приготовления газобетонной смеси.
Управление всем процессом смесеприготовления осуществляется с пульта управления, расположенного под смесительной башней и рядом с постом заливки смеси в формы.
Дозировка компонентов и процесс смешивания газобетонной смеси происходят полностью автоматически и контролируются компьютером управления, в котором заложены программы рецептов для получения ячеистого бетона требуемого качества.
Оператор в режиме реального времени отслеживает все процессы работы установки. В случае необходимости оператор за короткое время может скорректировать или изменить текущий состав, время перемешивания, температурный режим и другие технологические параметры на электронной панели главного пульта или при помощи компьютера. Также оператор может перевести работу установки в полуавтоматический или ручной режим управления.
Резка блоков автоклавного газобетона
Резка газобетонных массивов осуществляется на резательных станках Риф-1 или на струнном резательном станке.
Автоклавная обработка массива занимает 12 часов и состоит из четырех этапов:
— вакуумирование;
— подъем давления;
— изотермическая выдержка;
— сброс давления и подготовка к выгрузке.
В зависимости от состава смеси, в процессе изотермической выдержки поддерживается температура от 180 до 193 С, давление от 8 до 13 бар.
Управление процессами автоклавной обработки происходит на специальном пульте управления в автоматическом режиме.
Транспортировка автоклавных блоков
Пройдя этап автоклавной обработки, разрезанный массив на тележке выкатывается на разборку. Блоки укладываются на транспортировочные поддоны, стягиваются скреплентой и при помощи погрузчиков подаются на складскую площадку или в складское помещение.
www.promcompany.ru
Линии для производства газобетона — АлтайСтройМаш
Грамотно подобранное оборудование для производства газобетона поможет с полным правом рассчитывать на прибыль. Компания «Алтайстроймаш» способна реализовать любой ваш проект по производству газобетонных блоков. Это доказано нашим 20-летним опытом в сфере строительного машиностроения и многочисленными историями успеха наших клиентов. С ними вы можете познакомиться на нашем сайте. А пока подробней рассмотрим оборудование для газобетона.
Линии по производству газоблоков отличаются комплектацией и соответственно производительностью. Чтобы оптимально подобрать оборудование для производства газобетона, нужно учесть несколько параметров: необходимое количество м3 газоблоков, площадь помещения и ваш бюджет.
Мы выпускаем около 200 наименований оборудования и любое из них по своей комплектации является полноценным заводом по производству неавтоклавного газобетона. В отличие от производства автоклавного газобетона, где стоимость оборудования превышает в десятки раз, а себестоимость продукции выше на 32%, наши линии спроектированы и изготовлены таким образом, что даже новичок сможет на них работать.
Все линии можно разделить на 2 категории — это оборудование конвейерного типа и стационарного. Основное их отличие состоит в следующем: в линии конвейерного типа — формы перемещаются по рельсам, а смеситель зафиксирован, а оборудование стационарного типа — смеситель перемещается по рельсам вдоль ряда форм.
Конвейерные линии — легко автоматизируются и позволяют сэкономить:
- площадь помещения — благодаря минимальному расстоянию между формами
- трудозатраты — т.к. выход готовой продукции всегда в одной точке, в отличие от стационарного типа, где готовые газоблоки нужно собирать по всему периметру расположения форм.
Стационарные линии — проще в монтаже и любую стационарную линию можно укомплектовать до конвейерной, установив рельсы для форм и камеры основного и предварительного прогрева, а также установив полную автоматизацию.
И в той и в другой категории оборудования есть мини линии — стационарного и мини линия конвейерного типа. Они в свою очередь отличаются объемом смесителя и количеством форм.
Все оборудование имеет различную производительность ( до 200 м3/сут.) и вы можете подобрать для себя самый оптимальный вариант — по объему производства и по цене. Но самое главное, любую линию можно модифицировать:
- Увеличивая количество форм — вы повышаете объем производства газоблоков в сутки
- Устанавливая автоматическую резку — добиваетесь идеальной геометрии блока, исключая человеческий фактор
- Добавляя автоматическую подачу песка и цемента (весовой дозатор, который позволяет произвести точный замер сырья) — вы не зависите от труда наемных работников.
Пример: Производительность автоматизированной, неавтоматизированной конвейерной линии и стационарной в помещении 200 м2.
Автоматизированная конвейерная линия |
Неавтоматизированная конвейерная линия |
Стационарная линия |
|
---|---|---|---|
Число рабочих на производстве |
2-4 чел.
|
2-6 чел
|
2-4
|
Объем м3/сутки |
До 40 м3/сут.
|
До 40 м3/сут.
|
20м3/сут.
|
Независимо от вашего выбора — будет это мини линия или крупный завод по производству газоблоков — мы оказываем всестороннюю профессиональную поддержку на всех этапах запуска производства газобетона: монтаж оборудования, пуско-наладка, поиск сырья, расчет себестоимости, предоставление рецептуры газобетонной смеси и продвижение готовой продукции на рынок (все это совершенно бесплатно). Это позволит вам изготавливать газобетонные блоки высокого качества.
asm.ru
технология производства и сферы применения
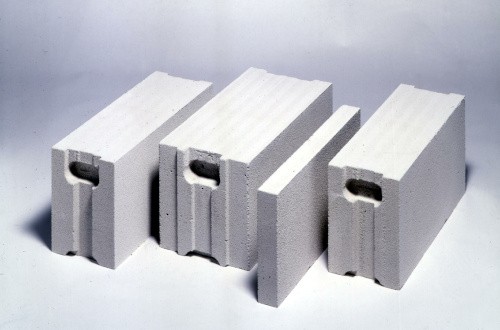
Видов автоклавного газобетона довольного много, перед тем как выбрать материал для строительства необходимо изучить его свойства и характеристику.
Легкий, сборный пенобетон был изобретен еще в 1920-х годах. Постоянно развиваясь, производство АГБ сейчас предлагает очень удобный современный строительный материал.
Что это такое
Газобетон автоклавный — это строительный материал на основе бетона. Он легко и быстро кладется, потому что его можно резать обычными электроинструментами из углеродистой стали сразу по месту работ.
Он выпускается в виде панелей, блоков или облицовочного материала.
Изготавливают его на заводах в Европе, Америке, России и Китае.
С АГБ строительство частных домов и высоток становится экономичнее и быстрее.
Виды и сфера применения
Газобетон автоклавный обладает положительными качествами: экологичность, теплоизоляция и легкость. Благодаря этим свойствам материал применяется в частном строительстве и при сооружение общественных зданий: школ, больниц, госучреждений.
Блоки меньших размеров используются при строительстве дач, загородных домов, гаражей и технических построек.
Благодаря малому весу выпускаются блоки следующих размеров (длина, ширина и высота в мм):
- 625 / 200 / 100;
- 625 / 250 / 400;
- другие размеры плит.
Блоки крупные применяются при возведении многоэтажных домов, для стен внутри помещений или ремонта старинных зданий.
Различают 3 категории АГБ по свойствам:
- Теплоизоляционный газобетон. Плотность до 400 кг/м2. Теплоизоляционный материал, который применяют в районах с холодными климатическими условиями.
- Конструкционный газобетон. Плотность 700 кг/м2. Применяется для несущих конструкций зданий до 3 этажей.
- Конструкционно-теплоизоляционный газобетон. Плотность 500 кг/м2. Универсальные качества теплоизоляции и прочности.
Если выполнить еще и армирование стен при строительстве из автоклавного легкого газобетона, то увеличится прочность конструкции. Архитекторы уже в проекте указывают необходимость данных работ.
Состав и характеристики автоклавного газобетона
При производстве используются следующие компоненты:
- портландцемент, без активных минеральных добавок от 35 до 49%;
- известь негашеная кальциевая с содержанием CaO не менее 70%;
- кварцевый песок с содержанием кварца SiO2 не менее 85%, а глинистых примесей не более 3%;
- гипсовый камень;
- алюминиевая пудра с содержанием активного алюминия не менее 80%;
- вода пресная для доведения массы к 100% объема;
- хлорид кальция от 0,18 до 0,25%
Достоинства автоклавного газобетона
- Соответствует нормам по пожарной безопасности за счет своей пористой конструкции.
- Легкий. Упрощается монтаж и снижается нагрузка на основание зданий.
- Не горит.
- Быстрая сборка, потому что выпускается в различных вариантах блоков и просто подгоняется под нужные размеры.
- Отличная звукоизоляция.
- Высокие теплоизоляционные свойства.
- Экологичность производства.
- Долгий срок службы газобетона проверен временем.
Однако имеются недостатки у данного вида стройматериала:
- Хрупкая структура из-за пористости.
- Крепления на стену из пенобетона требуется делать глубже и более тонкими крепежами.
- Низкая влагостойкость. Не рекомендуется использовать в душевых.
Автоклавный ГБ способен поглощать и выделять влагу. Это может быть не только недостатком. Это качество помогает избежать конденсата и плесени на стенах.
Оборудование для производства автоклавного газобетона
Этот процесс полностью автоматизирован и отлажен поставщиками оборудования.
Что он включает:
- Складирование и подготовка сырья. Цемент и известь пневмотранспортом с помощью компрессорной установки загружаются в расходные силосы. Жидкости заливаются в специальные емкости и доводятся до нужной температуры. Песок обрабатывается в мельнице и подается в шламовый бассейн. Алюминиевая пудра подготавливается в суспензиаторе.
- Смешивание компонентов производится в смесительной башне с пультом управления.
- Заполнение и формовка блоков делается на посту заливки.
- Резка блоков автоклавного газобетона на струнном резательном станке.
- Автоклавные печи для доведения блоков нагреваются до требуемых характеристик.
- Транспортировка готовых блоков осуществляется на поддонах погрузчиками.
- Готовые изделия отправляются на склад.
Технология производства
- Подготовка компонентов. Некоторые составляющие приходят на производство уже в готовом виде, другие проходят подготовку. Кварцевый песок, соединенный с водой перемалывается для образования шлама, а затем в шламбассейнах постоянно перемешивается и доводится до нужного показателя. Пудра из алюминия так же проходит предпроизводственную подготовку.
- Дозировка и перемешивание. Дозирование и подготовка смеси выполняется автоматически. Все компоненты, подготовленные заранее, точно взвешиваются и заполняются в большой миксер.Подготовленную смесь заливают в металлические формы — ванны на ½ от объема. В результате происходит химическая реакция компонентов с образованием водорода и блок заполняет всю форму и приобретет пористость. Пузырьки водорода могут быть до 3 мм. Но главное, что они практически равномерны. Это дает однородность структуры. Время смешивания всех компонентов составляет 5 минут на высокой скорости.
Алюминиевая пудра является взрывоопасным элементом, поэтому требуется строгое соблюдение противопожарных мероприятий в помещении, где производится АГБ.
Нарезка на блоки. Смеси дают немного затвердеть в форме, по технологии 2,5 часа, а когда извлекают, то она все еще достаточно мягкая. Резка на блоки нужного размера происходит на автоматизированной линии специальной струной.
- Автоклавная обработка. Затем подготовленные блоки-панели из АГБ оставляют в автоклаве на 12 часов. Там он при температуре 1900С и давлением пара 8 — 12 бар становится особо прочным, благодаря химической реакции кварцевого песка и гидроксида кальция.
- Сортировка и упаковка. После обработки в автоклаве газобетон сразу готов к использованию по назначению. Его выгружают из печей на поддоны и заворачивают в пленку для изоляции от влаги. В таком виде он хранится на складе. Затем его закупают строительные компании или специализированные магазины.
Отличия газобетона автоклавного и неавтоклавного
Различия этих двух строительных материалов очень большое, начиная от производства и заканчивая выдержкой перед поставкой потребителю. Состав их рецептур может быть одинаков, но технология, при которой автоклавный газобетон принимает качества искусственного камня, существенно различается.
Характеристики для сравнения представлены ниже.
Автоклавный | Не автоклавный газобетон | |
Качество структуры | За счет нагрева в автоклаве приобретает структуру искусственного камня. | Застывает естественным путем на воздухе или с применением пара при нормальном атмосферном давлении. |
Срок службы | Более 100 лет | До 50 лет. |
Прочность по регламентированию стандартов | В 2,5 — 5 | В 1,5 — 2,5 |
Морозостойкость | F 20 | F 15 — 35 |
Теплоизоляция и прочность одних параметров | Блоки толщиной 40 см | Блоки 65 — 75 см. |
Размеры блоков | Нарезка происходит автоматически с минимальными погрешностями. Допустимые отклонения в среднем 2,5 мм. | Изготавливается в разборной опалубке, что допускает значительные отклонения в готовых изделиях. Отклонения в размерах до 5 мм. |
Укладка | Точные размеры требуют минимум соединительного раствора. | Требуется больше раствора для выравнивания неровностей блоков. |
Усадка готового изделия | До 0,4 мм/м | До 5 мм/м |
Структура готового блока | Равномерна по всей глубине. | Различаются в блоке и по всей партии. |
Цвет | Равномерно белый. ВНИМАНИЕ! Неравномерный цвет автоклавных пеноблоков говорит о нарушении рецептуры или технологии изготовления. | Разнородный серый. |
Важный фактор — экономия времени на сборку конструкций зданий. За счет точной обрезки АГБ уже на заводе по известным размерам, на строительной площадке времени на подгонку уходит меньше и, соответственно, процесс получается менее трудозатратным.
Автоматизированный процесс делает такой газобетон дорогим, но выгоды и преимущества говорят о правильности вложения средств. Автоклавный газобетон более качественный, и зарекомендовавший себя с лучшей стороны как по техническим свойствам, так и по внешнему виду. Технология изготовления делает газобетон отличным материалом как для строительства зданий, так и для создания бизнеса.
Популярное
dvabrevna.ru
обзор типов линий и установок

Производство блоков из газобетона
Еще не так давно, производство популярного материала в виде строительного камня было возможно лишь в условиях завода. Но с усовершенствованием технологий такая возможность появилась не только у мелких предпринимателей, но и у самих застройщиков.
На данный момент существует большое количество различного оборудования, предназначенного для изготовления данного представителя ячеистых бетонов. Комплекты отличаются между собой по ряду признаков, а в первую очередь ценовой категорией и объемом выпуска.
В данной статье мы будем рассматривать оборудование для производства газобетонных блоков разного типа, и проанализируем сам процесс изготовления изделий. А также сравним материал, произведенный в домашних и заводских условиях.
Содержание статьи
Общая технология производства газобетона
Предварительно, пожалуй, рассмотрим общий принцип технологического процесса. Ведь для полноценного обзора линий оборудования, нам нужно иметь представление о том, как именно изготавливается газобетонный блок.
Необходимое сырье
Для приготовления газобетонной смеси, понадобится наличие следующего сырья:
- Цемент марки не менее М400;
- Вода;
- Известь негашеная;
- Гипс;
- Песок кварцевый;
- Алюминиевая пудра.

Алюминиевая пудра
Также не помешает добавить в раствор пластификатор. Основное его предназначение – повышение пластичности раствора, что предотвращает растрескивание изделий на стадии сушки и твердения.

Пластификатор
Другие химические добавки также используются. Как правило, они добавляются с целью повышения качеств готовых изделий.

Пропорции сырья вместе с добавками
Обратите внимание! Вышеуказанный состав является классическим. Многие компоненты могут заменяться. В этом случае набор числовые значения свойств также будут варьироваться.
- Кремнеземистый компонент может быть представлен в виде: песка, золы и иных вторичных продуктов промышленности;
- Тип вяжущего также может быть разным: цементным, шлаковым, известковым, смешанным, зольным.
Примерное содержание пропорций – следующее:
- 50-60% — цемент;
- 20-40% — песок;
- 1-10% — известь;
- До 1% — вода.
На заметку! При желании повысить плотность изделий, следует увеличить количество цемента. В этом случае также изменится и масса готового материала, и коэффициент теплопроводности.

Пропорции в зависимости от желаемой плотности
Основные этапы
Краткая инструкция выглядит следующим образом:
- Первым делом взвешиваются компоненты и смешиваются в необходимых пропорциях. При изготовлении своими руками это делается вручную, в заводских условиях, как правило, в автоматическом режиме.
- Все ингредиенты попадают в смеситель, где и происходит смешивание.
- Следующим этапом станет формовка. Формы наполняются примерно на 1/3, так как при порообразовании смесь попросту может вытечь.
- Следом, после завершения процесса вспучивания, выжидается некоторое время до частичного застывания.
- Далее производят резку единого пласта или просто распалубку, если формы используются уже готовых типоразмеров.
- Последним этапом станет автоклавирование либо отправление блоков на сушку при неавтоклавном способе производства.
Обратите внимание! Ход процесса может несколько отличаться в зависимости от того, какое оборудование для изготовления газобетонных блоков используется. Однако в целом, общий принцип будет аналогичным.
Типы установок и линий
Теперь перейдём непосредственно к обзору типов оборудования.
Конвейерный тип
Оборудование для газобетона конвейерного типа отличается:
- Максимальной автоматизацией производства;
- Минимальным участием работников;
- Высокой стоимостью;
- Большими объемами производства;
- Полной комплектацией;
- И, как правило, наибольшей рентабельностью.

Большая конвейерная линия
Рассмотрим подробнее комплектацию и возможности такого газобетонного оборудования на примере линии популярного китайского производителя, являющегося дилером компании Премиум Кирпич Плюс.
В стандартный комплект входят:
- Емкости и бункеры для сырья;

Бункер для сырья
- Ленточные конвейеры для транспортировки компонентов;

Ленточный конвейер
- Узел растворосмесительный;

Узел бетоно-растворный

Автоклавы

Сборная форма для блоков
- Резательный комплекс;
- Транспортер перемешивающий;
- Дробилки;
- Тележки;
- Узел для автоматического управления линией;
- Погрузчик вилочный.
Такое оборудование для производства стоит около 55 000 000. Согласитесь, сумма, не маленькая. Однако при этом, производительность составляет около 300 тысяч метров кубических в год. Площадь, необходимая для размещения такой линии должна быть около 4000 м2.
В качестве альтернативы, можно рассмотреть возможность приобретения конвейерной линии в бывшем употреблении. Это – своеобразный риск, однако стоимость ее значительно ниже.
Также стоит обратить внимание на мини линию конвейерного типа «Иннтех-100». Ее производительность значительно ниже и составляет 100 м3 в сутки. Цена ее – около 3 000 000.

Мини конвейерная линия
Данная линия характеризуется неподвижным смесителем. Формы передвигаются по рельсовому транспортеру как тележка. Компоненты подаются и дозируются в автоматическом режиме. Резательный комплекс – механический.
Больше всего среди производителей ценятся линии известных немецких производителей оборудования. Они отличаются высокой продуктивностью, долговечность в использовании. С их помощью можно изготавливать блоки самого высокого качества.

Немецкое оборудование для изготовления газоблока
Видео в этой статье продемонстрирует принцип работы оборудования для изготовления газобетона.

Производство газобетона Поревит
Стационарный тип
- Такой тип оборудования гораздо менее дорогостоящий. Однако и производительность ее гораздо ниже и составляет около 50 м3 в сутки.
- Как правило, в комплект таких линий входят дозаторы компонентов и ленточный транспортер, который и подает ингредиенты в смеситель.
- Однако полностью автоматизированным такой комплект назвать уже нельзя. Для полноценной работы требуется наличие как минимум нескольких человек.
- Необходимая квадратура для размещения производства и склада составляет около 500 м2.

Линия стационарного типа для производства газобетонного блока
В качестве примера, кратко рассмотрим комплектацию и возможности линии АСМ-1МС.
- Производительность составляет около 60 м3;
- Для работы потребуется привлечение 3-4-х человек;
- Песок и цемент подаются в автоматизированном режиме.
Комплектация:
- Смеситель для вяжущего и иных компонентов;
- Конструкция для резки блочного массива с пилами;
- Формы и поддоны;
- Транспортер.
Мобильные установки и мини-линии
Такое оборудование для производства блоков газобетонных идеально подойдет для начинающих предпринимателей либо застройщиков, желающих изготовить изделия для собственных нужд.
При помощи мобильной установки можно произвести исключительно только газоблок неавтоклавного твердения. Ниже мы рассмотрим основные его отличия от основного конкурента.
Такой оборудование требует наличия сети в 220 Вт, в то время как другие типы машин требуют подключения к сети в 360 Вт. Объем производства составляет около 2-10 м3 в сутки.

Установка мобильная для изготовления газобетона
Рассмотрим характеристики установки на примере комплекта Газобетон 500Б.

Установка газобетон 500 Б
- В комплект входит: смеситель, соединительные рукава и компрессор. Для производства необходимо участие нескольких человек.
- Практически весь процесс работ происходит с участие человека. В автоматическом режиме производится только смешивание.
- Дозирование также придется производить самостоятельно.
- Объем выпуска 3 м3 пористой смеси.
- Емкость для смешивания- 500 литров.
Мини-линии более производительны. С их помощью возможно изготовление вплоть до 25 м3 в сутки. Для мелких предпринимателей – отличный вариант начать свое дело.
Принцип их устройства – аналогичен мобильным установка, больше – мощность и объем смесителя.
Подробнее об автоклавировании
Теперь давайте более подробно поговорим об автоклавной обработке газоблока и разберемся, в чем заключаются основные различия между изделиями самостоятельного производства и материалом, выпущенным в условиях завода.
Что представляет собой автоклавная обработка?
При помощи автоклавной обработки удается повысить качества готовых изделий.
- Разрезанные на типоразмеры блоки помещаются в автоклав и обрабатываются под действием давления выше атмосферного водяным паром, при этом преобладает высокая температура.
- Обработка длится в течение 12-ти часов.
- По окончании обработки, блоки практически сразу можно использовать в строительстве, ведь марочной прочности они уже достигнут.
- Неавтоклав же набирает прочность в течение 4-х недель.
- При автоклавной обработке повышаются такие качества как: прочность, плотность, долговечность. Изделия становятся менее хрупкими
Стоит отметить, что изготовление блоков автоклавного твердения возможно только в заводских условиях.

Процесс автоклавирования
Сравнение автоклавного и неавтоклавного газоблока
А теперь сравним свойства автоклавного газобетона и изделий, достигающий прочности естественным способом.
Характеристика | Сравнительный анализ |
![]() Сочетание плотности и теплопроводности | За счет специализированной обработки в автоклаве, изделия синтезного твердения отличаются лучшим сочетанием показателей плотности и теплопроводности. |
![]() Морозостойкость и долговечность | В соответствии с ГОСТ, требования к марке по морозостойкости к неавтоклавному блоку несколько ниже. Точные сроки долговечности обоих изделий не установлены опытным путем, в силу недостаточного времени существования материала на рынке строительных материалов. |
![]() Внешний вид и геометрия изделия | Автоклав имеет практически идеальную геометрию. Неавтоклавный блок, изготовленный в домашних условиях в данном отношении серьезно ему уступает. |
![]() Требования к оборудованию и сложность производства | Оборудование для газобетона автоклавного, в целом, отличается лишь наличием автоклавов. Технология производства – аналогична, порядок – тоже. |
![]() Хрупкость | Неавтоклавные блоки больше уязвимы к механическому воздействию, они более хрупкие. |
![]() Стоимость | Автоклавные изделия дороже примерно на 10%. |
![]() Усадка | Неавтоклавные блоки больше подвержены усадке. Показатель составляет до 1 мм/м2. |
В заключение
На современном рынке существует большое количество различных комплектов оборудования для производства газобетонных блоков, начиная от дорогостоящих крупномасштабных конвейерных линий и заканчивая бюджетными мобильными установками. Именно поэтому производство данного материала стало еще более популярным.
beton-house.com
Автоклавный и неавтоклавный газобетон — АлтайСтройМаш
Вы обязательно должны выделить несколько минут своего времени, чтобы прочитать эту важную статью. Сегодня мы расскажем вам всю правду об автоклавном и неавтоклавном газобетоне (а точнее, о его производстве):
— Почему неавтоклавное производство с каждым годом становится все популярнее?
— Чем отличается автоклавный газобетон от неавтоклавного?
— Почему сроки окупаемости бизнеса на производстве неавтоклавного газобетона как минимум в 20 раз меньше, чем на автоклавном производстве?
— Почему неавтоклавное производство намного выгоднее для производителей?
Итак, что лучше: автоклавный или неавтоклавный газобетон? Читайте нашу статью, и вы все узнаете!
1. Технология производства
Основной компонент автоклавного газобетона – известь, которая затвердевает только при особой обработке. Для этого используются автоклавы – герметично закрывающиеся аппараты, в которых поддерживается постоянная температура (180-200С) и давление (12-14 атм). Твердение автоклавных газоблоков происходит в течение 12 часов.
Основной компонент невтоклавного газобетона – цемент, который смешивается с наполнителем (песок, зола уноса ТЭЦ, доломитовая мука и др.) и газообразователем (алюминиевая пудра/паста). Для затвердевания таких газобетонных блоков необходимо добиться температуры всего 40-60С (для этого используются простые прогревочные камеры). Необходимое время для набора первоначальной прочности – 6-10 часов.
2. Стоимость
Для запуска автоклавного производства потребуются огромные финансовые вложения. Например, минимальная стоимость китайского оборудования – 1 500 000 долларов. При этом стоит учитывать тот факт, что вам вряд ли будет оказана полноценная техподдержка.
Если рассматривать качественное оборудование от немецких производителей, то стоимость линии с производительностью 200 кубометров газобетона в сутки составит примерно более 6 000 000 долларов!
Линию для производства неавтоклавного газобетона можно купить за 85 000 долларов. Это стоимость оборудования с максимальной производительностью – 200 кубометров в сутки. При этом линию с минимальной производительностью можно купить всего за 3 000 долларов.
3. Сроки изготовления оборудования
Если вы хотите организовать бизнес «здесь и сейчас», то автоклавное производство – точно не для вас. Сроки изготовления автоклавного оборудования – минимум 1 год (а в среднем – 1,5 года) после официального заключения сделки.
Срок изготовления и поставки оборудования по производству неавтоклавного газобетона в среднем составляет 10-30 дней.
4. Затраты на электроэнергию
Энергозатраты на автоклавном производстве в десятки раз больше. К примеру, мощность электродвигателя шаровой мельницы – около 100 кВт, а это обязательное оборудование на автоклавном производстве. А теперь представьте, сколько энергии нужно, чтобы поддерживать в автоклавах температуру до 200 градусов и давление до 14 атмосфер!
Энергозатраты на неавтоклавном производстве минимальны:
— Электропитание основного оборудования: от 4 до 15 кВт (зависит от типа оборудования).
— Нагрев воды до 50-60С.
— Нагрев прогревочной камеры до 40-60С (требуется только поддержание температуры).
5. Сроки окупаемости бизнеса
Учитывая все предыдущие пункты, приходим к логичному заключению: бизнес по производству автоклавного газобетона окупится минимум через 5-10 лет!
Срок окупаемости бизнеса по производству неавтоклавных газоблоков составляет всего 5-6 месяцев!
Отличия автоклавного и неавтоклавного газобетона: есть или нет?
Мы рассмотрели основные различия бизнеса по производству автоклавного и неавтоклавного газобетона. Переходим к подведению итогов!
1. Автоклавный и неавтоклавный газобетон должны отвечать требованиям одного и того же ГОСТа.
2. Соответственно, при соблюдении технологии производства на выходе мы получим одинаковые по характеристикам материалы.
3. Самое интересное, что после отделки многие не могут отличить дома, построенные из автоклавного и неавтоклавного газобетона. Единственное отличие – цвет блоков; прочностные характеристики будут идентичны.
Более 5 000 клиентов компании АлтайСтройМаш уже стали производителями неавтоклавного газобетона!
А какой бизнес выберете вы?
Подобрать оборудование
asm.ru
Линия для производства автоклавного газобетона(AAC) /Линия по производству газобетонных блоков автоклавного твердения
Технические характеристики:
1. технологии германии
2. опыт 20 года
3. 30 линиий за рубежом
Линия для производства автоклавного газобетона(AAC)
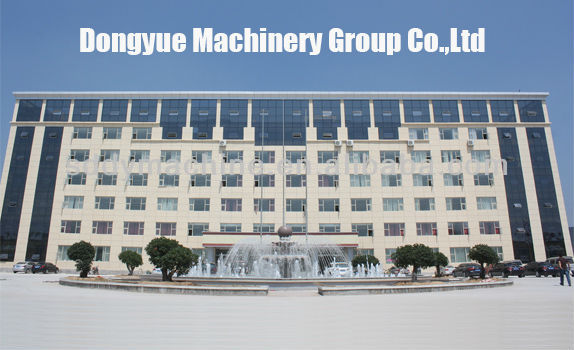
Dongyue Machinery Group является компанией, специализирующаяся в производства AAC МАШИНА БЛОКА , AAC МАШИНА ПАНЕЛИ, объём производства завода 50000-300000 кубических метров готовой Продукции в год. При технологического сотрудничества с AAC КОНЦЕПЦИЕЙ Германской компании, наша AAC Машина блока наследует технологии Германии. По настоящее время у нас уже 15 линий AAC в Индонезии, 10 линий в Индии, 5 линий во Вьетнаме, 2 линии в Бума, 2 линии в Монголии, 1 линия в Казахстане, 1линия в Болгарии.
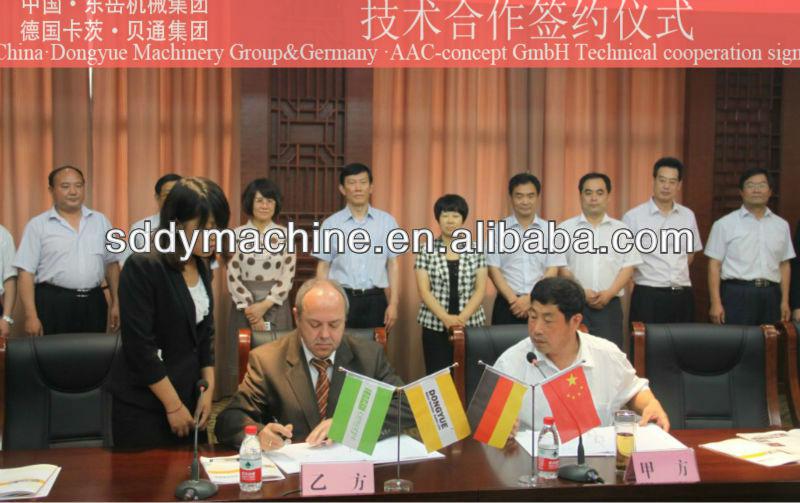
Технические обмени и сотрудничества со Германией AAC коцепция GMBH
2. Что такое ААС?
ААС-легкие сотовые силикатные продукты. Его основной материал на основе кремневого материалов (песок, зола, пустая порода с содержанием кремнием) и кальция (цемент и известь), смешается с пенообразователем (алюминиевая пудра), после дозирования, смешивания, заливки, предварительного отверждения, резка, потока (autocaled) и другой процесс, наконец этот легкое бетонноеизделие образование.

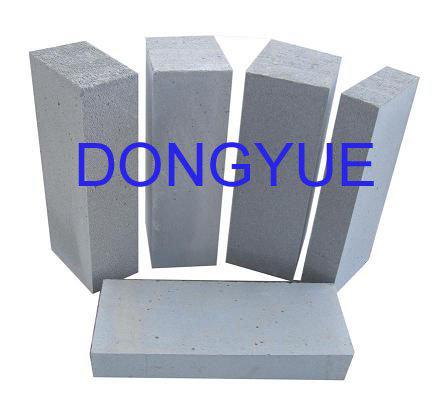
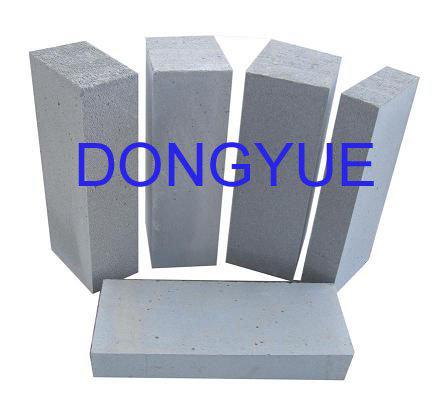
3. Введение серья ААС
Летучая зола: это отходы тепловой завода. Она богата кремнезем и оксидом алюминиям и является хорошим сырьем чтобы сделать AAC блок. Летучая зола также делится на два вида — мокрой летучей золы и сухой летучей золы .Способ обработки будет меняться в соответствии с условием летучей золы
Песок: Кроме летучей золы, песок может быть основным материалом, но содержание кремния сбязательно выше 69%. Морской песок не может быть использован в качестве исходного материала AAC.
Известь: Активная известь является необходимой условией для предоставления реального аэрации к продукту. В первом фазе мы можем непосредственно купить активные извести. Во второй фазе мы можем образовать обратную интеграцию и принять известь подачи питания прибор на сайт, чтобы получить больше конкурентных преимуществ, Мы также можем установить известообжигательную печь на заводе.
Цемент OPC: Это обычный портландцемент. Данный проект направлен использовать OPC цемент в качестве основного связующего материала. Это даст более быстрое силы кирпичей, кроме предоставления улучшенной стабильное качество. Он также обеспечивает лучшую эффективность затрат для того же. Использование OPC будет стандартизированной практикой. Другие преимущества использования OPC (по сравнению с другими связующими) является его лёхкой доступностей через общенациональной розничной сети цементных компаний.
Гипс: Это тоже промышленный отход. В качестве промышленного побочный продукт завода по производству удобрений. Гипс лёгко доступно и отвечает дать долгосрочную прочность к блокам.
Аюминиевая пыль: Аюминиевая пыль используется в очень ограниченном количестве (менее 0,5%), так, что она вступает в реакцию с активной известью и кремнезем в основной материал, чтобы сделать аэрации,
Название | объединение | цемент, известь, летучая зола |
летучая зола | % | 65-70 |
цемент зола | % | 6-15 |
известь | % | 18-25 |
гипс | % | 3-5 |
раствор алюминиевой порошка | 1/1000 | 8 |
вода& скорость материала | 0.6-0.65 | |
система литья | °c | 36-40 |
время смешивания алюминия | S | 30-40 |
Доля цемента, извести и песка по производству газобетонного блока
Название | объединение | цемент, известь, летучая зола |
летучая зола | % | 55-65 |
цемент зола | % | 10-20 |
известь | % | 20-30 |
гипс | % | 2-3 |
раствор алюминиевой порошка | 1/1000 | 8 |
вода& скорость материала | 0.65-0.75 | |
система литья | °c | 35-38 |
время смешивания алюминия | S | 30-40 |
4. Описание процесса производства автоклавного газобетона
01. Запас и подготовка сырья
02. Дозирование, смешивание и заливка
03. Созревание и резка массива
04. Автоклавная обработка и упаковка продукта
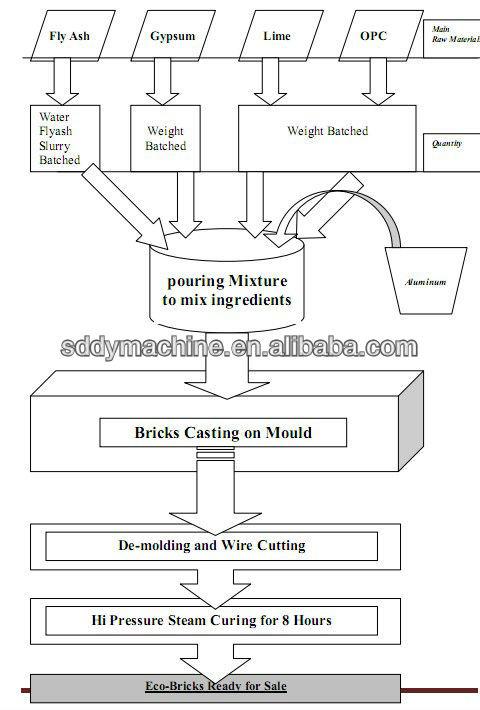
Течение работы ААС
5. подготовительная работа линии ААС
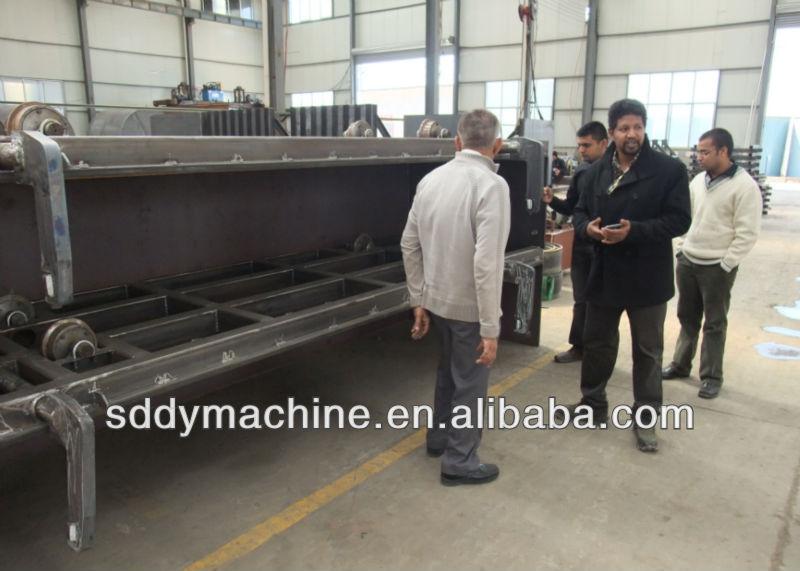
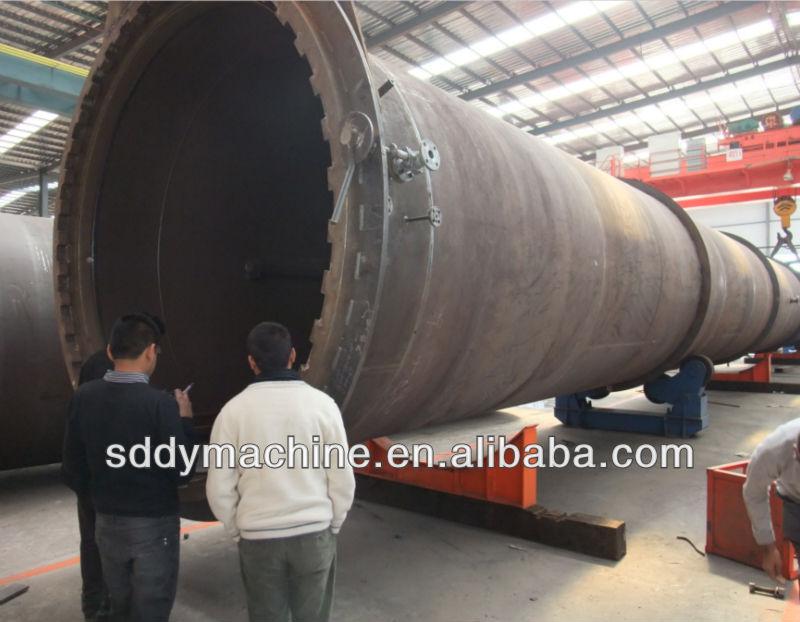
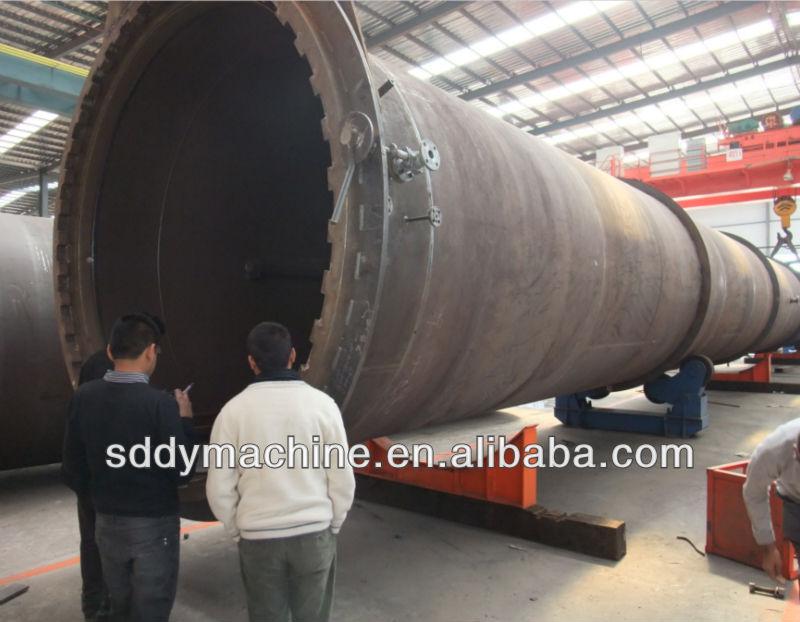
6. Обзор транспрота линии ААС
1. Обычно резательная машина и котёл будут погружены плоской стойки
2. Автоклавы погружен навалочными грузами
3. Другие части будут погружены содержаться в контейнере
7. Обзор установки линии ААС
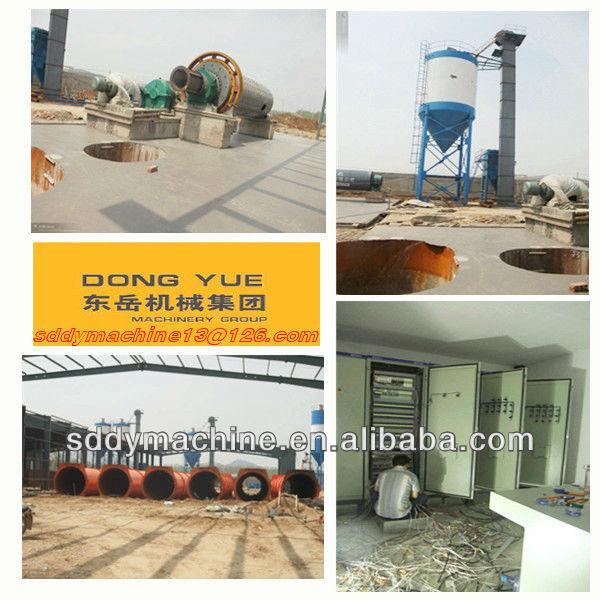
8. Обзор линия ААС
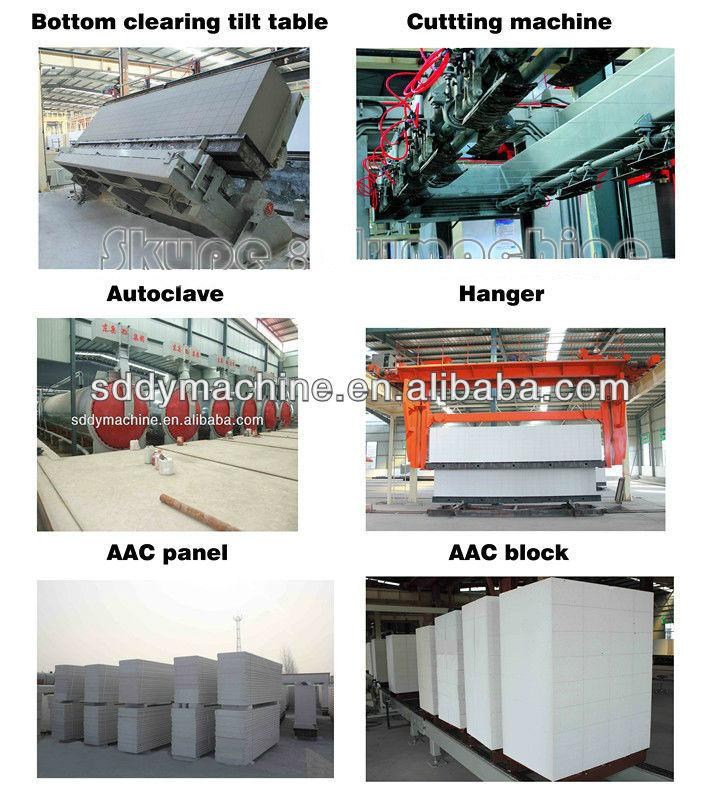
russian.alibaba.com
Оборудование для производства газобетона_ГРУППА КОМПАНИЙ
Процесс производства:
Более 500 линий для производства газобетона, произведенные Группа Компаний “Дунюе”, сданы в эксплуатацию внутри Китая и за рубежом (Россия, Казахстан, Монголия, Индонезия, Вьетнам, Индия, Филиппины и т.д.). Преимущества нашей компании являются техническое сотрудничество с aac-concept GmbH Германии и качественные оборудования.
1.Подготовка сырья
Используя технологию “DONYUE”, исвесть, цемент, гипс и кварцевый песок размалываются до плотности шлама 4000см2/g, так как больше активные вещества участвуют в химическую реакицю, повышается прочность газобетона.
Шаровая мельница
В шаровой мельнице песок и гипсовый камень (при совместном помоле) вместе с водой размалываются до плотности шлама 1,60 — 1,70 кг/л. Мощность мельницы зависит от производительности линии, потребляющей в среднем около 0,4 — 0,5 т шлама на один кубометр газобетона.
Шламбассейны
Шлам потом перекачивается в один из шламбассейнов оснащённых мощным приводом и одновальной мешалкой. Помимо шламбассейнов прямого шлама существуют шламбассейны возвратного шлама, предусмотренные для хранения шлама, возвращающегося с производственного процесса. Количество бассейнов зависит от производительности линии, местных условий и предписаний заказчика.
2. PLC автоматическая система дозирования и смешивания
При помощи специально сконструированной дозирующей системы и на основе отработанной сырьевой рецептуры, заложенной в системе управления, их содержимое дозируется, взвешивается перед смешиванием и затем подается в смеситель в определенном порядке в полностью автоматическом режиме. Кроме массы измеряется температура компонентов и плотность шлама. Температура смеси регулируется посредством добавления точного объема холодной или горячей воды.
3. Заливка смеси и зона созревания
Приготовленная бетонная смесь заливается в прямоугольные стальные формы закрытого типа, с одним съемным бортом (платформой). Затем массив-сырец подвергается предварительному выдерживанию на участке созревания с целью набора определенной структурной прочности газобетоном, достаточной для последующей его распалубки и резки на определенные изделия. Срок созревания зависит как от сырьевых параметров, так и от внешних условий. Как только массив приобретет достаточную твердость для последующей резки, форма автоматически транспортируется из зоны созревания под кантующий манипулятор.
3.1 Производство армированных панелй из газобетона
Для производства армированных панелей требуется стальная арматура. После заливки устанавливается дополнительная секция в технологическом процессе, на которой в свежую смесь устанавливается арматура.
4. Кантование массива
Кантующий манипулятор поднимает форму с массивом, разворачивает ее на 90 град. и устанавливает на борту формы для последующей резки.
5. Линия резки газобетонных блоков
Устройство вертикальной, пред-варительной и последующей боковой резки (боковой триммер) обрезает массив по длине, высоте и ширине. Оно состоит из устройств предварительной и последующей боковой резки, оборудовано ножами предварительной резки и режущими струнами (боковой триммер) с возможностью регулировки толщины срезаемого слоя для резки массива или выравнивания его поверхности уже после предварительной резки.
Устройство боковой контурной обработки при помощи режущего инструмента соответствующей конфигурации вырезает профиль (система паз-гребень).
6. Обратное кантование массива
Подъемный манипулятор поднимает разрезанный массив, стоящий на борту, и перекладывает его на стол кантования, на котором массивы разворачиваются на 90° и помещаются на специальную решетку, на которой они далее транспортируются в автоклавы.
7. Автоклавная обработка
Выдержка изделий в автоклаве обычно длится 12 часов, однако это время зависит от характеристик сырья и объемной плотности продукта.
8. Разделение массива
После процесса пропарки, манипулятор переносит масив на тележке и перемещается к разделению, разделитель можно передвижным или фиксированным, передвижной разделитель DONYUE получен патент на изобретение Китая.
9. Упаковка:
Изделия упаковываются в термоусадочную пленку и перевозятся вилочными погрузчиками на склад.
10. Отгрузка
Продукция отгружается заказчику в специально отведенной зоне погрузки.
www.donyuegroup.ru